Auswirkung bearbeitungsinduzierter unterirdischer Defekte auf die Versetzungsentwicklung und die mechanischen Eigenschaften von Materialien durch Nano-Eindrückung
Zusammenfassung
Defekte unter der Oberfläche haben einen erheblichen Einfluss auf die Präzision und Leistung von Nanostrukturen. In diesem Beitrag wird eine molekulardynamische Simulation von Nano-Indentation durchgeführt, um den Einfluss von bearbeitungsinduzierten unterirdischen Defekten auf die Versetzungsentwicklung und die mechanischen Eigenschaften von Materialien zu untersuchen, wobei das Probenmodell mit unterirdischen Defekten durch Nanoschneiden realitätskonform aufgebaut wird. Der Bildungsmechanismus von unterirdischen Defekten und der Wechselwirkungsmechanismus zwischen maschineninduzierten Defekten und Versetzungsentwicklung werden diskutiert. Die Härte und das Elastizitätsmodul von einkristallinen Kupferproben werden berechnet. Die Simulationsergebnisse zeigen, dass im Untergrund des Werkstücks stabile Defektstrukturreste vorhanden sind, wie beispielsweise Atomcluster, Stapelfehlertetraeder und Treppenstangenversetzungen. Die Sekundärbearbeitung der Nano-Eindrückung kann innere Defekte des Werkstücks wiederherstellen, aber die Schäden unter der Oberfläche im Sekundärbearbeitungsbereich werden verschlimmert. Die Nano-Eindruckhärte von Proben nimmt mit dem Einbringen von Fehlern unter der Oberfläche zu, was zur Ausbildung eines Kaltverfestigungseffekts führt. Das Vorhandensein von Defekten unter der Oberfläche kann die Fähigkeit des Materials schwächen, elastischen Verformungen zu widerstehen, wobei die gegenseitige Entwicklung zwischen Versetzungen und Defekten unter der Oberfläche eine wichtige Rolle spielt.
Hintergrund
Die Ultrapräzisionsfertigung im nanometrischen Maßstab wird allgemein als effektive Methode angesehen, um Nanokomponenten mit Submikrometer-Abmessungsgenauigkeit und nanoskaliger Oberflächenqualität zu erhalten [1]. Einige stabile Fehler unter der Oberfläche verbleiben nach der Herstellung im Werkstück [2,3,4,5]. Die Fehler unter der Oberfläche wirken sich nicht nur auf die Verarbeitungsgenauigkeit und Oberflächenqualität aus, sondern wirken sich auch entscheidend auf die mechanischen Eigenschaften und die Lebensdauer von Nanobauteilen aus. Viele Studien über Defekte unter der Oberfläche wurden mit der Methode der Molekulardynamik (MD) durchgeführt und konzentrierten sich hauptsächlich auf die Bildung und Entwicklung von Defekten unter der Oberfläche s[6, 7], die Dicke der Schicht von unterirdischen Defekten (SSD) [8, 9] und den Einfluss unterirdischer Defekte auf die Oberflächenintegrität [10, 11]. Der Einfluss von Fehlern unter der Oberfläche auf die mechanischen Eigenschaften von Werkstückmaterialien wird jedoch weniger untersucht. Die mechanischen Eigenschaften von Nanostrukturen sind entscheidend für ihre Leistungsfähigkeit und Lebensdauer. Daher ist die Auswirkung von Defekten unter der Oberfläche auf die mechanischen Eigenschaften von Materialien zu einem der wichtigsten zu untersuchenden Themen geworden.
Es wurden viele Forschungen durchgeführt, um die SSD-Schicht durch molekulardynamische Simulation eines Nanoschneidprozesses zu untersuchen. Narayanan [12] untersuchte die Bildung von Stapelfehlertetraedern (SFT) in Einkristallgold und stellte den verformungsinduzierten Mechanismus der SFT vor. Inamura [13] untersuchte die Spanbildung und Materialgleitverformung während des Nanoschneidprozesses und wies darauf hin, dass die Spanbildung hauptsächlich durch Schergleitverformung induziert wird. Pei [14] untersuchte den Einfluss von Schneidparametern auf die Versetzungsentwicklung und die Schneidkraft während des Nano-Schneidprozesses und stellte fest, dass der Größeneffekt nicht signifikant ist, wenn das Werkstück größer als 40 nm ist. Dai [15] und Liu [16] wendeten MD-Simulations- bzw. Experimentmethoden an, um den Einfluss der Diamantwerkzeugstruktur und des Größeneffekts auf die Entwicklung von Werkstückfehlern unter der Oberfläche zu untersuchen. Die bisherigen Studien zeigen, dass nach dem Nanoschneiden stabile Untergrundfehler im Werkstück vorhanden sind. Schnittparameter und Werkzeuggeometrieparameter haben großen Einfluss auf die Dicke und Entwicklung der unterirdischen Schadensschicht und sogar auf die Bearbeitungsgenauigkeit. Die mechanischen Eigenschaften von Werkstückmaterialien können jedoch nicht durch die Analyse der relevanten Daten aus dem Nanoschneiden berechnet werden.
Nano-Indentation ist eine effektive Technik zur Charakterisierung der mechanischen Eigenschaften wie Härte und Elastizitätsmodul [17]. Es wurden viele Studien zur Nano-Eindrückung durchgeführt, um die Leistung mechanischer Eigenschaften durch experimentelle und theoretische Modelle zu bewerten. Zimmerman [18] analysierte die Versetzungsemission beim Nano-Indentationsprozess durch den Gleitvektor. Ruestes [19] untersuchte die Nano-Eindrückung von Einkristall-Fe durch MD-Simulation und stellte fest, dass die Erzeugung von Versetzungen im Untergrund notwendig ist, um das Material aus der Eindruckzone zu entfernen. Huang [20] führte MD-Simulationen von Nano-Indentation auf einer einkristallinen Diamantmatrix durch und stellte fest, dass die Deformation von Diamantmaterial während der Indentation von der Keimbildung und Ausbreitung von 〈110〉 {111}-Versetzungsschleifen dominiert wurde. Sharma [21] konstruierte künstlich ein Hartpartikelmodell in einer Kupfermatrix und analysierte den Einfluss von Hartpartikeln auf die Entwicklung von Untergrunddefekten im Bearbeitungsprozess. Peng [22] untersuchte die Verstärkungsmechanismen von Graphenbeschichtungen auf Cu-Substraten durch Nano-Eindrückung, die aus dem durch die Grenzfläche erzeugten Spannungshomogenisierungseffekt resultiert. Aus der obigen Analyse ist ersichtlich, dass die bisherigen Studien zur Wirkung von unterirdischen Defekten hauptsächlich auf perfekten Kristallmaterialien oder künstlich konstruierten hypothetischen Defekten basieren, die weit entfernt von den tatsächlichen unterirdischen Defekten sind. Daher ist die realistische Konstruktion des Werkstückmodells mit unterirdischen Defekten unerlässlich, um den Einfluss von unterirdischen Defekten auf die mechanischen Eigenschaften des Werkstücks zu analysieren.
