Gängige Oberflächenbehandlungen für Spritzgusswerkzeuge und wie man die richtige auswählt
Der Spritzgussprozess ist recht komplex. Dabei arbeiten mehrere verschiedene Teile zusammen, um ein Kunststoffprodukt herzustellen. Ein herausragender Teil ist jedoch die Form selbst, in die der geschmolzene Kunststoff eingespritzt wird, um die feste und gewünschte Form des Kunststoffprodukts zu bilden. Das Werkzeug ist offensichtlich eines der wichtigsten Funktionsteile des Spritzgießens, aber auch eines der teuersten. Schäden an der Form stellen eine erhebliche finanzielle Verpflichtung dar. Glücklicherweise ist dies eine Verpflichtung, die Sie vermeiden können. Wie? Durch die richtige Schimmelbehandlung. Hier geben wir einen Überblick über einige Oberflächenbehandlungen von Spritzgusswerkzeugen.
Warum ist die Spritzgussbehandlung wichtig?
Die vielleicht einfachste Antwort auf diese Frage lautet – um Kosten zu sparen. Das macht Sinn, wenn man bedenkt, wie viel Formen kosten. Eine einzelne Form kann Hunderttausende von Dollar kosten, und das sind nur die Anschaffungskosten. Diese Kosten können und sollten vermieden werden, und die Oberflächenbehandlung von Spritzgusswerkzeugen ist eine Möglichkeit, dies zu erreichen.
Formen sind überhaupt nicht schwach, typischerweise aus gehärtetem Stahl. Der Prozess des Einspritzens geschmolzener Harze bei hohen Temperaturen und Drücken wird jedoch letztendlich seinen Tribut von den Spritzgussformen fordern. Viele der heute verwendeten thermoplastischen Materialien sind auch abrasiv und verursachen nach vielen Einspritzzyklen Abrieb und Reibung an den Formoberflächen. Außerdem besteht die Gefahr von Korrosion und Ermüdung nach fortgesetztem Gebrauch.
Während das Endergebnis in der Regel eine Beschädigung des Formwerkzeugs ist, ist die Arbeitsqualität von Formen, die durch Korrosion, Reibung, Verschleiß und Abrieb beeinträchtigt sind, in der Regel geringer als erforderlich. Der Formfluss kann auch ohne ordnungsgemäße Formbehandlung leiden. All dies kann Kunden vertreiben, und es ist normalerweise schwierig, sie zurückzugewinnen, selbst nach dem Austausch der Form. Dies unterstreicht noch einmal, warum Spritzgießer über die Formbehandlung und die verschiedenen Formenendbearbeitungswerkzeuge geschult werden müssen.
Arten der Oberflächenbehandlung für Kunststoffspritzgusswerkzeuge
Stahl ist hart, ja. Aber ist es schwer genug, Spritzgussformen vor Verschleiß zu schützen, nachdem sie längere Zeit geschmolzenem Harz bei hoher Temperatur und hohem Druck ausgesetzt waren? Nein, nicht ganz. Verschiedene Oberflächenbehandlungen können den dringend benötigten zusätzlichen Schutz bieten. Wir werden einige davon im Folgenden kurz untersuchen.
Plattierung
Das Plattieren ist eine der häufigsten Lösungen für Formverschleiß und -abrieb. Es gibt zwei Hauptformen des Plattierens – elektrolytisch und stromlos. Der Unterschied zwischen den beiden ergibt sich aus dem Vorhandensein von elektrischen Strömen oder nicht. Das elektrolytische Plattieren erfordert einen elektrischen Strom, während das stromlose Plattieren dies nicht tut.
