Nachweisen des LM-PAEK-Schweißens für einen multifunktionalen Rumpfdemonstrator
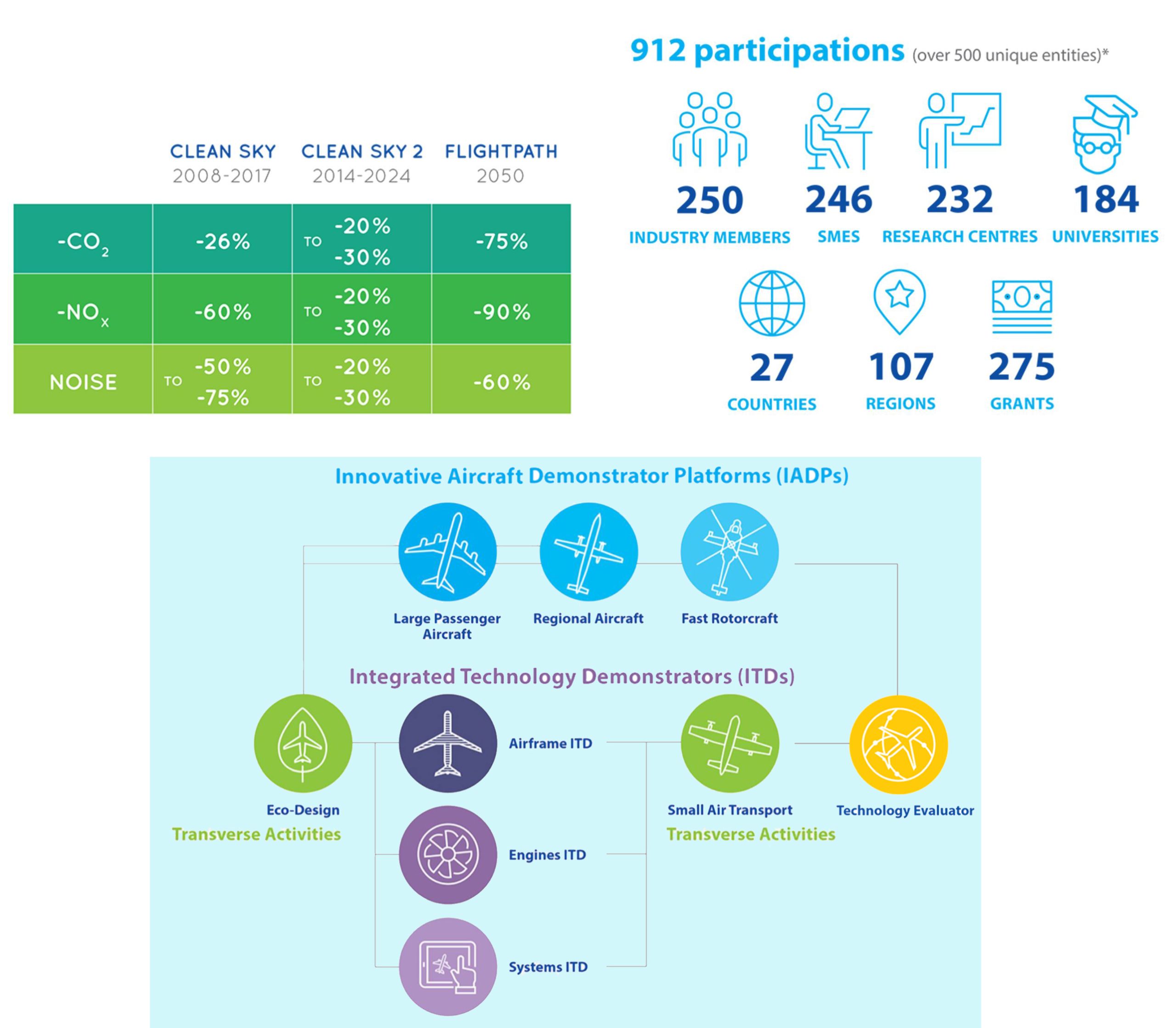
Diese Art der Luftfahrtforschung begann mit dem Rahmenprogramm (RP) der Europäischen Kommission zur FuE-Förderung, das sich vom 2. RP (1987-1991) bis zum 7. RP (2007-2013) erstreckte. Diese Programme haben wesentlich dazu beigetragen, eine Vielzahl von Technologien zum Technologiereifegrad (TRL) 6 zu reifen und in Flugzeugen wie dem Airbus A350 zu implementieren.
Einer der Unterschiede in Clean Sky 2 ist die Organisation rund um große Demonstranten. Das MFFD ist eine von drei Rumpfsektionen in Originalgröße, die innerhalb der Innovative Aircraft Demonstrator Platform (IADP) für Large Passenger Aircraft (LPA) produziert werden (siehe blauer Text oben im blauen Quadrat in der Infografik oben) . Innerhalb der LPA IAPD gibt es drei Plattformen. Das MFFD befindet sich innerhalb der Plattform 2 „Innovative Physical Integration Cabin-System-Structure“, die zwei weitere große Demonstratoren umfasst.
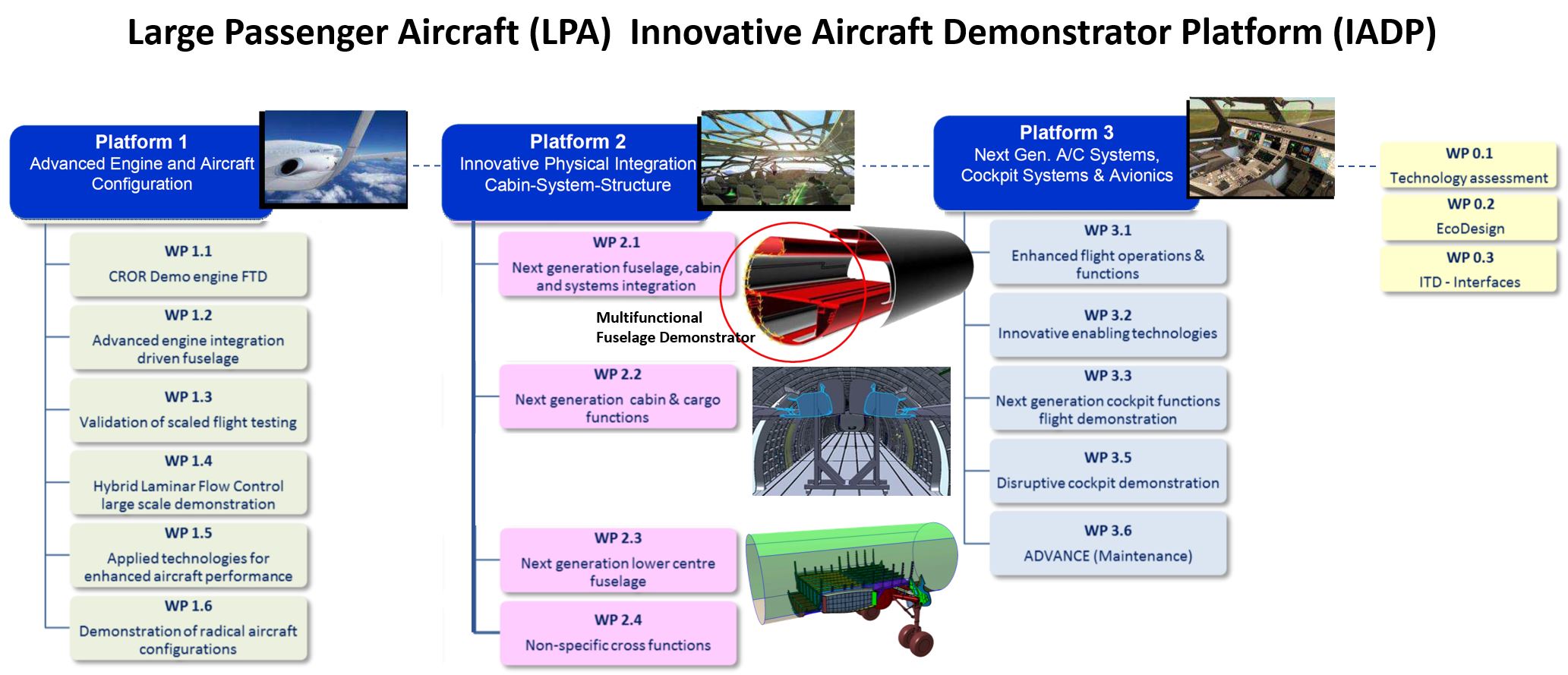
Um zu verstehen, was das bedeutet, gehe ich auf etwas zurück, das mir Ingenieure von Airbus Airframe Research &Technology (R&T) aus Getafe, Spanien, während meiner Forschungen zu multifunktionalen Verbundwerkstoffen im Jahr 2015 erzählten Verschwendung bei der Herstellung eines äußeren Strukturzylinders und eines inneren Zylinders; wir wollen die strukturelle Flugzeugzelle in die Kabinensysteme integrieren.“ Ich hatte Mühe, mir vorzustellen, was das bedeutete – bis ich eine Skizze des MFFD sah.
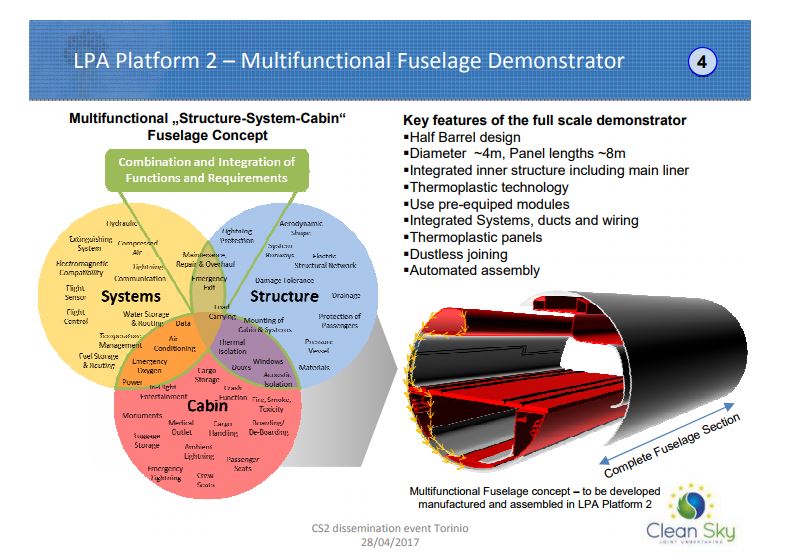
QUELLE | Verbreitung von Clean Sky 2 (CS2) und „Demonstratoren für thermoplastische Verbundwerkstoffe – EU-Fahrplan für zukünftige Flugzeugzellen“.
