Wiederaufbereitbare, reparierbare und recycelbare Epoxidharze für Verbundwerkstoffe
Für die meisten Verbundstrukturen in der Luft- und Raumfahrt war duroplastisches Epoxid aufgrund seiner hohen mechanischen Eigenschaften, seiner geringen Härtungsschrumpfung und seiner Temperatur- und Feuchtigkeitsbeständigkeit das bevorzugte Matrixharz, wodurch eine Umweltzerstörung während des Betriebs verhindert wird. Diese Vorteile resultieren aus der vernetzten Molekülstruktur des Epoxids, die während der Härtung gebildet wird. Diese wärmehärtende kovalente Chemie hat jedoch auch dazu geführt, dass herkömmliche gehärtete Epoxid-Verbundwerkstoffe nicht ohne weiteres umgeformt, umgeformt oder aufgelöst werden können, was das Recycling und die Reparatur erschwert.
In den letzten zehn Jahren dynamisch Es wurden Chemien entwickelt, bei denen kovalente Bindungen durch einen Stimulus wie Wärme ausgetauscht und neu angeordnet werden. Diese Polymere, die als „reversible Harze“ bezeichnet werden, haben Duroplast Eigenschaften unterhalb der Glasübergangstemperatur (Tg ), verhalten sich aber wie ein Thermoplast bei erhöhten Temperaturen, z. B. 80°C über Tg . CIDETEC (Donostia-San Sebastian, Spanien) ist ein Institut für angewandte Forschung, das seit 2013 an solchen Harzen arbeitet. Es hat thermomechanisch wiederverarbeitbare Epoxidharze und Verbundwerkstoffe auf Basis des Austauschs aromatischer Disulfide patentiert, die Wiederaufbereitung, Reparatur und Recycling ermöglichen (3R-Technologie) von ausgehärteten Kompositen. CIDETEC leitet nun 11 Partner im Horizon2020-Projekt AIRPOXY, um diese Technologie vom Technologiereifegrad (TRL) 3 auf TRL 5 zu reifen.
Dieses 42-monatige Projekt startete im September 2018 und wird 3R-Composite-Thermoformprozesse für die Großserienproduktion, die kostengünstige Reparatur und Montage von 3R-Composites durch Duroplastschweißen und verbesserte Klebeverbindungen vorantreiben. Diese Technologien werden in zwei Demonstratoren für die Luft- und Raumfahrt präsentiert:ein Verbundstoff-Fan-Cowl-Abschnitt mit einer Resin Transfer Moulded (RTM)-Haut und einer Querversteifung, die mit einer thermogeformten Längsversteifung verklebt ist; und einen Abschnitt einer Flügelvorderkante mit thermogeformten Rippen, die an eine Haut geschweißt sind, die unter Verwendung des gleichen qualifizierten RTM (SQRTM) hergestellt wurde. CIDETEC untersucht auch das Recycling von 3R-Verbundwerkstoffen und -Teilen und bewertet die Vorteile dieser Technologie gegenüber herkömmlichen Verbundwerkstoffen mithilfe von Methoden zur Lebenszyklusbewertung (LCA) und Lebenszykluskosten (LCC).
