Selbstpolarisation von PVDF-Folie ausgelöst durch hydrophile Behandlung für pyroelektrische Sensoren mit extrem niedrigem piezoelektrischem Rauschen
Zusammenfassung
Folien aus Polyvinylidenfluorid (PVDF) besitzen multifunktionale Fähigkeiten für piezo-/pyro-/ferroelektronische Anwendungen. Eine kritische Herausforderung der traditionellen Techniken ist der komplizierte Herstellungsprozess zum Erhalten der gepolten Filme. In dieser Arbeit wird die PVDF-Folie einfach hergestellt, indem die Lösung auf hydrophil behandelte Substrate gegossen wird. Die erhaltenen PVDF-Filme weisen eine ziemlich gute Pyroelektrizität auf, die mit denen vergleichbar ist, die durch thermische Polung hergestellt wurden, was anzeigt, dass der Film selbstpolarisiert ist. Dieses Ergebnis wird auf die durch Wasserstoffbrücken induzierte geordnete Anordnung der ersten Sub-Nanoschicht an der Unterseite zurückgeführt, die als „Keimschicht“ dient und die Ausrichtung des restlichen Films in einem schichtweisen Ansatz auslöste. Um das piezoelektrische Rauschen zu unterdrücken, wird außerdem ein pyroelektrischer Sensor mit einer neuartigen Doppelschichtstruktur unter Verwendung des so hergestellten PVDF-Films entwickelt. Im Vergleich zum herkömmlichen Monolayer-Sensor ist das Signal-Rausch-Verhältnis des Bilayer-Sensors von 18 dB auf 38 dB drastisch verbessert. Die obigen Ergebnisse bieten großartige Möglichkeiten, einen tragbaren pyroelektrischen Hochleistungssensor mit reduzierten Kosten und einfachen Verfahren zu erreichen.
Einführung
Polyvinylidenfluorid (PVDF) und seine Copolymere [1,2,3,4,5] sind in den letzten Jahren aufgrund ihrer guten piezoelektrischen und pyroelektrischen Leistung, Flexibilität und . zu heißen Kandidaten für tragbare Elektronik, multifunktionale flexible Sensoren und Nanogeneratoren geworden einfacher Prozess [6,7,8,9,10,11]. Es ist jedoch immer noch eine große Herausforderung, eine gute pyroelektrische Funktion in PVDF zu realisieren. Bei herkömmlichen Verfahren sind zwei Schritte, d. h. Strecken und thermisches Polen, unvermeidlich. Der erste Schritt besteht darin, einen hohen β-Phasengehalt zu erhalten [12,13,14,15,16], und der zweite besteht darin, die Dipolvektoren in der β-Phase senkrecht zur Filmoberfläche weiter auszurichten [17,18,19,20 ]. Die kompliziert erhaltenen PVDF-Proben zeigen Nachteile wie kleine aktive Fläche, große Anzahl von Defekten, geringer Wirkungsgrad und sorgfältiger Schutz gegen elektrischen Schlag [12, 13, 18, 19, 20]. Darüber hinaus sind aufgrund der intrinsischen piezoelektrischen Natur von PVDF herkömmliche Infrarotsensoren aus einschichtigem PVDF anfällig für Umgebungsvibrationsgeräusche, die die pyroelektrische Leistung des Geräts stark beeinträchtigen.
