Glasfaserverbundwerkstoffe ermöglichen ein leichteres, stabileres Design von COVID-19-Testkabinen
Inspiriert von einem COVID-19-Teststand aus Polycarbonat und Aluminium, der Anfang des Jahres vom Brigham and Women's Hospital (Boston, Massachusetts, USA) entworfen und gebaut wurde, hat Imagine Fiberglass Products Inc. (Kitchener, Ontario, Kanada) sein eigenes leichteres, robusteres . entwickelt Version mit glasfaserverstärkten Verbundwerkstoffen.
„Wir waren der Meinung, dass wir eine Kabine schaffen könnten, die schnell in vielen verschiedenen Umgebungen eingesetzt werden kann, indem wir sie extrem leicht, robust und tragbar machen“, sagt Jim Ashton, Präsident von Imagine Fiberglass.
Die IsoBooth des Unternehmens, die auf einem Design basiert, das ursprünglich von Forschern der Harvard Medical School entwickelt wurde, ermöglicht es einem Kliniker, außerhalb des Patienten im Inneren zu stehen und einen Tupfertest über behandschuhte externe Handanschlüsse durchzuführen. Ein Regal oder eine individuell gestaltete Ablage an der Vorderseite der Kabine enthält Testkits, Zubehör und einen Kanister mit Desinfektionstüchern, die zum Reinigen der Handschuhe und des Schildes zwischen den Patienten verwendet werden.
„Die IsoBooth soll Gesundheitsdienstleistern einen sicheren und komfortablen Ort für die Durchführung von Tests bieten und gleichzeitig den Verbrauch an PSA [persönlicher Schutzausrüstung] bei herkömmlichen Testmethoden erheblich reduzieren“, sagt Ashton. „Die Kabine kann bis zu 143.000 Pfund biomedizinischen Abfall pro 1 Million Tests beseitigen.“
Er fügt hinzu, dass allein die Vereinigten Staaten beabsichtigen, bis zu 5 Millionen Tests pro Woche hochzufahren, wobei mit traditionellen Methoden pro Woche bis zu dreiviertel Million Pfund Abfall in Form von Einweghandschuhen, Gesichtsmasken und anderer PSA produziert werden. Die IsoBooth könnte zu erheblichen Kosteneinsparungen führen und biomedizinischen Abfall reduzieren, sagt er.
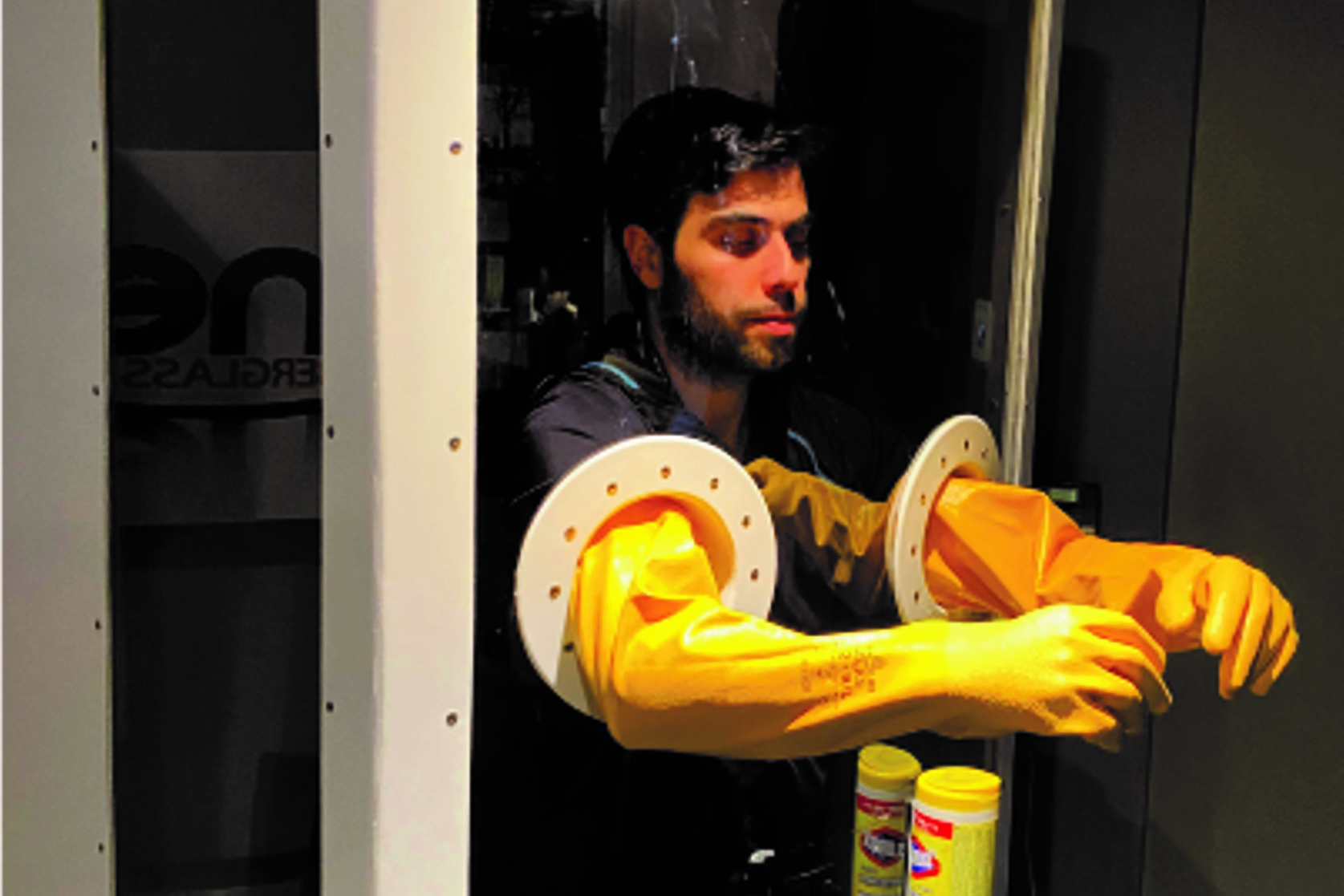
Das Design von Imagine Fiberglass besteht aus drei klaren Polycarbonat-Sichtscheiben, die an drei getönten Fiberglas-Kanonen-Roving-/Polyester-Paneelen befestigt sind, die an Stellen, die zusätzliche Steifigkeit erfordern, mit einem Polypropylen-Wabenkern verstärkt sind. Die Verbundplatten sind offen geformt und außen mit einem weißen Gelcoat beschichtet. „Sobald die Nachfrage steigt, wird der Prozess auf leichtes RTM [Resin Transfer Moulding] umgestellt“, sagt Ashton. Die Polycarbonatplatten und Armanschlüsse werden auf dem CNC-Router von Imagine Fiberglass bearbeitet; Die einzigen Teile, die nicht im eigenen Haus hergestellt werden, sind laut Ashton die Handschuhe.
Die Kabine wiegt etwa 90 Pfund, kann leicht von zwei Personen getragen werden und ist mit einer Tiefe von 33 Zoll so konzipiert, dass sie durch die meisten handelsüblichen Türen passt.