„Modularität, Integration und die Schaffung gemeinsamer Plattformen sind der Schlüssel“, sagt Ralf Herrmann, Airframe R&T Typical Fuselage bei Airbus Operations GmbH (Bremen, Deutschland) und Leiter des MFFD-Programms. Ich zitiere hier von der MFFD-Seite auf der Clean Sky 2-Website:
Herrmann:"Wir wissen seit langem, dass die Vorteile der Gewichtsreduzierung und der Senkung wiederkehrender Kosten in der Flugzeugproduktion — beim Einsatz von thermoplastischen Verbundwerkstoffen — kann nur durch die Integration mehrerer Disziplinen erreicht werden. Dies bedeutet, dass die Konzentration auf die Struktur allein kann nicht den vollen Nutzen der Verbundwerkstofftechnologie erzielen.“
Die Vielseitigkeit von Thermoplasten muss in Kombination mit einem Designansatz genutzt werden, so Clean Sky 2-Projektleiter Paolo Trinchieri:„Es ist notwendig, die künstliche Funktionstrennung aufzuheben in der Flugzeug-Vorentwurfsphase und eine hohe Produktionsrate der Flugzeugfertigung, Montage und Installation gleich zu Beginn einzuplanen.“
Herrmann war zuvor Projektleiter für das FP7-Projekt MAAXIMUS (More Affordable Aircraft Structure through eXtended, Integrated, &Mature nUmerical Sizing). MAAXIMUS, das von April 2008 bis September 2016 lief, umfasste 60 Partner und zielte darauf ab, die schnelle Entwicklung und die richtige Validierung auf Anhieb – durch gleichzeitige Reifung virtueller und physischer Voraussetzungen – eines hochoptimierten Rumpfes aus Verbundwerkstoff zu demonstrieren, um eine Reduzierung der Montagezeit um 50 % von zu erreichen große Rumpfsektionen, 10 % weniger wiederkehrende Kosten, 10 % geringeres Strukturgewicht und 20 % kürzerer Entwicklungszyklus. Die Ziele der MFFD können als Erweiterung gesehen werden:
- Ermöglichen Sie Produktionsraten von 70-100 Flugzeugen/Monat
- Rumpfgewicht um 1.000 kg reduzieren
- Reduzieren Sie wiederkehrende Kosten um 20 %.
Ein Schlüsselfaktor ist das staubfreie Verbinden (keine Löcher, keine Befestigungselemente) über geschweißte thermoplastische Verbundkomponenten. Herrmann erklärt, dass der derzeitige sequentielle Ansatz im Flugzeugbau – bei dem die Rumpfstruktur ziemlich vollständig sein muss, bevor Systeme sowie Kabinen- und Frachtfunktionen installiert werden können – zeitaufwändig und „fehleranfällig“ ist. Stattdessen verfolgt MFFD vorbestückte, hochintegrierte Strukturelemente und Systemmodule, die schon sehr früh, lange vor der Endmontage, eingebaut werden können.
Wechsel zu Längsfugen und LM PAEK
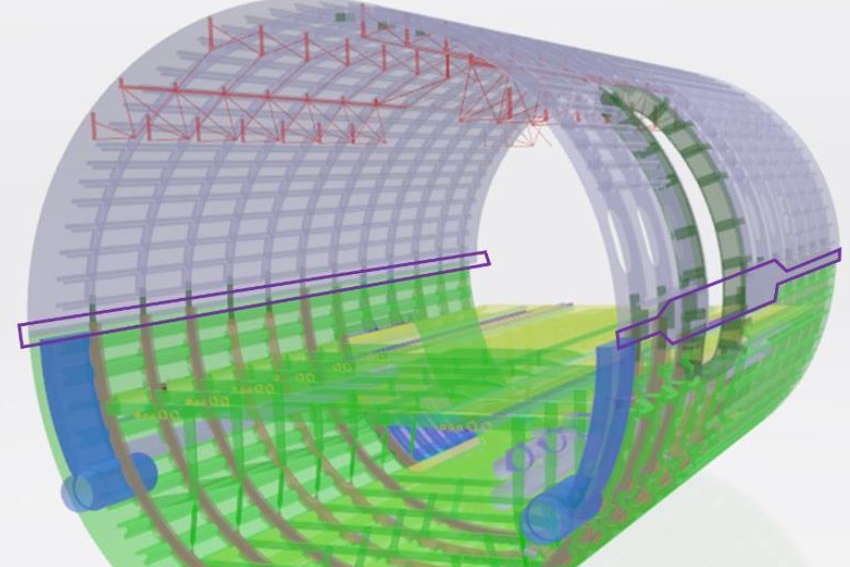
Die Projektaktivitäten des MFFD haben 2017 begonnen. Jedes Jahr gibt es mindestens einen Call for Proposals (CFP), in dem die ProjektleiterInnen Themen mit Weiterentwicklungsbedarf skizzieren. Wie in der Abbildung unten zu sehen ist, wurde das in CFP08 (April 2018) gezeigte Diagonalgelenk-Design bis CFP09 (Sep 2018) in ein Längsgelenk geändert.
„Die Schrägfuge brachte Probleme in Bezug auf die Zugänglichkeit und Befestigung von Bodenkonstruktionen mit sich, von denen wir erkannten, dass sie im gegebenen Zeitrahmen nur schwer zu bewältigen waren“, erklärt Herrmann. „Deshalb haben wir uns entschieden, auf das konventionelle Design zurückzugreifen, um das Risiko zu senken. Unser Hauptinteresse besteht darin, zu zeigen, wie alle Systeme und Kabinenelemente integriert werden können, die vor der Hauptkomponentenmontage (MCA) installiert werden können. Dies ist auch das erste Mal, dass dieser thermoplastische Verbundwerkstoff in großformatigen Primärrumpfstrukturen für große Passagierflugzeuge eingesetzt wird.“
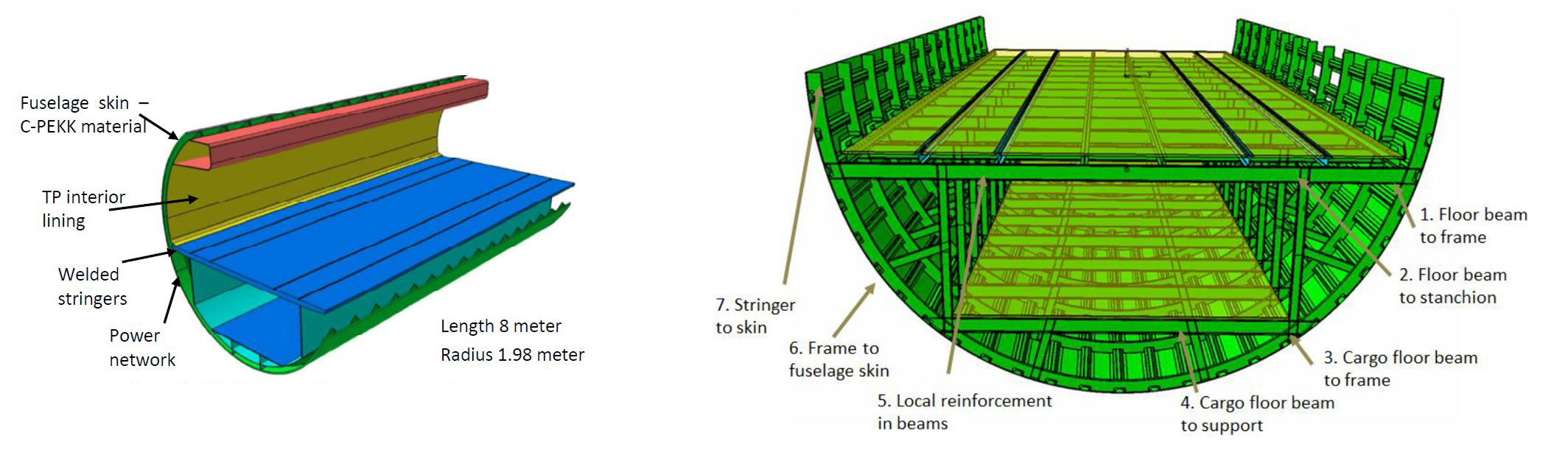
Das MFFD-Design wurde 2018 von einem Schräggelenkdesign zu einem konventionelleren Längsgelenk geändert. QUELLE | CFP08 S.87 (links) und CFP09 S. 133 (rechts).
Eine weitere Änderung betraf das thermoplastische Verbundmaterial (TPC)-Matrixmaterial. MFFD-Themen in CFP08 und CFP09 beziehen sich auf Kohlefaser/PEKK (Polyetherketonketon), aber in CFP10 (März 2019) wurde das Basismaterial als Kohlefaser und PAEK (Polyaryletherketon) beschrieben. PAEK ist die Gesamtfamilie von Polymeren, in der PEEK, PEKK und LM PAEK enthalten sind.
Wie in meinem Blog zu PEEK vs. PEKK vs. PAEK beschrieben, stellt der Cetex-Materiallieferant TenCate, jetzt Toray Advanced Composites, alle drei Polymere als carbonfaserverstärktes Band her und behauptet, die Eigenschaften seien im Wesentlichen gleich. Cetex TC1225 CF/LM PAEK Klebeband schmilzt bei 305 °C während TC1320 CF/PEKK Klebeband schmilzt bei 340 °C . Und laut Scott Unger, dem globalen CTO von Toray Advanced Composites, „hat LM PAEK einen viel besseren Fluss … und kann auch mit höheren Geschwindigkeiten als PEKK und PEEK verarbeitet werden.“ TC1225 kostet auch weniger.
Unterer Rumpf des MFFD:Projekt ATEMBERAUBEND
STUNNING ist der Projektname für die Entwicklung und Fertigung der voll ausgestatteten unteren Hälfte des MFFD. Das Projekt soll weiter reifen:
- Automatisierte Montageprozesse
- Thermoplastische Fertigungs- und Montagetechnologien
- Integrierte Design- und Fertigungsentwicklungstechnologien
- Entwicklung fortschrittlicher elektrischer Systemarchitekturen.
Bas Veldman, Programmmanager bei GKN Fokker (Hoogeveen, Niederlande) und Projektmanager für STUNNING, erklärt, dass das MFFD 8 Meter lang und 4 Meter breit mit einem Radius von 2 bis 2,5 Metern sein wird, was für einen Single-Aisle ein echter Maßstab ist Flugzeuge der A320-Familie. „Sie ähnelt der A321, die nicht genau kreisförmig ist, sondern ungefähr eiförmig (etwas höher als breit)“, fügt er hinzu.