Kürzlich wurden verschiedene Methoden entwickelt, um selbstpolarisierte PVDF-Filme ohne thermische Polung zu realisieren, einschließlich Gießen [21,22,23,24,25], Spincoating [26, 27], Langmuir-Blodgett (LB)-Abscheidung [28 ], Elektrospinnen [29,30,31,32,33,34,35] und Abscheidung auf wässriger Salzlösung [36]. Im Allgemeinen kann die Selbstpolarisation der PVDF-Filme durch die obigen Techniken aufgrund verschiedener Mechanismen beobachtet werden, wie der salzunterstützten [21,22,23,24,25], Wasserstoffbrücken-Wechselwirkung [21,22,23 ,24,25, 27, 36], eingebautes Feld [26] oder starkes elektrisches Feld [29, 35] während der Abscheidung und Dehnung während der Beschichtung [26, 28, 36]. Die meisten dieser Methoden konzentrierten sich jedoch nur auf die piezoelektrische Leistung von PVDF-Filmen und vernachlässigten ihre pyroelektrischen Eigenschaften. Darüber hinaus waren Schleuderbeschichtung und LB-Techniken nur für ultradünne Filme anwendbar [26, 28], während das Gießverfahren ein Salzadditiv erforderte, um eine Selbstpolarisation zu erreichen [21,22,23,24,25] und der Polarisationsmechanismus des Elektrospinnens erforderte ein weiteres Verständnis [29,30,31,32,33,34,35]. In Bezug auf den Sensor ist die selektive Polung von ferroelektrischen keramisch dotierten PVDF-Verbundwerkstoffen eine gängige Methode, um den Einfluss von Umgebungsschwingungsgeräuschen zu verringern [37, 38]. Diese dotierten Keramiken, z. B. Bleizirkonattitanat (PZT), haben das gleiche Vorzeichen des pyroelektrischen Koeffizienten (p ) während das entgegengesetzte Vorzeichen des piezoelektrischen (d 33 ) als PVDF (oder sein Copolymer). Wenn also zwei Phasen parallel polarisiert sind, wird die pyroelektrische Reaktion verstärkt und die piezoelektrische Aktivität wird teilweise aufgehoben, was das vibrationsinduzierte elektrische Rauschen in pyroelektrischen Sensoren reduzieren kann. Allerdings sind die ganzen Verfahren ziemlich kompliziert; außerdem werden nach der Dotierung mit Keramik die dielektrischen Eigenschaften von PVDF verschlechtert, was die Effizienz dieser Technik stark einschränkt [39]. Daher ist es immer noch eine große Herausforderung, einen pyroelektrischen Hochleistungsfilm sowie den Sensor effizient zu erhalten.
In dieser Arbeit entwickeln wir eine einfache Technik zur Herstellung von pyroelektrischen PVDF-Filmen, indem wir das konventionelle Gießverfahren mit der hydrophilen Modifizierung des Substrats kombinieren. Die Ergebnisse zeigen, dass die so hergestellten PVDF-Filme gleichzeitig einen hohen β-Phasengehalt und eine signifikante pyroelektrische Reaktion erreichen. Ein Polarisationsmechanismus basierend auf einem Dipol-Ausrichtungs-Relais-Prozess wird eingeführt, um die obigen Ergebnisse zu verdeutlichen. Außerdem wird durch die Verwendung der präparierten PVDF-Probe als empfindliches Material ein flexibler Infrarotsensor mit Doppelschichtstruktur vorgeschlagen, um ein extrem niedriges piezoelektrisches Rauschen in der Vorrichtung zu erreichen. Diese Technik zeigt ein großes Potenzial für den Einsatz in tragbaren Infrarotsensoren oder Temperatursensoren in rauen Umgebungen, in denen starke akustische Geräusche und/oder mechanische Vibrationen auftreten.
Methoden
Vorbereitung des PVDF-Films und des pyroelektrischen Doppelschichtsensors
Der Herstellungsprozess der PVDF-Folie ist in Abb. 1 dargestellt. Zuerst wurde ein Stück Glassubstrat in die Piranha-Lösung (Gemisch:H2 SO4 (98% Konzentration, Kelong Chemical, China) und H2 O2 (30% Konzentration, Kelong Chemical, China) mit einem Volumenverhältnis von 7:3) für die hydrophile Behandlung. Die Lösung wurde für 2–8 Stunden bei 60 °C in einen Inkubator gestellt. Eine bestimmte Menge PVDF-Pulver (durchschnittliches Mw ~534.000 , Sigma-Aldrich, USA) wurde mit N . gemischt -Methylpyrrolidon (NMP) (99 % Reinheit, Kelong Chemical, China) Lösungsmittel mit einem Massenverhältnis von 10 Gew.-%, das dann unter magnetischem Rühren 4 h auf 50 °C erhitzt wurde, bis eine vollständig einheitliche Lösung erreicht wurde. Diese erhaltene Lösung wurde auf das oben erwähnte behandelte Substrat gegossen und 10 h bei 80ºC gehalten, um das NMP-Lösungsmittel zu entfernen. Um den Kanteneffekt in den Filmen zu reduzieren, wurde der so hergestellte PVDF-Film mit einer Fläche von 10 mm × 10 mm schließlich durch Ausschneiden der Probe aus dem zentralen Bereich des gegossenen 50 mm × 50 mm-Films erhalten. Zum Vergleich wurde die PVDF-Probe auch auf einem unbehandelten Substrat hergestellt und die Dicke aller Proben beträgt 50 µm. Auf beiden Seiten der Proben wurden Aluminiumelektroden zur pyroelektrischen und piezoelektrischen Leistungsmessung aufgedampft.
