Highlights:Composites Convention 2019
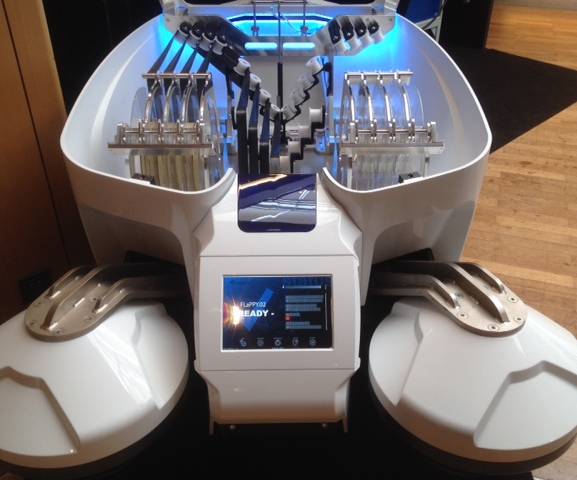
Der faszinierend benannte Flappybot-Prototyp (Flexible Autonomous Production, Placement and Assembly Robot) des DLR ist eine radikale Abkehr von den großen und teuren statischen Maschinen, die bei der Herstellung großer Luft- und Raumfahrtkomponenten üblich sind. Diese kompakte autonome AFP-Einheit ist so konzipiert, dass sie direkt über das Werkzeug „fährt“. Quelle | DLR
Wenn die Composites-Industrie weiter wachsen und ihre Wettbewerbsfähigkeit verbessern soll, muss sie die Chancen der Digitalisierung und Automatisierung nutzen. Zwei kürzlich in Deutschland stattfindende Konferenzen zum Thema Luft- und Raumfahrt befassten sich mit der Zukunft der Verbundwerkstoffherstellung.
Zu Besuch in der Fabrik der Zukunft in Stade
Future Factory for Composites war das Thema der diesjährigen Composites Convention in Stade, Deutschland, die vom 12. bis 13. Juni stattfand. Gemeinsam organisiert von CFK Valley e.V. (Stade, Deutschland) und Carbon Composites e.V. (Augsburg, Deutschland) verzeichnete die Veranstaltung einen Besucherrekord von fast 450 Personen. Eine starke Präsenz in den USA resultiert aus einer Zusammenarbeit mit der Utah Advanced Materials and Manufacturing Initiative (UAMMI, Kaysville, Utah, USA) als Partnernetzwerk und den USA als Partnerland.
In der Eröffnungs-Keynote mit dem Titel „Digitalisierung:Übergang von Computer Aided Manufacturing zu Human Aided Automation“ erläuterte Dr. Jan Stüve, Leiter des Zentrums für Leichtbau-Produktionstechnik des Deutschen Zentrums für Luft- und Raumfahrt (DLR; Stade, Deutschland) bot einen Vorgeschmack auf das kommende Programm. Zukünftige Fabriktechnologien, die im DLR entwickelt werden, umfassen mehrere kooperierende Roboter, die zusammenarbeiten, um die Produktionszeit zu verkürzen, und digitale Zwillinge von Maschinen, die eine Prozessoptimierung ermöglichen. Ein weiterer Schwerpunkt sind mobile autonome Roboter für flexible Produktionsszenarien. Dazu gehören der Prototyp FlappyBot, eine kompakte Faserbestückungseinheit, die über die Form fährt. Stüve warnte vor den Gefahren einer Überautomatisierung und diskutierte, wie die Digitalisierung soll Menschen wieder in den Herstellungsprozess einbeziehen.
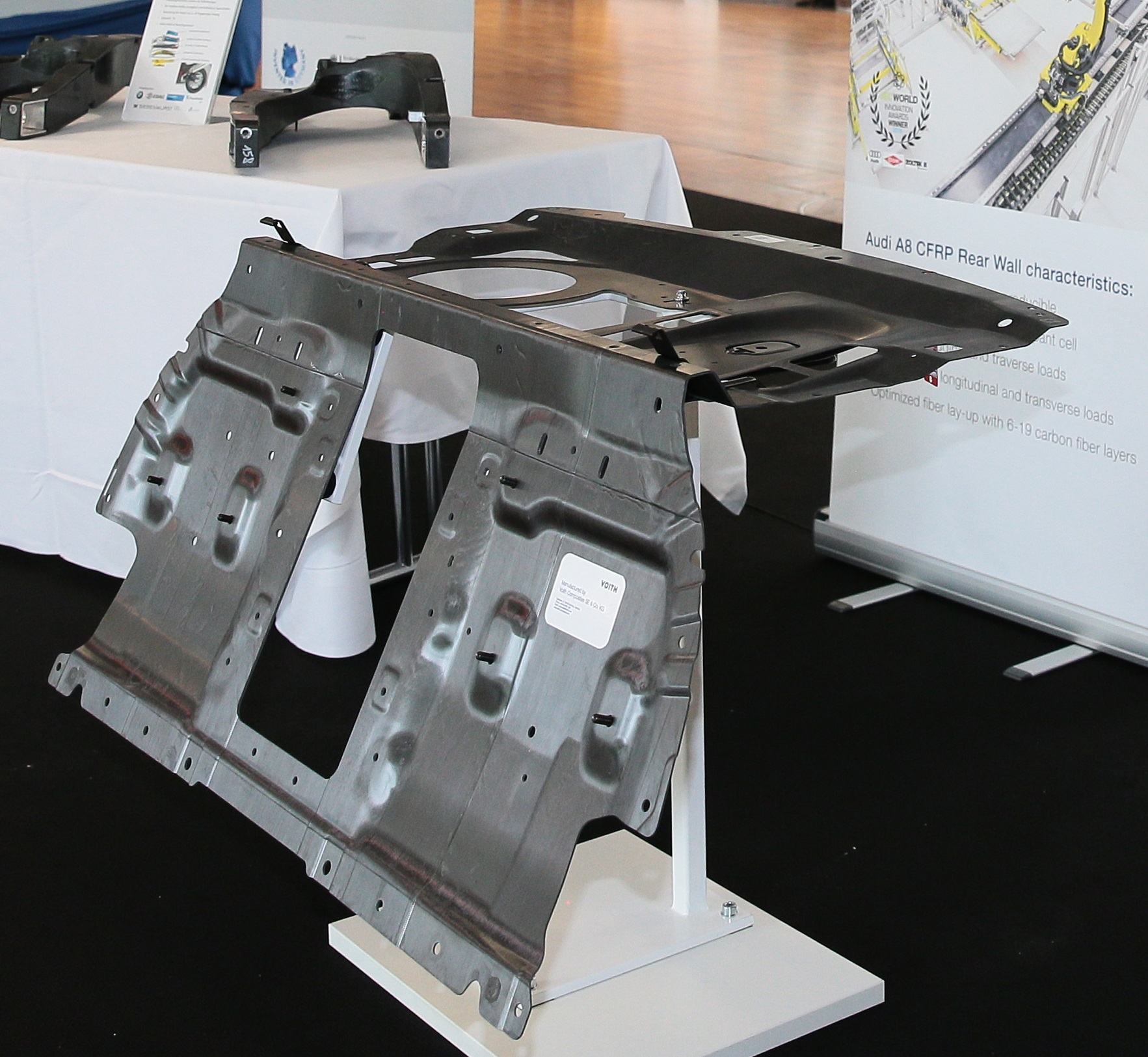
Die Audi A8 CFK-Rückwand, das größte Bauteil der Fahrgastzelle, wird von Voith Composites in einem hochautomatisierten Prozess gefertigt, der Produktionsvolumen von 65.000 Bauteilen pro Jahr ermöglicht. Quelle | CFK-Tal
In einer zweiten Keynote „Rapid Manufacturing and Thermoplastic Composites – Trends and Technologies“ entführte Dr. Robert G. Bryant, leitender Werkstoffingenieur am NASA Langley Research Center (Hampton, Virginia, USA) die Delegierten aus den Grenzen der terrestrische Fabrik in Richtung Gebäude im Weltraum. Eine langfristige menschliche Präsenz im Weltraum erfordert als ersten Schritt Schutzräume und Plattformen. Die Entwicklung immer größerer Raketen, um immer komplexere Strukturen außerhalb des Planeten zu platzieren, ist wirtschaftlich nicht nachhaltig. Lösungen erfordern eine Fertigung in der Nähe oder vor Ort. Der Einsatz eines werkzeuglosen Advanced Tape Placement (ATP)-Prozesses, der eine in-situ-Konsolidierung von thermoplastischen Verbundteilen ermöglicht, könnte die Antwort sein. Bei dieser neuen Technik arbeiten sich zwei ATP-Roboter gegenüber, einer zum Ablegen des thermoplastischen Prepreg-Bandes, der andere als Werkzeug. Die werkzeuglose Fertigung könnte die Kosten der Luft- und Raumfahrtfertigung senken, die Wirtschaftlichkeit der Weltraumforschung verbessern und auch anderen Marktsektoren zugute kommen (weitere Informationen finden Sie in „General Atomics Aeronautical Entwicklung werkzeugloser thermoplastischer Verbundwerkstoffe“).
Nachhaltigkeit
