DC-Dielektrikumssensoren für die industrielle Herstellung von Verbundwerkstoffen
Da Hersteller versuchen, gleichzeitig die Kosten zu senken und die Produktionsgeschwindigkeit für Verbundteile zu erhöhen, wird die Möglichkeit, in Echtzeit in den Spritzgießprozess zu sehen und Harzfluss, Viskosität, Temperatur, Druck und Tg/Aushärtungszustand zu überwachen, zu einem Unterscheidungsmerkmal. Synthesites (Uccle, Belgien) hat diese Fähigkeit entwickelt. Basierend auf Ergebnissen des Deutschen Zentrums für Luft- und Raumfahrt (DLR, Stade) und des National Composites Centre (NCC, Bristol, UK) hat diese Technologie das Potenzial, die Zykluszeiten um bis zu 50 % zu verkürzen, wobei die Aushärtungsentscheidungen auf Tg und Grad basieren der Aushärtung pro Harz und Teil im Vergleich zu konservativen Zeiträumen basierend auf generischen Materialstudien. Es ist in der Tat ein Fortschritt in Richtung Composites 4.0-Produktion, bei der Daten von Sensoren verwendet werden, um Prozesse und Geräte zu steuern und auch Simulation und Design zu verbessern.
Ich habe zum ersten Mal über Synthesites über das OPTO-Light-Projekt berichtet (siehe „Thermoplastisch umspritzte Duroplaste , 2-Minuten-Zyklus, eine Zelle“). Tatsächlich ist die Möglichkeit, Thermoplaste mit Duroplasten in OPTO-Light ohne . zu verbinden laserablationierte Oberflächen wurden durch den Einsatz von In-Mold-Sensoren für Druck, Temperatur, Gleichstromwiderstand (DCR) und dielektrische Analyse (DEA) ermöglicht. Die DCR-Sensoren wurden von Synthesites geliefert und diejenigen für DEA wurden von Netzsch (Selb, Deutschland) geliefert. Beides sind dielektrische Sensoren, die die elektrischen Eigenschaften des Harzes messen. Im Folgenden werde ich die Geschichte und die Unterschiede dieser Technologien diskutieren.
Die Technologie, die Synthesites mit einer Reihe von kommerziellen Kunden entwickelt hat, ist beeindruckend, darunter die industrielle Produktion von Windflügeln und die harzverstärkten Flügel für die C-Serie, jetzt Airbus 220. Sie wurde auch für eine Reihe von Materialien und Prozessen, einschließlich Autoklaven, demonstriert -ausgehärtetes Prepreg, Harzinfusion und Hochdruck-Harzspritzpressen (HP-RTM).

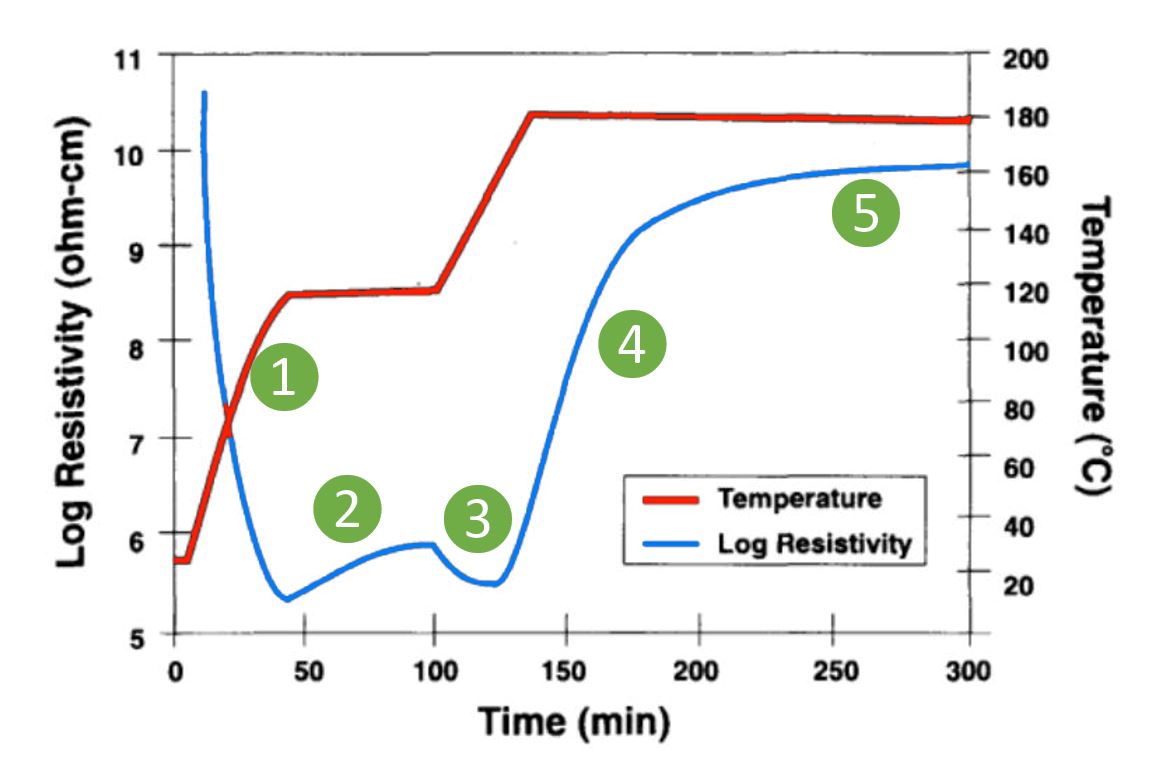
- Die anfängliche Abnahme des spezifischen Widerstands spiegelt die Abnahme der Harzviskosität während des Anstiegs auf ≈120°C wider.
- Während dieser Verweilzeit bei 120 °C erhöht sich der spezifische Widerstand, wenn die Harzviskosität aufgrund der Harzreaktion und des Verlustes an flüchtigen Bestandteilen zunimmt.
- Der spezifische Widerstand nimmt wieder ab und erreicht ein Minimum, wenn das Harz auf 177°C erhitzt wird.
- Der spezifische Widerstand steigt dann schnell an, wenn die Härtungsreaktion schnell abläuft.
- Der Anstieg des spezifischen Widerstands verlangsamt sich, wenn sich die Härtungsreaktion verlangsamt, und nähert sich nach 300 Minuten einer Steigung von Null, wenn sich die Härtungsreaktion dem Abschluss nähert.
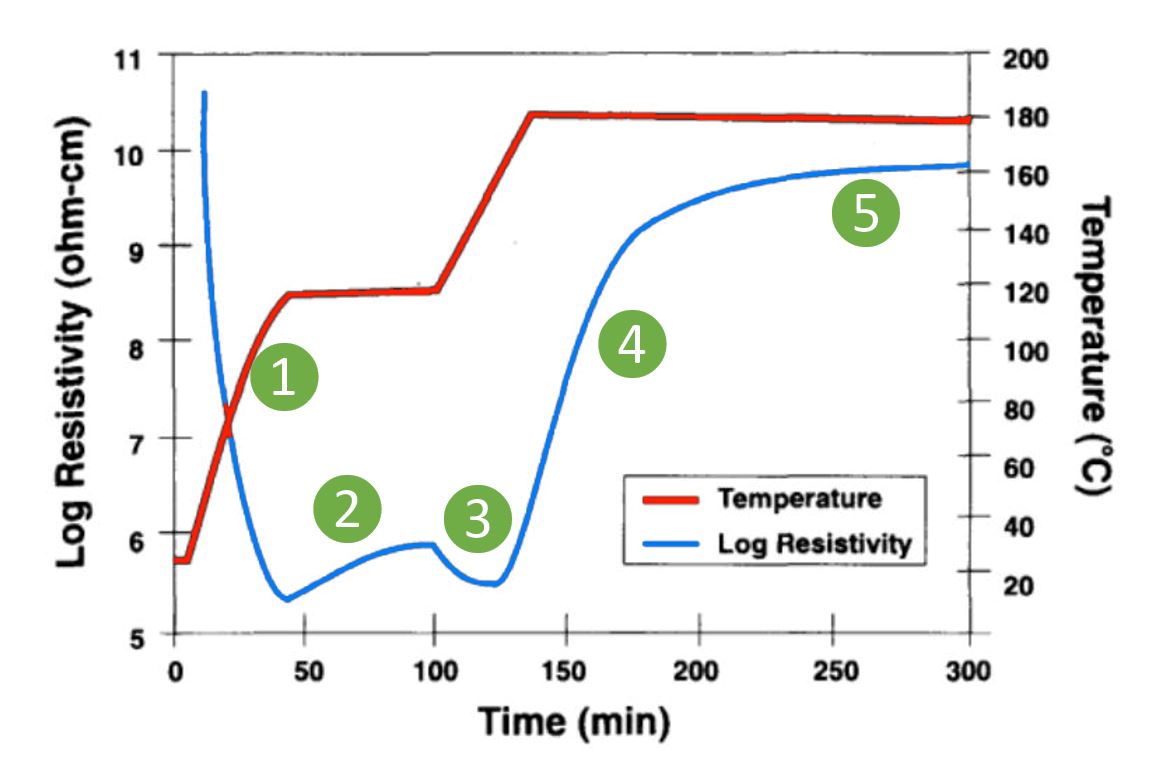
QUELLE | Zerstörungsfreie Charakterisierung von Materialien VIII herausgegeben von Robert E. Green, p. 385.
Die Ionenleitfähigkeit steht in umgekehrter Beziehung zur Harzviskosität vor der Gelierung und zur Steifigkeit nach der Gelierung (hohe Ionenmobilität, niedrige Harzviskosität und geringe Steifigkeit). Die Umkehrung der Ionenleitfähigkeit, der spezifische Widerstand, steht somit in direktem Zusammenhang mit Viskositäts-/Steifigkeitsänderungen im Matrixharz.
Es hat sich gezeigt, dass eine Erhöhung des spezifischen Widerstands mit einer Erhöhung der Tg korreliert. Dies ist die Grundlage des Gleichstromwiderstands (DCR), der nur DEA unter Verwendung von Gleichstrom (DC) ist, und die anfängliche Beschreibung des von Synthesit entwickelten Prozesses.
Wie oben erläutert, basiert diese Technik der Verwendung von Gleichspannung für DEA auf Korrelationen zwischen dem spezifischen Widerstand und dem Härtungszustand. Diese wurden 1962 von R. W. Warfield in „Properties of Crosslinked Polymers as Evidenced by Electrical Resistivity Measurements“, Makromolekulare Chemie, . beschrieben vol. 58. (Siehe unten für die in diesem Abschnitt verwendeten Referenzen.)