Die 180°-Rumpfuntersektion umfasst die untere Rumpfschale mit verschweißten Stringern und Spanten, die Kabinen- und Ladebodenstruktur sowie relevante Hauptinterieur- und Systemelemente. „Wir werden große, vormontierte Module für eine sehr schnelle Plug-and-Play-Montage liefern“, sagt Veldman.
GKN Fokker ist der Lead Partner von STUNNING und hat vier Geschäftsbereiche beteiligt, darunter Aerostructures (Papendrecht, Niederlande), Fokker ELMO (Hoogerheide, Niederlande), GKN Fokker Engineering Romania (Bukarest) und GKN Fokker Technologies (Papendredcht, Niederlande). GKN Fokker ELMO ist ein Anbieter von Flugzeugkabelbäumen und elektrischer Systemtechnik. „Es ist für die Systemarchitektur in STUNNING verantwortlich und wird sich auf die Optimierung des elektrischen Systems konzentrieren“, erklärt Veldman, „und arbeitet mit dem CFP08-Konsortium MISSION an der Entwicklung eines innovativen Energiebussystems.“
„Diehl Aviation (Laupheim, Deutschland) ist verantwortlich für die Innenstruktur, einschließlich der Subsysteme und des Bodens, der Seitenwandpaneele und ihrer Verbindung, der Monument-Schnittstellen und der intelligenten System-Multiports“, so Veldman weiter. „Das NLR (Netherlands Aerospace Centre, Amsterdam) ist für die Fertigung der Rumpfhaut und der Stringer verantwortlich, und die TU Delft unterstützt mit ihrer Expertise beim Ultraschallschweißen bei der Montage.“ (Weitere Informationen zum Ultraschallschweißen finden Sie unter „Schweißen von thermoplastischen Verbundwerkstoffen“.)
MECATESTERS-Schweißtestprogramm
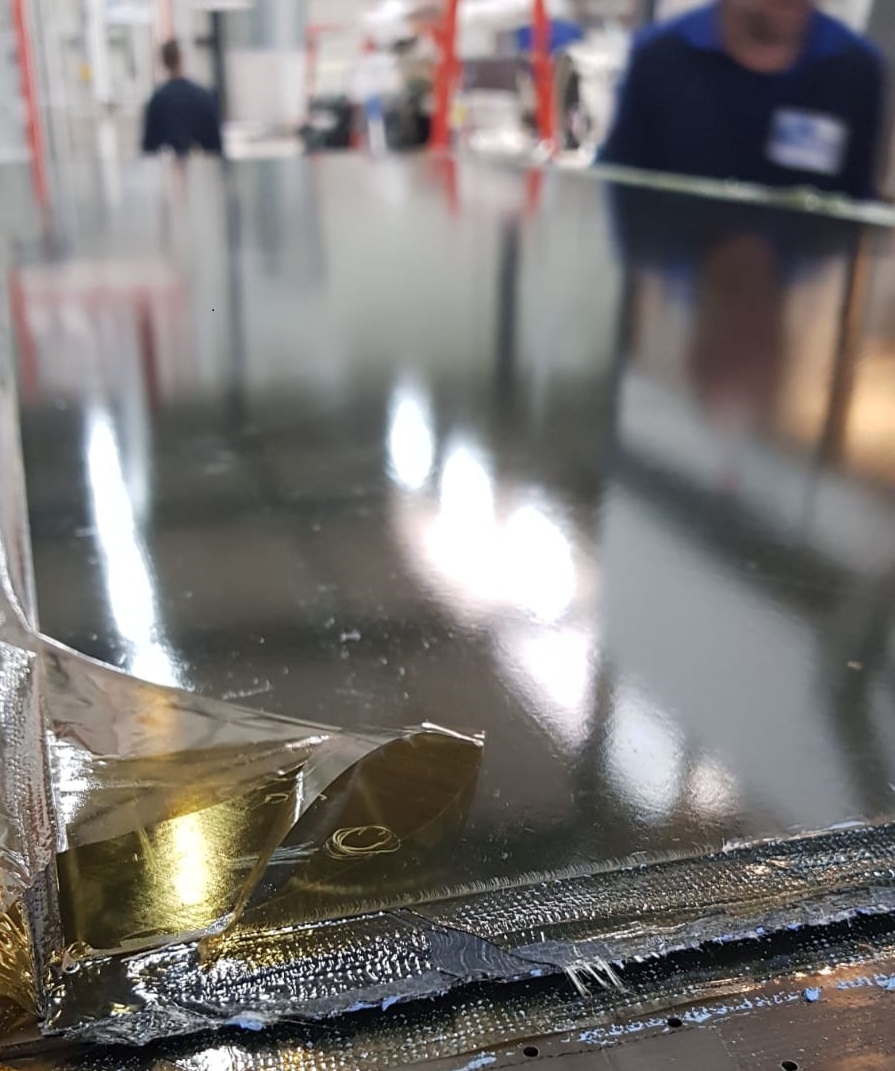
„STUNNING hat sieben GFP-Themen auf den Weg gebracht und fünf haben mit der Arbeit begonnen, darunter MAYA, MISSION, EMOTION, TCTool und MECATESTERS“, sagt Veldman. Letzteres ist ein großes Schweißtestprogramm mit KVE Composites (Den Haag, Niederlande) und Recoll (Pessac, Frankreich), die im April 2019 mit einer Laufzeit von 30 Monaten begann. Veldman erklärt, dass, obwohl KVE eine lange Geschichte mit dem Induktionsschweißen von thermoplastischen Verbundstoffen sowohl von Geweben als auch von UD-Band hat, die induktionsgeschweißten Teile, die bis heute in Flugzeugen fliegen, Gewebe verwendet haben. „In STUNNING etablieren wir Best Practices mit UD-Verstärkungen und LM PAEK-Materialien und vergleichen auch das Induktionsschweißen mit dem Leitungsschweißen unter typischen Belastungs- und Umgebungsbedingungen im Betrieb.“ Obwohl Widerstandsschweißen und Ultraschallschweißen in anderen MFFD-Arbeitspaketen und CFPs enthalten sind (siehe „Die beiden Hälften verbinden ” unten), Induktionsschweißen und Konduktionsschweißen sind die einzigen beiden Techniken in MECATESTERS.
Labordus von KVE erklärt, dass KVE für die drei MECATESTERS-Arbeitspakete (WP 1, 2 und 3) alle Testlaminate mit autoklavgehärtetem TC1225 UD-Kohlefaser-/LM-PAEK-Band herstellen wird (siehe „Erstes Toray LM-PAEK-Laminat für Clean Sky MECATESTERS-Projekt“). KVE wird auch induktionsgeschweißte Proben für Tests vorbereiten, während GKN Fokker konduktionsgeschweißte Proben herstellt und Rescoll alle physikalischen Tests durchführt. „Der Name Rescoll leitet sich von Research und Collage ab, was französisch für Bindung ist“, sagt Labordus. „Sie sind bekannt für ihre Forschung zu allen Arten von Kleben und bieten ein gut ausgestattetes Testlabor für Polymere und Verbundwerkstoffe, einschließlich mechanischer, Umwelt-, Entflammbarkeits- und allen möglichen Tests zur Qualifizierung in der Luft- und Raumfahrt, Automobilindustrie, Bahn und anderen Industrien.“
Prozessparameter und Tests
„Wir beginnen eigentlich mit WP 2, um Prozessparameter wie Ober- und Untergrenzen für Induktionsschweißtemperatur und -druck festzulegen“, sagt Labordus. „Zum Beispiel haben wir ein nominales Druck, den wir normalerweise verwenden, aber wir gehen zu niedrigeren Drücken, bis wir beginnen, Defekte wie Hohlräume zu sehen, und dann werden wir diese Schweißeigenschaften bewerten, um die niedrigere Druckgrenze festzulegen.“ Die Prüfung wird auch die Schweißgeschwindigkeit bewerten, die die Abkühlgeschwindigkeit und Kristallinität der Schweißnaht und möglicherweise die mechanischen Eigenschaften beeinflusst. Dieselben Parameter werden bei Fokker für das Leitungsschweißen untersucht.
Zur Bewertung führt das MECATESTERS-Programm mehrere Tests durch, darunter:
- Überlappungstest gemäß ASTM D5868-01
- Abzieh- und Schertest an L-Profil-Coupons
- GIC und GIIC nach ISO 15024 bzw. ISO 15114
(diese Zähigkeitsprüfung wird tatsächlich in WP 1 abgeschlossen)
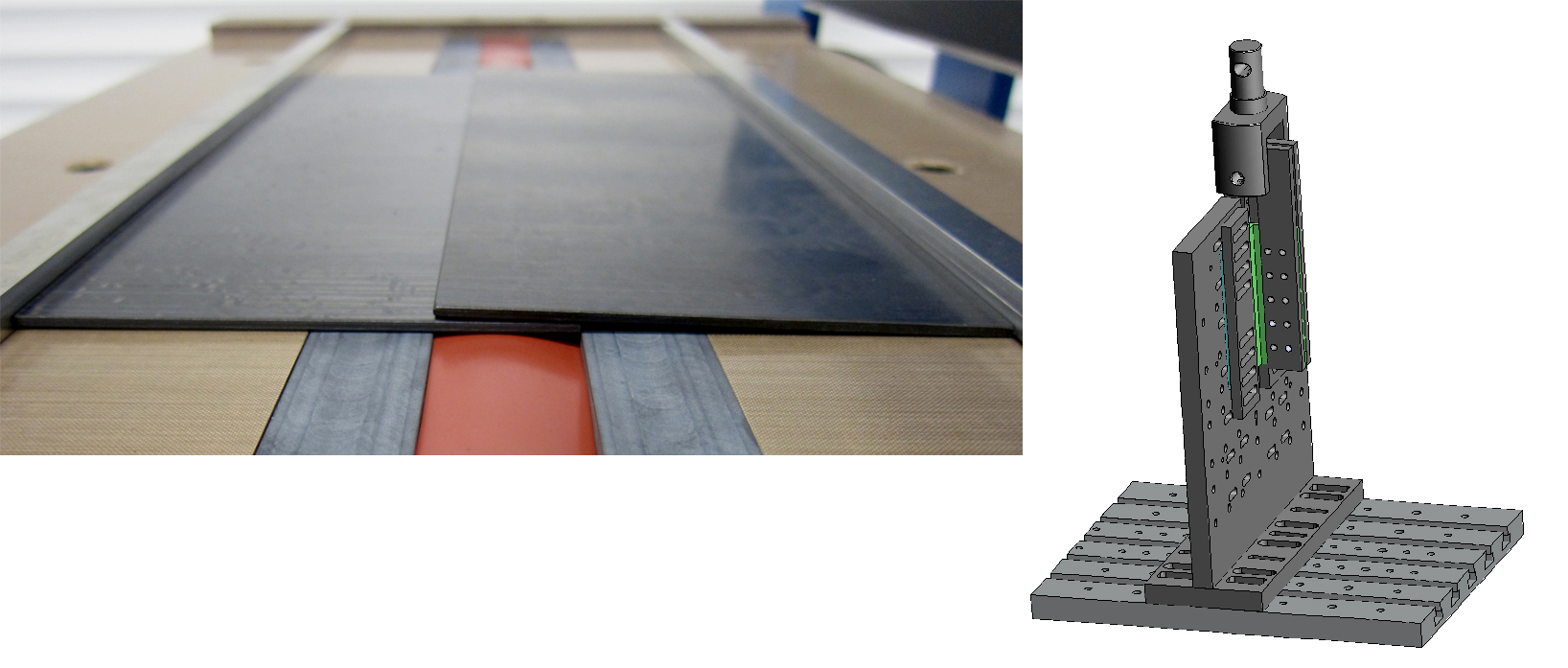
Einzel-Überlappungs-Scher-Coupon aus UD-Bandlaminat bereit zum Induktionsschweißen (links) und Prüfvorrichtung für kombinierte Scher- und Abschälprüfung von geschweißten L-Profil-Coupons mit einem von Rescoll entwickelten Werkzeug (rechts). QUELLE | KVE Composites, Rescoll.