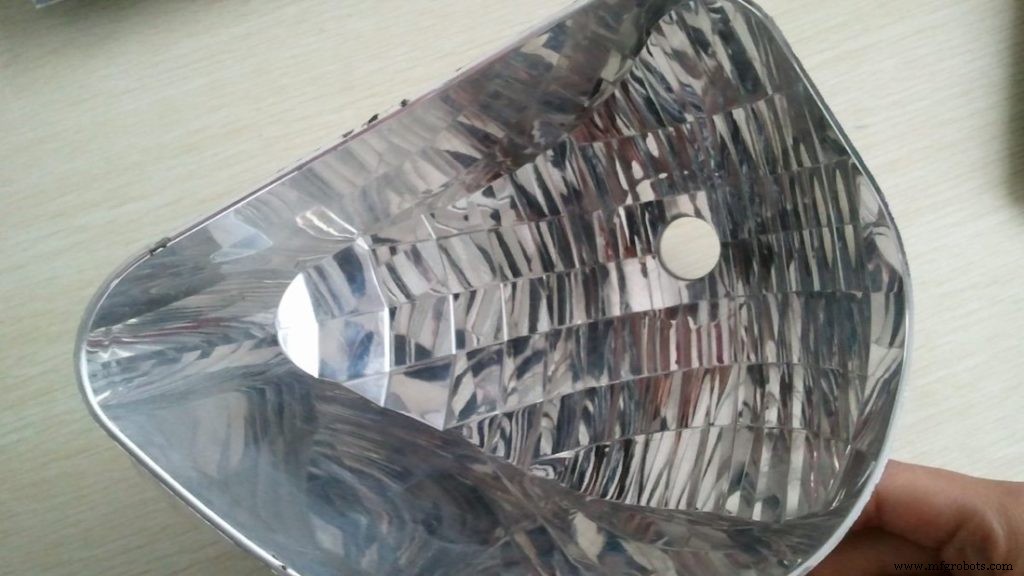
Verchromung und stromlose Vernickelung sind die beiden typischsten Arten der Beschichtung von Formen. Beim Verchromen wird eine dünne Chromschicht auf die Form galvanisiert. Das Produkt der Verchromung ist Chrom. Anders als beim Vernickeln erfordert das Verchromen die Verwendung einer konformen Anode, die in den Formhohlraum eingeführt wird. Dies bedeutet, dass das Verchromen mehr Zeit in Anspruch nimmt, insbesondere bei detaillierten Formen, und folglich mehr kosten kann. Ein weiterer Nachteil hier ist, dass eine zu lange Verchromung eine gleichmäßige Beschichtung verhindern kann, insbesondere bei detaillierten Formen. Die Oberflächenstruktur der Form ist mit Chrom härter, was sie widerstandsfähiger gegen Rost macht. Die Verchromung ist normalerweise glatt und sehr funktionell.
Die stromlose Vernickelung ist eine der vielseitigsten Oberflächenbehandlungen für Spritzgussformen. Das stromlose Plattieren beruht eher auf chemischen Reaktionen als auf elektrischem Strom. Es bietet Schutz vor Korrosion, Schmierproblemen, Abrieb und sogar chemischen Angriffen. Diese Form der Plattierung erfordert keine Anode, was eine gleichmäßigere Plattierung impliziert als eine Chromplattierung. Schwarzes Nickel ist eine der am besten erkennbaren stromlosen Vernickelungen.
Ob Chrom oder Nickel, eine Beschichtung garantiert Langlebigkeit. Die Formbehandlung mit Plattierung stellt sicher, dass die Formen mehr Spritzzyklen überstehen, ohne die Produktqualität zu beeinträchtigen.
Nitrieren
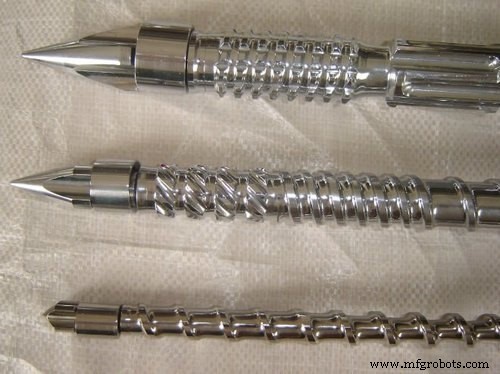
Nitrieren ist ein thermochemischer Diffusionsprozess. Neben dem Aufkohlen ist diese Formbehandlung die am weitesten verbreitete Wärmebehandlungspraxis. Dieser Prozess ermöglicht die Diffusion von Stickstoffatomen in die Formoberfläche bei niedrigen Temperaturen ohne Veränderung der Phasenstruktur der Formoberfläche. Keine Phasenänderung bedeutet minimale Verformung des Formstahls.
