Herstellung von Dotterschalen-Cu@C-Nanokompositen als Hochleistungskatalysatoren für die oxidative Carbonylierung von Methanol zu Dimethylcarbonat
Zusammenfassung
Es wurde ein einfacher Weg entwickelt, um Dotter-Schale-Verbundstoffe mit abstimmbaren Cu-Kernen herzustellen, die in hohlen Kohlenstoffkugeln (Cu@C) mit einem durchschnittlichen Durchmesser von etwa 210 nm und einer Hohlraumgröße von etwa 80 nm eingekapselt sind. Während der Pyrolyse sorgt der begrenzte Nanoraum des Hohlraums dafür, dass der Nukleations- und Wachstumsprozess von Cu-Nanokristallen ausschließlich innerhalb der Hohlräume stattfindet. Die Größe von Cu-Kernen kann durch Variation der Kupfersalzkonzentration leicht von 30 bis 55 nm eingestellt werden. Durch die bewusste Erzeugung von Schalenporosität durch chemische KOH-Aktivierung wird bei einem optimierten KOH/HCS-Massenverhältnis von 1/4 die katalytische Leistung für die oxidative Carbonylierung von Methanol zu Dimethylcarbonat (DMC) der aktivierten Probe mit TOF bis zu 8,6 . deutlich verbessert h −1 bei einer Methanolumwandlung von 17,1 %. Der aktivierte Dotterschalen-Katalysator zeigt vielversprechende katalytische Eigenschaften, einschließlich der Wiederverwendbarkeit mit leichtem Verlust an katalytischer Aktivität und vernachlässigbarem Auswaschen aktivierter Komponenten selbst nach sieben Recyclingvorgängen, was der Umsetzung einer sauberen Produktion für die umweltfreundliche Chemikalie DMC durchweg zuträglich ist.
Hintergrund
Dimethylcarbonat (DMC) hat aufgrund seiner hervorragenden biologischen Abbaubarkeit (z. B. geringe Bioakkumulation und Persistenz) und seiner geringen Toxizität als weit verbreiteter Baustein große Aufmerksamkeit auf sich gezogen [1]. Die potentiellen industriellen Anwendungen von DMC umfassen viele Bereiche, wie ungiftige Lösungsmittel, alternativer Ersatz für Phosgen, Kraftstoffadditiv und Zwischenprodukt für die Synthese von Polycarbonaten und Isocyanaten [2,3,4,5]. Im Hinblick auf verschiedene Synthesemethoden von DMC, die oxidative Carbonylierung von Methanol (MeOH) mit CO, O2 , und MeOH als Rohstoffe stellt aufgrund der hohen Nutzungsrate der Kohlenstoffquelle und der Vorteile für die Umwelt eines der vorgeschlagenen günstigen Verfahren dar. Die bei dieser Reaktion verwendeten Katalysatoren können hauptsächlich in zwei Typen eingeteilt werden:chlorhaltige Katalysatoren und chlorfreie. Da es einige Probleme gibt, wie z. B. schwere Korrosionsprobleme, eine Verschlechterung der Produktqualität und eine Katalysatordesaktivierung, die auf den Chlorverlust der chlorhaltigen Katalysatoren zurückzuführen sind, wurden chlorfreie Katalysatoren ausführlich untersucht [6, 7]. Aktivkohle (AC) getragenes Kupfer oder Kupferoxid hat sich als vielversprechende katalytische Aktivität für die DMC-Synthese erwiesen [8,9,10] und Forscher haben vorgeschlagen, dass Cu das aktive Zentrum für diese Reaktion ist [10,11,12,13]. Die Deaktivierung von Kupferkatalysatoren auf Trägern wird jedoch im Allgemeinen der Agglomeration von Kupferpartikeln, dem Verlust aktiver Spezies und der Änderung des chemischen Zustands von Kupfer zugeschrieben, wobei ersteres schwerwiegender ist. Um solche Nachteile zu überwinden, ist das Design und die Herstellung von Nanopartikeln, die in eine Schutzhülle eingekapselt sind, aus technologischer Sicht vorteilhaft, um die katalytische Aktivität und Stabilität reaktiver Zentren bei der oxidativen Carbonylierung von Methanol zu DMC zu verstärken.
Auf dieser Linie sind Dotter-Shell-Nanostrukturen (YSNs) oder Rassel-artige Nanokomposite, bei denen Kern-Nanopartikel (NPs) von einer äußeren Schicht mit einem Zwischenraum zwischen ihnen eingeschlossen sind, aufgrund ihrer einzigartigen hierarchischen/mehrstufigen Nanostrukturen besonders beliebt. , und damit einhergehende optische und elektrische Eigenschaften und ein großes Potenzial in der katalytischen Anwendung [14]. Die Schutzhülle in YSNs kann das Kernelement auch unter rauen Bedingungen effektiv stabil halten und seine aktive Oberfläche ausreichend freilegen [15]. Es wird erwartet, dass der geschlossene Leerraum für die chemische Lagerung, Kompartimentierung und Eingrenzung von Wirt-Gast-Wechselwirkungen nützlich ist und, was noch wichtiger ist, eine einzigartige Umgebung für die Erzeugung konzertierter Aktionen zwischen dem Kern und einer durchlässigen Hülle bietet [16]. Diese bemerkenswerten Textureigenschaften ermöglichen es YSNs, als vielversprechende Kandidaten zu fungieren, um Anforderungen wie Sinterstabilität und Wiederverwendbarkeit für Anwendungen in der Katalyse zu erfüllen. Unter diesen haben Dotter-Kohlenstoff-Schalen-Nanostrukturen aufgrund der inhärenten Leitfähigkeit sowie der ausgezeichneten chemischen und thermischen Stabilität der Kohlenstoffbeschichtung sofort großes Interesse auf sich gezogen [17,18,19,20,21].