In diesem Artikel wurde die Nanoschneidmethode angewendet, um das Werkstückmodell mit unter der Oberfläche liegenden Defekten zu erhalten, die den praktischen Eigenschaften entsprechen. Auf dieser Grundlage wurde eine Nano-Indentation-Simulation durchgeführt, um den Einfluss von unterirdischen Defekten auf die mechanischen Eigenschaften von einkristallinem Kupfer zu untersuchen. Zunächst werden der Entstehungs- und Entwicklungsmechanismus von unterirdischen Defekten während des Nanoschneidprozesses diskutiert und die typischen Defektstrukturen des Werkstückuntergrunds nach dem Nanoschneiden analysiert. Zweitens wird der Wechselwirkungsmechanismus zwischen bearbeitungsinduzierten Untergrunddefekten und Versetzungskeimen während des Eindrückens analysiert. Drittens werden basierend auf den durch Nano-Indentation erhaltenen Last-Verschiebungs-Daten die Härte und der Elastizitätsmodul von einkristallinen Kupferproben berechnet. Abschließend werden einige neuartige Schlussfolgerungen zusammengefasst.
Methoden
Simulationsmodell
Um den Einfluss von unterirdischen Defekten auf die mechanischen Eigenschaften von Materialien in der Nanobearbeitung zu untersuchen, sollte das Probenmodell mit unterirdischen Defekten konstruiert werden. In dieser Forschung wird dies durch MD-Simulation des Nanoschneidprozesses realisiert. Zunächst wird das MD-Simulationsmodell erstellt und die Nano-Schneidprozesssimulation durchgeführt. Dann entspannten sich Probe und Schneidwerkzeug während der MD-Simulation ausreichend lange . Schließlich blieben einige stabile Defekte im Untergrund des Werkstücks. Die schematische Darstellung der dreidimensionalen MD-Simulationsmodelle ist in Fig. 1 gezeigt, in der das Nano-Schneidmodell in Fig. 1a und das Nano-Indentation-Modell mit Subsurface-Defekten in Fig. 1b gezeigt ist. In Abb. 1 sind die Materialien des Werkstücks und der Probe einkristallines Kupfer und das Werkzeug und der Eindringkörper sind Diamantmaterialien. Das Diamantwerkzeug mit Lichtbogenklinge wird im Nano-Schneidprozess verwendet und der Werkzeugkantenradius beträgt 3 nm. Der Eindringkörper hat eine halbkugelförmige Form im Nano-Indentationsprozess und der Durchmesser beträgt 6 nm. Das Werkstück und die Probe werden in drei Teile unterteilt, die Newton-Schicht, Temperaturschicht bzw. Grenzschicht sind. Um den Größeneffekt und den Grenzeffekt zu reduzieren, wird die periodische Grenzbedingung (PBC) in Richtung [010] des Simulationssystems übernommen. Um die anfängliche Wechselwirkung zwischen Werkzeug und Werkstück zu vermeiden, wird das Schneidwerkzeug 3 nm rechts oben am Werkstück und der Eindringkörper 6 nm bis zur Probe angesetzt. Die detaillierten Simulationsparameter sind in Tabelle 1 aufgeführt.
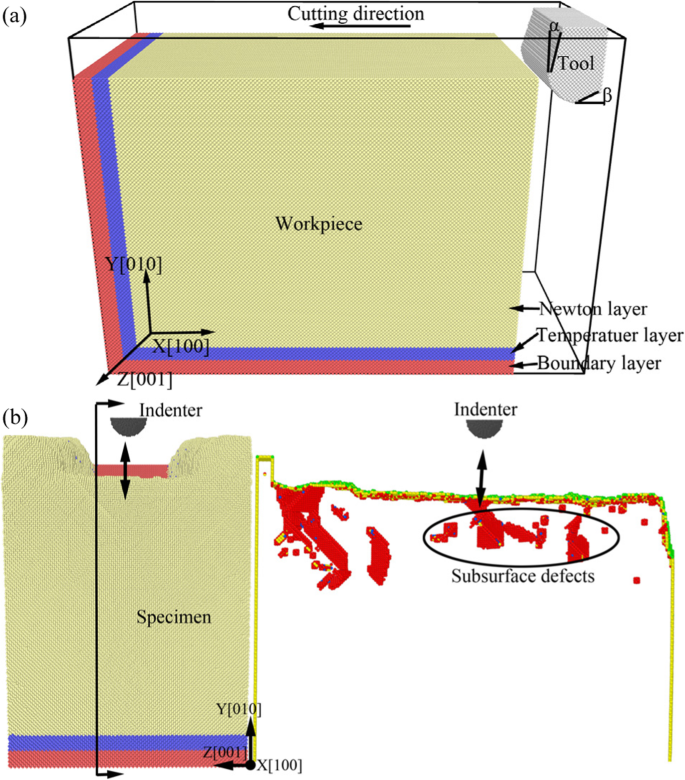
Schematische Darstellung von 3-D-MD-Simulationsmodellen von einkristallinem Kupfer für das Nanoschneiden und Nano-Eindrücken. a Das Modell für den Nano-Schneidprozess. b Das Modell für den Nano-Indentationsprozess mit unterirdischen Defekten
Interatomare Potentialfunktionen
In dieser Forschung wurden die dreidimensionalen MD-Simulationen mit einem großskaligen atomaren/molekularen massiv parallelen Simulator (LAMMPS) durchgeführt. Die parallele Berechnung wurde mit Hilfe der Message Passing Interface Library realisiert. Das Morse-Potential, das Embedded-Atom-Methode-(EAM)-Potential und das Tersoff-Potential werden in der Simulation verwendet, die vom LAMMPS-Softwarepaket aufgerufen werden. Die Wechselwirkung zwischen Cu-Atomen im Werkstück und C-Atomen im Werkzeug wird durch das Morsepotential berechnet, das in Gl. 1 [23].
$$ u\left({r}_{ij}\right)=D\left[\exp \left(-2\alpha \left({r}_{ij}-{r}_0\right)\right )-2\exp \left(-\alpha \left({r}_{ij}-{r}_0\right)\right)\right] $$ (1)wo r 0 , α , und D sind jeweils Atomabstand, Elastizitätsmodul und Bindungsenergie. Der Wert ist in Tabelle 2 aufgeführt.
