Neue Horizonte beim Schweißen thermoplastischer Verbundwerkstoffe
Dieser Blog begleitet das Feature „Schweißen von thermoplastischen Verbundwerkstoffen“ vom September 2018. Es ist eine Zusammenstellung von Bildern und Details, die nicht in den gedruckten Artikel passten, darunter eine Zeitleiste der Entwicklungen beim Induktionsschweißen und Details zur Qualifizierung für zukünftige Verkehrsflugzeuge sowie kurze Abschnitte über Reparaturen, Entwicklungen für Automobile und Duroplaste zu Thermoplasten (TS -TP) Schweißen.
Um noch einmal zu wiederholen, warum geschweißte thermoplastische Verbundbaugruppen (TPC) sowohl für Leichtbaustrukturen in der Luft- und Raumfahrt als auch in der Automobilindustrie von Interesse sind, vergleichen Sie die beiden folgenden Bilder des hinteren Druckschotts des Airbus A320. Das obere Bild ist die aktuelle Version aus Aluminium. Beachten Sie die große Anzahl von Nieten. Vergleichen Sie das jetzt mit dem geschweißten TPC-Demonstrator, den Premium Aerotec auf der ILA 2018 in Berlin präsentiert hat. Beachten Sie das Fehlen von Nieten. Bei Verbundwerkstoffen entfallen dadurch nicht nur das Gewicht, die Zeit und die Kosten von Befestigungselementen, sondern auch der Zeit- und Kostenaufwand für das Positionieren und Bohren von Löchern sowie das Reinigen und Inspizieren dieser Löcher. Es bedeutet auch viel leichtere Strukturen ohne die Laminatpolster, die erforderlich sind, um Schnitte durch tragende Fasern auszugleichen.
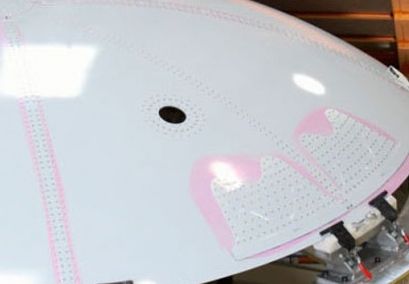
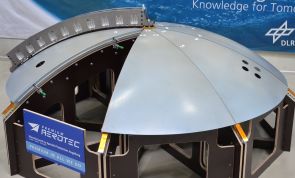
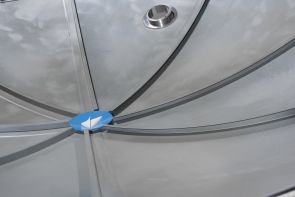
Eine geschweißte hintere A320-Druckwand aus thermoplastischem Verbundwerkstoff (unten) bietet eine nietenlose Lösung im Vergleich zur aktuellen Aluminiumkonstruktion (oben).
QUELLE:RUAG (oben) und Premium Aerotec (unten), DLR-Zentrum für Leichtbauproduktionstechnik (Augsburg, Deutschland)
„Ein weiterer Vorteil besteht darin, dass die Prüfung von Schweißkonstruktionen im Vergleich zu geklebten Baugruppen einfacher ist“, sagt Dr. Hans Luinge, R&D für thermoplastische Verbundwerkstoffe und Produktentwicklungsleiter beim TPC-Materiallieferanten TenCate-Toray Group. „Der C-Scan funktioniert gut und zeigt, ob das Laminat keine Porosität aufweist, was bedeutet, dass die Schweißnaht gut ist. Bei geklebten Strukturen kann es zu Kissing Bonds oder schwer zu erkennenden Verunreinigungen kommen.“ Obwohl TenCate-Toray selbst keine Schweißtechnik entwickelt, unterstützt es eine Vielzahl von Industrie- und Kundenprojekten. „Wir optimieren unsere Materialien nach Bedarf“, sagt Luinge, „und versuchen, die Entwicklung durch unsere langjährige Beteiligung an Initiativen wie TAPAS und mit Partnern wie KVE Composites, TPRC, Tierlieferanten und OEMs in die richtige Richtung zu lenken.“
Entwicklungen beim Induktionsschweißen
KVE Composites entwickelt seit 2001 Induktionsschweißen für TPCs. Frühe Anwendungen verwendeten Kohlefasergewebe/PPS-Laminate, einschließlich Höhenruder und Seitenruder für die Geschäftsflugzeuge Gulfstream G650 und Dassault Falcon 5X.
