Molekulardynamikstudie zur spitzenbasierten Nanobearbeitung:Ein Rückblick
Zusammenfassung
Ansätze der spitzenbasierten Nanobearbeitung (TBN) haben sich als leistungsfähige und praktikable Technik zur Herstellung von Mikrostrukturen erwiesen. Die Molekulardynamik (MD)-Simulation wurde im TBN-Ansatz weit verbreitet eingesetzt, um den Mechanismus zu erforschen, der durch Experimente nicht vollständig aufgeklärt werden konnte. Dieses Papier gibt einen Überblick über die jüngsten wissenschaftlichen Fortschritte bei der MD-Simulation des TBN-Ansatzes. Zunächst werden die sich etablierenden Methoden des Simulationsmodells für verschiedene Materialien vorgestellt. Anschließend wird die Analyse des Bearbeitungsmechanismus für den TBN-Ansatz diskutiert, einschließlich der Schnittkraftanalyse, der Analyse des Materialabtrags und der Fehleranalyse im Untergrund. Abschließend werden aktuelle Mängel und Zukunftsaussichten der TBN-Methode in MD-Simulationen aufgezeigt. Es ist zu hoffen, dass diese Überprüfung eine gewisse Referenz für die Folgeforschung bieten kann.
Einführung
Mikro-/Nanofertigungstechnologie wird in verschiedenen Bereichen, einschließlich Umwelt, Energie, Biologie, Medizin, Landesverteidigung und anderen Bereichen, weit verbreitet eingesetzt, was eine immer wichtigere Rolle bei der Förderung der nationalen Entwicklung und des sozialen Fortschritts spielt [1,2,3,4] . Um eine hochpräzise Mikro-/Nanofertigung zu realisieren, bietet der auf Rasterkraftmikroskopie (AFM) basierende mechanische Bearbeitungsansatz, der als TBN bekannt ist, eine einfache Ausrüstung und Bedienung, eine Bearbeitungsgenauigkeit im Nanobereich mit geringen Umgebungsanforderungen und hat sich als leistungsstark und machbar erwiesen Ansatz zur Herstellung von Mikrostrukturen [5, 6]. Bislang wurden Nanopunkte, Linien/Rillen, zweidimensionale (2D)/dreidimensionale (3D) Strukturen und sogar Nanostrukturen auf gekrümmten Oberflächen, die als Hauptkomponenten von Nanogeräten bekannt sind, bereits erfolgreich mit der TBN-Methode hergestellt [7].
Um Nanostrukturen mit höherer Präzision herzustellen, ist ein tiefes Verständnis des Bearbeitungsprozesses von TBN-Verfahren erforderlich. Viele Wissenschaftler haben den Mechanismus des TBN-Ansatzes mit Experimenten in verschiedenen Materialien wie Metallen [8], Halbleitern [9, 10] und Polymeren [11] untersucht. Es ist jedoch schwierig, den inneren Mechanismus von TBN-Ansätzen experimentell weiter zu untersuchen. Die Molekulardynamik (MD)-Simulation hat sich als leistungsfähiges Werkzeug zur Erforschung des Nanobearbeitungsprozesses erwiesen, der durch Experimente nicht vollständig aufgeklärt werden konnte [12, 13]. Im Vergleich zur experimentellen Methode kann die MD-Methode den mikroskaligen Mechanismus des Materialabtrags und der Oberflächenerzeugung durch die Analyse von Schnittkräften, Spannungszustand, Energiedissipation und Oberflächentopographie besser erklären [12].
In der Vergangenheit haben einige Wissenschaftler bereits die MD-Simulationstechnologie verwendet, um die TBN-Prozesse zu untersuchen. Fanget al. untersuchten die Auswirkungen des Ritzvorschubs und des Konuswinkels auf den Nanolithographieprozess [14, 15]. Isono und Tanaka analysierten die Auswirkungen von Temperatur, Bearbeitbarkeit und interatomaren Kräften des Nickelmetalls [16, 17]. Yanet al. untersuchten die Spitzengeometrieeffekte in AFM-basierten Lithographieprozessen [18]. Derzeit wurden einige neuartige TBN-Prozesse mit MD-Simulationen untersucht. Xiaoet al. verglichen den Unterschied zwischen statischer Pflugmethode und dynamischer Pflugmethode und fanden heraus, dass kleinere Nanostrukturen mit dynamischer Pflugmethode hergestellt werden konnten [19]. Geng et al. haben MD-Simulationen des lastgesteuerten Nanoscratching durch direktes Anlegen einer konstanten Normallast an der Sonde durchgeführt [20]. Um Nanorillen mit höherer Dichte herzustellen, sollte der Mindestvorschub (MF) untersucht werden. Renet al. präsentierten einen neuartigen Ansatz, der ein Grob-zu-Fein-Kriterium zur Bestimmung der MF unter Verwendung von MD-Simulationen beinhaltet [21]. Die Ergebnisse zeigen, dass MF mit hoher Genauigkeit erhalten wird. In der vorherigen Übersichtsarbeit [12, 13, 22, 23, 24] sind diese neuen Fortschritte der MD-Simulationstechnologie, die für den TBN-Prozess verwendet wird, jedoch nicht enthalten. Daher konzentrieren wir uns in diesem Aufsatz auf den neuesten Stand der Technik der MD-Simulation für TBN-Methoden. Zunächst werden die Modellierungstechnologien in verschiedenen Materialien und neuartige Bearbeitungsverfahren diskutiert. Anschließend wird der Mechanismus der TBN-Methoden untersucht, einschließlich der Schnittkraftanalyse, der Analyse des Materialabtrags und der Fehleranalyse im Untergrund. Schließlich werden in diesem Überblick auch die verbleibenden Herausforderungen und die Zukunftsaussichten bei der MD-Simulation von TBN gegeben.
Simulationsmethoden
Um genaue Vorhersageergebnisse zu erhalten, ist es notwendig, das Simulationsmodell und die zugehörige Verarbeitungskonfiguration zu optimieren. Das Simulationsmodell enthält hauptsächlich atomare Konfiguration und Potentialfunktion. Die atomare Konfiguration kann in kristalline und amorphe Strukturen eingeteilt werden. Die Atome in kristallinen Materialien wie Kupfer, Eisen, Silizium usw. sind regelmäßig und geordnet angeordnet und die amorphen Materialien wie Polymere bestehen aus unregelmäßigen Molekülketten. Das Materialverhalten im Nanobereich wird in MD-Simulationen durch Potentialfunktionen dargestellt und verschiedene Potentialfunktionen wurden vorgeschlagen und verwendet, um das Materialverhalten in atomistischen Simulationen zu simulieren. Außerdem sollte auch die Bearbeitungskonfiguration berücksichtigt werden, wie beispielsweise die verschiedenen Bearbeitungsbedingungen und Bearbeitungsansätze. In den folgenden Abschnitten werden die Methoden der Modellerstellung und die Verarbeitungskonfiguration vorgestellt.