3R-Epoxid-Vitrimer
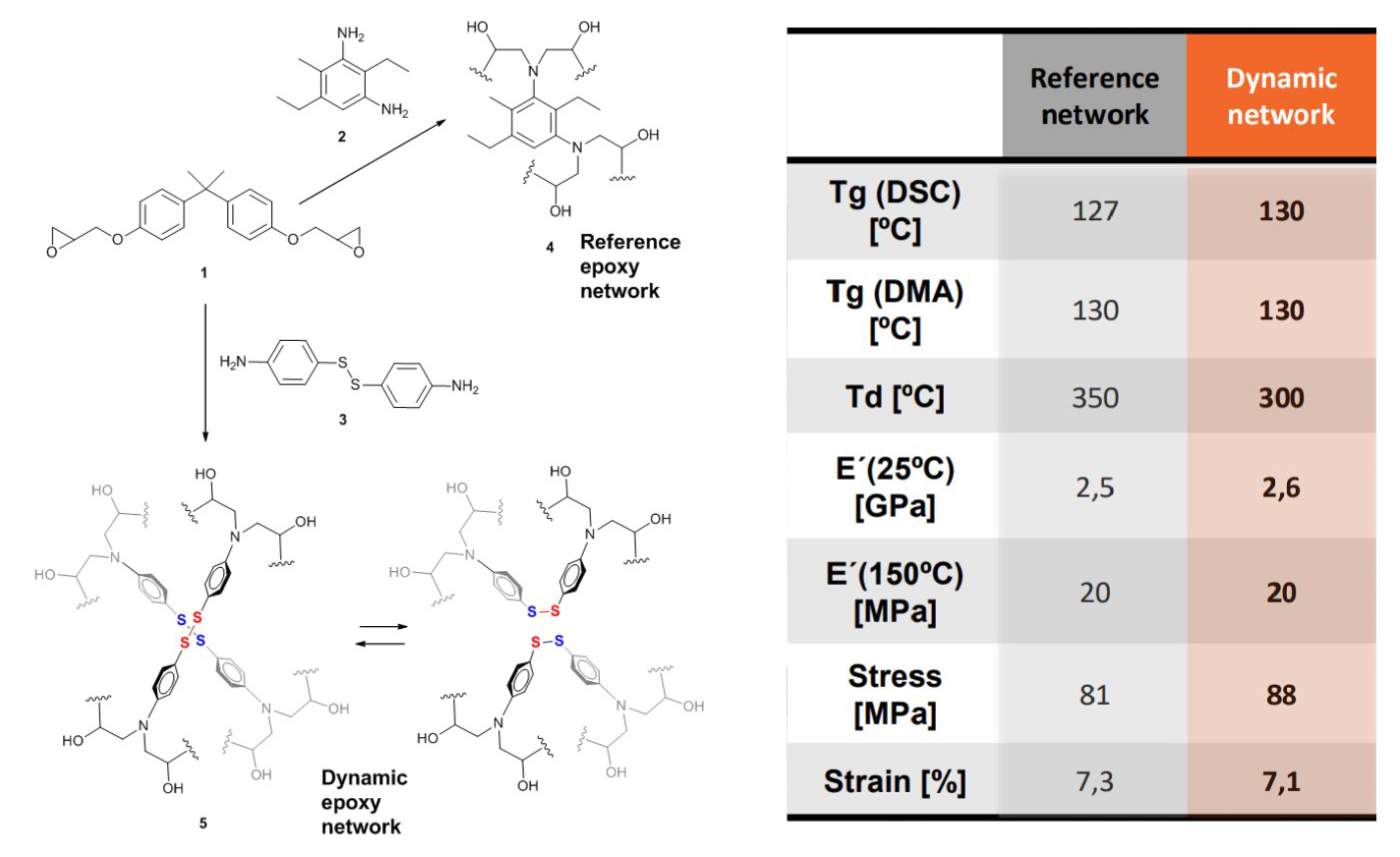
„Die dynamische Chemie lässt sich in zwei Typen einteilen:dissoziativ und assoziativ“, erklärt Alaitz Rekondo, Leiter Polymers and Composites bei CIDETEC. Sie stellt fest, dass bei der dissoziativen Chemie die Vernetzungen gebrochen werden. „Die Materialien werden also beim Thermoformen und Recycling aufgrund der gebrochenen Verbindungen ihre Integrität verlieren.“ CW hat über diese Art von Chemie über das thermoreversible vernetzte Harz von Evonik (Essen, Deutschland) auf Basis von Diels-Alder-Reaktionen und den Epoxidhärter Recyclamin von Connora geschrieben, der die Spaltung von Vernetzungen ermöglicht. Dies wird durch Eintauchen von Recyclamin-Verbundwerkstoffen in ein Lösungsmittel mit niedrigem pH-Wert bei erhöhter Temperatur erreicht, wodurch das Harz in ein thermoplastisches Epoxid umgewandelt wird, während die Endlosfaserverstärkung freigesetzt wird, sodass sowohl Harz als auch Fasern wiederverwendet werden können. Beachten Sie, dass Recyclamine 2019 von Aditya Birla Chemicals (Mumbai, Indien) erworben wurde und jetzt in recycelbaren Epoxidharzen von Epotec verwendet wird.