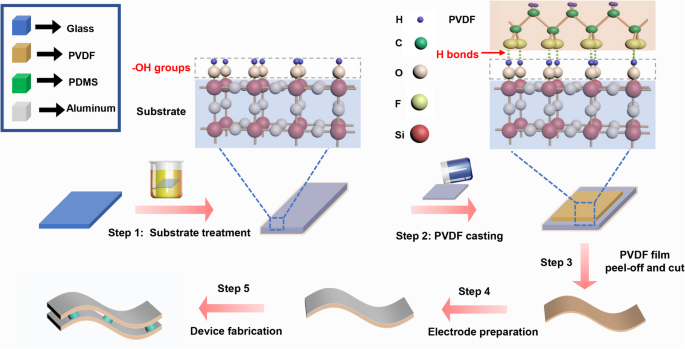
Illustration des PVDF-Film- und Gerätevorbereitungsprozesses. Schritt 1 wurde das Glassubstrat 2–8 h in Piranha-Lösung getränkt. Schritt 2, gut gerührte PVDF-Lösung wurde auf das Substrat gegossen und 10 h bei 80 °C getrocknet. Schritt 3, der PVDF-Film wurde vom Substrat abgezogen und die Kante wurde abgeschnitten, um den Kanteneffekt zu entfernen. Schritt 4, Aluminium wurde auf beide Seiten des Films als Elektroden aufgedampft. Schritt 5, die Doppelschichtvorrichtung wurde unter Verwendung von PDMS-Säulen hergestellt, die zwischen den beiden Schichten als Separatoren getragen wurden. Ebenfalls angegeben waren schematische Darstellungen der an der Oberfläche des Glassubstrats nach der Behandlung gebundenen Hydroxylgruppen, die Bildung von Wasserstoffbrücken nach dem PVDF-Gießen und die geordnete Anordnung der „ultradünnen Schicht“ an der Unterseite der PVDF-Folie
Löcher mit Durchmessern von 1 mm wurden in einer 1 mm dicken Acrylplatte (Xintao Plexiglass, China) mit einem Hochleistungslaserstrahl (Typ 4060, Ketai, China) hergestellt und als Säulenmodelle verwendet. Als Säulenvorläufermaterial wurde Silikonelastomer (Sylgard 184, DOW CORING) gewählt. Basis und Härter wurden im Gewichtsverhältnis 10:1 gemischt und dann in die Löcher getropft. Säulen aus Polydimethylsiloxan (PDMS) können nach 10-stündiger Härtung bei 60 °C erhalten werden. Die Doppelschichtvorrichtung wurde hergestellt, indem zwei polarisierte PVDF-Filme mit fünf Säulen mit einem Klebstoff (Typ 810, LEAFTOP, China) verklebt wurden.
Physische Charakterisierung und Testmethode
Das Kontaktwinkelmessgerät (CA) (Typ JC2000D1, POWEREACH, China) wurde verwendet, um die Hydrophilie des Substrats zu charakterisieren. Fourier-Transform-Infrarot (FTIR) (Typ 6700, NICOLET, US) Spektroskopietests wurden durchgeführt, um die Zusammensetzung und Phasenstruktur der Proben zu analysieren. Die Kristallinität wurde mit einem Differentialscanningkalorimeter (DSC) (Typ DSC 7020, SEICO INST., US) gemessen. Oberflächenmorphologien von Proben wurden durch ein Rasterelektronenmikroskop (REM) (Typ Inspect F50, FEI, US) charakterisiert. Die Beziehungen zwischen elektrischer Verschiebung und elektrischem Feld (D-E) der gepolten Proben wurden mit einem ferroelektrischen Analysator (Typ HVI40904-523, Radiant, US) aufgezeichnet. Die dielektrischen und dielektrischen Verlustkonstanten (ε′ und ε″) wurden mit einem Impedanzanalysator (Typ 4294A, Agilent, USA) gemessen.
Für die pyroelektrische Messung wurde ein selbstgebauter Aufbau basierend auf einer elektrisch modulierten Methode angewendet (Zusatzdatei 1:Abbildung S1a). Insbesondere wurden Rechteckwellen unterschiedlicher Frequenz durch einen Wellengenerator (Typ DG1022U, RIGOL Technologies Inc., China) erzeugt. Ein gepulster 980-nm-Laser wurde von der Rechteckwelle angetrieben und als modulierte Wärmequelle verwendet. Der pyroelektrische Strom der Proben wurde durch eine selbstgebaute Strom-Spannungs-Umwandlungsschaltung verstärkt und schließlich von einem digitalen Oszilloskop (Typ DSOX3012A, Agilent, US) ausgelesen. Für die piezoelektrische Messung wurde ein ähnlicher Aufbau aufgebaut, indem der Laser durch einen Vibrator ersetzt wurde, der über einen mit dem Wellengenerator verbundenen Leistungsverstärker sinusförmig angeregt wurde (Zusatzdatei 1:Abbildung S1a).