Die interatomare Funktion zwischen Cu-Atomen im Werkstück wird durch das EAM-Potential beschrieben, das in Gl. 2, 3 [24, 25].
$$ E=\sum \limits_i^N\left[F\left({\rho}_i\right)+\sum \limits_{j>i}^Nu\left({r}_{ij}\right) \right] $$ (2) $$ {\rho}_i=\sum \limits_jf\left({r}_{ij}\right) $$ (3)Die Wechselwirkung zwischen Kohlenstoffatomen im Diamantwerkzeug wird durch das Tersoff-Potential berechnet, das in Gl. 4, 5 [26].
$$ E=\frac{1}{2}\sum \limits_{i\ne j}{V}_{ij} $$ (4) $$ {V}_{ij}={f}_c\left ({r}_{ij}\right)\left[{V}_R^{\hbox{'}}\left({r}_{ij}\right)+{b}_{ij}{V} _A\left({r}_{ij}\right)\right] $$ (5)wo f c (r ij ) ist die Trunkierungsfunktion zwischen Atomen, V A (r ij ) ist das duale Potential des Absorptionsterms, V R (r ij ) ist das duale Potential des Abstoßungsterms und r ij ist der Atomabstand zwischen Atom i und Atom j .
Fehleranalysemethoden
Beim Nanoschneiden von einkristallinem Kupfer bilden sich Verformungen und Versetzungen unter der Oberfläche des Werkstücks. In diesem Beitrag wird der Zentrosymmetrieparameter (CSP) eingeführt, um die Versetzungskeimbildung und die Defektentwicklung des Werkstücks zu analysieren. Für kubisch-flächenzentrierte (FCC) Materialien kann der CSP-Wert nach Gl. 6 [27].
$$ CSP=\sum \limits_{i=1}^6{\left|{R}_i+{R}_{i+6}\right|}^2 $$ (6)wo R ich gleichlange benachbarte Atome und R i+6 ist die entgegengesetzte Richtung Nachbaratome. Die CSP-Werte von FCC-Kristall, partieller Versetzung, Stapelfehler und Oberflächenatomen betragen 0, 2.1, 8.3 bzw. 24.9 [27].
Die CSP-Methode ist in der Lage, die atomare Staffelung zu identifizieren, kann jedoch den lokalen atomaren Kristallstrukturzustand des Werkstücks nicht erkennen. Daher wird die Common-Neighbor-Analyse (CNA) eingeführt, um den lokalen Kristallstrukturdefekt zu identifizieren. In der ursprünglichen CNA-Methode, vorgeschlagen von Honeycutt und Andersen [28], werden die verschiedenen Strukturen durch Diagramme dargestellt. Derzeit gibt es fünf Arten von CNA-Mustern in OVITO [29], bei denen die lokalen Kristallstrukturen als kubisch-flächenzentrierte (FCC), dichtgepackte hexagonale (HCP), kubisch raumzentrierte (BCC), ikosoedrische (ICO), und unbekannt bzw. In dieser Arbeit wird auch der Versetzungsextraktalgorithmus (DXA) [30] vorgestellt, um die Entwicklung von Versetzungsdefekten zu analysieren. Durch DXA werden die unterschiedlichen Kristallstrukturen im Werkstück mit unterschiedlichen Farben markiert und die Versetzungsfehler im Werkstück werden durch verschiedenfarbige Linien dargestellt.
Ergebnisse und Diskussion
Entwicklung von unterirdischen Defekten im Nanoschneidprozess
Beim Nano-Schneidprozess wird unter der Extrusions- und Scherwirkung des Schneidwerkzeugs auf das Werkstück das Werkstückoberflächenmaterial mit der Dicke der Schnitttiefe entfernt und eine neue bearbeitete Oberfläche mit einer bestimmten Maßgenauigkeit und Oberflächenqualität gebildet. Die komplexe elastisch-plastische Verformung einschließlich Spannungsverformung und thermischer Verformung tritt in der Oberfläche und im Untergrund des Werkstücks auf, die mit der Energieumwandlung und der Spannungskonzentration einhergeht. Daher wird die unter der Oberfläche liegende Schadensschicht gebildet und der Chip wird entfernt. Abbildung 2 zeigt die Sofortansichten der Entwicklung von Defekten unter der Oberfläche und des Materialabtrags während des Nanoschneidprozesses von einkristallinem Kupfer. In Abb. 2 sind die Atome durch den Wert der CSP- und CNA-Analyseergebnisse gefärbt. In Fig. 2a und c sind die gelben, grünen, roten und blauen Atome Oberflächenatome, Atome mit Oberflächendefekten, Atome mit Defekten unter der Oberfläche und FCC-Atome. Aus Fig. 2 ist ersichtlich, dass während des Nanoschneidprozesses viele typische Defektstrukturen im Untergrund des Werkstücks gebildet werden, wie Punktdefekte, Leerstellendefekte, Stapelfehler, Clusterdefekte, prismatische Versetzungen und Schraubenversetzungsschleifen.
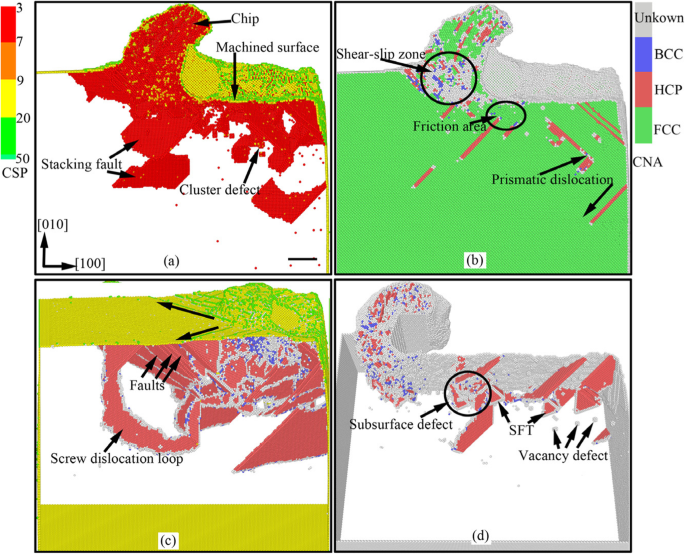
Sofortige Ansichten der Entwicklung von Defekten unter der Oberfläche während des Nanoschneidprozesses von einkristallinem Kupfer (Farbe online, Maßstabsbalken 5 nm). Die Schnittabstände von a , b , c , und d sind jeweils 18 nm, 18 nm, 6 nm und 32 nm
Durch die Quetsch- und Scherwirkung des Schneidwerkzeugs wird die Schubverformung für die Atome vor der Spanfläche erzeugt und die primäre Schubzone im Werkstück während des Nano-Schneidprozesses gebildet, wie in Abb 2b. Einige dieser Atome rutschen entlang der Spanfläche nach oben und der Schneidspan wird gebildet, wie in Fig. 2a gezeigt. Einige bewegen sich nach unten und die bearbeitete Oberfläche wird unter der Quetschreibung der Werkzeugflankenfläche gebildet, wie in Fig. 2b gezeigt. Andere bewegen sich nach innen und die unterirdischen Defekte werden gebildet, wie Stapelfehler, Clusterdefekte und prismatische Versetzungen, wie in Abb. 2a und b gezeigt.
