Kanfit zur Bewältigung von COVID-19 und zur Wachstumssteuerung mit Composites 4.0-Systemen
Während ich einen Artikel über die Digitalisierung der Produktion von Verbundwerkstoffen für unsere Juli-Ausgabe vorbereite, interviewte ich Shachar Fine, EVP of Business Development, Marketing &Sales von Kanfit Ltd. (Nof-Hagalil, Israel), einem wachstumsstarken, diversifizierten Verbundwerkstoffhersteller und Luft- und Raumfahrtunternehmen Anbieter. CW erwähnte kurz Kanfits Einsatz von Bluetooth-Sensoren in unserer Reihe von Werksbesichtigungen in Israel 2018 (siehe „Gedeihender Pionier in der Luft- und Raumfahrt baut Geschäft auf …“). In diesem Blog werde ich dieses auf künstlicher Intelligenz (KI) basierende System genauer untersuchen.
Mit COVID-19 fertig werden
Aber zuerst diskutierten Shachar Fine und ich kurz, wie Kanfit mit COVID-19 umgeht und die Produktion von Verbundwerkstoffen aufrechterhält. „Die israelische Regierung hat Richtlinien erlassen, die bestimmte ‚nicht wesentliche‘ Geschäfte schließen müssen (z. B. Fitnessstudios, Salons usw.),“ erklärt er, „aber diejenigen, die als ‚wesentlich‘ definiert sind (z. Essen etc.) kann auf jeden Fall arbeiten, solange die Mitarbeiter mindestens zwei Meter voneinander entfernt bleiben. Die Rüstungsindustrie kann bis zu 50 % ihrer Mitarbeiter beschäftigen und die verbleibende Industrie kann bis zu 30 % ihrer Belegschaft haben, solange diese Unternehmen die Abstandsvorschriften einhalten.“
„Wir stellen bis zu 50 % unserer Mitarbeiter pro Schicht ein und fahren zwei Schichten“, sagt Fine. „Eine dritte Schicht hat sich nie gerechtfertigt, weil die Produktivität einfach zu gering war. Auch jetzt werden wir das nicht tun. Aber wir verlängern einige unserer Schichten. Beispielsweise werden wir in Abteilungen wie der Zerspanung, in denen Mitarbeiter hauptsächlich automatisierte Anlagen überwachen, 12-Stunden-Schichten durchführen. Aber für Abteilungen, in denen Mitarbeiter mehr manuelle Aufgaben ausführen, werden wir Schichten von 8 bis 10 Stunden durchführen.“ Er erklärt, dass dies im Wesentlichen dazu dient, den Produktivitätsverlust aufgrund der erforderlichen sozialen Distanzierung auszugleichen.
Fine gab an, dass er gerne hören würde, wie sich andere Hersteller von Verbundwerkstoffen anpassen. „Ich bin mir sicher, dass ich von dem, was Verbundwerkstofffabriken in anderen Teilen der Welt tun, lernen könnte. Ich bin in einer Geschäftsentwicklungsgruppe auf WhatsApp hier in Israel und wir geben Ratschläge, wie Sie die Geschäftsentwicklung fortsetzen können, wenn Sie sich nicht treffen oder reisen können. Natürlich hat die Sicherheit und Gesundheit aller Priorität.“
Bluetooth vs. RFID-System
Wie im Tour-Artikel 2018 erklärt, wurde das von Kanfit installierte System von einem Tel-Aviv-Start-up, Trekeye, geliefert. Das System umfasst Bluetooth-Tags (drahtlos), die an den Läufern jedes Teils angebracht werden, was den Arbeitsauftrag bedeutet, der mit dem Teil reist.