Kürzlich haben Lu und Mitarbeiter über die Herstellung von Hohlkugeln durch schwache Säure-Base-Wechselwirkungen unter Verwendung von Ölsäure, einem weichen Templat, und funktioneller Dihydroxybenzoesäure (DA) als Vorstufe berichtet [22]. Hier erweitern wir ihre Arbeit, um eine Anlage zu den YSNs mit einstellbarer Cu-Kerngröße zu entwickeln, die in hohlen Kohlenstoffkugeln (HCSs) (Cu@C) eingekapselt ist, indem wir eine Ship-in-Bottle-Strategie anwenden. Die Schalenporosität von heterogenen Cu@C-Katalysatoren kann durch KOH-Aktivierung eingestellt werden, und ihre Auswirkungen auf die katalytische Leistung und Stabilität in der DMC-Synthese werden ebenfalls untersucht.
Methoden
Chemikalien
2,4-Dihydroxybenzoesäure (DA) wurde von J&K Scientific Ltd. bezogen. Ölsäure, Ammoniaklösung (25%), Formaldehyd, Kupfernitrat (Cu(NO3 )2 ·3H2 O), Kaliumhydroxid (KOH) und Methanol (MeOH) wurden von Sinopharm Chemical Reagent Co. Ltd. bezogen. Alle Chemikalien waren von analytischer Qualität und wurden ohne weitere Reinigung verwendet. Entionisiertes Wasser, das vom Milli-Q-System (Millipore, Bedford, MA) erhalten wurde, wurde in allen Experimenten verwendet. O2 (>99,99%) und CO (>99,99%) wurden von der Beijing ZG Special Gases Science &Technology Co. Ltd. geliefert.
Synthese hohler Kohlenstoffkugeln (HCS)
Die hohlen Polymerkugeln (HPSs) mit einem hohlen Kern und einer Polymerhülle wurden zunächst unter Verwendung von Ölsäure als weiches Templat und Phenolharz als Kohlenstoffvorläufer nach dem von Lu et al. beschriebenen Verfahren hergestellt. [22]. In einem typischen Verfahren wurden 2,5 mmol 2,4-Dihydroxybenzoesäure und 7,5 mmol Formaldehyd in 95 ml entionisiertem Wasser gelöst. Ein 5-ml-Volumen einer wässrigen Lösung, die 56 μl Ölsäure und 180 μl Ammoniaklösung (25%) enthielt, wurde bei 30 °C unter langsamem Rühren für 30 Minuten zu der oben hergestellten Lösung gegeben. Als nächstes wurde die Mischung in einen Autoklaven überführt, der 4 h bei 140 °C hydrothermal gealtert wurde. Nach dem Zentrifugieren, Waschen mit entionisiertem Wasser und Ethanol, Trocknen bei 50 °C über Nacht und anschließender Pyrolyse bei 700 °C für 2 h unter Stickstoffstrom wurde das HCS erhalten.
Synthese von Cu@C-Nanokompositmaterialien
Typischerweise wurden 0,3 g der hergestellten HCSs zuerst in 30 ml Kupfernitratlösung mit einem unterschiedlichen Konzentrationsbereich von 0,03 bis 0,24 M dispergiert. Dann wurde die Mischung in einen Autoklaven überführt, um eine hydrothermale Imprägnierung bei 100 °C für 10 . zu durchlaufen h. Die resultierende imprägnierte Probe, bezeichnet als HCS-Cu 2+ , wurde mit derselben Methode wie HPS abgerufen. Nach der Kalzinierung bei 400 °C für 2 h unter H2 /N2 (10%/90%), schließlich wurden die Dotterschalen-Cu@C-X (X = 0.03, 0.06, 0.12, 0.24) Nanokomposite erhalten.
Synthese des Cu@A-HCS-Katalysators mit KOH-aktivierter Kohlenstoffkugel als Unterstützung
Die Behandlung von HCS mit KOH wird mit der Absicht versucht, die Eigenschaften des Kohlenstoffträgers zu modifizieren und die Leistung des Cu-Katalysators weiter zu beeinflussen. Typischerweise wurden 0,3 g HCSs physikalisch in Abwesenheit von Wasser mit 0,15 g KOH gemischt. Nach der Vorbehandlung wurde die Probe in einem Stickstoffstrom von 80 ml/min mit einer Anstiegsrate von 10 °C/min auf 700°C für 2 h erhitzt und dann auf Raumtemperatur abgekühlt. Die mit KOH nachbehandelten Kohlen wurden wiederholt mit verdünnter HCl und anschließend mit destilliertem Wasser gewaschen, bis kein Chlorion mehr nachgewiesen wurde (AgNO3 Prüfung). Nach dem Trocknen bei 60 °C über Nacht wurde 0,12 M Kupfernitratlösung während der hydrothermalen Imprägnierung verwendet und die anderen Verfahren waren identisch mit denen von Cu@C-0,12, was schließlich die modifizierten Proben ergab, die als Cu@A-HCS bezeichnet wurden.