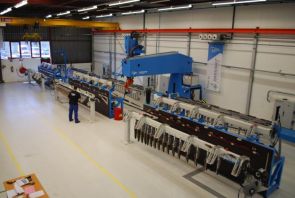
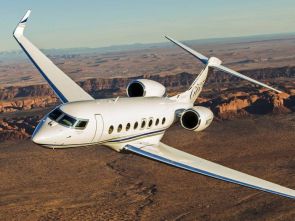
KVE Composites hat geholfen die Produktion von induktionsgeschweißten Höhenrudern und Seitenrudern (links) für die Gulfstream G650 (rechts) und Dassault Falcon 5X von GKN Fokker zu entwickeln.
QUELLE:KVE Composites, GKN Fokker (links) und Gulfstream (rechts).
Andere induktionsgeschweißte TPC-Anwendungen umfassen Kraftstofftank-Zugangstüren, die von AVIACOMP S.A.S. hergestellt werden. (Launaguet, Frankreich und jetzt Teil der Sogeclair Group) für den Airbus A220 Flügel (vormals Bombardier CSeries). (Aviacomp produzierte auch die Stringer für den geschweißten TPC-Rumpf von STELIA, der auf der Paris Air Show 2017 gezeigt wurde.)
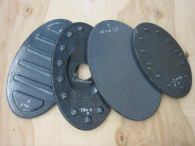
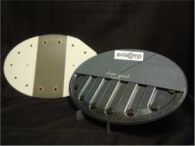
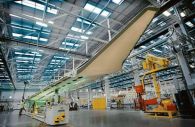
Aviacomp verwendet Induktion Schweißtechnologie, die KVE Composites bei der Herstellung von TPC-Kraftstofftank-Zugangstüren für das Narrowbody-Flugzeug Airbus A220 entwickelt hat.
QUELLE:Aviacomp, Teil der Sogeclair Group.
Diese allgemeine Kategorie von Zugangstüren bietet eine Möglichkeit für das TPC-Schweißen, um Kosten zu sparen, wie eine von KVE Composites durchgeführte Konstruktions- und Herstellungsstudie zeigt. Sogar kleinere Flugzeuge können bis zu 60 dieser Zugangsplatten haben, die alle unterschiedlich geformt sind und typischerweise in einer Verbund-Sandwich-Konstruktion mit bearbeitetem Wabenkern hergestellt werden. „Wenn Sie geschweißte thermoplastische Baugruppen verwenden, können Sie alle verschiedenen Zugangsplatten für ein Flugzeug mit nur 100.000 USD an Werkzeugkosten herstellen, was eine dramatische Einsparung darstellt“, sagt Harm van Engelen, Geschäftsführer von KVE Composites. „Wir müssen den Kern nicht bearbeiten, wir verwenden nur ‚legoartige‘ Komponenten – flache Bleche und gestanzte Versteifungen –, die zusammengeschweißt werden, um die verschiedenen Formen zu bilden. Außerdem ähneln unsere Werkzeuge eher einer Schweißvorrichtung und sind daher relativ kostengünstig im Vergleich zu dem, was sie heute verwenden. Alle Zugangsplatten für ein Flugzeug könnten in einer einzigen Schweißzelle hergestellt werden.“
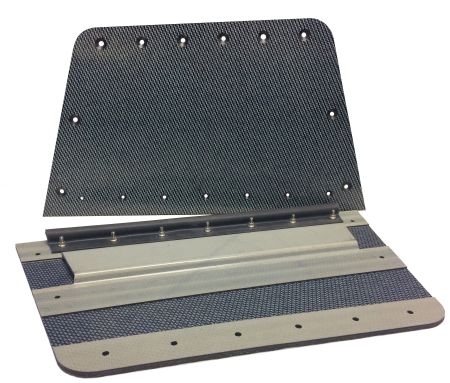
Geschweißte thermoplastische Baugruppe für Flugzeugüberhangplatten kann mit automatisierten Umform- und Schweißzellen hergestellt werden und sparen Sie 100.000 USD an Werkzeugkosten. QUELLE:KVE Composites.