Aufgrund der Reibung und Extrusion der Werkzeugflankenoberfläche tritt die Energieakkumulation für Atome in der Nähe der Flankenfläche auf und die Atome werden zu hochenergetischen Atomen. Wenn die Atomenergie ein bestimmtes Niveau überschreitet, wird die von energetischen Atomen getragene Energie freigesetzt und die Versetzung wird unter den treibenden energetischen Atomen gebildet. Daher werden viele Versetzungen im Reibungsbereich der Flankenfläche gebildet, wie in Fig. 2d gezeigt. Wenn die bearbeitete Oberfläche gebildet wird, bilden sich unter der Oberfläche Versetzungen, dehnen sich aus und vernichten sie. Schließlich verbleiben die Defektstrukturen wie Stapelfehler, SFT und Leerstellendefekte im Untergrund, wie in Fig. 2d gezeigt. Die Stapelfehler werden an der Schergleitzone unter dem Schneidwerkzeug nukleiert, dann in das Werkstück ausgedehnt und schließlich an der freien Oberfläche des Werkstücks vernichtet. Schließlich wird die Versetzungslinie an der Werkstückoberfläche gebildet. Und die Versetzungslinie wird entlang \(\left[\overline{1}0\overline{1}\right]\), \(\left[\overline{1}01\right]\) und [101] verlängert. Richtungen. Die Schneckenversetzungsschleife, die sich am Rand der Schergleitzone befindet, besteht aus mehreren Stapelfehlern und einer Reihe von Schneckenversetzungen. Die Schraubenversetzung entsteht unter dem Eintreiben des Druckspannungszustandes der Schub-Gleitzone [11].
Beim Nano-Schneidprozess werden die Versetzungen bekeimt und unter der Einwirkung des Schneidwerkzeugs ausgedehnt. Einhergehend mit der Aggregation und Freisetzung von Energie schwankt die Schnittkraft mit zunehmendem Schnittabstand, was in Fig. 3 dreidimensional dargestellt ist. In Abb. 3 sind die schwarze, rote bzw. blaue Kurve die Vorschubkraft (Fx), die Gegenkraft (Fy) und die Tangentialkraft (Fz). Aus Fig. 3 ist ersichtlich, dass der Schneidprozess in zwei Perioden unterteilt ist, nämlich die anfängliche Schneidstufe und die stabile Schneidstufe. Während der anfänglichen Schnittphase nehmen die Vorschubkraft und die Gegenkraft geradlinig schnell zu. Der Maximalwert der Vorschubkraft wird über 1100 nN erreicht, aber die Rückstellkraft liegt gerade bei 600 nN. Wenn die Werkzeugspitze vollständig in das Werkstück schneidet, wird die bearbeitete Oberfläche gebildet, die als erste kleine Grafik in Abb. 3 als Bearbeitete Oberfläche gekennzeichnet ist. Dann wird der Nano-Schneidprozess in eine stabile Schneidstufe überführt. Im stabilen Schneidzustand schwanken alle drei Kräfte in ihren Gleichgewichtspositionen. Die durchschnittliche Vorschubkraft liegt bei ca. 1000 nN und die durchschnittliche Gegenkraft beträgt nur ca. 500 nN. Aus Fig. 3 ist ersichtlich, dass die Vorschubkraft bei einem Schnittabstand von 20 nm schnell abnimmt. Dies liegt daran, dass die Energieakkumulation ein bestimmtes Niveau erreicht hat, das die kritische Gitterdehnungsenergie ist, die als zweites kleines Diagramm in Abb. 3 dargestellt ist. In der Zwischenzeit wird auf das Schneidwerkzeug ein großer Widerstand ausgeübt, der dazu führt, dass die Schnittkraft ein Spitzenwert. Dann wird die Energie freigesetzt, was zu einer Versetzungsemission führt, und die Schneidkraft wird verringert, wie als dritter kleiner Graph in Fig. 3 gezeigt. Daher schwankt die Schneidkraft während der stabilen Schneidephase. Die Keimbildung, Ausdehnung und Vernichtung von Versetzungen führte zu einer Schwankung der Schnittkraft und führte schließlich zu dem im Werkstück vorhandenen Untergrundfehler.
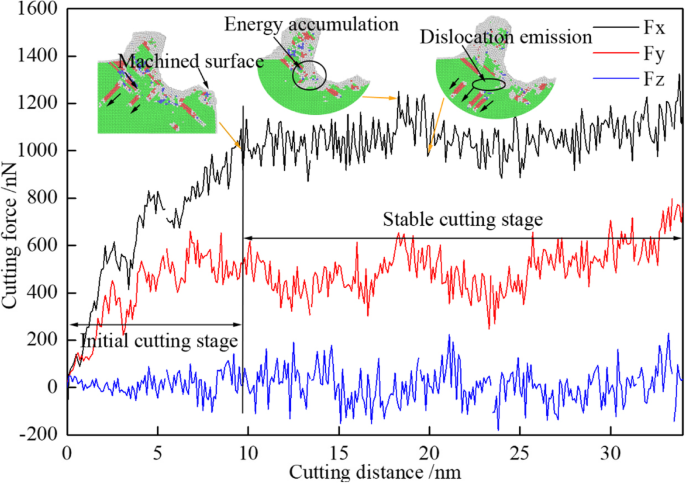
Die Variationskurve der Schnittkraft mit dem Schnittabstand (Farbe online). Die schwarzen, roten bzw. blauen Kurven sind die Vorschubkraft (Fx), die Gegenkraft (Fy) und die Tangentialkraft (Fz)