Die katalytische Leistung von Cu@C-X (X = 0,03, 0,06, 0,12, 0,24) und Cu@A-HCS
Die oxidative Carbonylierung von Methanol wurde in einem 25-ml-Edelstahlautoklaven durchgeführt, der mit Teflon ausgekleidet und mit einem Magnetrührer ausgestattet war. In einem typischen Experiment wurden 0,2 g Katalysator und 10 ml Methanol in den Autoklaven gefüllt, der dann fest verschlossen, dreimal mit CO gespült und als nächstes mit CO und O2 . auf 3,0 MPa unter Druck gesetzt wurde (PCO :PO2 = 2:1) bei Raumtemperatur. Die Reaktion lief bei 120 °C unter kontinuierlichem Rühren bei 750 U/min für 1,5 h ab. Nach der Reaktion wurde der Reaktor auf Raumtemperatur abgekühlt und entspannt. Die Katalysatoren wurden durch Filtration abgetrennt. Die Produktkonzentrationen im Filtrat wurden durch Gaschromatographie (GC) unter Verwendung eines FID-Detektors bestimmt. Die Recyclingfähigkeit des gebrauchten Katalysators wurde untersucht, indem eine Reihe aufeinanderfolgender Durchläufe durchgeführt wurden.
Die Hauptreaktion der oxidativen Carbonylierung von Methanol zu Dimethylcarbonat wurde wie folgt gezeigt:
2CH3 OH + 1/2 CO + O2 =(CH3 O)2 CO + H2 O.
Die Konzentration von Kupfer, MeOH-Umwandlung (CMeOH ), DMC-Selektivität (SDMC ) und die Umsatzfrequenz (TOF) wurden mit den folgenden Gleichungen berechnet:
Die Konzentration von Kupfer (CCu , mmol/g) = Cu-Gehalt (Gew.-%)/63,55 × 1000.
MeOH-Umwandlung (CMeOH , %) =umgesetztes Methanol/eingeführtes Methanol × 100 %.
DMC-Selektivität (SDMC , %) = 2 produziertes DMC/umgesetztes Methanol × 100 %.
Umsatzfrequenz = produziertes DMC/(die molare Menge an Kupfer × Reaktionszeit).
Charakterisierung
Röntgenbeugungsmuster (XRD) wurden auf einem Rigaku D-Max 2500 Diffraktometer unter Verwendung von Cu K . aufgenommen α-Strahlung (λ = 0,154 nm) bei 40 kV und 100 mA, mit einer Abtastrate von 4° min −1 um 2θ von 5°–85°. Die Analyse mit Transmissionselektronenmikroskopie (TEM) wurde auf einem Feldemissions-Transmissionselektronenmikroskop JEM 2100F (JEOL, Tokio, Japan), das bei 200 KeV betrieben wurde, durchgeführt. TEM-Proben wurden hergestellt, indem C-beschichtete Cu-Gitter in Ethanollösungen von Proben eingetaucht und bei Raumtemperatur getrocknet wurden. Die thermogravimetrische (TG) Analyse wurde auf einem thermogravimetrischen Analysator, STA 449 F3 Jupiter (NETZSCH), mit einem N2 . durchgeführt oder Luftstrom von 50 ml/min. Oberflächen und Porenvolumina wurden aus Stickstoffadsorptionsisothermen bei 77 K mit dem Oberflächenanalysator 3H-2000PS2 (Beishide) bestimmt. Die spezifischen Oberflächen nach Brunauer-Emmett-Teller (BET) wurden unter Verwendung von Adsorptionsdaten bei einem relativen Druckbereich von P . berechnet /P 0 = 0,04–0,3. Mesoporen-Porengrößenverteilungskurven wurden nach der BJH-Methode (Barrett-Joyner-Halenda) aus dem Adsorptionszweig berechnet. Die Gesamtporenvolumina wurden aus der bei einem relativen Druck (P /P 0 ) von 0,99. Der Kupfergehalt wird bestimmt durch Auflösen des Katalysators in einer starken Säuremischung, gefolgt von einer Analyse der Atomadsorptionsspektrometrie (AAS) unter Verwendung der SpectrAA-220 AAS-Ausrüstung. Die Analyse des Reaktionsprodukts erfolgte durch Gaschromatographie (GC; Agilent 6890) unter Verwendung eines FID-Detektors.
