Neustart der Rückwand:One-Stop, Abschleppen auf CFK-Teil
Zu Beginn des aktuellen Vordringens von Kohlefaserverbundwerkstoffen in Automobilanwendungen schien der Hersteller BMW Group (München, Deutschland) sich abzuheben. Erste Arbeiten zur Beschleunigung des Resin Transfer Moulding (RTM) für die Produktion des M Das Dach des Sportmodells führte zum Aufbau einer kompletten Lieferkette für kohlenstofffaserverstärkte Kunststoffteile (CFK) auf seinem i3 und i8 Fahrzeuge und dann zu völlig neuen Fertigungs- und Montagearbeitszellen für die Multi-Material-Carbon-Core-Karosserie (BIW) auf seiner 7er Serie .
BMW engagiert sich für den i3 2009 unter großem Getöse, doch im selben Jahr gründete die Audi AG (Ingolstadt, Deutschland) ein Technikum für faserverstärkte Kunststoffe. 2011 gab Audi eine Partnerschaft mit Voith Composites (Garching, Deutschland) zur Entwicklung und Produktion von CFK-Teilen in hohen Stückzahlen bekannt. Im folgenden Jahr veröffentlichte es die Entwicklung einer CFK-verstärkten B-Säule aus Stahl, die im Harzspritzpressverfahren (RTM), und hergestellt wurde seine Partnerschaft mit SOGEFI (Guyancourt, Frankreich) zur Vermarktung von Verbundschraubenfederungen. 2012 war Audi auch Gründungspartner des Spitzenclusters MAI Carbon, zu dem unter anderem BMW, Voith Composites, SGL Group (Wiesbaden, Deutschland) gehörten.
Vor allem beginnt Audis eigene Erzählung der CFK-Entwicklung mit der ersten Generation des R8 Sportwagen aus dem Jahr 2006. Er verfügte über Fachabdeckungen für das Cabrioverdeck sowie Sideblades aus Resin Transfer Moulding (RTM). Vom ästhetischen Exterieur und kleineren Strukturen entwickelte sich das Unternehmen zum Modularen Sportwagen-System (MSS) im Audi R8 e-tron . Obwohl die Hauptstruktur dieses Elektro-Supersportwagens aus stranggepressten Aluminiumträgern bestand, die durch Aluminiumgussteile verbunden waren, bestanden alle Verkleidungen und Füllungen aus CFK, einschließlich eines Kofferraumeinsatzes mit gewellten Crashstrukturen, der es dem Heckmodul ermöglichte, fünfmal so viel Energie aufzunehmen wie der Metallrahmen .
Das Rückgrat des MSS ist seine Rückwand , das sich von einem ersten Konzept im Jahr 2011 zum Modul entwickelt hat, das derzeit für den nichtelektrischen R8 produziert wird von SGL Technologies (vormals BENTELER-SGL, Ort im Innkreis, Österreich; siehe „Werksbesichtigung:BENTELER SGL“). Aber Audi plante bereits den nächsten Schritt:die Iteration der Rückwand für den Einsatz in seinem volumenstarken A8 Luxuslimousine mit Voith Composites als Fertigungspartner.
Voith Composites ist eine 10-jährige Tochtergesellschaft der 1867 gegründeten multinationalen Voith GmbH &Co. KGaA. Die Muttergesellschaft beschäftigt heute 19.000 Mitarbeiter, erwirtschaftet einen Jahresumsatz von 4,2 Milliarden Euro (5,2 Milliarden US-Dollar) und bietet Fertigungsanlagen und -technologien durch vier Divisionen:Voith Digital Solutions, Voith Hydro, Voith Paper und Voith Turbo. Voith Composites hat sich aus der Produktion von CFK-Walzen für die Papierherstellung zur Herstellung von Automobil- und Industrie-CFK-Antriebswellen/Kardanwellen und Flachlaminaten entwickelt.