„Das Abziehtestverfahren stammt aus einem internen Standard, den GKN Fokker entwickelt hat“, erklärt Rescoll-Ingenieur Thomas Salat. „Die Abziehprüfung der geschweißten Profile erfolgt senkrecht zur Außenhaut für die Schälbelastung“, bemerkt Labordus, „und parallel zur Außenhaut für die Scherbelastung. Schälen und Scheren sind die beiden Extreme, aber wir werden auch neue Kombinationen davon testen, die praktische Lastbedingungen im Betrieb widerspiegeln.“ Diese Tests werden für zwei unterschiedliche Laminatdicken, die aus dem MFFD-Rumpfdesign abgeleitet sind – 2,2 und 2,8 Millimeter – bei Raumtemperatur (RT), Kälte (-55 °C) und hoher Temperatur (80 °C) unter statischer Belastung durchgeführt.
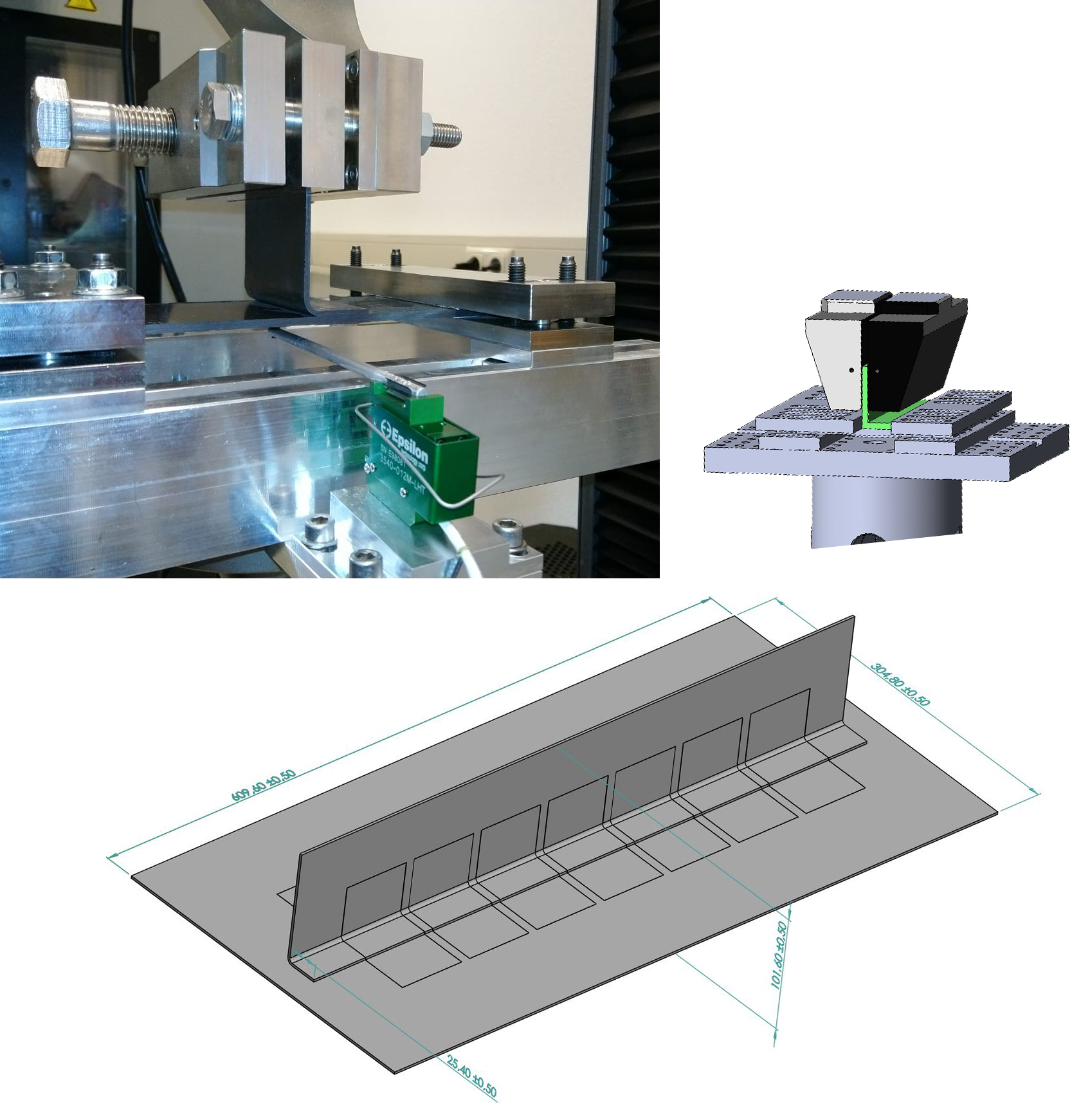
Abziehversuche an L-Profil-Coupons bei KVE Composites (oben links). Bei MECATESTERS wird diese Art von Tests einen von Rescoll entwickelten Greifer und einen Testaufbau verwenden, um die Hautdurchbiegung zu eliminieren (oben rechts). Testcoupons werden aus geschweißten Platten geschnitten (unten). QUELLE | Rescoll, KVE Composites.
Oberflächenvorbereitung, Alterung und Ermüdung
WP 1 beginnt mit der Zähigkeitsprüfung. „Für die Rissprüfung (GIC und GIIC) werden wir einen Riss im Verbund initiieren und messen, wie sich dieser Riss unter Belastung verhält“, erklärt Salat. „Einer davon ist ein statischer Test, der die Belastung bis zum Ausfall erhöht. Wir werden auch einen dynamischen Test durchführen, bei dem wir die statische Belastung eine Million Mal wiederholen, was ein bis zwei Wochen dauert. Wir werden sehen, ob die Verbundschweißung dieser Ermüdung standhält. Dieser Modus II ist eine neue Art des zyklischen Tests. Wir entwickeln eine Methode, die einem von der University of Europe veröffentlichten technischen Papier entnommen ist, und finalisieren die Parameter jetzt.“
Auch in AP 1 werden die in AP 2 festgelegten Schweißparameter verwendet, um die Auswirkungen der Oberflächenvorbereitung sowie Alterung und Ermüdung zu untersuchen. „Wir werden uns Oberflächenverunreinigungen ansehen und wie diese die Schweißnaht beeinflussen können“, sagt Labordus. „Wir werden auch drei verschiedene Arten von Trennmitteln untersuchen, die üblicherweise in der Pressen- und Autoklavenverarbeitung verwendet werden; spezielle Arten der Oberflächenvorbereitung, einschließlich Schleifen, Schleifmittel und Plasmabehandlung; und auch die Verwendung eines zusätzlichen Harzfilms an der zu schweißenden Oberfläche. Darüber hinaus werden wir den Einfluss der Faserorientierung untersuchen, zum Beispiel plus/minus 45 Grad an der Schweißgrenzfläche.“
Rescoll wird außerdem eine Konditionierungskammer bei 70 °C und 90 % Luftfeuchtigkeit verwenden, um die Alterung im Betrieb zu simulieren, sagt Salat. „Wir werden dann die Standardtests durchführen, um zu sehen, ob dies die Schweißleistung beeinflusst.“ Labordus fügt hinzu, dass eine begrenzte Anzahl von Proben bei 100 °C und 120 °C entnommen wird, „um die Behauptung zu bestätigen, dass thermoplastische Verbundwerkstoffe keinen starken Knockdown über 80 °C aufweisen.“
Neben dem dynamischen Riss-/GIIC-Test werden Ermüdungstests in den Modi Single-Laps-Shear und Pull-Off durchgeführt. „Wir beginnen bei 80 Prozent der statischen Versagenslast und erreichen 50 oder 75 Prozent davon bei Ermüdung für eine Million Zyklen“, sagt Labordus. „Wir werden auch andere Tests durchführen, diskutieren diese aber noch“, fügt Salat hinzu.
