Autonome Wartung:Was es ist und warum es wichtig ist
Autonome Wartung steigert die Effizienz durch Schulung des Bedieners zur Durchführung kleinerer Wartungsaufgaben. Im Folgenden besprechen wir die Implementierung einer autonomen Wartung, deren Aufrechterhaltung und mehr.
Was ist autonome Wartung?
Autonome Wartung ist definiert als eine Wartungsstrategie, bei der Maschinenbediener ihre Ausrüstung kontinuierlich überwachen, Anpassungen vornehmen und kleinere Wartungsarbeiten an ihren Maschinen durchführen. Dies geschieht, anstatt einen dedizierten Wartungstechniker mit der Durchführung der Wartung und der regelmäßig geplanten Wartung zu beauftragen.
Die autonome Wartung ist die erste Säule in der Strategie für die produktive Gesamtwartung. Ein in autonomer Wartung geschulter Bediener bedeutet, dass er oder sie über umfassende Kenntnisse der Routineaufgaben wie Reinigen, Schmieren und Prüfen verfügt. Es verlangt von den Betreibern, dass sie das Eigentum an ihrer Ausrüstung und deren Umgebung übernehmen. Dies beginnt damit, dass die Maschine auf einen "neuwertigen" Reinigungsstandard gebracht und dort gehalten wird, die Bediener in den richtigen technischen Fähigkeiten für die Durchführung von Routineinspektionen geschult werden und ein autonomer Inspektionsplan standardisiert wird.
Die autonome Wartung folgt zwei Kernprinzipien:
- Um eine Verschlechterung der Ausrüstung durch ordnungsgemäßen Betrieb zu verhindern, und;
- Ausrüstung durch Restaurierung und ordnungsgemäße Verwaltung in den Zustand "wie neu" bringen und halten.
Vieles davon hängt davon ab, dass die Bediener wissen, wann eine Maschinenaufrüstung erforderlich ist oder wann eine einfache Fehlerbehebung die Maschine schnell wieder zum Laufen bringen kann. Autonome Wartung erfordert, dass Bediener Fähigkeiten wie das Erkennen von Anomalien beherrschen, indem sie die Komponenten der Maschine verstehen, Verbesserungen vornehmen, mögliche Qualitätsprobleme identifizieren und deren Ursachen ermitteln.
Da das ultimative Ziel einer produktiven Gesamtwartung darin besteht, die Gesamtanlageneffektivität Ihres Unternehmens zu verbessern, gibt es einen Grund dafür, dass dies mit der autonomen Wartung beginnt. Es entlastet qualifiziertes Wartungspersonal von den einfachen, alltäglichen Wartungsaufgaben, damit es sich auf spezielle Wartungsprojekte konzentrieren kann. Dies führt zu mehreren Vorteilen wie:
- Erhöhung der Kenntnisse der Bediener über ihre Ausrüstung
- Halten Sie die Ausrüstung in einem "wie neu" Zustand und stellen Sie sicher, dass sie sauber und geschmiert sind
- Die Fähigkeit, aufkommende Probleme zu erkennen, bevor sie zu Fehlern werden
Dadurch, dass Maschinenbediener diese routinemäßigen Wartungsinspektionen und -aufgaben bewältigen können, wird die OEE durch die Reduzierung von Ausfällen und Verschlechterung der Ausrüstung weiter maximiert.
So implementieren Sie eine autonome Wartung
Die Implementierung der autonomen Wartung kann je nach Betrieb der einzelnen Anlagen leicht variieren, ist jedoch in der Regel in sieben Schritte unterteilt.
- Erhöhen Sie die Kenntnisse der Bediener. Bediener mögen die Meister darin sein, ihre Maschine mit maximaler Kapazität zu betreiben, aber für eine effektive autonome Wartung müssen sie die Besonderheiten ihrer Maschine kennen. Dabei geht es um Schulungen von Instandhaltern zu technischen Details zur Funktionsweise und Verwendungszweck der Maschinenkomponenten sowie zur Schulung von Problemlösungskompetenzen. Kurz gesagt sollten Bediener über vier ausrüstungsbezogene Fähigkeiten verfügen:
- Auffälligkeiten erkennen
- Korrigieren und Wiederherstellen von Anomalien
- Einstellung optimaler Ausrüstungsbedingungen
- Aufrechterhaltung dieser optimalen Ausrüstungsbedingungen
Sobald diese Fähigkeiten im Klassenzimmer überprüft wurden, können Bediener grundlegende Wartungsaufgaben an ihren Maschinen durchführen, während Wartungstechniker beobachten, um sicherzustellen, dass alles abgedeckt ist.