Die 3R-Harze von CIDETEC sind jedoch anders. „Unsere Chemie ist assoziativ , so dass die Querverbindungen nie unterbrochen werden“, bemerkt Rekondo. „Unsere Harze sind Vitrimere.“ CW stellte Vitrimere in Jeff Sloans Artikel aus dem Jahr 2020 über Mallinda (Denver, Colorado, USA) vor. „Die Harze verhalten sich also während der gesamten Verarbeitung wie ein Thermoplast“, erklärt sie, „durch den dynamischen Austausch beim Erhitzen – bei uns geschieht dies in aromatischen Disulfidbrücken – aber die Harze bleiben immer Duroplaste. Im Gegensatz zu vielen Vitrimeren benötigen 3R-Harze keine Katalysatoren. Aber wir können bei Bedarf Katalysatoren verwenden, um unterschiedliche Anforderungen für Fast-Cure/Snap-Cure-Zyklen oder die Aushärtung bei Raumtemperatur zu erfüllen.“
CIDETEC begann seine Vitrimer-Forschung mit weichen Elastomermaterialien auf der Suche nach selbstheilenden Eigenschaften. „Wir haben einen handelsüblichen dynamischen Härter verwendet und dann festgestellt, dass es sich auch um einen Härter für Epoxide handelt“, sagt Rekondo. Erste 3R-Epoxidharzformulierungen in Industriequalität zeigten Eigenschaften, die mit aktuellen Epoxidharzen für die Luft- und Raumfahrt vergleichbar sind (Abb. 1). „Angesichts des großen Potenzials von wiederaufbereitbaren und recycelbaren Harzen für die Luft- und Raumfahrt ist dies jetzt einer unserer Hauptforschungsbereiche.“
Nerea Markaide, die AIRPOXY-Projektkoordinatorin bei CIDETEC, erklärt, dass das Potenzial in der Tat groß ist:3R-Thermoformen ermöglicht die Herstellung von Verbundwerkstoffen in großen Stückzahlen, die im Vergleich zum Autoklaven deutlich schneller und kostengünstiger sind, 3R-Reparatur ist 50 % billiger als die aktuellen Bonded-Composite-Patch-Verfahren, 3R Schweißen reduziert die Montagekosten um 55 % im Vergleich zu aktuellen Klebeverbindungen und 3R-Klebeverbindungen sind robuster als herkömmliche Methoden. Letztendlich stellt sich CIDETEC eine Familie vor von 3R-Harzen und -Klebstoffen, um die Kosten und die Nachhaltigkeit der Produktion von Verbund-Flugzeugstrukturen zu verbessern.
Prepregging, RTM und Thermoformen
CIDETEC, verantwortlich für die Formulierung des 3R-Harzes in Luft- und Raumfahrtqualität, identifizierte die beste Harzformulierung für Demonstrationsversuche. Dieses System zur Harzinfusion oder RTM hat eine Tg von 170 °C trocken/150 °C nass, eine Viskosität von 200 Centipoise bei 70 °C und eine geringe Feuchtigkeitsaufnahme (2-3%). Es kann als Ein- oder Zweikomponentensystem mit einer typischen Aushärtung von einer Stunde bei 130 °C und einer Nachhärtung von 30 Minuten bei 180 °C formuliert werden.
CIDETEC verwendete diese 3R-Harzformulierung zur Imprägnierung von Chomarat (Le Cheylard, Frankreich) Fünf-Harness-Satin (5HS)-Gewebe aus Carbonfasern mit mittlerem Modul in einem kontinuierlichen Prepreg-Verfahren. Dieses Prepreg wurde dann vom Leibniz-Institut für Verbundwerkstoffe (IVW, Kaiserslautern, Deutschland) zur Herstellung von mehrlagigen flachen und 3D-geformten 3R-Laminaten im Continuous Compression Moulding (CCM) verwendet.
3R-Laminate wurden auch unter Verwendung von RTM hergestellt, um 5HS- und unidirektionale (UD)-Gewebe unter Verwendung von Prozessparametern zu infundieren, die für das 3R-Harz von Eurecat (Barcelona, Spanien) optimiert wurden. Ingeniería y Desarrollos en Composites (IDEC, Araba, Spanien) wird die RTM-Produktion in einer industriellen Umgebung unter Verwendung desselben Harzes demonstrieren, während die Versuche zur Herstellung der RTM-Haut- und Querversteifung für den 0,5 m x 0,5 m großen Lüfterhauben-Teilkomponenten-Demonstrator beginnen.