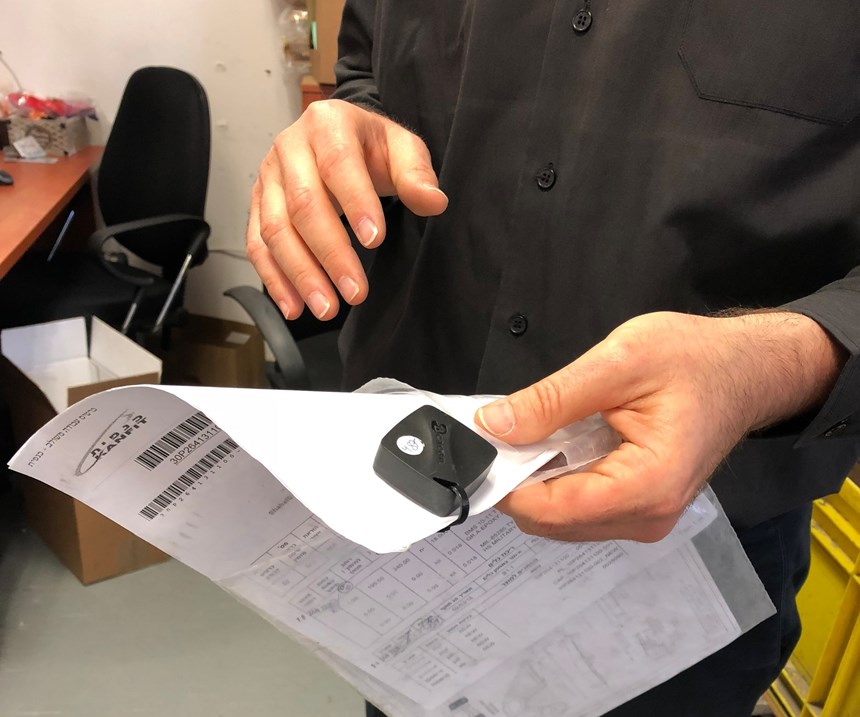
Wenn der Arbeitsauftrag für ein Teil gedruckt wird, wird das Etikett daran befestigt und dann an die Produktion geliefert. Bei Verbundteilen könnten die nächsten Schritte das automatisierte Schneiden und Kitten von Prepregs oder Trockenverstärkungen, Layup, Preforming/Debulking, Resin Transfer Moulding (RTM) oder Vakuumverpackung und Autoklavenhärtung, Trimmen, zerstörungsfreie Prüfung (NDT) und Lackieren umfassen. In der Regel liegen zwischen diesen Schritten mehrere Inspektionen. Die Prozesskette könnte auch die Montage von kleinen und großen Metallteilen zu größeren Modulen umfassen. Die Herstellung solcher Module, einschließlich der Installation verschiedener Systeme (z. B. Verkabelung, Isolierung, dezentrale Stromversorgung usw.), ist ein wachsender Trend für Zulieferer der Luft- und Raumfahrt. Sobald die Prozesskette abgeschlossen ist und das Teil/die Baugruppe versandfertig ist, wird das Bluetooth-Tag entfernt und für einen neuen Arbeitsauftrag wiederverwendet.
Fine erklärt, dass dies Tags sind, keine Sensoren. „Ein Tag erkennt nicht, sondern überträgt nur ein Signal“, bemerkt er. In diesem Fall überträgt jeder der Bluetooth-Tags alle 10 Sekunden seine Seriennummer. „Antennen empfangen diese Signale und triangulieren die Position jedes Tags“, sagt Fine. Die letzte