- Erste Reinigung und Inspektion der Maschine. In diesem Schritt wird die Ausrüstung in einen "Grundzustand" zurückversetzt, mit dem Ziel, sie wieder in einen "wie neu" Zustand zu versetzen. Für diese Aufgabe sind alle Mitarbeiter an Deck, darunter Mitglieder aus Produktion, Instandhaltung, Technik und Bedienern. Nicht nur die Geräte werden gründlich überholt und gereinigt, sondern auch die Umgebung wird gereinigt. Das Ziel besteht darin, die volle Leistungsfähigkeit jedes Gerätes wiederherzustellen, indem Anzeichen von Verschlechterung erkannt und beseitigt werden. Teams sollten nach Dingen suchen und diese korrigieren:
- Lecks
- Lose Schrauben
- Richtige Schmierung
- Risse – sowohl sichtbar als auch nicht sichtbar
- Kontaminationsraten von Flüssigkeiten
- Entfernung von Material aus Wasser und Öl
- Entfernung von Staub und Schmutz
- Leitfähigkeitseinschränkung in der Elektrofertigung durch Öl- und/oder Staubablagerungen
- Beseitigung von Unterbrechungen durch Staubansammlung
Es ist eine gute Idee, das Protokoll während dieser gründlichen Reinigung zu dokumentieren, damit Probleme leicht zurückverfolgt werden können und Bediener auf etwas zugreifen können, das leicht zu befolgende Schritte enthält.
- Beseitigen Sie die Ursache der Kontamination und verbessern Sie den Zugang. Nachdem die anfängliche Reinigung abgeschlossen ist und alle Geräte wiederhergestellt sind, stellen Sie sicher, dass sie nicht wieder in einen schlechten Zustand geraten. Dies kann erreicht werden, indem alle möglichen Kontaminationsquellen eliminiert und die Zugänglichkeit für Reinigung und Wartung verbessert werden.
Dieser Schritt berücksichtigt auch die Sicherheit. Die Wartung einer laufenden Maschine ist gefährlich, daher ist die Verbesserung der Sicherheit und Sichtbarkeit durch bessere Zugangspunkte von größter Bedeutung. Ein beliebter Weg, dies zu tun, besteht darin, blickdichte Abdeckungen durch transparente zu ersetzen, um die laufenden Teile schnell und einfach zu visualisieren. Die Beseitigung der Kontaminationsursache kann erfolgen durch:
- Etablierung und Einhaltung von Reinigungsstandards.
- Vermeiden von Verschmutzungen. Qualitätsdichtungen und Maschinenabdeckungen sind gute Ausgangspunkte, aber einige Verunreinigungen können nur durch Investitionen in Pumpen oder Entstaubung eingedämmt werden – entweder pneumatisch oder durch Trockensiebung.
- Förderung der Sauberkeit. Wiederholen Sie die Sauberkeit bei Inspektionen und Wartungsarbeiten ständig.
- Förderung von Ordnung. Sicherzustellen, dass Werkzeuge ihren Platz haben und dort bleiben, erhöht die Effizienz.
- Entwickeln Sie Standards für Schmierung und Inspektion. Dieser Schritt kann je nach Ausrüstung und Bediener nach Bedarf angepasst werden. Die Festlegung von Standards für Bediener in Bezug auf Reinigung, Inspektion und Schmierung sollte mit der aktuellen Dokumentation in den Akten beginnen und mit verbesserten Möglichkeiten zur Durchführung dieser Verfahren enden. Normen sollten angeben, welche Komponenten gereinigt und geschmiert werden sollten, wie sie gereinigt und geschmiert werden sollten und alle anderen Wartungsaufgaben zuzuweisen sind. Die Standards variieren je nachdem, ob die Maschine als unkritisch oder kritisch eingestuft wird.
- Bei nicht kritischen Maschinen werden die Bediener von einem erfahrenen Wartungstechniker geschult, um die etablierten Standards einzuhalten. Die Bediener können dann ihre eigene Routine erstellen.
- Für kritische Maschinen kann ein Team von Wartungsingenieuren gebildet werden, die sich mit Wartungsmethoden befassen, um Standards zu entwickeln.
Nach der Fertigstellung sollten alle Standards dokumentiert und den Betreibern leicht zugänglich gemacht werden.
- Inspektion und Überwachung. Da nun eine Reihe von Standards befolgt werden müssen, können Bediener ihre grundlegende Wartungsroutine ändern, um Aufgaben zu rationalisieren und zu verbessern. Die Wartungsaufgaben des Betreibers werden verfolgt und mit den eigenen Zeitplänen der Wartungsabteilung (normalerweise durch ein computergestütztes Wartungsmanagementsystem) verglichen, um sicherzustellen, dass doppelte Aufgaben kein Problem darstellen. Bediener führen die grundlegenden, oft übersehenen Wartungsarbeiten durch, z. B. das Überprüfen des Schmierstoffstands, das Auffinden von Lecks, das Anziehen von Schrauben, das Suchen nach drohenden mechanischen Problemen wie Rissen und Verschleiß und das Durchführen mechanischer Einstellungen wie Spannungsmessungen, Sensorregelung usw.