Aufstellung des MD-Modells
Die innere atomare Konfiguration kristalliner Materialien ist unterschiedlich, wie Kupfer (kubisch flächenzentriert), Eisen (kubisch raumzentriert), Titan (dichtes Hexagonal) und Silizium (Diamantstruktur) [27, 28]. Die meisten kristallinen Materialien liegen in Form einer einkristallinen und polykristallinen Struktur vor. Der Einkristall-Feststoff weist eine atomare Struktur auf, die sich ohne Defekte über sein gesamtes Volumen periodisch wiederholt. Durch Duplizieren der Elementarzelle in allen drei Raumrichtungen kann das Einkristallmodell leicht erstellt werden [13]. Bei der Erstellung eines atomaren MD-Modells sollten die verschiedenen Oberflächenorientierungen berücksichtigt werden, die die Bearbeitungseigenschaften des Werkstücks beeinflussen können [29,30,31]. Die polykristalline Struktur weist die Struktur mit unterschiedlichen Korngrößen auf, die nach der Voronoi-Tessellationsmethode konstruiert wurde [32]. Nanotwined (NT)-Material ist eine Art Sonderstruktur aus polykristallinem Material, das aufgrund seiner hervorragenden mechanischen Eigenschaften, wie ultrahohe Festigkeit, gute Duktilität und hohe Bruchzähigkeit, an Bedeutung gewonnen hat [33,34,35,36] . In dieser Übersicht wird die Methode zum Aufbau von NT polykristallinem Cu als Beispiel gegeben [25]:Zuerst wird eine Multilayer, die aus mehreren einkristallinen Cu-Schichten gleicher Dicke besteht, aufgebaut und TB bildet sich zwischen benachbarten Schichten. Zweitens wird der Winkel jedes Korns berechnet. Schließlich wird NT polykristallin mit periodischen Randbedingungen unter Verwendung der Voronoi-Konstruktion erzeugt, die die Multischicht und den erhaltenen Kornwinkel aufnimmt. Abbildung 1a zeigt die Atomkonfigurationen von Kupfer einschließlich singulärem kristallinem Cu, polykristallinem Cu und NT polykristallinem Cu, in denen Atome durch den gemeinsamen Nachbarn gefärbt sind.
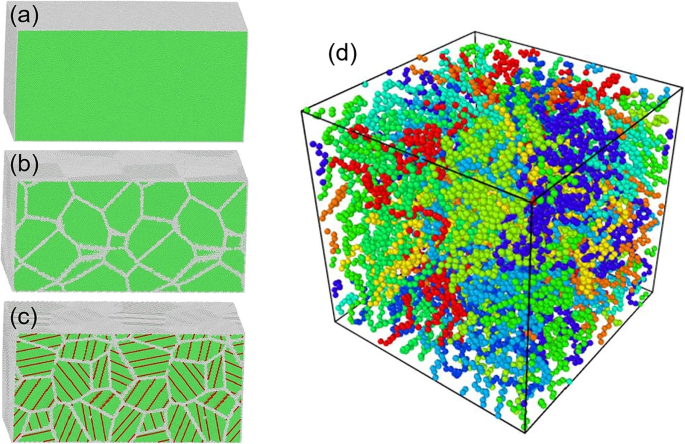
a Mikrostruktur von einkristallinem Cu. b Mikrostruktur von Nanopolykristallin. c Mikrostruktur von NT polykristallin. Atome werden nach CNA-Werten gefärbt, da Grün und Weiß für FCC- und Defektatome stehen [25]. d Das äquilibrierte United-Atom-Modell von amorphem PE, das Modell wurde durch verschiedene Molekülketten gefärbt [26]
In früheren Studien wurde das Polymer mit einem generischen grobkörnigen Modell modelliert [37, 38]. Zum Beispiel werden die Details zur Etablierung des Modells von Polyethylen (PE) wie folgt angegeben [39]:(i) Das ursprüngliche PE-System mit 10 Molekülketten wurde unter Verwendung des selbstvermeidenden Random-Walk-Algorithmus von Monte Carlo erhalten [39]; (ii) das erste Atom jeder Kette wurde zuerst an einer verfügbaren Stelle des Gitters eingefügt und dann begann die Molekülkette basierend auf einer probabilistischen schrittweisen Weise entsprechend der Bindungslänge und den unbesetzten Stellen in der Zelle in einer bestimmten Richtung zu wachsen .; (iii) sobald die Anfangsdichte angegeben ist, wird die Größe der Simulationsbox bestimmt. In unserer Simulation betrug die Größe der anfänglichen Simulationsbox etwa 80,06 × 80,06 × 80,06 Å 3 für das System bestehend aus 10 PE-Ketten. Das MD-Modell von PE ist in Abb. 1d dargestellt.
Die Spitzengeometrie ist im Allgemeinen komplex und variabel, einschließlich der Kegelform [40], der dreieckigen Pyramide [18] und der Halbkugel (stumpfe Form) [21], die beim TBN-Prozess eine wichtige Rolle spielt. Insbesondere stimmt die Form des Pyramidenwerkzeugs im MD-Modell mit der beim AFM-Bearbeitungsprozess überein und das kugelförmige Werkzeug stimmt mit dem Schleifkorn beim Schleifprozess überein; Somit kann der Bearbeitungsmechanismus besser erklärt werden, indem die Simulationsergebnisse mit den experimentellen Ergebnissen verglichen werden. In den meisten Fällen wird die Spitze als unendlich starr angesehen, was dadurch erreicht wird, dass die relativen Positionen der Atome konstant gehalten werden und sich mit konstanter Geschwindigkeit fortbewegen [41].