Systemkomponente ist die Software, die die Daten sammelt, Algorithmen anwendet, um sie zu analysieren und mit Alarmen und/oder vorgeschlagenen Maßnahmen reagiert. Die Bluetooth-Tags sind batteriebetrieben, aber die Software warnt, wenn die Batterien schwach sind und die Batterien länger als ein Jahr halten.
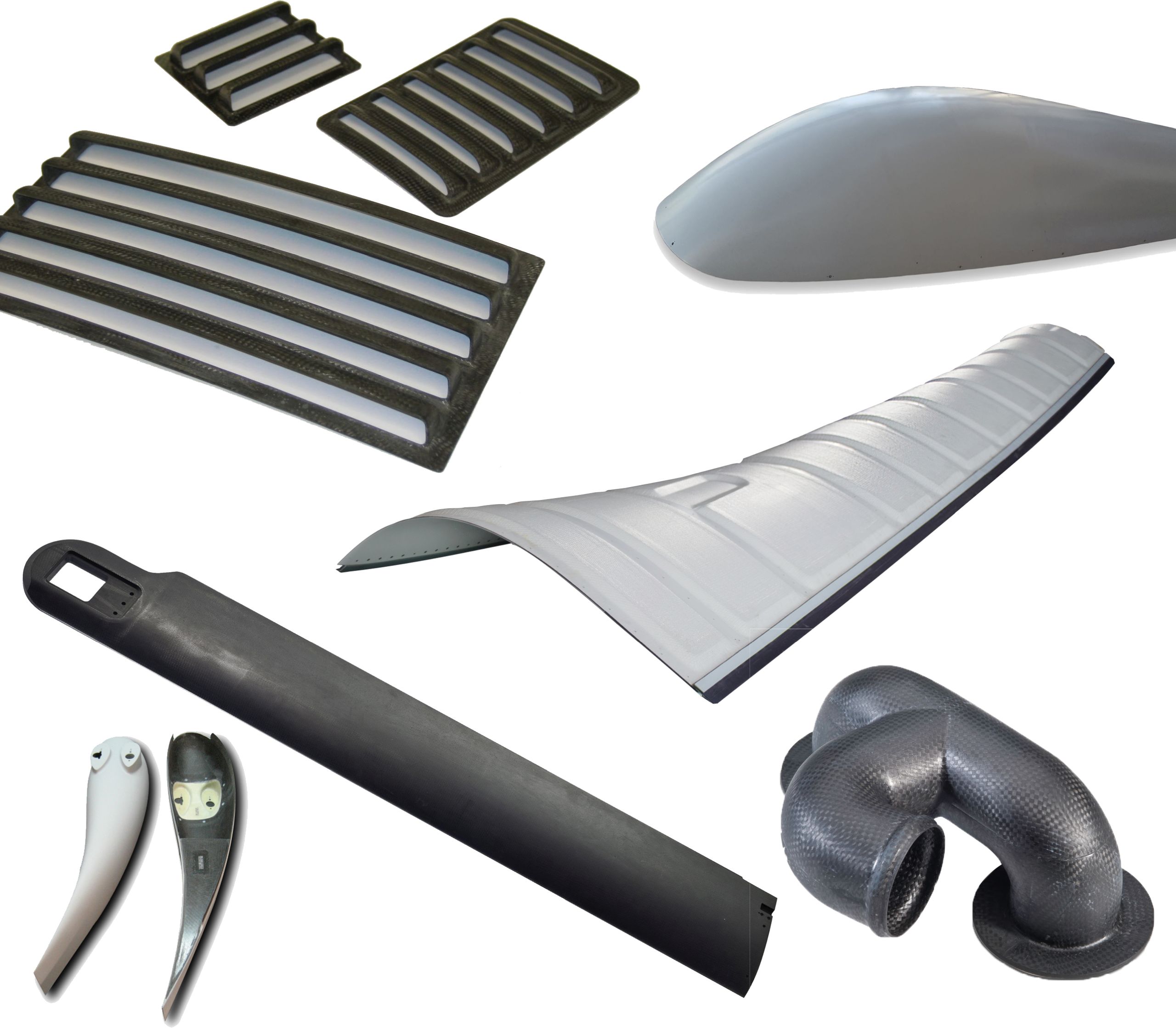
Kanfit erforschte die Verwendung von RFID-Tags, aber da sie Hochfrequenz (elektromagnetische Felder) verwenden, um Daten zu übertragen, stört Metall das Signal. „Wir haben viel Metall in unserer Produktionsumgebung“, erklärt Fine. „Man muss sich also überlegen, wo im Gebäude die RFID-Antennen platziert werden sollen, damit das Signal jedes Tags immer empfangen wird. Wenn sich die RFID-Tags regelmäßig nicht registrieren, ist der gesamte Datenstrom kompromittiert. Mit unseren Bluetooth-Tags haben wir eine 100%ige Registrierung nachgewiesen. Wir haben sie mit Metallteilen eingeworfen und in die Nähe verschiedener Antennen gestellt. Jedes Mal hat das System 100 % der Tags erfasst.“
Ein weiterer Unterschied besteht darin, dass die Bluetooth-Tags aktiv sind und ein Signal aussenden, während RFID-Tags typischerweise passiv sind – ihre Signale werden nur aufgenommen, wenn sie an einer entsprechend positionierten Antenne vorbeikommen. „Mit den Bluetooth-Tags positionieren Sie Antennen