Mehrschichtige thermoplastische Bänder, AFP und Harzinfusion für demokratischere Verbundwerkstoffe
Novotech (Neapel, Italien) begann als Spin-off der Universität Neapel „Federico II“ in Süditalien, die 1992 von Professor Leonardo Lecce gegründet wurde. „Wir haben Unternehmen der allgemeinen Luftfahrt unterstützt und F&E-Dienstleistungen in ganz Italien erbracht“, sagt Lecce der jetzt CEO von Novotech ist. „Wir haben Strukturanalysen für Flugzeugteile erstellt und auch bei der Flugzeugentwicklung geholfen.“
Novotech liegt in der Nähe des Leonardo-Werks, das die Rumpfsektionen aus Verbundwerkstoffen für die Boeing 787 herstellt. Seit 2014 konzentriert sich Novotech auf Verbundwerkstoffe. Es kaufte eine automatisierte Faserplatzierungszelle (AFP) von Coriolis Composites (Queven, Frankreich) und entwickelte aus Autoklaven ( OOA) Verarbeitung, einschließlich Harzinfusion und Herstellung thermoplastischer Verbundwerkstoffe, mit besonderer Expertise in der in-situ-Konsolidierung mit AFP.
Novotech hat an zahlreichen Industrieforschungsprojekten teilgenommen, darunter:
- MESEMA (Magnetoelastische Energiesysteme für noch mehr elektrische Flugzeuge)
- SARISTU (Smart Intelligent Aircraft Structures)
- ASAM (Erweiterte Simulation von Flugzeugmechanismen)
- LAMITECH (Innovative Testmethoden für die automatische Schichtung von Hybridverbundwerkstoffen)
- PROALATECH (Strukturelle Charakterisierung und Analyse von Reparaturlösungen innovativer CFK-Leitwerke)
- GESICHT (Friendly Aircraft Cabin Environment)
- AIRGREEN 2 - CLEAN SKY 2 (Entwicklung innovativer Tragflächenkonzepte und -methoden für Regionalflugzeuge der nächsten Generation)
- SCHWESTER-CHECK (Untersuchung und Integration eines innovativen Systems für die zerstörungsfreie Inspektion von AFP)
- TRINITI - CLEAN SKY 2 (Multi-Material Thermoplastische Hochdruck-Stickstofftanks für Flugzeuge)
- NHYTE - H2020 (Neue hybride thermoplastische Verbund-Flugzeugstrukturen, hergestellt von OOA)
„Wir haben auch eine besondere Beziehung zu Cytec in Großbritannien, um neue Verbundwerkstoffe und -verfahren zu entwickeln“, sagt Lecce. Beachten Sie, dass Cytec von Solvay übernommen wurde und der referenzierte Standort Solvay Composite Materials in Heanor, Großbritannien, ist – ein Standort mit einer langen Innovationsgeschichte, einschließlich des kürzlich im Rahmen des RAPM-Programms getesteten Doppelmembran-Formungsprozesses. „Unsere letzte derartige Aktivität war die Entwicklung eines thermoplastischen OOA-Prozesses, der eine neue, innovative Presse verwendet, die PEEK (Polyetheretherketon) und PEI (Polyetherimid) zu einem neuen Verbundmaterial kombiniert.“ Dieses neue Material, die neue Ausrüstung und das neue Verfahren wurden jetzt in einem Flugzeugstringer aus kohlenstofffaserverstärktem Kunststoff (CFK) demonstriert, der mithilfe von AFP-In-situ-Konsolidierung und -Schweißen im Rahmen des NHYTE-Projekts hergestellt wurde.
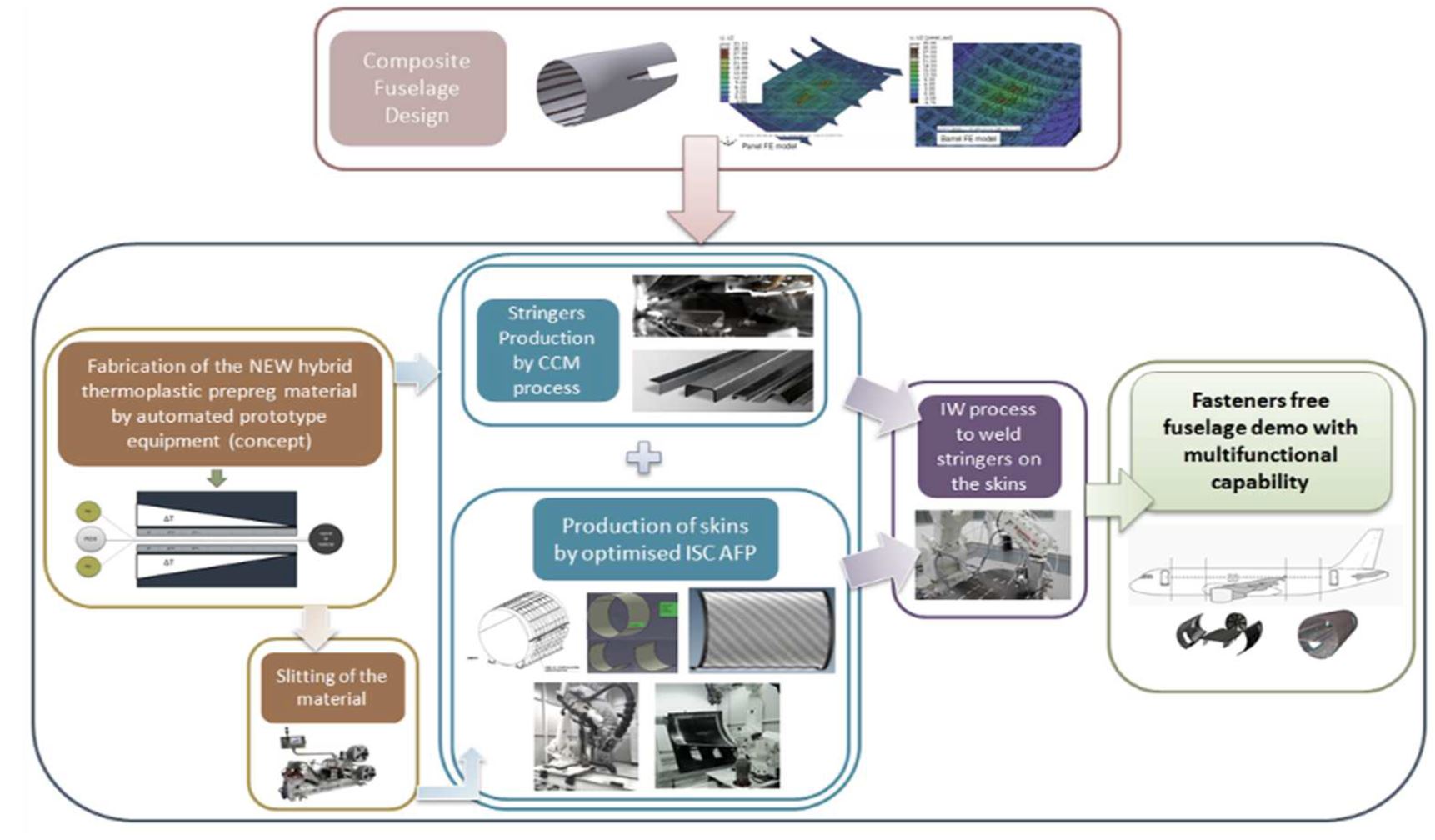
NHYTE
NHYTE ist ein vom Horizon 2020-Programm der Europäischen Kommission finanziertes Forschungsprojekt, das von Mai 2017 bis Oktober 2020 durchgeführt wird. „Bei NHYTE geht es darum, amorphe Bindungen zu nutzen, um nachhaltige Temperatur- und Prozessbedingungen für thermoplastische Verbundwerkstoffe zu ermöglichen“, erklärt Dr. Marco Barile, NHYTE-Projektkoordinator und CTO von Novotech. Dieses amorphe Bonding (siehe Diagramm unten) ist ein Konzept, das von einem anderen NHYTE-Partner patentiert wurde, der Aerostructures Division von Leonardo (Rom, Italien), die mehrere Produktionsstätten in Süditalien hat.
