VBO-Hinterholm außerhalb des Autoklaven, thermoplastische Rippen zielen auf Wing of Tomorrow
Airbus (Toulouse, Frankreich) befindet sich inmitten umfassender Bemühungen, mit Herstellern von Aerokomposite an der Entwicklung von Strukturen außerhalb des Autoklaven (OOA) für das Wing of Tomorrow (WOT)-Programm des Unternehmens zusammenzuarbeiten. Diese Strukturen werden 2021 an Airbus geliefert und zu einem Demonstratorflügel zusammengebaut, der auf den möglichen Einsatz in einem Single-Aisle-Flugzeug der nächsten Generation getestet und bewertet wird. Wann ein solches Programm angekündigt werden könnte, ist unbekannt und Gegenstand vieler Spekulationen, aber die gesamte Lieferkette von Aerocomposites positioniert sich als Teil der nächsten Generation des Flugzeugbaus, sei es für Airbus oder Boeing oder beides.
CW hat über einige dieser WOT-Aktivitäten bereits in Berichten über die untere Flügelhaut von Spirit AeroSystems (Wichita, Kan., USA) und thermoplastische Rippen von GKN Aerospace (Hoogeveen, Niederlande) berichtet. Zu den Bemühungen von WOT gehört der Flugzeughersteller und Anbieter von Flugzeugstrukturen Daher (Paris, Frankreich), der einen OOA-Hinterholm und fünf thermoplastische Rippen für das Programm entwickelt, hergestellt und geliefert hat.
„Daher ist stolz, an diesem WOT-Programm teilzunehmen. Diese Entwicklung bestätigt Dahers Position als einer der weltweit führenden Anbieter von thermoplastischen Technologien und duroplastischen integrierten Funktionsstrukturen sowie als starker Partner für Flugzeughersteller und Tier 1 für komplexe Teile“, sagt Dominique Bailly, VP R&D bei Daher.
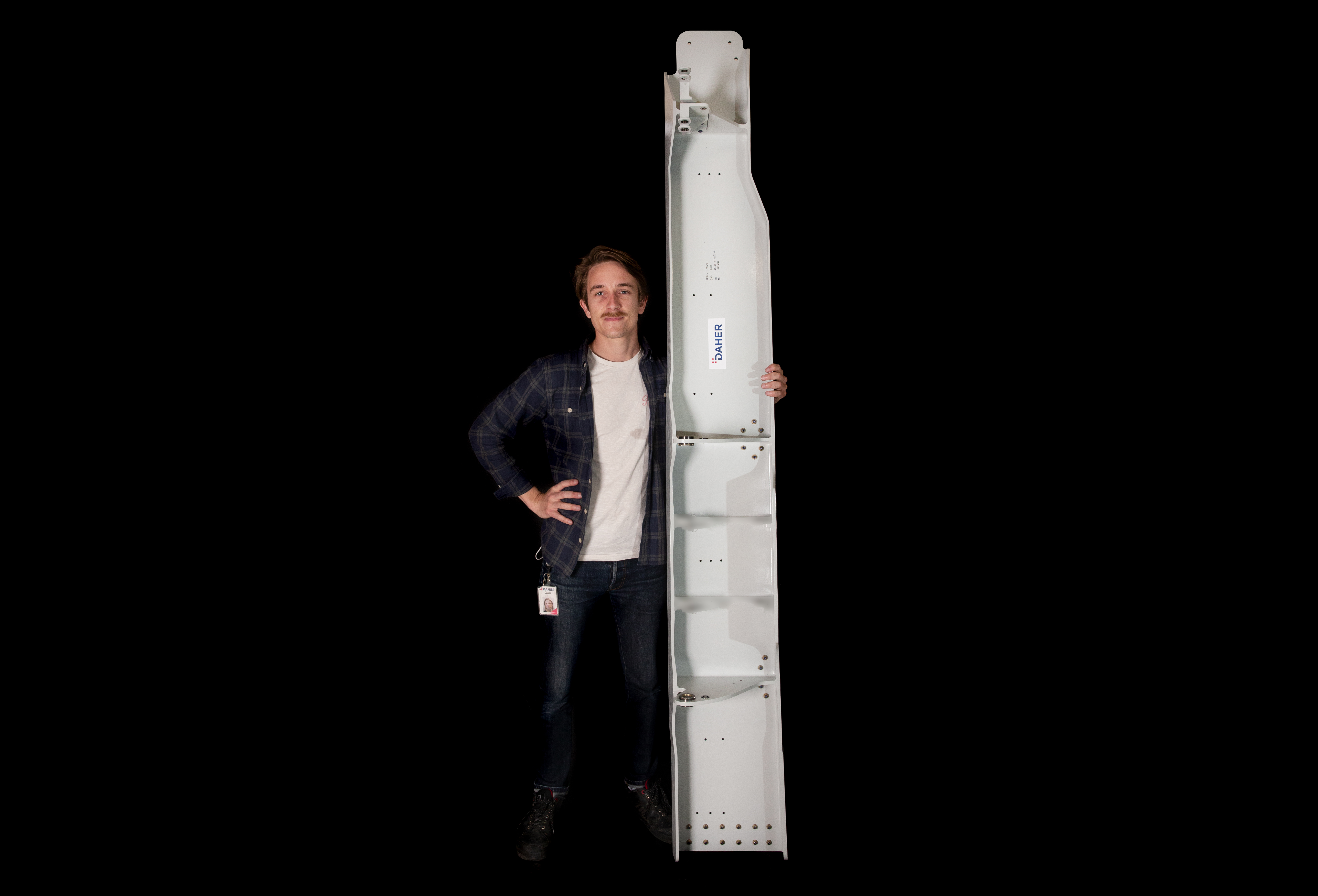
Hochleistungsholm