In der Zwischenzeit werden Coexpair (Namen, Belgien) und Sonaca (Charleroi, Belgien) Hexcel (Stamford, Connecticut, USA) HexPly 8552 gehärtetes Epoxid-Prepreg mit einer 3R-Harzfolie kombinieren, die das Schweißen (siehe unten) ermöglicht, um die gebogene Nase zu produzieren Struktur für den 1 Meter langen Leading-Edge-Teilkomponenten-Demonstrator mit dem gleichen qualifizierten RTM (SQRTM)-Prozess (siehe „SQRTM ermöglicht netzförmige Teile“).
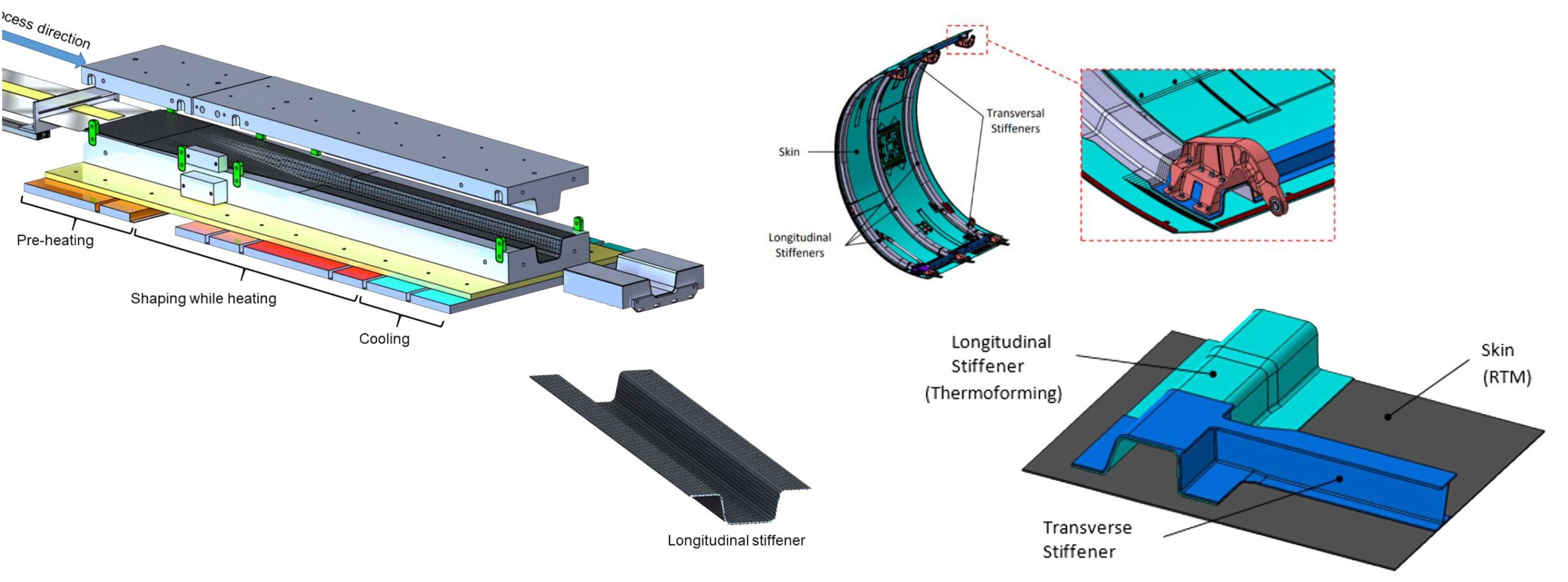
Abb. 2. Demonstrator für Lüfterhauben-Unterkomponenten
IDEC wird die Verklebung von 3R-Laminatversteifungen und Haut mit 3R-Klebefolie beaufsichtigen. IDEC wird die Haut- und Querversteifung mit RTM herstellen, während EireComposites die Längsversteifung mit CCM herstellen wird. Bildnachweis:IVW (links und rechts unten) und IDEC (rechts oben)
Sowohl Prepreg- als auch RTM-Flat-3R-Laminate wurden ebenfalls verwendet, um das Thermoformen zu demonstrieren. Die verwendeten Simulationen basierten auf von Altair Engineering (Antony, Frankreich) entwickelten mikro- und makroskopischen Finite-Elemente-Modellen (FEMs), IVW-optimiertem diskontinuierlichem Formpressen (DCM oder Stanzen) und CCM-Prozessen für 3R-Materialien. EireComposites (County Galway, Irland) verwendet DCM, um die Rippen und Längssteifen für die Demonstratoren herzustellen, während IVW Längssteifen mit CCM produziert. Bei beiden Verfahren wird mit ca. 20 bar Druck auf ca. 210°C erhitzt und anschließend das Teil im geschlossenen Werkzeug abgekühlt (Abb. 2). Tests unter der Leitung von Eurecat haben gezeigt, dass thermogeformte 3R-Verbundteile die typischen Anforderungen an Aeroverbundwerkstoffe erfüllen, einschließlich eines Hohlraumgehalts von <2 %. Es stellte sich auch heraus, dass die interlaminare Scherfestigkeit (ILSS) für die thermogeformten Laminate mit 5HS ungefähr 80% (43 MPa) derjenigen für die RTM-Teile (54 MPa) betrug.