Ergebnisse und Diskussion
Der PVDF-Film
Abbildung 2a zeigt die CA der in Piranha-Lösung eingetauchten Glassubstrate für unterschiedliche Behandlungszeit. Es zeigt deutlich, dass die hydrophile Eigenschaft des Substrats nach der Behandlung verbessert wird. Die CA nimmt mit zunehmender Eintauchzeit weiter ab und neigt zur Sättigung bei 8 h. Der mögliche Grund kann sein, dass bei längerer Behandlungszeit mehr hydrophile hängende Si-OH-Gruppen an der Oberfläche des Glases entstehen. Ein weiterer Beweis für diese Schlussfolgerung ist die Tatsache, dass es mit zunehmender Behandlungszeit schwieriger wurde, die PVDF-Folie vom Substrat abzulösen (Einschub in Abb. 2a).
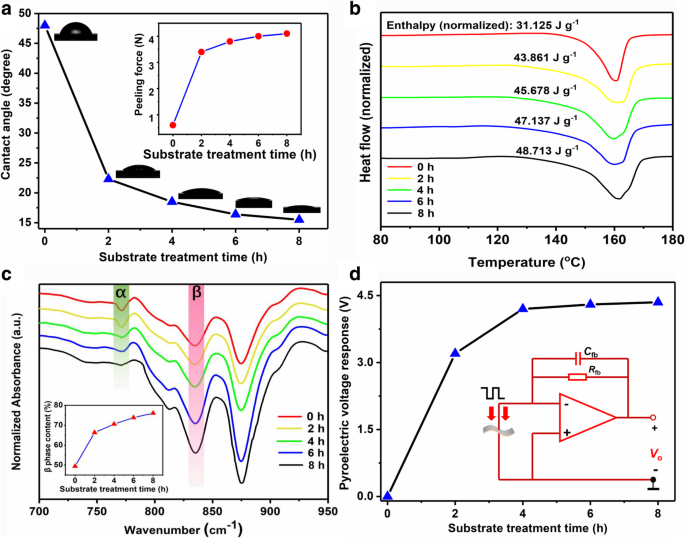
a CA der in Piranha behandelten Glassubstrate für unterschiedliche Zeit, Einschub ist die Schälkraft als Funktion der Behandlungszeit. b DSC-Muster von PVDF-Proben. c FTIR-Spektren von PVDF-Proben, Einschub ist der β-Phasen-Gehalt als Funktion der Behandlungszeit, berechnet aus den FTIR-Ergebnissen. d Pyroelektrische Reaktion von PVDF-Proben ohne thermische Polung, Einschub ist das vereinfachte Schema der selbstgebauten Signalausleseschaltung
DSC-Charakterisierungen werden durchgeführt, um den Einfluss einer hydrophilen Behandlung auf die Kristallinität von PVDF-Proben zu untersuchen. In DSC-Ergebnissen kann der Kristallinitätsprozentsatz von PVDF bestimmt werden durch [40].
$$ {X}_{\mathrm{C}}=\left(\frac{\Updelta {H}_{\mathrm{m}}}{\Updelta {H}_{\mathrm{m}}^0 }\rechts)\mal 100\%, $$ (1)wobei X C ist der Kristallinitätsprozentsatz von PVDF, ΔH m ist die Schmelzenthalpie des PVDF und \(\Updelta {H}_{\mathrm{m}}^0\) ist der Schmelzenthalpiewert eines 100% kristallinen PVDF. Abbildung 2b zeigt das gemessene ΔH m Werte von PVDF-Proben, die auf Substrate mit unterschiedlicher Behandlungszeit gegossen wurden. Dementsprechend kann leicht berechnet werden, dass X C in der 8-h-behandelten Probe um mehr als 50 % im Vergleich zur unbehandelten Probe erhöht.