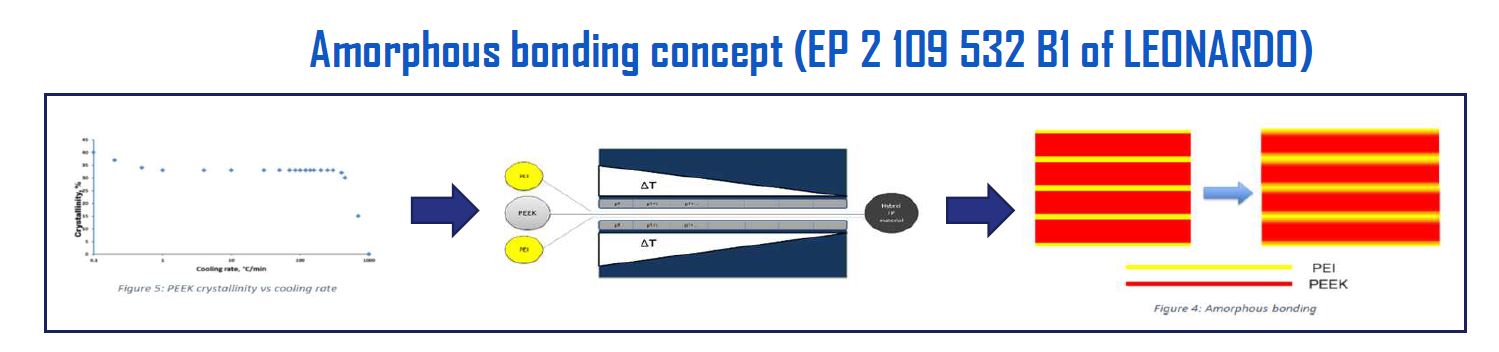
Bildnachweis:NHYTE-Projekt
„Mit dem in NHYTE entwickelten Material können wir die aktuellen Materialbeschränkungen mit der AFP-In-situ-Konsolidierung (ISC) von thermoplastischen Verbundwerkstoffen (TPC) überwinden. Anstatt die teilkristallinen PEEK-Polymere bei Temperaturen knapp unter 400 °C zu verarbeiten, können wir für die amorphe PEI-Schicht knapp über die 215 °C Glasübergangstemperatur (Tg) heizen. Das Schmelzen und Abkühlen von PEI ist auch schneller und muss im Vergleich zu PEEK nicht so kontrolliert werden.“ Barile stellt fest, dass dieses Konzept andere amorphe Thermoplaste verwenden kann. PEI wurde ausgewählt, weil es gut an PEEK haftet, ein Material, das sich in mehreren AFP-Flugzeugstrukturdemonstratoren bewährt hat.
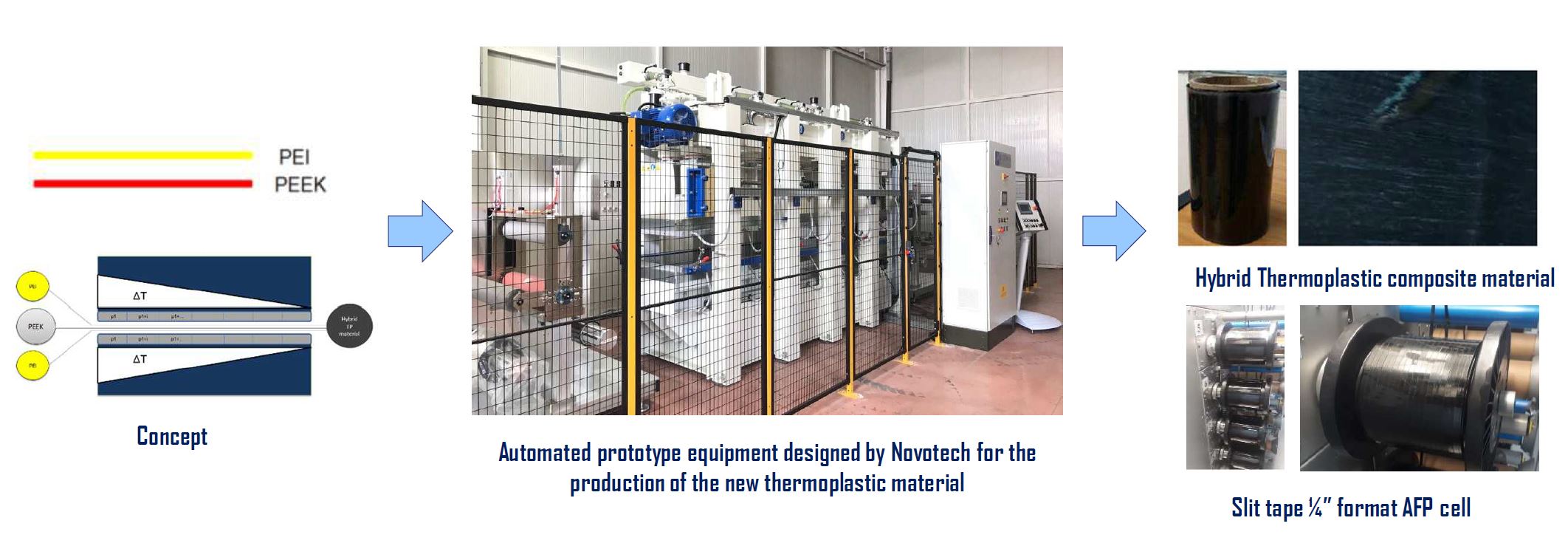
Dieses in NHYTE entwickelte neue Material wurde in einer von NOVOTECH entwickelten kontinuierlichen Presse hergestellt. Orma Macchine (Bergamo, Italien) lieferte den Pressenkörper und COMEC Innovative (Chieti, Italien) lieferte die Auf- und Abwickelmodule. „Diese Presse kann eine kontinuierliche Materialrolle herstellen, die wir dann für die Verwendung in einer AFP-Maschine zu Schlitzband aufschneiden“, sagt Barile. Drei verschiedene Materialien kommen von links in die Presse, wie im Bild oben zu sehen. „Wir haben PEI oben und unten und dann PEEK in der Mitte“, erklärt Barile.