Ergebnisse und Diskussion
Texturparameter und thermische Stabilität des vorbereiteten Trägers
Die BET-Oberfläche und das Porenvolumen der Proben, die in den verschiedenen Vorbereitungsstufen beteiligt waren, sind in Tabelle 1 zusammengefasst. Wie in Abb. 1a und Tabelle 1 zu sehen ist, hat das erhaltene HPS niedrige BET-Oberflächen (~23 m 2 g −1 ). Daher ist es kaum möglich, die Einführung der Katalysatorvorläufer durch herkömmliche Imprägnierverfahren zu verfolgen. Daher verwenden wir ein hydrothermales Imprägnierungsverfahren, um die Diffusionsfähigkeit zu verbessern, damit Kupfervorläufer erfolgreich in die Kavität von HPS gezogen werden können. Die BET-Oberfläche von HPS und HPS-Cu änderte sich von 23 auf 15 m 2 g −1 die Aussage bescheinigt. Darüber hinaus bestätigen TEM-Bilder in Abb. 2 die ausschließlich innerhalb der Kohlenstoffhülle gebildeten Cu-Nanopartikel.
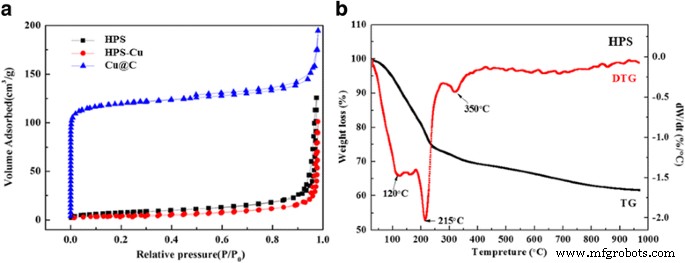
a N2 Adsorptions-Desorptions-Isotherme der nach jedem Schritt erhaltenen Produkte:HPS, HPS-Cu 2+ , und Cu@C. b TG-DTG-Profile von HPS
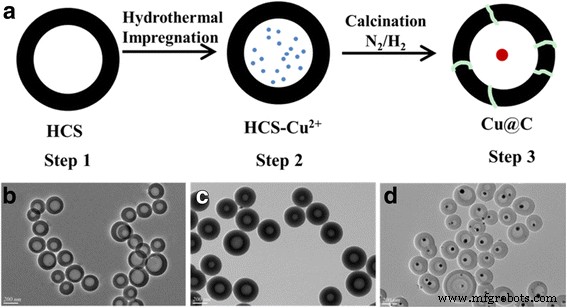
a Schematische Darstellung für die Synthese von Cu@C-Nanokompositen unter hydrothermalen Imprägnierbedingungen. TEM-Bilder der Produkte, die nach jedem Schritt erhalten wurden:b HCS, c HCS-Cu 2+ , und d Cu@C
Der Karbonisierungsprozess des HPS wird von TG untersucht. Abbildung 1b zeigt das Ergebnis von TG-DTG in N2 . Während dieses gesamten Intervalls tritt der Hauptverlust von HPS bei 215 °C auf und ist bei etwa 350 °C vollständig. Dies kann auf die Zersetzung der in HPS eingebetteten Ölsäure und die Karbonisierung des Polymergerüsts zurückgeführt werden [22]. Daher wurde im Vergleich mit TG-Kurven von Cu@C-Katalysatoren (siehe in Abb. 5b) 400 °C als optimale Herstellungstemperatur bestimmt, um die vollständige Karbonisierung von HPS sicherzustellen und die Aggregation der Cu-Nanopartikel zu verhindern.
Struktureigenschaften von Cu@C-Nanokompositen
Am Beispiel eines [email protected] Dotterschalen-Nanokomposits ist das Syntheseverfahren zur Herstellung von Dotterschalenstrukturen mit Cu-NPs umhüllt von einer Kohlenstoffhülle nach einer Ship-in-a-Bottle-Strategie in Abb. 2a dargestellt. Abbildung 2b, c zeigt typische TEM-Bilder des resultierenden Produkts, das in jedem Schritt erhalten wurde. Wie zu sehen ist, wurden HCSs mit einer einheitlichen Größe von etwa 210 nm erfolgreich synthetisiert (Abb. 2b). Während der hydrothermalen Imprägnierung kann kein offensichtlicher Unterschied zwischen HCSs und HCS-Cu 2+ . beobachtet werden (Abb. 2c). Nach der Kalzinierung bleibt die hohle Morphologie jedoch erhalten, aber Cu-NPs können aufgrund der Zersetzung von Kupfersalzen beobachtet werden. Schließlich wird das Dotterschalen-strukturierte Cu@C (Abb. 2d) mit einem Durchmesser von ~200 nm und einer Hohlraumgröße von ~80 nm erreicht. Hochauflösende Transmissionselektronenmikroskopie (HRTEM) (Abb. 3b) zeigt, dass die Kernpartikel einen Raum von 0,18 nm aufweisen, der zur Cu-Ebene (2 0 0) indiziert ist. Dies stimmt mit den Ergebnissen von XRD (Abb. 3c) überein, wo Beugungspeaks bei 2θ = 43,3°, 50,4° und 74,1° wurden beobachtbar, weil Cu 2+ Spezies auf der Vorstufe (HCS-Cu 2+ ) werden unter einer reduzierenden Atmosphäre zu metallischem Cu reduziert, entsprechend den spezifischen (1 1 1), (2 0 0) bzw. (2 2 0) Kristallebenen von Cu, basierend auf der JCPDS-Karte 04-0836 . Die N2 -Adsorptions-Desorptions-Isotherme des resultierenden Cu@C-0,12 stellt eine Typ-I-Isotherme dar, was zeigt, dass die Kohlenstoffhüllen von Cu@C-0,12 reichlich Mikroporen aufweisen (Abb. 3d). Diese Probe hat eine BET-Oberfläche von 365 m 2 /g begleitet von einem Porenvolumen von 0,23 cm 3 /g. Eine geringe spezifische Oberfläche zusammen mit einer engen Mikroporosität werden gewöhnlich als Hauptnachteile genannt, die ihre Anwendungen einschränken, die weiter unten diskutiert werden. Detaillierte Texturparameter der Proben sind in Tabelle 2 zusammengefasst.