Schweißen an kurze Verbundklammern
Obwohl die Details von WP 3 noch nicht abgeschlossen sind, sollen Schweißnähte von formgepressten Brackets aus Kurzfasermaterial mit der UD-Laminathaut untersucht werden. „Wir werden erneut Prozessparameter vergleichen und die mechanischen Eigenschaften der Schweißnaht charakterisieren“, sagt Labordus, „aber wir arbeiten noch daran, die Geometrie für Tests zu definieren.“
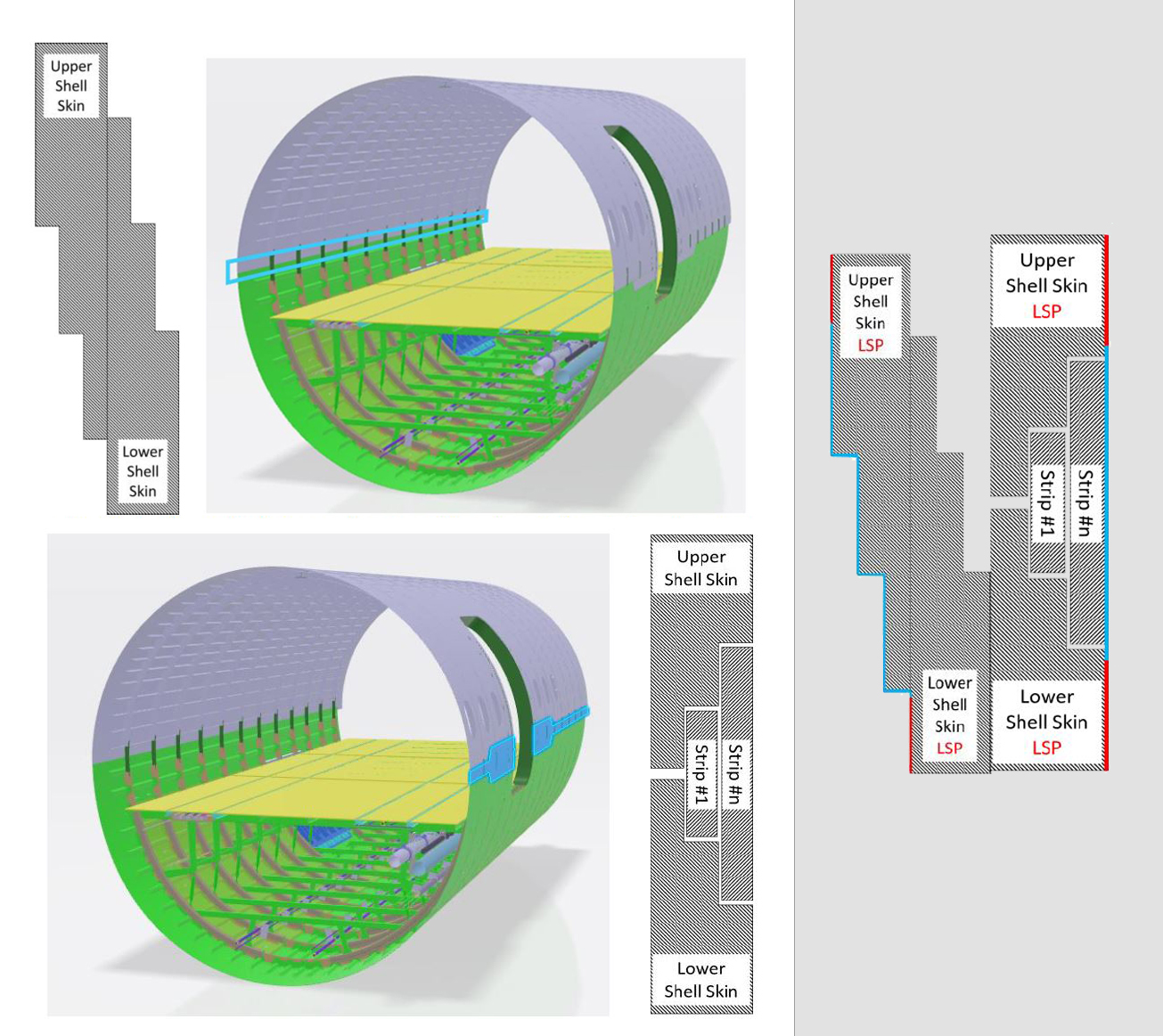
Stringer und Clips an einen thermoplastischen Rumpf geschweißt. QUELLE:Clean Sky 2 11 th Aufforderung zur Einreichung von Vorschlägen JTI-CS2-2020-CfP11-LPA-02-35, „Innovative Disbond-Arretierfunktionen für lange thermoplastische Schweißverbindungen“, Abbildung 2, p. 94.
Geschweißte Clips und Halterungen
Wie im CFP10-Thema JTI-CS2-2019-CfP10-LPA-02-31 beschrieben, werden alle Rahmenclips und Systemhalterungen für das MFFD-Rumpfunterteil im Spritzguss von Kurzfaser-Compounds hergestellt, die durch Wiederverwendung von Fabrikabfällen aus die Produktion von Endlosfaser-TPC-Laminaten bei GKN Fokker. CF/PAEK ist das Basismaterial und Schweißen ist das Basisverbindungsverfahren, obwohl das spezifische Schweißverfahren nicht vorgeschrieben ist.
Laut CFP10-Text wird der untere MFFD-Rumpf 13 Spanten und etwa 36 Stringer haben, was ungefähr 500 Spanten-Clips erfordert (beachten Sie, dass dies primäre Strukturen sind, die strukturelle Tests erfordern, und diese Gesamtzahl umfasst Clips, die zum Testen verwendet werden) und ungefähr 270 Systemhalterungen (die Sekundärkonstruktionen) aufgeteilt nach den unten aufgeführten Typen:20 Systemkonsolen (1), 120 Systemkonsolen (2), 50 Systemkonsolen (3) und 80 Systemkonsolen (4).
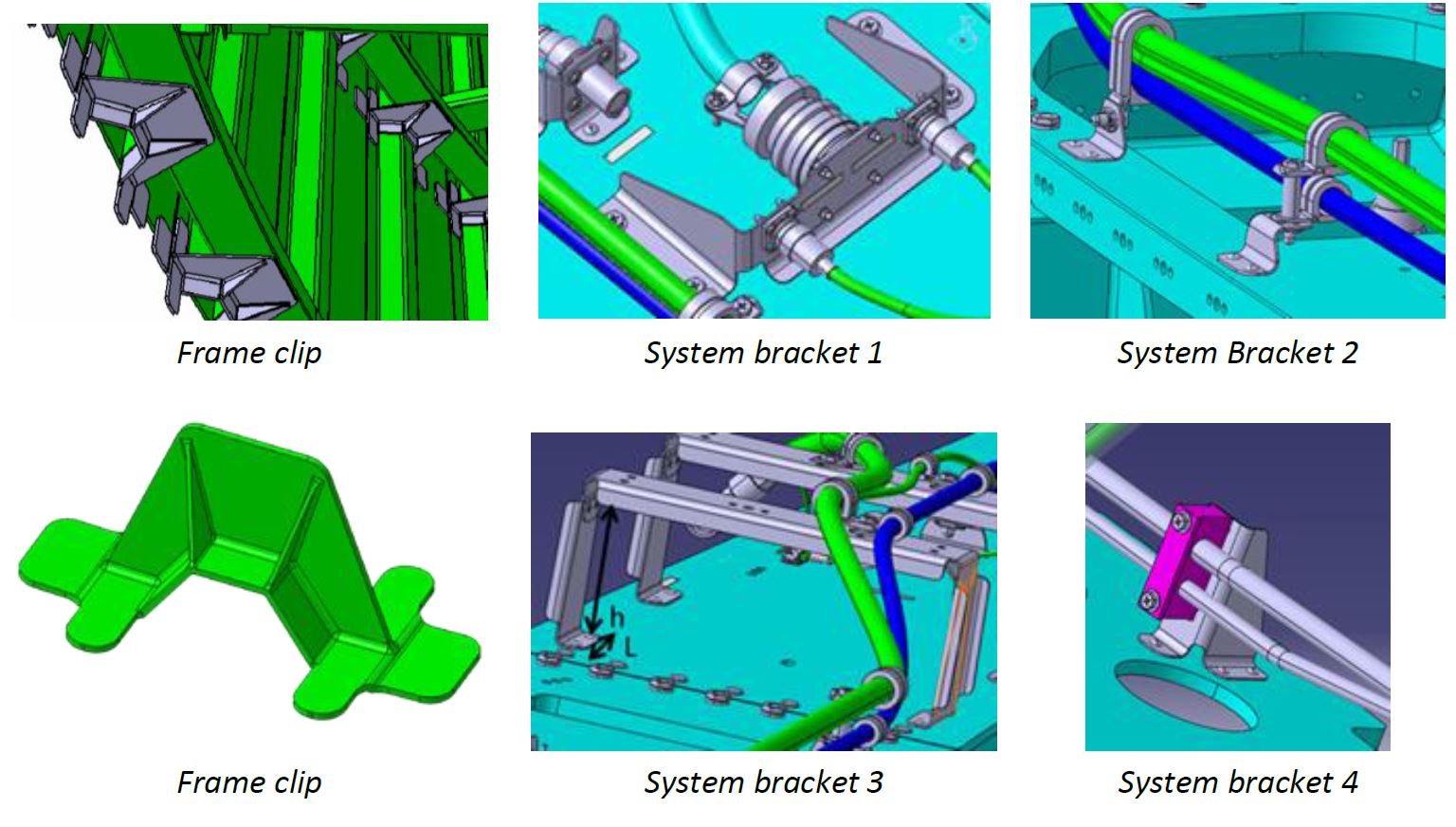
Beispiele für zu liefernde Teile in Clean Sky 2 Thema JTI-CS2-2019-CfP10-LPA-02-31, Abbildung 2. QUELLE | Clean Sky 2 CFP10, p. 146.
Ebenfalls in CFP10 ist das MFFD-Oberrumpfthema JTI-CS2-2019-CfP10-LPA-02-30, „Entwicklung innovativer Schweißsysteme für strukturelle Verbindungen von thermoplastischen Verbundwerkstoffen auf Matrixbasis“ unter der Leitung von Aernnova Composites Illescas (Illescas, Spanien). Der Beginn nach dem 1. Quartal 2020 ist die Entwicklung eines Schweißsystems, um eine strukturelle Verbindung zwischen Verstärkungsteilen (Zwickel, Keile, Beschläge) und Strukturrahmen zu erreichen, um eine hochintegrierte Türumfassungsstruktur (DSS) zu erhalten. Ich hoffe, in einem zukünftigen Blog mehr Details zum oberen Rumpf des MFFD geben zu können. Im Moment reicht es aus zu verstehen, warum das MECATESTERS-Arbeitspaket 3 wichtig ist und wie viel erreicht wird, wenn MECATESTERS, STUNNING und die MFFD abgeschlossen sind.
Die beiden Hälften vereinen
Nach Fertigstellung wird die untere Hälfte des MFFD an das Fraunhofer-Institut für Fertigungstechnik und Angewandte Materialforschung IFAM (Stade, Deutschland) gehen, um mit der oberen Hälfte verbunden zu werden, erklärt Veldman. „Wir sind entschlossen, unsere Rumpfhälfte bis Ende 2021 zu liefern“, fügt er hinzu.
