Fortschritt beim multifunktionalen Rumpfdemonstrator (MFFD)
Reduzierte Treibstoffemissionen und geringerer Energieverbrauch sowie die Möglichkeit, Verkehrsflugzeuge mit einer Geschwindigkeit von mindestens 60 pro Monat zu produzieren, treiben die Technologieentwicklung der europäischen Clean Sky 2-Partnerschaft für die nächste Generation von Flugzeugen an, die im Jahr 2035 und darüber hinaus in die Lüfte steigen werden . Leichte Verbundwerkstoffe und schnellere, umweltbewusstere Herstellungsverfahren lassen diese Ziele Wirklichkeit werden, insbesondere für das Projekt Multifunctional Fuselage Demonstrator (MFFD).
Das wichtigste Ergebnis dieses Projekts, das von Airbus (Hamburg, Deutschland) mit Partnern aus der Wissenschaft und der Luftfahrtindustrie geleitet wird, ist ein 8 Meter langer, thermoplastischer Verbundstoff-Demonstrator für die Rumpftonne von Verkehrsflugzeugen, der von 2022. Das MFFD ist eine von drei Rumpfsektionen in Originalgröße, die innerhalb der innovativen Flugzeugdemonstratorplattform (IADP) für große Passagierflugzeuge (LPA) von Clean Sky 2 hergestellt werden.
Das 2014 begonnene MFFD-Projekt hat folgende Ziele:
- Ermöglichen Sie Produktionsraten von 60-100 Flugzeugen pro Monat
- Rumpfgewicht um 1.000 Kilogramm reduzieren
- Reduzieren Sie wiederkehrende Kosten um 20 %.
Um diese Ziele zu erreichen, werden Dutzende von Einzelprojekten und Arbeitspaketen abgeschlossen, wobei zwei Hauptstrukturen hergestellt werden:eine Rumpfoberschale und eine Rumpfunterschale, die zum endgültigen Demonstrator zusammengeschweißt werden. Tatsächlich ist das staubfreie Fügen (ohne Befestigungselemente oder Löcher) durch Schweißen ein wichtiger Bestandteil des Programms. Beide Hälften werden aus Toray Cetex TC1225 niedrig schmelzendem Polyaryletherketon (PAEK)-Kohlefaser-Thermoplast-Prepreg von Toray Advanced Composites (Morgan Hill, Kalifornien, USA) hergestellt. Laut Dr.-Ing. Lars Larsen, Leiter Füge- und Montagetechnik des Deutschen Zentrums für Luft- und Raumfahrt (DLR; Augsburg), testen beide Hälften den Einsatz unterschiedlicher Fertigungstechniken.
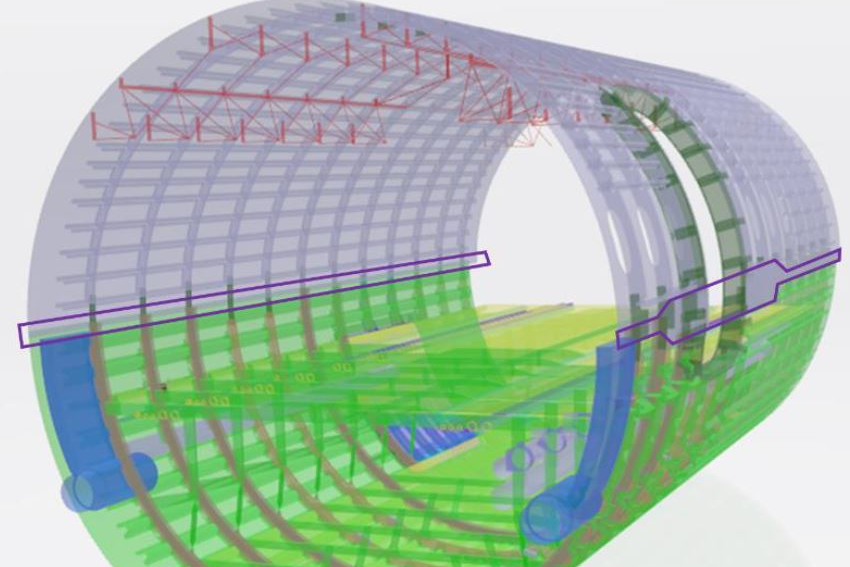
Die untere Rumpfsektion des MFFD wird durch das Projekt STUNNING (SmarT mUlti-FuNctionNal and INtegrated thermoplastischer Rumpf) hergestellt, das selbst viele Projekte unter sich hat (zB MECATESTERS, fokussiert auf Induktionsschweißen). Der untere Bereich umfasst die untere Rumpfschale mit verschweißten Stringern und Spanten, die Kabinen- und Ladebodenstruktur sowie relevante Interieur- und Systemelemente.
STUNNING wird von GKN Fokker (Papendrecht, Niederlande) mit den wichtigsten Partnern Diehl Aviation (Laupheim, Deutschland), dem Netherlands Aerospace Center (NLR; Amsterdam, Niederlande) und der Technischen Universität Delft (TU Delft; Delft, Niederlande) geleitet. Das Projekt zielt darauf ab, automatisierte Montageprozesse, thermoplastische Fertigungs- und Schweißtechnologien, integrierte Konstruktions- und Fertigungsentwicklung sowie fortschrittliche elektrische Systemarchitekturen weiterzuentwickeln.
