FACC betont schnell härtende Prepregs, thermoplastische Kunststoffe und biobasierte Verbundwerkstoffe für die Nachhaltigkeit von Flugzeugstrukturen der nächsten Generation
FACC (Ried im Innkreis, Österreich) ist ein führender Tier-1-Zulieferer in der Luft- und Raumfahrt, der sich auf die Herstellung von Leichtbausystemen für Interieur, Triebwerke und Flugzeugzellen spezialisiert hat. In der Ausgabe September 2021 seines Magazins BEyond hebt FACC sein neues Werk in Kroatien für Flugzeugkabinenkomponenten, das COMPETE-Programm für seine Zulieferer, das Materialien der Zukunft betont, und drei F&E-Technologien mit Fokus auf Verbundwerkstoffe hervor:Induktionsschweißen, Hybrid-Spritzgießen und schnell aushärtende Prepregs.
FACC in Kroatien
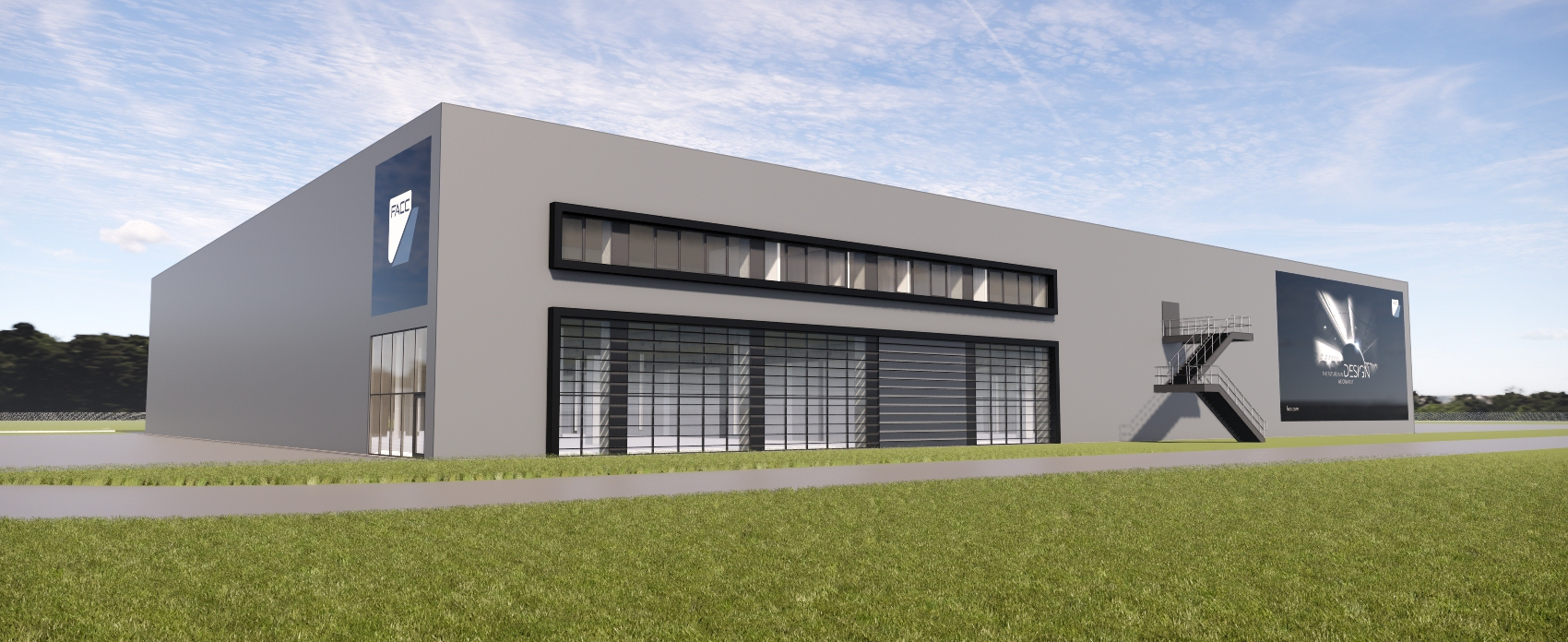
In der Nähe von Zagreb, Kroatien, entsteht derzeit ein Hightech-Werk. Diese 10.000 Quadratmeter große Anlage, die 2022 eröffnet werden soll, wird leichte Kabinenkomponenten für Verkehrsflugzeuge und Business-Jets unter Verwendung neuester Faserverbundwerkstoff-Technologie produzieren. „Diese Greenfield-Investition ermöglicht es uns, eine erstklassige Anlage zu schaffen, die Spitzentechnologie, Automatisierung und 4.0-Methoden vereint“, erklärt FACC-CEO Robert Machtlinger. Er weist darauf hin, dass sich die Anlage in der Nähe der FACC-Standorte in Österreich sowie des Tiefwasserhafens Koper befindet. Das Werk integriert auch ehemalige Fremdleistungen in die eigene Wertschöpfungskette und legt die Basis für zukünftige Kapazitätserhöhungen.