KVE Composites setzt seine Entwicklung der TPC-Schweißtechnologien fort, wie in den folgenden Zeitleisten dargestellt. Die unten gezeigte Produktionszelle für 2019 ist die Falko ATL (Automated Tape Laying) Maschine, hergestellt von Boikon (Leek, Niederlande) mit einem von GKN Fokker entwickelten Ultraschallschweißendeffektor. „Diese Roboterzelle ermöglicht ein effizienteres Prozess- und Kontrollsystem für die nächste Stufe der Serienfertigung von TPC-Teilen im Vergleich zu den heute verwendeten Pick-and-Place-Methoden“, erklärt Maarten Labordus, R&D-Leiter bei KVE Composites. „Sie können zum Beispiel die Skin- und Rippenlaminate für eine regionale Jet-Control-Oberfläche (die ungefähr 60 mm x 3 m groß ist) vollautomatisch auflegen, einen Konsolidierungs- und Formschritt außerhalb des Autoklaven durchführen und dann die Montage in einem angrenzende Schweißzelle.“ Die Falko ATL-Maschine demonstriert auch die bereits von GKN Fokker entwickelte Regelung für das Ultraschallschweißen. „Die Maschine ist in der Lage, das Energieniveau je nach Materialart, Dicke und Form nach Bedarf zu steuern, jedoch ist anschließend während des Formens des fertigen TPC-Teils eine vollständige Schmelzekonsolidierung des flachen Preforms erforderlich“, erklärt Arnt Offringa, Leiter Aerostructures R&T bei GKN Fokker.
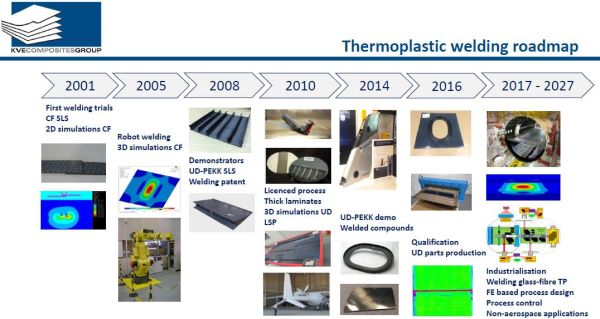
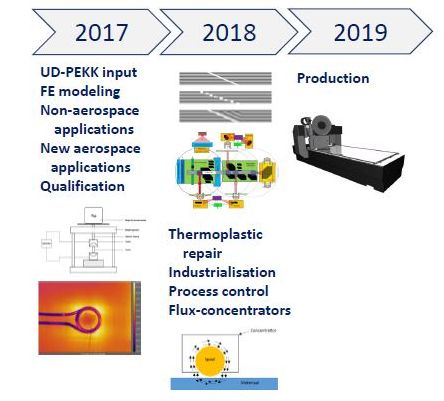
Qualifikation
Oben als wichtige Entwicklungsinitiative im Jahr 2017 gezeigt, Qualifizierung von Induktionsschweißprozessen für TPC-Flugzeugstrukturen hat weiterhin Priorität. Laut dem Abstract für die bevorstehende Präsentation von KVE Composites auf der 4. ten Int. Konf. und Ausstellung für thermoplastische Verbundwerkstoffe (ITHEC, 30.-31. Oktober 2018 in Bremen, Deutschland), hat sich in den letzten Jahren das Schweißen von thermoplastischen Verbundwerkstoffen (TPC) von Polymeren wie PPS und PEI hin zu höherwertigen Polymeren wie PEEK . verlagert , PEKK und jetzt Low Melt PAEK (LM PAEK, lesen Sie mehr in meinem Blog „PEEK vs. PEKK vs. PAEK ...“), sowie hin zu automatisch platzierten UD-Tapes und dickeren Laminaten für höher belastete Strukturen. Als Reaktion darauf hat KVE Composites versucht, Werkzeuge und Ausrüstung sowie FEM-basierte Simulationsmodelle zu verbessern und zu standardisieren.
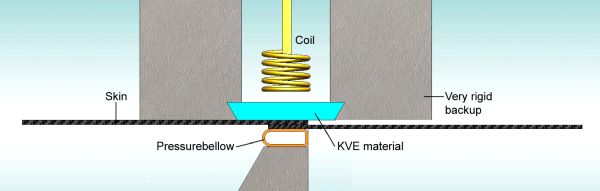
Standardisierter Aufbau zur Qualifizierung des Induktionsschweißens mit neuen Werkstoffen.