Kleben, Schweißen, SHM und Reparatur
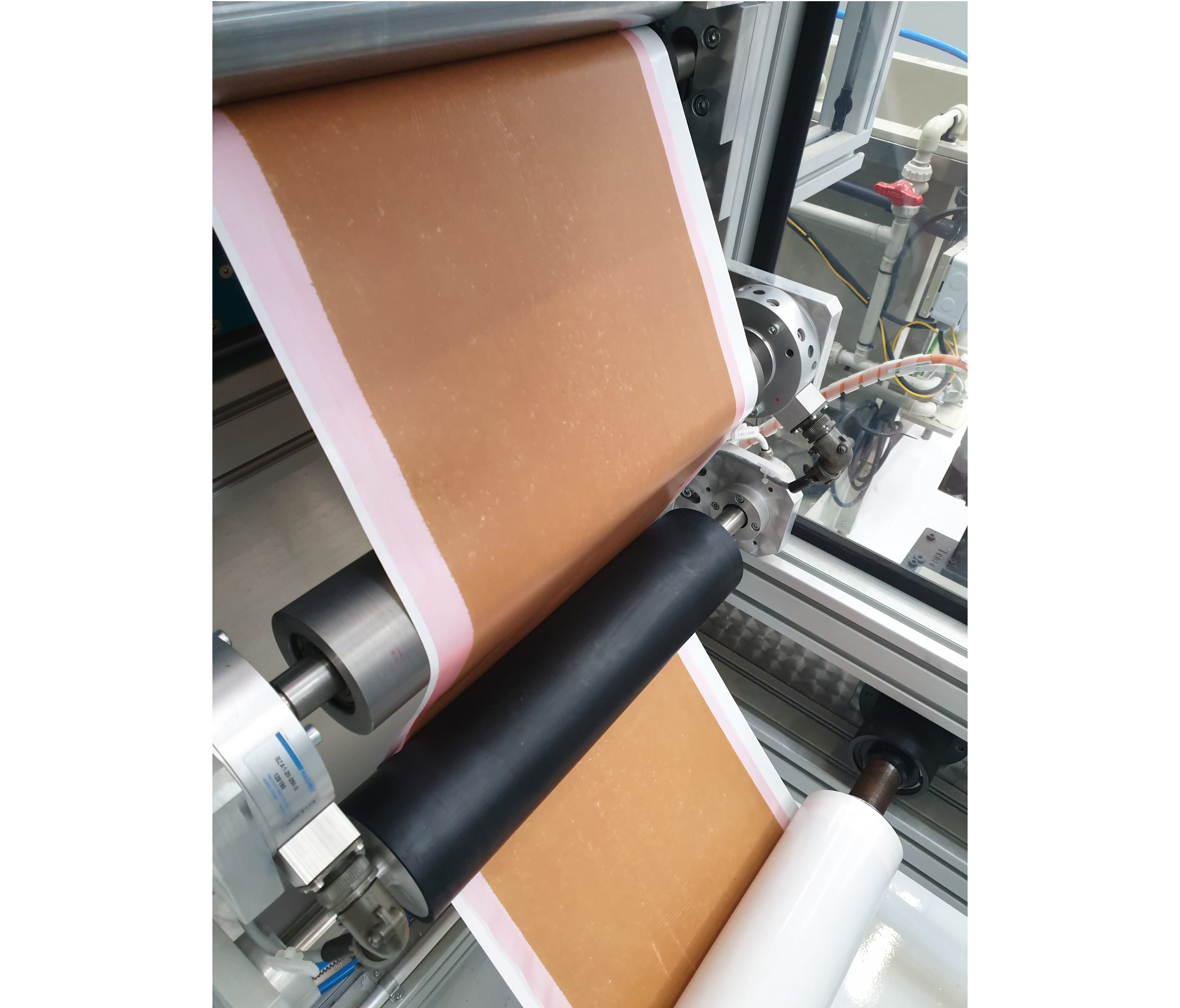
CIDETEC hat das 3R-Harz neu formuliert, um es für die Verklebung zu optimieren und im Februar 2020 die ersten 3R-Klebefilme produziert die Neuordnung der Disulfidbindung, die die Integrität der Verbindung verbessert.“ IDEC wird die Verklebung von Versteifungen und Haut mit 3R-Klebefolie überwachen, um den Demonstrator für die Lüfterhauben-Teilkomponente zu produzieren (Abb. 2).