COMPETE-Partnerprogramm
FACC hat im Februar 2021 das Partnerprogramm COMPETE ins Leben gerufen, um die Bindung zu ausgewählten Partnern zu stärken und die Zusammenarbeit nachhaltig zu intensivieren. FACC-Lieferanten werden trotz des Auf und Ab im Luftfahrtmarkt die Möglichkeit haben, neue Aufträge zu generieren, müssen sich aber erst erfolgreich gegen andere Lieferanten behaupten. FACC bewertet seine Lieferanten nach folgenden Kriterien:
- Kosteneffizienz
- Operative Exzellenz
- Werkstoffe der Zukunft – innovative Werkstoffe für einen sprunghaften Wandel bei Produkten und Produktionsprozessen
- Partnerschaft und Leidenschaft
- Effizienz in allen Prozessen – inklusive fokussierter Digitalisierung
- Transparenz in Zitaten
- Umwelt- und Sozialverantwortung.
„COMPETE steht für fairen Wettbewerb und starke Partnerschaften mit Lieferanten, die konstant gute Leistungen erbringen und ein besonders hohes Potenzial haben“, sagt Andreas Ockel, COO von FACC. „Wir konzentrieren unser zukünftiges Einkaufsvolumen auf unsere COMPETE-Programmpartner.“ Innerhalb der nächsten drei Jahre wird FACC 75 Millionen Euro an Einkäufen umverteilen, mit dem Ziel, von 440 auf weniger als 400 Lieferanten zu sinken.
Ockel erläutert die Materialien der Zukunft genauer und erklärt, dass das Angebot von Materialinnovationen entscheidend ist:„Neue faserverstärkte Verbundwerkstoffe Materialien gestalten unsere Zukunft! Schnellhärtende, schnellhärtende Harzsysteme, die die Produktionszykluszeiten drastisch verkürzen, sind eine Innovation, die echte Stufenänderungen in Herstellungsprozessen einführt. Wir suchen daher eine enge Zusammenarbeit mit Lieferanten, die diesen technologischen Wettbewerbsvorteil bieten.“
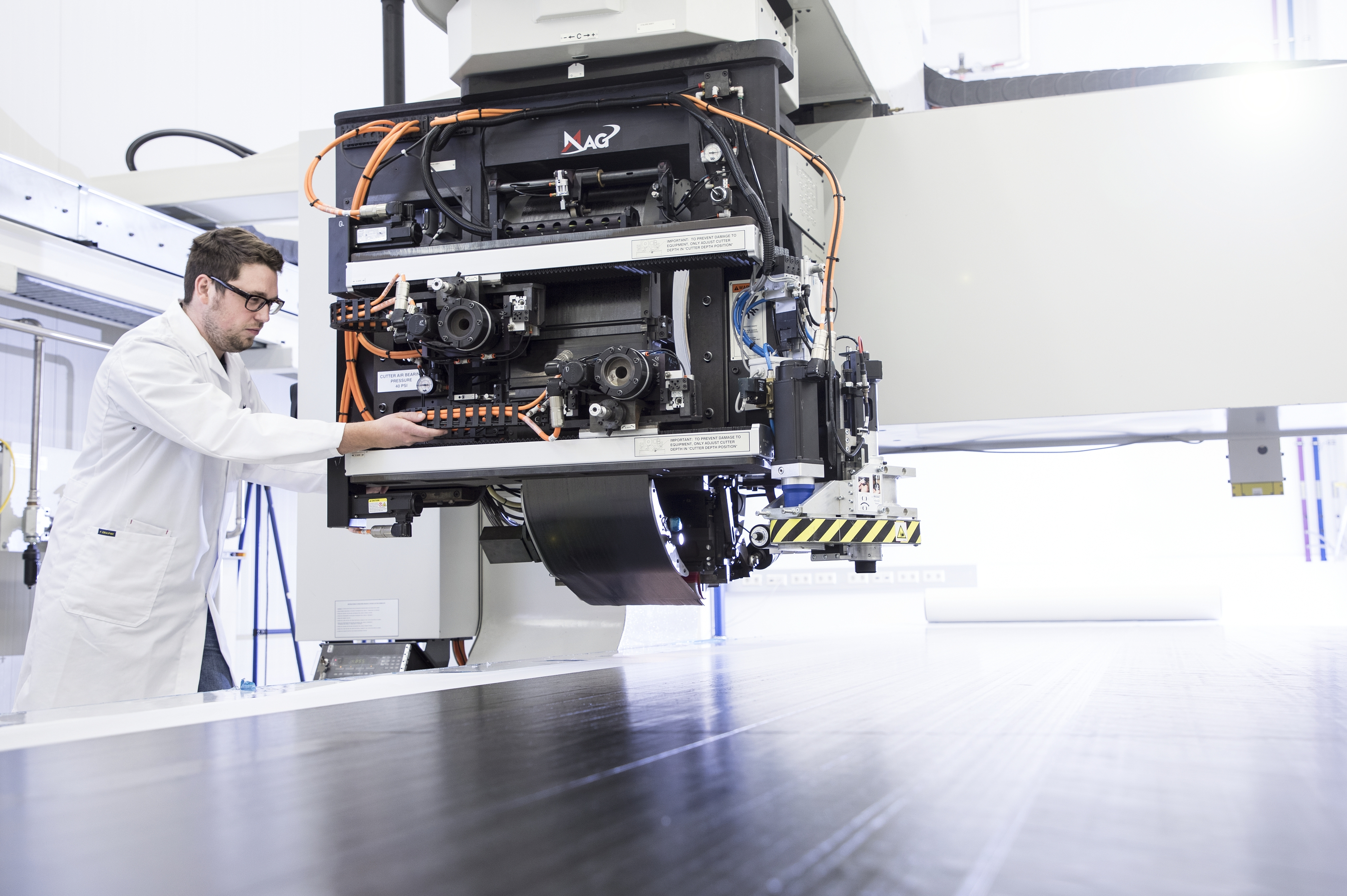
Nachhaltigkeit, Investitionen und Innovation
FACC behauptet, durch die Herstellung von Flugzeugteilen aus leichten Verbundwerkstoffen und neuen aerodynamischen Formen zur Steigerung der Nachhaltigkeit in der Luftfahrtindustrie beigetragen zu haben. Um das globale CO2 weiter zu reduzieren -Emissionen der Zukunft arbeitet das Unternehmen intensiv an der Entwicklung von Technologien, die Flugzeuge noch leichter, leiser und effizienter machen.
