Das PASSARO-Projekt von Clean Sky 2 zielt auf ein einmaliges OOA-Composite-Cockpit ab
Das Projekt PASSARO (caPAbilities for innovati Technologien wie In-situ-Konsolidierung aus thermoplastischen Verbundwerkstoffen und Flüssigharzinfusion. Dieses Composite-Cockpit wurde von Airbus Defence and Space (Madrid, Spanien) während Clean Sky 1 auf Basis des Flugzeugs C295 entwickelt. Das Projekt zielt auch auf die Automatisierung von Fertigungsprozessen sowie auf neue Testansätze basierend auf Industrie 4.0-Konzepten und die Entwicklung ergonomischer fortschrittlicher Konzepte, die den Pilotenkomfort und eine verbesserte Mensch-Maschine-Schnittstelle fördern.
Das PASSARO-Projekt, Teil der Airframe-Plattform von Clean Sky 2, startete im Juli 2016 mit einer Gesamtlaufzeit von 48 Monaten. Es besteht aus elf Partnern aus Portugal und Spanien, die eng mit Airbus Defence and Space zusammenarbeiten.
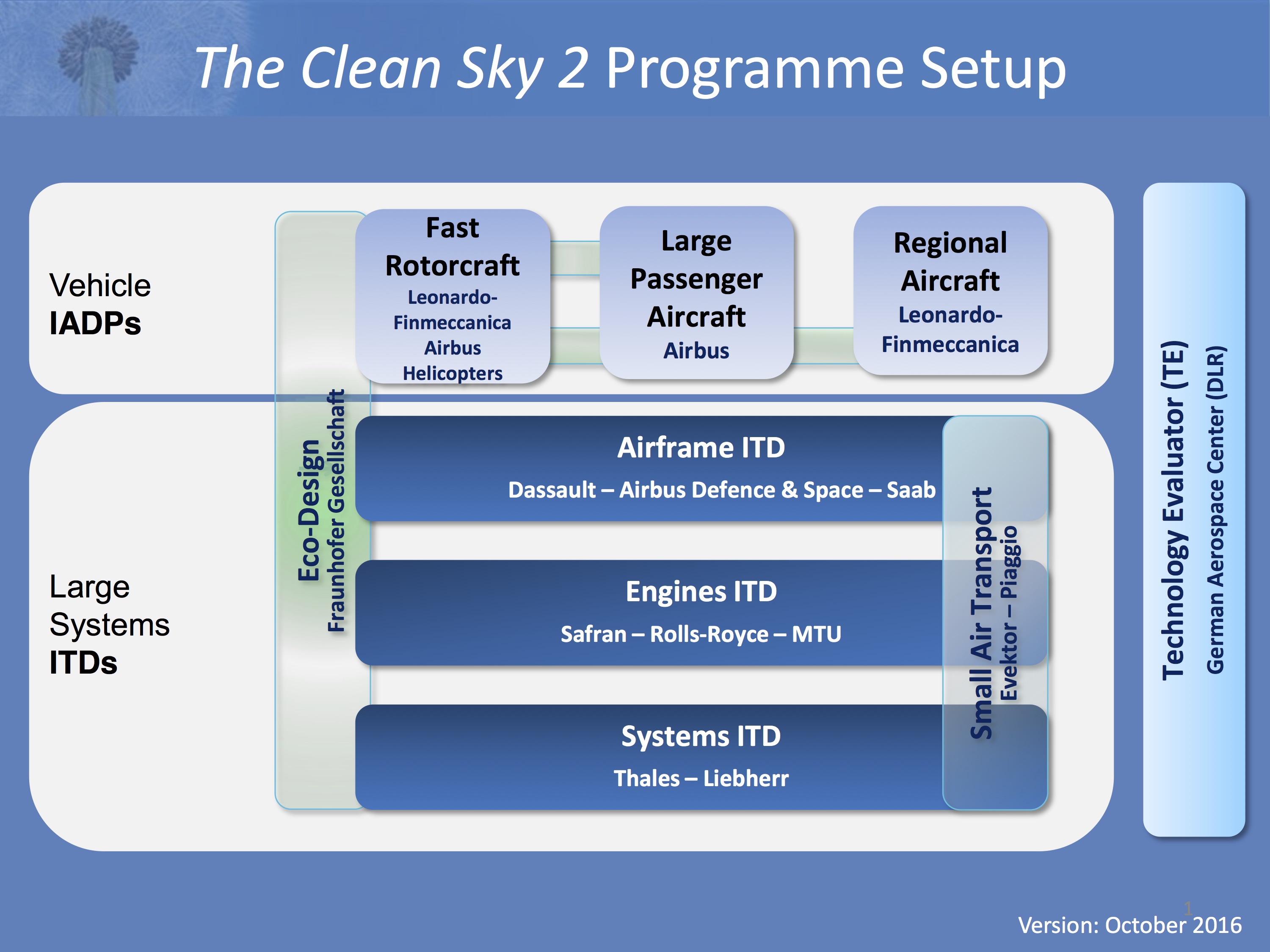
QUELLE:Clean Sky 2
Synergien mit dem portugiesischen regionalen MOSHO-Projekt
Viele Clean Sky 2 (CS2)-Projekte nutzen Synergien mit regionalen EU-Mitgliedsinitiativen (z. B. CORAC in Frankreich). Das PASSARO-Projekt hat ergänzende Aktivitäten mit portugiesischen nationalen FuE-Initiativen gefördert. Das Projekt MOSHO (Advanced solutions for impact materials, repair of composite aero-structures and their monitoring) ergänzt die Aktivitäten von PASSARO, an denen einige der Partner beteiligt sind, und wird von ADS (Airbus Defence and Space) als Clean Sky 2-Koordinator für die Flugzeug-ITD. Das Projekt wird fortschrittliche Lösungen für die Reparatur von Verbund-Flugzeugstrukturen entwickeln und integrieren.
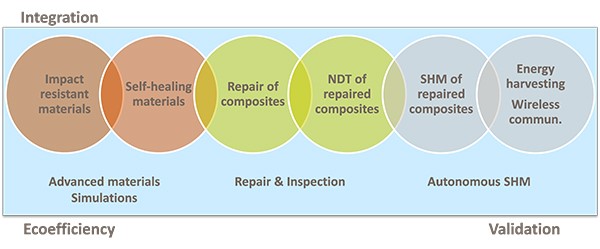
Abbildung 3:Technischer Umfang des MOSHO-Projekts QUELLE: https://www.cleansky.eu/commissioner-moedas-meets-passaro-at-isq
Die kollaborativen Roboter von PASSARO verkürzen die Zykluszeit für das Handlegen um bis zu 70 %