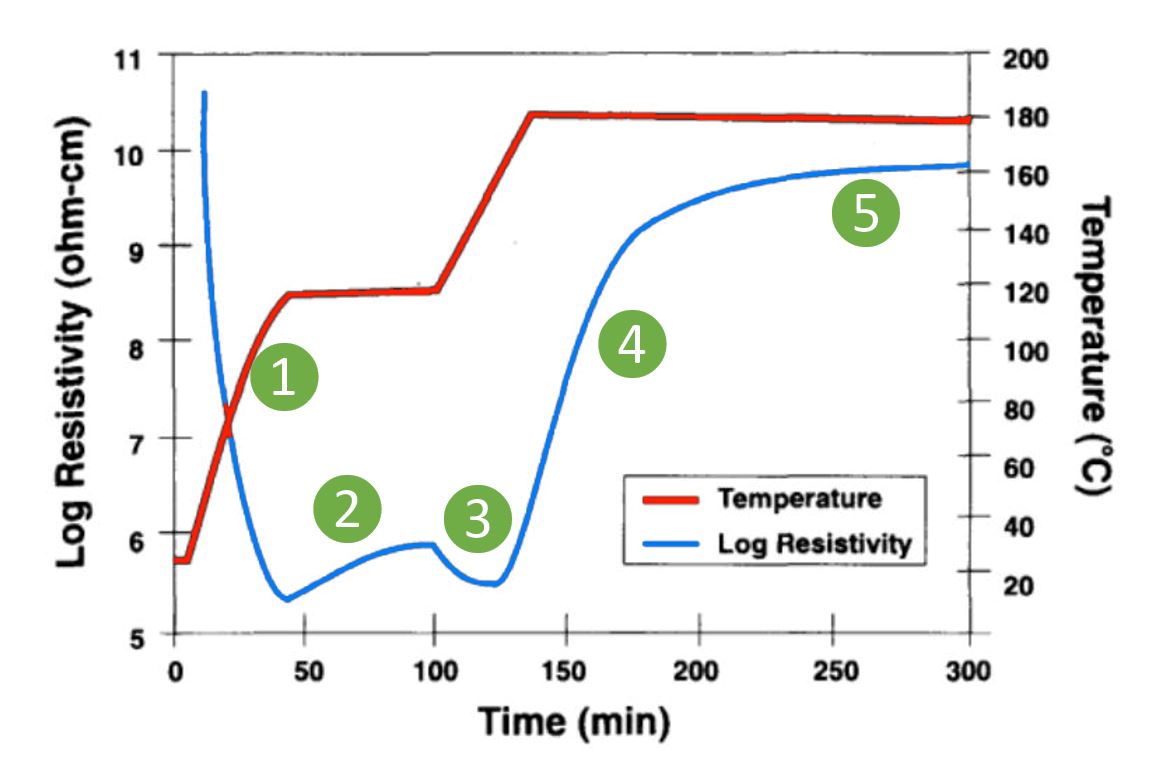
Geschichte der DEA- und AC- vs. DC-Sensoren
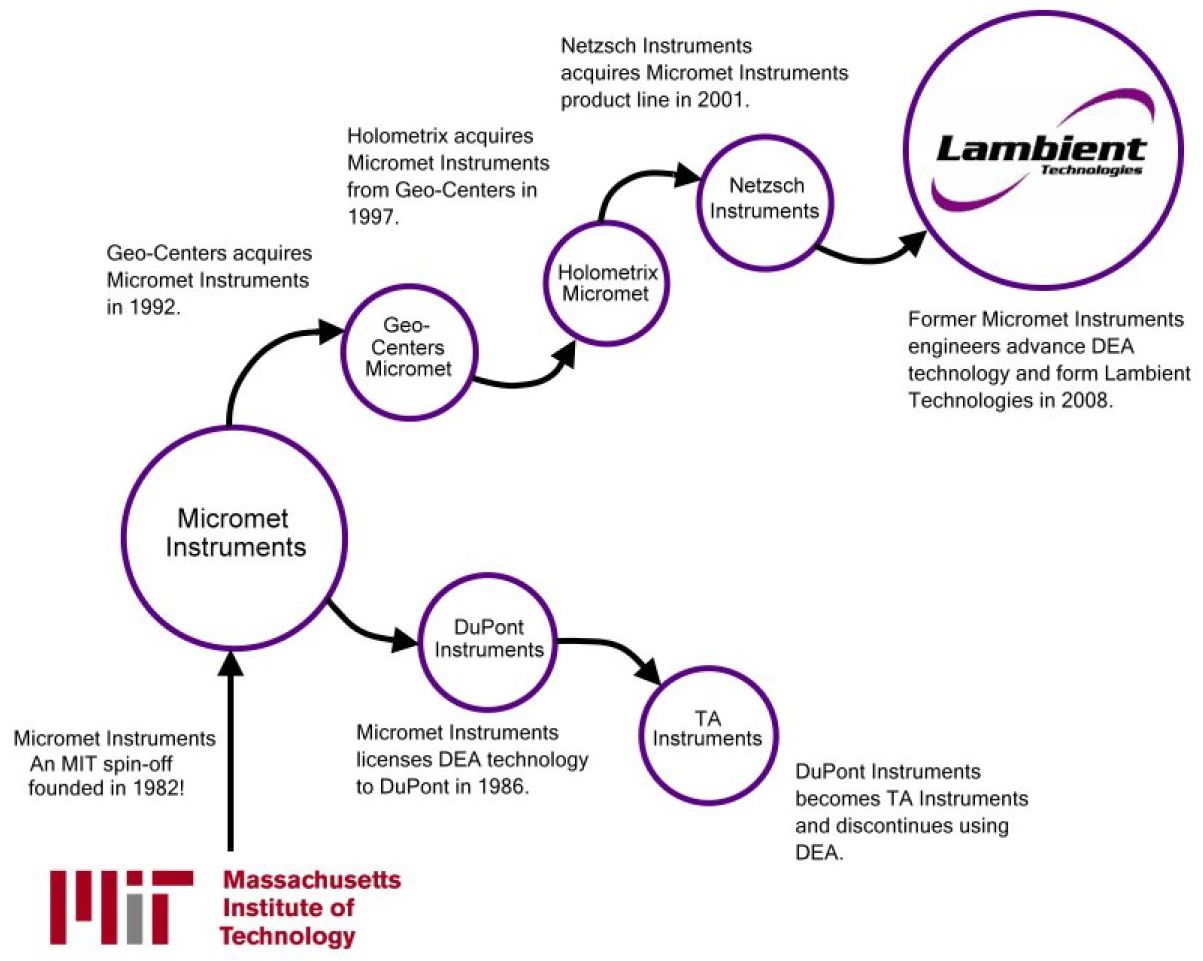
„Die Idee der Heilungsüberwachung ist ziemlich alt“, erklärt Dr. Nikos Pantelelis, Direktor von Synthesites. „In den 1980er Jahren galt die Methode der dielektrischen Sensorik als ausgereifter als andere, wie zum Beispiel optische Fasern. Das MIT (Massachusetts Institute of Technology) hat daran gearbeitet und versucht, es in der Produktion umzusetzen. Diese Technologie hat Netzsch gekauft und verwendet sie heute.“
Synthesites wurde 2008 gegründet. „Wir haben unsere Technologie von Grund auf mit elektrischen Sensoren mit Gleichstrom und nicht mit Wechselstrom entwickelt“, erzählt Pantelelis. „Für uns besteht der Nachteil bei der Verwendung herkömmlicher dielektrischer Wechselstromsensoren darin, dass das Harz in einem Bereich von Frequenzen angeregt und dann die Impedanzantwort für verschiedene Signale gemessen werden muss. Es ist nicht nur eine Herausforderung, all diese Daten zu verarbeiten, sondern wenn sich das Harz von flüssig zu fest ändert, müssen Sie sich auf verschiedene Signalfrequenzen konzentrieren, um die richtigen Informationen zu erhalten.“
Pantelelis sagt, dass die DC-Sensoren von Synthesites sehr niedrige Leitfähigkeit und einen hohen spezifischen Widerstand messen können, „der notwendig ist, um die Umwandlung von Harzen während der Aushärtung zu messen“. Er behauptet, dass die Verwendung herkömmlicher DEA bei nur einer Frequenz zur Vereinfachung keine genauen Daten liefert. „Wir haben nicht mehrere Frequenzen, sondern legen einfach eine konstante Spannung an. Der Nachteil ist, dass dieser Ansatz sehr eng ist, was bedeutet, dass er für sehr spezifische Anwendungen wie die Harzhärtung gut funktioniert, aber nicht für alles. Wenn wir jedoch die Leistung unserer Geräte mit konventioneller DEA vergleichen, können wir den gesamten Bereich der Aushärtung auch bei niedrigeren Temperaturen messen. Unternehmen, die Instrumente und Dienstleistungen außerhalb von Verbundwerkstoffen anbieten, mögen unseren Ansatz nicht, da er nur begrenzte Parameter zur Abstimmung hat.“
Für Synthesites ist dies kein Problem, da es speziell auf Verbundwerkstoffe ausgerichtet ist. „Unser Ansatz funktioniert bei einer Vielzahl von Verbundharzen und -prozessen, einschließlich Duroplasten, RTM, Prepreg und sogar reaktiven Thermoplasten wie Elium.“ (Elium ist der dünnflüssige Thermoplast von Arkema (Colombes, Frankreich), der mittels Harzinfusion verarbeitet werden kann.)
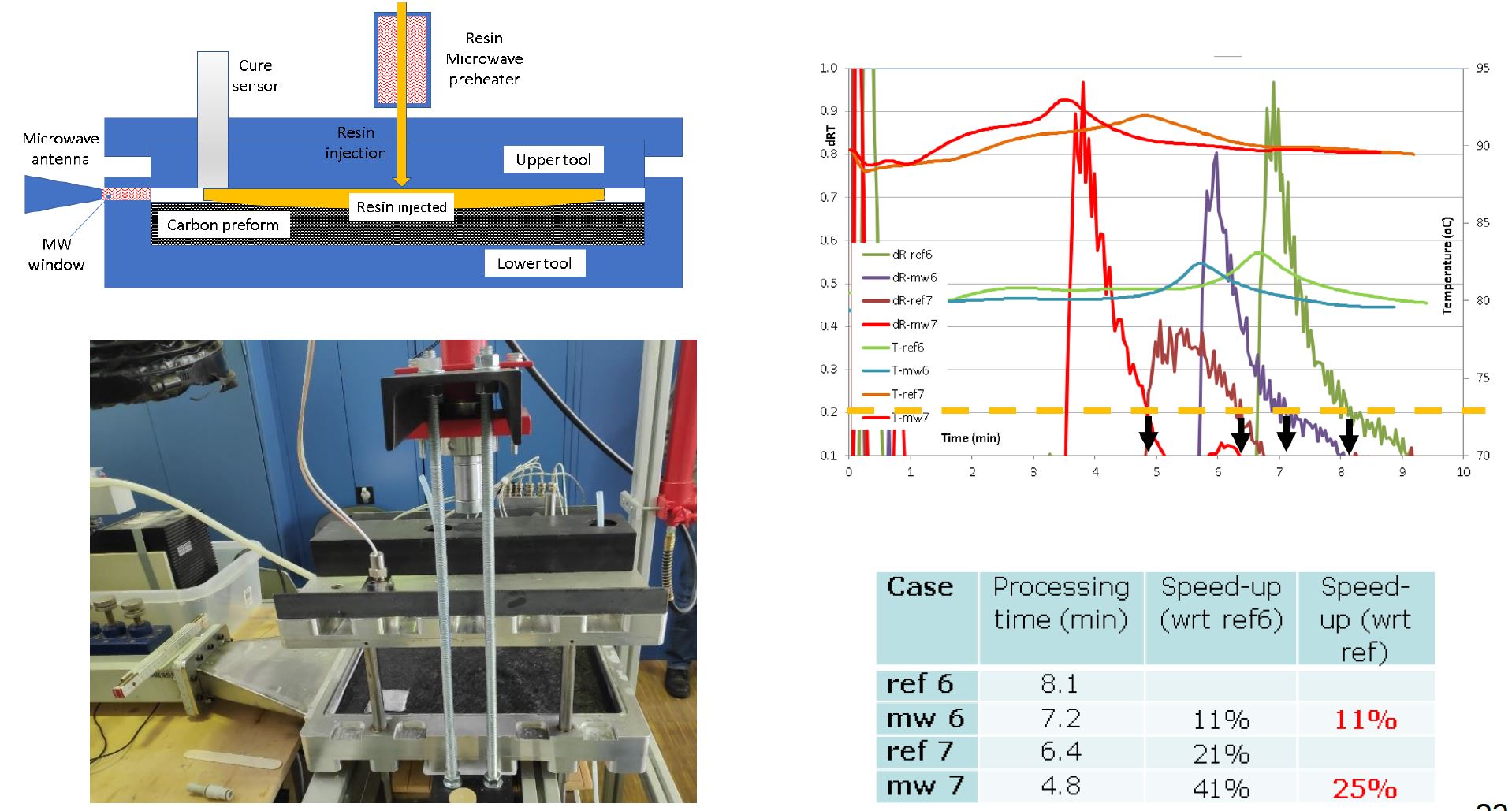
Wenn in den 1960er Jahren DEA mit Gleichstrom bekannt war, warum wurden dann AC-Sensoren in den 1980er Jahren bevorzugt und schritten voran? „Vor dreißig Jahren war die Technologie für DEA mit DC-Sensoren noch nicht so weit entwickelt“, betont Pantelelis. „Aber wir haben unseren Ansatz weiterentwickelt, um sehr reibungslose und genaue Messungen für die industrielle Produktion zu liefern. Wir haben unsere Systeme bei Kunden wie GE Aviation (Batesville und Ellisville, Miss., USA) und Bombardier, die große Teile mit Flüssigharzguss verarbeiten, demonstriert und weiterentwickelt. Unsere Systeme werden auch täglich in der Windblattproduktion eingesetzt und haben die Fähigkeit zur industriellen Herstellung von autoklavgehärteten Prepreg-Laminaten bewiesen.“
Prozesskontrolle
Pantelelis erklärt, wie die DC-Sensoren von Synthesites nur ein Teil eines integrierten Systems zur Überwachung der Verarbeitung und Aushärtung von Verbundwerkstoffen sind. „Wir messen direkt Widerstand und Temperatur und berechnen daraus online Viskosität, Gelier- und Aushärtungsgrad. Wir verwenden langlebige In-Mold-Sensoren, aber auch Anschnittsensoren und Inline-Sensoren für Harzein-, -aus- und -zuleitungen sowie Einwegsensoren an Teilen. Sie verwenden die Sensoren nur dort, wo Sie sie brauchen.“
Die Temperatursensoren sind Platin-Widerstandstemperaturdetektoren (RTDs), die eine viel höhere Genauigkeit (innerhalb von 0,1 °C) als Thermoelemente sowie eine jahrelange Stabilität gegenüber der bei Thermoelementen möglichen Messdrift bieten. RTDs gehören in vielen industriellen Anwendungen zur Standardausrüstung. Angusssensoren (siehe Prozesssteuerungsdiagramm unten) sind binär und melden den Harzfluss als ein oder aus, obwohl es eine zweite Version gibt, die auch die Viskosität melden kann. Synthesites hat Sensoren für die Verwendung mit Kohlefasern ohne das Risiko galvanischer Korrosion entwickelt, Sensoren, die durch einen Vakuumbeutel verwendet werden können und geformte In-Mold-Sensoren, die der Formgeometrie entsprechen.