Als teilkristallines Polymer bietet PEEK die für Primärstrukturen notwendigen hohen mechanischen Eigenschaften, während die amorphen PEI-Schichten ein schnelles und einfaches Aufschmelzen für die Verklebung ermöglichen. „Wir steuern den Druck und die Abkühlung des Materials entlang der Pressplatten, beginnend bei ca. 400 °C am Anfang der Presse bis unter 200 °C am Ende der Presse. Das Ergebnis ist ein Material, das eine Kombination der drei Eingabeschichten ist.“
Dieses neuartige thermoplastische Klebeband wird bereits bei der Herstellung verfestigt, sodass es beim AFP nur noch erhitzt werden muss, um die PEI-Schichten für die amorphe Verklebung aufzuschmelzen und zu verdichten. Das Ergebnis ist ein Laminat aus vollverfestigtem PEEK zu PEI-Band und PEI zu PEI-Schichten, wie im Leonardo-Patent gezeigt. Dieser AFP-Prozess stellt weniger Hürden im Vergleich zu aktuellen AFP-ISC mit PEEK- und PEKK-(Polyetheretherketon)-Bändern. Wie in Teil 2 meines 2018er-Features zur In-situ-Konsolidierung erklärt, erfordert die aktuelle AFP-ISC das Erhitzen des Bandes und des Substrats auf Schmelztemperatur, das Auflegen des Bandes auf das Substrat und das anschließende Verfestigen mit einer Walze, damit der Kühlprozess genau gesteuert wird, was ermöglicht die halbkristallinen Polymere, um eine ausreichend hohe Kristallinität (30-40%) und geringe Hohlräume (<3-5%) für strukturelle Eigenschaften zu erreichen.
Kritiker von AFP ISC behaupten, es sei zu langsam – eine Ablegerate von 60-100 mm/s gegenüber 600-700 mm/s für das „zweistufige“ Verfahren, das schnelles AFP-Layup gefolgt von einem zweiten Schritt im Ofen oder Autoklaven bis zur vollständigen Auflösung umfasst konsolidieren/glühen thermische Spannungen im Laminat. „Mit unserem Material können Sie AFP-Auftragsraten erreichen, die nicht so langsam sind wie bei der typischen in-situ-Konsolidierung, und die während der AFP erforderliche Erwärmung kann auch unter 300 °C gehalten werden“, sagt Barile. „Man kann die Leistungslücke mit Standardmaterialien schließen, die wir jetzt haben.“ Hier vergleicht Barile die AFP-ISC von thermoplastischen Verbundwerkstoffen mit duroplastischen Verbundwerkstoffen, die in den Flugzeugen Boeing 787 und Airbus A350 verwendet werden. „Bei großen Komponenten wie Rumpfsektionen liegt das Problem in der Erschwinglichkeit bei der Verwendung von Autoklavenhärtung. Thermoplaste ermöglichen einen kostengünstigeren Produktionsprozess, aber mit den derzeit auf dem Markt erhältlichen Materialien in Luft- und Raumfahrtqualität haben Sie hohe Temperaturen und langsame AFP-Raten. Unser Ansatz hilft, diese Probleme zu lösen. Über die kontinuierliche Presse können wir etwa 30 Prozent Kristallinität im Band erreichen. Somit haben Sie diese Kristallinität im Teil und arbeiten nur mit der amorphen Schicht während der AFP. Obwohl dies noch ein experimentelles Material ist, das verbessert werden kann, ist das Ziel des NHYTE-Projekts ein einstufiger Herstellungsprozess, der in strukturellen Luft- und Raumfahrtanwendungen verwendet werden kann.“
Tape- und AFP-Optimierung
„Hier bei Novotech wurden die ersten mehrschichtigen Bandmaterialien hergestellt“, sagt Barile. Diese Bänder verwendeten Sabic (Riad, Saudi-Arabien) Ultem 1000 ungefüllte Schlitzfolie für das PEI und APC-2/AS4 kohlenstofffaserverstärktes PEEK-Band von Solvay. Die Gesamtdicke betrug 0,26 mm und umfasste PEI-Schichten, die entweder 1 oder 2 mil (0,001 oder 0,002 Zoll) dick waren. In der ersten Projektphase wurden mehrere Coupons beider Varianten auf interlaminare Scherfestigkeit (ILSS) getestet, um den Herstellungsprozess von thermoplastischen Hybridmaterialien zu validieren. Kleine Coupons wurden auch vom NHYTE-Partner Applus Laboratories (Barcelona, Spanien) auf eine vollständige Palette mechanischer Eigenschaften getestet, einschließlich Zug- und Druckfestigkeit und -modul, Kompression bei offenem Loch (OHC), Spannung bei gefüllten Löchern, Kompression nach Aufprall (CAI), kaum sichtbar Impact Damage (BVID) und Eigenschaften nach Flüssigkeitskonditionierung.
„Wir hatten nicht die gleiche Erfahrung wie die Lieferanten von thermoplastischen Verbundbändern, sodass die Qualität des Materials verbessert werden kann. Zum Beispiel variiert das Faservolumen von niedrig bis hoch durch die Dicke, was die Eigenschaften des Bandes und Laminats, einschließlich ILSS, beeinflusst. Aber NHYTE sollte das Konzept demonstrieren, was wir getan haben.“
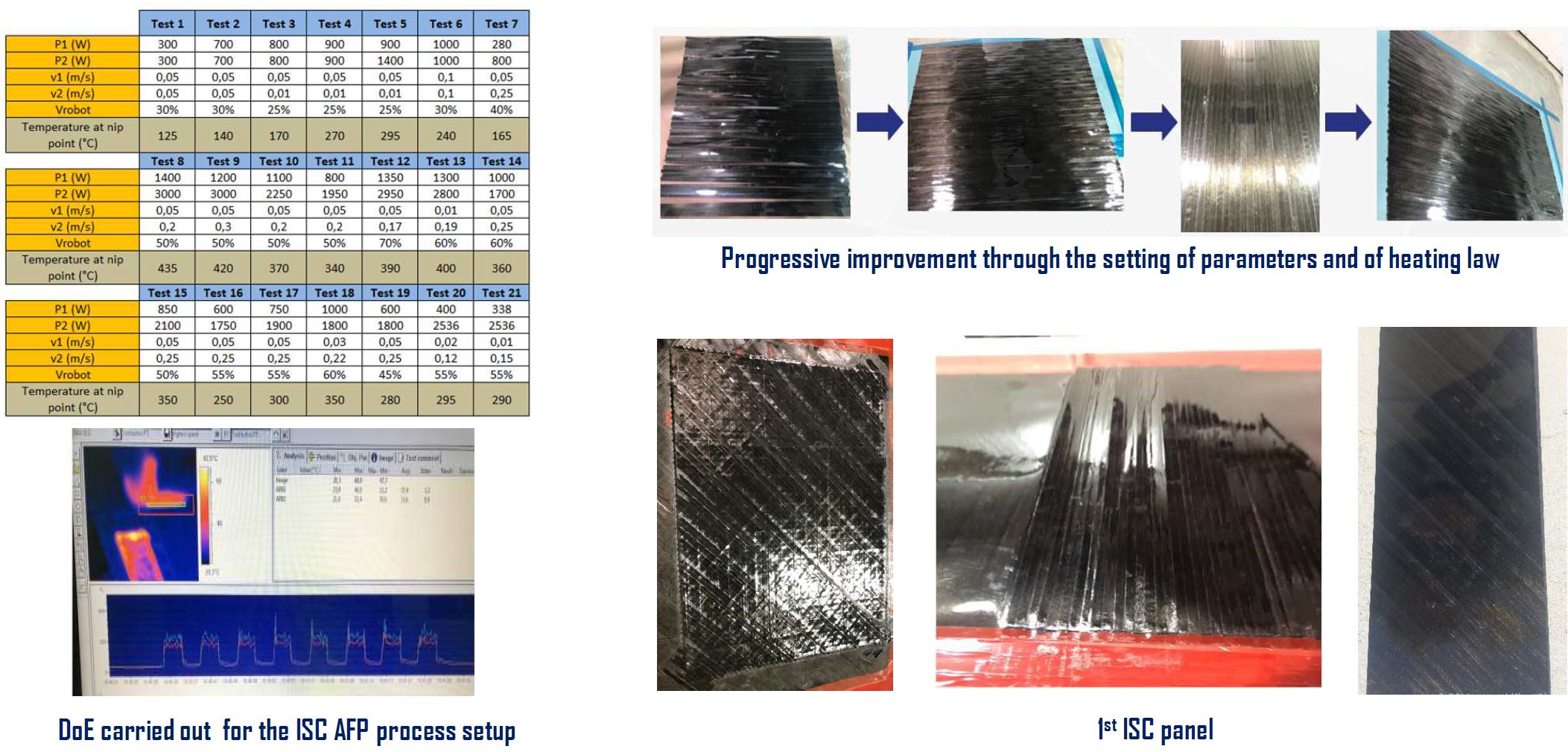
Wie in den obigen Bildern zu sehen ist, erforderte die Optimierung des AFP-Prozesses für das neue Material erhebliche experimentelle Arbeit. „Wir haben auch einen Design-of-Experiment-Ansatz (DOE) verwendet, um die AFP-Parameter zu optimieren, und ein Werkzeug wurde vom NHYTE-Partner University of South Brittany (USB, Lorient, Frankreich) entwickelt, um die Laserheizlast durch prädiktive numerische Simulation zu verbessern.“ notiert Barile.