Entscheidend ist auch die Auswahl geeigneter potentieller Energiefunktionen, die die Glaubwürdigkeit der Simulationsergebnisse bestimmen [21]. EAM ist ein für metallische Systeme geeignetes Mehrkörperpotential [24]. Es bietet eine realistischere Beschreibung des metallischen Zusammenhalts und vermeidet Mehrdeutigkeiten, die durch die Volumenabhängigkeit geerbt werden, die verwendet wird, um die Wechselwirkung zwischen Metallatomen wie Kupfer [42] und Eisen [43] zu beschreiben. Für die Modellierung von Materialien mit diamantkubischer Struktur haben sich die Tersoff- [44] und Stillinger-Weber (SW) [45]-Potentiale als besonders geeignet erwiesen. Um den Mechanismus von Si im TBN-Prozess zu untersuchen, sollten der Versetzungsschlupf und die Phasenumwandlung in MD-Simulationen beobachtet werden. Im Vergleich zum Tersoff-Potential bietet das SW-Potential nicht nur genügend Flexibilität, um eine Reihe verschiedener Siliziumkonfigurationen zu beschreiben, sondern liefert auch die beste Übereinstimmung mit den Ergebnissen der Ab-initio-Versetzungsnukleation in defektfreiem Silizium [46, 47]. Somit hat die SW-Potentialfunktion möglicherweise mehr Potenzial, um die Wechselwirkung zwischen Siliziumatomen zu beschreiben. Potentiale der analytischen Bindungsordnung (ABOP), der reaktiven empirischen Bindungsordnung (REBO) und der adaptiven intermolekularen reaktiven empirischen Bindungsordnung (AIREBO) sind eine Klasse von Potenzialen, die die Potenzialfunktion von Tersoff gemäß der engen Bindungsnäherung erweitern und auf fundamentalen Größen beruhen [ 48]. Das ABOP-Potenzial ist ideal für die Wechselwirkungen zwischen den Atomen von Silizium und Kohlenstoff, das zur Untersuchung der Materialverformung und des Abtragsverhaltens im Prozess von SiC genutzt wird. Das REBO-Potenzial ist besonders beliebt bei Simulationen von Kohlenstoff und Kohlenstoffnanoröhren. Das AIREBO-Modell wurde entwickelt, um die Unzulänglichkeiten der REBO-Potenzialfunktion zu überwinden, indem es eine genauere Näherung als die der REBO-Terme bietet und auch Möglichkeiten zur Modellierung komplexerer Wechselwirkungen bietet [41]. Die intermolekularen und intramolekularen Wechselwirkungen in der Polystyrolprobe werden durch das gut etablierte AIREBO-Potential beschrieben [49].
Die meisten MD-Simulationen wurden mit dem Large-scale Atomic/Molecular Massively Parallel Simulator (LAMMPS) durchgeführt [50]. Einige komplexe Werkstückmodelle wie polykristalline und nanotwined polykristalline Materialien könnten mit Atomsk durchgeführt werden [51]. Die Konstruktion von Polymeren, einschließlich Atomen, Bindungswinkeln, unechten und ihren verschiedenen Typen, werden aus der von Material Studio (MS) generierten Datendatei erhalten [52]. Sowohl Open Visualization Tool (OVITO) [53] als auch Visual Molecular Dynamics (VMD) [54] sind nützliche Werkzeuge, um das Modell oder den Bearbeitungsprozess zu visualisieren.
Durch den Einsatz von MD-Simulationen konnten verschiedene Materialmodelle effektiv erstellt werden. Die meisten Werkstückmodelle sind jedoch kleiner als 50 nm × 50 nm × 50 nm, was zu Abweichungen von den tatsächlichen Ergebnissen führen kann [40, 55, 56]. Außerdem fehlt es noch an potentiellen Funktionen, die einige Materialien wie GaAs und Lu2 . effektiv beschreiben könnten O3 . Daher müssen MD-Modelle und zugehörige potenzielle Funktionen noch optimiert werden, um den Simulationsprozess genauer zu beschreiben.
Verarbeitungskonfiguration
Bei TBN-Experimenten wird der belastungsgesteuerte Modus normalerweise durch Aufbringen einer konstanten Normallast auf die Spitze durchgeführt. Es hat sich gezeigt, dass dieser Modus von höherer Präzision ist, insbesondere bei der Durchführung von Nanobearbeitungen auf geneigten oder gekrümmten Oberflächen. Viele MD-Simulationen von TBN-Prozessen werden jedoch im Displacement-Controller-Modus durchgeführt, was zu Unterschieden zwischen Simulation und Experiment führen kann [18, 57]. Daher haben einige Wissenschaftler eine MD-Simulation eines lastgesteuerten Nanoscratching-Prozesses durchgeführt, indem sie direkt eine konstante Normallast auf die Sonde aufgebracht haben [20, 58]. Bei den Bearbeitungsprozessen kann es in drei Teile unterteilt werden:Relaxationsphase, Penetrationsphase und Ritzphase. Außerdem steht die Spitze wegen der Strahlkrümmung des Rasterkraftmikroskops (AFM), des Substrats mit Neigungswinkel sowie der Rauhigkeit der Probenoberfläche nicht vollständig senkrecht zum Werkstück. Daher sollte der Effekt der Spitzenneigung nicht vernachlässigt werden. Liuet al. wählten Spitzen mit unterschiedlichen Neigungswinkeln aus, um den Einfluss der Spitzenneigung auf die Bearbeitungsergebnisse zu untersuchen [59]. Darüber hinaus ist der Spitzenverschleiß ein Schlüsselfaktor für den Bearbeitungsprozess, der großen Einfluss auf die Bearbeitungsqualität hat. Nanoscratching mit Wasserschichtschmierung kann den Spitzenverschleiß reduzieren, um die Standzeit zu erhöhen und die Bearbeitungsqualität zu gewährleisten. Der durch die Wasserschichtschmierung beeinflusste Bearbeitungsmechanismus ist jedoch noch nicht gut verstanden. Um diesen Punkt zu lösen, haben Ren et al. verwendete MD-Simulationsmethode, um die Auswirkungen der Wasserschichtschmierung auf die Bearbeitungsergebnisse mit einem monokristallinen Kupfer zu untersuchen [60].