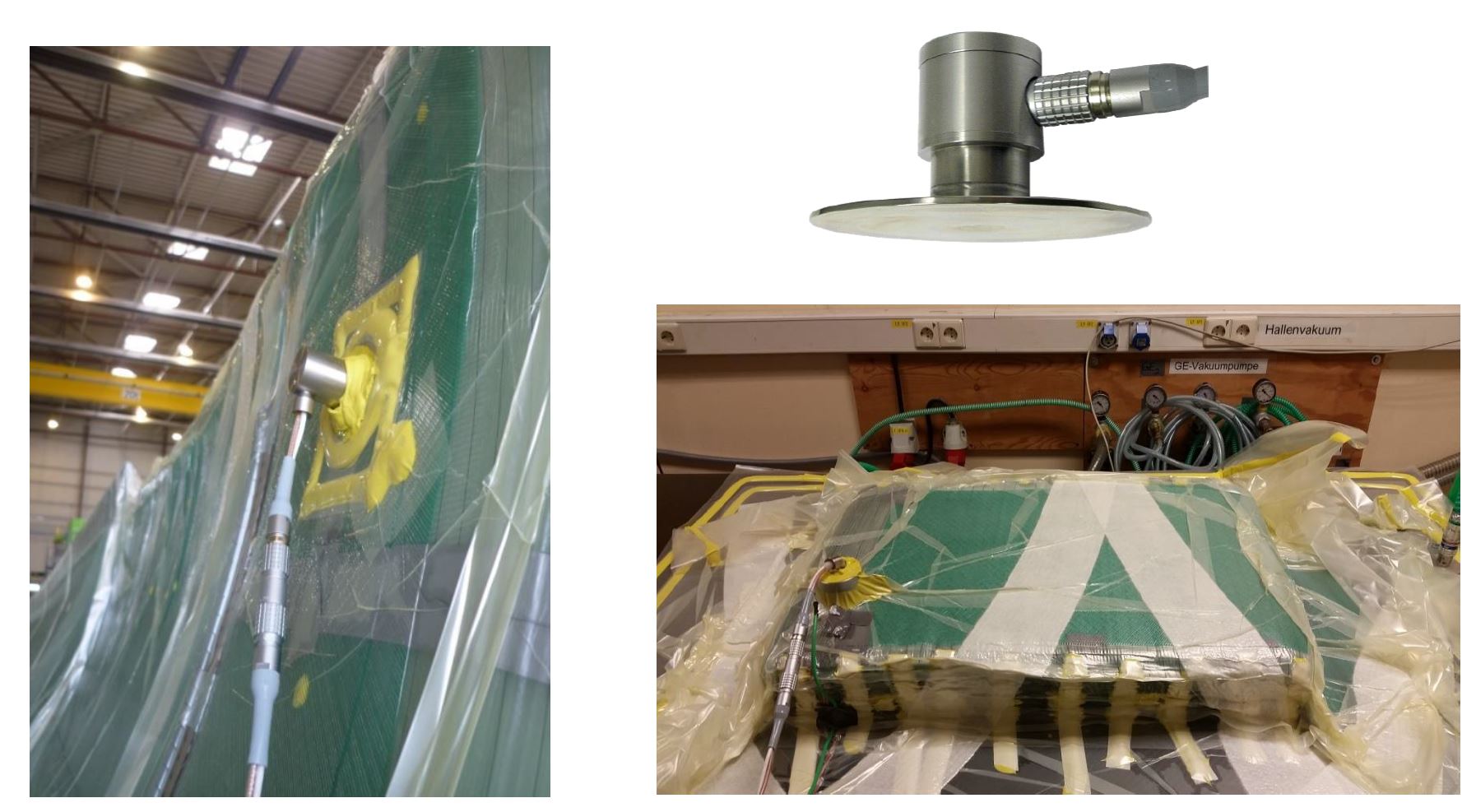
Die nächsten Komponenten sind OPTIFLOW und OPTIMOLD Datenerfassungseinheiten. OPTIFLOW bietet eine Echtzeit-Überwachung der Harzankunft und -temperatur vor Ort beim Spritzgießen von flüssigen Verbundwerkstoffen. Es überprüft und protokolliert den Harzfluss und kann Produktionsabweichungen während der Harzinfiltration erkennen. OPTIMOLD verwendet Temperatur- und Harzwiderstandsmessungen, um Berechnungen durchzuführen und den Zustand des Harzes zu überwachen, einschließlich Mischungsverhältnis, chemische Alterung, Viskosität, Tg und Aushärtungsgrad. Es kann mit Prepreg- und Flüssigformverfahren verwendet werden.
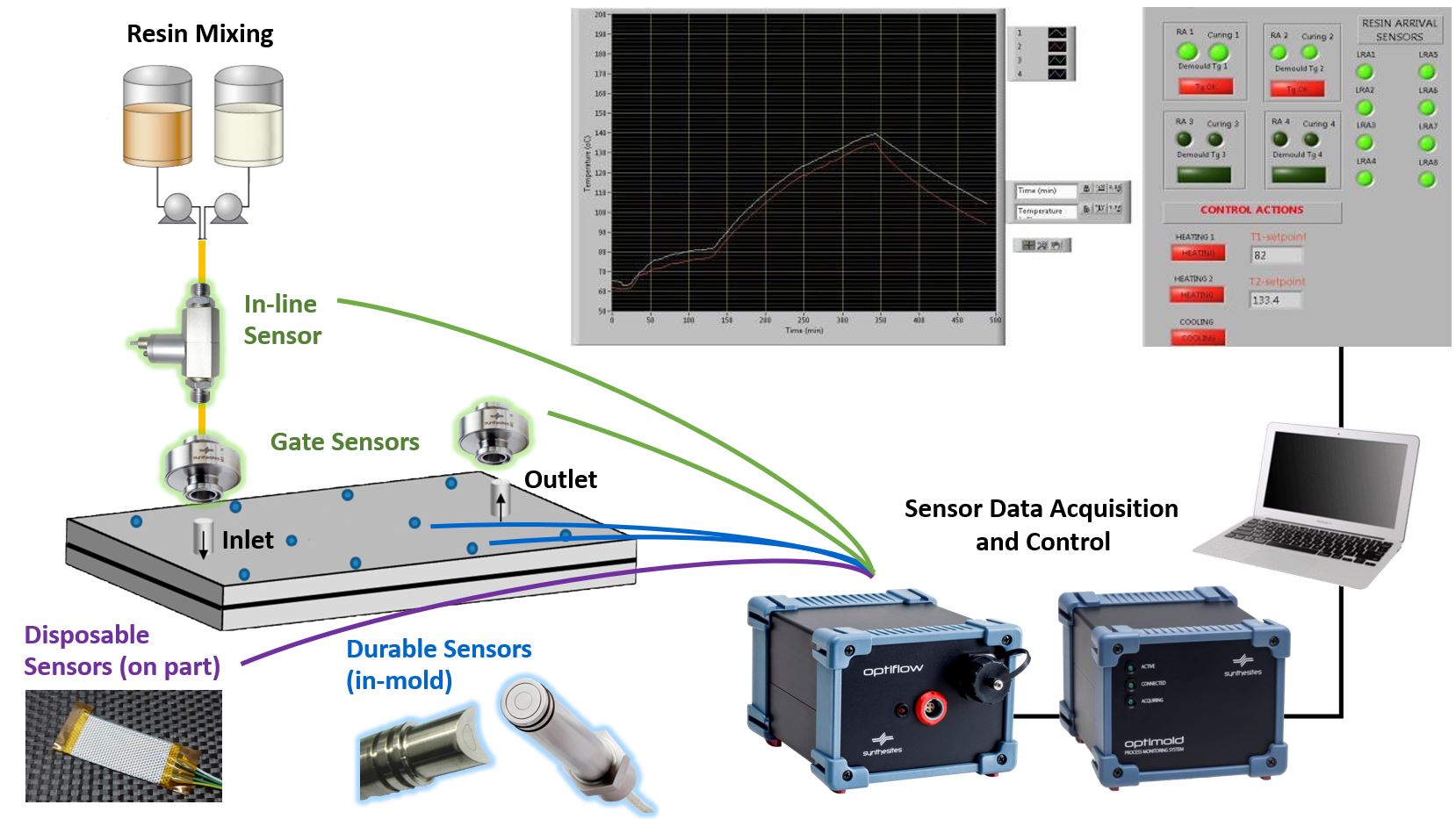
OPTIFLOW- und OPTIMOLD-Geräte werden von der OPTIVIEW-Software gesteuert. „Diese Software bietet Datenerfassung und -speicherung und wird kostenlos mit unseren Geräten zur Verfügung gestellt“, erklärt Pantelelis. „Wir bieten auch Online Resin State (ORS)-Software an, eine erweiterte Option, die Kunden zusätzlich erwerben können. Es sammelt Eingaben, führt Online-Berechnungen durch und sendet Ausgaben für eine intelligente Prozesssteuerung.“
Sowohl OPTIFLOW- als auch OPTIMOLD-Systeme überprüfen kontinuierlich, ob die Sensoren angeschlossen sind und die Messwerte innerhalb des Bereichs liegen. „Wenn Sie sich auf diese Sensoren zur Prozesskontrolle verlassen, ist es zwingend erforderlich, dass das System alarmiert, wenn ein Sensor nicht funktioniert oder seine Messwerte über den vorgeschriebenen Grenzen liegen“, sagt Pantelelis. Beide Systeme verfügen außerdem über Relaisausgänge zur Steuerung von Prozessanlagen. Zum Beispiel können Zufuhrleitungsventile basierend auf Harzankunftsdaten geöffnet oder geschlossen werden und Heiz-/Kühlgeräte können basierend auf der Harzviskosität verwaltet werden. „Sie können die Ausgabe von Drucksensoren in OPTIMOLD einspeisen“, bemerkt Pantelelis, „und so den Druck im Werkzeug basierend auf Viskositätsdaten steuern.“
Messungen und typische Datenkurven
Die folgenden Screenshots zeigen OPTIMOLD-Messungen aus Hochdruckkompressions-RTM (HP-CRTM)-Versuchen bei NCC (Bristol, Großbritannien). Der erste Satz aus einem einfachen Versuch bei 115 °C zeigt, wie Echtzeitmessungen des elektrischen Widerstands und der Temperatur des Harzes in die geschätzte Viskosität und Tg durch die ORS-Software umgewandelt werden.