Fortschritte in der Herstellung müssen auch mit einer Verringerung der Umweltbelastung einhergehen. In diesem Sinne argumentierte Jörg Spitzner, Gründer der Spitzner Engineers GmbH (Finkenwerder, Deutschland), in der nächsten Sitzung, dass zum Erreichen der Klimaziele negative Emissionstechnologien benötigt werden. Das Unternehmen von Spitzner behauptet, dass sein patentiertes Blancair-Windturbinenkonzept sowohl den Turbinenwirkungsgrad verbessert als auch CO2 . entfernt aus der Atmosphäre. Luft wird in ein an der Gondel montiertes Filtermodul gesaugt, wo CO2 wird für die Lagerung und das Recycling bei der Herstellung von synthetischen Kraftstoffen und anderen Anwendungen getrennt. Die gereinigte Luft wird durch Öffnungen in den Rotorblattspitzen abgegeben. Ein Video zur Erläuterung des Konzepts ist auf der Website von Blancair verfügbar.
Die Organisatoren der Sitzung präsentierten außerdem ein Konzept für eine intelligente Ökoeffizienzbewertung in der Verbundstoffproduktion (DLR) und vorgespannte Prepregs bei Raumtemperatur außerhalb des Autoklaven mit Feuer-, Rauch- und Toxizitätsfähigkeit (FST) (TCR Composites; Ogden, Utah, USA).
Empowerment durch Simulation
Für den Rest des ersten Konferenztages wandte sich die Aufmerksamkeit der Simulation zu.
Dr. Lars Herbeck, Chief Technology Officer bei Voith Composites (Garching, Deutschland), erläuterte, wie die automatisierte Faserplatzierung (AFP) Voith Roving Applicator die Prozesskette vereinfacht und einen effizienten automatisierten Preforming-Prozess mit reduzierten Zykluszeiten ermöglicht. Er skizzierte die Struktur- und Prozesssimulation der automatisierten Fertigungslinie, mit der jährlich 65.000 Bauteile für die Rückwand aus kohlenstofffaserverstärktem Kunststoff (CFK) des Audi A8 gefertigt werden können.
Mark Bludszuweit von der MET Motoren- und Energietechnik GmbH (Rostock, Deutschland) erläuterte, wie die Simulation Einblicke in die beste Art und Weise bietet, Teile in einen Autoklaven zu laden, wodurch der Härtungsprozess optimiert und die Produktivität gesteigert werden kann. Ein digitaler Zwilling, der für den größten Autoklaven am DLR-Standort Stade entwickelt wurde, kann parallel zum realen Prozess oder schneller laufen, um Vorhersagen über das Teileverhalten zu treffen.
Weitere Themen der virtuellen Prozessentwicklung betrafen die Modellierung von SMC-Prozessen (ESI Group; Chartres-de-Bretagne, Frankreich) und die Prozesssimulation von Sandwichpaneelen, um Kernquetschungs- und Prepreg-Faltenprobleme im Autoklaven zu verstehen (Airbus Helicopters; Marignane, Frankreich).
In Bezug auf die virtuelle Sicherheitsmodellierung diskutierte Jochen Rühl von der Reichenbacher Hamuel GmbH (Dörfles-Esbach, Deutschland), ein Teil der Scherdel Gruppe, wie ein simulationsbasierter Ansatz zum Management von Staub und Partikeln, die bei der Bearbeitung von CFK-Teilen entstehen, Vorteile für Kunden wie z wie Airbus und Premium Aerotec (Augsburg, Deutschland). Bearbeitungssimulationen und Visualisierung von Partikelverteilungen helfen Herstellern, die strenger werdenden Gesundheits- und Sicherheitsvorschriften einzuhalten und verbessern die Bearbeitungsergebnisse sowie die Reduzierung von Maschinenstillstands- und Wartungszeiten, was sich letztendlich in niedrigeren Kosten pro Teil niederschlägt.
Die Simulationssitzung präsentierte auch ein von Boeing gesponsertes Projekt zur virtuellen Kostenmodellierung der Verbundwerkstoffherstellung unter Berücksichtigung der komplexen Interaktionen zwischen Konstruktion, Produktion und Finanzen, um Kostentreiber zu identifizieren (Massachusetts Institute of Technology; Cambridge, Massachusetts, USA) und a digitales Fabrikplanungskonzept basierend auf simulativer Modellierung optimaler Composites-Wertschöpfungsketten (Fraunhofer IGCV; Augsburg, Deutschland).