FACC erforscht derzeit Verbundwerkstoffe unter Verwendung biobasierter und/oder biobasierter Materialien, von denen behauptet wird, dass sie bald ein vollständiges Recycling von Flugzeugkomponenten ermöglichen sollten. „Es geht darum, biologische Materialien und neue Verfahren zu entwickeln, die weniger Energie verbrauchen und mehr Leistung bieten, aber dennoch bezahlbar sind“, sagt Machtlinger.
Auch das Unternehmen selbst wird nachhaltiger und strebt an, dass seine Werke bis 2040 energieautark und seine Produktionsprozesse klimaneutral sind. Für das laufende Jahrzehnt sieht die FACC-Roadmap 2030 Investitionen in neue Anlagen wie Zagreb, sowie neue Produktionsmethoden, die als nächstes hervorgehoben werden.
Drei F&E-Initiativen
FACC entwickelt das Induktionsschweißen von thermoplastischen Verbundwerkstoffen, um Schrauben und Nieten in Flugzeugkomponenten und -baugruppen zu ersetzen. Eine Induktionsspule induziert in Kohlefasern einen Wirbelstrom, der Wärme erzeugt (siehe „Schweißen von thermoplastischen Verbundwerkstoffen“). Anschließend wird der Hochleistungsthermoplast aufgeschmolzen und im Schweißbereich verfestigt. Homogene Schweißverbindungen aus faserverstärkten thermoplastischen Verbundwerkstoffen werden in Rudern, Höhenrudern und Klappen eingesetzt. Sie lassen sich im Vergleich zum mechanischen Befestigen oder Kleben schneller und effizienter fügen und sind vollständig automatisierbar.
Hybrid-Spritzguss wird als effizienter Weg zur Funktionalisierung von Faserverbundwerkstoffen beschrieben. Dabei wird ein Halbzeug zu einem Laminat verfestigt, das anschließend erhitzt, umgeformt und mit einer Spritzgussmasse umspritzt wird. Ein großer Vorteil dieses Verfahrens besteht darin, dass es ein Recycling ermöglicht; Abfälle können wiederaufbereitet und in der Spritzgussmasse verwendet werden. Auch die Integration von Versteifungselementen und die Fertigung komplexer Bauteile wie Flugzeuginnenräume oder Verkleidungen sind möglich.