Um die Entwicklung und Emotion von Versetzungsdefekten im Untergrund des Werkstücks während des Nano-Schneidprozesses detailliert zu untersuchen, werden die Versetzungsverteilung und ihre Variation mit dem Schnittabstand durch die CNA-Methode genau analysiert. Die Entwicklung von Fehlern unter der Oberfläche des Werkstücks in einem bestimmten Bereich ist in Fig. 4 gezeigt, in der die Schnittabstände von Fig. 4a, b, c, d, e bzw. f 8 nm, 10 nm, 12 nm, 20 nm betragen , 24 nm und 32 nm. Aus Fig. 4a ist ersichtlich, dass viele Versetzungsdefekte in der Schergleitzone unter der Extrusionsscherwirkung des Schneidwerkzeugs während der Vorstufe des Schneidprozesses nukleiert werden. Insbesondere werden eine V-förmige Versetzung und eine Verwerfung unter der Antriebswirkung von atomarer Spannung und Energie in der Schergleitzone gebildet, wie in Fig. 4b gezeigt. Im anschließenden Bearbeitungsprozess wird die Scher-Gleitzone mit dem Schneidwerkzeug in Bewegung gehalten. Aufgrund der abnehmenden Deformationsenergie wird der Fehler allmählich vernichtet. Während sich das Schneidwerkzeug weiter vorwärts bewegt, wird die Freiflächenreibungszone in die Nähe der Verwerfung bewegt. Und die rauh bearbeitete Oberfläche wird unter der Extrusion und Reibung der Flankenfläche gebildet. Dann wird der Fehler weiter vernichtet und allmählich von der Werkstückoberfläche gelöst, wie in Fig. 4d gezeigt. Schließlich wird der Fehler in einen Cluster-Fehler umgewandelt, der ständig im Untergrund des Werkstücks vorhanden ist. In ähnlicher Weise entwickelt sich die gebildete V-förmige Versetzung unter der Interaktion von zwei Stapelfehlern und einer Versetzungssperre allmählich zu SFT. Diese stabilen Defekte setzen sich aus der unter der Oberfläche verformten Schicht zusammen, wie in Fig. 4e und Fig. 4f gezeigt
Entwicklung von Fehlern unter der Oberfläche des Werkstücks (Farbe online). Die Schnittabstände von a , b , c , d , e , und f sind jeweils 8 nm, 10 nm, 12 nm, 20 nm, 24 nm und 32 nm
Wie wir wissen, erfolgt die Restspannungsfreisetzung und die Behebung interner Fehler auf dem Werkstück nach der Alterungsbehandlung. Bei der tatsächlichen Nanofabrikation werden einige der während der Verarbeitung gebildeten unterirdischen Defekte nach dem Bearbeitungsprozess verschwinden. Um den Zustand des Werkstücks nach der Alterungsbehandlung zu simulieren, wird am Schneidsystem über längere Zeit eine molekulardynamische Relaxation durchgeführt. Das Verteilungsdiagramm von Restfehlern im Untergrund des Werkstücks nach MD-Relaxation für eine lange Zeit ist in Abb. 5 gezeigt, in der die Atome entsprechend den Analyseergebnissen durch CSP- und CNA-Methoden gefärbt sind. Aus Abb. 5 ist ersichtlich, dass die primären Versetzungen nach der Relaxation vernichtet werden. Die Leerstellendefekte, Stapelfehler, Atomcluster, prismatische Versetzung, Schraubenversetzung, SFT und Treppenstangenversetzung sind im Untergrund des Werkstücks vorhanden, wie in Abb. 5 gezeigt. Gemäß der obigen Analyse sind diese Defekte, die unter B. die Induktion komplexer Eigenspannungen und die Wechselwirkung von Versetzungsfehlern, beeinflusst die Maßhaltigkeit und Oberflächenqualität des Werkstücks nach der Nanobearbeitung.
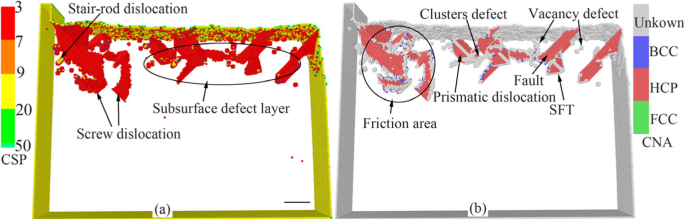
Verteilung von Restfehlern im Untergrund des Werkstücks nach Nanometer-Schneiden (Farbe online, Maßstabsbalken 5 nm). a Die gelben, grünen, roten und blauen Atome sind Oberflächenatome, Oberflächendefektatome, unterirdische Defektatome und FCC-Atome. b Die grünen, roten, grauen und blauen Atome sind FCC-, HCP-, unbekannte und BCC-Struktur
Nano-Eindrückungstest an Kupferproben mit bearbeitungsbedingten Defekten unter der Oberfläche
Die bearbeitungsbedingten Restfehler im Untergrund bestimmen die mechanischen Eigenschaften der Oberfläche, insbesondere die Härte und den Elastizitätsmodul. Daher scheint die Untersuchung der Nukleation und Wechselwirkung von Versetzungen während der Nanoindentation dringend erforderlich. Um den Einfluss der zerspanungsinduzierten Oberflächendefekte auf die mechanischen Eigenschaften von einkristallinem Kupfer zu untersuchen, wurde der Nano-Indentationsprozess an der Probe nach dem Nanoschneiden mit den gleichen Parametern wie die Nanoschneidsimulation in die Praxis umgesetzt. Das Simulationsergebnis ist in den Fign. 6, 7, 8, 9 und 10. Das momentane atomare Bild der Verteilung von Defekten unter der Oberfläche im Anfangszustand der Nanoeindrückung ist in Abb. 6 gezeigt. Aus der Abbildung ist ersichtlich, dass es mehrere SFTs gibt, eine V-förmige Versetzung, einige prismatische Versetzungen und einige Clusterdefekte unterhalb des Eindringkörpers. Diese Defekte unter der Oberfläche können die Versetzungskeimbildung und die Ausdehnung des Werkstücks während des Nano-Eindruckprozesses beeinflussen. Und dann werden die mechanischen Eigenschaften des Werkstückmaterials geändert.