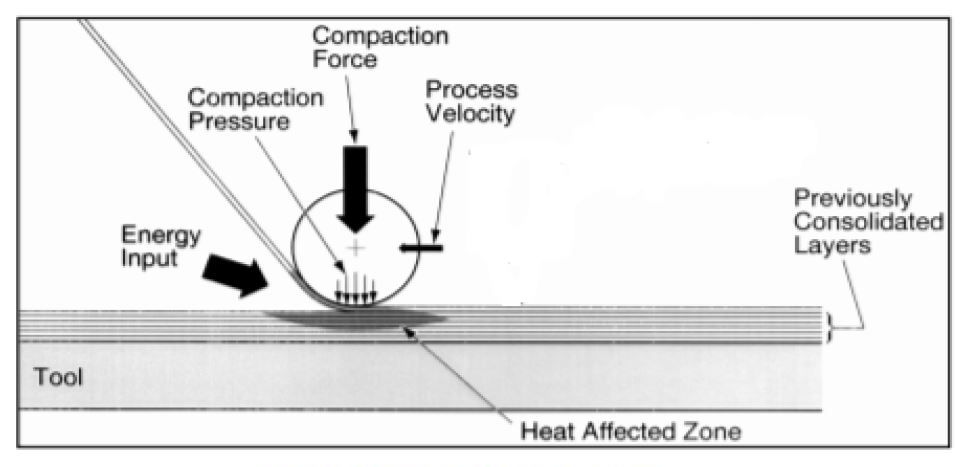
Diese Simulation wurde zuerst auf dem APC-2-Band verwendet, um die Qualität des Vorhersagewerkzeugs zu überprüfen, und dann auf das neue, mehrschichtige Material angewendet. Ein Paper zu dieser Arbeit wurde zur Veröffentlichung in der Zeitschrift Composite Structures eingereicht . „Sie modellieren die Wärmeleitfähigkeiten am Nip-Punkt“, sagt Barile. „Wir verifizieren dann experimentell, was in der numerischen Simulation vorhergesagt wurde. Dies ist erforderlich, um den besten Kompromiss zwischen Ablegegeschwindigkeit, Schmelzfluss der Polymere und Alterung [Kochen] der Verbundschicht zu bestimmen. Es ist ein Gleichgewicht mehrerer Variablen während des in-situ-Konsolidierungsprozesses. Wir betrachten den Temperaturabfall des einlaufenden Bandes auf das bereits auf dem Werkzeug platzierte Band. Wenn Sie diese Temperaturänderung bewältigen, können Sie die Restspannung im Laminat reduzieren. Also haben wir daran gearbeitet, die Temperaturschwankungen während des Ablegens zu bewerten. Sie müssen die Heizung entsprechend der Form des Pfades und der Ausrichtung des Plättchens anpassen.
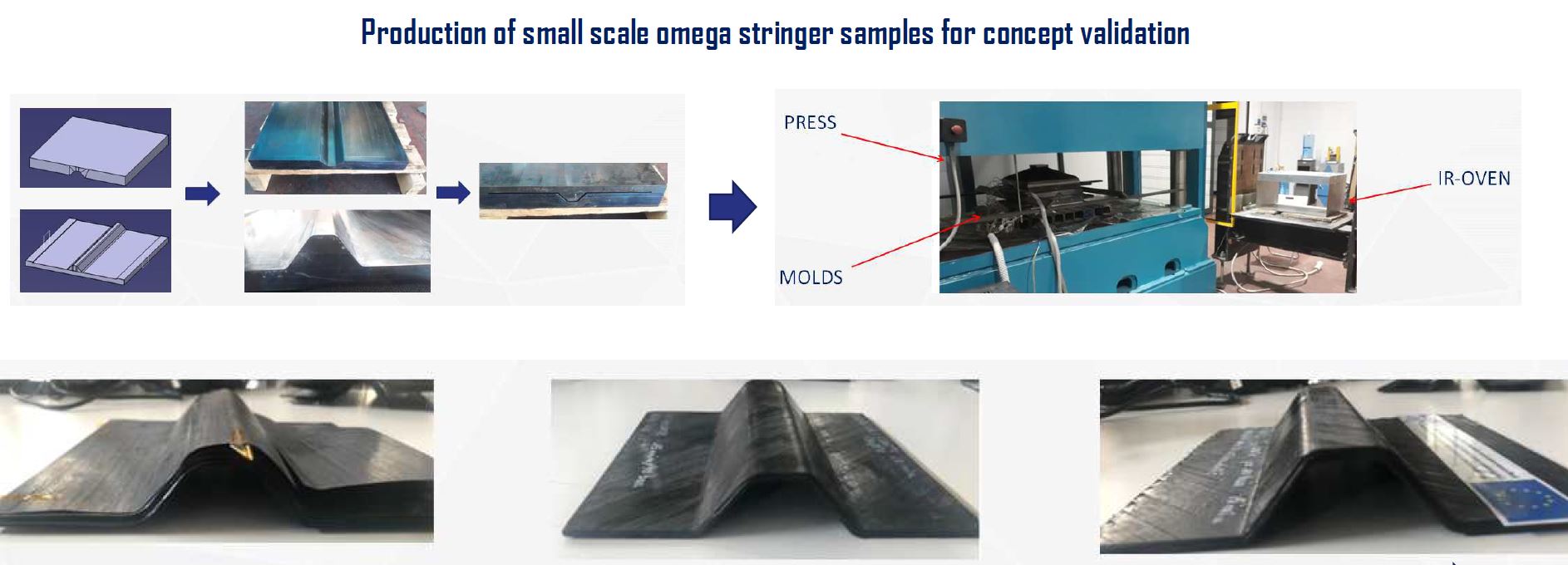
String- und Rumpfdemonstratoren
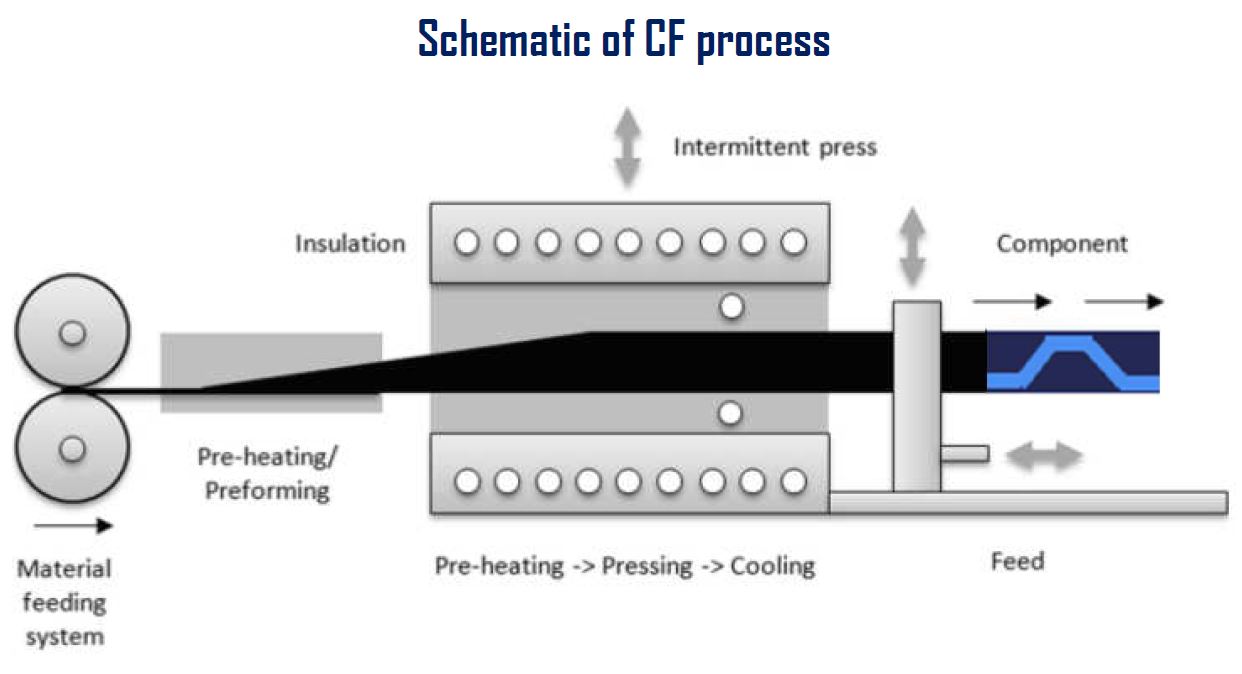
Der nächste Schritt bestand darin, Stringer-Demonstratoren herzustellen, zunächst als Kleinstmuster mit einer stationären Presse und dann als Demonstratoren eines kontinuierlichen Stringer-Umformprozesses, um die Anforderungen für die industrielle Teilefertigung zu verifizieren. Diese Stringer wurden dann mittels Induktionsschweißen, das von der Forschungs- und Entwicklungsorganisation CETMA (Brindisi, Italien) entwickelt wurde, an einem AFP-Rumpfhautpaneel-Demonstrator befestigt.