Das FTIR-Spektrum wird außerdem verwendet, um die Phasenzusammensetzung in den Proben zu untersuchen. Die Peaks bei der Wellenzahl 764 cm −1 und 840 cm −1 (Abb. 2c) werden normalerweise den Eigenschaften der α- und β-Phase und der Fläche des Peaks (A 764 oder A 840 ) ist proportional zum entsprechenden Phasengehalt [41, 42]. Wie in Abb. 2c gezeigt, A764 nimmt ab, während A 840 nimmt mit der Behandlungszeit monoton zu. Um den Einfluss der Behandlungszeit auf den Phasengehalt in PVDF quantitativ zu beurteilen, kann die folgende Formel (2) angewendet werden [42],
$$ {F}_{\mathrm{rel}}\left(\upbeta \right)=\frac{X_{\upbeta}}{X_{\upalpha}+{X}_{\upbeta}}=\frac {A_{\upbeta}}{\left({K}_{\upbeta}/{K}_{\upalpha}\right){A}_{\upalpha}+{A}_{\upbeta}} $ $ (2)wobei X α und X β sind der absolute Prozentsatz der α- und β-Phasen, A α und A β sind Peakflächen bei 764 cm −1 und 840 cm −1 , und Kα = 6.1 × 10 4 cm 2 mol −1 und Kβ = 7,7 × 10 4 cm 2 mol −1 sind Absorptionskonstanten.
Der Einschub von Fig. 2c zeigt, dass der berechnete β-Phasen-Gehalt monoton parabolisch mit der Behandlungszeit ansteigt. Sie erreicht bei einer Behandlungszeit von 8 h einen Maximalwert von 76,05 %, was etwa 50 % länger ist als bei der unbehandelten Probe. Dieses Ergebnis in Kombination mit dem DSC-Ergebnis zeigt, dass das erhöhte X C wandelt sich hauptsächlich in die β-Phase um. Wir messen weiterhin die D-E- und ε′-Beziehungen aller Proben, deren Ergebnisse ebenfalls sehr ähnliche Trends wie FTIR zeigen (Zusatzdatei 1:Abbildung S2 und S3).
Darüber hinaus ist es überraschend, eine ausgeprägte pyroelektrische Reaktion von PVDF-Proben auf den behandelten Substraten zu finden, ohne einem weiteren thermischen Polungsverfahren unterzogen zu werden (Abb. 2d). Die Signalaufbereitung, wie durch den Einschub angedeutet, erfolgt über eine Strommodusschaltung. Ähnlich wie bei den FTIR-Ergebnissen steigt das Ausgangssignal mit der Behandlungszeit an und sättigt sich bei einer Behandlungszeit von 8 h schließlich bei 4,3 V. Im Vergleich dazu ist in der unbehandelten Probe keine pyroelektrische Reaktion nachweisbar (Behandlungszeit = 0 h). Dieses Ergebnis zeigt, dass die hydrophilen Gruppen auf dem Substrat nicht nur den β-Phasengehalt fördern, sondern auch den PVDF-Film polarisieren können. Um die genaue Richtung der Dipolvektoren in der Probe zu untersuchen, wird eine kommerziell gepolte PVDF-Folie (Jinzhoukexin, China) mit bekannter Polrichtung als Referenzprobe verwendet. Durch Bestrahlen beider Proben mit zwei synchron modulierten Lichtquellen werden die Ausgangssignale aufgezeichnet, wobei ihre Phasen verglichen werden:Wenn zwei Signale in Phase sind, sind die Dipole in beiden Proben parallel zueinander; wenn ihre Phasen umgekehrt sind, sind Dipole antiparallel. Die Ergebnisse zeigen, dass die Richtung der Dipole in den behandelten Proben vom Substrat zum Film zeigt (Zusatzdatei 1:Abbildung S1b und S1c).
Basierend auf den obigen Ergebnissen kann der Polungsmechanismus von PVDF-Filmen durch die hydrophilen Gruppen wie folgt geschlossen werden (schematisch in Abb. 1 dargestellt):Die baumelnden Siliziumbindungen an der Oberfläche des Glassubstrats werden nach der hydrophilen Behandlung. Beim Gießen der PVDF-Lösung können aufgrund ihrer großen elektrischen Negativitätsunterschiede Wasserstoffbrückenbindungen zwischen Fluoratomen in den VDF-Einheiten und Wasserstoffatomen in Hydroxylgruppen gebildet werden. Dadurch sind die Dipolvektoren in der ersten Sub-Nanoschicht der PVDF-Folie unten nach oben ausgerichtet. Diese erste Sub-Nanoschicht spielt dann als Keimschicht, und danach wird die benachbarte obere Sub-Nanoschicht durch elektrische Kraft weiter ausgerichtet, die von den bereits ausgerichteten Dipolvektoren in der Keimschicht herrührt. Dieser Vorgang wird sich dann in allen obigen Sub-Nanoschichten wiederholen, wenn die Zeit lang genug wird. Mit anderen Worten, die Ausrichtung der Dipolvektoren in PVDF-Filmen wird von unten nach oben übertragen (Abb. 3a). Dieser Dipol-Ausrichtungs-Relais-Prozess kann nur stattfinden, wenn die Molekülketten in PVDF hochflexibel und aktiv sind, bevor der Film vollständig ausgehärtet ist. Folglich wird der β-Phasen-Gehalt im Film gefördert, da der „Relaisprozess“ beendet ist, nachdem der Film vollständig ausgehärtet ist, und gleichzeitig wird der gesamte Film polarisiert.