Der WOT-Demonstrator hat, wie alle Tragflächen von Verkehrsflugzeugen, mehrere Holmstrukturen. Der daher für WOT entwickelte hintere Holm befindet sich außerhalb des Tanks und ist der zweitnächste von zwei Holmen direkt neben dem Rumpf, direkt über dem Fahrwerk. Es ist mehr als zwei Meter lang und 10 Millimeter dick und muss erhebliche Festigkeits- und Steifigkeitsanforderungen erfüllen – „einige Tonnen auf die Elemente aufgebracht und mehrere zehn Tonnen für Scherung und Zug in Spannweitenrichtung“, sagt Bailly – angesichts seiner Nähe zu Rumpf und zum Fahrwerksystem.
Darüber hinaus, so Alexandre Condé, Chefingenieur bei Daher, der am Holm gearbeitet hat, suchte Airbus nach der Entwicklung eines hochautomatisierten Fertigungsprozesses, der es dem Unternehmen ermöglichen würde, das Flugzeuggewicht zu reduzieren und die Flugzeugproduktionsraten von 60-100 Schiffssätzen kostengünstig zu erreichen pro Monat. Daher schlug eine Konstruktion vor, die in der Lage ist, 15 metallische Komponenten und Befestigungselemente zu ersetzen, die ursprünglich aus der Basiskonstruktion des Verbundholms stammten. „Die Idee war, die meisten Funktionen zu integrieren, um kosteneffektiv zu sein und Gewicht zu sparen“, sagt Condé.
Die resultierende Holmstruktur ist ein Nebenprodukt eines OOA-Vakuumbeutel-only (VBO) Duroplastholms, der 2018 von Daher für einen Dassault Aviation (Paris, Frankreich) Business Jet entwickelt wurde. Bailly sagt, dass der Dassault Holm mit M56 Epoxidharz-basiertem Prepreg von Hexcel (Stamford, Connecticut, U.S.), gehärtetem OOA VBO, hergestellt wurde. Als Daher in das Airbus-WOT-Programm involviert wurde, beschloss das Unternehmen, das Design, die Prozesse und die Begründung des Dassault-Holms anzupassen und auf die neue Airbus-WOT-Struktur anzuwenden Hexcel AS4 Kohlefasergewebe und IM7 UD Kohlefaser.