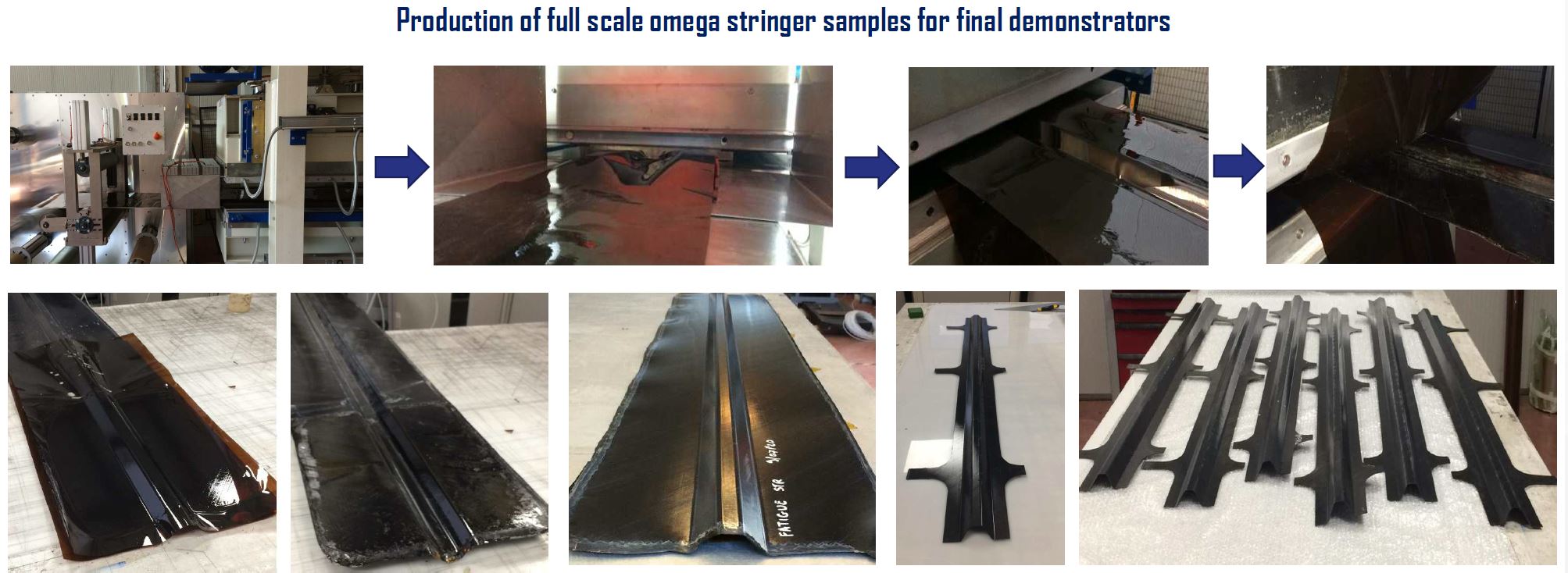
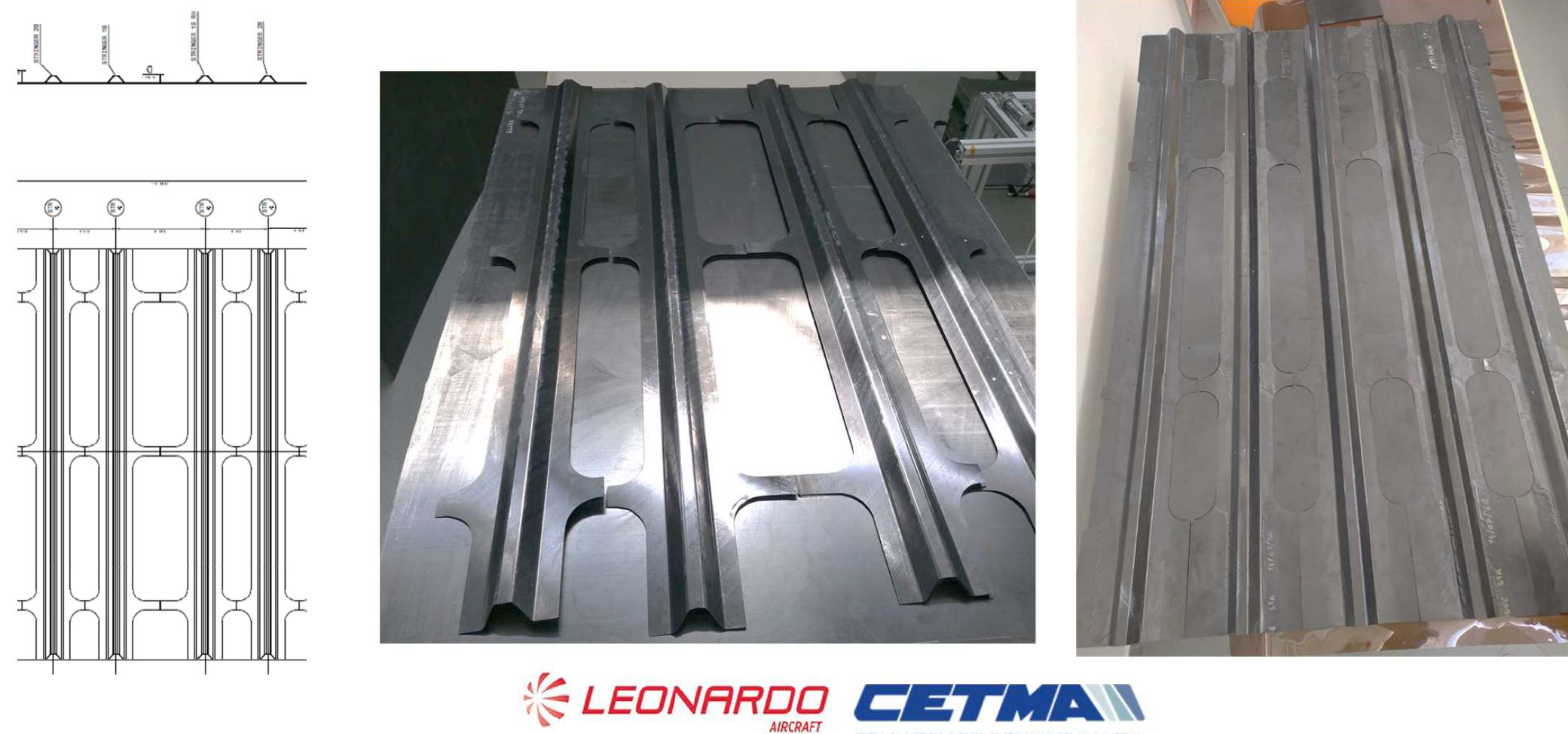
Hat das neue Mehrschichtmaterial Vorteile beim Induktionsschweißen gebracht? „Im Grunde hat es das gleiche verarbeitet“, sagt Barile. „Allerdings war es für CETMA nicht einfach, Parameter für den Schweißprozess zu definieren, da unser neues Material im Vergleich zu Standardbändern einen geringeren Anteil an Kohlefasern hat.“ Die Stringer-Demonstratoren und der letzte Rumpfpaneel-Demonstrator wurden dann von Applus getestet. Die NHYTE-Projektpartner University of Bath (Bath, Großbritannien) und Leonardo Aircraft verwendeten ebenfalls NDI, um die Qualität von Paneelen und Stringern zu bewerten.
„Wir haben viele Coupons und Kleinteile sowie den großen Demonstrator gemacht“, sagt Barile. „Die Testergebnisse von Applus sind sehr gut, wenn man bedenkt, dass der Herstellungsprozess im Vergleich zum heutigen Standard niedriger ist. Wir haben 20-25% geringere Festigkeits- und Steifigkeitseigenschaften als derzeit verfügbare thermoplastische Bandmaterialien, aber wir haben Verbesserungen des Prozesses identifiziert, die dazu beitragen sollten, dies zu verbessern.“
NHYTE endete am 30. Oktober 2020. „Unsere Idee ist es, mit einem neuen Projekt fortzufahren, das alle Verbesserungen einbezieht, die wir im Sinn haben“, sagt Barile. „Wir haben bewiesen, wie das Material hergestellt und verarbeitet wird, indem wir AFP-In-situ-Konsolidierung, kontinuierliches Umformen und Induktionsschweißen verwenden. Jetzt müssen wir weiter optimieren für die Industrialisierung.