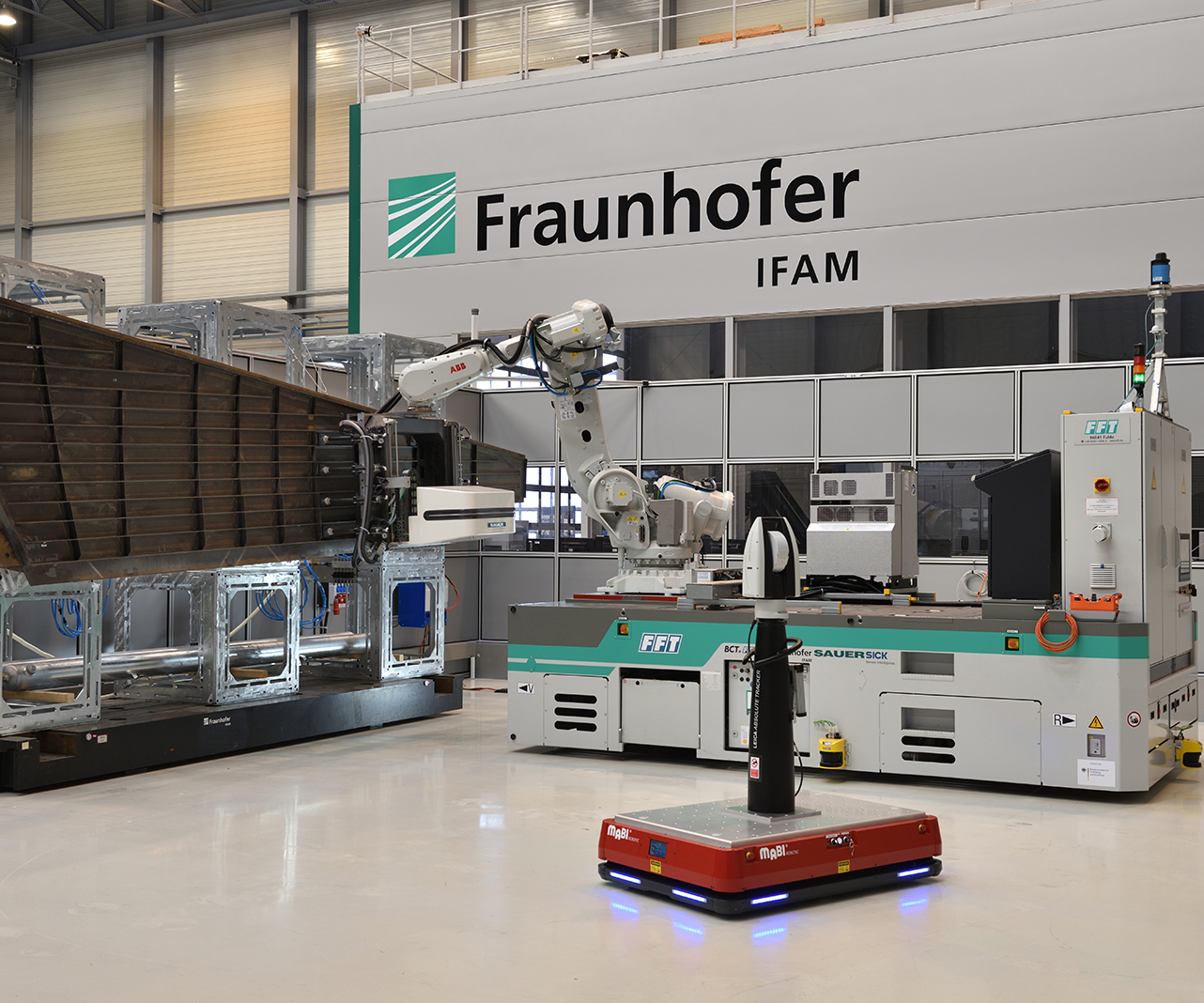
Das mobile Bearbeitungskonzept MBFast18 besteht aus einem fahrerlosen Transportfahrzeug, einem Roboter und einer tragbaren CNC-Maschine und bietet eine gesteigerte Produktivität bei der Herstellung großer CFK-Flugzeugteile. Quelle | Fraunhofer IFAM
Preisträger
In diesem Jahr teilten sich zwei Projekte den CFK Valley Innovation Award und das 7.500 Euro Preisgeld.
Der erste Platz (und 4.500 €) ging an das Projekt MBFast18 Mobile Robotic Systems, das ein fahrerloses Transportsystem (FTS)-basiertes mobiles CNC-Bearbeitungssystem für große CFK-Flugzeugteile entwickelte.
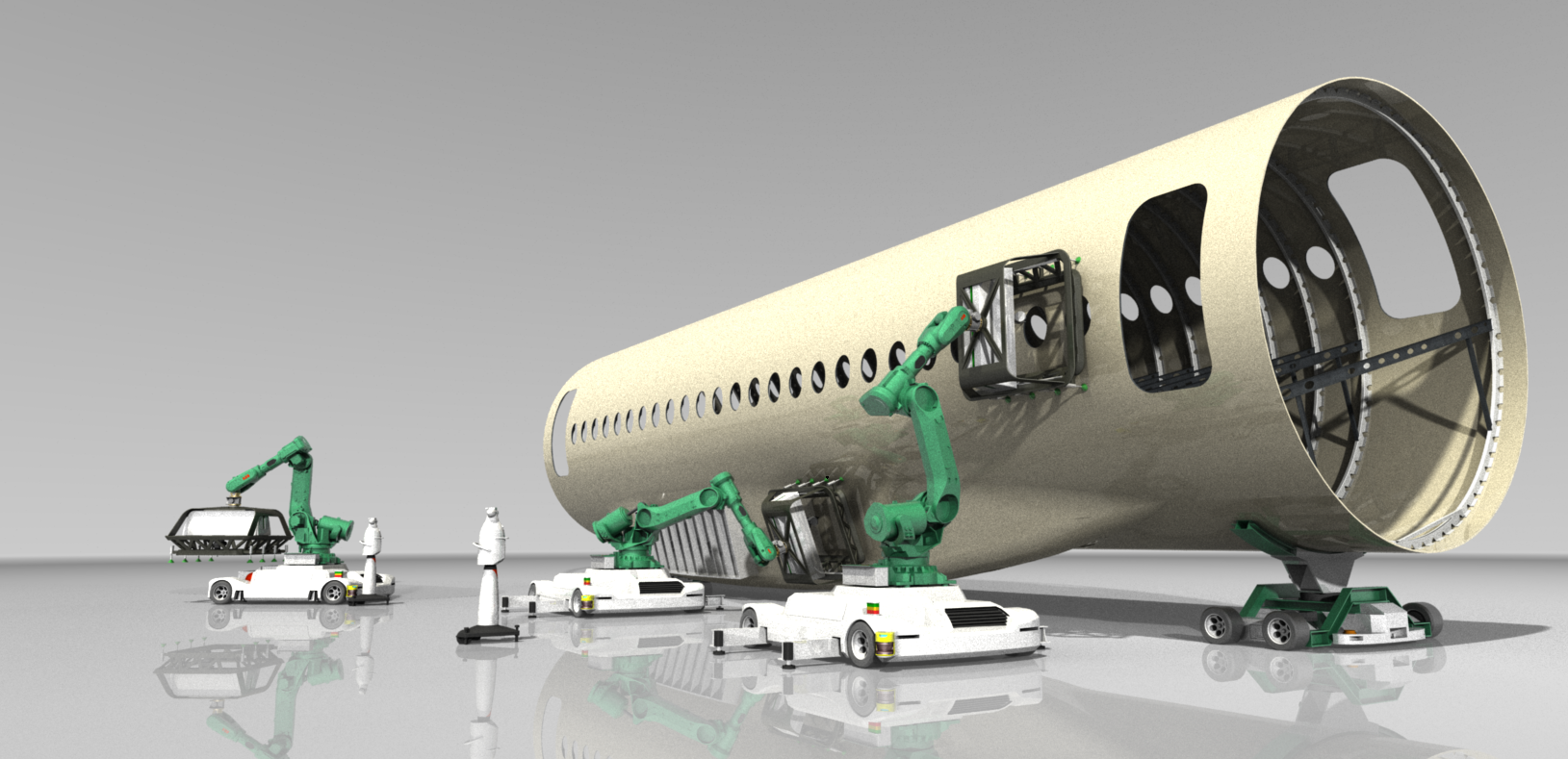
Quelle | Fraunhofer IFAM
Im Vergleich zu den heutigen teuren, statischen Bearbeitungssystemen für große Flugzeugstrukturen ermöglichen kleinere mobile Robotersysteme eine flexible Fertigung und eine höhere Produktivität.