Die dynamische Chemie von 3R-Harzen ermöglicht auch die Bildung kovalenter Bindungen zwischen zwei 3R-Verbundlaminaten, wenn sie mit Hitze und Druck verbunden werden – von CIDETEC als Duroplastschweißen beschrieben. Dies wird von EireComposites verwendet, um gestanzte 3R-Laminatrippen mit der SQRTM-Nase für den Flügelvorderkanten-Demonstrator zu verbinden (Abb. 3). Für die 3R-Laminate wurden von IVW optimierte Schweißparameter entwickelt. Bemerkenswert ist, dass die mit dem kommerziellen Prepreg hergestellte SQRTM-Nase einen zusätzlichen 3R-Harzfilm an der Oberfläche integriert, um das Verschweißen der beiden Stege zu ermöglichen. „Der Prozess zur Durchführung des Schweißens auf Demonstratorebene wird derzeit untersucht“, bemerkt Rekondo.
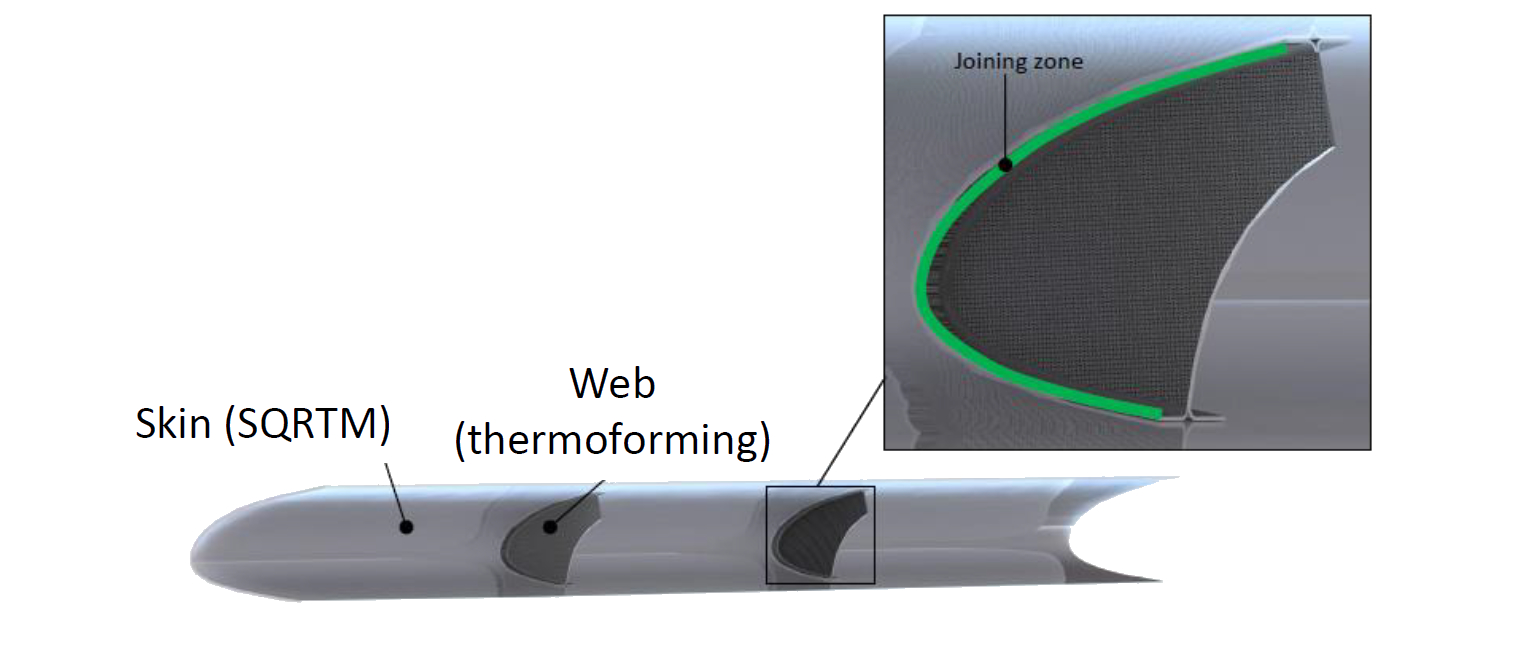
Im Arbeitspaket 4 – Structural Health Monitoring (SHM) und Instandsetzung – untersuchte das IVW die Reparierbarkeit von Defekten, wie Delaminationen und gelöste Schweißnähte in 3R-Verbunden. Das Team reparierte Delaminationen, indem es den Defektbereich auf die Reparaturtemperatur von 220 °C erhitzte und einen konstanten Konsolidierungsdruck von 20 bar anlegte, während die Temperatur konstant gehalten wurde.