“ Novotech strebt an, mit demselben Konsortium fortzufahren, das mit neuen Partnern angereichert ist.
Insbesondere arbeitet Leonardo auch an der Verbesserung der AFP-In-situ-Konsolidierung durch Induktionsschweißen und TPC-Band, das schnell erhitzt und abgekühlt werden kann. Darüber hinaus haben Forscher des IMDEA Materials Institute (Madrid, Spanien) und der FIDAMC (Madrid, Spanien), die seit vielen Jahren führend in der AFP-In-situ-Konsolidierung ist, gerade ermutigende Ergebnisse zu PEI/PEEK-Mehrschichtverbundwerkstoffen veröffentlicht. Weitere technische Artikel finden Sie in den Veröffentlichungen von NHYTE.
SWING-Projekt
Der Smart Wing for New General Aviation (SWING) ist ein Projekt, das mit Unterstützung von Piaggio Aerospace (Villanova d’Albenga, Italien) begann und vom italienischen Ministerium für wirtschaftliche Entwicklung (MISE) kofinanziert wird. Das italienische Projektkonsortium umfasst neben Novotech das Technologieentwicklungsunternehmen Protom (Neapel) als Koordinator, Laer Aeronautical Manufacturing (Airola), A. Abete Aerostructures (Nola) und den Raumfahrtspezialisten ItalSystem (Avellino). Eines der SWING-Ziele besteht darin, automatisierte Verfahren aus Verbundwerkstoffen aus dem Autoklaven (OOA) – einschließlich AFP und Flüssigharzinfusion (LRI) – für die kostengünstige und nachhaltige Produktion kleinerer Flugzeuge mit Piaggios P.180 Avanti Frontflügel als Demonstrationsplattform.