QUELLE:KVE Composites
Um die Reifung und Qualifizierung des Induktionsschweißprozesses mit diesen neuen Verbundlaminaten zu unterstützen, hat KVE Composites einen standardisierten Aufbau zum Schweißen von Einzellappen-Scheren sowie L- und T-Abzugstestcoupons entwickelt. Dieses Setup beinhaltet:
- Ein starrer Rahmen, um die Belastungen durch Druck auf das Laminat während des Schweißens aufzunehmen.
- Ein unterer Werkzeugblock, der unter dem Rahmen positioniert werden kann, um reproduzierbares Schweißen von Standardplatten zu ermöglichen.
- Ein aufblasbarer Dorn (Druckbalg in der Abbildung oben) im unteren Werkzeugblock, der sich nur in eine Richtung ausdehnen kann, um das zu schweißende Laminat gegen einen speziellen Kühlkörper („KVE-Material“ in der Abbildung oben) zu komprimieren, um die Hitze beim Schweißen zu begrenzen Schnittstelle.
Durch Austauschen der unteren Werkzeugblöcke können verschiedene Standard-Coupons geschweißt und anschließend mit Ultraschall geprüft werden, wonach kleinere Coupons geschnitten und mechanisch geprüft werden können. Dieses standardisierte Setup wurde bereits installiert von:
- Thermoplastisches Forschungszentrum (TPRC, Enschede, Niederlande)
- McNair Center an der University of South Carolina (Columbus, SC, USA)
- Niederländisches Luft- und Raumfahrtzentrum (NLR, Marknesse, Niederlande).
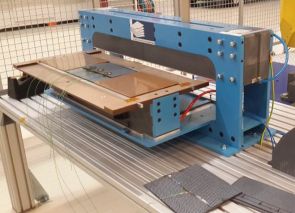

Standardisiertes Induktionsschweißen Aufbau bei KVE (links) und geschweißte UD-Kohlefaser/PEKK-Probe mit Thermoelementen zur Temperaturerfassung an der Bindenaht (rechts).
QUELLE:KVE Composites.
Reparatur
Ein weiterer wichtiger Entwicklungsbereich ist die Reparatur von TPC-Flugzeugstrukturen. „Wir konzentrieren uns zunächst auf qualifizierte und fliegende CF-Gewebe/PPS-Strukturen“, sagt Labordus. „Der Vorgang ist im Grunde der gleiche wie bei der Reparatur von Duroplasten:Das beschädigte Material entfernen, diesen Bereich mit einem Taper-Schal vorbereiten und dann ein Prepreg-Reparaturpflaster einkleben. Laut Labordus besteht eines der Probleme darin, dass thermoplastisches Prepreg bei Raumtemperatur brettartig ist und nicht klebt, „also ist es schwierig, die Geometrie anzupassen“. Er glaubt jedoch, dass die Roboterreparatursysteme, die von Airbus, Lufthansa und anderen entwickelt werden, eine Lösung bieten.
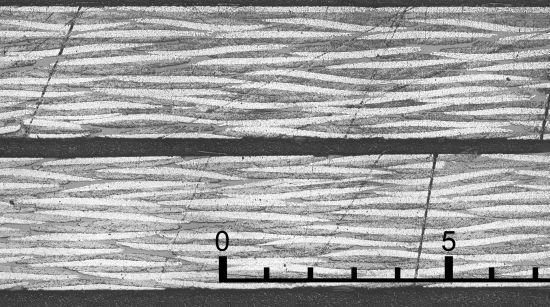
Im Rahmen seiner kontinuierlichen Entwicklung von geschweißten strukturellen thermoplastischen Verbundreparaturen hat KVE Composites induktionsgeschweißte 2D-Linearkonusverbindungen in CF-Gewebe/PPS-Laminaten mit einheitlicher Dicke und 90 % Neumaterialeigenschaften erzielt.
QUELLE:KVE Composites.