2011 begann Voith Composites mit der Arbeit an einer hochautomatisierten CFK-Prozesskette zur Herstellung des A8 Rückwand. Sein Herzstück war der Voith Roving Applicator (VRA), der in einer einzigen Linie 35K Kohlefaserkabel von Zoltek (St. Louis, MO, USA) zu gebundenem unidirektionalem (UD) Tape verteilt, das dann geschnitten und gestapelt wird einen zugeschnittenen Rohling formen. Der VRA wurde 2017 mit einem JEC Innovation Award ausgezeichnet. Er hat auch eine solide Basis für nachfolgende Preforming- und Molding-Vorgänge geschaffen. Voith Composites und Audi erhielten auf der JEC World 2018 für die fertige VRA-basierte digitale 4.0-Fertigungslinie zur Herstellung des Audi A8 erneut die höchsten Auszeichnungen in der Kategorie Auto Rückwandmodul. In Zusammenarbeit mit dem Harzlieferanten Dow Automotive (Auburn Hills, MI, USA) und Zoltek haben diese Partner nicht nur die Materialien, Verfahren und integrierten Inline-Inspektionssysteme entwickelt, die für die Herstellung von Hochleistungs-CFK-Teilen in hohen Stückzahlen erforderlich sind, sondern auch die vollständige Suite wesentlicher computergestützter Konstruktions-/Fertigungs- (CAD/CAM) und Simulationstools, die bereits zur Entwicklung zukünftiger Teile eingesetzt werden.
Effizienzorientierte Designentwicklung
„Wir haben schon früh mit Audi zusammengearbeitet“, sagt Dr. Jaromir Ufer, Leiter Business Development bei Voith Composites. An erster Stelle stand die Entwicklung des neuen A8 Rückwanddesign, das die Herstellung des Teils bestimmt.
„Als wir mit dem Engineering für diese Produktion begannen, konnten wir keine handelsüblichen [Software-]Produkte finden, die alles enthielten, was wir brauchten“, erklärt Ufer. „Also haben wir Designtools wie ABAQUS zusammengebracht, aber eigene Materialkarten gebaut und eigene Simulationsmethoden entwickelt.“ Audi hatte bereits beim R8 ein reduziertes BIW-Gewicht und eine erhöhte Torsionssteifigkeit als Hauptziele identifiziert Rückwandgestaltung (siehe „Audi R8 Sitzwand:Ein Auftakt zur Produktion“). Für den A8 Modul wurde ein integrales Design entwickelt, um das mehrkomponentige MSS zu reduzieren Montage zu einer einzigen, geformten CFK-Platte mit wenigen verklebten und vernieteten Befestigungen. Dieses Design trieb die Entwicklung eines stark anisotropen Laminats mit lokalisierten Lastpfaden voran, wodurch das fertige Teil bei 50 % des Gewichts 33 % der Torsionssteifigkeit der Antriebszelle im Vergleich zu einer Baugruppe aus drei bis fünf geschweißten Aluminiumteilen bereitstellt.
„Die Composite-Preform für den Audi A8 Rückwandpaneel variiert von einer Basis von 6-lagig bis zu 19-lagig mit lokaler Verstärkung – zum Beispiel bei Ausschnitten oder punktuellen Belastungen, wie den Kinderwagen-Rückhaltesystemen“, erklärt Ufer (Bild 2).
Voith Roving-Applikator
Ufer stellt fest, dass die Entwicklung dieses Entwurfs und des VRA parallel erfolgten. „Nur durch die Gestaltungsfreiheit, die der VRA bietet, war die Leistung des neuen A8 Rückwand möglich.“ Wichtig war auch die Tatsache, dass der Faserlieferant Zoltek eine 7-jährige Preisverpflichtung für das Programm eingegangen ist.