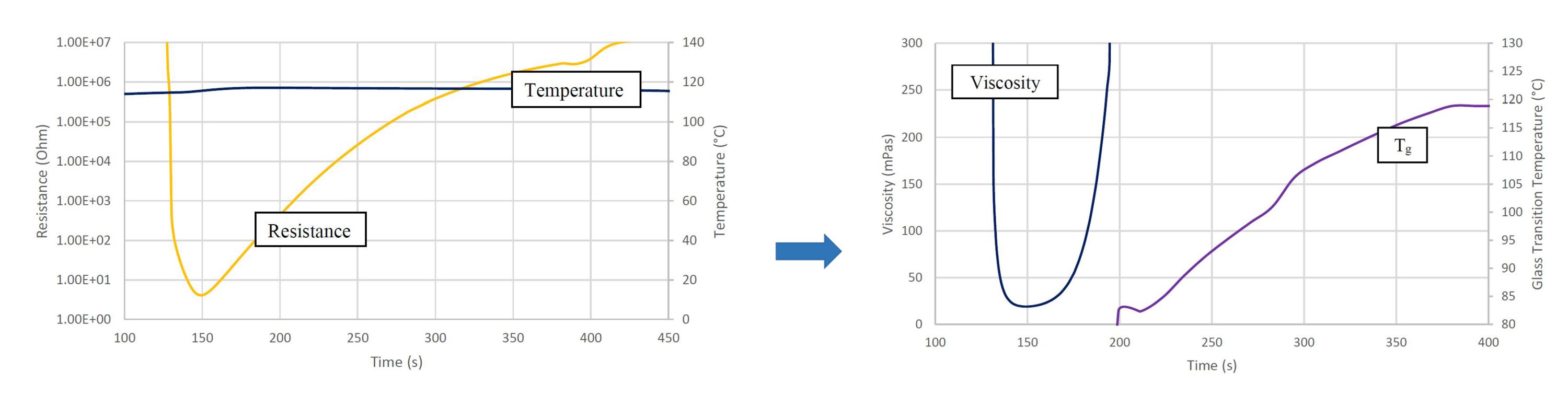
In den folgenden Grafiken sind der elektrische Widerstand und die Temperatur (obere Grafiken) wurden bei 110° aufgenommen (links) und 120°C (rechts). Unterhalb der Widerstands- (R)- und Temperatur- (T)-Messwerte sind die Diagramme mit der berechneten Viskosität und Tg bei 110 °C (links) und 120°C (rechts) . Diese Messungen stammen von zwei OPTIMOLD-Sensoren in der oberen Werkzeughälfte (Sn.1 und Sn.2, Foto unten ) während der Werkzeuginnendruck mit zwei Kistler 6162A Drucksensoren (Sn.3 und Sn.4) aufgezeichnet wurde.
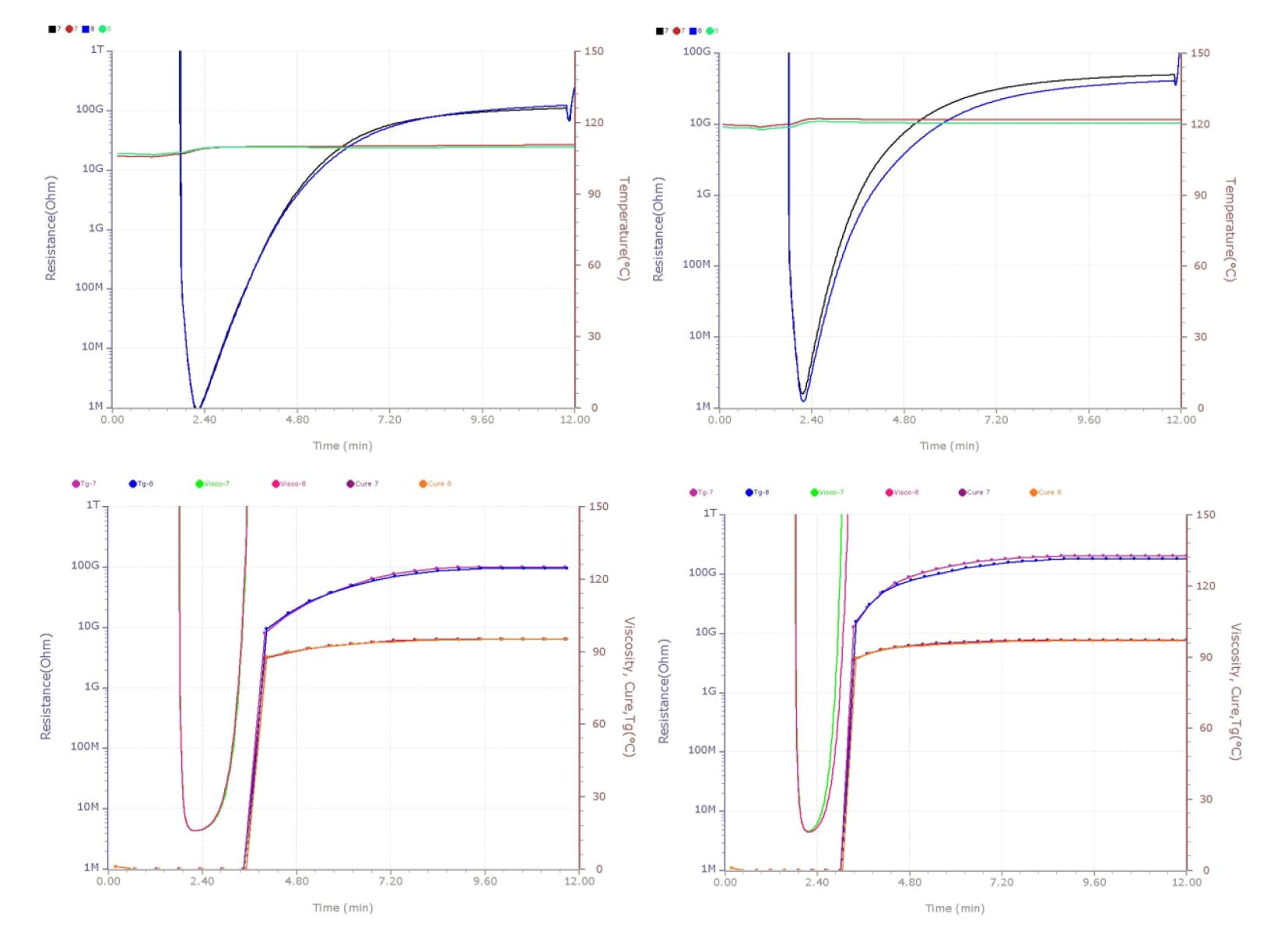
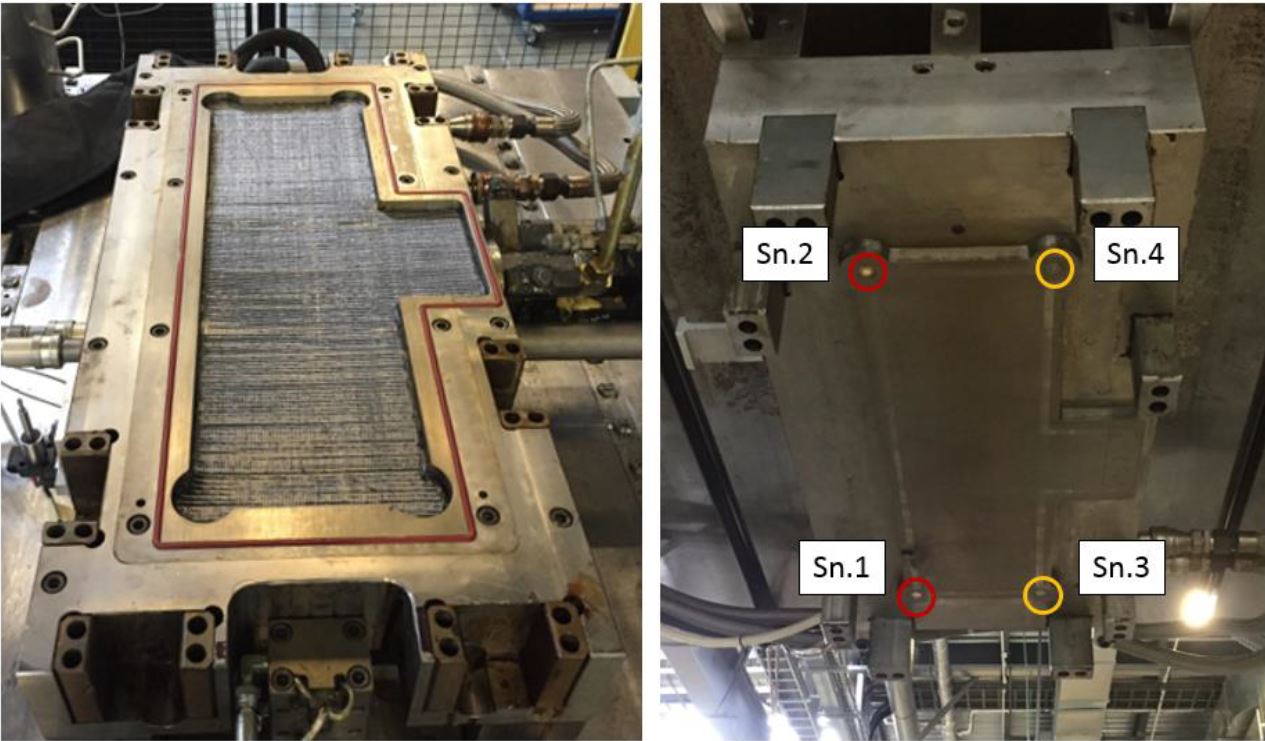
Alle Daten, die von den In-Mold-Sensoren sowie der Press- und Spritzgießausrüstung erfasst werden, können in einer einzigen Protokolldatei zusammengeführt werden, die ein detailliertes Bild des Herstellungsprozesses für jedes erstellte Bauteil ermöglicht.
Verkürzung der Aushärtungszeit
„Wir haben das Potenzial, die Aushärtungszeit um mehr als 30 % zu verkürzen, da der Hersteller die Tg in Echtzeit sehen kann, sodass er entscheiden kann, wann der Aushärtungszyklus beendet werden soll“, erklärt Pantelelis. „Sie müssen nicht warten, um einen längeren als nötigen Legacy-Zyklus abzuschließen. Zum Beispiel beträgt der Legacy-Zyklus für RTM6 2 Stunden bei 180 °C für eine vollständige Aushärtung. Wir haben gesehen, dass dies bei bestimmten Geometrien bis zu 70 Minuten dauern kann.“
Das Ziel ist es also, den Prozess zu stoppen, sobald die Aushärtung abgeschlossen ist? „Es geht nicht um die vollständige Aushärtung, sondern darum, den Aushärtungsgrad zu erreichen, den jede Komponente benötigt“, sagt Pantelelis. „Eine vollständige Heilung dauert zu lange. Der Schlüssel ist, zu sehen, wann eine ausreichende Heilung erreicht ist. Windblatthersteller haben eine Ziel-Tg. Wenn sie das erreichen, können sie mit der Kühlung beginnen. Daher ist ein Sensor erforderlich, der in Echtzeit sehr genaue Tg-Messungen liefern kann.“
Synthesites hat mit Hutchinson (Paris, Frankreich) ein Demonstrationsprojekt zur Herstellung eines aus Glasfaser/Epoxid und RTM hergestellten Fahrzeugaufhängungsblatts für das EU-finanzierte Projekt ECOMISE (Enabling Next Generation COmposite Manufacturing by In-Situ Structural Evaluation and Process Adjustment, 2013) abgeschlossen -2016). Das Ziel dieses Projekts war es, den RTM-Zyklus basierend auf Echtzeit-Prozessüberwachung zu optimieren:
- Die erste Heizrampe würde durch den Abschluss der Harzinfiltration basierend auf Sensoren ausgelöst.