Das MBFast18-System verwendet eine 4,6 Meter lange autonome Plattform der FFT Produktionssysteme GmbH &Co. KG (Fulda, Deutschland), Navigations- und Sicherheitssensoren der SICK AG (Waldkirch, Deutschland) und eine 5-Achs-CNC-Maschine von SAUER /DMG MORI (Suhl und Bielefeld, Deutschland). Ein mobiler Lasertracker, der vom Fraunhofer-Institut für Fertigungstechnik und Angewandte Materialforschung (IFAM; Stade, Deutschland) entwickelt wurde, positioniert den Roboter präzise. Die Bohreinheit mit einer Arbeitsfläche von bis zu 0,5 Quadratmetern wird mit Vakuumgreifern am Bauteil gespannt; Bohrpositionen werden mit einer Software der BCT GmbH (Dortmund, Deutschland) berechnet und an die Maschine übertragen. Dieses Konzept ist auch auf Handhabungs- und Montagebetriebe und andere Industrien wie Windenergie und Bahn anwendbar.
Sehen Sie sich ein Video über das MBFast18-Projekt an:
Der zweite Platz ging an das Start-up Hyconnect GmbH (Hamburg, Deutschland) für seine FAUSST Metall-Verbund-Fügetechnologie. Das Unternehmen zielt zunächst auf den Schiffbausektor ab, wo das Verbinden von Verbundwerkstoffen mit Metall ein Haupthindernis für eine breitere Einführung von Verbundwerkstoffen darstellt. Bei der FAUSST-Lösung kommt ein Hybridgewebe aus gewirkten Glas- und Metallfasern zum Einsatz, das eine feste mechanische Verbindung von Metallen und Verbundwerkstoffen ermöglicht. Die Metallfaserseite wird mit einem Stahlprofil verbunden, das mit Metallkonstruktionen verschweißt werden kann, und die andere Seite wird mit dem Verbundbauteil laminiert. Die patentierte Technologie soll den Design- und Klebeprozess deutlich beschleunigen. Erste Prototypanwendungen werden derzeit getestet.
Sehen Sie sich eine Einführung in den FAUSST-Fügeprozess an:
Aktivierung durch Automatisierung
Am zweiten Tag wurde das preisgekrönte Projekt MBFast18 in Vorträgen von Christoph Brillinger, Projektleiter am Fraunhofer IFAM, und Dr. Gregor Graßl von FFT näher beleuchtet und diskutierten die Herausforderungen bei der Entwicklung intelligenter Prozess- und Anlagenleitsysteme für den Mehrroboterbetrieb . Jerome Berg, Stabsingenieur bei Northrop Grumman Innovation Systems (Clearfield, Utah, USA), beschrieb die automatisierte Herstellung von Airbus-Flugzeugstringern im Werk in Utah mit einem selbst entwickelten AFP-Verfahren, und Uwe Lang von Evonik Resource Efficiency GmbH (Darmstadt) , Deutschland) führte mit der „Sandwich Technology 4.0“ eine automatisierte Fertigungstechnologie für hohe Produktionsraten ein, die das Kernmaterial ROHACELL des Unternehmens verwendet. In Zusammenarbeit mit dem DLR und dem Technologiezentrum CTC GmbH von Airbus (Stade, Deutschland) wurde ein hochautomatisierter Preforming-Prozess für eine Flugzeugbugfahrwerkstür demonstriert.
Sehen Sie sich ein Video des Preforming-Prozesses an:
Auf einer Reise in die virtuelle Realität zeigte Felix Hünecke, Leiter Business Development der ABSOLUTE Reality GmbH (Hamburg, Deutschland), wie 3D-Modelle von Gebäuden erstellt, bearbeitet und mit Bildern, Dokumenten und Videos ergänzt werden können, um virtuelle Umgebungen zu erstellen, die von überall auf der Welt betrachtet. Das Unternehmen erstellte einen 3D-Rundgang durch eine DLR-Fertigungshalle in Stade.
Machen Sie einen Spaziergang durch die Produktionshalle des DLR:
Felix Schreiber, CEO, ARK Group (Aachen, Deutschland), diskutierte die Prozess- und Kostenvorteile strukturierter Maschinendaten in einer automatisierten Resin Transfer Moulding (RTM) Produktionslinie, während Sascha Backhaus von der CTC GmbH über modulare Automatisierung in der Composites-Fertigung und die Hybr -iT-Projekt, das Teams entwickelt, in denen Mensch und Roboter mit softwarebasierten Assistenzsystemen zusammenarbeiten.
Keine Veranstaltung zur Fabrik der Zukunft darf das Thema Künstliche Intelligenz (KI) vernachlässigen, und Amir Ben-Assa, CMO von Plataine (Waltham, Massachusetts, USA) diskutierte die Chancen und Herausforderungen der Implementierung von KI in der Verbundwerkstoffherstellung. Er stellte praktische Anwendungen der KI vor, von Warnmeldungen (zum Beispiel Produktionsverzögerungen oder Qualitätsproblemen) bis hin zu Empfehlungen (zum Beispiel optimierte Materialauswahl). KI-basierte digitale Assistenten auf Google Glass könnten eine weitere Möglichkeit sein, die eine „freihändige“ Benutzerinteraktion mit KI in der Produktionshalle und eine Audio- und visuelle Darstellung von Warnungen in Echtzeit bieten.