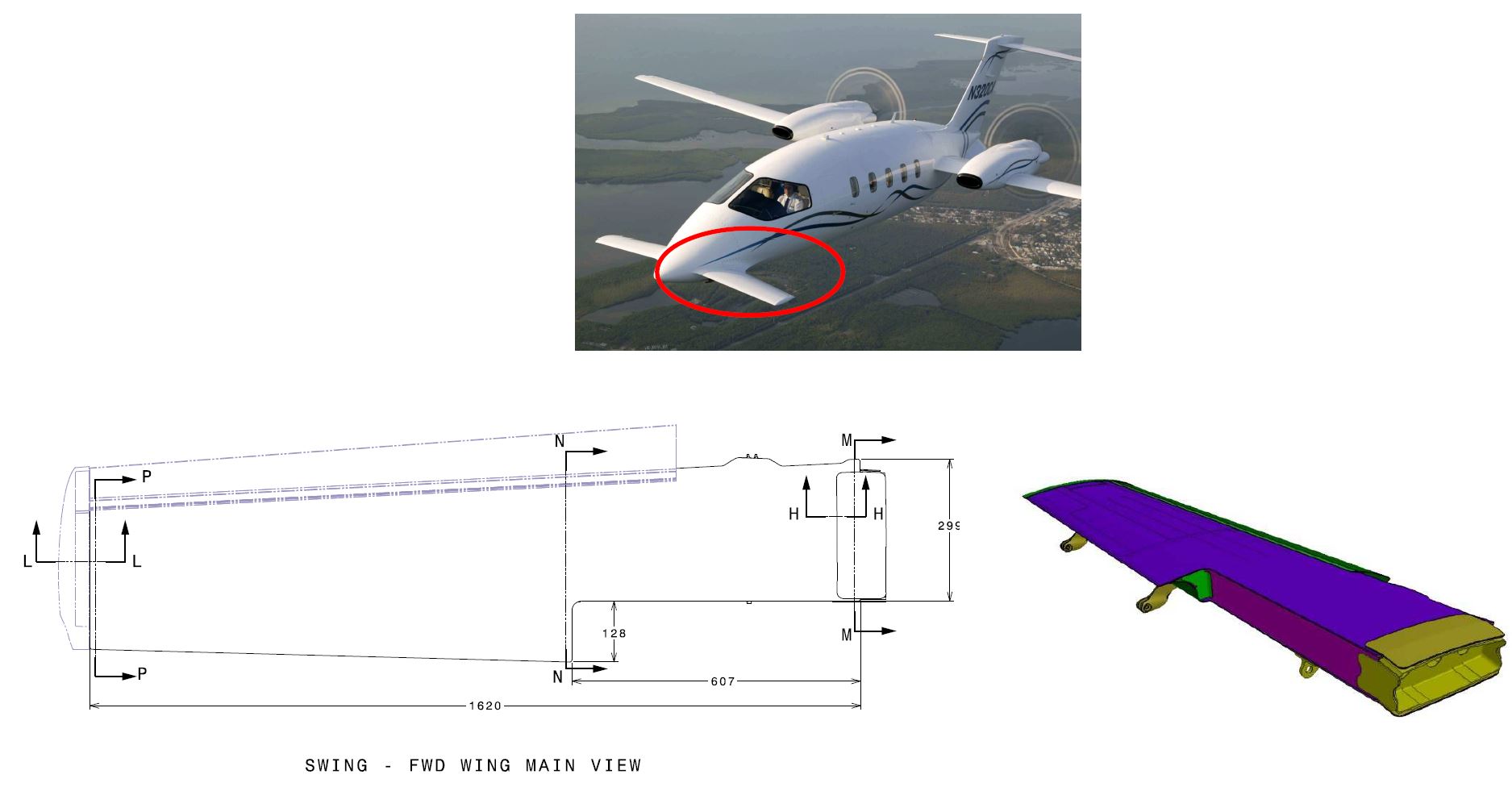
„Die Idee ist, den vorderen Flügel des P.180 in nur zwei Hauptteilen herzustellen:einer oberen und einer unteren Verkleidung, die beide mit integrierten Stringern und Holmen geformt sind“, sagt Lecce.
„Für uns begann dies mit unserer Arbeit als qualifiziertes Labor für Solvay in Großbritannien. Wir kooperieren seit 2015 an neuen Materialien und Verfahren für AFP, LRI und thermoplastische Verbundwerkstoffe. Wir stellten trockene Preforms mit dem Trockenfaserband PRISM TX1100 von Solvay für die Verwendung mit AFP her. Diese Vorformlinge wurden dann mit Solvay PRISM EP 2400 gehärtetem Epoxidharz infundiert und in einem Ofen ausgehärtet. Wir haben diese Arbeit im Rahmen des AIRGREEN 2-Projekts für das Clean Sky 2 Green Regional Aircraft-Programm durchgeführt und dann im SWING-Projekt weitergeführt.“ Beachten Sie, dass PRISM TX1100 und PRISM EP 2400 von der United Aircraft Corporation für die Produktion des ersten harzgetränkten Flügels für ein Verkehrsflugzeug qualifiziert wurden – des von AeroComposit hergestellten Single-Aisle-Jetliners Irkut MS-21.
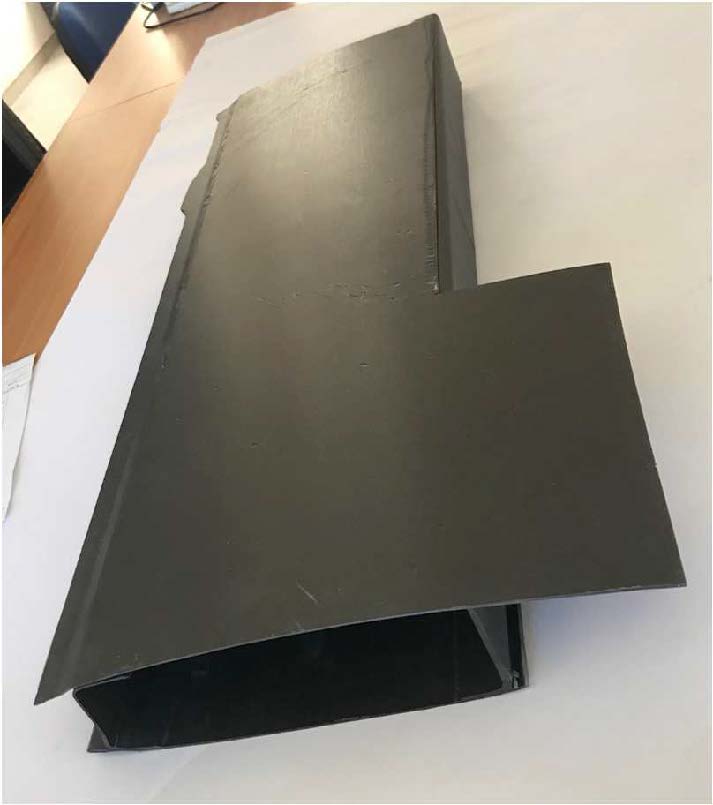
Die geformten oberen und unteren Platten werden mit Strukturkleber verbunden und im nächsten Jahr statisch getestet. „Parallel charakterisieren wir einen weiteren Verbundwerkstoff auf Basis von TX1100 Dry Tape und einer Harzmischung von Covestro (Leverkusen, Deutschland), der eine valide Alternative zu Harzen in Luft- und Raumfahrtqualität sein kann, insbesondere für Sektoren, die höhere Produktionsraten erfordern“, fügt Barile hinzu. „Dieses Harz ist nicht so leistungsstark wie diese Systeme, aber es funktioniert gut mit Infusion und erfüllt die Anforderungen für die Flügelbox. Wenn Sie die Kosten senken möchten, müssen Sie Kompromisse eingehen. Wir hoffen, dass diese Entwicklung dazu beitragen wird, die AFP-Technologie in der Allgemeinen Luftfahrt einzuführen. Es könnte auch im Automobilbereich eingesetzt werden.“
TRINITI
Novotech arbeitet auch am Clean Sky 2-Projekt TRINITI – Thermoplastische Hochdruck-Stickstofftanks aus mehreren Materialien für Flugzeuge –, das 2019 begann und 2021 endet. Der Einstieg von Novotech in dieses Projekt ging erneut aus der Entwicklung mit einem italienischen Luft- und Raumfahrtunternehmen hervor. „Wir haben daran gearbeitet, das Potenzial von AFP mit unserem mehrschichtigen Klebeband bei der Herstellung von kryogenen Treibstofftanks für Trägerraketen im Vergleich zu den derzeit verwendeten Filamentwickelprozessen zu überprüfen“, erklärt Barile. „Im Wesentlichen wird TRINITI ein mehrschichtiges Materialkonzept ähnlich dem von NHYTE entwickeln und dann einen Tank unter Verwendung von AFP in-situ-Konsolidierung herstellen.“
„Der Vorteil von AFP gegenüber FW“, fährt er fort, „ist, dass Sie entscheiden können, wo Sie das Material platzieren möchten. Sie werden nicht durch das kontinuierlich um das Teil gewickelte Filament eingeschränkt. Stellen Sie sich einen Tank vor, bei dem Sie viel Material an den Endkappen haben, da Sie das Material während des Filamentwickelns nicht schneiden können. Durch das Schneiden und Neustarten von Fasern/Bändern an den gewünschten Stellen mit AFP wird Material nur dort verwendet, wo es benötigt wird. So können Sie Lücken zwischen den Bändern bewältigen, was wichtig ist, um das Eindringen von Gas zu verhindern. Um dies beim Filament Winding zu tun, müssen Sie das aufgetragene Material erhöhen, auch wenn Sie bei AFP Schlitzband und kein Towpreg verwenden. Und bei der in-situ-Konsolidierung ist kein Autoklav erforderlich. Wir haben gezeigt, dass AFP eine praktikable und sehr erschwingliche Alternative sein könnte.“