Das Composites and Smart Materials Lab (CSML) der Universität Ioannina (Ioannina, Griechenland) bewertete diese Reparaturtechnik als erfolgreich unter Verwendung mechanischer Tests sowie verschiedener zerstörungsfreier Bewertungstechniken (NDE), einschließlich Phased-Array-Ultraschall, Infrarotthermografie, Schallemission, Impedanzspektroskopie und das elektrische Widerstandsänderungsverfahren (ERCM). Diese innovative plattformübergreifende NTE-Methodik lieferte eine detaillierte Schadenserkennung und wichtige Informationen über die Entwicklung des Schadensprozesses.
In Bezug auf die Reparatureffizienz zeigten die 3R-Verbundwerkstoffe in ILSS-Tests eine Wiederherstellung ihrer ursprünglichen mechanischen Eigenschaften von 72 % nach der Reparatur und eine Wiederherstellung von ≈ 90 % in Schlagtests mit niedriger Geschwindigkeit bei 9 und 15 Joule Aufprallenergie.
Recycling und AIRPOXY 2
Obwohl das Recycling im Rahmen des AIRPOXY-Projekts nicht angesprochen wird, hat CIDETEC gezeigt, dass Schrott gemahlen und umgeformt werden kann, beispielsweise durch Formpressen bei 210°C. Ähnlich wie bei Connora können 3R-Laminate jedoch auch in eine Lösung getaucht werden, die ein mildes Reduktionsmittel enthält, das, wie Rekondo erklärt, „das dynamische Netzwerk auflöst und somit das Harz auflöst, so dass es ausgefällt und wiedergewonnen werden kann“ ein Pulver.“ Sie stellt fest, dass dieser Auflösungsprozess durch Erhitzen auf Temperaturen bis zu 100°C beschleunigt werden kann. „Das Pulver könnte dann für eine zweite Composite-Anwendung wiederverwendet werden, aber dies wird noch erforscht“, sagt Rekondo.