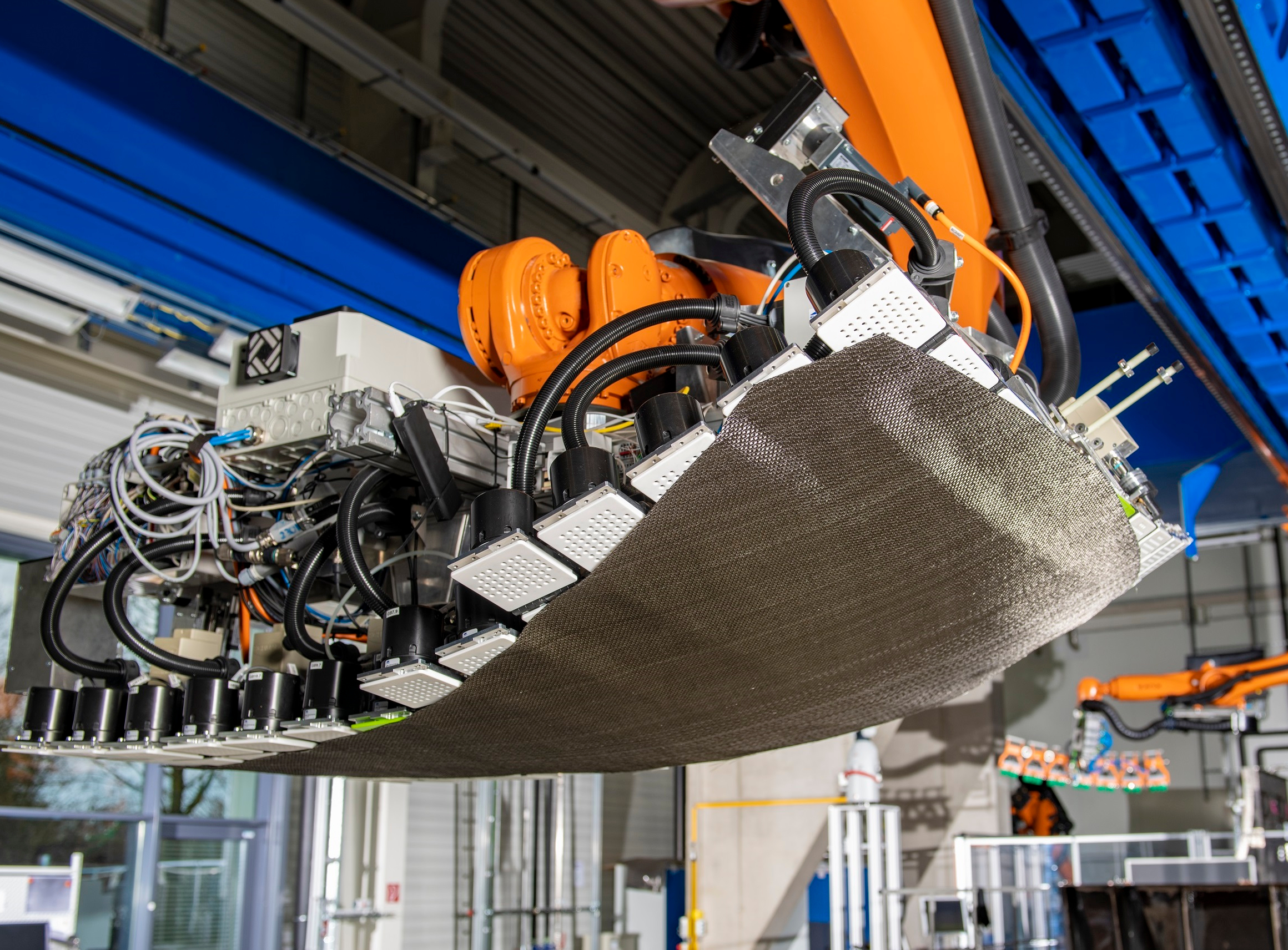
Die multifunktionale Roboterzelle am ZLP Augsburg wurde entwickelt, um die Entwicklung integrierter Prozesse zur Herstellung großer Verbundbauteile im industriellen Maßstab zu ermöglichen. Quelle | DLR
Weitere Themen enthalten:
- Faseroptische Sensorik für die intelligente Prozessüberwachung in großen Verbundstrukturen (MT Aerospace AG; Augsburg, Deutschland);
- Ein intelligentes Steuerungssystem für die automatisierte Herstellung von Verbundwerkstoffen (National Composites Centre, Bristol, Großbritannien);
- Ein modellbasiertes Qualitätskontrollsystem für das Thermoformen von Kleinteilen (Faserinstitut Bremen e.V.; FIBRE, Bremen, Deutschland);
- Ein Verfahren zum Formpressen diskontinuierlicher faserverstärkter Thermoplaste für Flugzeuganwendungen, basierend auf flexibler Automatisierung und skalierbar auf große Teilegröße (ACT Aerospace; Gunnison, Utah, USA);
- Ein isothermer RTM-Prozess mit reduzierten Zykluszeiten für die Großserienfertigung von CFK-Teilen (Airbus Helicopters)
- Großserienfertigung von komplexen Carbonfaser-Hochleistungs-Thermoplastprofilen für Federbeine, Rohre und Antriebswellen unter Verwendung von endkonturnahen Tape-Preforms und Spritzgussverfahren (herone GmbH; Dresden, Deutschland). Erfahren Sie mehr über herone und dieses Verfahren in „Spritzgießen für hochleistungsfähige, vereinheitlichte thermoplastische Strukturen“.
10 Jahre Fortschritt in Augsburg
Zum 5. Kolloquium Produktionstechnik des DLR am 15. Mai kamen in einer gesonderten Veranstaltung knapp 200 Gäste im Zentrum für Leichtbauproduktionstechnologie (ZLP) in Augsburg zusammen. Die Veranstaltung feierte das 10-jährige Bestehen von ZLP in Augsburg, wo sich heute rund 60 Mitarbeiter mit der Automatisierung und Digitalisierung der Composites-Produktion beschäftigen.