- Standardisieren Sie die visuelle Wartung. Die Standardisierung der autonomen Wartung und die "Visualisierung" von Geräten ist ein wichtiger Schritt, um die Integrität jedes Maschinenteils zu erhalten. Wie macht man Ausrüstung sichtbar? Beispiele hierfür sind die Identifizierung des Durchflusses von Flüssigkeiten durch Rohrleitungen, das Ersetzen von undurchsichtigen Abdeckungen durch transparente, wenn möglich, die Kennzeichnung der Öffnungs-/Schließrichtung von Ventilen und Hebeln und die grüne Markierung von "sicheren" oder "normalen" Betriebswerten auf Manometern und Schaugläsern mit gefährlichen Ebenen in rot. Kurz gesagt, machen Sie die Dinge an der Maschine so offensichtlich wie möglich.
- Kontinuierliche Verbesserung. Es ist wichtig, sich regelmäßig die Zeit zu nehmen, einen Schritt zurückzutreten und standardisierte Prozesse zu analysieren, um zu sehen, wo Verbesserungspotenzial besteht, um sicherzustellen, dass Sie effizient arbeiten. Eine gute Aufzeichnung von Ausfällen ist unerlässlich, um Daten bereitzustellen, die Wartungsingenieure bei der Konstruktion zukünftiger Maschinen verwenden können, um den Zugriff und die Wartung dieser Maschinen noch einfacher zu machen.
Kontinuierliche Verbesserung kann auch dadurch erfolgen, dass Teamleiter und Wartungstechniker regelmäßig die Arbeit der Bediener überprüfen. Auf diese Weise können sie nicht nur Verbesserungspotenziale aufzeigen, sondern auch den Bedienern zu ihrer guten Arbeit gratulieren.
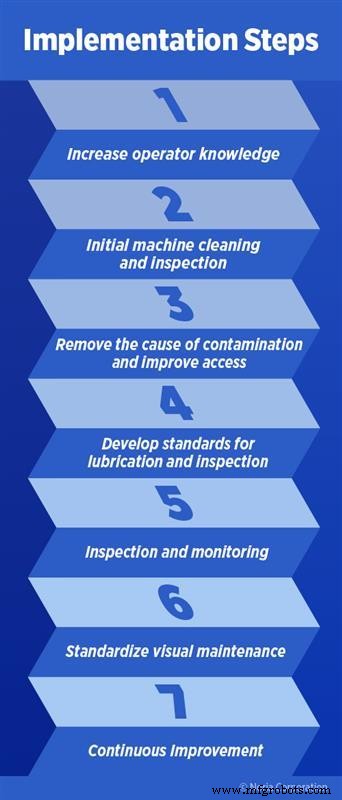
Aufrechterhaltung der autonomen Wartung
Sobald Ihre Bediener ordnungsgemäß in der autonomen Wartung geschult sind, die Verfahren standardisiert sind und ein Auditsystem eingerichtet ist, ist es an der Zeit, sich auf die Aufrechterhaltung dieses Prozesses zu konzentrieren. Es gibt ein paar einfache Tools, die Sie in Ihre tägliche Routine integrieren können, um den autonomen Wartungsprozess aufrechtzuerhalten.
Ein tägliches Stand-up-Meeting ist eine großartige Möglichkeit für Betreiber und ihre direkten Vorgesetzten, sich jeden Morgen zusammenzudrängen, um zu besprechen, wie die Dinge laufen. Diese Treffen funktionieren, indem sie im Kreis herumlaufen und es jeder Person ermöglichen, zu besprechen, was gut funktioniert, und alle Probleme zu erwähnen, auf die sie gestoßen ist. Weitere Tagesordnungspunkte sind die gewonnenen Erkenntnisse, der Personalstatus, Aktualisierungen des Managements sowie die Ziele und Maßnahmen des Tages. Tägliche Stand-up-Meetings können Probleme hervorheben, mit denen Betreiber zu kämpfen haben, oder Änderungen des oberen Managements einführen, die integriert werden müssen.