Ein einzelner Scratch-Prozess hat sich als einfaches Verfahren zur Herstellung von Nanorillen erwiesen, weist jedoch eine Einschränkung hinsichtlich der Dimension der Rille auf. Die Multi-Pass-Scratching-Methode wurde vorgestellt, um die Größe der Nanorille zu vergrößern [62]. Geng et al. haben den Unterschied zwischen Single-Pass-Ansatz und Multi-Pass-Ansatz mit MD-Simulation und experimentellen Ergebnissen untersucht [20]. Sowohl Single-Pass- als auch Multi-Pass-Ansätze können als statische Pfluglithographie betrachtet werden, die mit dem Kontaktmodus des AFM-Systems durchgeführt werden. Die statische Pfluglithographie kann jedoch einen nicht zu vernachlässigenden Spitzenverschleiß verursachen, wenn ein Langstrecken-Ritzprozess durchgeführt wird. Die auf dem Gewindeschneidmodus basierende Bearbeitungstechnik wird als dynamische Pfluglithographie bezeichnet, die das Potenzial hat, den Spitzenverschleiß zu reduzieren. Abbildung 2 zeigt das Schema der statischen bzw. dynamischen Pfluglithographie auf einkristallinem Kupfer. Beim statischen Pflügen wurde die Diamantspitze zuerst nach unten geführt und dann in negativer Richtung des x . gepflügt Achse. Nachdem das Pflügen beendet war, wurde die Spitze nach oben in die ursprüngliche vertikale Position zurückgezogen. Beim dynamischen Pflügen bewegte sich die Diamantspitze entlang einer Sinuskurve mit spitzer Scheitelhöhe und Periode [19]. Basierend auf dem Prinzip der gewindeschneidenden Bearbeitungstechnik haben Sundaram et al. haben ein neuartiges Nanobearbeitungsverfahren mit AFM entwickelt, das als Vibration-Assisted Nano Impact Machining by Loose Abrasives (VANILA) bezeichnet wird. Bei diesem Verfahren wird das AFM als Plattform verwendet und Nanoschleifmittel werden in die Aufschlämmung zwischen dem Siliziumwerkstück und der Vibration der AFM-Spitze eingespritzt. Die kinetische Energie für die Schleifmittel wird durch die Vibration der AFM-Spitze erzeugt und führt folglich zu einem nanoskaligen Materialabtrag der Probe [61]. Schematische Darstellung des VANILA-Prozesses ist in Abb. 2b, c gezeigt.
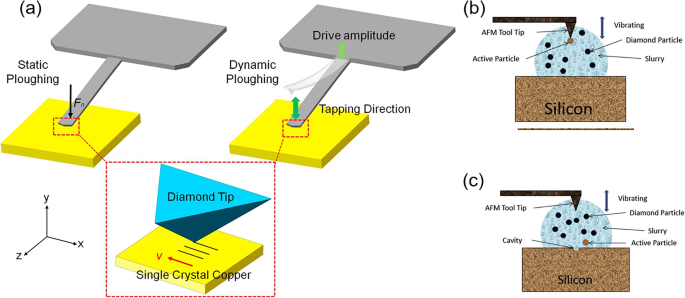
a Die Schemata der statischen und dynamischen Pfluglithographie auf einkristallinem Kupfer [19]. b AFM-Werkzeugspitze trifft auf ein Diamantpartikel. c Diamantpartikel, die auf das Werkstück treffen [61]
Analyse des Simulationsergebnisses
Schnittkraftanalyse
Die Schnittkraft könnte den Materialabtragsprozess und den Evolutionsfehler deutlich widerspiegeln, was ein wichtiger physikalischer Parameter zum Verständnis des Schnittphänomens ist [19, 63, 64]. Darüber hinaus steht die Schnittkraft in engem Zusammenhang mit der Schnittleistung und der Standzeit, was eine Orientierung beim TBN-Bearbeitungsprozess geben könnte [65]. Beim TBN-Verfahren wird die Schnittkraft hauptsächlich nach dem Kraftkalibrierverfahren bewertet, die Querkraft konnte mit diesem Verfahren jedoch nicht ermittelt werden [66, 67]. Durch den Einsatz der Molekulardynamiktechnologie kann die Variation der Schnittkräfte einschließlich Quer- und Tangentialkräfte in Echtzeit für den gesamten Prozess beobachtet werden [68]. Darüber hinaus könnten die durchschnittliche Kraft und die resultierende Kraft auch durch die MD-Simulationsmethode erfasst werden.
Durch die Analyse der Schnittkraftvariation können die Unterschiede verschiedener Materialstrukturen und der Einfluss von Bearbeitungsparametern auf den TBN-Prozess reflektiert werden. Liet al. fanden höhere Kratzkräfte auf polykristallinem Cu im Vergleich zum einkristallinen Cu wird der Tatsache zugeschrieben, dass die Anisotropie des Oberflächenkorns zwischen Werkstück und Spitze wenig Einfluss hat, wenn die Spitze von einem Korn zu einem anderen Korn mit unterschiedlicher Kristallorientierung übergeht, während die stabiles plastisches Fließen zeigt sich beim Materialabtrag von einkristallinem Cu aufgrund seines einzigen Orientierungssystems [25]. Es zeigt sich auch, dass die Schnittkraft für verschiedene Kristallstrukturen mit zunehmender Schnittgeschwindigkeit zunimmt, da eine höhere Nanokratzgeschwindigkeit mehr Späne erzeugt [69]. Im Gegensatz dazu führt die Änderung der Schnittkraft beim Ritzprozess von SiC zu einem ungünstigen Verhalten, da eine höhere Geschwindigkeit mehr amorphe Kristallstrukturatome erzeugen kann, was das SiC-Material duktiler und leichter zu entfernen macht [70]. Yanet al. untersuchten die Verarbeitbarkeit von Cu/Ni-Doppelschichten mit der MD-Simulationsmethode und fanden heraus, dass die Kraft von Ni-Cu-Doppelschichten im Vergleich zu Cu, Ni und Cu-Ni-Doppelschichten höher ist, da die Bewegung der Versetzungen durch die Grenzfläche der Doppelschichten, die diente, behindert wurde als Ausbreitungsbarriere [71]. Bei amorphen Polymeren wurde die Zerspanungseigenschaft durch die Ritzgeschwindigkeit in drei verschiedenen Aspekten wie folgt beeinflusst [72]:Erstens führt die bei höherer Geschwindigkeit erzeugte größere Stapelhöhe vor der Spitze zu einer größeren Tangentialkraft aufgrund von mehr Widerstand gegen die Spitze. Dann führt eine höhere Geschwindigkeit zu einer höheren Verformungsrate, die eine Kaltverfestigung des Materials bewirken kann. Dies würde auch zu einer Zunahme der Schnittkräfte führen. Schließlich ermöglicht der thermische Weichheitseffekt mit zunehmender Geschwindigkeit eine leichtere Bearbeitung des Werkstücks, wodurch die Tangentialkraft und die Normalkraft reduziert werden. Bei den Bearbeitungsprozessen von Polymeren nehmen die Schnittkräfte mit zunehmender Geschwindigkeit zu, was darauf hindeutet, dass der Stapel- und Dehnratenhärtungseffekt eine wichtigere Rolle bei der Bestimmung der Kratzkräfte spielt. Neben dem Einfluss der Werkstückstoffe spielt auch die Spitzengeometrie eine wichtige Rolle im Bearbeitungsprozess [18, 73, 74]. Renet al. untersuchten den Einfluss von Spitzenwinkeln auf die Schnittkräfte mit kegelförmiger Spitze. Es zeigt sich, dass die Kräfte mit zunehmendem Semi-Apex-Winkel aufgrund des Wachstums der Kontaktfläche zwischen Kopf- und Werkstückmaterialien zunehmen [21]. Außerdem nimmt der Reibungskoeffizient mit dem Semi-Apex stark ab, während die Härte zunimmt [75].