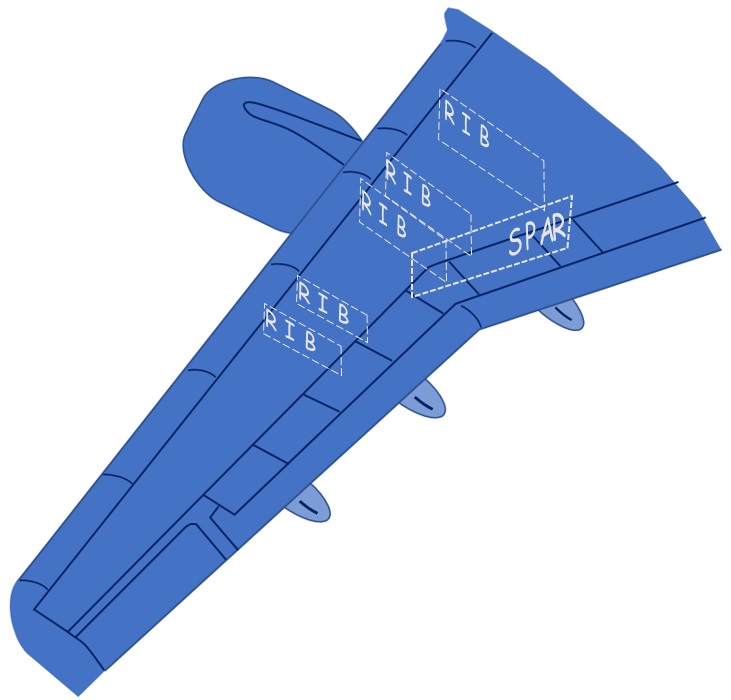
Der zur Herstellung des Holms verwendete Herstellungsprozess ist die automatisierte Faserplatzierung (AFP) unter Verwendung eines Systems von Coriolis Composites (Queven, Frankreich), das Material über einer Patrize aufbringt. Die Härtung wird unter Vakuumbeutel in einem Ofen durchgeführt. Das resultierende Teil, sagt Condé, hat eine Porosität von 0,1%.
Condé sagt, dass das Prepreg aus dem gleichen Grund dem Flüssigharzguss vorgezogen wurde, aus dem Prepreg in den letzten 30 Jahren zu einem festen Bestandteil der Luft- und Raumfahrtfertigung geworden ist:Es bietet ein konsistentes und zuverlässiges Harz-/Faservolumen, das die Produktion von Teilen mit konsistenten und zuverlässigen Abmessungen ermöglicht und Masse. „Wenn Sie diese neue Generation von OOA-Harz nur mit Vakuum verwenden, haben Sie eine perfekte Robustheit des Fasergehalts in der Dicke des Verbundwerkstoffs nach dem Aushärten“, sagt Condé. „Außerdem ist das Gewicht des Teils sehr stabil, da das Harz nicht aus der Faser gedrückt wird.“
Daher sagt, dass es der erste Partner war, der Ende 2020 eine WOT-Komponente – einen Holm an Airbus in Bristol, Großbritannien – zur Integration in den ersten WOT-Demonstrator lieferte; Das Unternehmen ist dabei, zwei weitere zu liefern. Über diese Demonstrationsphase hinaus denkt Daher auch über die Industrialisierung der Holmfertigung nach und arbeitet an einer Analyse des Fertigungssystemdesigns (MSD), die den Betriebs-, Anlagen-, Ausrüstungs- und Personalbedarf für die Vollproduktion einer Single-Aisle-Produktion der nächsten Generation schätzt und simuliert Flugzeug.
Mehrere Rippen, verschiedene Größen
Die Bemühungen von Daher, Rippen zu entwickeln für das WOT-Programm war komplexer und anspruchsvoller. Das Unternehmen hat im Inneren des Flügels fünf Rippen unterschiedlicher Größe und Abmessungen entworfen; die anderen Rippen sind eine Kombination aus Aluminium- und Verbundkonstruktionen, einschließlich einer thermoplastischen Verbundrippe, die von GKN Aerospace entwickelt wurde.
