Maßgeschneidertes Verfahren produziert jede Minute ein Verbundbremspedal
Die Tier 1 Boge Rubber &Plastics Group (Damme, Deutschland) produziert die ihrer Meinung nach leichtesten, kostengünstigsten und stärksten Vollverbund-Bremspedale der Welt und die ersten in kommerzieller Produktion. Wie im FOD vom Januar beschrieben (siehe „Thermoplastische Verbundstruktur ersetzt Metalle auf sicherheitskritischen Bremspedalen“) produziert der Zulieferer derzeit eine Viertelmillion Bremspedale pro Jahr für vier Fahrzeugplattformen deutscher Autohersteller und das System könnte bis zu 1 Millionen Pedale jährlich. Dies ist von Bedeutung, da die Pedale strukturell sind, dieselben strengen Leistungsanforderungen erfüllen müssen wie herkömmliche Stahl- und Aluminiumelemente und die Konstruktionen drei verschiedene Arten von glasfaserverstärkten thermoplastischen Verbundwerkstoffen aufweisen.
Drei Materialien erhöhen die Fasereffizienz
Um die Pedale leicht, dünn, kostengünstig und in der Lage zu halten, anspruchsvolle OEM-Spezifikationen zu erfüllen, verwendet Boge Endlosglasfaser-Organoblech als Schalenstruktur, um die Hauptlasten des Teils zu tragen, die bis zu 3.000 Newton betragen können. Organoblech-Zuschnitte werden auf Maß zugeschnitten geliefert, mit zwei oder drei Lagen vollkonsolidiert vom Lieferanten Lanxess Deutschland GmbH (Köln, Deutschland). Um die Hauptlastpfade auf dem Organoblech-Rohling zu verstärken, fügt Boge Streifen aus unidirektionalen (UD) Glasfaserbändern (geliefert von Celanese Corp., Irving, Texas, USA) in Ausrichtungen und Lagen basierend auf Finite-Elemente-Simulationsergebnissen hinzu. Dazu verwendet Boge modifizierte Software und Materialkarten, die das Unternehmen mit seinen Lieferanten entwickelt hat, basierend auf Spannungs-/Dehnungskurven, die für jedes Material unter Temperatur- und Feuchtigkeitsbedingungen gemessen wurden, die von OEM-Kunden spezifiziert wurden. Um funktionale Geometrie hinzuzufügen, verwendet Boge umspritzte Schnittglasfaser-Compounds (von mehreren Lieferanten), um Strukturrippen und Befestigungselemente bereitzustellen.
Alle Materialien verfügen über Matrizen aus vorgefärbtem schwarzem Polyamid 6 (PA6), einem zähen Polymer, das in der Automobilindustrie weit verbreitet ist. Sollten die OEM-Spezifikationen dies erfordern, hat Boge auch die Möglichkeit, eine höhertemperaturige, weniger hygroskopische PA6/6-Matrix in der Overmolding-Masse zu verwenden, da beide Polymere ähnlich genug sind, um sich miteinander zu verbinden. Durch die Verwendung von drei verschiedenen Arten von Verbundwerkstoffen mit Glasverstärkung in drei verschiedenen Formen ist Boge in der Lage, Fasern genau dort zu platzieren, wo sie für die Leistungsanforderungen erforderlich sind, und gleichzeitig ein Over-Engineering zu vermeiden. Der weitere Effekt dieses Hybrid-Verbund-Ansatzes besteht darin, dass er den Materialverbrauch, die Nennwandstärke, die Zykluszeit und die Gesamtkosten der Teile reduziert.