Als Teil der Ziele des PASSARO-Projekts, zu erforschen und zu entwickeln, wie kollaborative Roboter bei der Herstellung von Verbundwerkstoffen eingesetzt werden können, entwickelte das OPTIMAL-Projekt eine praktische und kostengünstige automatisierte Lösung, um das traditionelle Handlaminieren unter Verwendung qualifizierter Materialien zu ersetzen.
Traditionell ist die Herstellung von Verbundbauteilen aus Prepreg im Wesentlichen eine handwerkliche Tätigkeit, aber es werden Schritte in Richtung Automatisierung unternommen. In den letzten zehn Jahren sind mehrere automatisierte Lay-up-Lösungen für Teile mit relativ einfacher Geometrie entstanden. Diese Lösungen sind oft recht teuer und erfordern häufig, dass Fabriken für ihre Installation von Grund auf neu entworfen werden. Sie erfordern typischerweise spezielle Umgebungen in Form von isolierten Zellen mit dedizierten Sicherheitssystemen. Alternativ könnten kollaborative Roboter (Cobots) in die bestehenden Fertigungsabläufe integriert werden, um einige Aufgaben zu automatisieren und die Produktivität zu verbessern, ohne die Umgebung drastisch zu verändern.
Industrieroboter sind schnell, stark und haben eine außergewöhnliche Genauigkeit und Wiederholbarkeit, aber sie werden nur mit dem Ziel entwickelt, das Endergebnis zu optimieren. Im Vergleich dazu sind Cobots langsamer, weniger genau und handhaben kleinere Nutzlasten, verfügen aber über das, was benötigt wird, um einfache Aufgaben, insbesondere neben dem Menschen, zu deutlich geringeren Kosten zu automatisieren. Cobots verfügen über Lastsensoren, die kleinste Stöße erkennen und sicher stoppen.
Das Ziel von OPTIMAL bei der Entwicklung von Cobot-Technologien ist es, die eigene Kapazität und die anderer Unternehmen zu verbessern, um wiederholbare, qualitativ hochwertigere Produkte in großen Mengen und zu niedrigeren Preisen anzubieten.