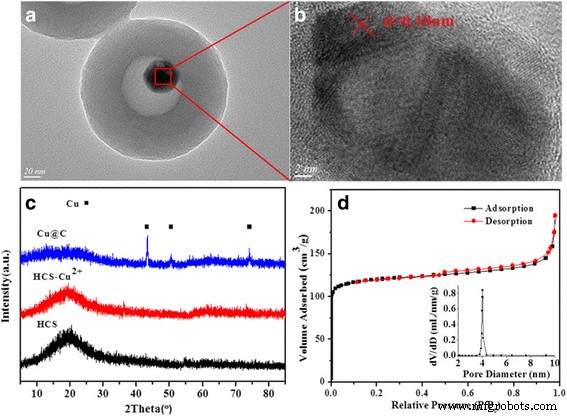
a , b TEM-Aufnahmen des Kupferkerns in [email protected]. c XRD-Muster der nach jedem Schritt erhaltenen Produkte:HCS, HCS-Cu 2+ und Cu@C-0,12. d N2 Adsorptions-Desorptions-Isotherme und Porengrößenverteilung von Cu@C-0,12
Der mechanistische Weg zur Bildung einzelner Cu-NPs innerhalb der Kohlenstoffhülle kann durch den begrenzten Keimbildungs- und Wachstumsprozess erklärt werden. Im Verlauf der Pyrolyse bildeten sich viele anfänglich winzige CuO-Keime und verteilten sich aufgrund der Zersetzung des eingebauten Cu(NO3 )2 Moleküle. Wenn das Reduktionsmittel H2 diffundiert in den Hohlraum, werden die gebildeten CuO-Keime weiter zu metallischen Cu-Kernen reduziert, die dazu neigen, zu wandern und zu größeren Partikeln zu aggregieren. Sobald sich die größeren gebildet haben, werden die verbleibenden Cu-Keime innerhalb des Hohlraums sukzessive auf der Oberfläche der vorgeformten Partikel absorbiert, was zum Wachstum von Cu-Nanokristallen führt. Ein ähnlicher Mechanismus wurde auch an anderer Stelle vorgeschlagen [23]. Basierend auf dem Keimbildungs- und Wachstumsprozess konnte gefolgert werden, dass die Größe des resultierenden Cu-Kerns durch Einstellen der Menge an Kupfersalzvorstufe, die in der begrenzten Kavität untergebracht ist, gesteuert werden kann.
Größenkontrolle des Cu-Kerns
Durch Variation von Cu(NO3 )2 Konzentrationen von 0,03 bis 0,24 M wurde eine Reihe von Dotterschalen-Nanokompositen, bezeichnet als Cu@C-X (X = 0,03, 0,06, 0,12, 0,24), erhalten. Die Morphologie und Größe der Produkte wurden durch TEM untersucht. Wie in Abb. 4a–d zu sehen ist, bestehen fast alle hohlen Nanokugeln im Inneren aus einem einzigen Partikel. Die Cu-Kerngröße der resultierenden Nanokugeln steigt jedoch von 30 ± 1,3 auf 55 ± 2,5 nm (Abb. 4e–h) mit zunehmendem Cu(NO3 )2 Konzentrationen, ermittelt aus TEM-Bildern unter Berücksichtigung von mindestens 150 Partikeln. Bemerkenswert ist, dass ein Bruchteil von hohlen Kohlenstoffkugeln (HCSs) mit YSNs für das niedrige Cu(NO3 )2 Konzentration (Abb. 4a). Außerdem sind einige kleine Cu-NPs auf der äußeren Oberfläche der Kohlenstoffhülle dekoriert (Abb. 4d), die durch die Zersetzung und Aggregation des restlichen Cu(NO3 )2 außerhalb der Schale.