Einige Wissenschaftler untersuchten auch die Variation der Schnittkraft unter bestimmten Bearbeitungsbedingungen. Renet al. analysierten den Zusammenhang zwischen der Dicke der Wasserschicht und den Kratzkräften. Die Variation der Kratzkräfte bei Änderung der Wasserschichtdicke ist in Abb. 3 dargestellt. Im Gegensatz zum Makrokratzverfahren, bei dem die Wasserschicht hauptsächlich die Schmierung und Reduzierung der Schnittkraft übernimmt, ist der Widerstand der Wasserschicht gegenüber der Schmierwirkung dominant und die dickere Wasserschicht führt zu größeren Gesamtschnittkräften [60]. Daneben wird der Einfluss der Spitzenneigung auch durch die Analyse von Härte (Normalkraft pro Atom) und Reibungskoeffizient diskutiert [59]. Die Ergebnisse zeigen, dass die normale Härte im Vergleich zur Vorwärts- oder Rückwärtsrichtung empfindlicher ist und der Effekt der seitlichen Neigung der Spitze vernachlässigt werden kann. Außerdem ist der Kippeffekt auf die Normalkraft der Hauptgrund für die Änderung des Reibungskoeffizienten und der Kippeffekt auf die Kratzkraft ist viel geringer als der Einfluss auf die Normalkraft.
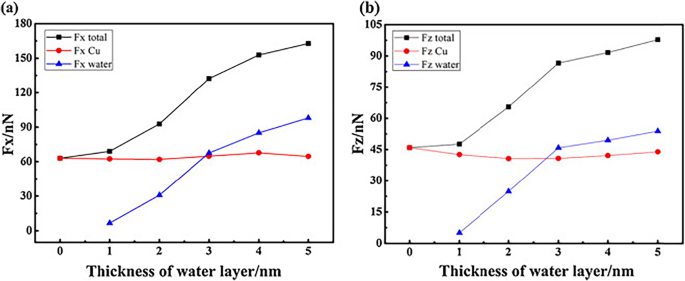
a Variation der durchschnittlichen Kratzkräfte bei Änderung der Wasserschichtdicke:a Tangentialkräfte und b Normalkräfte [60]
Durch den Vergleich der Schnittkraft zwischen statischem Pflügen und dynamischem Pflügen kann der Unterschied der Mechanismen aufgedeckt werden. Die Schnittkraft bei der dynamischen Pfluglithographie oszilliert mit dem periodischen Klopfen der Diamantspitze drastisch, während beim statischen Pflügen leichte Schwankungen zu beobachten sind. Darüber hinaus ist die durchschnittliche Bearbeitungskraft beim dynamischen Pflügen kleiner als die Hälfte der beim statischen Pflügen, was auf einen geringeren Spitzenverschleiß bei der dynamischen Pfluglithographie hinweist [19]. Beim dynamischen Pflugverfahren hat die Spitzenorientierung großen Einfluss auf die Schnittkraft. Yanet al. kombinierten die Nuttiefe und die Pflugkraft, um die Bearbeitungseffizienz zu vergleichen. Die Ergebnisse zeigen, dass die seitliche Vorderseite der Spitze die beste Effizienz hat, da sie die gleiche Pflugkraft wie die Ausrichtung der Vorderseite der Spitze hatte, aber gleichzeitig mehr als die doppelte Nuttiefe [63]. Durch die Analyse der Schnittkräfte konnte der Mechanismus des TBN-Bearbeitungsprozesses mit verschiedenen Materialien und Bearbeitungsbedingungen weiter erklärt werden. Darüber hinaus könnte der Vergleich der Schnittkräfte in verschiedenen Bearbeitungsmodi eine Orientierungshilfe für die Prozessoptimierung des TBN-Ansatzes sein.
Materialentfernungszustandsanalyse
Die Analyse des Materialabtragszustands ist auch eine wesentliche Methode, um den Mechanismus des TBN-Ansatzes aufzudecken. Der Materialabtrag und die Topographie im Bearbeitungsprozess werden normalerweise mit Rasterelektronenmikroskop (REM) und AFM beobachtet. Die Rillenmorphologie und der Abtragszustand können jedoch erst nach der Bearbeitung erfasst werden und der Materialabtragsprozess konnte nicht dynamisch verstanden werden. Vor kurzem haben Zhang et al. verwendeten lineare Schneidwerkzeuge, die direkt in REM verbunden sind, um den Spanbildungsprozess beim Materialschneiden zu sehen, während dieses Verfahren kompliziert ist und REM modifiziert werden sollte [76]. Daher ist dieses Verfahren schwer zu verallgemeinern. Im Vergleich zur experimentellen Methode kann die MD-Simulationsmethode leicht verwendet werden, um den Materialabtragsmechanismus und die Oberflächenerzeugung im Nanomaßstab zu untersuchen, und der Bearbeitungsprozess kann durch die MD-Methode in Echtzeit beobachtet werden.