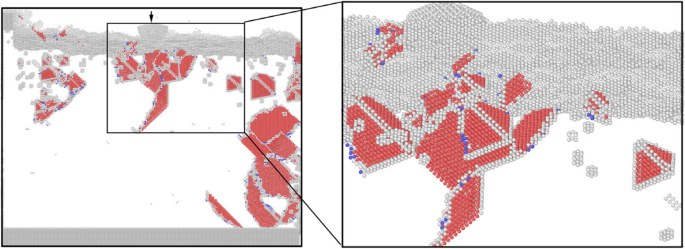
Fehlerverteilung unter der Oberfläche des Werkstücks im anfänglichen Eindruckzustand (Farbe online). Die roten, grauen und blauen Atome sind HCP, unbekannt und BCC-Struktur
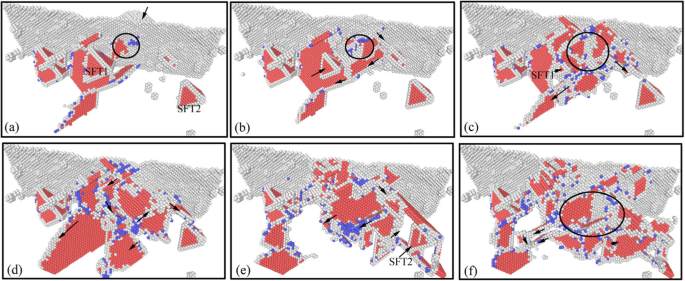
Entwicklung von Versetzungsdefekten unter der Oberfläche beim Ladeprozess der Nano-Eindrückung (Farbe online). Die entsprechenden Einrückungstiefen von a –f sind 0 nm, 0,5 nm, 1 nm, 2 nm, 3 nm bzw. 4 nm
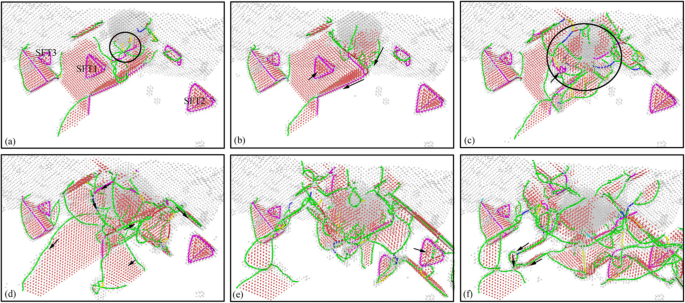
Verteilung von Untergrundversetzungen beim Belastungsprozess der Nanoindentation (Farbe online). Die entsprechenden Einrückungstiefen von a –f 0 nm, 0,5 nm, 1 nm, 2 nm, 3 nm bzw. 4 nm betragen. Farbschema:tiefblau für perfekte Luxationen, grün für Shockley-Dislokationen, pink für Stair-rod-Dislokationen, gelb für Hirth-Dislokationen, hellblau für Frank-Dislokationen und rot für nicht identifizierte Luxationen
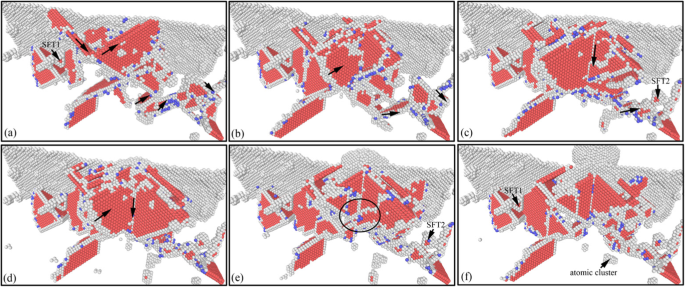
Entwicklung von unterirdischen Defekten beim Entladeprozess der Nano-Eindrückung (Farbe online). Die entsprechenden Einrückungstiefen von a –f sind 4 nm, 3 nm, 2 nm, 1 nm, 0 nm bzw. − 1 nm
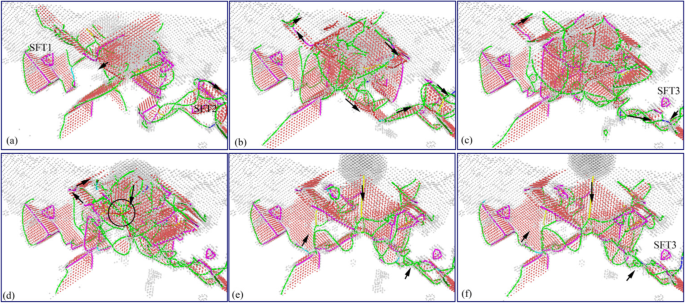
Verteilung von unterirdischen Versetzungen beim Entladevorgang der Nanoindentation (Farbe online). Die entsprechenden Einrückungstiefen von a –f sind 4 nm, 3 nm, 2 nm, 1 nm, 0 nm bzw. −1 nm. Farbschema:tiefblau für perfekte Luxationen, grün für Shockley-Dislokationen, pink für Stair-rod-Dislokationen, gelb für Hirth-Dislokationen, hellblau für Frank-Dislokationen und rot für nicht identifizierte Luxationen
Das Bild der atomaren Evolution von Versetzungen unter der Oberfläche während des Ladevorgangs mit Nanoindentation ist in Abb. 7 gezeigt. Aus Abb. 7a ist ersichtlich, dass die anfängliche Versetzungsnukleation auf der Oberfläche der Probe auftritt, wenn der Eindringkörper die Oberfläche des Probe. Durch den Abwärtsdruck des Eindringkörpers werden die nukleierten Versetzungen allmählich ausgedehnt. Unter dem Einfluss der vom Eindringkörper ausgeübten Spannung bildeten sich unterdessen eine große Anzahl von Versetzungen und bewegten sich entlang des Gleitsystems, wie in Fig. 7b gezeigt. Unter der Wechselwirkung zwischen neu gebildeten Versetzungen und ursprünglichen unterirdischen Defekten verschwinden einige einfache Defekte allmählich, und die V-förmigen Versetzungen entwickeln sich weiter und werden allmählich vernichtet. Die SFT unter dem Eindringkörper wird allmählich verringert, wie in Fig. 7c gezeigt. Während der Eindringprozess voranschreitet, nimmt das Ausmaß neuer nukleierter Versetzungsdefekte zu und die V-förmige Versetzung und SFT1 unter dem Eindringkörper verschwinden allmählich. Gleichzeitig entwickeln sich die während des Eindrückens gebildeten Versetzungsdefekte allmählich zu einer prismatischen Versetzungsschleife, in der Stapelfehler allmählich verschwinden, wie in Fig. 7d gezeigt. Die neu gebildete prismatische Versetzungsschleife erstreckt sich weiter bis SFT2 unten rechts am Eindringkörper. Aufgrund seiner stabilen Struktur bleibt der SFT2 während der Expansion der prismatischen Versetzungsschleife unverformt, wie in Fig. 7e gezeigt. Wenn der Eindringkörper nach unten drückt, dehnt sich die prismatische Versetzungsschleife weiter nach unten aus, und das Ausmaß der Versetzungsdefekte im Untergrundbereich nimmt allmählich zu. Die SFT2-Struktur existiert stabil im Untergrund der Probe und ändert sich während der Bewegung und Interferenz der Versetzungsdefekte nicht, wie in Fig. 7f gezeigt.
Um die Entwicklung und Verteilung von Fehlern unter der Oberfläche während des Eindruckprozesses klarer zu zeigen, wird die DXA-Methode verwendet, um die Probe nach dem Eindruck zu analysieren. Das Bild der unterirdischen Versetzungsverteilung zu jedem Zeitpunkt entsprechend Abb. 7 wird durch DXA-Analyse erhalten, wie in Abb. 8 gezeigt. Versetzungen werden nach folgendem Schema eingefärbt:tiefblau für perfekte Versetzungen, grün für Shockley-Versetzungen, rosa für Stair-rod Luxationen, gelb für Hirth-Dislokationen, hellblau für Frank-Dislokationen und rot für nicht identifizierte Luxationen.