In einem früheren Projekt mit Dassault Aviation hatte Daher seine Fähigkeit unter Beweis gestellt, relativ kleine Rippen aus thermoplastischen Verbundwerkstoffen zu entwickeln und herzustellen, erklärt Bailly. Mit WOT hatte das Unternehmen die Möglichkeit, seine Fähigkeiten auf die Entwicklung größerer (~2 Meter langer) und höher belastbarer Rippen auszuweiten.
Darüber hinaus strebt Daher gemäß den WOT-Zielen einen Technologiebereitschaftsgrad (TRL) von 6 bis Ende 2023 an. „Am Ende des WOT-Programms, wenn wir bewiesen haben, dass wir bei TRL 6 für große Rippen zwischen diesen liegen zwei Programme [WOT und Dassault Aviation] haben wir gezeigt, dass wir in der Lage sind, den gesamten Rippenbereich des Flügels abzudecken – das ist die Idee“, sagt Bailly.
„Wir haben dieses Programm genutzt, um verschiedene Möglichkeiten zur Herstellung von Teilen zu untersuchen, das mechanische Verhalten zu vergleichen und auch die Auswirkungen auf die Fertigung zu untersuchen. Parallel arbeiten wir an der Simulation, um das Bauteilverhalten wie Rückfederung oder Stanzwirkung vorherzusagen. Ziel ist es, Versuche während der Entwicklung und damit die einmaligen Kosten zu reduzieren“, sagt Condé.
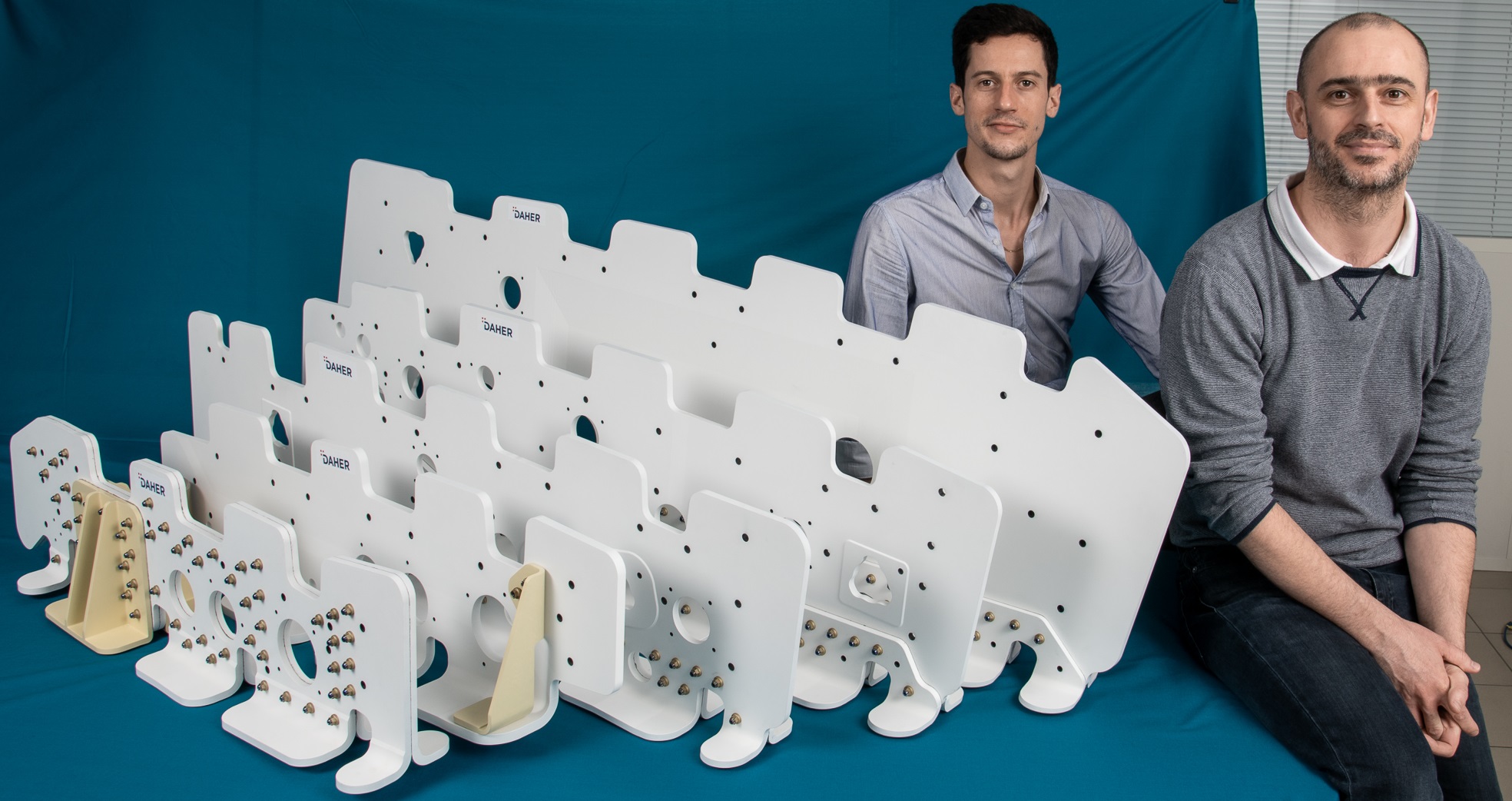
Wie beim Holm begann die Entwicklung auf Coupon-, Element- und Detailebene, gefolgt von der Herstellung von Kleinteilen, bevor die endgültigen Teile in Originalgröße gebaut wurden. Auf jeder Ebene wurden Tests durchgeführt, bemerkt Condé, einschließlich spezifischer Tests, die von Daher für Rippenmerkmale entwickelt wurden.