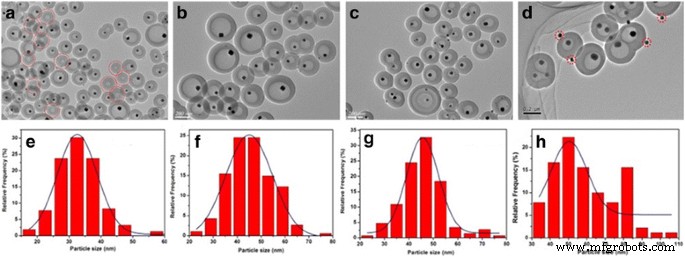
TEM-Bilder und entsprechende Größenverteilungshistogramme von Cu-NPs in Proben:a , e Cu@C-0,03, b , f [email protected], c , g Cu@C-0,12 und d , h Cu@C-0,24
Abbildung 5a zeigt die XRD-Muster von Cu@C-X wie hergestellt (X = 0.03, 0.06, 0.12, 0.24). Alle Proben zeigen drei typische Reflexionspeaks, die auf Cu-Kristalle indiziert sind (JCPDS Card No. 04-0836). Mit zunehmender Kupfersalzkonzentration sind die Beugungspeaks viel stärker und schärfer, während die Cu-NP-Größe von 26,6 auf 52,2 nm ansteigt, indem die Scherrer-Gleichung verwendet wird, die auf dem stärksten Peak der Muster basiert, was gut mit den TEM-Ergebnissen übereinstimmt . Darüber hinaus wurde eine TG-Analyse durchgeführt, um den Cu-Gehalt der Nanokugeln in Fig. 5b zu bestimmen. Unter der Annahme, dass die Reste vollständig aus CuO bestehen, werden die Cu-Beladungsmengen von Cu@CX (X = 0,03, 0,06, 0,12, 0,24) mit ungefähr 5,9, 7,5, 8,0 bzw. 9,9 Gew.-% berechnet, was identisch mit ist die aus der AAS-Analyse ermittelten Werte.
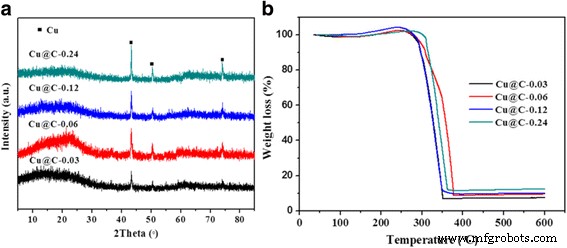
a XRD-Muster und b TG-Kurven von Proben:Cu@C-0,24, Cu@C-0,12, Cu@C-0,06, Cu@C-0,03
Katalytische Leistung von Cu@C-X (X = 0,03, 0,06, 0,12, 0,24)
Der so hergestellte Cu@C-Katalysator wurde auf die oxidative Flüssigphasen-Carbonylierung von Methanol zu DMC getestet (Tabelle 2). Obwohl er besser als andere war, ergab der Katalysator Cu@C-0,12 unerwarteterweise nur eine extrem ineffiziente Methanolumwandlung von 0,82%. Die geringe katalytische Aktivität könnte mit dem Fehlen einer ausreichenden Porosität und einem großen Porenvolumen in der Schale in Verbindung gebracht werden. Nach unserem besten Wissen fungieren Poren, die sich auf der Hülle befinden, als Kanäle, die den Hohlraum der Kugeln mit der äußeren Umgebung verbinden [24]. Obwohl die Schalendicke von Cu@C-0,12 ~15 nm beträgt, fehlt es an ausreichender Porosität (das strukturelle Porenvolumen beträgt 0,23 cm 3 /g mit einer geringen spezifischen Oberfläche von 365 m 2 /g) schränkt die Menge der Reaktantenmoleküle ein, in die Hohlräume zu diffundieren und weiter mit der vergrabenen aktiven Komponente von Cu-Kernen in Kontakt zu treten. Daher ist es entscheidend, mehr Porosität in den Schalen zu erzeugen, um den Massentransport zu erleichtern. Die KOH-Aktivierung ist bekanntlich eine etablierte Methode zur Einstellung der Porosität von Kohlenstoffmaterialien [25,26,27]. Mit dieser Methode können Mikroporen und Mesoporen in Kohlenstoff eingebracht werden, zusammen mit einer signifikanten Erhöhung der spezifischen Oberfläche und des Porenvolumens [28]. Während des Aktivierungsverfahrens wird die KOH-Menge im Allgemeinen als kritischer Faktor betrachtet, um die poröse Struktur zu beeinflussen; daher wurden unterschiedliche Massenverhältnisse von KOH/HCS hergestellt, um das aktivierte Cu@C-0,12 zu optimieren.