dort, wo das System Teile melden soll“, sagt Fine. „Es gibt also keine technologische Einschränkung wie beim RFID-System. Sie können die Antennen an einer Wand, Decke oder einem Arbeitsplatz anbringen. Wo und wie viele Sie in einem Bereich verwenden, hängt von der Auflösung ab, die Sie benötigen. Für In einem Wartebereich reicht beispielsweise eine Antenne an der Decke aus, in einem Bereich mit mehreren Prozessschritten benötigen Sie jedoch möglicherweise mehrere Antennen.“
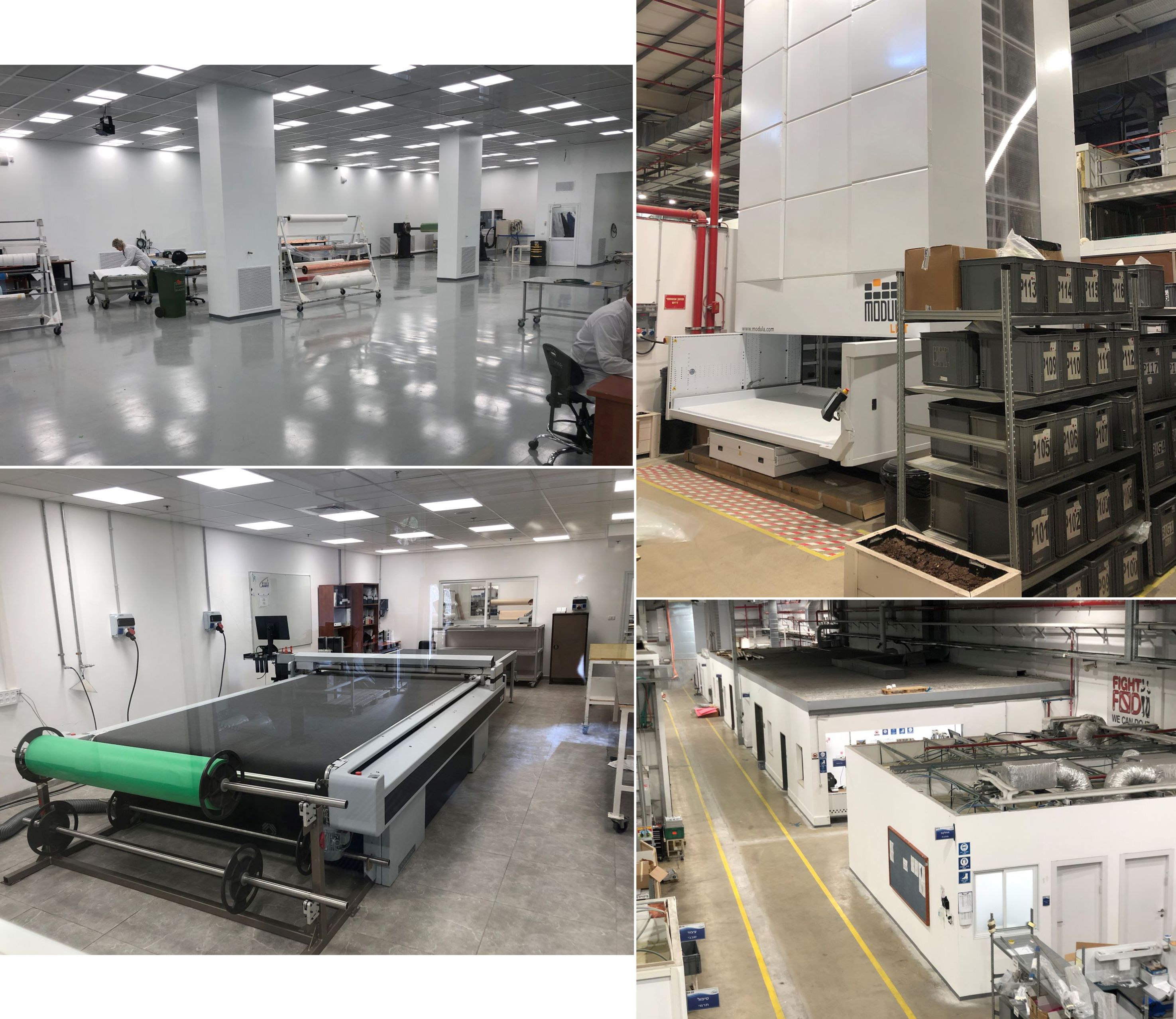
Ein Nachteil des von Trackeye installierten Bluetooth-Systems Kanfit sind die Kosten. „Es gibt viel Infrastruktur“, sagt Fine, „und diese Bluetooth-Tags kosten Dollar, keine Cent wie RFID-Tags.“ Es gab auch eine bedeutende Entwicklung, bei der Trekeye-Entwickler vor Ort sein mussten. „Sie halfen uns, die Antennen so zu lokalisieren, dass die gesammelten Informationen für unser Ziel optimiert wurden“, erklärt er. „Sie haben uns beigebracht, wie man Probleme mit überlappenden Antennenbereichen angeht, damit das System nicht verwirrt wird, wenn ein Tag von zwei Antennen mit der gleichen Intensität gelesen wird. Es war ein Prozess.“
Teilekarten und Spaghettidiagramme