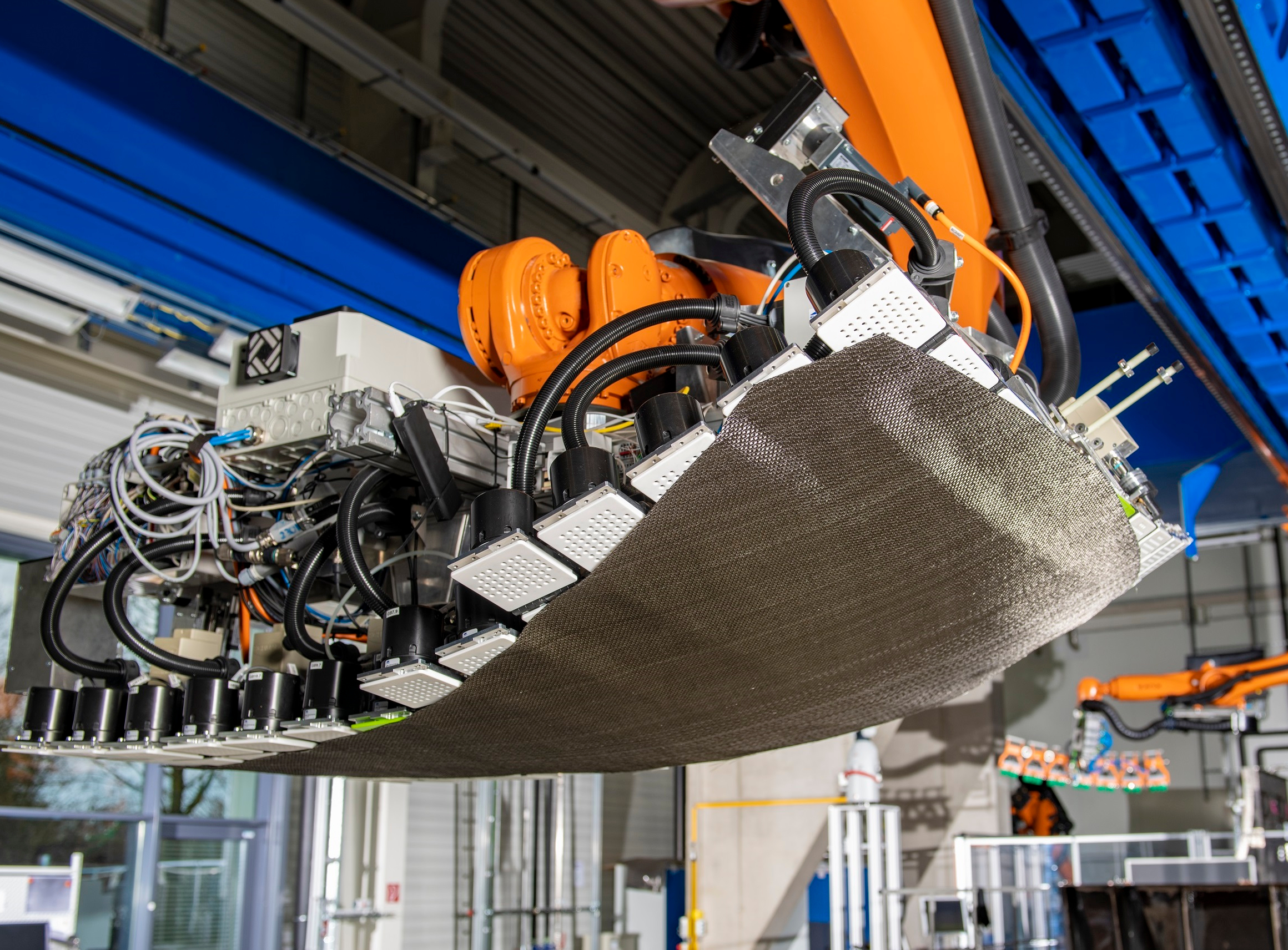
Ein Robotergreifer für das automatisierte Drapieren, Teil des integrierten Fertigungsprozesses von ZLP Augsburg für vollwertige Strukturbauteile. Quelle | DLR
Der Tag begann mit zwei Präsentationen der University of British Columbia (UBC; Vancouver, Kanada), die 2016 eine Kooperation mit dem DLR begann. Prof. Dr. Anoush Poursartip, Co-Direktorin der Digital Learning Factory Initiative der UBC, stellte das Konzept vor einer Lernfabrik für Verbundwerkstoffe inspiriert von medizinischen Lehrkrankenhäusern. Die Lernfabrik für Verbundwerkstoffe, die sich auf dem UBC-Campus Okanagan befinden soll, soll Forschung und Bildung mit industriellen Aktivitäten verbinden. Ein digitaler Zwilling, der bei UBC Vancouver gehostet wird, wird Daten aus der physischen Fabrik mit Simulationen kombinieren, um die Herstellungsprozesse von Verbundwerkstoffen für die Luft- und Raumfahrt zu optimieren. Als nächstes diskutierten Prof. Dr. Homayoun Najjaran von der UBC und Marian Körber vom DLR über die Optimierung komplexer Fertigungsprozesse in einer virtuellen Umgebung und wie die Expertise von UBC in maschinellen Lerntechniken und künstlicher Intelligenz genutzt wird, um Zeit und Kosten der Entwicklung von Robotersystemen im DLR zu reduzieren . Mit einer Deep-Learning-Methode wurde der Robotergreifer von ZLP für das automatisierte Drapieren trainiert, ein wesentlicher Bestandteil der automatisierten Prozesskette des Augsburger Standorts zur Herstellung großer CFK-Teile. Der Greifer mit 127 Saugmodulen mit variabler Saugkraft erkennt und greift Schnittgut; die Module nehmen die erforderliche Geometrie zum Drapieren im Werkzeug an.