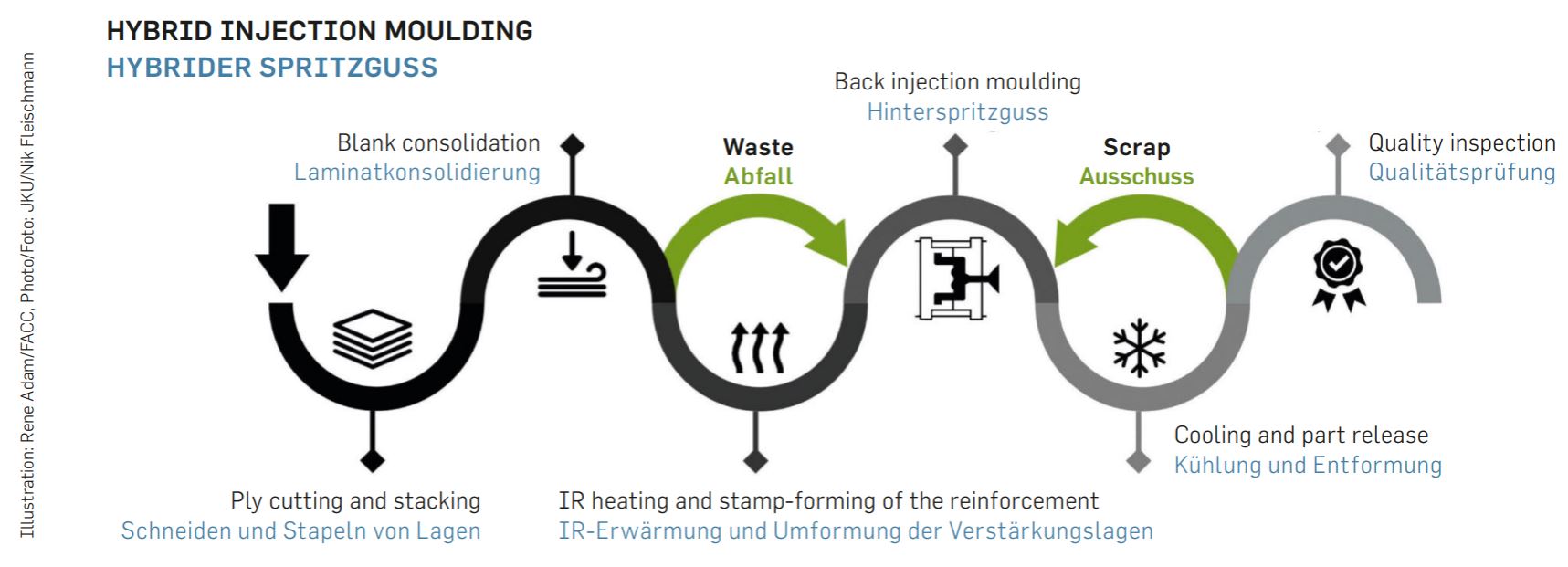
Schnell aushärtende Prepregs bieten ein enormes Potenzial, die Aushärtezeit von Composites während der Produktion um bis zu 90 % zu verkürzen. Dies ermöglicht sogar Teile, die mit Duroplast hergestellt wurden in Minutenschnelle in einem robusten und energieeffizienten Verfahren hergestellt werden. FACC berichtet, dass schnell härtende Prepregs einfacher zu verarbeiten sind als thermoplastische Verbundmaterialien. Das Unternehmen sieht in diesen Materialien auch einen Weg zu mehr Nachhaltigkeit, denn die Harze, die beispielsweise für Interieur-Produkte benötigt werden, können aus nachwachsenden Rohstoffen auf Basis von Zuckerrohr, Bambus oder Algen hergestellt werden.
Harz
- Ultraleichte TPE-Verbundwerkstoffe für Schuhe
- RS Electric Boats wählt Norco für die Herstellung von Verbundwerkstoffen
- PEEKSense Hochtemperatur-Thermoelement für die Aushärtung von PEEK-Verbundwerkstoffen
- Solvay-Folie auf Epoxidbasis für Prepregs
- Hexion erhält Genehmigung für DIP-Finanzierung
- Solvay-Verbundwerkstoffe für Rennkatamarane ausgewählt
- Teijin liefert kohlenstofffaserverstärkte Thermoplaste für Boeing
- Thermoplastische Tür eine Premiere für Automobilverbundwerkstoffe
- CAMX 2018-Vorschau:PolyOne Advanced Composites
- Ashland arbeitet mit Velox für den Vertrieb von Verbundwerkstoffen in Frankreich zusammen