Aus MD-Simulationsergebnissen des TBN-Prozesses ist bekannt, dass die Verformungszustände in Pflugzustand und Schnittzustand eingeteilt werden. Mit der Bewegung der Spitze werden die Werkstückmaterialatome vor der Spitze gequetscht und sammeln sich dann an, um im Schneidzustand den kontinuierlichen Span zu bilden. Gleichzeitig stapeln sich nach dem Passieren der Spitze auch einige Werkstückmaterialatome auf der linken und rechten Seite der hergestellten Nut [57]. Durch den Vergleich des Verhältnisses des Schneidzustandes zum Nicht-Schneidzustand können wir feststellen, ob der Schneidzustand oder der Pflugzustand den dominierenden Anteil einnehmen, wenn die verschiedenen Spitzenradien zum Ankratzen in den unterschiedlichen Ritztiefen verwendet werden [77]. In den letzten Jahren haben viele Wissenschaftler die Materialeigenschaften der Materialabtragszustände weiter untersucht. Beispielsweise zeigt einkristallines Material im TBN-Verfahren Anisotropie, die einen großen Einfluss auf den Materialabtrag hat [20]. Korngrenzen haben im Vergleich zu einkristallinen Materialien einen wichtigen Einfluss auf die mechanischen Eigenschaften polykristalliner Materialien. Gaoet al. fanden heraus, dass auch die Kornorientierung und nicht die Korngröße das Profil der Anhäufung maßgeblich bestimmt [78]. Darüber hinaus hat auch die Spitzengeometrie einen starken Einfluss auf den Materialabtrag. Drei Arten von Spitzen (konisch, dreieckig pyramidenförmig und halbkugelförmig) wurden ausgewählt, um den Einfluss der Spitzengeometrie auf den Materialabtragszustand aufzuzeigen. Für die konische Spitze besteht eine deutliche Abhängigkeit vom halben Apexwinkel. Ein größerer halber Spitzenwinkel der Spitze führt zu mehr Spanvolumen und verbessert die Glattheit der Kratzoberfläche, erfordert jedoch eine höhere Kratzkraft, erzeugt einen größeren Reibungskoeffizienten und eine höhere Temperatur im Werkstück und erhöht die Beschädigung unter der Oberfläche [40]. Alhafez untersuchte auch den Einfluss des halben Apexwinkels auf die Pile-up-Bildung [75]. Es zeigt sich, dass beim Ankratzen mit kleinem halben Spitzenwinkel der Spitze die Auflagerung meist in Vorwärtsrichtung akkumuliert, während die seitliche Auflagerung für die Bearbeitungsbedingung des großen halben Spitzenwinkels der Spitze dominiert. Einige Studien konzentrierten sich auf die dreieckige Pyramidenspitze, die mit der realen Geometrie der Spitze in AFM-basierten Bearbeitungsprozessen übereinstimmt [19, 20, 63, 79]. Es wurden hauptsächlich drei Bearbeitungsrichtungen verglichen, nämlich Kante-vorwärts, Stirnseite-vorwärts und Seitenfläche-vorwärts. Beim Bearbeitungsprozess von SiC kann der Materialabtragszustand einfach durch Einstellen der Ritzrichtung des Werkzeugs gesteuert werden. Die Kratzrichtung von der Kante nach vorne kann einen stabileren Prozess bieten, was zu einer besseren Größengenauigkeit und Konsistenz der erhaltenen Rillen führen kann [79]. Der Materialabtragszustand von Polymeren ist jedoch im Vergleich zu Metall- oder Halbleitermaterialien temperaturempfindlicher. Während des Ritzprozesses ist die lokale Temperatur in der Ritzzone höher als die Glasübergangstemperatur, was darauf hindeutet, dass das Werkstück in der Ritzzone duktil abgetragen werden kann [72]. Zhanet al. untersuchten die mikroskopischen Reibungsmechanismen von amorphem Polystyrol. Sie fanden heraus, dass die Flexibilität der Molekülketten mit steigender Temperatur zunimmt, wodurch sich die Molekülketten leichter kräuseln und in ihren ursprünglichen Zustand zurückkehren können [56]. Du et al. fanden heraus, dass die Bearbeitungsgeschwindigkeit einen großen Einfluss auf die Bearbeitungsergebnisse von Polystyrol hat. Die Veränderung innerhalb der Kette dominiert die permanente Verformung von Polystyrolproben, wenn die Bearbeitungsgeschwindigkeit klein ist, während das Gleiten zwischen den Ketten ausgeprägter ist, wenn die Bearbeitungsgeschwindigkeit groß ist [80].
Wie aus der obigen Diskussion hervorgeht, konzentrierten sich die meisten Studien hauptsächlich auf den trockenen Zustand anstelle von Flüssigkeiten. Allerdings werden vor dem Werkzeug angesammelte Atome reduziert und die Grate entlang der Rillen sind bei hoher Dicke der Wasserschicht nicht sichtbar und die Oberflächenrauheit nimmt sichtbar ab und führt zu einer relativ glatten Oberfläche. Es kann erklärt werden, dass die Wasserschicht als Schmiermittel wirkt, um den Klebebereich zwischen dem Werkzeug und der frisch geformten Spanoberfläche zu reduzieren und die an der Span-Werkzeug-Stirngrenze auftretende Widerstandskraft zu reduzieren. Die direkte Folge ist, dass die Oberflächenqualität stark verbessert wird. Mit zunehmender Dicke der Wasserschicht kann die Oberflächenqualität schrittweise verbessert werden [60]. In einigen neuartigen Bearbeitungsansätzen haben Shockly et al. untersuchten die Auswirkungen von Parametern (Aufprallgeschwindigkeit, Aufprallwinkel und Betriebstemperatur) bei der vibrationsunterstützten Nanoschlagbearbeitung auf die Bildung von Nanokavitäten und fanden heraus, dass die Betriebsparameter einen wesentlichen Einfluss auf die Tiefe und Breite der erzeugten Nanokavitäten haben, wie in Abb 4 [61]. Xiaoet al. fanden heraus, dass die Tiefe und Breite der Rillen beim dynamischen Pflugprozess kleiner sind als beim statischen Pflugprozess, was bedeutet, dass Nanostrukturen mit kleinen Strukturen durch die dynamische Pfluglithographie hergestellt werden könnten. Außerdem konnten die Rillendimensionen durch das Antriebsamplitudenverhältnis im dynamischen Pflugverfahren gesteuert werden, und dies zeigt, dass auch die Herstellung der Rillen kontrollierbar sein könnte [19].
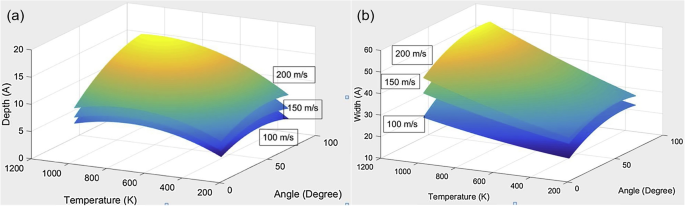
Mehrfaches lineares Regressionsdiagramm für a Tiefe der Nanokavität (Aufprallgeschwindigkeit, Aufprallwinkel und Betriebstemperatur) und b Breite der Nanokavität (Aufprallgeschwindigkeit, Aufprallwinkel und Betriebstemperatur) [61]
Beim Abtragsprozess besteht an der Spitze ein Verschleißverhalten. In den meisten früheren Studien wurde die Spitze als starrer Körper definiert, was bedeutet, dass das Phänomen des Werkzeugverschleißes nicht direkt beobachtet werden konnte [13]. Viele Wissenschaftler untersuchten den Werkzeugverschleiß, indem sie den Abtragszustand, die Belastung und die Temperaturverteilung untersuchten [70, 77]. Um das reale Verschleißphänomen der Spitze während des Bearbeitungsprozesses widerzuspiegeln, haben Meng et al. setzen die Spitze als verformbaren Körper und fanden das Verschleißverhalten der Spitze während des Bearbeitungsprozesses [81]. Die Ergebnisse zeigen, dass die Form des Diamantschleifverschleißes hauptsächlich adhäsiven Verschleiß in der Anfangsphase und Atom-für-Atom-Verschleiß in der Bearbeitungsstabilitätsphase ist und die Menge des Atom-für-Atom-Attributionsverschleißes des Schleifmittels weniger von der Schnittgeschwindigkeit beeinflusst wird [ 81]. Auffällig ist, dass es relativ wenige Berichte über das Verschleißverhalten der Spitze gibt. Es ist zu hoffen, dass die Verwendung des verformbaren Spitzenkörpers die Untersuchung des Spitzenverschleißverhaltens während des Nanobearbeitungsprozesses weiter fördert.