Wie oben erwähnt, ist Ralf Herrmann bei Airbus der MMFD-Projektleiter; Damit integriert Airbus die Arbeit des Fraunhofer IFAM und des Konsortiums CFP07 MultiFAL (Multifunktionales Automatisierungssystem für Rumpfmontagelinie) —um Lösungen für die unzähligen Herausforderungen zu entwickeln.
Einige davon werden im 11. ten in zwei Themen enthüllt Aufforderung zur Einreichung von Vorschlägen (Nov. 2019), beide unter der Leitung von Airbus, beginnend nach dem 4. Quartal 2020 und mit dem Titel „Werkzeuge, Ausrüstung und Hilfsmittel für die Schließung einer longitudinalen Fassverbindung:“
- JTI-CS2-2020-CfP11-LPA-02-33, „:Integration der Schulterriemen und Kontinuität des Blitzschlagschutzes“
- JTI-CS2-2020-CfP11-LPA-02-34, „:Überlappungsverbindung und Rahmenkupplungsintegration“
Geschrieben von Piet-Christof Woelcken, Themenmanager bei Airbus Bremen und Leiter des MFFD-Arbeitspakets, sind die wichtigsten Herausforderungen in diesen Themen:
JTI-CS2-2020-CfP11-LPA-02-33
- Stoßriemenverbindung (Abb. 3 unten):
- Die linke Seite des Demonstrators (in Flugrichtung) enthält die Beifahrertürverkleidung. Die Variation der Hautdicke in diesem Bereich erfordert eine abgestufte Integration des Gesäßriemens, die die obere und untere Haut verbindet.
- Angesichts der Komplexität der Verbindung, Leitungsschweißen die Verwendung einer beheizten Druckplatte ist die bevorzugte Fügetechnik.
- Elektrische Kontinuität des Blitzeinschlagschutzes (Abb. 4 unten):
- Elektrischer Durchgang des metallischen Blitzeinschlagschutzes (LSP) muss über beide Längsfugen an der Außenseite des Rumpfes erreicht werden.
- Es wird erwartet, dass zu diesem Zweck der für die Hinterriemenintegration vorgesehene Werkzeugkopf verwendet werden kann.
JTI-CS2-2020-CfP11-LPA-02-34
- Überlappungsstoß (Abb. 2 unten):
- Die 8 Meter lange Überlappungsfuge auf der rechten Seite der Demonstratoren (in Flugrichtung) verbindet die obere und untere Rumpfhaut. In Längsrichtung ist eine Hautdicke unter 3 mm in der Schweißzone konstant. In Umfangsrichtung weisen die Häute eine abgestufte Geometrie für eine verbesserte strukturelle Leistung auf.
- Ultraschallschweißen ist die bevorzugte Verbindung, um eine hohe Produktionsrate zu erreichen.
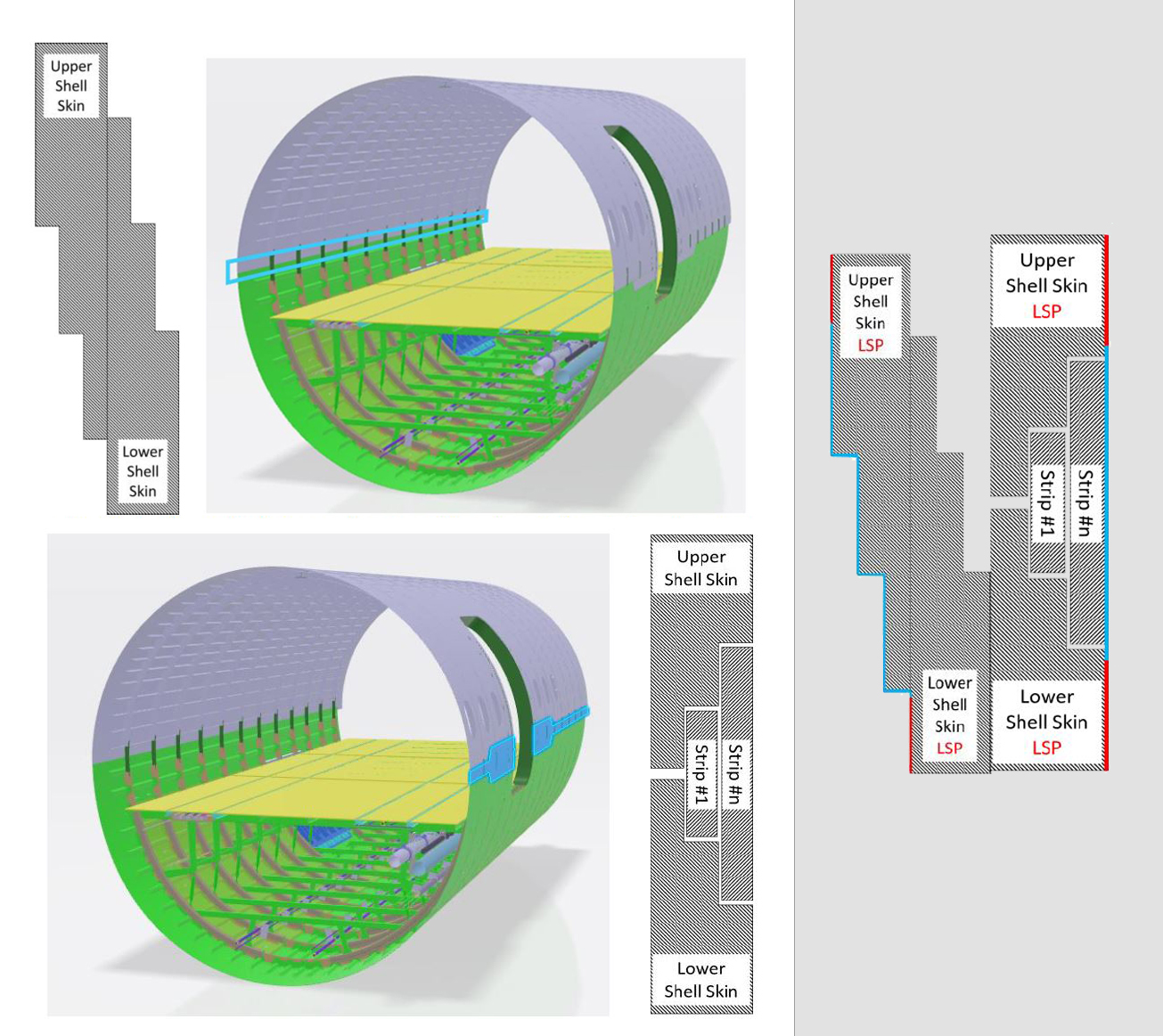
Abb. 2 (oben links) :Überlappungsstoß:Bei der Gestaltung der Überlappungsfuge wurde ein gestufter Ansatz gewählt. Beachten Sie, dass die untere Schale auf der Innenseite des Rumpfes liegt. Abb. 3 (unten links) : Integration des Stoßriemens:Eine Reihe von übereinander liegenden Streifen erfordert eine Integration über die Stufenverbindung. Beachten Sie, dass der Butt Strap an der Außenseite des Rumpfes sitzt. Abb. 4 (Rechts) :Über die Längsfugen an der Außenseite des CFK-Rumpfes muss eine elektrische Durchgängigkeit von metallischem LSP erreicht werden. Rot weist auf vorgerüstetes LSP hin, blau bedeutet LSP, das als Teil dieses Themas angewendet werden soll. QUELLE | Clean Sky 2 11. th Aufforderung zur Einreichung von Vorschlägen JTI-CS2-2020-CfP11-LPA-02-33 und -34, „Integration von Stoßriemen und Kontinuität des Blitzschlagschutzes“, S. 78 und 86.
JTI-CS2-2020-CfP11-LPA-02-34
- Integration der Frame-Kopplung (Abb. 5):
- Überlappungsstoß:Rahmenkupplungen unter dem Überlappungsstoß müssen den oberen und den unteren Schalenrahmen strukturell verbinden.
- Butt Strap:Rahmenkupplungen unter dem Butt Strap müssen den oberen und unteren Schalenrahmen strukturell verbinden und mit der Haut verbinden.
- Widerstandsschweißen ist die bevorzugte Technologie für diese technische Herausforderung.
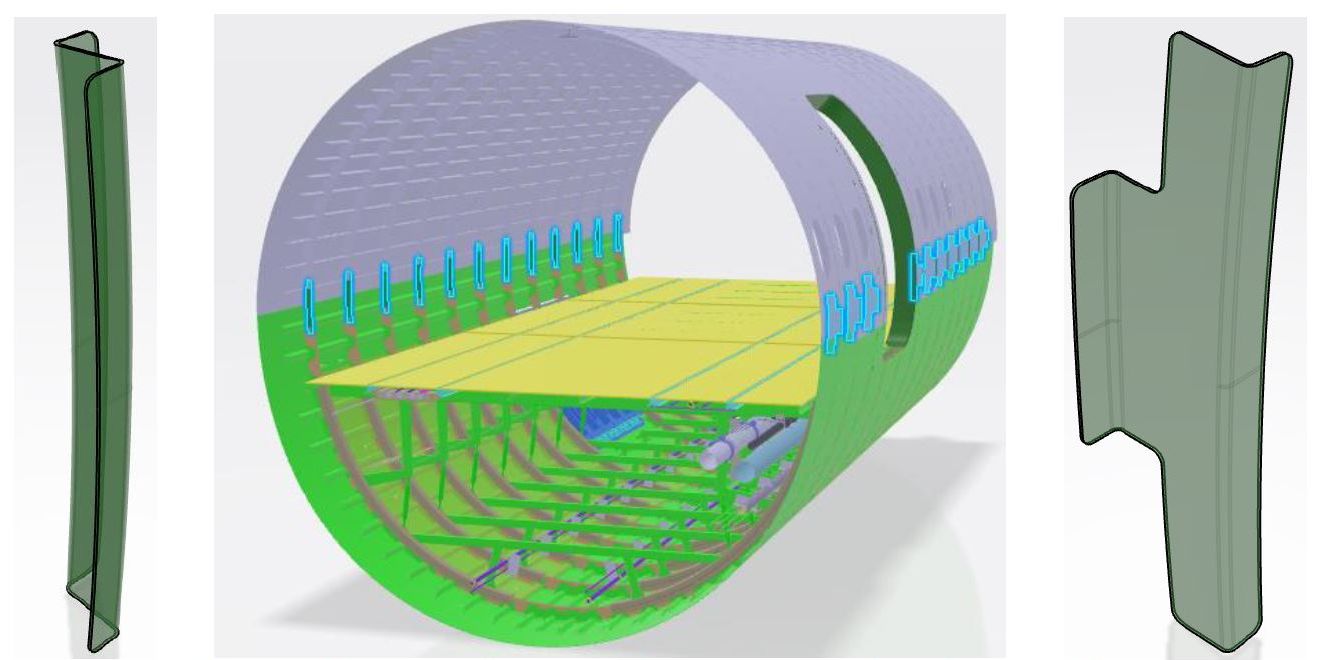
Integration der Rahmenkopplung. Beachten Sie, dass sich die Rahmenkupplungen im Rahmen der Technologiedemonstration von Seite zu Seite unterscheiden. QUELLE | Clean Sky 2 11. th Aufforderung zur Einreichung von Vorschlägen JTI-CS2-2020-CfP11-LPA-02-34, „Werkzeuge, Ausrüstung und Hilfsmittel für den Verschluss einer längs verlaufenden Tonnenverbindung:Überlappungsverbindung und Integration der Rahmenkupplung“, Abb. 5, S. 86.