Es gibt verschiedene Formen des Nitrierens, einschließlich Ionennitrieren, Packungsnitrieren, Salzbadnitrieren und Gasnitrieren, alle mit dem gleichen Zweck, die Textur und Leistung der Formteiloberfläche zu verbessern.
Für diesen Prozess werden die Formteile aktivem Stickstoff zwischen 925 und 985 °F ausgesetzt. Die richtige Temperaturkontrolle ist für den Nitrierprozess entscheidend, um eine minimale Verformung des Stahls zu gewährleisten. Darüber hinaus werden die mittels Nitrieren behandelten Spritzgussformteile vor der endgültigen Bearbeitung typischerweise spannungsfrei geglüht, um vernachlässigbare Größenänderungen zu gewährleisten.
Im Laufe der Zeit wurde der Nitrierprozess von den traditionellen Gasnitriertechniken zu einem kontrollierteren Nitrieren unter Verwendung eines Computers zur Steuerung der Nitrierparameter weiterentwickelt und verbessert.
Das Nitrieren führt zur Entwicklung einer harten Gussform, aber Teile, die weich bleiben müssen, können beim Nitrieren maskiert werden. Das harte Formgehäuse macht es verschleiß- und abriebfest.
Aufkohlen
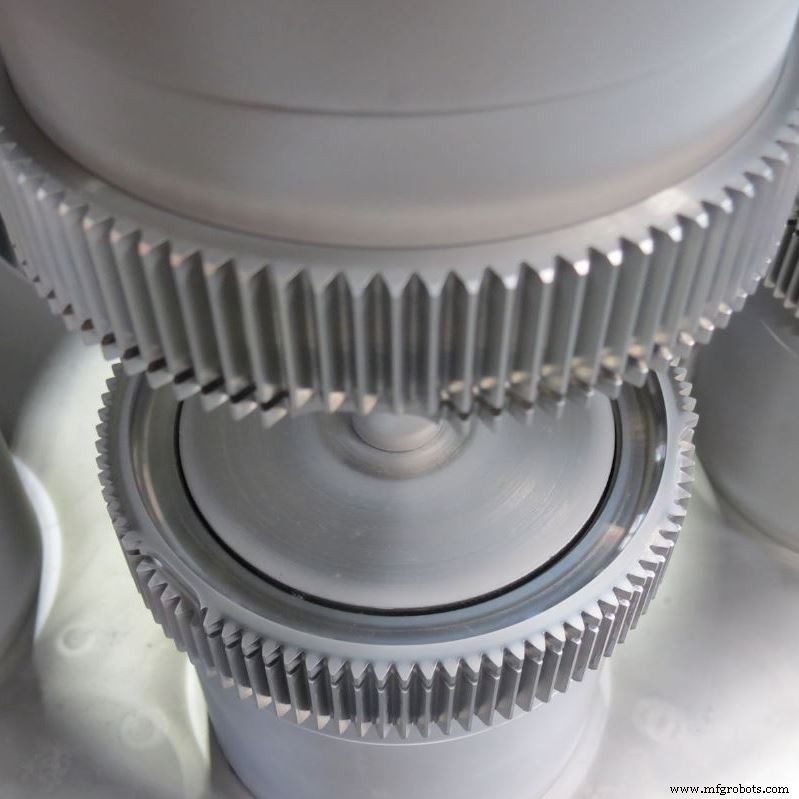
Eine weitere Formbehandlungspraxis, die Wärme erfordert, ist das Aufkohlen. Dieser Prozess ähnelt dem Nitrieren. Der Hauptunterschied besteht in der Diffusion von Kohlenstoffatomen in die Oberfläche der Spritzgusskomponenten während der Verarbeitung und nicht von Stickstoffatomen beim Nitrieren.
Aufkohlen führt oft zu verschleißfesten und zähen Formen. Bei diesem Verfahren werden die Spritzgussteile in einem Schachtofen erhitzt. Dann Einleiten der Aufkohlungsgase, um eine Diffusion in die Formoberfläche zu ermöglichen.
Wie beim Nitrieren gibt es verschiedene Formen von Aufkohlungsprozessen, einschließlich Gasaufkohlung, Vakuumaufkohlung, Aufkohlung mit gepulstem Plasma und Hochtemperaturaufkohlung.