„Unser Einfluss auf die Branche ist zweifach:der Automatisierungsgrad, den wir auf die Montage des Demonstrators anwenden, und die Entwicklung nachhaltiger Wege zur Herstellung von Teilen“, sagt Dr. Bas Veldman, Programmmanager bei GKN Fokker.
Laut einem im Februar 2020 veröffentlichten Papier Veldman ist die modulare Montage des unteren Rumpfes der Schlüssel zum Erreichen des Ziels schneller Produktionszeiten. Zur Herstellung der Haupthaut des Rumpfes werden große Preforms aus Kohlefaser/Thermoplast-Prepreg von einer ultraschall- oder laserbeheizten automatischen Tapelegemaschine (ATL) gelegt, aber nicht vor Ort konsolidiert. Details werden von einer automatischen Faserplatzierungsmaschine (AFP) gelegt. Roboter legen die Preforms dann in eine weibliche Konsolidierungsform und nach dem Absacken wird die Haut in einem Autoklaven konsolidiert. Laut Veldman werden auch Verfahren außerhalb des Autoklaven untersucht. Die Stringer und Spanten werden mit der Haut verschweißt.
„Ursprünglich war geplant, alle Teile noch dieses Jahr fertigen zu lassen“, sagt Veldman, aber aufgrund von Verzögerungen im Zusammenhang mit dem Coronavirus „geht es jetzt auch ins nächste Jahr. Aber wir haben einige Teile, die jetzt fertig sind“, darunter viele der kleineren Pressformteile wie Clips, Streben und Halterungen, die zur Befestigung von Flugzeugsitzen und anderen Komponenten verwendet werden. Veldman betont die nachhaltige Herstellung und fügt hinzu, dass einige der Clips aus wiederverwendeten Resten anderer Teile des Demonstrators im Rahmen eines Clean Sky 2-Projekts namens ECO-CLIP hergestellt werden.
Das Konsortium, das Anfang 2020 die 8 Meter lange Oberschale herstellt, umfasst Airbus, Premium Aerotec (Augsburg, Deutschland), die den Industrie- und Strukturentwurf führen; DLR, zuständig für die Entwicklung von Skin Layup und Schweißtechnik; und Aernnova (Vitoria-Gasteiz, Spanien), die die Stringer herstellt.
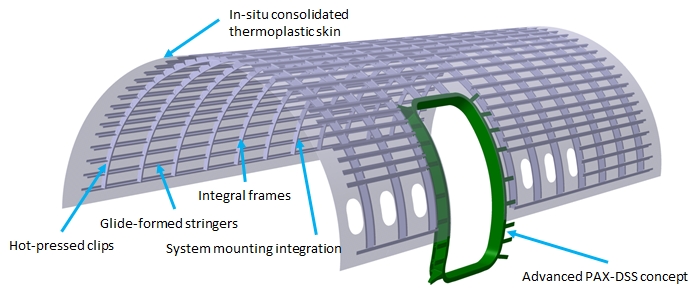
Damit die Luft- und Raumfahrtindustrie auf teurere thermoplastische Materialien umsteigen kann, sagt Larsen:„Wir müssen zeigen, dass wir bei der Produktion Kosten sparen können.“ Das Konsortium der oberen Hälfte entwickelt eine neuartige Advanced Fiber Placement (AFP)-Technologie mit insbesondere einer in-situ-Konsolidierung für das Carbonfaser/PAEK-Skin-Layup sowie die Industrialisierung des kontinuierlichen Ultraschallschweißens und des Widerstandsschweißens zur Integration der Stringer, Rahmen und anderen Komponenten, verbessert die Sicherheit und senkt die Kosten. Das DLR baut zunächst eine 1 Meter lange Pre-Demonstrator-Testschale, um die Technologien zu validieren, bevor der Demonstrator in Originalgröße gebaut wird, und plant, die Haut für die Pre-Demonstrator-Schale bis Ende 2020 fertigen zu lassen die Stringer sind für Anfang 2021 geplant.
Die Vollversionen beider Hälften sollen bis Ende 2021 fertiggestellt sein. Nach Fertigstellung werden sie am Fraunhofer-Institut für Fertigungstechnik und Angewandte Materialforschung IFAM (Stade, Deutschland) zum finalen Demonstrator eingeschweißt.
Harz
- Über die Grundlagen hinausgehen:Maschinelles Lernen und AM
- Die Vorteile der Flugzeugkonstruktion aus Verbundwerkstoffen in Flugzeugen aller Größen
- Warum Automatisierung der einzige Weg in die Zukunft für die Fertigung ist
- 5 Roboteranwendungen in der Luft- und Raumfahrtindustrie
- Die Produktionslandschaft:Rückblick und Ausblick
- Drei Vorteile der Verlagerung des Ausgabenmanagements in die Cloud
- Die erste Rumpfsektion aus Verbundwerkstoff für den ersten Verkehrsflugzeug aus Verbundwerkstoff
- Im Dienste der Composites-Welt in Israel und den USA
- Was ist die Diodendurchlassspannung?
- Stickstofferzeugung in der Luft- und Raumfahrtindustrie