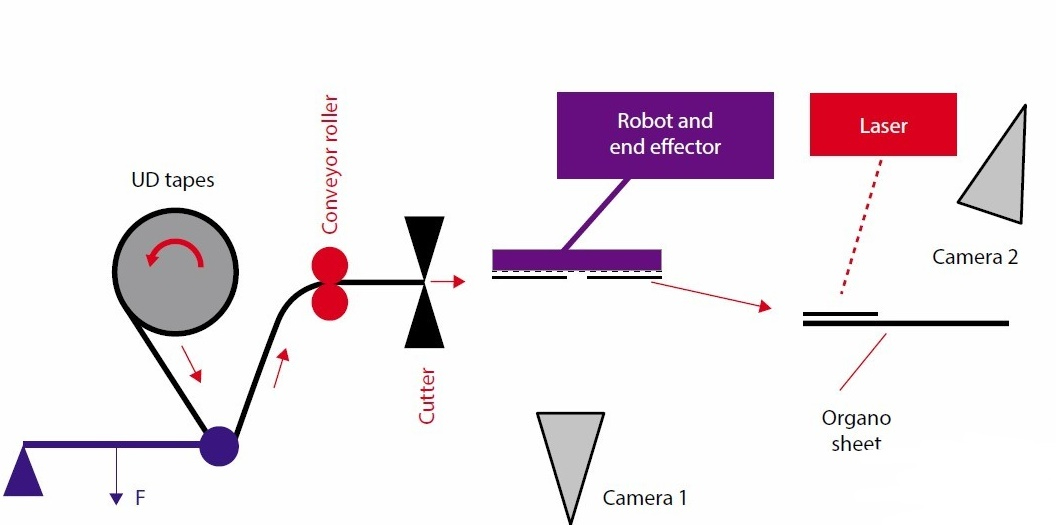
Prozessschritte und Ausrüstungskriterien
Partnerschaft mit dem Automatisierungs-/Fließbandentwickler M.A.i. GmbH &Co. KG (Kronach, Deutschland) hat Boge einen dreistufigen Produktionsprozess entwickelt, der schnell und effizient ist und qualitätsgeprüfte Teile zu erschwinglichen Kosten produziert. Bei der Entwicklung von Prozessen und Geräten stellte das Team eine Reihe von Anforderungen. Um die Teilekosten niedrig zu halten, mussten die Unternehmen erstens eine effektive Gesamtzykluszeit von ~1 Minute einhalten. Um dies zu erreichen, wäre eine Automatisierung erforderlich, um einen reibungslosen Materialtransport durch die Fertigungszelle zu gewährleisten.
Zweitens:Während die Organoblech-Zuschnitte vorgestapelt, vollständig konsolidiert und vorgeschnitten (konturiert) geliefert werden, benötigte das Team aufgrund der Anforderungen verschiedener Pedaldesigns Flexibilität, um Bandstreifen unterschiedlicher Länge an verschiedenen Stellen und Richtungen zu schneiden, auszurichten und zu platzieren, um die Hauptlastpfade der Organoblechschale. Um die Kosten niedrig zu halten, wurde wiederum ein maßgeschneiderter Tapelegeprozess entwickelt, der ein hohes Maß an Flexibilität und Kontrolle sowie Geschwindigkeit bietet.
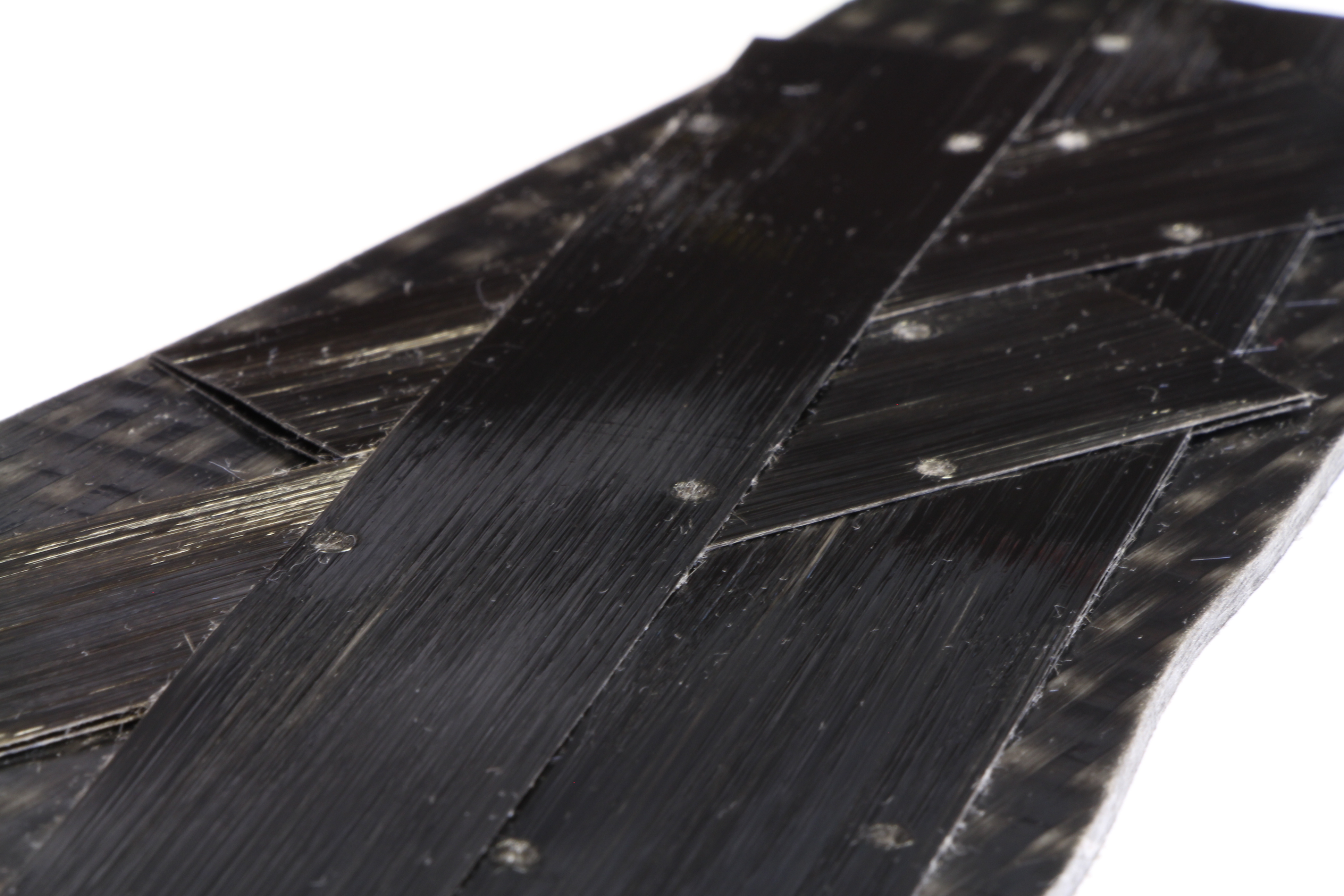
Zu Beginn des Prozesses enthält die Fertigungszelle zwei Stapel vorgeschnittener Organoblech-Rohlinge in Kassetten und vier Gatter UD-Bänder gleichzeitig. Zunächst nimmt ein Roboter einen konturierten Rohling aus Organoblech auf und bewegt ihn auf die Arbeitsfläche. Gleichzeitig wird UD-Band ausgegeben und auf die gewünschte Länge geschnitten. Die Streifen werden dann auf ein Vakuumband gelegt, das sie während des Vorschubs des Förderers an Ort und Stelle hält. Anschließend zupft ein Roboter mit einer umlaufenden Pick-and-Place-Einheit (Endeffektor) einen Streifen nach dem anderen vom Vakuumband und eine Kamera prüft