Aufkohlen ist eine bessere Oberflächenbehandlung von Spritzgusswerkzeugen als Nitrieren für schwerere und stärker belastete Formkomponenten, wie große Zahnräder und Lager. Im Gegensatz zum Nitrieren erfordert das Aufkohlen eine Wärmenachbehandlung. Dies liegt an der deutlich höheren Temperatur, bei der die Aufkohlung auftritt.
PVD-Beschichtung
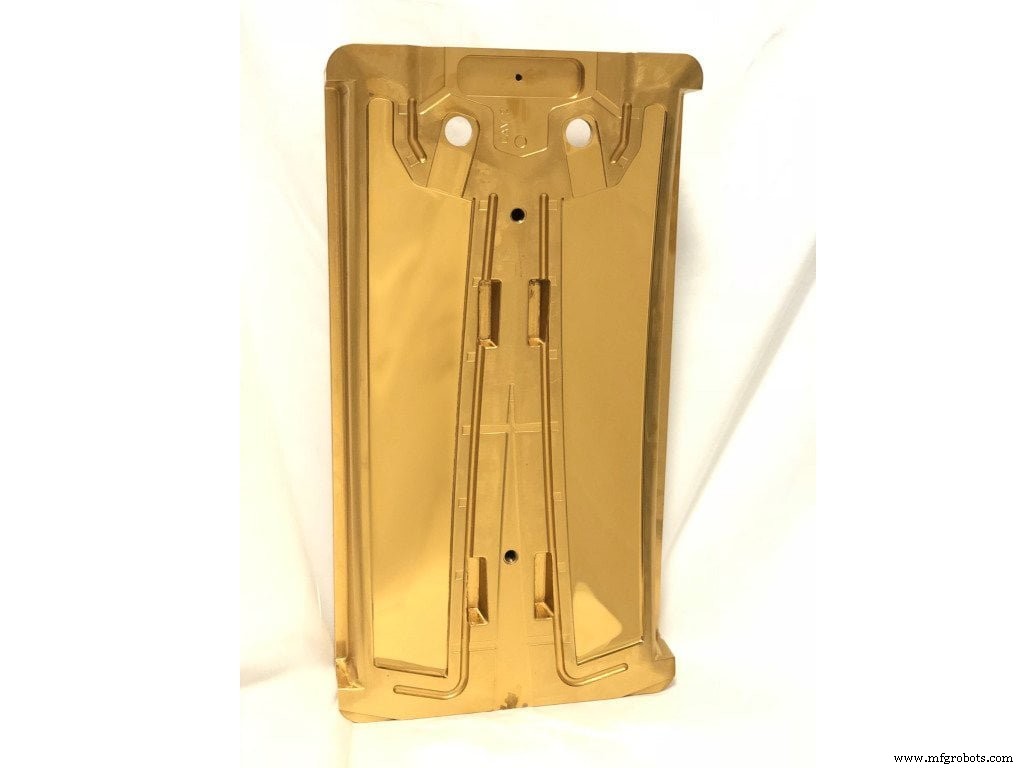
PVD ist ein Akronym für Physical Vapour Deposition. Auch als Dünnschichtbeschichtung bekannt, ist diese Art der Formbehandlung ein Prozess, bei dem ein festes Material, bekannt als Quelle, im Vakuum verdampft und auf der Oberfläche einer Formkomponente abgeschieden wird. Die Quelle ist typischerweise ein Keramik- oder Metallstab.
Die gängigsten PVD-Beschichtungsverfahren sind Aufdampfen und Sputtern. Beim Verdampfen verwendet das Verfahren eine kathodische Lichtbogen- oder Elektronenstrahlquelle. Auf der anderen Seite beinhaltet das Sputtern die Verwendung von magnetisch verstärkten Quellen.
Das Prinzip hinter diesem Verfahren ist die Bildung von Formoberflächen mit hoher Dichte durch den Beschuss des Formbestandteils mit energiereichen, positiv geladenen Ionen. Das Ausgangsmaterial wird in ein Plasma gesputtert, wodurch starke Bindungen mit der Formoberfläche gebildet werden und eine dünne Klebeschicht entsteht.