Die Zustandsanalyse des Materialabtrags bietet eine wirksame Unterstützung für die Echtzeitüberwachung des Bearbeitungsprozesses. Aufgrund der oben erwähnten Begrenzung der Längenskala konnte die Morphologie der bearbeiteten Oberfläche und der Abtragsprozess jedoch nur durch einen qualitativen Vergleich analysiert werden. It is difficult to predict the accurate processing results.
Defect Evolution Process Analysis
To obtain the information about the defects generated during the scratching process, TEM is usually employed after the FIB sample preparation techniques, which has several disadvantages, such as relatively complicated operation, high cost, and strong material dependence.
The MD simulation method can obtain the defects generated beneath the sample surface easily. Moreover, the defect evolution process during the scratching could also be observed by using the MD simulation approach, which could not be obtained by experimental method. Many available algorithms to extract defect types were presented, including common neither analysis (CNA) [82], centro-symmetry parameter (CSP) [83], slip vector analysis [84], Ackland-Jones analysis [85], etc. However, these methods are not suitable for tracing the propagation of dislocations, especially when a large number of dislocations are generated by tip scratching along certain direction, and we can no longer investigate what is going on inside the specimen using these methods [86]. Chenet al. presented slipping analysis for visualizing the atomic slipping process for material deformation, which could filter out those atoms that have slipped relative to its neighbor atoms during a specified period of time in the condition with large numbers of atoms [86]. By using this method, Xiao et al. investigated the slipping process during dynamic and static ploughing lithography [19]. The relationship between the cutting force and slipping process is shown in Fig. 5. It could be seen that for dynamic ploughing, the sample material mainly flows downwards and sidewards, whereas no obvious downwards material flow is observed in static ploughing process. In addition, the propagation of the dislocation is dependent on the orientation of the tip, leading to the various morphologies of the grooves. Dislocation extraction algorithm (DXA) is also a useful dislocation analysis tool to identify the lattice dislocation and to determine their Burger vector [87]. By using this method, Gao et al. investigated the behavior of the nanoscratching of iron. They found that a distinct reorganization of the dislocation network. At the beginning, the plastic zone grows linearly with the scratching length along the path. Then, the dislocation density decreases rapidly after some length dislocation reactions. Plastic activity then is concentrated only on the scratch front. Only few dislocations remain in the middle of the scratch. Vacancies in this zone are created by dislocation reactions. It is also found that point defects vacancies generated by dislocation reactions and deformation twining [88].
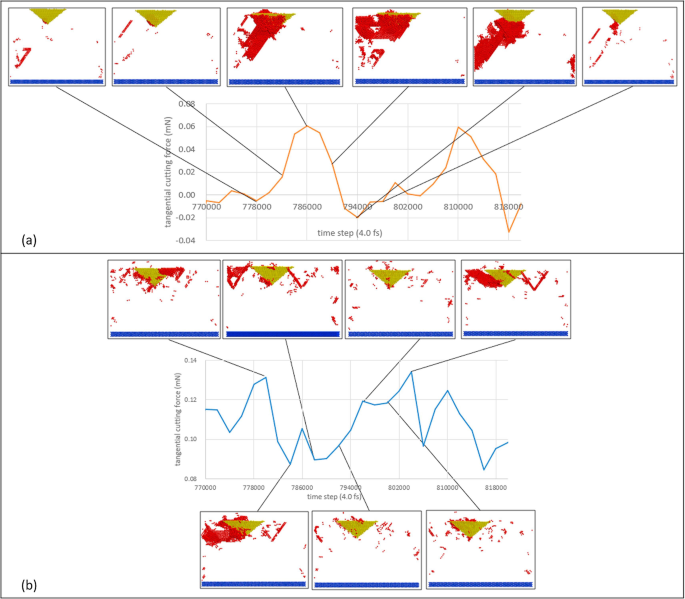
Slipping processes in a dynamic ploughing and b static ploughing [19]
For the polycrystalline materials, the deformation mechanism was mediated by dislocation nucleation within grain interior as well as grain boundary dislocations in polycrystalline material [43]. While the dislocation propagation is associated with the formation of nanovoids and interstitial clusters in the case of larger grain size, and the formation of twins at the grain boundary was dominating for smaller clusters. This behavior was attributed to the transition of dislocation movement from smooth (larger grain) to rough (smaller grain) during scratching process. Li further concluded the difference of material deformation mechanism about single crystal Cu, polycrystalline Cu, and NT polycrystalline Cu. The results show that the plastic deformation is mainly affected by the interaction between dislocations during scratching process in single crystal Cu; while for polycrystalline Cu both dislocations and GB dominate the plastic deformation; and the plastic deformation is controlled by the interactions of the dislocation, grain boundary (GB), and twin boundary (TB) accompanied with twinning/detwinning [25].