Der Prozess des VRA beginnt mit einem Spulengatter aus Zolteks PX 35 Kohlefaser. In jede VRA-Linie werden mehrere Spulen mit 50.000 Kabeln eingespeist und gespreizt, um 50 mm breite Bänder zu produzieren. Als nächstes wird ein Bindemittel auf Epoxidbasis aufgetragen, das später beim Resin Transfer Moulding (RTM) des Verbundteils mit dem Dow VORAFORCE Snap-Cure Epoxidmatrixharz reagiert. Eine kleine Menge Infrarot (IR)-Wärme wird angewendet, um das Bindemittel ausreichend zu schmelzen, um das Band durch die nachfolgenden Konsolidierungs-, Schneid- und Stapelschritte zusammenzuhalten (Schritt 1).
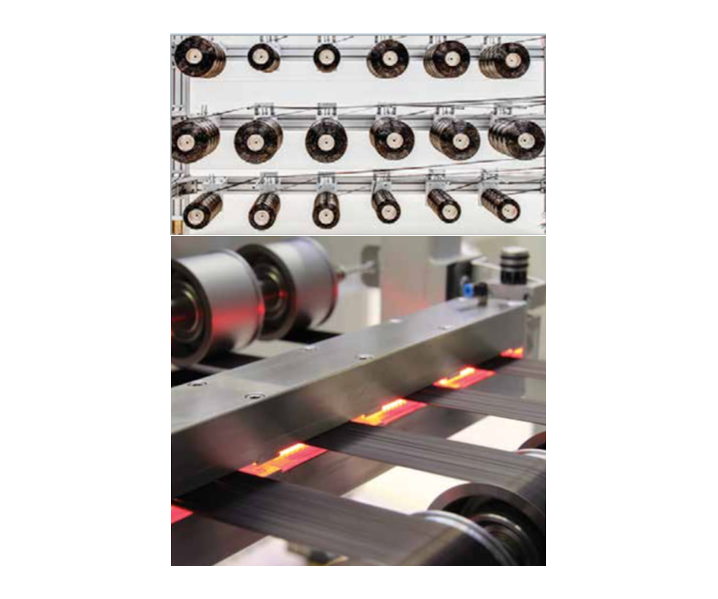
Schritt 1: Zoltek 50K Kohlefaserkabel werden dem Voith Roving Applicator (VRA) zugeführt, wo es zuerst verteilt, dann mit einem Bindemittel auf Epoxidbasis beschichtet und anschließend IR-erhitzt wird, um das Bindemittel teilweise zu schmelzen.
„Das ist ein kontinuierlicher Prozess, der vollständig automatisiert ist“, sagt Ufer. „Wenn es aus irgendeinem Grund notwendig ist, die Linie zu stoppen, reagiert das Gerät automatisch. So wird beispielsweise die IR-Heizung sofort ausgeschaltet und eingefahren, um eine Beschädigung des Bandes durch Überhitzung zu vermeiden. Es gibt Hunderte solcher Details in der Ausrüstung und der digitalen Steuerung, die diese Technologie ermöglicht.“
Schritt 2: Das Spread-Tow-Band wird dann konsolidiert, während es unter Spannung durch mehrere Rollen läuft.
Nach dem Auftragen des Bindemittels wird die Bandkonsolidierung erreicht, indem es unter Spannung durch mehrere Walzen läuft (Schritt 2). Ufer erklärt, dass dies auch einen Puffer für die Leitung einbaut. „Wir haben eine Einheit, die den kontinuierlichen Zugfluss der Faser unterbricht und einen Übergang zum Pulsformat des Bandschneid- und -platziermechanismus ermöglicht.“ Dieser Gantry-basierte Mechanismus schneidet die Bänder auf maßgeschneiderte Längen und legt sie in vorgegebenen Winkeln von 0-360° auf einen Drehtisch (Schritt 3). Jeder Tailored Stack, bestehend aus 6 bis 19 Lagen Tape, hat eine Dicke von jeweils 1,5 bis 3,7 mm.