Solche Systeme verwenden Messtechnik, um roboterbearbeitete Taper-Schals präzise zu messen und dann einen vorgefertigten Patch zu kleben, der roboterbearbeitet wurde, um zu passen. „Wir wollen Induktionsschweißen verwenden, um einen thermoplastischen Flicken an die ursprüngliche Struktur zu schweißen“, sagt Labordus, aber es gibt noch Fragen, die gelöst werden müssen. „Abhängig von der Form des Teils und des Flickens bilden sich nicht überall Wirbelströme, sodass wir kühle oder überhitzte Bereiche bekommen können. KVE Composites hat dies durchgearbeitet und konnte eine 2D-Linearkegelverbindung in CF-Gewebe/PPS-Laminaten mit gleichmäßiger Dicke und perfekter Schweißnaht erzielen. „Wir lagen innerhalb von 10 % der Neuware-Eigenschaften“, sagt Labordus.
Der nächste Schritt besteht darin, zwei rechteckige Teile mit jeweils einer angerauten Kante induktiv zu schweißen und dann einen konischen Flicken mit einem konischen Schal an ein kreisförmiges / elliptisches Loch zu schweißen, was im Wesentlichen das Verfahren ist, das für Reparaturen von Duroplasten verwendet wird. „Wenn das funktioniert, werden wir auf UD-Laminate aus PEEK und PEKK umsteigen“, sagt Labordus. Ein System zum Einsatz einer Induktionsspule zur Durchführung von Reparaturen im Feld sei noch nicht demonstriert, „aber im Labor möglich“, stellt er fest. Ein weiteres Problem besteht darin, wie Druck ausgeübt wird, um einen ausreichend engen Kontakt zwischen dem Reparaturflicken und der sich verjüngenden Oberfläche zu erzielen. „Derzeit beträgt der Druck im Laborgerät 5 bar. Ich bin mir nicht sicher, ob nur der Druck vom Vakuumbeutel ausreicht, aber bei flacherem UD-Material kann 1 bar nur vom Vakuumbeutel in Ordnung sein.“
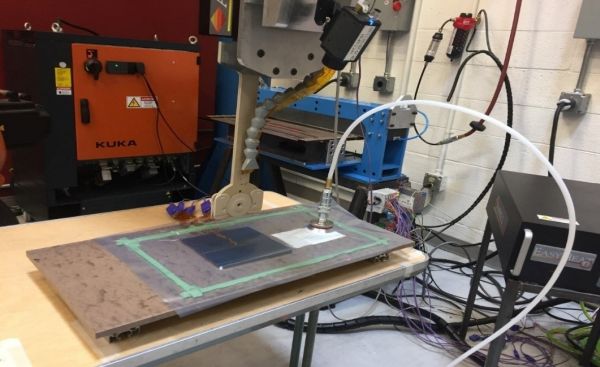
Induktionsschweißen unter einem Vakuumbeutel – ein möglicher Wegbereiter für zukünftige Reparaturen von thermoplastischen Verbundwerkstoffen vor Ort – wird von Michel van Tooren und seinem Team am McNair Center der University of South Carolina entwickelt. QUELLE:Michel van Tooren.
Diese Arbeit bei KVE Composites wird von Michel van Tooren, Direktor des SmartState Center for Multifunctional Materials and Structures, das zum McNair Center an der University of South Carolina (Columbia, SC, USA) gehört, erweitert. „Wir schweißen thermoplastische Verbundwerkstoffe induktiv unter einem Vakuumbeutel, was sehr ähnlich ist, wie heute Verbundreparaturen vor Ort mit einem heißen Bonder und einer Wärmedecke durchgeführt werden“, erklärt er. „Der Vakuumbeutel verhält sich wie ein weiches Werkzeug zum Komprimieren der beiden Teile. Sie legen Induktionsstrom an und erreichen eine Schmelzreparatur. Sie müssen nur die Prozessgrenzen und Parameter definiert haben. In gewisser Weise ist es einfacher als die Reparatur von Duroplasten, da Sie die Reparatur bei Bedarf jederzeit wieder einschmelzen können, auch auf der anderen Seite der Welt oder nach 20-jähriger Betriebszeit. Und das Ergebnis ist keine Klebeverbindung, sondern ein kohäsives Teil, sodass Sie alle Probleme mit der Verklebung beseitigen und wissen, ob Sie bei einer Duroplast-Reparatur eine gute Verbindung haben.“ Auch er glaubt, dass mit den jetzt entwickelten automatisierten Roboterreparaturtechnologien „eine Reparatur durch Induktionsschweißen relativ einfach wäre“.