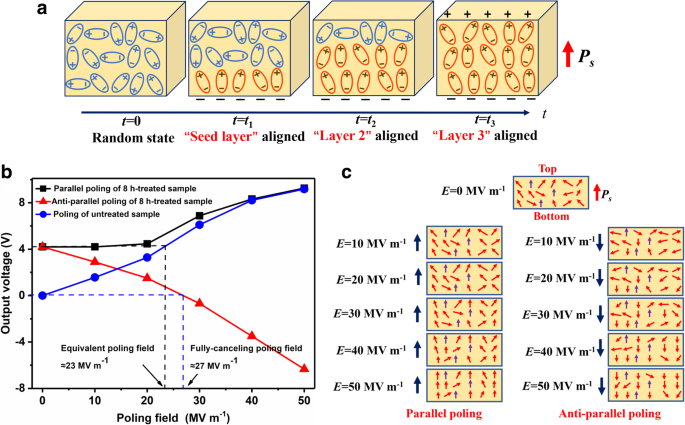
a Dipolausrichtungsrelaisprozess in PVDF, ausgelöst durch die hydrophilen Gruppen zwischen den Substraten. b Einflüsse des thermischen Polungsfeldes und der Richtung auf die pyroelektrischen Reaktionen einer 8-h-behandelten Probe. c Schematische Darstellung der parallelen und antiparallelen Polung
Um den Polarisationsgrad in den Proben weiter zu untersuchen, wird ein konventioneller thermischer Polungsprozess durchgeführt. Im Gegensatz zur thermischen Polung der unpolarisierten Probe sind die Dipolvektoren in den behandelten Proben bereits ausgerichtet, sodass die Richtung des elektrischen Polungsfelds (E p ) soll Einfluss auf die Filmpolarisation haben. Daher wird sowohl die parallele als auch die antiparallele Polung durchgeführt. Wie in Abb. 3b gezeigt, sind für parallel gepoltes behandeltes PVDF die Ausgangssignale (V o ) bleibt zunächst stabil und vergrößert sich dann mit der Zunahme von E p ungefähr am Knoten von 20 MV m −1 . Im Vergleich dazu V o steigt monoton mit dem E p für die unbehandelte Probe im gesamten Polbereich; außerdem V o der unbehandelten Probe ist immer kleiner als E p kleiner als 40 MV m −1 . ist . Als E p erhöht sich weiter, V o beider Proben werden äquivalent, das Maximum beträgt 8,8 V als E p = 50 MV m −1 . Diese Ergebnisse zeigen, dass der Polarisationswert in behandelten Proben als Behandlungszeit = 8 h mit dem Polarisationswert vergleichbar ist, wenn sie einer konventionellen thermischen Polung bei E . unterzogen wurden p ≈ 23 MV m −1 (äquivalentes Polfeld). Andererseits, wenn die behandelte Probe umgekehrt gepolt wird, V o nimmt monoton mit E ab p , und, wie in der Abbildung gezeigt, V o ≈ 0 V als Ep ≈ 27 MV m −1 (vollaufhebendes Polfeld). Dieses Phänomen weist darauf hin, dass die hydrophil induzierte Polarisation durch Umkehrpolung vollständig aufgehoben werden kann. Dies bedeutet jedoch nicht notwendigerweise, dass die induzierte Polarisation vollständig depolarisiert ist; im Gegenteil, ein Bruchteil der induzierten Polarisation bleibt immer noch als E p = 50 MV m −1 (Abb. 3c), da das negative Maximum V o (= − 6.2 V) ist offensichtlich kleiner als das maximale V o (= 8,8 V) von parallelen thermisch gepolten Gegenstücken. Diese nicht depolarisierbaren Dipolvektoren benötigen möglicherweise ein viel größeres E p (> 50 MV m −1 ) zur Umorientierung, was an ihrer viel geringeren potentiellen Energie und höheren Stabilität im Vergleich zu anderen Vektoren liegen könnte [43]; dies erklärt auch den Unterschied zwischen dem äquivalenten Polfeld und dem vollständig aufhebenden Feld.