Nachdem das System installiert und in Betrieb war, wurden unter anderem Teilekarten und Spaghetti-Diagramme zurückgegeben. „Unsere IT-Abteilung hatte die Online-Karte für das System die ganze Zeit geöffnet“, erklärt Fine. „Wenn ein Mitarbeiter ein Teil suchte, ging er zur IT, fand das Teil schnell und holte es dann im Werk ab. Es war sehr leicht zu erkennen, wo sich alle Teile befanden.“
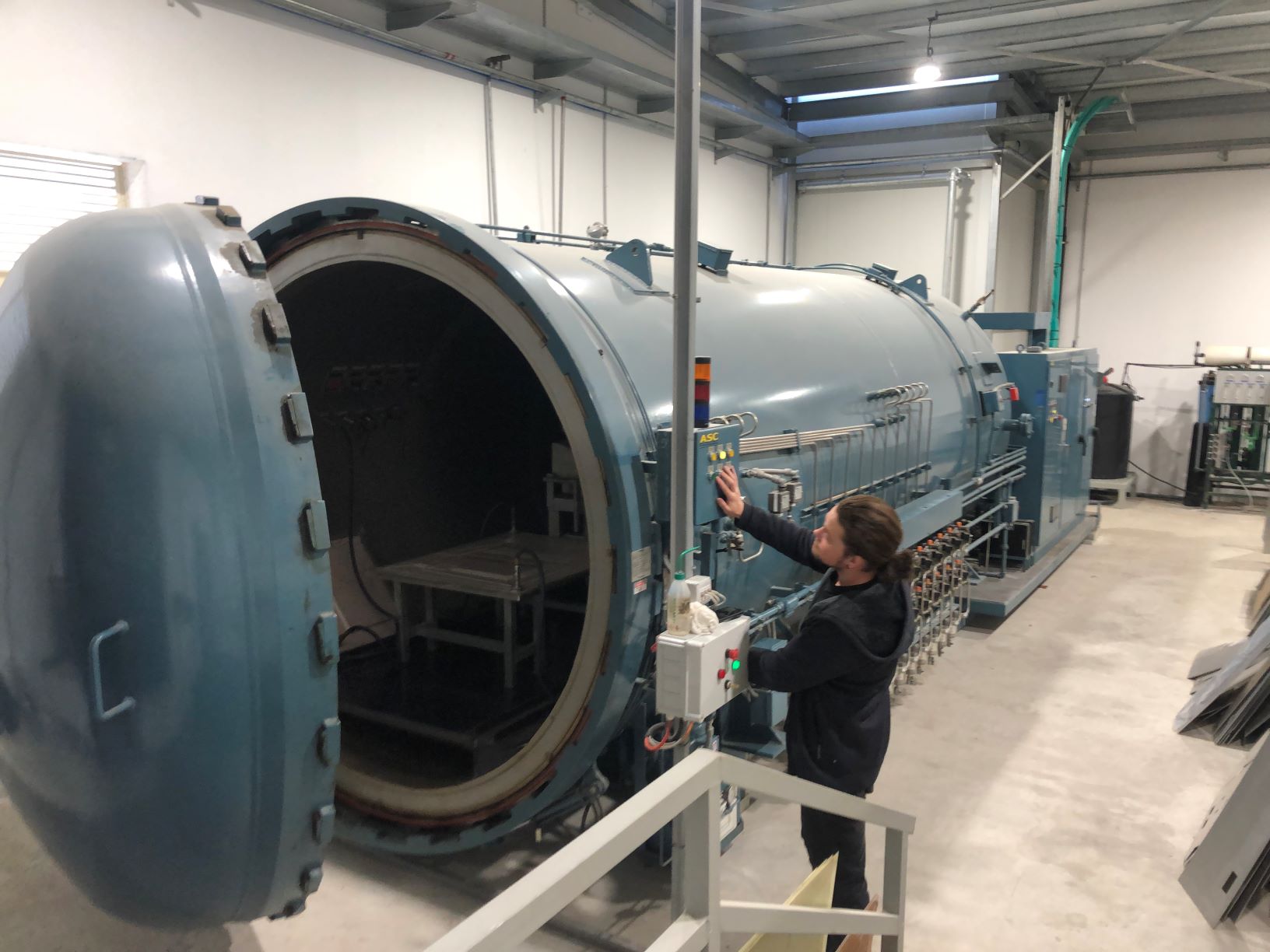
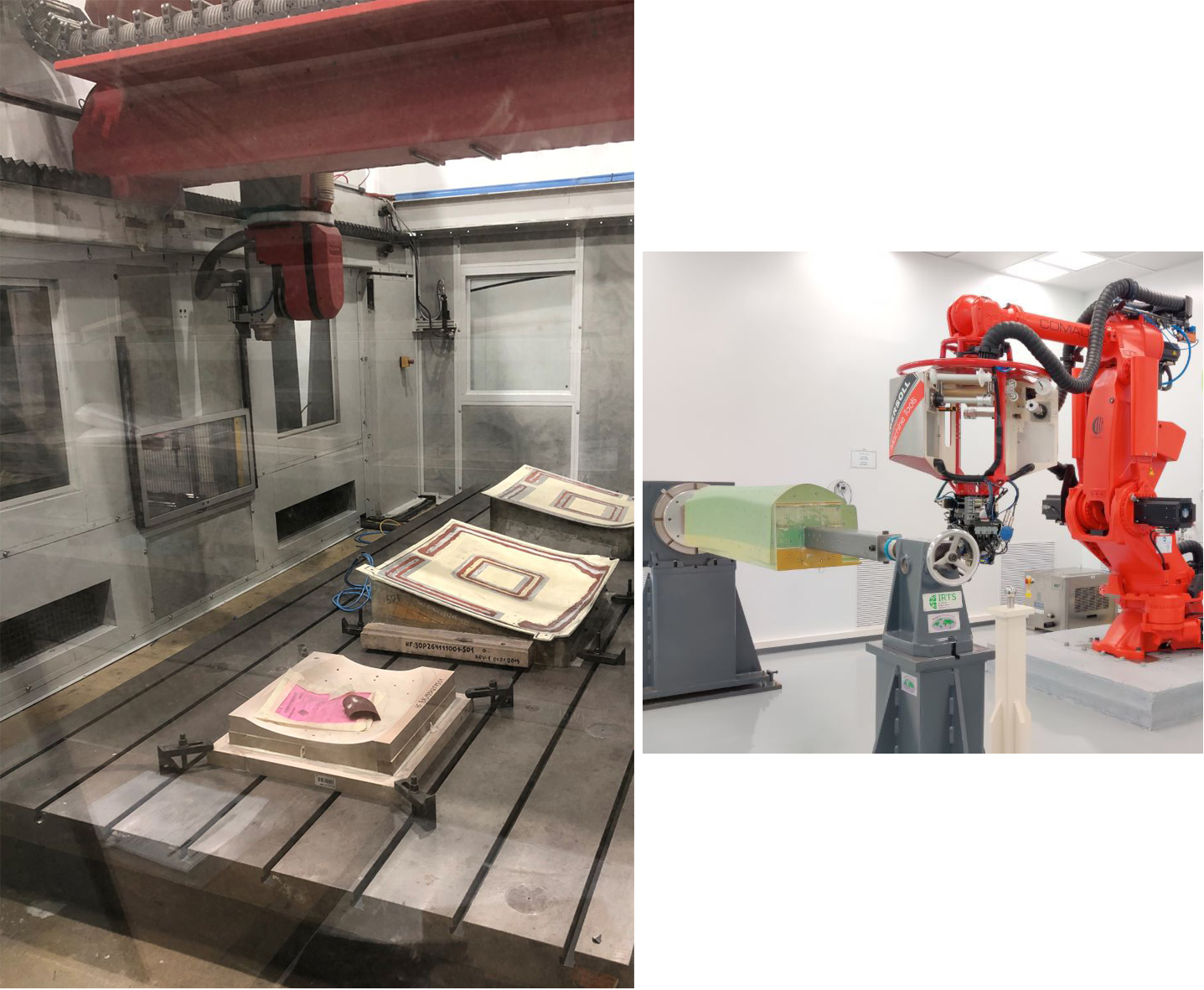
Er erklärt, dass Kanfit Tausende von Teilen in der gesamten Produktionshalle hat (3.000 offene Arbeitsaufträge pro Minute), „und es ist kein standardisiertes Fließband. Die Mischung der vorgenommenen Teile ändert sich und einige Teile erfordern andere Schritte als andere. Beispielsweise wird nicht jedes Teil autoklaviert oder bearbeitet. Wenn Sie ein Teil sehen, wissen Sie nicht immer, ob es an der richtigen Stelle ist. Sie müssen die Papiere des Teils überprüfen, um das zu verstehen.“
Das Trekeye-System funktionierte jedoch erstaunlich gut. „Obwohl es kein billiges System war, war der ROI (Return on Investment) sehr kurz“, sagt Fine. „Das System verfügt über eine sehr fortschrittliche KI. Es wurde nicht gewartet, bis ein Teil fehlte. Es würde eine SMS (Textnachricht) an den Manager senden, dass der „ABC“-Teil an die falsche Station ging. Es gab kein Warten. Das System warnt, wenn ein Teil nicht seiner normalen Route folgt.“