Duroplast-zu-Thermoplast-Schweißen
Van Tooren entwickelt auch das Induktionsschweißen zum Verbinden von duroplastischen und thermoplastischen Verbundwerkstoffen. „Wir führen Thermoplaste in einen duroplastischen Verbund ein, aber nur dort, wo wir schweißen wollen“, erklärt er. „Wir pfropfen auf ein Nanopartikel und führen eine kleine Kreuzpolymerisation durch. Das Ergebnis ist eine thermoplastische Insel, die in den duroplastischen Verbundwerkstoff implantiert und chemisch mit diesem verschmolzen wird. Dann kann ich auf die Thermoplastinsel schweißen.“ Die Vision sind auch hier alternative Methoden zum Fügen und Zusammenfügen von Verbundwerkstoffen, die das Bohren von Löchern und die Probleme, die mit konventionellem Kleben verbunden sind, vermeiden.
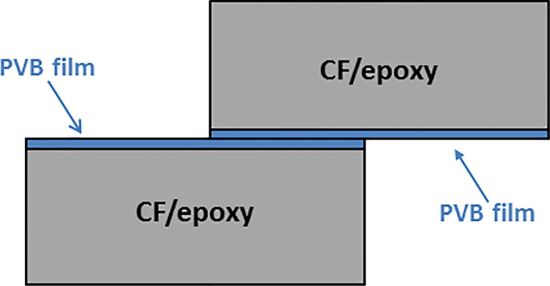
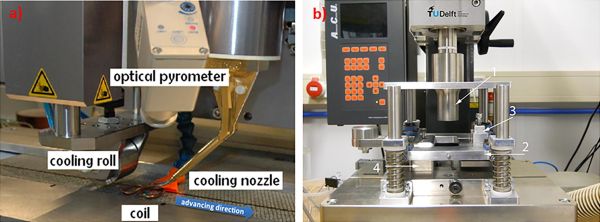
Schema einer TSC-TSC-Verbindung über eine thermoplastische PVB-Koppelschicht vor dem Schweißen (oben). Aufbauten (unten) für Induktionsschweißen (links) und Ultraschallschweißen (rechts).
QUELLE:„Hybridschweißen von Verbundwerkstoffen auf CF/Epoxid-Basis“.
Das Schweißen von duroplastischen Verbundwerkstoffen (TSC) mit TPC-Laminaten (oder TS-TP-Schweißen) wird von mehreren Forschungseinrichtungen verfolgt. Irene Fernandez Villegas von der TU Delft – die in dem Printartikel als führend bei der Entwicklung des kontinuierlichen Ultraschallschweißens von TPCs erwähnt wird – hat 2017 zusammen mit Francesca Lionetto ein Papier mit dem Titel „Hybrid Welding of carbon-fiber verstärkt epoxy based composites“ verfasst Universität Salento (Lecce, Italien), Silvio Pappadà von CETMA Composites (Brandisi, Italien) und andere. Die Grundlagen sind wie folgt:
- Polyvynilbutyral (PVB) ist ein teilkristallines, kostengünstiges thermoplastisches Polymer mit einer Schmelztemperatur von 150-170 °C, das sich durch hervorragende Binde- und Filmbildungsfähigkeit sowie Haftung auf vielen Oberflächen auszeichnet.
- PVB (Mowital, geliefert von Kurakay) wurde als Kopplungsschicht verwendet, hinzugefügt und zu einem 14-lagigen Kohlefasergewebe/Epoxid-TSC-Laminat (Hexcel 3501-6 Prepreg mit einem Faservolumengehalt von 58 % und 180 °C Aushärtung).
- Die makromechanische Verzahnung zwischen der PVB-Kopplungsschicht und dem CF/Epoxid-Verbundstoff wurde durch teilweises Eindringen des PVB-Harzes in die erste Schicht des TSC (typischerweise zwischen 10 und mehreren hundert Mikrometern Dicke) während des Co-Härtens erreicht und Diffusion der Epoxidmonomere in den thermoplastischen PVB-Film.
- Induktionsschweiß- und Ultraschallschweißverfahren führten zu ausreichend starken Schweißverbindungen, wobei die resultierenden CF/Epoxid-auf CF/Epoxid-Verbindungen, die durch die PVB-Kopplungsschichten geschweißt wurden, eine Überlappungsscherfestigkeit von ≈25 MPa zeigten, die im typischen Bereich von Festigkeitswerte für CF/Epoxid-Klebeverbindungen.