jeden Streifen auf Qualität, Abmessung und Position. Wenn alle vier Teile aufgenommen sind, fährt der Roboter in den Arbeitsraum und beginnt, einen Streifen nach dem anderen an der durch die bildbasierte Positionskorrektur ermittelten Position und Position auf dem Organoblech-Zuschnitt zu platzieren. Während jeder Streifen positioniert wird, wird er durch mehrere Punktschweißungen, die von einem Laser erzeugt werden, daran gehindert, sich zu verschieben. In der Zwischenzeit werden weitere Klebestreifen geschnitten und auf das Vakuumband gelegt und der Vorgang wiederholt sich, bis alle für ein bestimmtes Bremspedaldesign erforderlichen Klebebänder gestapelt und in der richtigen Position auf dem Organoblech geheftet sind.
Das System, das diesen Tailored-Fibre-Rohling produziert, wird zu 100 % numerisch gesteuert, wobei jeder Aspekt des Betriebs für maximale Flexibilität vollständig programmierbar ist. Bei jedem Schritt erkennen Kameras oder andere Sensoren, die mit dem Online-Qualitätskontrollsystem (QC) des Systems verbunden sind, alle Kanten und Positionen von Klebebandstreifen und der Organoblechschale und vergleichen geometrische Daten für diese Materialien mit bekannten Parametern, um sicherzustellen, dass jedes Material positioniert, wo es sein muss.
Um die Produktionsgeschwindigkeit hoch zu halten, bewegt sich der Tailored-Fiber-Rohling als nächstes in einen Infrarotofen, um beide Materialien zu erhitzen, kurz bevor die Bänder auf das Organoblech drapiert/vorgeformt/verfestigt werden. Ein spezielles Antioxidanspaket in Klebeband- und Organoblech-Harzsystemen verhindert thermische Schäden. Als nächstes wird der heiße Rohling schnell in den Drapier-/Vorformhohlraum bewegt, wo Hochdruck verwendet wird, um den Rohling in eine U-Kanalform zu formen, während eine hochwertige Oberfläche gewährleistet wird. Das QC-System überwacht wiederum die Konsolidierungs- und Preformingqualität über Zeit, Temperatur und Druck.