- Die zweite Heizrampe würde nach Abschluss der Aushärtung basierend auf der Tg-Berechnung ausgelöst.
- Die Kühlung würde durch den Abschluss der Nachhärtung basierend auf der Tg-Berechnung ausgelöst.
Das Synthesites-System umfasste zwei (2) in-mold Sensoren zum Aushärten (CS1, CS2), ein (1) in-mold Sensor für Harzfluss und Temperatur (Flow Sensor 1) und acht (8) Einweg Sensoren für Harzfluss/-temperatur – vier (4) in das Testteil eingebettet und vier (4) an der Werkzeugoberfläche befestigt.
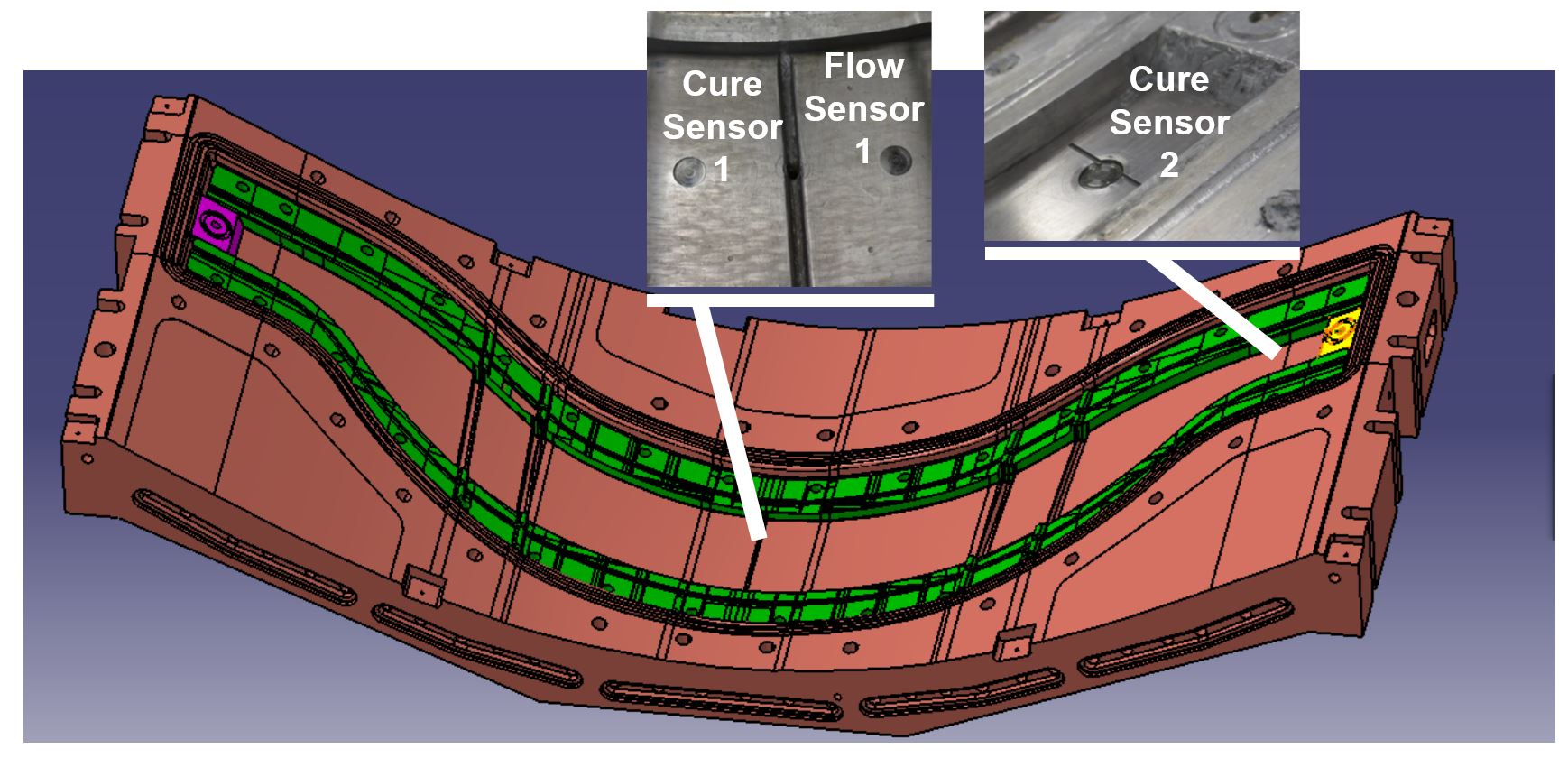
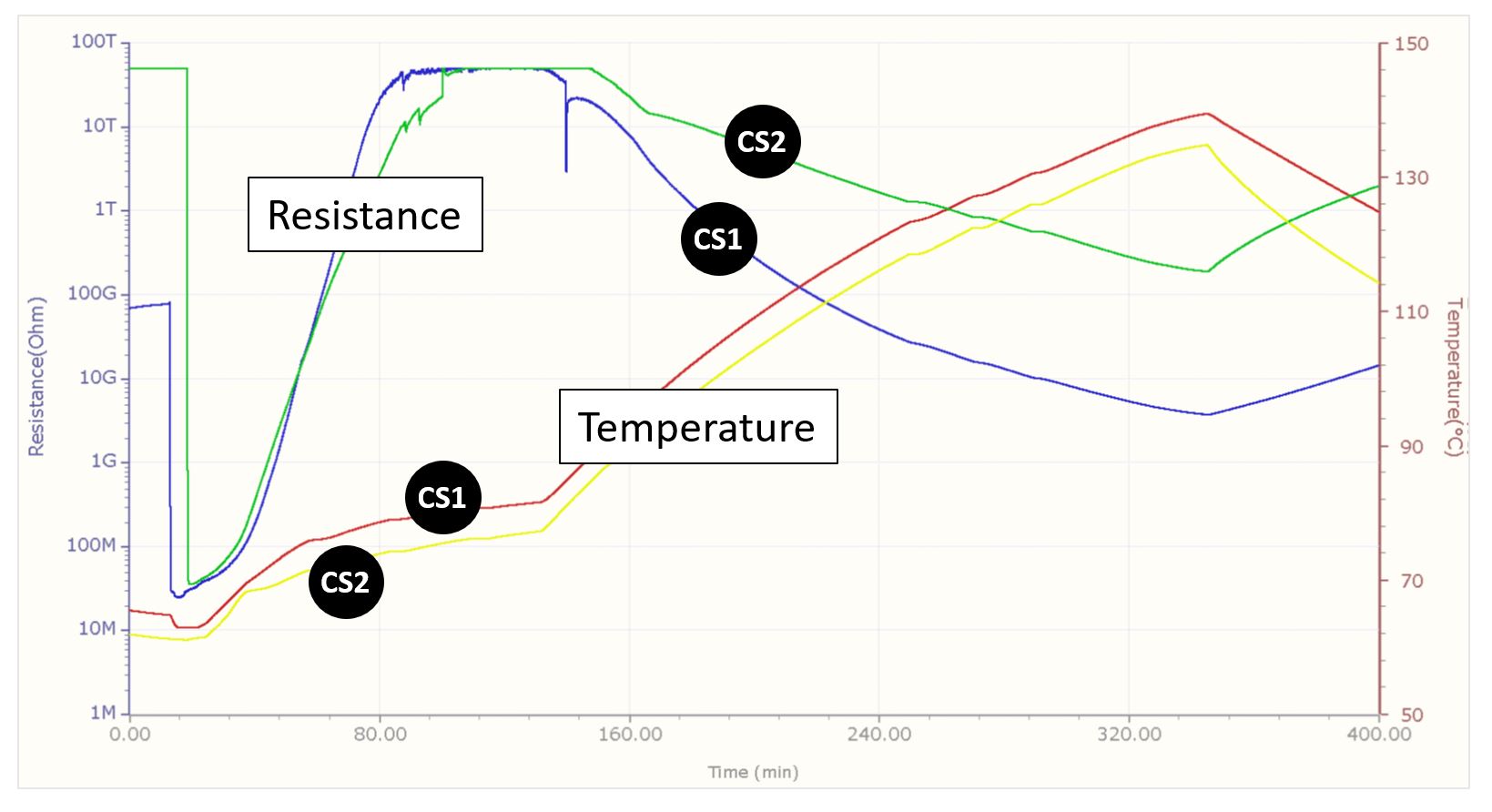
„OPTIMOLD- und OPTIFLOW-Geräte können über Ethernet miteinander verbunden werden, sodass alle Sensoren in einer Optiview-Sitzung aufgezeichnet werden können“, erklärt Pantelelis. „So wurden CS1 und CS2 an zwei OPTIMOLD-Einheiten, der In-Mold-Flowsensor 1 und die acht Einweg-Flowsensoren an drei OPTIFLOW-Einheiten angeschlossen.“
Dieses System aus Sensoren, OPTIMOLD/OPTIFLOW-Datenerfassungseinheiten und OPPTIVIEW/ORS-Software wurde dann während RTM-Formgebungsversuchen angewendet, um Targets für verschiedene Prozessstufen festzulegen, einschließlich