Diese Teilstrecken oder Pfade werden auf sogenannten Spaghetti-Karten dargestellt. „Diese zeigen die Wege der Teile durch unsere Fabrik- und Prozessketten“, sagt Fine. „Wir begannen, Trends zu erkennen. Wenn Ingenieure beispielsweise die Arbeitsaufträge für Teile erstellten, führten sie gemäß ihrem Wissen und ihrer Erfahrung Prüfschritte ein. Die Teile würden zuerst zur Inspektion gehen, bevor sie zur nächsten Station bewegt werden. Die Spaghetti-Diagramme würden zeigen, dass Sie einige Aktionen ändern und die Entfernung reduzieren können, die Teile zurücklegen. Wir würden sehen, dass ein Teil zwischen den Abteilungen für mehrere Aktionen hin und her geht. Wir saßen dann bei der Technik und fragten, warum es hin und her geht? Wie könnten wir zum Beispiel das Vierfache auf das Zweifache reduzieren? Dies ist in der Grafik leicht zu erkennen, aber im tatsächlichen täglichen Betrieb auf dem Boden schwer zu erkennen und auch, wie sich dieses Hin und Her tatsächlich auf die Gesamtproduktion auswirkt. Sie können die Schritte als Einzelposten sehen, während Sie sie in den Arbeitsauftrag schreiben, aber die Pfade im Spaghetti-Diagramm sind mehr Daten und eine Visualisierung dieser Daten, die wirkliche Auswirkungen haben.“