Für alle fünf Rippen entschied sich Daher schließlich, unidirektionale (UD) Kohlefaser-/Polyaryletherketon (PAEK)-Bänder mit niedrigem Schmelzpunkt zu verwenden, die von Toray Advanced Composites (Morgan Hill, Kalifornien, USA) mit Harz von Victrex (Cleveleys, Lancashire, Großbritannien) geliefert werden ). Zur Herstellung der Rippen werden flache Platinen mit AFP hergestellt, gefolgt von einer Ofenkonsolidierung – in einigen Fällen werden Materialien vor dem Stanzformen vorverfestigt. Bei Bedarf werden zusätzliche Flansche oder andere Komponenten mechanisch an den Stanzteilen befestigt.
Jede Rippe wurde entsprechend ihrer Position entlang des Flügels, Größenspezifikationen und Belastungsanforderungen (eine Tonne bis 50 Tonnen) konstruiert und ist somit in mehrfacher Hinsicht einzigartig. Die größte Rippe misst 2 Meter lang x 1 Meter breit. Unabhängig davon beginnt jeder mit einem flachen Steg, der zu einer „L“-Form gestanzt wird, um einen Flansch entlang der Unterseite des Teils zu bilden, wo er mit der Flügelhaut verbunden ist. Für zusätzliche Stabilität bestanden mehrere der Rippen aus zwei „L“-förmigen Komponenten, die mechanisch Rücken an Rücken befestigt wurden, um eine „T“-Form mit bidirektionalen Flanschen zu bilden.
Zu den speziellen Merkmalen gehörten eine Halterung (hergestellt aus duroplastischen Verbundwerkstoffen) zur Verbindung mit der an der Rippe befestigten Klappenschiene und eine Reihe von Löchern oder Lagenabfällen in bestimmten Rippen, um das Teilegewicht zu reduzieren.