Automobil
Fast alle Unternehmen, die in dem Druckartikel zum thermoplastischen Schweißen enthalten sind, befassen sich sowohl mit Automobil- als auch mit Luft- und Raumfahrtanwendungen. „Schweißen trägt dazu bei, Verbundwerkstoffe gegenüber Aluminium wettbewerbsfähig zu machen“, sagt Offringa von GKN Fokker. „Automotive betrachtet Schweißen auch als schnelle Alternative zum Kleben. Wir haben mit mehreren Automobilunternehmen über die schnelle Verarbeitung von Verbundwerkstoffen gesprochen.“ Er weist darauf hin, dass Karosserien aus Kohlefaserverbundwerkstoffen meist duroplastisch sind und mit einer bestimmten Klebstoffdicke verklebt werden. „Wenn Sie diese Teile aus Thermoplast herstellen könnten Verbundwerkstoffe und beseitigen Lücken zwischen den Komponenten durch Schweißen der Baugruppe, dann können Sie eine steifere Karosseriestruktur herstellen, die Gewichts-, Kosten- und Leistungsvorteile bringt.“
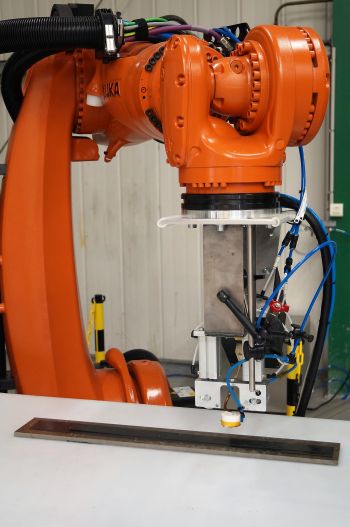
Die Dynamik von Composite Integrity Induktionsschweißverfahren einrichten.
QUELLE:Composite Integrity.
Potenzial sieht auch Jérôme Raynal, Business Development Manager für Composite Integrity. Sein Unternehmen arbeitete mit STELIA Aerospace zusammen, um das dynamische Induktionsschweißverfahren zu entwickeln, das zum Verbinden von CF/PEKK UD-Bandstringern und Rumpfschalen im TP-Demonstrator verwendet wird, der auf der Paris Air Show 2017 vorgestellt wurde. „Wir haben Widerstandsschweißen für die Automobilindustrie mit Verbundwerkstoffen aus Polyamid [PA, Nylon] und Polypropylen [PP] entwickelt“, sagt Raynal. „Dafür haben wir verschiedene Technologien. Wir können beispielsweise einen Metalldraht in ein Teil einbetten, mit einem anderen Teil in Kontakt bringen und Strom einspeisen. Wir können auch einen Widerstandsfleck aus Kohlefaser an der Schweißschnittstelle platzieren, um die erforderliche Schweißwärme zu erzeugen.“ In einer Entwicklung wurden zwei Bauteile aus CF/PA mit einem speziell entwickelten Widerstandspatch aus dem gleichen Polymer und einem Glasfaservlies verschweißt, um das angrenzende Laminat elektrisch zu isolieren und die Energie an der Bindelinie zu konzentrieren. Wie sieht es mit Metalleinlagen aus, die bei Automobilteilen sehr typisch sind? „Teile mit Metalleinlagen sind beim Widerstandsschweißen kein Problem, und beim Induktionsschweißen würde man eine speziell konstruierte Spule verwenden oder die elektromagnetischen Felder und den Strom auf andere Weise modifizieren“, antwortet Raynal. „Das müsste noch entwickelt werden, ähnelt aber dem, was wir bereits für die automatisierte Fertigung von Flugzeugstrukturen demonstriert haben.“
Weitere Entwicklungen und andere Projekte