Es ist auch möglich, zusammengesetzte Beschichtungszusammensetzungen herzustellen, indem während des Beschusses reaktive Gase wie Sauerstoff und Stickstoff in die Vakuumkammer eingeführt werden.
Die PVD-Beschichtung trägt dazu bei, die Festigkeit der Form zu verbessern. Da die entstehenden Schichten zudem sehr dünn sind, hat die Beschichtung wenig Einfluss auf die Endabmessungen der Formteile. Die Oberflächenbehandlung von PVD-Spritzgusswerkzeugen ist heute eine der akzeptabelsten in der Industrie; Seine Verwendung gilt jedoch nur für Materialien, die den sehr hohen Temperaturen standhalten, die dieser Prozess mit sich bringt. Dieser Prozess ist auch nicht ideal für sehr detaillierte Formen mit vielen versteckten Teilen.
Die PVD-Beschichtung kann funktional oder dekorativ sein, je nachdem, ob der Schwerpunkt auf der Verbesserung der Gesamtleistung bzw. der Verbesserung der Ästhetik liegt. Titannitrid (TiN) ist ein Beispiel für eine funktionelle PVD-Beschichtung, während ein Zr-basierter Film ein Beispiel für eine dekorative PVD-Beschichtung ist.
CVD-Beschichtung
CVD ist ein Akronym für Chemical Vapour Deposition. Das Prinzip hinter dieser Beschichtung ähnelt dem von PVD, mit dem Hauptunterschied, dass eine chemische Reaktion verwendet wird, um den dünnen Film zu erzeugen, der die Form bei der CVD-Beschichtung überzieht.
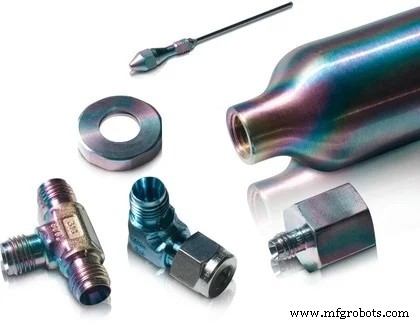
Der CVD-Beschichtungsprozess wird üblicherweise in einem CVD-Reaktor durchgeführt. Eines der Probleme bei der PVD-Beschichtung ist die hohe Temperatur, bei der sie durchgeführt wird; Nun, die CVD-Beschichtung wird bei noch höheren Temperaturen (um 1925F) durchgeführt. Wie Sie sich vorstellen können, beschränkt dies diese Formbehandlung auf Komponenten, die erhöhten Temperaturen standhalten können.
Der bei diesem Beschichtungsprozess gebildete dünne Film entsteht durch Reaktionen zwischen Gasphasen und der heißen Formoberfläche in den Reaktoren.
Wie PVD sorgt die CVD-Beschichtung für eine zähe Form, verschleiß- und abriebfest. Der gebildete Film ist außerdem sehr dünn, normalerweise im Nanometerbereich, wodurch sichergestellt wird, dass die Endabmessungen der Form nicht wesentlich verändert werden.
Die CVD-Beschichtung ist für eine Vielzahl von Formkomponenten nützlich, insbesondere für solche, die viel Gleiten erfordern. Aufgrund der gasabhängigen Natur dieses Prozesses kann es jedoch schwierig oder sogar unmöglich sein, einige Bereiche zu maskieren.
Bemerkenswert ist, dass viele dieser Prozesse beim Rapid Tooling gebührend berücksichtigt werden. Und die besten Rapid-Tooling-Services finden Sie bei RapidDirect.
Überlegungen zur Schimmelbehandlung
Es sind mehrere Faktoren zu berücksichtigen, bevor die verschiedenen Formbearbeitungswerkzeuge eingesetzt werden. Hier sind einige davon.
- Die Art der Formkomponente oder des Teils, das dem Formbehandlungsprozess unterzogen wird, muss sorgfältig untersucht werden. Wählen Sie nicht irgendein Formbearbeitungswerkzeug. Berücksichtigen Sie stattdessen die Wärmetoleranz der Formkomponente, da unterschiedliche Prozesse unterschiedliche Wärmeeinwirkungen auf die Formoberfläche haben. Auch der Spielraum, den Sie sich bei endgültigen Dimensionsänderungen leisten können, sollte ins Spiel kommen. Einige Formkomponenten benötigen extrem dünne Filme, während andere relativ dicke Beschichtungen aufnehmen können.