„Das hat uns auch beim Einzug in unser neues, größeres Werk geholfen“, fügt Fine hinzu. „Eine unserer Lektionen ist, die Inspektionsabteilung zentral im Produktionsbereich anzusiedeln. Ich bin mir also sicher, dass die KI uns im Laufe der Zeit weiterhin dabei helfen wird, Maschinen und Stationen besser zu lokalisieren, selbst wenn sich unsere Teile und Abläufe im Laufe der Zeit ändern. Es kann auch Werkzeuge verfolgen.“
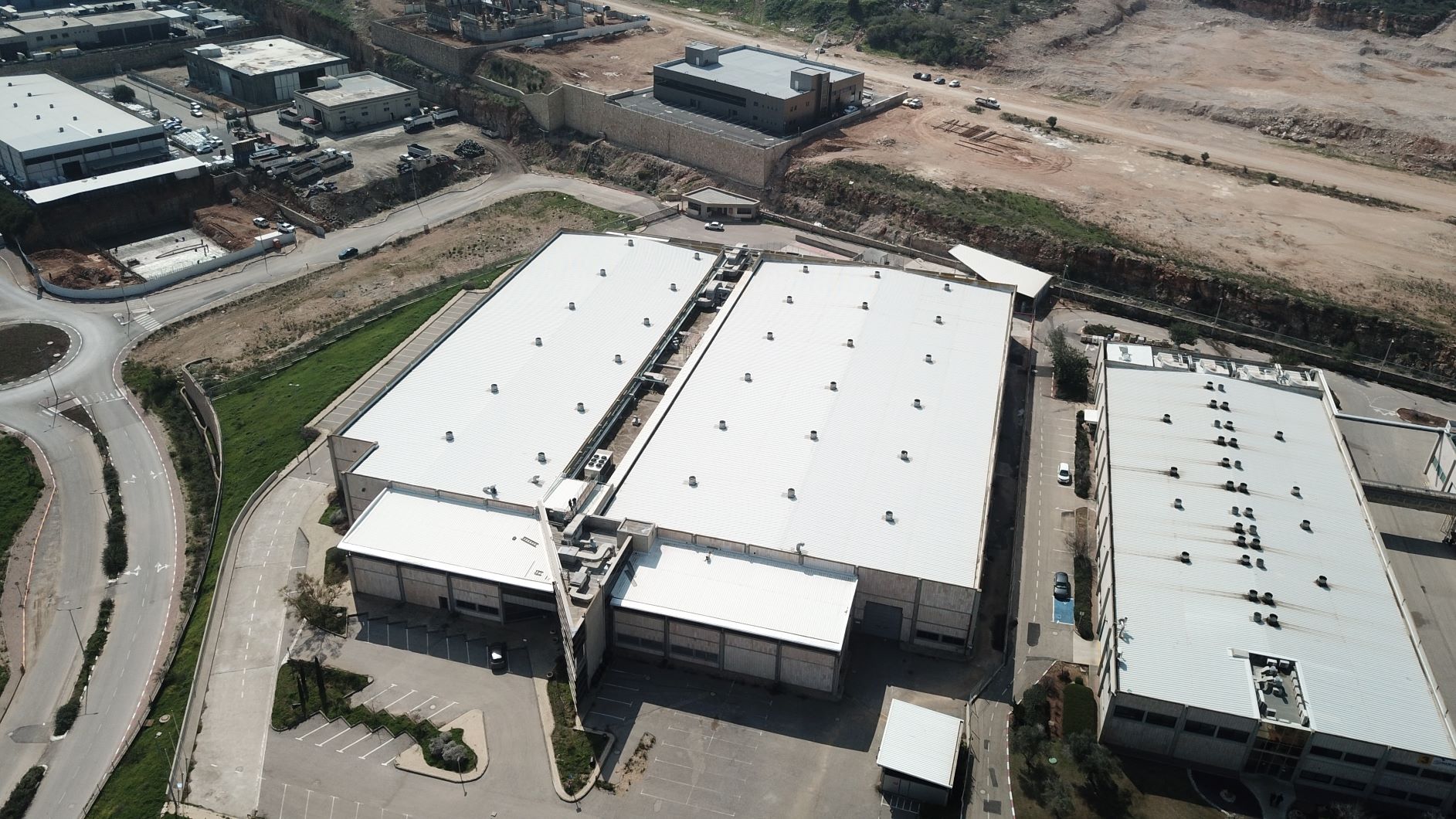
Ein weiterer Vorteil besteht darin, dass Kanfit verfolgen kann, wie viel Zeit ein Teil an jeder Station verbringt. „Obwohl wir dies noch nicht implementiert haben, könnte dies den Zeitaufwand für die Eingabe solcher Daten durch die Mitarbeiter reduzieren“, bemerkt Fine. „Wir haben immer noch ein ERP-System, in das sich die Mitarbeiter melden, aber das Bluetooth-Tag-System gab genauere Informationen darüber, wann ein Teil eine Station betreten und verlassen hat usw.“
Guter Hinweis, dass diese Teile- und Werkzeugüberwachungssysteme das ERP nicht ersetzen, sondern integriert werden müssen, um damit zu arbeiten. „Wir entwickeln unser ERP-System im eigenen Haus weiter, weil wir große Kunden haben und jeder von ihnen seine eigenen Anforderungen hat. Wir müssen also viel in unser System hineinentwickeln, um alle Informationen bereitzustellen, die sich jeder Kunde wünscht.“ Aber er sieht die Kraft der Bluetooth-Tag-/KI-Technologie zur Verbesserung dieser Systeme und den Vorteil in der weiteren Effizienz, die sich daraus ergibt.