Harzinjektion/Infiltration und zwei Tg-Targets. „Dies war ein dickes Teil, das aus unidirektionalen Fasern und Huntsman-Epoxidharz hergestellt wurde“, sagt Pantelelis. „In diesem Fall haben wir Flussdrahtsensoren verwendet, um den Fluss innerhalb dieser UD-Lagen zu überprüfen, die normalerweise dicht gepackt sind und bei der Harzinfiltration zu Herausforderungen führen können.“
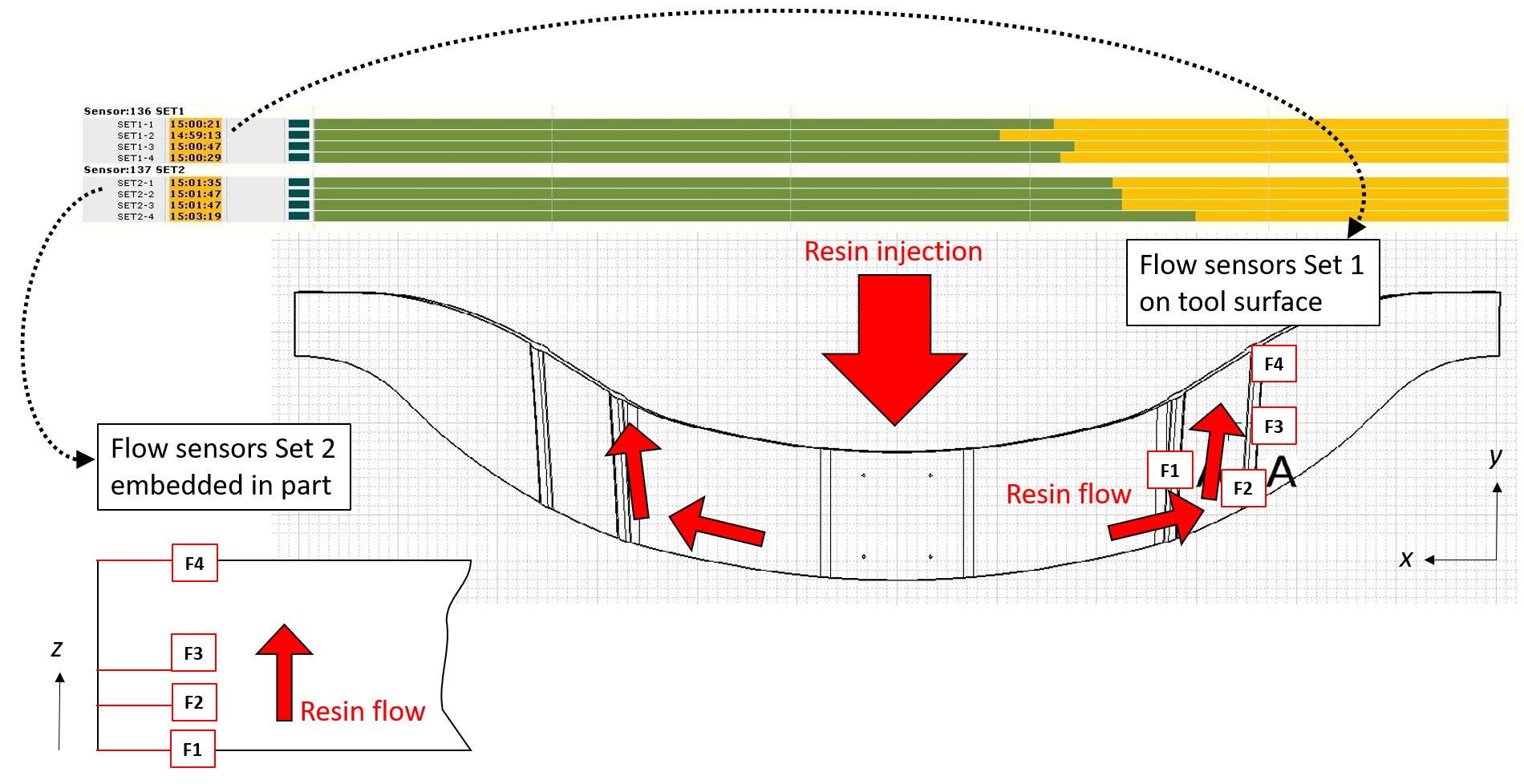
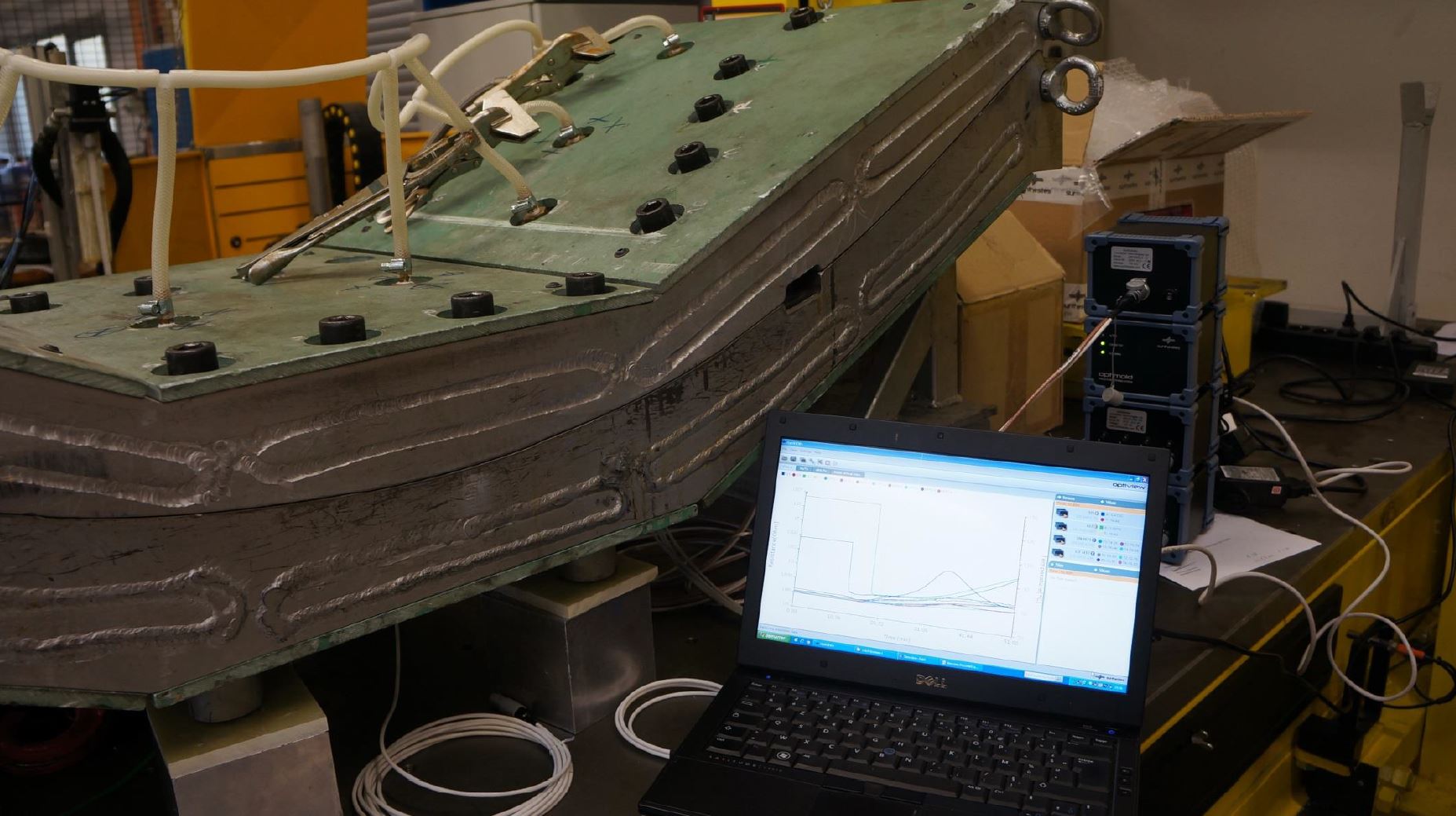
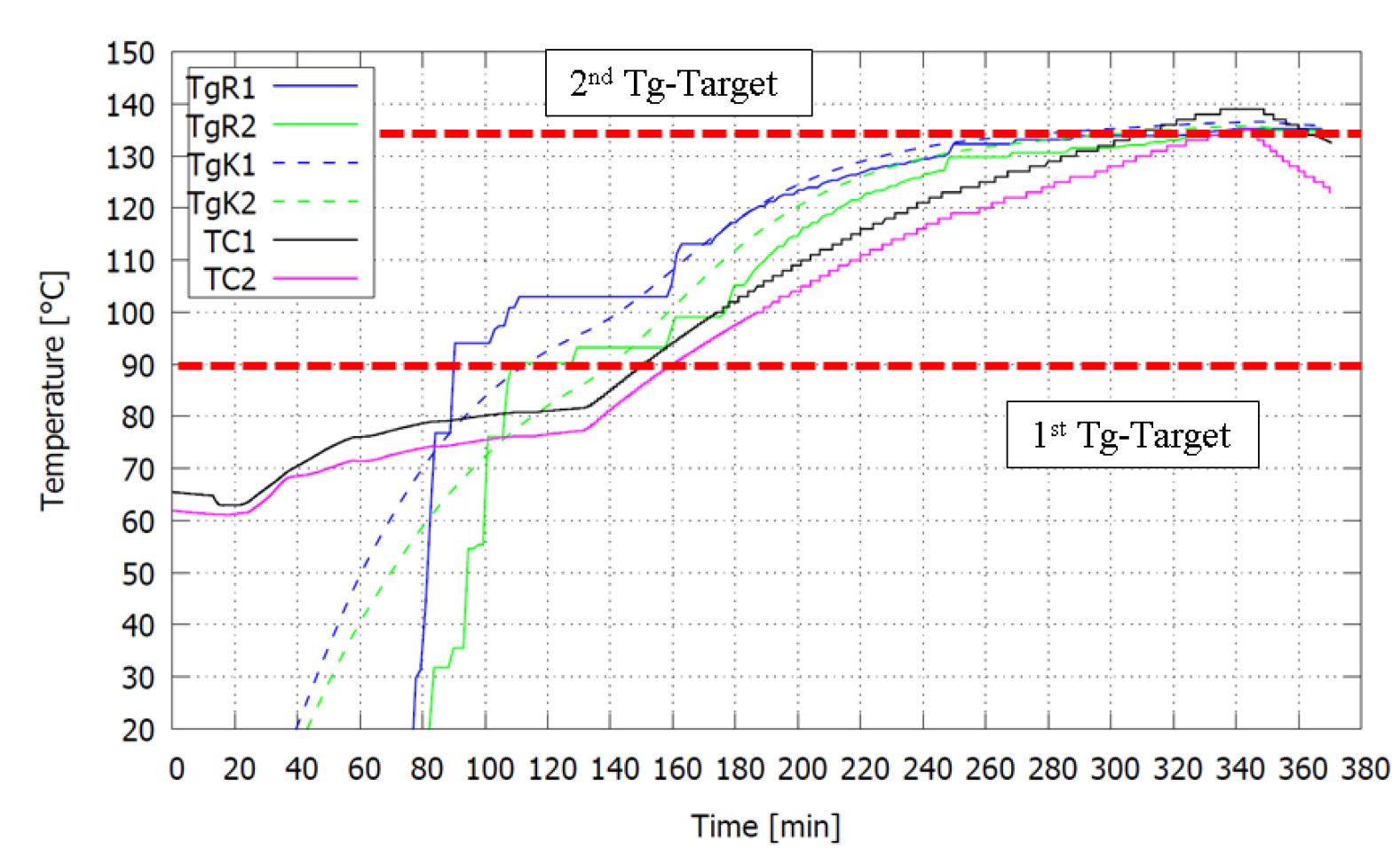
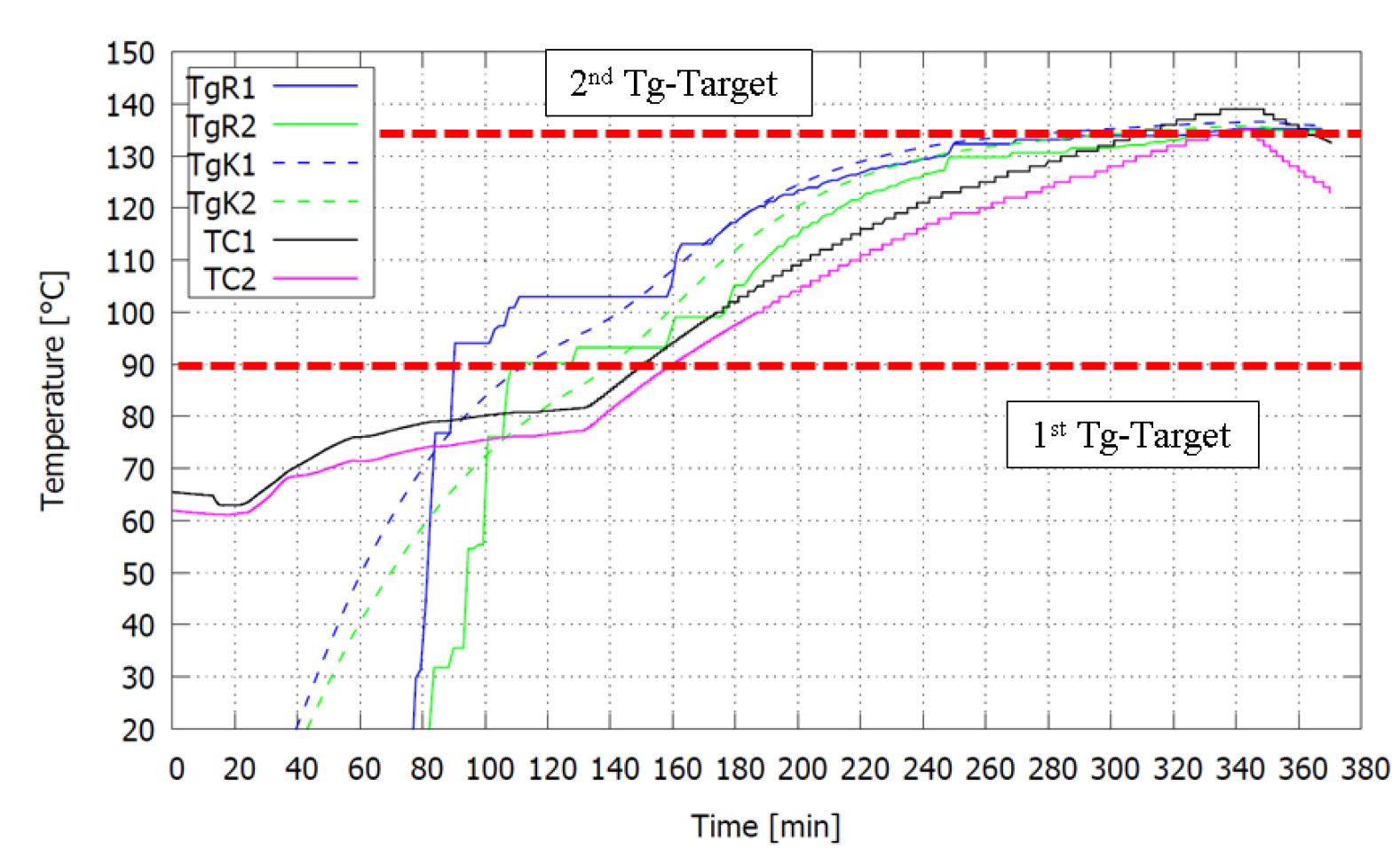
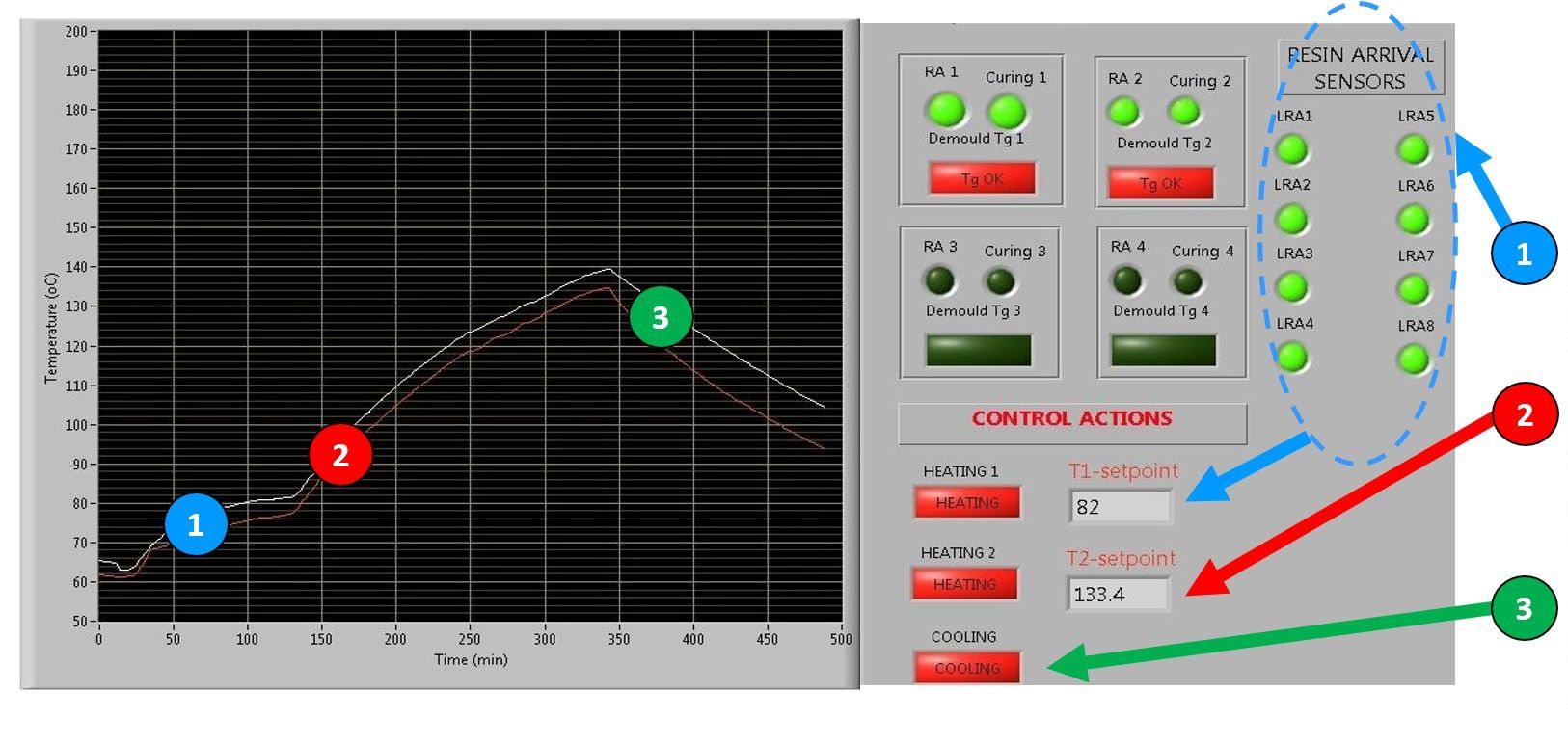
Mit diesem Prozessleitsystem konnte das ECOMISE-Projekt bei Hutchinson den Aushärtungszyklus um mehr als 30 % reduzieren.
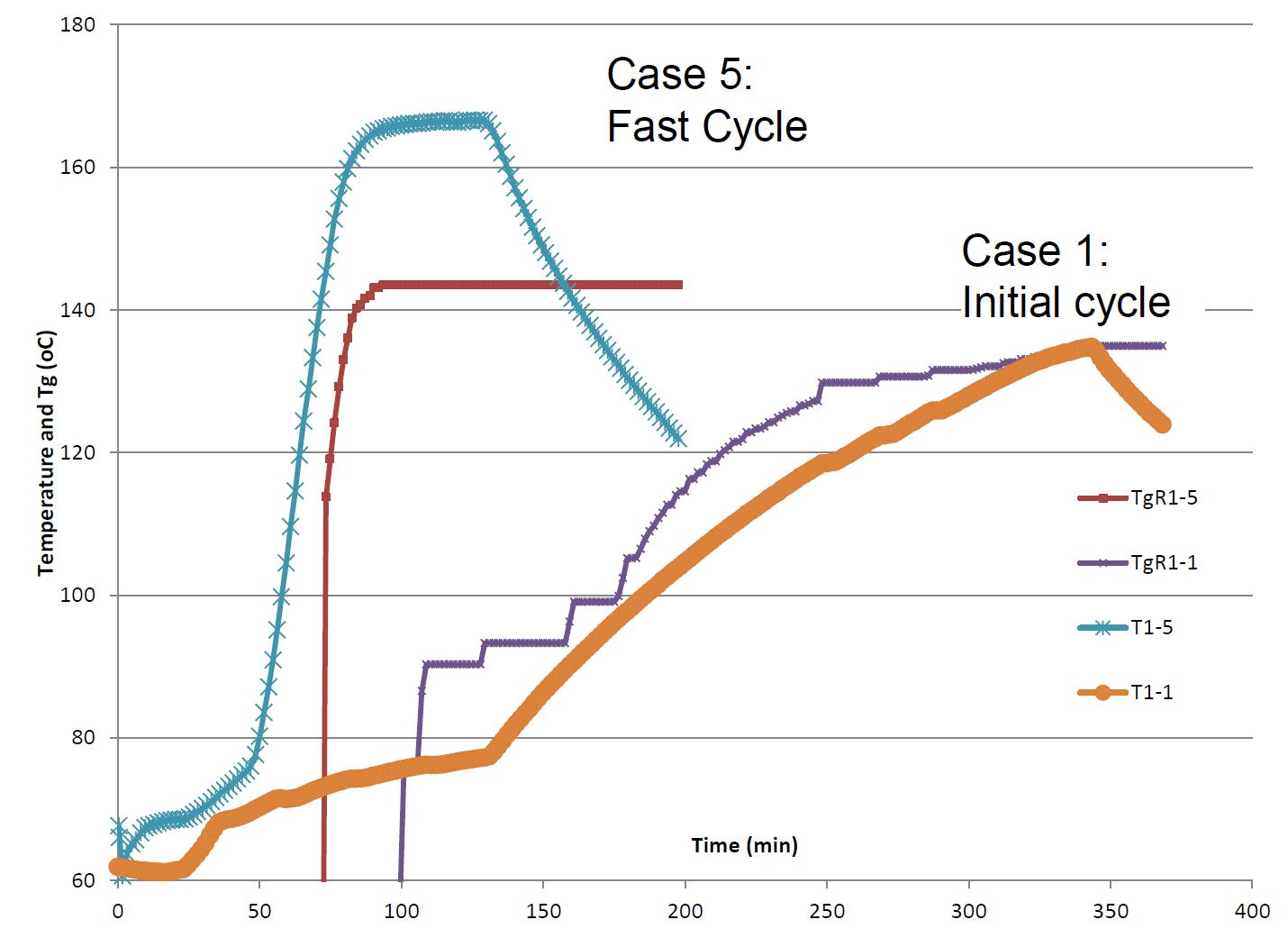
Kalibrierung
Für die Online-Tg-Überwachung ist eine Kalibrierung erforderlich. Da die Messwerte von den Sensoren über OPTIMOLD-Einheiten erfasst werden, übersetzt die ORS-Software diese basierend auf der Kalibrierung für dieses spezifische Harz in Viskosität und Tg. „Diese Kalibrierung ist Arbeit, die vor der Verarbeitung durchgeführt wird, um die Korrelationen