Schweißmethoden, Werkzeugköpfe und Toleranzen
Herrmann erläutert, dass auf der linken Seite über die Stoßlaschenverbindung das Konduktionsschweißen und auf der rechten Seite über die Überlappungsverbindung das Ultraschallschweißen demonstriert wird, während für die Rahmenkupplungen Widerstandsschweißen verwendet wird. „MFFD wird viele technische Ansätze demonstrieren, es ist also nicht dasselbe wie bei der Herstellung eines tatsächlichen Rumpfes, sondern ist stattdessen als Vehikel zur Demonstration und Ausreifung von Technologien konzipiert“, fügt er hinzu.
Entwicklung von Schweißwerkzeugköpfen
Ziel dieser beiden von Wölcken verfassten Themen ist es, die erforderlichen Werkzeugköpfe für diese Schweißverbindungen zu entwickeln. „Wenn Sie zwei Teile zusammenschweißen, müssen Sie Hitze und Druck anwenden“, erklärt er. „Dies wird also vom Werkzeugkopf beim Schweißen aufgebracht. Beim Konduktionsschweißverfahren nach Fokker wird auf der einen Seite aktiv Wärme und Druck ausgeübt, auf der anderen Seite wird passiver Druck von einem Träger ausgeübt. Die Stoßverbindung ist ein Stapel von sechs Bändern, und beim Verbinden werden wir den Stapel platzieren und während des Schweißens erhitzen. Da das LM PAEK UD-Bandmaterial jedoch relativ neu im Schweißen ist, müssen wir die Prozessbedingungen verstehen und wie wir Toleranzen ausgleichen können. Daher müssen wir die Materialien und die Dicke sowie die Geometrie des Werkzeugkopfs definieren.“
„Beachten Sie, dass die Verwendung dieser Art von Stoßfugen ein Standardverfahren für das ist, was wir an anderen Verbindungen in unseren Flugzeugen tun“, betont Wölcken. „Für das MFFD möchten wir den oberen und unteren Rumpf von dieser Standardpraxis unverändert lassen, um den Materialaufwand zu minimieren, den wir maßschneidern müssen.“
Flexibilität bei Toleranzen
Da die obersten Schweißflächen quasi flüssig aufgeschmolzen und dann zusammengepresst werden, „gibt dies viel Flexibilität, um Toleranzen auszugleichen“, sagt Wölcken. Hinweis derzeit mit Thermoset Bei Tragflächen und Rümpfen aus kohlenstofffaserverstärktem Polymer (CFK) werden diese Toleranzprobleme durch Auftragen eines flüssigen Zwischenlagenklebers behoben. Obwohl nur wenige Leute dies öffentlich diskutieren wollen, ist das allgemeine Problem des Shimming in Verbund-Flugzeugstrukturen weithin anerkannt und es wurden Initiativen zu seiner Reduzierung und/oder Eliminierung veröffentlicht, wie zum Beispiel die Flexmont-Montagemethode für Seitenleitwerke.
“ Vorteile bei der Einhaltung von Toleranzen erwarten wir uns durch den Einsatz thermoplastischer Verbundwerkstoffe“, sagt Wölcken, „insbesondere durch die Nutzung unserer Konstruktionskonzepte und unsere Erfahrungen mit duroplastischem CFK und metallischem Schweißen. Der Schlüssel wird die In-Situ-Überwachung während des Erhitzens und der Druckanwendung sein.“ Er betont, dass Wärme der Parameter Nummer eins ist. „Ich bin überrascht, wie drucktolerant die Schweißprozesse von thermoplastischen Verbundwerkstoffen sind. Die größte Herausforderung besteht darin, diesen Druck einzudämmen und wie er abfällt. Derzeit überwachen wir die Rückseite der Schweißverbindung.“
Automatisiertes Montageanlagensystem des Fraunhofer IFAM (oben links) mit Maßangaben zu Beginn des CFP07-Arbeitsthemas (oben rechts) wird umgebaut, um einen 360°-Rumpf zum Schweißen der Längs- und Umfangsfugen des MFFD aufzunehmen. QUELLE | Fraunhofer IFAM und cfk-valley.com, Clean Sky 2 7 th Aufforderung zur Einreichung von Vorschlägen, JTI-CS2-2017-CfP07-LPA-02-22, p. 76.
Montageautomatisierung
Im 7. ten Call for Proposals, das Thema JTI-CS2-2017-CfP07-LPA-02-22, »Entwicklung eines vollwertigen, automatisierten Anlagensystems für Rumpflängs- und Umfangsfugen« wird vom Fraunhofer IFAM innerhalb des MultiFAL-Konsortiums geleitet. Der folgende Auszug gibt Aufschluss darüber, wie die oben diskutierten Schweißwerkzeugköpfe, die sich derzeit in der Entwicklung befinden, implementiert werden könnten:
“Um den Montageprozess eines thermoplastischen Rumpfes zu realisieren, werden Toleranzen zu einem großen Thema. The positioning and orientation of the fuselage shells, as well as resulting deformations caused by the welding process, need to stay within the tolerances. Comparable accuracies can be oriented to the state-of-the-art process of longitudinal joint. Here, the position error in each direction should be within 0.5 mm (in some exceptions up to 1 mm). … it can be assumed that a pre-load on the joint surface from both sides of approximately 1000N (independent of the welding technology) for a welding seam of 20 mm width is required by the automation system.”
Fraunhofer IFAM — which was also CTC Stade’s partner in developing the Flexmont VTP assembly process — describes its starting point:an in-house assembly plant system which can manipulate parts from 2 to 8 meters long and up to 6 meters high, including a 180° shell of a single-aisle aircraft. The system is enabled by a flexible arrangement of 10 cooperating hexapods (see “Reconfigurable Tooling:Revolutionizing composites manufacturing”), 24 linear units and modular rack elements. Vacuum grippers with 6-axis force and torque sensors adjust the pose and shape of the part, as required, to manage tolerances during assembly. The guidance and monitoring of these rapid, iterative adjustments is achieved through optical measuring devices.
According to the CFP07 text, Fraunhofer IFAM will modify this assembly plant system for holding a complete 360° fuselage, with work scheduled to begin in Q2 2018 and completed in 36 months.
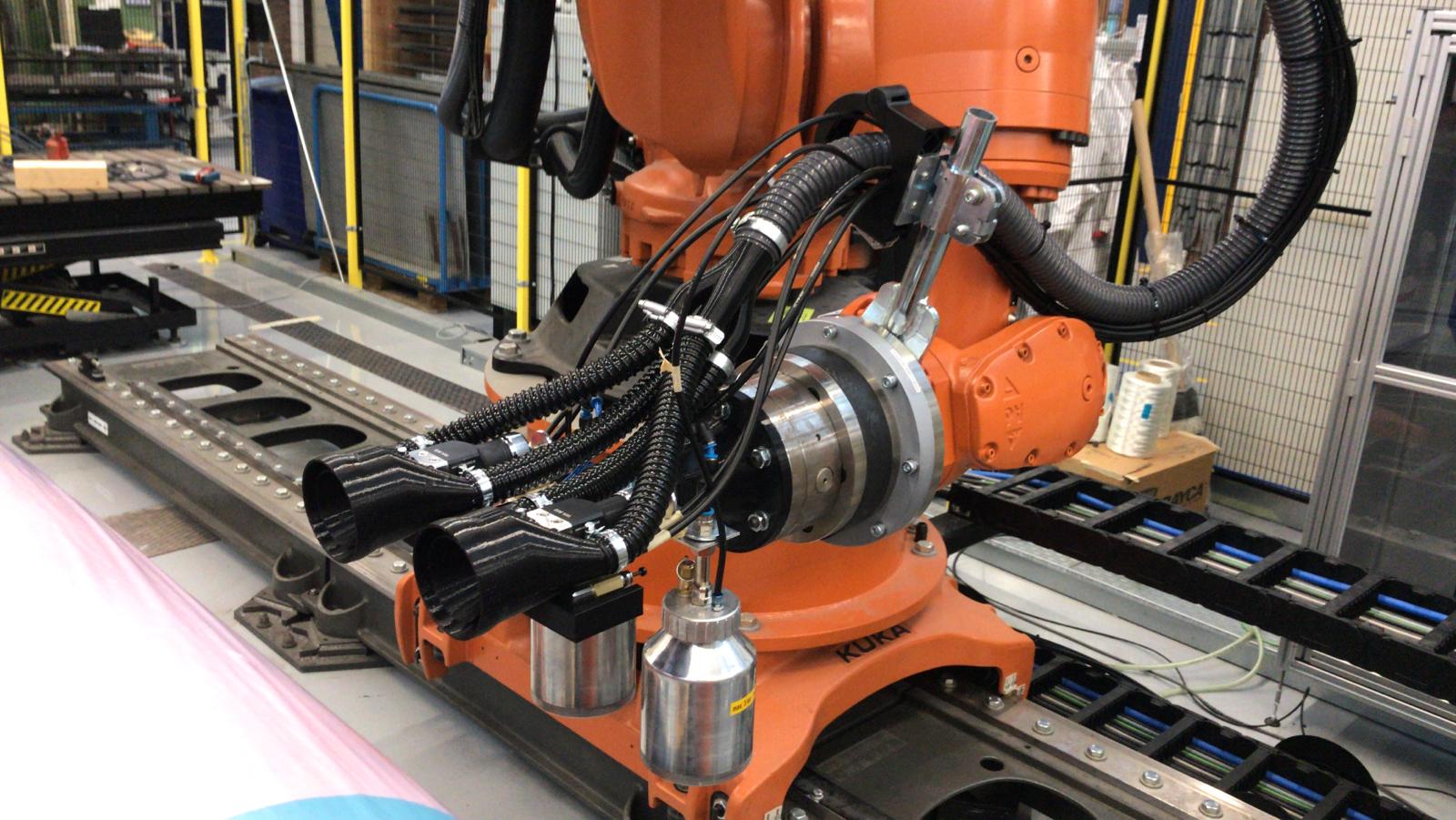
The STUNNING consortium is working with SAM|XL to develop automation for assembling the MFFD lower fuselage. SOURCE | samxl.com
Within STUNNING, activities are planned with the collaborative research center SAM|XL (Smart Advanced Manufacturing XL, Delft, Netherlands) to demonstrate automated welding techniques for assembling the lower fuselage. Specializing in automation for manufacturing large, lightweight composite structures, SAM|XL brings together TU Delft’s Aerospace Engineering group and Robotics Institute. GKN-Fokker is a major participant. One of the methods being investigated is sequential spot ultrasonic welding, which was proven in the Clean Sky 1 Eco Design project and TAPAS 2 as a fast and effective for connecting short fiber-reinforced brackets or clips to fuselage structures.