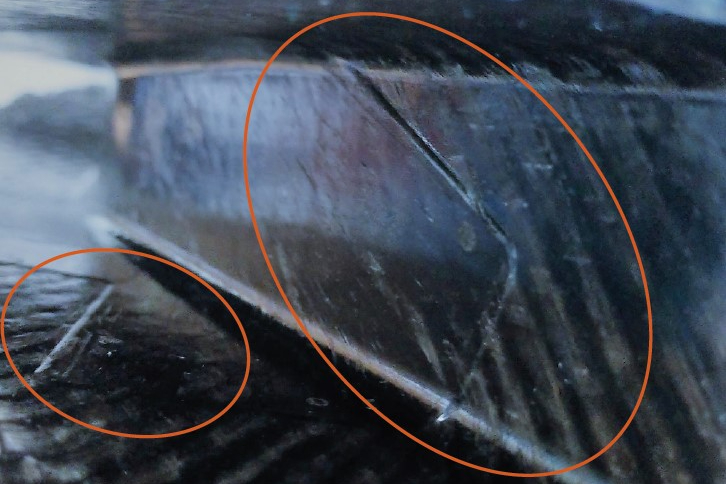
Schließlich wird das noch warme und drapierte Perform in ein Spritzgießwerkzeug geschoben und dort mit einem Kurzglas/PA-Compound umspritzt, um zusätzliche Geometrie wie eine komplexe Rippenstruktur auf der Unterseite zu erzeugen. Nach der Entformung erfolgt eine schnelle, automatisierte Besäum- und Sichtprüfung. Es ist keine Farbe oder andere Oberflächenveredelung erforderlich. Die endgültige Pedalgröße beträgt ungefähr 350 x 90 x 60 Millimeter. Vor dem Verlassen der Fertigungszelle wird an jedem Pedal ein eindeutiger QR-Code angebracht, um ihn wieder mit den Fertigungs- und Materialdaten für dieses Pedal im Qualitätssystem zu verknüpfen. Nach der Montage erfolgt ein Funktionstest des Pedals in seiner Halterung und eine Roboterendkontrolle. Wenn das Gerät erfolgreich ist, wird ein weiterer QR-Code an der fertigen Bremspedalbaugruppe angebracht, um eine vollständige Rückverfolgbarkeit jedes Pedals und zusätzlicher Komponenten vor dem Versand an den OEM zu gewährleisten.
Da Bremspedale sicherheitskritische Teile sind und die anspruchsvollen OEM-Leistungs- und Qualitätsanforderungen erfüllen müssen, haben Boge und seine Partner mehrere ausfallsichere Mechanismen in das Industrie 4.0-konforme QC-System eingebaut, um schnell und genau zu überprüfen, ob die Spezifikationen bei jedem Schritt eingehalten wurden der Prozess. QC-Daten werden gespeichert und jedes Pedal erhält eine eindeutige Identifikationsnummer in Form eines QR-Codes, um eine 100-prozentige Rückverfolgbarkeit von Material, Schichten und Prozessbedingungen bei der Herstellung dieses Teils zu gewährleisten.
Die von Boge hergestellten Vollverbund-Bremspedale sind etwa halb so schwer wie Pedale aus Metall. Außerdem verbessern sie die Fahrhaptik für Verbraucher, sind am Ende ihrer Lebensdauer zu 100 % recycelbar und erfüllen oder übertreffen die Festigkeitsanforderungen für etablierte Stähle.
Harz
- Die beliebtesten Verfahren zur Herstellung von Verbundwerkstoffen
- Kryogenes Entgraten und Entgraten
- Erstes Vollkunststoff-Bremspedal für batterieelektrische Sportwagen
- Solvay erweitert die Kapazität von thermoplastischen Verbundwerkstoffen
- Thermoplastisches Rad nimmt die raue Straße
- Verbundwerkstoff für Architekturverkleidungen enthüllt
- In Arkansas bessere Composite-Bikes herstellen
- Funktionsweise des CMC-Prozesses
- Die 4 kritischen Dinge, die jeder Bediener von Abkantpressen wissen sollte
- 4 Dinge, die jeder Bediener einer Abkantpresse im Schlaf wissen sollte