Keine Dateneingabe
Mussten Sie beim Erstellen des Arbeitsauftrags und Anbringen des Sensors viele Daten für jedes Teil eingeben? „Nein, das ist das Erstaunlichste“, sagt Fine. „Es gab keine Dateneingabe. Es ist das KI-System. Alles, was es erhielt, waren die Arbeitsauftragsnummern. Diese bestehen aus Buchstaben und Zahlen, aber es gibt eine Art Logik in der Art und Weise, wie wir diese finden und was sie bedeuten. Das muss die KI gelernt haben. Sobald es mit dem Sammeln von Daten begann, lernte es, wo die Teile sein sollten. Zum Beispiel waren alle „ABC“-Arbeitsaufträge nur aus Metall und sollten nie an die Verbundwerkstoffabteilung gehen. Als ein Metallteil irrtümlicherweise in die Verbundwerkstoffabteilung gelangte, gab das System Alarm. Selbst die KI-Designer waren überrascht, wie schnell das System lernte. Wir haben zunächst 100 Teile getestet. Es hat in dieser ersten Charge gelernt.“
Fine erklärt, dass das System dafür entwickelt wurde. Trekeye begann in Krankenhäusern und arbeitete mit einem Wartungsunternehmen für mobile Medizingeräte zusammen, das bei der Wartung von Blutdruckmanschetten, Thermometern, Monitoren usw. half. Dieses Unternehmen beschwerte sich, dass es 80 % der Zeit des Wartungstechnikers damit verbrachte, nach den Geräten zu suchen, die gewartet werden mussten. „Wenn dieses System installiert war, kam der Techniker herein, stellte eine Verbindung zum System her und sah genau, wo sich alle Geräte im Krankenhaus befanden“, sagt Fine. „Ein zusätzlicher Vorteil war, dass Diebstähle zurückgegangen sind. Immer wenn jemand mit einem Gerät nach draußen ging, wurde das System alarmiert und ein Sicherheitsbeamter wurde nach unten geschickt, um das Gerät zu bergen.“
Zukünftige Implementierung
Leider hat Trekeye als Startup die kritische Phase des „Death Valley“ nicht überstanden und ist nicht mehr aktiv. „Wir haben alles, was wir brauchen, um das System am Laufen zu halten, außer dass jemand es beaufsichtigt“, sagt Fine. „Für diese Art von System kann man nicht nur einen allgemeinen IT-Mitarbeiter haben. Sie brauchen jemanden, der sich mit KI auskennt. Wir sind auch gerade mit dem Umzug in unsere neue Einrichtung fertig und haben das System noch nicht neu in Betrieb genommen.“ Er hat nach einem anderen Unternehmen gesucht, das etwas Ähnliches macht, sagt aber, dass er noch nichts gefunden hat, das den Anforderungen von Kanfit entspricht. „Wir werden einen Weg finden, es bald wieder in Betrieb zu nehmen“, fügt er hinzu.
Was ist also der wahre Vorteil? „Erstens, was man nicht messen kann, kann man auch nicht managen“, sagt Fine. „Zweitens ist die Datenmenge, die wir haben, selbst für uns als kleine Fabrik so riesig, dass wir schon längst nicht mehr eine oder mehrere Personen haben, die mit all diesen Daten umgehen können. Ich kann mir gar nicht vorstellen, wie das für Boeing oder Airbus sein muss. Wir müssen die Maschinen jetzt miteinander sprechen lassen. Lassen Sie sie tun, was sie gut können, und lassen Sie uns Menschen das große Ganze betrachten und neue Lösungen entwickeln, die auf dem basieren, was sie uns zeigen können.“
Bleiben Sie dran für weitere Blogs zu Composites 4.0 und CW 's Feature-Artikel im Juli.
Harz
- So entwerfen Sie industrielle IoT-Systeme mit DDS und LabVIEW 2017
- Wärme und Lager:Wellendehnung bewältigen
- Additive Fertigung mit Verbundwerkstoffen in der Luft- und Raumfahrt und Verteidigung
- Braskem kooperiert mit Universität für nachhaltige Kunststoffproduktion durch CO2-Abscheidung und -Verwendung
- Können ERP- und MES-Systeme mit dem IIoT Schritt halten?
- Bewältigung des Black Friday 2020 – und des „Crazy Thursday“ der Hersteller
- TxV Aero Composites erfüllt die AS9100-Standards
- Composites One und IACMI veranstalten zweitägigen Workshop
- 3D-Druckverbundwerkstoffe mit Endlosfasern
- Kopplung von KI und Robotik mit mehreren Inspektionssystemen