„Während der gesamten Entwicklung mussten wir die Komplexität im Vergleich zu den Kosten managen“, sagt Bailly. „Das war schon immer unser Gedanke, etwas Einfaches, aber Kosteneffizientes zu machen.“ Einfachheit war auch aus Sicht der Produktionsrate von entscheidender Bedeutung, bemerkt Condé. „Wenn es zu komplex ist, ist das aus Kundensicht nicht wettbewerbsfähig, zu den sehr hohen Preisen, die sie haben wollen.“
Eine Herausforderung, die das Design komplizierter machte, war die relative Dicke jeder der Rippen – bis zu 12 Millimeter für die größte Rippe. Dickere Stoffe neigen beim Stanzformen dazu, sich zu knittern oder sich falsch zu formen, und dickere Teile können schwierig in die fertige Form zu bearbeiten sein.
Für die Bearbeitung verwendete Daher eine Mischung aus Wasserstrahlschneiden und mechanischer Bearbeitung, abhängig von den Anforderungen der Teile, um sowohl Probleme bei der Teiledicke zu verringern als auch die Temperatur zu steuern. Darüber hinaus konstruierte das Team an der 12 Millimeter dicken Rippe ein Ply-Drop-Fenster in die Mitte des Bauteils, um das Gesamtgewicht des Bauteils zu reduzieren. Neben der Lösung dieser potenziellen Probleme stellt Condé fest, dass das Ply-Drop-Fenster es Daher auch ermöglichte, „verschiedene Arten von Fertigungsmerkmalen an den Teilen auszuprobieren, um unser Verständnis des Verhaltens der Teile zu verbessern.“
Als noch größere Herausforderung erwies sich der Stanzformprozess. „Wir mussten uns eine neue Art des Stempelns vorstellen, um das Risiko von Falten zu verringern“, sagt Bailly. Daher entwickelte letztendlich eine proprietäre Methode zur Lösung des Problems.
Nächste Schritte
Über WOT hinaus evaluiert Daher alternative Herstellungsverfahren zur Herstellung thermoplastischer Rippen und plant, in Zukunft eine vollständige Produktionslinie für die Hochgeschwindigkeitsfertigung zu entwickeln.
Während die WOT-Demonstratoren beispielsweise Befestigungselemente verwenden, stellt Bailly fest, dass Daher durch die Übernahme des thermoplastischen Verbundwerkstoffs und des Induktionsschweißspezialisten KVE Composites (Den Haag, Niederlande) im Jahr 2019 die Fähigkeit besitzt, geschweißte Komponenten in Zukunft zu fertigen. „Wir arbeiten an einem weiteren, separaten Projekt, um ein höheres TRL-Niveau beim Schweißen von UD-Dickteilen zu erreichen [für den Einsatz in Single-Aisle-Flugzeugen der nächsten Generation]“, sagt er.
Daher arbeitet daher auch an der Entwicklung einer kompletten Produktionslinie, um in Zukunft thermoplastische Rippen zu produzieren. „Wir verbessern das Konzept wirklich und reduzieren die Anzahl der Maschinen, die für alle Aufgaben benötigt werden, und senken die Prozesskosten“, sagt Bailly mit dem Ziel, die Ziele der Großserienflugzeugproduktion zu erreichen.
Harz
- Covestro verstärkt Investitionen in thermoplastische Verbundwerkstoffe
- Graphenverstärkte thermoplastische Masterbatches auf den Markt gebracht
- Solvay erweitert die Kapazität von thermoplastischen Verbundwerkstoffen
- Thermoplastische Verbundwerkstoffe bei Oribi Composites:CW Trending, Episode 4
- Suprem erweitert thermoplastische Fähigkeiten
- Kordsa erweitert sein Angebot an thermoplastischen Prepregs
- Thermoplastische Verbundwerkstoffe von LANXESS in der Audi A8-Rücksitzschale
- EconCore Produktionstechnologie für thermoplastische Wabenplatten
- Thermoplastische Verbundwerkstoffe:Malerische Aussicht
- Schweißen von thermoplastischen Verbundwerkstoffen