Aus Fig. 8 ist ersichtlich, dass der Werkstückuntergrund im anfänglichen Eindruckzustand hauptsächlich aus Shockley-Versetzung und Stair-Rod-Versetzung besteht. Die im Untergrund vorhandene SFT ist eine regelmäßige tetraedrische Struktur, die aus sechs treppenförmigen Versetzungen besteht. Wenn der Eindringkörper das Werkstück berührt, sind die Versetzungskeime auf der Werkstückoberfläche gelbe Hirsh-Versetzungen, wie in Fig. 8a gezeigt. Beim Niederdrücken des Eindringkörpers wird eine große Anzahl von Versetzungen nukleiert und entlang des Gleitsystems bewegt. Die gelben Hirsh-Dislokationen gehen allmählich in grüne Shockley-Dislokationen über, wie in Abb. 8b gezeigt. Unter der Wechselwirkung zwischen neu gebildeten Versetzungen und der ursprünglichen SFT1 verschwinden einige einfache Versetzungen allmählich, wie in 8c gezeigt. Das Ausmaß der unterirdischen Versetzungen nimmt mit fallendem Eindringkörper zu, und die neu gebildeten Versetzungen sind hauptsächlich grüne Shackley-Versetzungen. Die Wechselwirkung zwischen Shockley-Dislokationen und SFT1 führt zu einer allmählichen Abnahme der Größe von SFT1 und schließlich zum Verschwinden von SFT1, wie in 8d gezeigt. Mit zunehmender Größe der Defekte nehmen Anzahl und Art der Versetzungen im Untergrund der Probe zu. Es gibt rote unbekannte Arten von Versetzungen, die im Untergrund gebildet wurden, und mehrere Shockley-Versetzungen bildeten die Prismenversetzungsschleife, wie in 8e gezeigt. Unter der Wechselwirkung der Shockley-Dislokation und der Stair-Rod-Dislokation verschwanden die SFT2 und SFT3 weit von der Eindringregion nicht zuletzt aufgrund der schwächeren Extrusion des Eindringkörpers, wie in Abb. 8f gezeigt.
Das Bild der Entwicklung der Versetzung unter der Oberfläche während des Entladevorgangs durch Nano-Eindrückung ist in Abb. 9 gezeigt. Abbildung 10 zeigt das in Abb. 9 entsprechende Verteilungsbild der Versetzung unter der Oberfläche zunächst und nimmt dann während des Vorgangs der Aufwärtsbewegung des Eindringkörpers allmählich ab. Sie entsteht durch die umfassende Funktion zwischen kontinuierlicher Freisetzung der Materialverformungsenergie und der vom Eindringkörper auf die Probe ausgeübten Adhäsionskraft. In der Anfangsphase des Entladevorgangs ist die nach oben gerichtete Adsorptionskraft des Eindringkörpereffekts auf die Probe nicht signifikant. The evolution of subsurface defect is mainly driven by the material deformation energy, which results in the scale of subsurface defects increase. And the main types of dislocations in the stage are the green Shockley dislocation and the pink ladder dislocation, as shown in Figs. 9a, b and 10a, b. The interaction between the SFT2 and Shockley dislocation nearby makes pink stair-rod dislocation turn into green Shackley dislocation in the area far away indenter action. Meanwhile, the SFT2 is transformed into a smaller defect which is SFT3, as shown in Figs. 9c and 10c. With the continuous lifting of the indenter, the bonding and adsorbing effect exerted by the indenter on the specimen increases gradually. Accompany with the deformation energy release, the size and types of dislocations in subsurface increase. And more perfect dislocations, Hirh dislocations, and unknown dislocations are formed, as shown in Figs. 9d and 10d. In later stage of unloading process, the material deformation energy is basically released, and the evolution of subsurface defects is dominated by the adsorption from the indenter. Therefore, the subsurface defects are annihilated rapidly, and the scale of subsurface defects decreases rapidly. And a typical Hirsch dislocation is formed in the direction of the indenter upward, which is shown in Figs. 9e, f and 10e, f. Finally, the scale of subsurface defects decreases considerably, and some typical subsurface defects, such as SFT and atomic clusters, are gradually disappeared. From the above analysis, it can be seen that secondary processing (nano-indentation) can restore the typical internal defects formed in nano-cutting, and the subsurface damage becomes more serious in the secondary processing area. These characteristics of subsurface defects will affect the mechanical properties of materials. Hence, it is necessary to study the effect of subsurface defects on the mechanical properties of material.
Mechanical properties of materials can be calculated by load-displacement curve, such as hardness, elastic modulus, and yield strength. In this study, hardness and Young’s modulus of single crystal copper were investigated. The variation of load on the indenter was monitored during the nano-indentation process, and the load-displacement curve of the nano-indentation process was drawn, as shown in Fig. 11. The max indentation depth of the red and black curves respectively is 2 nm and 3 nm, in which both loading and unloading processes are included. The upward direction of load is defined as positive direction, so the load-displacement curves are all above the zero line in the process of loading, while the load on the indenter changes from positive to negative during unloading. The elasticity restore of deformed matrix material exerts an upward force on the indenter. Therefore, in order to keep the indenter raising in uniform speed, a downward force (positive) is required. With the gradual recovery of deformation, the force gradually decreases until it disappears. Then the force applied on the indenter becomes negative, and the absolute value of the force first increases and then decreases. From the graph, it can be seen that the specimen is in the stage of elastic deformation during loading process, and the load increases in proportion to the displacement. When the displacement of the indenter is 1 nm, the load on the indenter is fluctuated dramatically, as indicated by the arrow on the left side of Fig. 11. This is because that the indenter is pressed down to the SFT1 shown in Fig. 7, which results in the greater impediment to the indenter. When the indenter displacement is in the range of 2 to 3 nm, the fluctuation amplitude of the load increases. This is because the indenter is pressed down to the SSD layer, and the impediment of the indenter to the subsurface defect in the specimen is more significant, so the fluctuation amplitude of the load increases significantly.
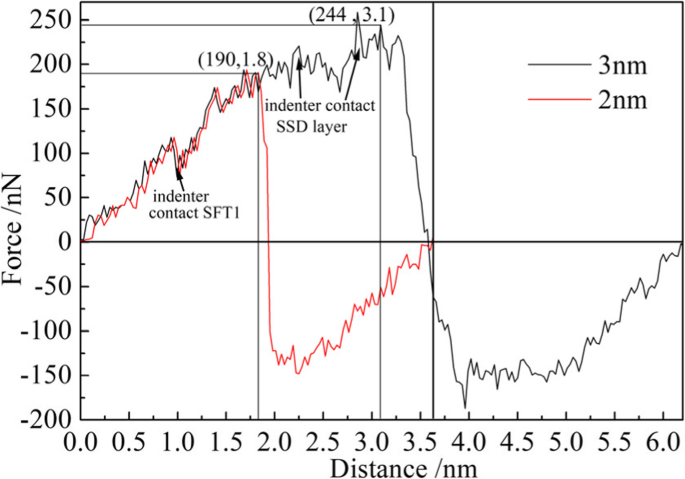
Load-displacement curve of nano-indentation on the machining-induced specimen (color online). The maximum indentation depth of the black curve and the red curve respectively is 3 nm and 2 nm
According to Oliver-Pharr Method [31], nano-indentation hardness can be defined as indentation load divided by the contact area between indenter and specimen, which is calculated by Eq. 7.
$$ H={F}_{\mathrm{max}}/{A}_c $$ (7)In which, F max is the peak value of the load. A c is projected contact area for indenter and specimen, which can be obtained by
$$ {A}_c=\pi {r}^2 $$ (8)wo r is contact radius for indenter. Because the indenter is hemispherical in shape, r is approximately equal to indentation depth.