Der pyroelektrische Doppelschichtsensor
Da alle pyroelektrischen Materialien von Natur aus piezoelektrische Eigenschaften besitzen, wird daher unvermeidlich ein unerwünschtes Signal erzeugt, wenn ein pyroelektrischer Sensor durch Stoß oder Vibration mechanisch erregt wird. Wenn zwei PVDF-Elemente verwendet werden, wobei eines als empfindliches Material und das andere als Referenz verwendet wird, um das piezoelektrische Signal zu kompensieren, könnte ein pyroelektrischer Sensor mit minimiertem piezoelektrischem Rauschen erzielt werden. Zu diesem Zweck schlagen wir einen pyroelektrischen Sensor mit einer neuartigen Doppelschichtstruktur vor (Abb. 4a), bei dem zwei identische PVDF-Folien mit fünf winzigen Säulenseparatoren dazwischen montiert sind. Bei diesem Gerät ist die obere Folie das empfindliche Material und die untere der piezoelektrische Kompensator. Die fünf Säulen spielen zwei wichtige Rollen:(1) gute thermische Isolierung, d. h. Verhinderung der Wärmeableitung von der oberen Schicht zur unteren; und (2) Übertragung mechanischer Schwingungen zwischen zwei Schichten ohne Verzerrung. Sobald die beiden Anforderungen erfüllt sind, kann ein hochwertiges pyroelektrisches Signal mit extrem niedrigem piezoelektrischem Rauschen erwartet werden, indem das Signal des unteren Elements vom oberen abgezogen wird.

Simulations- und Messergebnisse des pyroelektrischen Sensors mit Doppelschichtstruktur. a Erkundetes Schema der Gerätestruktur. b Modell und Ergebnisse der piezoelektrischen Antwortsimulation. c Modell und Ergebnisse der thermischen Simulation. d Optisches Foto des hergestellten Geräts. e Piezoelektrische Antwort bei verschiedenen Frequenzen. f Reaktionen von Doppelschicht- und konventionellen Monoschicht-Bauelementen bei gleichzeitiger Stimulation durch mechanische Schwingungen (5 Hz) und Wärmestrahlung (1 Hz)
Unter Verwendung der piezoelektrischen und thermischen Modelle der COMSOL Multiphysics-Software werden mechanische und thermische Simulationen des Geräts durchgeführt, um das Design dieses Doppelschicht-Prototyps zu validieren. Wie in 4b gezeigt, zeigen die piezoelektrischen Reaktionen von beiden Schichten ähnliche Variationstrends mit der ausgeübten Beschleunigungsrichtung. Die maximalen Antworten und deren Unterschiede treten in der Normalkraftrichtung auf, wobei die Antwort des unteren Elements etwa 93,7% der des oberen beträgt, was bedeutet, dass das piezoelektrische Rauschen des Doppelschichtsensors um mindestens 93,7 % gegenüber unterdrückt werden kann sein einschichtiges Gegenstück. Die thermische Simulation erfolgt durch senkrechtes Einstrahlen einer periodischen Wärmewelle auf die Oberseite des Sensors (Abb. 4c). Verglichen mit der oberen Schicht bleibt die Temperaturänderungsrate (dT/dt) der unteren Schicht nahezu stabil, was darauf hindeutet, dass der Wärmeverlust von der oberen Schicht zur unteren Schicht vernachlässigbar ist. Folglich sind die beiden oben genannten Anforderungen tatsächlich erfüllt (Anmerkung:Abb. 4b und c sind Simulationsergebnisse mit optimierten Parametern in Tabelle 1, mehr Details zu Simulationen, dh Abhängigkeiten der piezoelektrischen und thermischen Eigenschaften des Sensors von geometrischen Parametern (Durchmesser und Höhe) ) und Position der Säulen finden Sie in Teil 2 der Zusatzdatei 1).