- Der Preis der Schimmelpilzbehandlung ist ein weiterer wesentlicher Faktor, den es zu berücksichtigen gilt. Die besten Verfahren kosten in der Regel mehr, aber manchmal ist es wirtschaftlicher, zu günstigeren Optionen zu greifen, insbesondere wenn das Spritzgießwerkzeug nur sporadisch verwendet wird.
- Sie sollten auch die Kompatibilität des Prozesses mit Ihrem Werkzeug sicherstellen. Beispielsweise ermöglichen einige Prozesse eine Maskierung; andere nicht. Wenn also das Maskieren einiger Formkomponenten für Ihre Formbehandlung unerlässlich ist, sollten Sie Prozesse auswählen, die das Maskieren ermöglichen. Das gleiche Prinzip gilt für die Gleichmäßigkeit der Beschichtung.
RapidDirect-Spritzgussservices
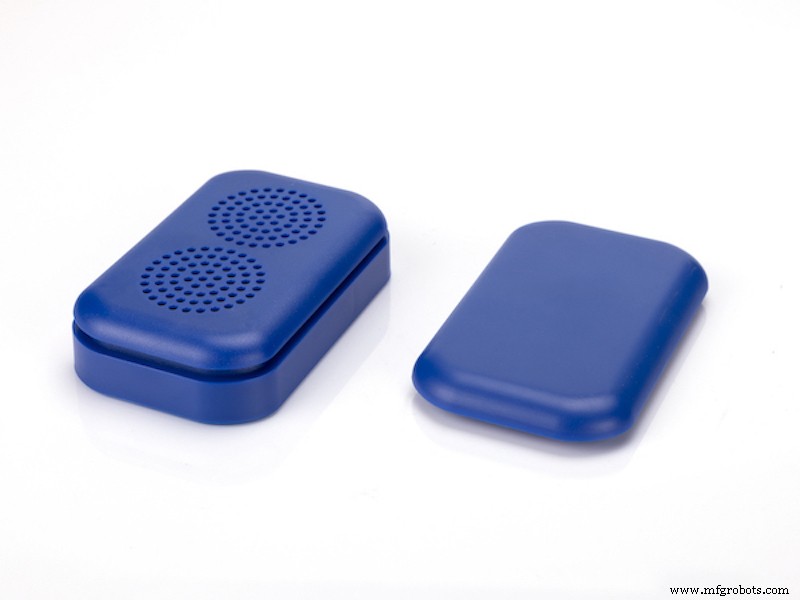
Bei RapidDirect haben wir jede Menge Erfahrung mit dem Design von Spritzgussformen und der Formbehandlung auf unserer Seite. Unser Expertenteam steht Ihnen zur Verfügung und hilft Ihnen bei all Ihren Spritzgussproblemen. Es gibt mehr. Wir bieten Formgebungsservices von höchster Qualität, um sicherzustellen, dass Sie sich keine Gedanken über die richtige Oberflächenbehandlung machen müssen, und maximieren dennoch das Potenzial und die Lebensdauer Ihrer Formkomponenten.
Verbundwerkstoff
- So wählen Sie die richtigen Nivellierfüße aus
- So wählen Sie die richtigen Schubladenführungen aus
- 3 Arten von Passformen und wie wählt man die richtige aus?
- Die Bedeutung der Spritzgusstechnik
- Was ist ein Verdichter und wie wähle ich den richtigen aus?
- Kran kaufen:So wählen Sie den richtigen aus
- So wählen Sie das richtige CNC-Drehzentrum aus, um Aufträge schnell und präzise abzuschließen
- Wie wählt man den richtigen Fräser und die richtige Programmierung für CNC aus?
- Häufige Begriffe des Spritzgießens erklärt:Mehrkavität, Familie, Einsätze und mehr
- Wie arbeiten CNC-Werkstätten und wie wählen Sie die richtige aus?