The elastic deformation of single crystal copper material is caused by the load exerted from indenter. Based on the previous load-displacement curve, Young’s modulus (E ) of single crystal copper can be calculated by Eq. 9.
$$ E=\frac{\sigma }{\varepsilon }=\frac{F/S}{DL/L}=\frac{F/\pi {r}^2}{DL/L} $$ (9)wo F is applied load, S is contact area, r is projection radius of indenter, DL is material deformation along loading direction, which is equal to indentation depth, and L is the total length of material along loading direction. In this study, L is equal to 30 nm.
According to the Oliver-Pharr method and load-displacement data, nano-indentation hardness and Young’s elastic modulus of single crystal copper materials with subsurface defects can be calculated based on Eqs. 7, 8, 9. Table 3 shows the applied load acting on the specimens by indenter with different indentation depths.
The nano-indentation hardness of single crystal copper can be calculated by Eqs. 7 and 8 combining the data in Table 3. When the maximum depth is 2 nm, F max =190.67 nN and from Fig. 11 r =2.75 nm. The calculated value of nano-indentation hardness H2 is 8.029 GPa. When the maximum depth is 3 nm, F max =244.66 nN and r =3 nm. The calculated value of nano-indentation hardness H3 is 8.675 GPa, which is slightly larger than it obtained at indentation depth of 2 nm. It is because the indenter is pressed down to the subsurface defects area at indentation depth of 3 nm, and the deformation resistance of the subsurface defects increases. Therefore, the hardness of the single crystal copper increased. It can be concluded from the result that the subsurface defects make the machined surface much harder, which is work-hardening phenomenon.
The Young’s modulus E of single crystal copper can be calculated by Eq. 9 combining the data in the Table 3. The calculation results are shown in Table 4. It can be noted that the Young’s modulus becomes distinctly higher when the indentation depth is smaller than 1.5 nm. In the initial stage of nano-indentation, the indenter does not contact the defects residual area in subsurface. However, the work-hardening effect makes the specimen material not easily be occurred elastic deformation; therefore, the Young’s modulus of single crystal copper is larger in the initial stage of indentation. The value of Young’s modulus is 119.4 GPa when indentation depth is 2 nm, which is almost the same with Zhang’s research (120.4 GPa) [14]. With the increase of indentation depth, the Young’s elastic modulus of single crystal copper specimens decreases gradually, and the ability of materials to resist elastic deformation is weakened. It is due to the permanent elastic deformation is derived from the dislocation motion and its interaction with subsurface defects. It has been revealed that the nano-cutting-induced subsurface defects will affect the physical and mechanical properties of single crystal copper materials, which is also applicable to other FCC materials. The existence of subsurface defects will enhance the hardness of machined surface and weaken the ability of material to resist elastic deformation, in which the mutual evolution between dislocations and subsurface defects plays an important role. Therefore, it is very important to predict the thickness of subsurface deformation layer and study the surface properties for nano-fabrication.
Schlussfolgerungen
The subsurface defects stable exist in workpiece after nano-cutting can affect the mechanical properties, which is critical to the service performance and life of nano-structures. The previous studies are mainly based on perfect crystal materials or artificial constructing hypothetical defects, which is far from the actual subsurface defects. In this paper, molecular dynamics simulation of nano-cutting is performed to construct the specimen model with subsurface defects. Based on the built MD model, nano-indentation simulation is carried out to study the influence of machining-induced subsurface defects on the physical and mechanical properties of single crystal copper materials. The interaction mechanism between dislocation and complex defects during nano-indentation is studied. The nano-indentation hardness and Young’s elastic modulus of single crystal copper materials are calculated. Based on the above analysis, some interesting conclusions can be drawn as follows.
- 1.
The dislocation nucleation and expansion in workpiece subsurface are driven by the extrusion and shearing action of cutting tool during the nano-cutting process, which results in the fluctuation of cutting force. After nano-cutting, there are stable defect structure residues in the subsurface of workpiece, such as vacancy defects, stacking faults, atomic clusters, SFT, and stair-rod dislocations, which together constitute the subsurface defect layer of workpiece.
- 2.
The existence of subsurface defects affects the nucleation and expansion of dislocations during nano-indentation process. Some stable defects directly below the indenter, such as V-shaped dislocation and SFT1, are annihilated after indentation. And SFT2 far from the indentation region is transformed into a smaller one. Secondary processing of nano-indentation can restore typical internal defects of the workpiece, but the subsurface defects in the secondary processing area are aggravated.
- 3.
The nano-indentation hardness of specimens increases with the introduction of subsurface defects, which results in the formation of work-hardening effect. The Young’s modulus of single crystal copper is larger in the initial stage of indentation and gradually decreases with the increase of indentation depth. The existence of subsurface defects can weaken the ability of material to resist elastic deformation, in which the mutual evolution between dislocations and subsurface defects plays an important role.
Verfügbarkeit von Daten und Materialien
The conclusions made in this manuscript are based on the data which are all presented and shown in this paper.
Abkürzungen
- MD:
-
Molecular dynamics
- SSD:
-
Subsurface defects
- SFT:
-
Stacking fault tetrahedral
- PBC:
-
Periodic boundary condition
- LAMMPS:
-
Large-scale atomic/molecular massively parallel simulator
- EAM:
-
Embedded-atom method
- CSP:
-
Centro-symmetry parameter
- FCC:
-
Face center cubic
- CNA:
-
Common neighbor analysis
- HCP:
-
Close-packed hexagonal
- BCC:
-
Body centered cubic
- ICO:
-
Icosohedral
- DXA:
-
Dislocation extract algorithm
Nanomaterialien
- Die Entwicklung des Marktes für 3D-Druckmaterialien:Trends und Chancen im Jahr 2019
- Die Entwicklung von SLS:Neue Technologien, Materialien und Anwendungen
- Wie bewerten Ingenieure Kunststoffmaterialien und Materialfestigkeit?
- Nanostrukturiertes Siliciumdioxid/Gold-Cellulose-gebundenes Amino-POSS-Hybrid-Komposit über den Sol-Gel-Prozess und seine Eigenschaften
- Die Wirkung von Kontakt-Nichtgleichgewichtsplasma auf die strukturellen und magnetischen Eigenschaften von Mn Х Fe3 − X О4 Spinellen
- Paramagnetische Eigenschaften von Fulleren-abgeleiteten Nanomaterialien und ihren Polymerverbundstoffen:Drastischer Pump-Out-Effekt
- Eigenschaften technischer Werkstoffe:Allgemeines, Physikalisches und Mechanisches
- Liste von 14 verschiedenen mechanischen Eigenschaften von Materialien
- Eigenschaften von Stahlmaterialien und Werkzeugen, die für Stanzen verwendet werden
- Verschiedene Arten von mechanischen Materialeigenschaften