Physikochemische Eigenschaften von Cu@A-HCS
TEM-Bild (Abb. 6a) zeigt, dass die aktivierte Cu@A-HCS-Probe die kugelförmige Morphologie bei dem niedrigeren Massenverhältnis von KOH/HCS (1/4) beibehält, aber teilweise oder stark geätzt ist mit einem KOH/HCS-Massenverhältnis von mehr als 1 /2 (Siehe die Hintergrundinformationen Abb. 2a, b). Dieses Ergebnis stimmt gut mit früheren Berichten überein, dass eine übermäßige Menge an KOH zu mehr Kohlenstoffabbrand führt und die Morphologie zerstört [29]. Interessanterweise sind für Cu@A-HCS-Nanokomposite nach der Aktivierung überwiegend hochdisperse Kupferpartikel in die Hülle der Hohlkugeln eingebettet, die neben mehreren in den Hohlräumen eingeschlossenen koexistieren. Im Vergleich zu Cu@C-0,12 zeigen die Cu-NPs, die die Schale einfügen, die relativ kleinere Partikelgröße, die bei 18 ± 2 nm zentriert ist (Abb. 6b), da die Schalenmatrix die kleinen Cu-Cluster daran hindert, größer zu werden. Die Existenz von weißen Punkten in der Schale deutet auf die Existenz ungeordneter Mikrosporen hin. Abbildung 6c zeigt die N2 -Adsorptions-Desorptions-Isothermen des Cu@C-HCS, die repräsentative Typ-IV-Kurven zeigen, die mit Mesoporenmerkmalen assoziiert sind und zeigen, dass die aktivierten Proben hierarchisch mikro-/mesoporöse Strukturen aufweisen. Außerdem wurde festgestellt, dass nach der KOH-Aktivierung bei 700 °C für 2 h die Oberfläche von A-HCS von 471 auf 989 m 2 . anstieg /g, sogar größer als Aktivkohle (812 m 2 /g) und das Mikroporenvolumen (Vmic ), das Mesoporenvolumen (Vmes ) und das Gesamtvolumen (VT ) ebenfalls erhöht, aber das Verhältnis von Vmic nach VT neigt dazu, abzunehmen. Dieses Ergebnis weist darauf hin, dass nach der KOH-Aktivierung mehr Mesoporen gebildet werden, was möglicherweise mit der Erweiterung der Mikroporen oder der Bildung von Mesoporen durch die Anwesenheit von KOH zusammenhängt [30]. Die typische große Oberfläche und die entwickelte Porosität von Cu@A-HCS-Katalysatoren begünstigen die Verteilung der aktiven Phase auf dem Träger, garantieren einen schnellen Stoffübergang zwischen dem eingeschlossenen Katalysator und der äußeren Umgebung (Reaktanten) und erhöhen seine Sinterbeständigkeit bei hoher Metallbelastung [31]. Wie durch das XRD-Muster in Fig. 6d von Cu@A-HCS bestätigt, können alle Peaks unbestritten auf kubisches Cu indiziert werden (JCPDS 04-0836); währenddessen impliziert die Verbreiterung der charakteristischen Peaks die Bildung der Cu-NPs mit kleiner Größe. Tatsächlich wird die durchschnittliche Größe der Cu-NPs in Cu@A-HCS gemäß der Scherrer-Gleichung auf 15 nm geschätzt, was mit dem durch TEM erhaltenen Ergebnis übereinstimmt. Wie vorhergesagt, wurden die Cu@A-HCS-Katalysatoren mit 11 Gew.-% Cu, bestimmt durch AAS, mit der gleichen Methode erhalten, höher als Cu@C-0,12. Noch wichtiger ist, dass während des Aktivierungsprozesses zwangsläufig sauerstoffhaltige funktionelle Gruppen, die möglicherweise aus der KOH-Aktivierung stammen, in HCSs eingeführt werden [27]. Insgesamt führen die Erzeugung von Oberflächengruppen, die Zunahme der Oberfläche und des Porenvolumens synergistisch zu einer starken Dispersion von Cu-NPs, was der Förderung der katalytischen Aktivität zugute kommt [32,33,34]. Detaillierte Textureigenschaften sind in Tabelle 3 zusammengefasst.
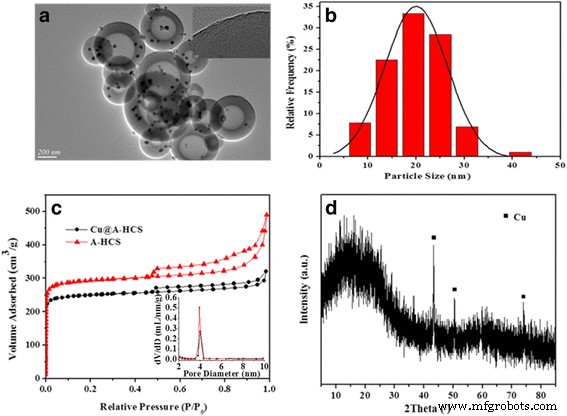
a TEM-Aufnahme von Cu@A-HCS und b seine entsprechende Cu-Partikelgröße. c N2 Adsorptions-Desorptions-Isothermen und Porengrößenverteilungen von A-HCS und Cu@A-HCS. d XRD-Muster des Cu@A-HCS-Katalysators
katalytische Leistung von Cu@A-HCS
Die katalytischen Leistungen von A-HCS und Cu@A-HCS sind in Tabelle 4 zusammengefasst. Wie in Tabelle 4 gezeigt, ist klar, dass der Träger A-HCS keine katalytische Aktivität bei der DMC-Synthese zeigte. Wie erwartet verbesserten sich die katalytischen Eigenschaften aktivierter Proben im Vergleich zu nicht aktivierten drastisch. Es ist bemerkenswert, dass im Vergleich zu 2,04 h −1 und 4,38 % für Cu@C-0,12, die beginnende Aktivität von Cu@A-HCS zeigt einen fast vierfachen Anstieg der TOF von 8,6 h −1 begleitet von einem entsprechend dramatischen Anstieg von CMeOH von 17,1% jeweils unter den gleichen Bedingungen. Diese bemerkenswerten Ergebnisse sind angesichts des