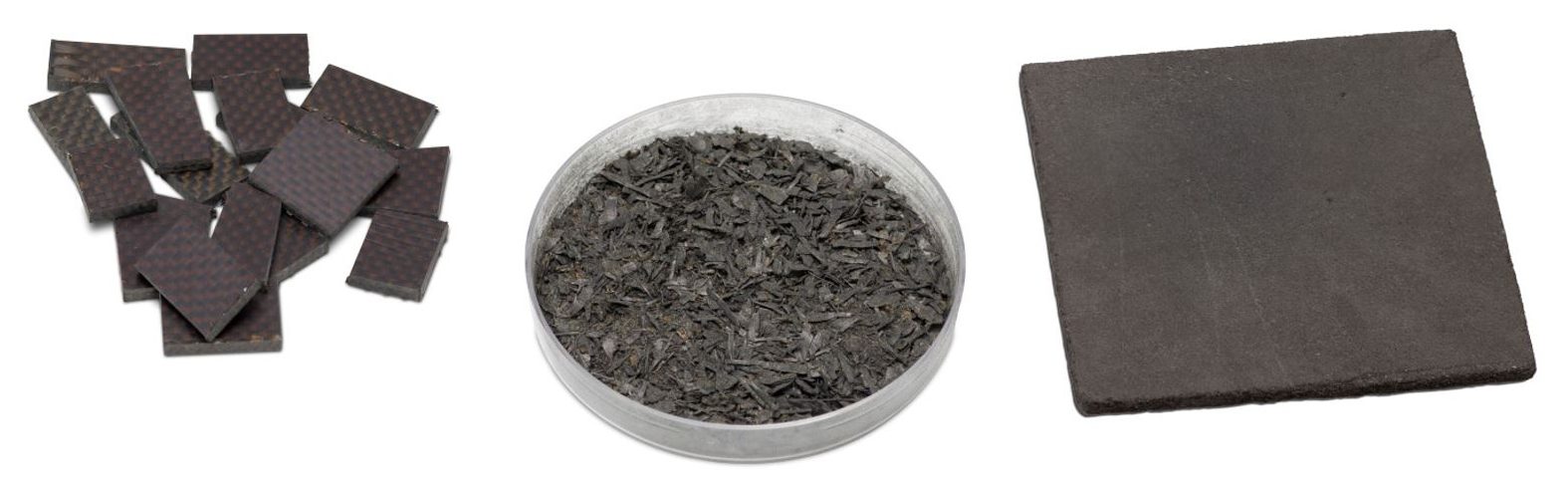
„Für das Recycling von Schrott halten wir zwei bis drei Zyklen für möglich“, fährt sie fort. „Aber für echte End-of-Life-Anwendungen wird es nach vielen Jahren im Einsatz immer eine Verwitterung des Teils und andere Verschlechterungen des Materials geben. In diesen Fällen denken wir, dass nicht mehr als ein Recycling möglich ist. Die zweite Anwendung des Materials wird in Ordnung sein, aber wahrscheinlich keine dritte. Dies ist Teil dessen, was wir jetzt testen, zunächst für 3R-Kunststoffe in Industriequalität, während wir die vollständige Charakterisierung von 3R-Materialien abschließen.“
Die beiden Demonstratoren werden noch in diesem Jahr fertiggestellt, sagt Markaide. „Wir werden diese dann mechanisch testen, einschließlich Schadens- und Reparaturbewertungen. Unser Ziel ist es, bis 2022 TRL 5 zu erreichen.“ Und dann was? „Wir planen ein weiteres Projekt, AIRPOXY Part II“, sagt sie, „um die Optimierung der Verarbeitung und die mechanische Charakterisierung sowie die Validierung und Zertifizierung von Materialien und Prozessen fortzusetzen. Wir werden ein zweites Projekt brauchen, um die Technologie auf den Markt zu bringen.“
Die Fähigkeit zum Thermoformen und Schweißen von Epoxid-Luft- und Raumfahrtteilen scheint eine Technologie zu sein, die praktisch für die urbane Luftmobilität geschaffen wurde. „Wir müssen jetzt überlegen, wie wir das bereitstellen können, was diese Sektoren benötigen“, fügt Markaide hinzu und weist darauf hin, dass eine Roadmap für die Kommerzialisierung tatsächlich eines der Ergebnisse von AIRPOXY Teil I sein wird. „Recycling ist auch eine notwendige Lösung, die noch nicht für Verbundwerkstoffe, wird es aber in Zukunft sein. Wir wollen bereit sein.“
Harz
- Preiserhöhung für großvolumige Harze
- PHA-basierte Harze für Blasfolien, Spritzguss und Thermoformen
- Holzbearbeitung und Epoxidharz
- Graphen- und Polymerverbundstoffe für Superkondensatoranwendungen:ein Rückblick
- Anpassung von Ultraschallsensoren für die Optimierung und Steuerung von Verbundwerkstoffprozessen
- Sicomin liefert Epoxidharze für das Flugfahrzeugkonzept von ENATA Aerospace
- Hexion führt Zweikomponenten-Epoxidlösung für die Herstellung von Verbundwerkstoffen in der Luft- und Raumfahrt ein
- AMRC und Prodrive arbeiten zusammen, um die Herstellung recycelbarer Verbundkomponenten voranzutreiben
- PES-Additiv erhöht die Bruch- und Mikrorissbeständigkeit in Epoxidverbundwerkstoffen
- Konsortium für thermoplastische Verbundwerkstoffe strebt die Massenproduktion für die Automobil- und Luftfahrtindustrie an