Furthermore, many studies focused on the MD simulation of the TBN process on the semiconductor materials, such as silicon, silicon carbide, gallium arsenide, and aluminum nitride. To investigate these brittle materials, phase transformation is also an important deformation mode in addition to dislocation slip [89]. The interaction between dislocation and phase transformation varies with the crystal orientation. The results indicate that prior to the “Pop-In” event, Si (010) undergoes inelastic deformation accompanied by the phase transformation from the Si-I to the Si-III/ Si-XII, which is not occurred in Si (110) and Si (111). While, the phase transformation from the Si-I to the bct-5 is the dominant mechanism of incipient plasticity for each crystallographic orientation, and dislocation nucleation is also an operating deformation mode in the elastic-plastic transition of Si (010). Dai et al. investigated the subsurface damage mechanism on single crystal silicon during TBN process. It is found that the evolution of crystalline phases is consistent with the distribution of hydrostatic stress and temperature [40]. SiC is also a kind of important semiconductor material, which has the similar property as silicon. The SiC material removal process is achieved through the phase transfer from zinc blended to amorphous structure with few hexagonal diamond structures. Higher scratching speed generates more amorphous structure atoms, fewer hexagonal diamond atoms, and fewer dislocation atoms due to larger impaction and less rearrangement time [90]. While Meng et al. found when the phase transition is not the dominant deformation mechanism, the Schmidt coefficient method can effectively predict the sliding motion of 3C-SiC during the TBN process (elastic sliding motion and dislocation slip motion) [79]. Moreover, Meng et al. further studied on the strain rate and heat effect on the removal mechanism of SiC. They found that the strain rate effect and the thermal softening effect directly affect the material removal amount and form of the subsurface damage (SSD). The influence of the thermal softening effect on the stress in the processing region under the condition of high strain rate exceeds that of the decrease in the growth rate of the dislocation generation speed. The polycrystalline SiC removal process is dominated by the amorphous phase transition. Furthermore, several hexagonal diamond structure atoms and dislocations are found in the GBs during the scratching. Higher scratching speed and larger depth of cut promotes more atoms to transfer into the amorphous structure due to larger impaction [81]. Compared with monocrystalline SiC, the microstructure in polycrystalline makes the SiC more soften by generating less normal scratching force and amorphous structure phase transition and thinner plastic deformation induced SSD [91]. Dislocation propagation and phase transition analysis could explain the mechanism in machining process. However, most researches focused on single crystalline materials and the materials with complex structure are rarely reported, which should be further studied.
Future Research Directions and Challenges
At present, the research on the TBN process through MD simulation is widely reported. However, there are still some limitations to be considered. Thus, future directions are discussed in this review.
- (1)
With the development of TBN methods, some novel technologies have been proposed in this field. For example, AFM tip-based nanomilling process has a broad prospect due to its great machining performance and size control properties [92, 93]. However, the mechanism of nanomilling has not been fully understood due to limitation of the detection equipment. With the use of MD simulation, it is hopeful that the variation of the cutting force, the dynamics change of defects, and the removal state of workpiece materials during rotating process of the tip. In addition, sample vibration-assisted nanoscratching method has not been reported yet. MD simulation approach could provide meaningful guidance in the early stage.
- (2)
Due to the limitation of the length and time scales, MD methods still could not fully describe the experimental process quantitatively. In some studies combining experiments and MD simulations, MD simulation approach could only qualitatively explain the experimental phenomena [19, 20, 94]. In particular, for some time-dependent materials such as amorphous polymers, the velocity of the probe has a significant impact on the removal state of polymers. Thus, in order to accurately predict the experimental process and quantitative analyze the experimental results, the improvement of algorithm and computing capability is indispensable.
- (3)
Many nanostructures have been achieved on polymer materials using the TBN method [95,96,97]. In particular, the mechanical machining process of polymer materials based on TBN method keeps the normal load constant so as to guarantee the accuracy of the machined nanostructures [98]. However, the reports of MD simulation of polymer in TBN process are limited until now. Moreover, thermal scanning probe lithography is developing in polymer, which has the potential to improve the machining accuracy of the TBN process. It is necessary to reveal the material removal mechanism of the polymer materials when conducting nanoscale scratching process with the mechanical-thermal effect.
Schlussfolgerung
It is undeniable that MD simulations technology plays an increasingly crucial role in nanomachining process to reveal hitherto unknown phenomena [99]. This review concluded the recent progress in MD simulation of TBN method, and the above contents are summarized as follows:
- (1)
The establishment of MD models of various materials and related potential function were summarized. In particular, the modeling process of NT polycrystalline materials and amorphous polymers were discussed in this section. The accuracy of MD models is of great significant to the subsequent simulation results.
- (2)
The new technologies of TBN methods, including multi-scratching, dynamic ploughing, and VANILA were presented. With the help of MD simulation, the mechanism of these methods could be better understood. In particular, the essential difference between static ploughing and dynamic ploughing was revealed by MD method from the aspects of internal defects, morphology and cutting forces.
- (3)
The analysis of MD simulations in TBN process, including the cutting force, the state of material removal, and defect analysis are also summarized. Besides, some novel analysis methods like slipping analysis are also given. With these methods, the processing mechanism based on TBN approach is reviewed, which shows the materials dependence on the TBN machining process.
Abkürzungen
- TBN:
-
Tip-based nanomachining
- AFM:
-
Rasterkraftmikroskopie
- MD:
-
Molekulardynamik
- NT:
-
Nanotwined
- PE:
-
Polyethylene
- EAM:
-
Eingebettete Atommethode
- SW:
-
Stillinger-Weber
- ABOP:
-
Analytical bond order potential
- REBO:
-
Reactive Empirical Bond Order
- AIREBO:
-
Adaptive Intermolecular Reactive Empirical Bond Order
- LAMMPS:
-
Large-scale Atomic/Molecular Massively Parallel Simulator
- MS:
-
Material studio
- OVITO:
-
Open Visualization Tool
- VMD:
-
Visual molecular dynamics
- VANILA:
-
Vibration-Assisted Nano Impact machining by Loose Abrasives
- SEM:
-
Rasterelektronenmikroskop
- CNA:
-
Common neighbor analysis
- CSP:
-
Centro-symmetry parameter
- DXA:
-
Dislocation extraction algorithm
- GB:
-
Grain boundary
- TB:
-
Twin boundary
- SSD:
-
Subsurface damage
Nanomaterialien
- Nano- und Batterieanode:Ein Rückblick
- Eine Übersicht über die Anwendung von Biosensoren und Nanosensoren in Agrarökosystemen
- Oberflächeneffekt auf den Öltransport in Nanokanälen:eine molekulardynamische Studie
- Molekulardynamische Modellierung und Simulation des Diamantschneidens von Cer
- Die Untersuchung eines neuartigen, durch Nanopartikel verbesserten wurmähnlichen Mizellensystems
- Antitumorstudie zu Chondroitinsulfat-Methotrexat-Nanogelen
- Studie zum Effekt der Aufprallrichtung auf den nanometrischen Schleifprozess mit Molekulardynamik
- Untersuchung des nanoskaligen Reibungsverhaltens von Graphen auf Goldsubstraten mittels Molekulardynamik
- Low Tunneling Decay von jodterminierten Alkan-Einzelmolekül-Übergängen
- Neue Studie untersucht Produktivitätsdynamik und -treiber in der US-Fertigung