Anstiegs der Oberfläche angemessen und die Porenvolumina der Kohlenstoffhüllen können mehr Reaktantenmoleküle aus der Volumenlösung positiv adsorbieren, die Diffusionsgeschwindigkeiten durch die Kanäle erheblich erleichtern und sie im Hohlraum der Katalysatoren, was zu einer höheren Reaktantenkonzentration für eine zugängliche begrenzte Katalyse führt. Ein Katalysator mit einigermaßen langer Lebensdauer ist entscheidend für seine Anwendung in der Industrie. Der gewählte Katalysator ist eine aktivierte Cu@A-HCS-Probe mit einer vielversprechenden Aktivität, um die Haltbarkeit in einem oben beschriebenen Chargensystem zu testen. Heterogene Katalysatoren leiden häufig unter einer Abnahme der Aktivität als extensives Auswaschen aktiver Metallspezies während der Reaktionen [35]. Ebenso wichtig ist die Stabilität gegen Koaleszenz für Katalysatoren auf Nanokristallbasis [36]. In unserem Fall, wie in Tabelle 3 zusammengefasst, behält der zurückgewonnene Cu@A-HCS-Katalysator (durch Filtration abgetrennt) selbst nach sieben Durchläufen (Einträge 2-8) eine viel höhere katalytische Aktivität als CuCl, und die durchschnittliche Auslaugung von Cu beträgt der aktive Bestandteil des Katalysators beträgt etwa 0,004% und bleibt damit dem frischen nahezu gleich. Kristallstruktur und Morphologie der Katalysatoren änderten sich indes nach aufeinanderfolgenden Zyklen kaum (zusätzliche Datei 1:Abbildung S2). Offensichtlich reicht die Anwesenheit der porösen Kohlenstoffhülle aus, um die aktiven Metallspezies zu stabilisieren, indem ihre Aggregation und Auswaschung verhindert werden; gleichzeitig sind die Schalen so durchlässig, dass katalytische Oberflächen für die Reaktanten und Produkte zugänglich und vorteilhaft bleiben [12]. Daher sind die YSN-Katalysatoren effektive und nichtkorrosive katalytische Systeme, bei denen die Cu-NPs als Kernmaterialien im Hohlraum von HCSs reaktive Zentren liefern und die poröse Kohlenstoffhülle verhindert, dass der Kern unter Reaktionsbedingungen aggregiert und ausgelaugt wird.
Schlussfolgerungen
Zusammenfassend haben wir eine einfache Ship-in-a-Bottle-Strategie für die Herstellung von Dotter-Kohlenstoff-Schalen-Nanostrukturen aus Cu-NPs mit maßgeschneiderter Größe in engen Verteilungen durch Anpassung der Konzentration von Kupfersalzen vorgestellt. Wie gezeigt, sind die katalytischen Eigenschaften dieses rasselartigen Systems bei der oxidativen Carbonylierung von Methanol zu DMC stark von der Porosität abhängig. Aktivierte Probe mit extrem großer Oberfläche ermöglicht die Herstellung hocheffizienter geschlossener Nanoreaktoren für katalytische Reaktionen mit deutlich höherem Umsatz (17,1 %) und TOF (8,6 h −1 .) ), lange Lebensdauer und vernachlässigbare Auslaugung in jedem Zyklus, die zweifellos die saubere Produktion von grüner chemischer DMC erfüllen. Darüber hinaus kann der in diesem Artikel beschriebene Syntheseweg neue Möglichkeiten zur Herstellung von Dotterschalen-Nanostrukturen mit verschiedenen Zusammensetzungen innerhalb der Kohlenstoffschale eröffnen.
Nanomaterialien
- Nanocups können Licht biegen
- Einfache Synthese von heterostrukturiertem WS2/Bi2MoO6 als Hochleistungs-Photokatalysatoren, die durch sichtbares Licht angetrieben werden
- Neue Nanokomposite aus Polystyrol mit mit Laurylschwefelsäure dotiertem Polyanilin
- Hochdurchsatz-Herstellung hochwertiger Nanofasern unter Verwendung eines modifizierten Elektrospinnens mit freier Oberfläche
- Durch sichtbares Licht angetriebene photokatalytische Leistung von N-dotierten ZnO/g-C3N4-Nanokompositen
- Herstellung und Charakterisierung eines neuen anodischen Tio2-Kohlenstoff-Nanofaser-Verbundkatalysators für eine Direkt-Methanol-Brennstoffzelle mittels Elektrospinnverfahren
- Magnetische Poly(N-isopropylacrylamid)-Nanokomposite:Einfluss des Herstellungsverfahrens auf die antibakteriellen Eigenschaften
- Herstellung, Charakterisierung und Zytotoxizität von kugelförmigen, konjugierten Gold-Cockle-Shell-abgeleiteten Calciumcarbonat-Nanopartikeln für biomedizinische Anwendungen
- Die Herstellung und hocheffiziente Absorption elektromagnetischer Wellen von CoFe/C-Kern-Schale-strukturierten Nanokompositen
- Herstellung und Charakterisierung von ZnO-Nano-Clips durch das Polyol-vermittelte Verfahren