„Derzeit führt CETMA Gaspermeationstests durch, um die Leistung der Mehrschichtmaterialien im Vergleich zu den Spezifikationen zu bewerten“, sagt Barile. Der Themenmanager Diehl Aviation (Gilching und Dresden, Deutschland) hat Anforderungen an einen Hochdruck-Langspeicher-Stickstofftank für den Einsatz in Flugzeug-Brandbekämpfungssystemen gestellt. Diese Tanks müssen Temperaturen von -55 °C bis 85 °C am Boden, -40 °C bis 70 °C im Flugbetrieb und Drücken bis zu 1.000 bar standhalten.
„Das Ziel ist es, Gewicht und Fertigungsschritte zu reduzieren“, bemerkt er. „Allerdings müssen die Herstellungskosten mit dieser Methode definiert werden. Gewicht wird eingespart, indem kein unnötiges Material platziert wird, aber das Filamentwickeln ist im Vergleich zu AFP ein schnellerer Prozess.“ Ein weiterer Faktor ist, dass diese Art von Tanks typischerweise eine Metall- oder Kunststoffauskleidung hat, die mit CFK umwickelt ist. Barile sagt, dass TRINITI nach einem Tank ohne Liner (Typ V) sucht. „Wir werden Gaspermeation vermeiden, indem wir ein hohlraumarmes AFP-Laminat verwenden. Wir testen jetzt bei CETMA mit verschiedenen Materialkombinationen und bereiten uns auf die Auswahl vor. Wir werden dann einen Prototypentank bauen, aber das Design des Tanks hängt vom ausgewählten Material und dem endgültigen Verfahren ab. Darauf arbeiten wir jetzt also hin. Die Testaktivitäten werden von CTL Composites (Galway, Irland) durchgeführt.“
MÖWE
Das anspruchsvolle Projekt SEAGULL wurde vor drei Jahren gestartet. „Unser Ziel ist es, ein kleines Wasserflugzeug der neuen Generation zu entwickeln, das eine neue Technologie zur Herstellung von Verbundwerkstoffen, einen hybriden Elektroantrieb und einen von uns entwickelten und patentierten automatisierten Faltflügel umfasst“, erklärt Lecce. „Die Absicht war ein Kurzstart- und Landeflugzeug (STOL), das mit vertikalen Start- und Landeflugzeugen (VTOL) konkurrenzfähig ist, aber erschwinglicher ist. Wir glauben, dass dies ein persönliches Flugzeug sein könnte, das von jeder Oberfläche aus betrieben werden kann und eine wichtige Möglichkeit für die zukünftige Luftfahrt und Mobilität darstellt.“
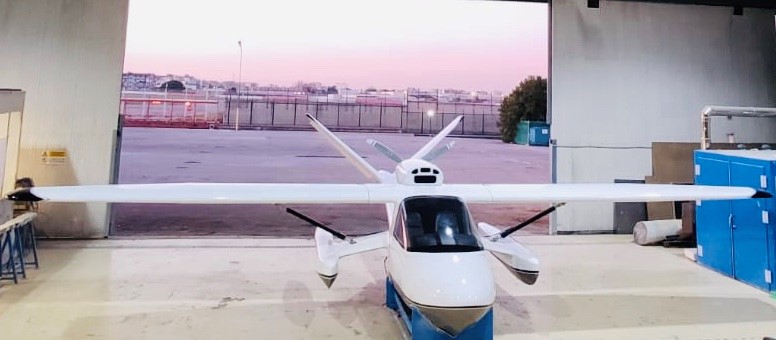
Das SEAGULL-Team hat ein Hybridantriebssystem getestet, einen ersten Prototyp im Wasser gebaut und im Oktober mit Tests im Wasser begonnen. „Nach Abschluss dieser Tests werden wir dann innerhalb weniger Monate einen fliegenden Prototyp bauen“, sagt Lecce. „Dies ist ein sehr erfahrenes Team, bestehend aus bedeutenden Unternehmen mit mehr als 50 Jahren Erfahrung in der Allgemeinen Luftfahrt.“
Der fliegende Prototyp der SEAGULL wird einen Rumpf, ein Leitwerk und eine Tragfläche aus Verbundwerkstoffen aufweisen. „Auch hier werden wir die Anwendung der automatisierten Fertigung mit AFP und Harzinfusion vorantreiben“, sagt Barile. „Eines der Hauptprobleme bei Verbundwerkstoffen, die diese Verfahren verwenden, sind die Materialkosten. Tatsächlich versuchen wir, auch eine Kombination aus Material und Verfahren zu finden, die in Bezug auf die Kosten demokratischer ist.“
Harz
- Fraunhofer IPT entwickelt thermoplastische Verbundwerkstoffe zur Wasserstoffspeicherung, Triebwerksschaufeln und mehr
- Composites Evolution präsentiert Hochleistungs-Prepregs, neuartige thermoplastische UD-Bänder
- Konstruktion für die automatisierte Herstellung von Verbundwerkstoffen von kleinvolumigen Flugzeugstrukturen
- Thermoplastische Bänder zeigen weiterhin Potenzial für Verbund-Flugzeugstrukturen
- Wiederaufbereitbare, reparierbare und recycelbare Epoxidharze für Verbundwerkstoffe
- Karl Mayer startet Produktionslinie für thermoplastische UD-Bänder
- SWM bringt Naltex-Durchflussmedien für die Harzinfusion auf den Markt
- Thermoplastische Tür eine Premiere für Automobilverbundwerkstoffe
- Konsortium für thermoplastische Verbundwerkstoffe strebt die Massenproduktion für die Automobil- und Luftfahrtindustrie an
- Im Dienste der Composites-Welt in Israel und den USA