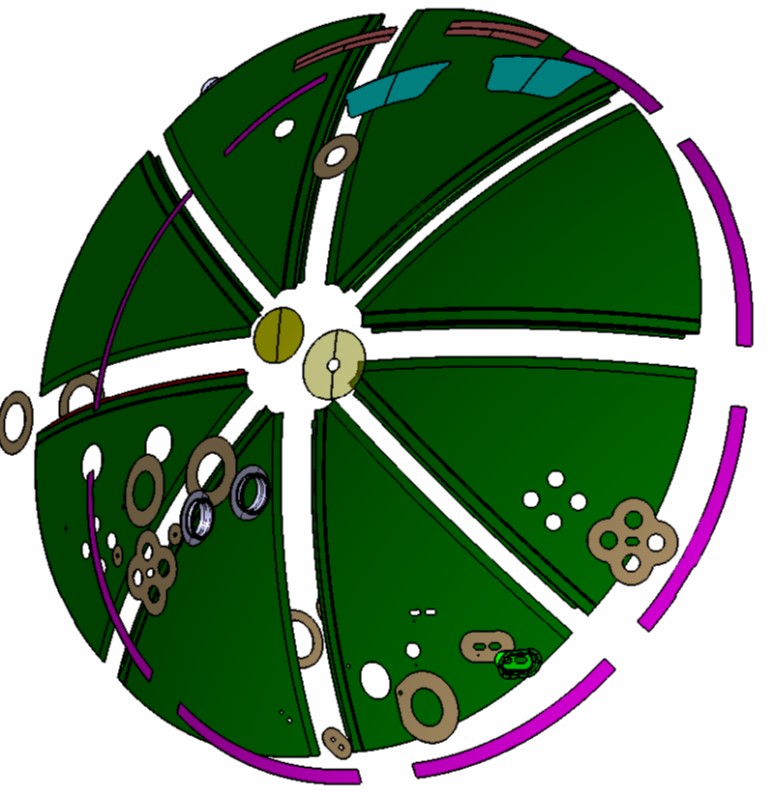
Die thermoplastischen Verbundkomponenten für das hintere Druckschott-Design von Premium Aerotec werden mit einem am ZLP Augsburg entwickelten Widerstandsschweißverfahren verbunden. Quelle | Premium-Aerotec
Thermoplastische Technologien sind ein weiterer Schwerpunkt des ZLP Augsburg. Ein Projekt zur Entwicklung des weltweit ersten thermoplastischen hinteren Druckschotts (RPB) für Single-Aisle-Flugzeuge wurde von Ralph Männich und Alexander Sänger von der Premium Aerotec GmbH skizziert. Das Unternehmen arbeitet mit dem ZLP Augsburg, Toray Advanced Composites und dem Institut für Verbundwerkstoffe (IVW) an einer Konstruktion bestehend aus acht CFK-Segmenten mit integrierten Stringern, die mit einer von ZLP entwickelten Widerstandsschweißtechnologie verbunden sind. Automatisierte Prozesse mit kurzen Zykluszeiten ermöglichen eine Großserienfertigung. Die Fertigstellung der Technologie (bis TRL 6) ist für 2020 geplant, die Umsetzung soll 2021/2022 erfolgen. Auf der Paris Air Show im Juni zeigte Premium Aerotec einen 1:1-Demonstrator für ein Flugzeug der Airbus A320-Serie. Im Vergleich zu aktuellen A320-Druckschotts aus genieteten Aluminiumbauteilen soll das thermoplastische Bauteil die gleichen mechanischen Eigenschaften bei 10-15 % Gewichtseinsparung und 50 % Verkürzung der Produktionszeit liefern. Im folgenden Vortrag setzten Dr. Stefan Jarka und Manuel Endraß vom DLR das Thema thermoplastisches Schweißen fort und gingen tiefer in die Füge- und ZfP-Fähigkeiten des ZLP Augsburg und seine Rolle im RPB-Projekt ein.
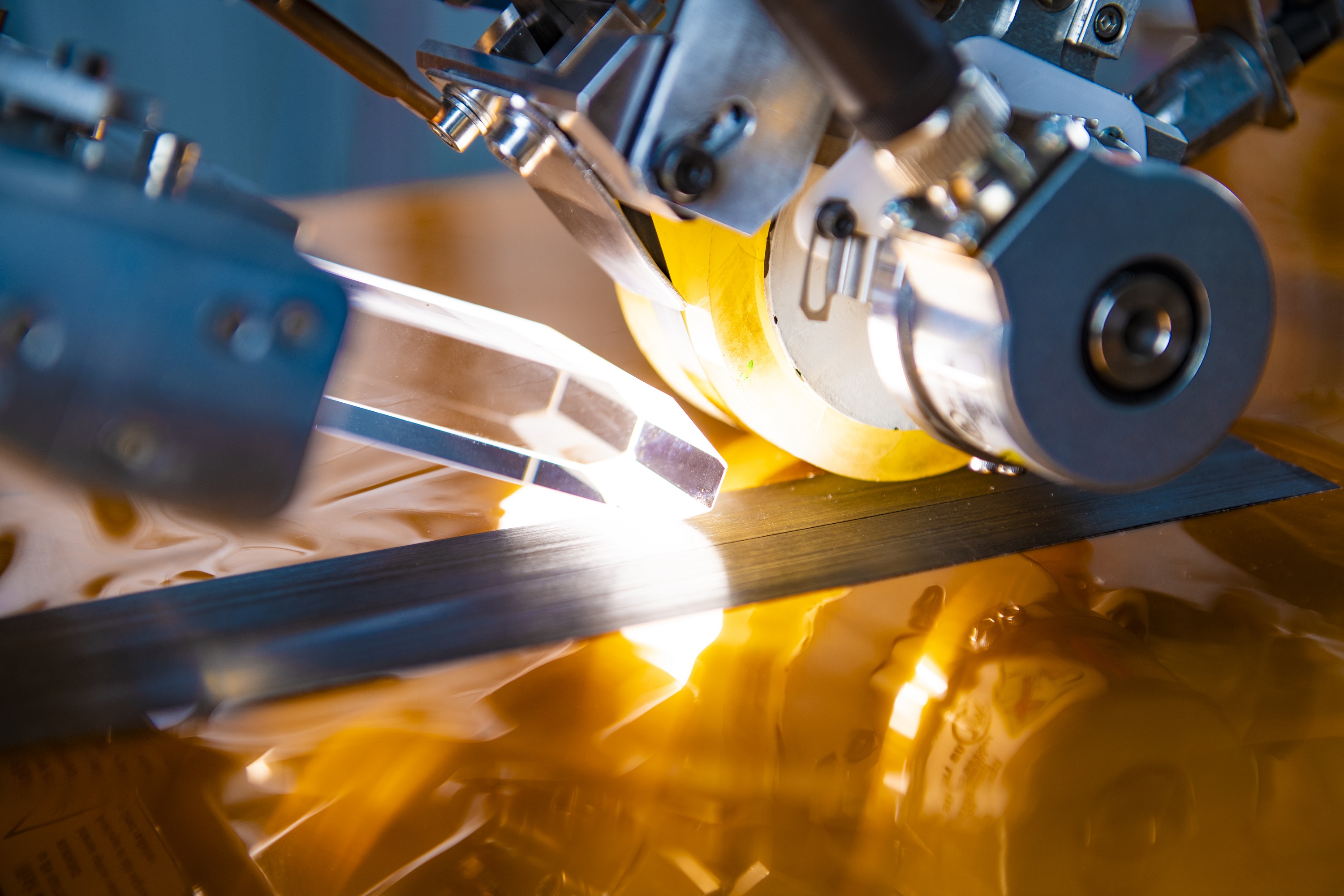
ZLP Augsburg untersucht blitzlampenbasierte In-situ-AFP von thermoplastischen Verbundwerkstoffen, eine gepulste Energielösung, die die für laserbasierte AFP erforderlichen Sicherheitsgehäuse überflüssig macht. Quelle | DLR
Thermoplastische Verbundwerkstoffe bieten auch Möglichkeiten in Raumfahrtanwendungen. Vorträge von Ralf Hartmond, MT Aerospace AG und Lars Brandt, Projektleiter für Raumfahrtanwendungen im DLR, skizzierten die Entwicklung einer carbonfaserverstärkten thermoplastischen Oberstufe für die nächste Generation der Ariane Raketenwerfer. Brandt erläuterte die Arbeit des DLR zum Materialscreening für den Flüssigwasserstofftank (LH2 .) ) Tank – wo Kohlefaser-PEEK und niedrig schmelzendes (LM) PAEK vielversprechend sind – und Entwicklung eines In-situ-AFP-Prozesses aus thermoplastischen Verbundwerkstoffen, um einen schlanken additiven Fertigungsansatz zu ermöglichen. ZLP vergleicht einen neuen blitzlampenunterstützten in-situ-AFP-Prozess mit herkömmlichem laserunterstütztem AFP.