bereitzustellen, die die ORS-Software für ihre Berechnungen verwendet“, erklärt Pantelelis. „Wir kalibrieren, indem wir das Harz in ein Rheometer geben und Temperatur und Viskosität messen. Durch Anwendung der entsprechenden Formeln berechnen Sie dann den entsprechenden Widerstand und Tg. Wir entwickeln für unsere Kunden Kalibrierungen von Harzen basierend auf ihren Standards und untersuchen die verschiedenen Härtungszyklen des Harzes. Diese Kalibrierungsdaten werden dann von der ORS-Software verwendet, wenn dieses Harz verarbeitet wird.“

Die Genauigkeit der Echtzeit-Tg-Berechnungen der ORS-Software wurde in Versuchen des Windblattherstellers Carbon Rotec Composite Technology (Lemwerder, Deutschland) gezeigt. Die online von der ORS-Software berechnete Tg wurde mit der Tg verglichen, die direkt nach dem Entformen durch Ausführen eines Differentialscanningkalorimeters (DSC) gemessen wurde. Bei der isothermen Verarbeitung betrug die mittlere Differenz 1,61 °C und bei der nicht-isothermen Verarbeitung 2,15 °C.
„Diese Genauigkeit hat sich bei privaten Projekten mit anderen Kunden immer wieder gezeigt“, sagt Pantelelis.