Eine Anmerkung zum Eröffnungsbild. Es zeigt ein CAD-Rendering des vom DLR-Zentrum für Leichtbauproduktionstechnik (DLR ZLP, Augsburg, Deutschland) entwickelten automatisierten Verfahrens mittels Ultraschallschweißen Kopf eines KUKA Quantec KR210 Industrieroboters, um acht TPC-Abschnitte zu einem hinteren Druckschott (RPB) für ein Flugzeug des Typs A320 zu verbinden. Im begleitenden Printartikel zum TPC-Schweißen habe ich die Entwicklung eines Widerstandsschweißens durch das DLR ZLP diskutiert Methode, die auf dem A320 RPB-Demonstrator von Premium Aerotec verwendet wurde, der auf der ILA 2018 in Berlin ausgestellt wurde. Lars Larsen, Gruppenleiter Montage- und Fügetechnik beim DLR ZLP:„Parallel zum Widerstandsschweißprozess mit einer ‚Schweißbrücke‘ haben wir auch einen robotergesteuerten Ultraschall-Schweißkopf entwickelt. Wir haben Vorversuche zur Ermittlung der relevanten Schweißprozessparameter abgeschlossen und werden in den nächsten Monaten die Integration dieses Ultraschallschweißendeffektors in unseren Roboter verfeinern. Unser Ziel ist es, einen einzigen industriellen Prozess zum Schweißen von Flugzeugrumpfstringern und hinteren Druckschotts aus thermoplastischen Verbundwerkstoffen zu entwickeln.“
Andere Projekte, die ich diesmal nicht behandeln konnte, sind EireComposites und seine Beteiligung an den Ybridio- und Innova-Projekten, bei denen das Potenzial des Schweißens zur Kostensenkung und Erhöhung der Automatisierung verfolgt wird. Das Unternehmen meldet Induktionsschweiß- und Widerstandsschweißmöglichkeiten für CF/PEEK-, CF/PEKK- und GF/PP-Verbundwerkstoffe und dass thermoplastisches Schweißen für den Flügel der Bombardier CSeries (jetzt Airbus A220) bewertet wurde.
Tods Aerospace, jetzt Teil von Unitech Aerospace, nahm an einem von Rolls-Royce gesponserten National Aerospace Technology Exploitation Program (NATEP) teil, das sich mit der Entwicklung einer Widerstandsschweißtechnik befasste, die keine metallisch eingebetteten Implantate verwendet. TenCate-Toray und das National Composites Centre (Bristol, UK) waren ebenfalls Partner.
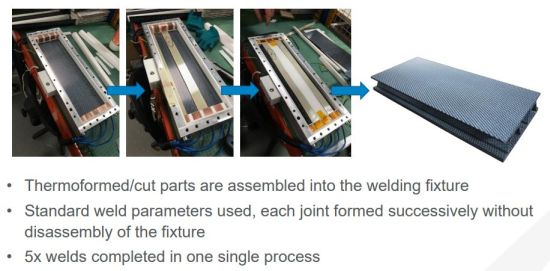
Dieser Prozessdemonstrator untersuchte ein Verfahren zur Herstellung von hutversteiften TPC-Strukturen. QUELLE:Unitech Aerospace (beginnen mit Abschnitt 6, S. 39)
Bleiben Sie dran, denn ich plane, in naher Zukunft über die Entwicklungen des Laser Zentrum Hannover (LZH) zum Laserschweißen von thermoplastischen Verbundwerkstoffen zu berichten.
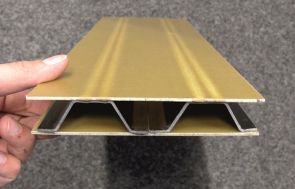
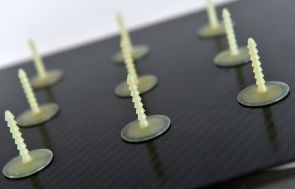
QUELLE:LZH Laser Zentrum Hannover eV
Harz
- Covestro verstärkt Investitionen in thermoplastische Verbundwerkstoffe
- Thermoplastische Verbundwerkstoffe bei Oribi Composites:CW Trending, Episode 4
- RECONTRAS-Projekt validiert den Einsatz von Mikrowellen und Laserschweißen, um recycelbare Verbundwerkstoffe zu erhalten
- Salewas neuer Wanderschuh mit thermoplastischen Verbundwerkstoffen
- Fehlerbehebung beim Thermoformen von thermoplastischen Verbundwerkstoffen
- Thermoplastische Verbundwerkstoffe:Strukturelle Stoßstangenhalterung
- Toray Advanced Composites erweitert seine Fähigkeiten im Bereich thermoplastischer Verbundwerkstoffe
- IRG CosiMo Konsortium für thermoplastische Verbundwerkstoffe enthüllt neue Anlagen
- Thermoplastische Verbundwerkstoffe:Malerische Aussicht
- Schweißen von thermoplastischen Verbundwerkstoffen