Im Arbeitspaket 10 des PASSARO-Projekts wurden drei Hauptschritte mit kollaborativen Robotern entwickelt:
- Aufnahme und Sortierung von Lagen direkt vom automatischen Lagenschneider;
- Ply Peeling mit einer speziellen Zelle;
- Positionieren und Stapeln von Lagen in einem Werkzeug.
Um diese Aktivitäten umzusetzen, wurde eine Zelle entwickelt, die Prepreg-Lagen vom Lagenschneider aufnimmt, automatisch schält und auf eine Form stapelt.
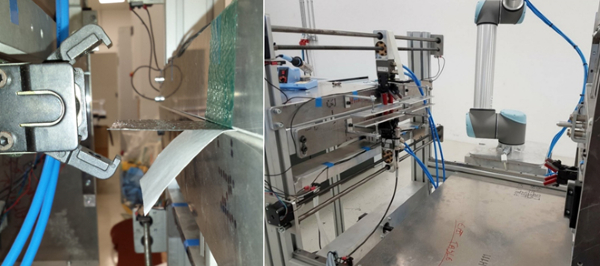
Kollaborative Roboter für die Composite-Fertigung im PASSARO-Projekt. QUELLE: ISQ-Gruppe
Positionier- und Stapelaufgaben übernimmt der Roboterarm mit speziellen Saugnäpfen für das Prepreg-Handling. Der Peeler ist eine komplexere Maschine, bei der das Prepreg mit Druckluft geschält wird, das durch zwei Beschichtungen geschützt ist – normalerweise eine Kunststoff- und eine Papierbeschichtung oder einfach nur zwei Kunststoffe. Das Peeling-Konzept basiert auf der Tatsache, dass unterschiedliche Materialien dazu neigen, bei gleicher Reizung mit unterschiedlichen Frequenzen zu vibrieren. Durch die unterschiedlichen Schwingungsfrequenzen entstehen Lufteinschlüsse zwischen dem Prepreg und den Deckschichten. Der Plattenresonator passt die Schwingungsamplitude für verschiedene Materialien an. Dieser Prototyp konnte Schälraten mit nahezu 100 % Erfolg für bestimmte Materialien und eine Stapelgenauigkeit von ± 0,5 mm in jedem der beiden Freiheitsgrade in der Formebene und ± 0,1 ° in der Rotation erreichen.
Der modulare Ansatz für dieses System macht es unabhängig von Lagenabmessungen. Die Breite wird durch das Hinzufügen weiterer paralleler Schälmodule und die Länge durch die Anpassung des Schäleröffnungsbereichs abgedeckt. Diese Technologie bietet im Vergleich zu einem menschlichen Bediener eine deutliche Verbesserung der Prozessgenauigkeit, Wiederholbarkeit und insbesondere der Zykluszeit mit einer Reduzierung um bis zu 70 %.
Autoren:António Reis, Nicole Cruz, Marco Neves (OPTIMAL) und Rúben Buelga Sanchez (ADS). Für weitere Informationen kontaktieren:
INEGI
Campus da FEUP
Rua Dr. Roberto Frias, 400
4200-465, Porto, Portugal
Tel:(+351) 229 578 710
E-Mail:[email protected]
Harz
- Solvay erweitert die Kapazität von thermoplastischen Verbundwerkstoffen
- Toray im niederländischen Projekt für Flüssigwasserstofftanks in Flugzeugen
- Clean Sky 2 FUSINBUL-Projekt entwickelt großformatige Druckschotts aus Kohlefaser
- Die Bedeutung der Harzauswahl
- Clean Sky 2 FRAMES-Projekt verbessert die Erwärmungssimulation von thermoplastischem Verbundwerkstoff AFP mit Xenon-Blitzlampe
- Clean Sky 2 veröffentlicht Projektergebnisse
- Deutscher Composite-Spezialist INVENT arbeitet mit SUSTAINair für mehr Kreisförmigkeit von Flugzeugen zusammen
- Wing of Tomorrow-Rippen:One-Shot, thermoplastisch, OOA-Konsolidierung
- Konsortium sucht Lösungen für thermoplastische Kohlefaser-Verbundstrukturen
- Schnelle Herstellung von Tailored Composite Blanks