Fortschritte für die industrielle Produktion
Diese sensor- und datengesteuerte Prozesssteuerung ist in der Tat ein großer Schritt in Richtung einer vollautomatisierten und intelligenten Composites 4.0-Fertigung. Obwohl es in ECOMISE und auch beim NCC in Bristol demonstriert wurde, wird es noch nicht im Produktionsalltag eingesetzt. „Die Idee, die Sensoren zu verwenden, um Tg zu sehen und dann mit der Kühlung zu beginnen, wurde zwar in der Windblattfertigung begonnen“, berichtet Pantelelis, „aber es ist noch nicht vollständig automatisiert. Das System gibt einen Alarm aus, wenn die Ziel-Tg erreicht ist, und dann stoppt der Bediener den Härtungszyklus. Die Automatisierung ist unkompliziert und wird abgeschlossen, sobald der Hersteller die Genauigkeit des Systems während der Pilotphase validiert hat.“
„Um dieses Ziel zu erreichen, haben wir einen neuen Arbeitsplatz entwickelt, der es dem Produktionsmitarbeiter ermöglicht, den automatisierten Prozess zu überwachen, der keine Eingaben von seiner Seite erfordert“, fährt er fort. „Wir haben bei der Herstellung von Windturbinenblättern gesehen, dass die Verwendung einer einzigen Arbeitsstation während der Harz- und Klebstoffhärtung die Zykluszeit um mindestens 2-3 Stunden ohne Qualitätseinbußen verkürzen kann.“
Obwohl Bombardier Belfast, jetzt Spirit AeroSystems, Synthesites-Geräte bei der Herstellung seines harzverstärkten Verbundtragflügels für die C-Serie, jetzt Airbus A220, verwendet, ist die Prozesssteuerung nicht automatisiert. Synthesites hat jedoch auch bei ECOMISE mit Bombardier zusammengearbeitet, und diese Entwicklung wird fortgeführt. Eine wichtige Errungenschaft waren Sensoren, die durch die Autoklavenwand führen. Wie in meinem 2013-Blog „C-Series Composite Wing“ erklärt:
Bombardier injiziert, nachdem das Layup in seinem 21,3 m langen und 5,6 m Durchmesser großen Autoklaven platziert wurde, wodurch Temperatur und Druck auf dem für eine reduzierte Viskosität und Benetzung erforderlichen Niveau gehalten werden können — Cytec 890 is injizierbar bei 80°C. . . Nachdem die Harzinjektion abgeschlossen ist, wird während der Verfestigung im Autoklaven Überdruck angelegt, wodurch sich die Werkzeugelemente schließen, das nasse Laminat verdichten und überschüssiges Harz wieder aus dem Harzeinlass in einen speziell entwickelten Harzbehälter ausstoßen.
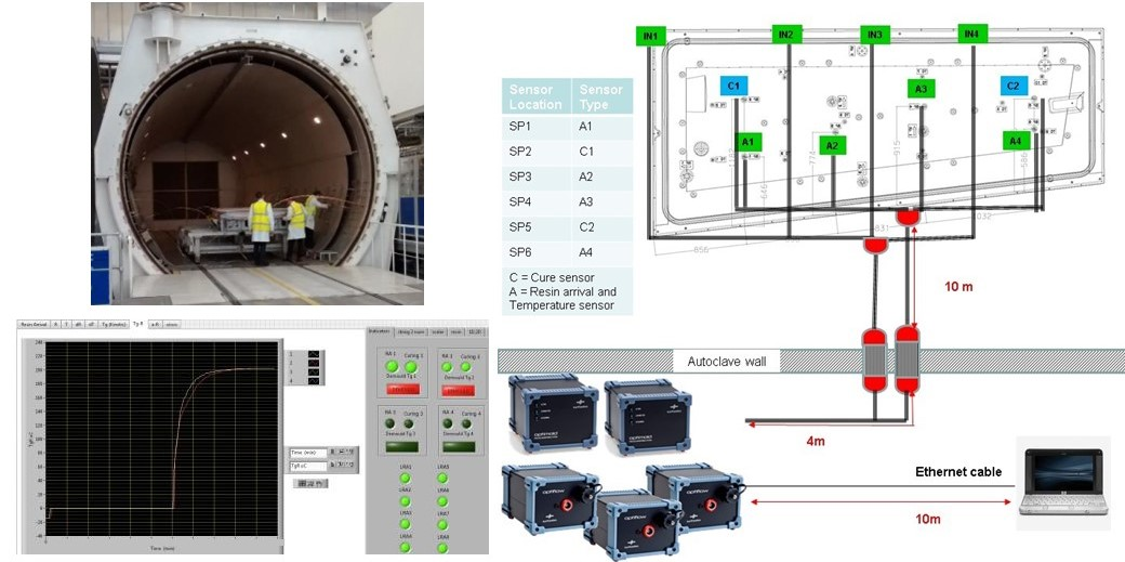
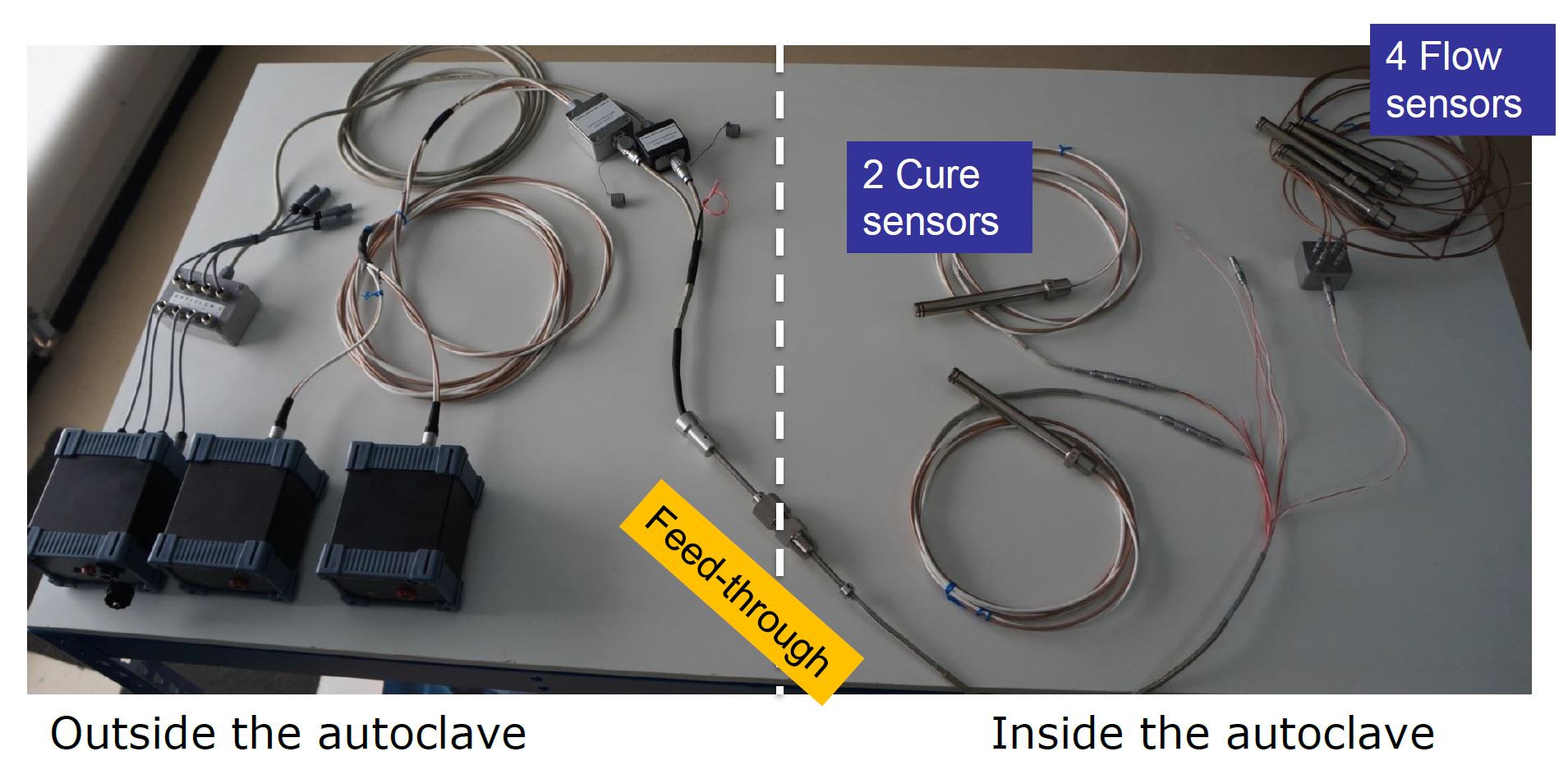
„Wie die meisten Hersteller in der kommerziellen Luft- und Raumfahrt ist es daran interessiert, die Qualität zu sichern und die Geschwindigkeit zu steigern“, erklärt Pantelelis. Das folgende Layout und die Ergebnisse von ECOMISE waren für einen Demonstrator, kein kommerzieller Teil. Es wurden zwei OPTIMOLD-Einheiten mit zwei In-Mold-Cure-Sensoren und drei OPTIFLOW-Einheiten mit vier In-Mold-Flow-Sensoren und vier Inline-Sensoren an den Vakuumleitungen verwendet. „OPTIFLOW kann bis zu vier Harzankünfte und vier Temperatur-/Widerstandssensoren überwachen“, bemerkt Pantelelis. „Die Ziele der Demonstration wurden vollständig erreicht. Wir haben bewiesen, dass die Sensoren, Verkabelung und Systeme problemlos unter den anspruchsvollsten Luft- und Raumfahrtspezifikationen funktionieren. Interessant war, dass die Harzankunftsmessungen große Unterschiede zu den Strömungssimulationen aufwiesen. Außerdem zeigte die Online-Tg-Überwachung, dass der Aushärtungszyklus für diesen speziellen Demonstrator deutlich kürzer hätte sein können.“
„Wir entwickeln jetzt ein Überwachungssystem für die Bondlines“, sagt Pantelelis, „in erster Linie für die Rotorblattproduktion, aber letztendlich für jeden Klebeprozess. Obwohl wir derzeit stark mit der Windturbinenindustrie beschäftigt sind, die versucht, Kosten zu senken, sehen wir immer mehr Interesse aus dem Luft- und Raumfahrtsektor, der sich dem Flüssigverbundpressen für die Massenproduktion nähert. Hersteller möchten mehr Einblicke in die Abläufe während des Spritzgießens gewinnen und wie sie ihre Prozesse stabilisieren und optimieren können.“
Ecomise- und Recotrans-Projekte wurden aus den Forschungs- und Innovationsprogrammen FP7 und Horizon 2020 der Europäischen Union im Rahmen der Grant Agreements Nr. NMP2-SL-2013-608667 bzw. 768737 gefördert.
Referenzen zum Abschnitt „Dielektrische Analyse (DEA), AC vs. DC“ beinhalten:
- „Echtzeit-UV-Härtungsüberwachung“ von VINCENTZ, veröffentlicht im European Coatings Journal, Ausgabe 11/2003, S. 7.
- „Online Process Monitoring Systems – Benchmark and Test Study“ von Reinhold Meier 1 , Swen Zaremba 1 , Florian Springl 1 , Klaus Drechsler 1 , Fabrice Gaille 2 und Christian Weimer 2 — 1 Institut für Carbon Composites, TU München, Garching, Deutschland. 2 Eurocopter Deutschland GmbH, Donauwörth. Flow Process in Composite Materials – FPCM 11, 9.-12. Juli 2012, Auckland, Neuseeland.
- Zerstörungsfreie Charakterisierung von Materialien VIII herausgegeben von Robert E. Green, Proceedings of the 8 th Intl. Symposium on Nondestructive Characterization of Materials, 16.-20. Juni 1997, Boulder, Colorado, USA, herausgegeben von Springer Science &Business Media, S. 384-385.
Eine weitere hilfreiche Referenz ist „The Handbook of Dielectric Analysis and Cure Monitoring“ von Huan L. Lee, herausgegeben von Lambient Technologies.
Harz
- Sensoren und Prozessoren konvergieren für industrielle Anwendungen
- BASF und Toray in Liefervertrag zur Herstellung von CFRT-Bändern für Automobil- und Industrieanwendungen
- Ultraleichte TPE-Verbundwerkstoffe für Schuhe
- Solvay-Verbundwerkstoffe für Rennkatamarane ausgewählt
- Hexion führt Zweikomponenten-Epoxidlösung für die Herstellung von Verbundwerkstoffen in der Luft- und Raumfahrt ein
- LANXESS erweitert Produktionskapazität für endlosfaserverstärkte thermoplastische Verbundwerkstoffe
- Konsortium für thermoplastische Verbundwerkstoffe strebt die Massenproduktion für die Automobil- und Luftfahrtindustrie an
- Ultradünne, batterielose Dehnungssensoren für industrielle Roboterarme
- Intelligente Sensoren:Vor- und Nachteile für Industriemaschinen
- Welche Innovationen gibt es für die industrielle Instandhaltung?