In her 2016 paper, titled “Smart ultrasonic welding of thermoplastic composites,” Villegas states that it is possible to scale up the ultrasonic welding process via sequential welding — that is, letting a continuous line of adjacent spot welds serve the same purpose as a continuous weld bead. Lab-scale sequential spot welding was used in the Clean Sky EcoDesign demonstrator’s TPC airframe panel, using flat energy directors to weld a CF/PEEK hinge and CF/PEKK clips to CF/PEEK C-frames (Fig. 6). Experimental comparisons with mechanically fastened joints in double-lap shear and pull-through tests showed promise. The process is further explored in 2018 papers {and 2019 papers} by Villegas’ TU Delft team member Tian Zhao {and in Villegas’ 2019 paper}.
— “Welding thermoplastic composites”, G. Gardiner, 2018.
The STUNNING consortium’s work with TU Delft and SAM|XL is adapting this technology to weld multiple system and semi-structural brackets, stiffening elements and stringers to the MFFD lower fuselage shell.
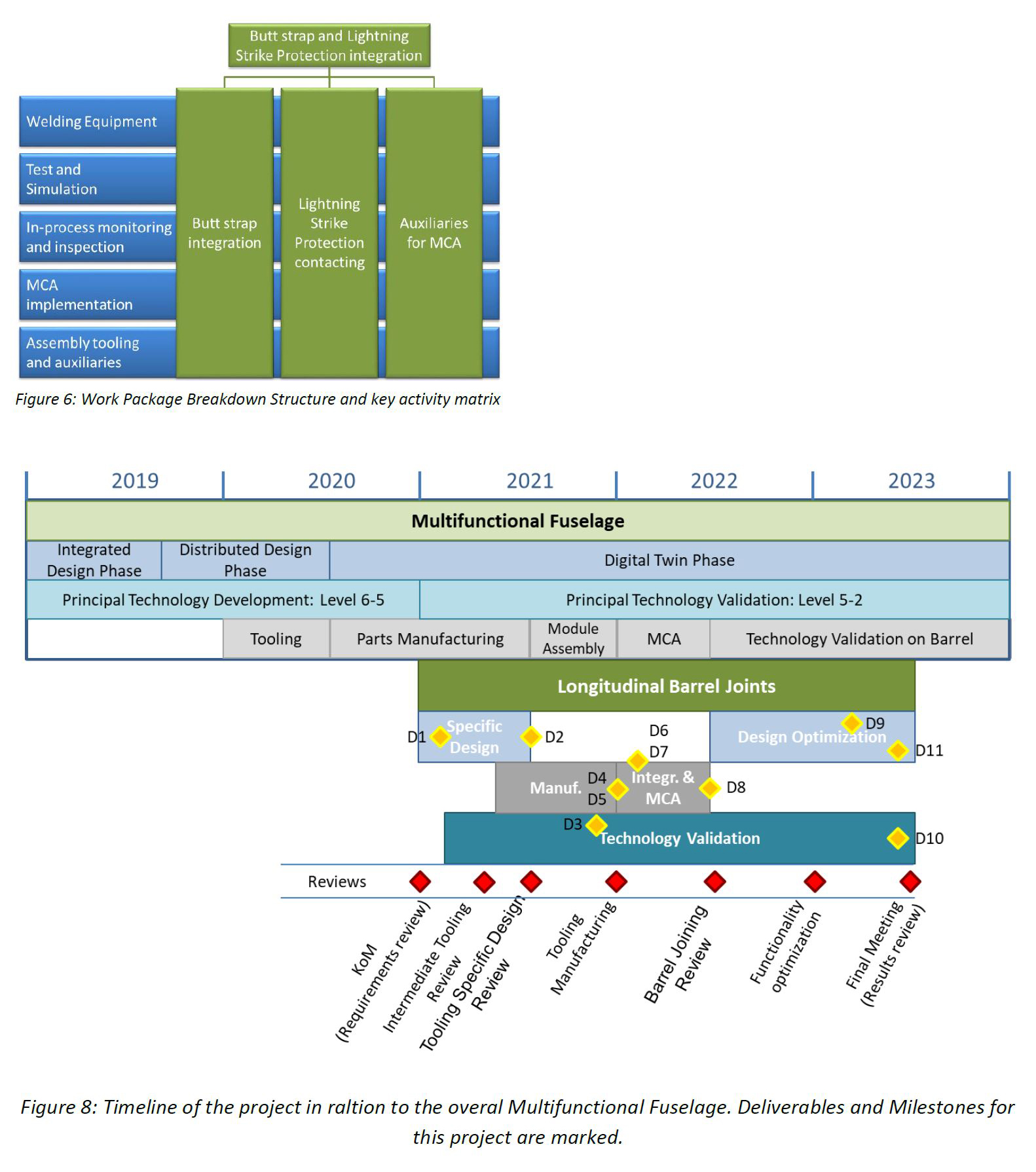
Work breakdown and timeline for MFFD assembly. SOURCE | Clean Sky 2 11 th Call for Proposals JTI-CS2-2020-CfP11-LPA-02-33, “Tooling, Equipment and Auxiliaries for the closure of a longitudinal Barrel Joint:Butt strap integration and Lightning Strike Protection continuity”, pp. 79 and 82.
Digital twin phase, 2020 and beyond
According to the Clean Sky website, the MFFD program reached an important milestone in Nov 2019 with the successful passing of its Critical Design Review (CDR). In the timeline above, the MFFD design enters a “Digital Twin Phase” in 2020-2021. What does this mean? “Though we have wrapped up the majority of the design phase, we are taking it a bit further by working with a specific lifecycle management approach,” explains Herrmann. “We are modeling imperfections and nonconformities from the NDT results and process parameters during component manufacturing. We want to combine this Industry 4.0 data with lifecycle management so that we continue to tailor the design according to what we are actually manufacturing. We want to see how far we can push this and what we can accomplish by the end of Clean Sky 2.”
For 2020, the chief agenda is manufacturing. “We hope to present various parts as they come together this year,” says Veldman. What will the largest challenge be for the STUNNING program? “Assembly,” he answers. “Not so much within STUNNING, but our lower fuselage has interfaces with the door surround structure, multiple Airbus-delivered components and the whole upper fuselage. Getting everything delivered at the right time and then bringing it all together will require a number of developments yet.”
That brings us to perhaps the biggest question:Will thermoplastic composites be used on the next aircraft entering production in 2030-35? “For sure, we want to try to use the technologies we are working on,” says Herrmann, “but I cannot say if or when thermoplastic composites will be on future aircraft. The most important part for us is that they are an enabler for dustless joining regarding ramping production to more than 70 aircraft per month. We have to show that it is feasible, not only with metallics but also with thermoplastic composites.”
“By the end of this project, we will have a more complete understanding of thermoplastic composite welding and will gain approval for its use in large primary aircraft structures,” says Salat. “If we can use this for future aircraft, we can achieve significant weight savings and improved sustainability.” But perhaps just as important is Clean Sky’s ability to bring Europe’s aviation research and innovation stakeholders closer together. “We have quarterly meetings where I sit with all of the LPA steering committee,” says Veldman. “I’m talking to the whole of the European aerospace industry, and it most certainly helps to open up opportunities for the future, not only for companies who can supply to us, but for a wide range of collaborations.”
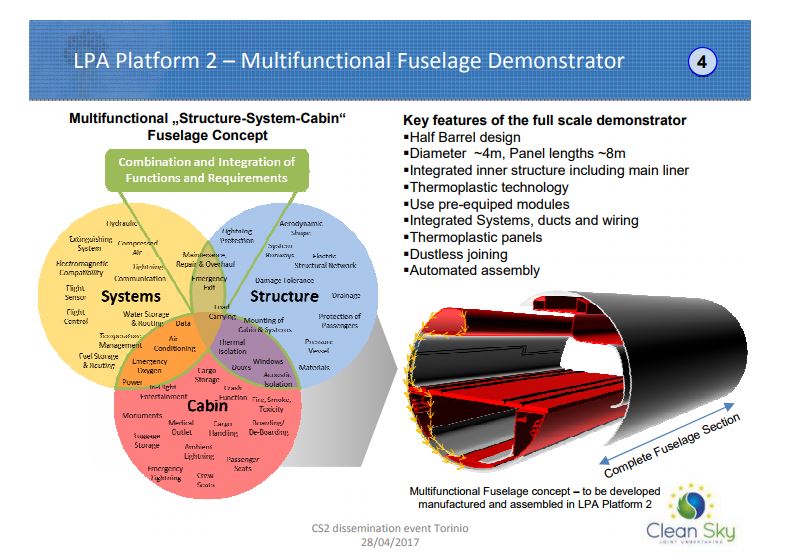
Harz
- 10 3D-Druck-Startups, auf die man 2020 achten sollte
- Anwendungs-Spotlight:3D-Druck für Flugzeugkabinen
- Wert aus Daten für KI herausquetschen
- 6 Schweißtipps für die Anlagenwartung
- Auf der Suche nach einem ultrastarken Kunststoff? Schauen Sie sich FR-4 an!
- Materialien:medizinische Verbindungen und Konzentrate für das Laserschweißen
- Tipps und Tricks zum Schweißen von Inconel
- Victrex- und Bond-Partner für den 3D-Druck von PAEK-Teilen
- Die erste Rumpfsektion aus Verbundwerkstoff für den ersten Verkehrsflugzeug aus Verbundwerkstoff
- Top-Tipps zum Schweißen von Aluminium