Laut Ashton gibt es mehrere andere konkurrierende Kabinen, die entworfen wurden, aber die meisten davon basieren auf Polycarbonat- oder Acrylplatten, die an den Ecken mit Aluminium verbunden sind. „Dies ist zerbrechlicher und umständlicher zu bewegen und auch erheblich schwerer“, sagt Ashton.
Neben dem geringen Gewicht und der Strapazierfähigkeit sind die geformten Verbundkabinen auch von hinten nach vorne verjüngt, sodass mehrere Einheiten für den Versand oder die Lagerung auf einem Gestell verschachtelt werden können. Im Gegensatz dazu, sagt Ashton, würden konkurrierende Plexiglaskabinen einen größeren Lagerraum oder ein Transportfahrzeug erfordern oder für den Transport oder die Lagerung zerlegt und wieder zusammengebaut werden müssen.
Nach Rücksprache mit Dr. Kris Olson, dem Direktor des Consortium for Affordable Medical Technologies an der Harvard University, entwarf Imagine Fiberglass die Armöffnungen seines Stands in ovaler Form, um maximale Bewegungsfreiheit zu ermöglichen. Das Design umfasst auch einen durchsichtigen Polyvinylchlorid (PVC)-Vorhang an der Rückseite der Station, damit HEPA-gefilterte Luft in das Gerät gepumpt werden kann, sodass der Gesundheitsdienstleister keine Maske, einen Kittel, einen Gesichtsschutz oder eine Schutzbrille tragen muss.
Darüber hinaus sind die Stände so gebaut, dass sie jahrelang halten. Ashton stellt sich vor, dass der IsoBooth in COVID-19-Testeinrichtungen, Notaufnahmen, Intensivstationen und Apotheken verwendet wird. IsoBooths könnten auch an Arbeitsplätzen verwendet werden, da Unternehmen Testverfahren implementieren, wenn Mitarbeiter wieder in ihre Büros zurückkehren.
„Unsere Absicht war es immer, Kosten und Umweltverschwendung zu reduzieren, indem wir Einweg-PSA für COVID-19-Tests eliminieren“, fügt Ashton hinzu. „Die IsoBooth ist auch eine große Hilfe, wenn es wie heute einen großen Mangel an PSA gibt. Eine IsoBooth kann in nur einem Testtag bezahlt werden, abhängig von den aktuellen Kosten für PSA und der Anzahl der Tests pro Tag.“
Harz
- COTS-Tests und Design für Sicherheit mit Samtecs SET-Initiative
- Entschlüsselung der SARS-CoV-2-Genome – diagnostische Tests
- Inventor spart Tausende bei Design und Tests
- Einfach zu verwendende Kits ermöglichen die Reparatur von Verbundstrukturen im Feld
- Verbundradom-Design sichert Patent, überwindet Herausforderungen bei der Signaldämpfung
- Durch Verbundwerkstoffe angetriebene Wasserturbinenschaufelkonstruktion
- Glasfaserverbundwerkstoffe ermöglichen ein leichteres, stabileres Design von COVID-19-Testkabinen
- MIT- und NASA-Ingenieure entwerfen leichte Polymertragflächen
- Hochleistungsverbundwerkstoffe in Israel
- Fräs-Dreh-Zentren' B-Achsen ermöglichen hochpräzise Bearbeitung