Einzelunterricht sind hervorragend geeignet, um Teammitglieder bei der Umsetzung von Änderungen zu unterstützen und ihnen dabei zu helfen, keinen Schritt zu übersehen, an den sie sich nur schwer erinnern können, oder um Probleme zu kommunizieren, die in der Vergangenheit aufgetreten sind, um zu verhindern, dass sie sich wiederholen. Ein-Punkt-Unterricht konzentriert sich im Allgemeinen auf Geräte-Subsysteme, Sicherheitspunkte und grundlegende Betriebsinformationen. Ein Beispiel für eine Ein-Punkt-Lektion wäre das Erstellen eines Klebeetiketts, das direkt auf einem Hebel oder einer Schutzvorrichtung angebracht wird, um einen Bediener daran zu erinnern, den Hebel oder eine Schutzvorrichtung wieder in die Sicherheitsposition zu drehen, bevor er zum nächster Vorgang.
Weitere Schritte zur Aufrechterhaltung der autonomen Wartung sind:
- Fehler- und Pannendaten verfolgen: Diese Daten sind unerlässlich, wenn Sie beginnen, Ihre autonomen Wartungsverfahren zu erstellen. Es zeigt Ihren Bedienern nicht nur an, welche Geräte die meiste Aufmerksamkeit erfordern, sondern ermöglicht Ihnen auch, Verbesserungen nachzuverfolgen, wenn Sie diese Daten im Laufe der Zeit verfolgen.
- Messwerte verwenden: Etablierte Metriken sind der Schlüssel zur Überwachung und Verfolgung der Gesamtanlageneffektivität in Bezug auf Reparaturen und Leistung. Das Analysieren von Mustern wie der mittleren Zeit zwischen Ausfällen und der mittleren Reparaturzeit hilft Ihnen, zukünftige Ausfälle vorherzusagen und sogar zu verhindern.
- Verschleiß der Dokumentkomponente: Verwenden Sie andere Mittel, um den Verschleiß der Komponenten zu verfolgen. Wartungstechnologien wie Ölanalyse, Schwingungsanalyse und Infrarotthermografie können Ihnen zusätzliche Einblicke in Geräteausfälle geben.
- Erstellung von Arbeitsaufträgen standardisieren: Die Verwendung von Arbeitsauftragssoftware hilft bei der Automatisierung und Verfolgung von Arbeitsauftragserstellungs- und Wartungsdaten. Software, die in ein computergestütztes Wartungsmanagementsystem (CMMS) integriert ist, ermöglicht es Ihnen, ein Wartungsprotokollblatt für jedes Gerät in Ihrer Anlage zu erstellen. Hier können Sie jeden Ausfall, jeden Austausch und wenn sich der Zustand der Komponenten ändert, protokollieren.
Vorteile der autonomen Wartung
Die meisten Unternehmen investieren viel in die Einstellung, Schulung und Entwicklung eines hochqualifizierten Wartungsteams, um festzustellen, warum kritische Anlagen ausfallen, und sie dann zu reparieren. Die autonome Wartung soll diese Techniker von der Durchführung geringqualifizierter Aufgaben wie Inspektionen, Schmierung und geringfügigen Anpassungen befreien. Unter anderem gibt es drei große Vorteile, die eine autonome Wartung einem Unternehmen bringt.
Der größte Vorteil sind niedrigere Arbeitskosten. Dies beinhaltet die Verringerung von Ineffizienzen in Bezug auf die Reisezeit und das Warten auf Verfügbarkeit. Dadurch, dass sich der Bediener jederzeit neben der Maschine befindet, werden diese Art von Problemen stark reduziert.
Ein weiterer Vorteil der autonomen Wartung besteht darin, die Verfügbarkeit von hochqualifiziertem Wartungspersonal zu erhöhen, damit es sich um kritischere Anforderungen kümmern kann. Der Einsatz einer autonomen Wartung ermöglicht es selbst den am engsten besetzten Wartungsabteilungen, sich um kritische Probleme zu kümmern, ohne auf Routinewartungen verzichten zu müssen.
Schließlich verbessert die autonome Wartung den Zusammenhalt im Team, indem sie die „Wir/Sie“-Mentalität beseitigt. Traditionell hat der Bediener eine "Ich benutze"-Mentalität, während der Wartungstechniker eine "Ich pflege und repariere"-Mentalität vertritt. Die autonome Wartung verschiebt dies in eine kohärentere „Wir behalten“-Haltung, die direkt in die Säulen der produktiven Gesamtwartung passt.
Gerätewartung und Reparatur
- Die digitale Fabrik:Was sie ist und warum sie wichtig ist
- Was ist Zuverlässigkeit?
- Was ist Anlagenwartung?
- Was ist Werkswartung?
- Was ist Notfallwartung?
- Was ist vorausschauende Wartung?
- Was ist vorbeugende Wartung?
- Was ist vorausschauende Wartung für Krane und warum ist sie wichtig?
- Was ist ein Instandhaltungsleiter und was macht er?
- Was ist nachhaltige Instandhaltung und warum ist sie wichtig?