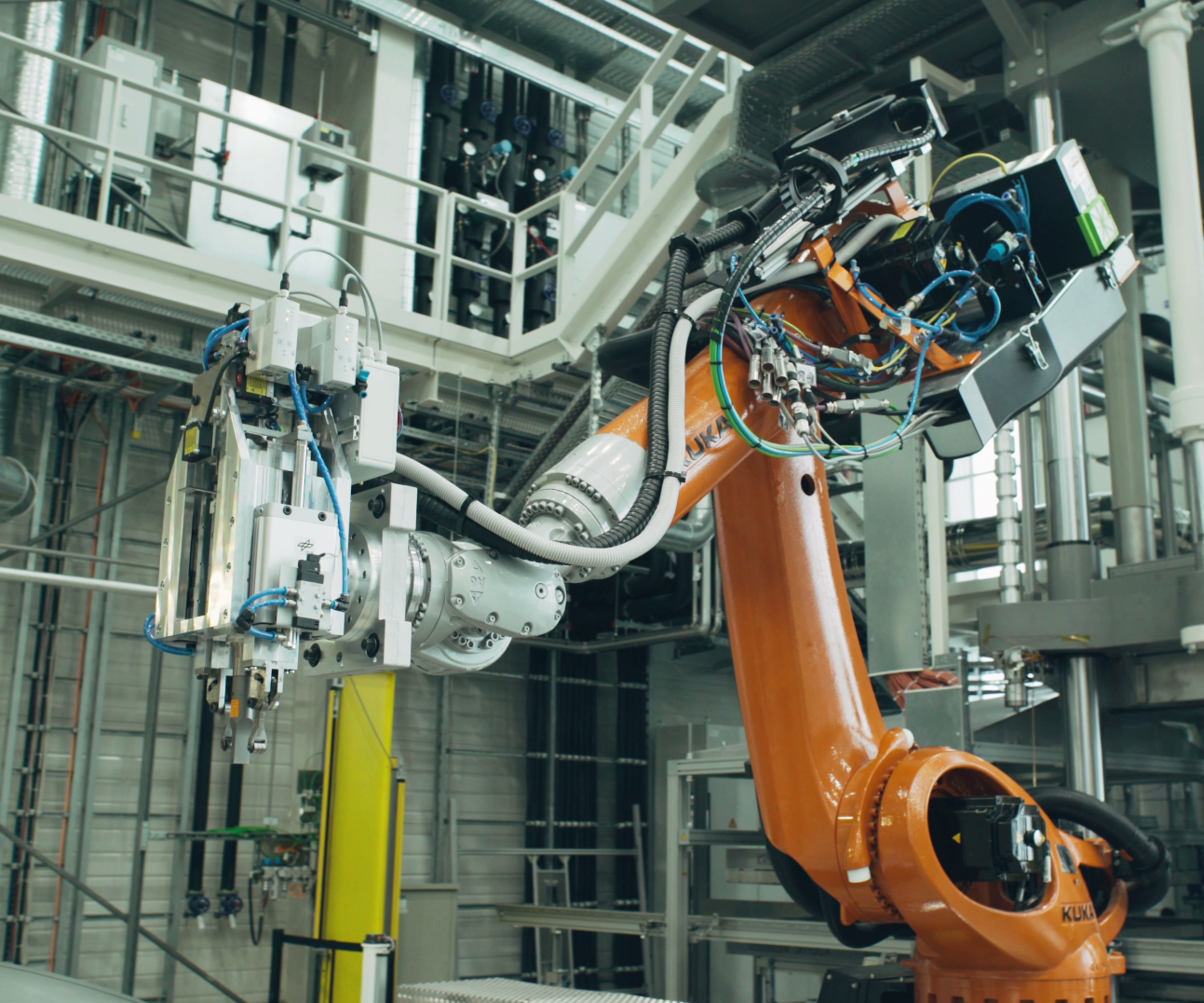
Fügetechnologien werden der Schlüssel zur erfolgreichen Einführung thermoplastischer Verbundwerkstoffe in zukünftigen Luft- und Raumfahrtanwendungen sein. ZLP in Augsburg hat ein roboterbasiertes kontinuierliches Ultraschallschweißsystem entwickelt, das aus einem Endeffektor besteht, der auf einem KUKA QUANTEC KR210 Roboter auf einer 7 m Linearbahn montiert ist. Dies wurde an Komponenten wie einer versteiften Rumpfplatte und einem hinteren Druckschott bewiesen. Quelle | DLR
Den Abschluss des Tages bildete eine anregende Keynote von Prof. Dr. Michael Kupke, Leiter des ZLP Augsburg, zum Thema „Digitalisierung und flexible Produktion“. Er fragte, ob der Aufstieg der digitalen Plattformökonomie Chancen oder Risiken für Hersteller von Verbundwerkstoffen birgt und wies darauf hin, dass die IT zu einer Kernkompetenz wird und als wertschöpfender Wettbewerbsvorteil und nicht als Kostenstelle behandelt werden sollte. Er sagte auch, es gebe einen anhaltenden Paradigmenwechsel von der Detailplanung hin zu Selbstorganisation (Lean Production) und Automatisierung in Kombination mit Digitalisierung. KI ermögliche eine autonome, flexible Produktion. Allerdings, so Kupke abschließend, ist es wichtig, menschliche Fähigkeiten zu schätzen und zu integrieren, die für die Entscheidungsfindung und Prozessverbesserung von entscheidender Bedeutung sind.
Harz
- 4 brennende Fragen für die additive Fertigung im Jahr 2019
- 25 wichtige Meilensteine für die additive Fertigung im Jahr 2019
- 3 Produktionsprognosen für 2019
- Die 10 wichtigsten Fortschritte in der Fertigungstechnologie für Verbundwerkstoffe
- Mehr von der JEC World 2019
- Vorschau der JEC World 2019:SABIC
- Menschen in Verbundwerkstoffen – Januar 2019
- Automatisierungstechnologie unterstreicht Sicherheit, flexible Fertigung
- 2019:Fertigungsprognosen
- Best Practices für das Fertigungsmarketing für 2019