Eine Doppelschicht-Sensorprobe wird entsprechend hergestellt (Fig. 4d) basierend auf den 8-h-behandelten Proben. Wie in 4e dargestellt, werden offensichtliche piezoelektrische Reaktionen der oberen und unteren Elemente beobachtet, die beide sehr ähnliche Ergebnisse bei unterschiedlichen Anregungsfrequenzen liefern. Darüber hinaus erweist sich die Schwankungsneigung der Ansprechamplituden mit der Frequenzänderung als typisches Merkmal piezoelektrischer oder pyroelektrischer Sensoren bei niedriger Frequenz [44]. Im Vergleich dazu zeigt der piezoelektrische Ausgang der Probe bei allen Frequenzen nur sehr kleine Signale. Darüber hinaus werden die Reaktionen der Probe mit einer Monoschicht verglichen, indem die Proben gleichzeitig mit einer 5-Hz-Vibrationsquelle und einer 1-Hz-Wärmequelle stimuliert werden. Die Ergebnisse (Abb. 4f) zeigen deutlich, dass im Signal der Monoschichtprobe mit einem pyroelektrischen Signal von 4,4 V eine ernsthafte piezoelektrische Reaktion (ca. 0,5 V) vorhanden ist, dh das Signal-Rausch-Verhältnis (SNR) = 18 dB, während die Doppelschicht nur ein vernachlässigbares piezoelektrisches Rauschen (etwa 0,05 V) mit einem etwas geringeren pyroelektrischen Signal von 4,1 V aufweist, dh SNR = 38 dB. Diese Ergebnisse zeigen, dass der Doppelschicht-Infrarotsensor in rauen Umgebungen eingesetzt werden kann, in denen akustische Geräusche und/oder andere mechanische Geräusche auftreten.
Schlussfolgerungen
Zusammenfassend wird eine einfache Technik zur Herstellung von pyroelektrischen PVDF-Filmen entwickelt, indem der Vorläufer auf ein hydrophiles Glassubstrat gegossen wird. Der Gehalt an β-Phase in der präparierten Probe steigt monoton mit der hydrophilen Eigenschaft des Substrats. VDF-Dipole im PVDF-Film sind vorzugsweise in der Normalenrichtung ausgerichtet, und dementsprechend kann ein offensichtliches pyroelektrisches Signal des empfindlichen Films erhalten werden, ohne einer weiteren herkömmlichen thermischen Polung unterzogen zu werden. Darüber hinaus wird ein neuartiger pyroelektrischer Doppelschichtsensor basierend auf den vorbereiteten PVDF-Proben vorgeschlagen. Im Vergleich zu herkömmlichen Monolayer-Gegenstücken wird das piezoelektrische Rauschen im Doppelschichtsensor um etwa 90 % unterdrückt, während das pyroelektrische Signal nahezu keine Verschlechterung zeigt.
Abkürzungen
- CA:
-
Kontaktwinkel
- D-E:
-
Elektrische Verschiebung-elektrisches Feld
- DSC:
-
Differenzkalorimeter
- FTIR:
-
Fourier-Transformations-Infrarot
- LB:
-
Langmuir-Blodgett
- NMP:
-
N-Methylpyrrolidon
- PDMS:
-
Polydimethylsiloxan
- PVDF:
-
Polyvinylidenfluorid
- PZT:
-
Bleizirkonattitanat
- SEM:
-
Rasterelektronenmikroskop
- SNR:
-
Signal-Rausch-Verhältnis
Nanomaterialien
- ST:Bewegungssensor mit maschinellem Lernen für hochpräzises, batterieschonendes Aktivitätstracking
- MoS2 mit kontrollierter Dicke für die elektrokatalytische Wasserstoffentwicklung
- Elektrogesponnene Polymer-Nanofasern, dekoriert mit Edelmetall-Nanopartikeln für die chemische Sensorik
- Hochleitfähige PEDOT:PSS transparente Lochtransportschicht mit Lösungsmittelbehandlung für Hochleistungs-Silizium/organische Hybridsolarzellen
- Großflächiger WS2-Film mit großen Einzeldomänen, die durch chemische Gasphasenabscheidung gewachsen sind
- Toxizität von PEG-beschichteten CoFe2O4-Nanopartikeln mit Behandlungseffekt von Curcumin
- Elektrisch leitfähiger TPU-Nanofaserverbundstoff mit hoher Dehnbarkeit für flexiblen Dehnungssensor
- Ultraempfindlicher Dehnungssensor auf Basis eines flexiblen piezoelektrischen Poly(vinylidenfluorid)-Films
- Sensorfolie für die Luft- und Raumfahrt
- Weicher Tastsensor mit hautähnlichen Eigenschaften für Roboter