Schritt 3: Der VRA schneidet dann das Band und legt bis zu vier Stücke gleichzeitig auf einen Drehtisch, wobei sowohl die Bandlänge als auch der Ausrichtungswinkel innerhalb des Laminatstapels angepasst werden (z. B. 45°/90°/30°).
Voith hat vier VRA-Linien installiert (siehe Eröffnungsfoto), und obwohl jede bis zu vier 50 mm breite Bänder gleichzeitig aufträgt, weist Ufer darauf hin, dass „die Linien einen modularen Ansatz haben, sodass sie 10 oder mehr Bänder gleichzeitig aufbringen können Zeit. Es hängt von der Teilegröße und der Produktionsrate ab.“
Zur Automatisierung gehört die Qualitätsprüfung. Scans der Bänder und Vorformlinge werden mit einem Zurückweisungsalgorithmus verglichen. „Die 100-prozentige Abtastung des Tapes durch den VRA gewährleistet die richtige Faserverteilung für die gesamte Produktionslinie“, erklärt Ufer. „Außerdem setzen wir Thermografie und Lasersensoren ein, um die Preforms an ausgewiesenen Stellen zu prüfen.“ Der VRA kann dann auf alle erkannten Probleme reagieren. „Wenn ein Band nicht richtig ist“, sagt er, „schneidet der VRA die mangelhafte Länge aus und produziert ein anderes, um es zu ersetzen.“ Zur Rückverfolgbarkeit wird ein QR-Code auf dem fertigen Preform platziert. (QR-Codes werden gegenüber Radio Frequency Identification (RFID)-Tags bevorzugt, da sie angeblich dem Harzinjektionsprozess besser standhalten.)
Formen, Formen und Montage
Der 2D-Stack verlässt den VRA und wird in den Umform-, Form- und Montagebereich der Produktionslinie transportiert. Die erste Presse, in die es eingesetzt wird, geliefert vom Composites-Automatisierungsspezialisten FILL (Gurten, Österreich), formt den 2D-Bandstapel mit Hitze und Druck zu einem 3D-Preform (Schritt 4). Ufer erklärt, dass die Presse aufgrund der unterschiedlichen Dicke und Form des Vorformlings den aufgebrachten Druck anpassen kann, während sie einzelne Bereiche des im Umformwerkzeug eingespannten Vorformlings stanzt. ALPEX Technologies (Mils bei Hall, Österreich) fertigte die Matched-Steel-RTM-Formen nach einem Entwurf von Voith Composites. „Wir haben den Werkzeug- und Pressprozess virtuell entwickelt“, sagt Ufer. „Obwohl keine eigentliche Testschleife erforderlich war, haben wir die Simulationsmodelle vor der Bearbeitung des A8 an anderen Formen und Teilen validiert und verifiziert Produktionswerkzeuge für die Rückwand. Diese Simulation des Formgebungsprozesses lief direkt in die reale Produktion ein und half dabei, die Optimierung zu beschleunigen.“
Schritt 4 :Der Bandstapel wird in eine Presse transportiert, wo er in die endgültige 3D-Teilform geformt wird.
Die Presse hält einige Sekunden, um das Pulverbindemittel zu reagieren und die Form zu fixieren, was zu einer stabilen Vorform führt, die dem Faserwaschen während der Harzinjektion widerstehen kann. „Die Binderpartikel dienen auch dazu, die Fasern auseinander zu halten, um den Harzfluss während der RTM zu verbessern“, bemerkt Ufer. „Dies ist hilfreich, da es keine Nähte in der Vorform gibt, die den Harzfluss unterstützen, sodass diese Binderpartikel als Mikroströmungskanäle wirken.“
Der geformte Vorformling wird anschließend per Roboter in eine CNC-Zelle der EiMa Maschinenbau GmbH (Frickenhausen, Deutschland) überführt, wo ein Ultraschallmesser die äußere Endkontur besäumt. Anschließend wird es robotisch in eine RTM-Presse (Schritt 5) von ENGEL (Schwertberg, Österreich) eingelegt. Alle Roboter der Linie werden von KUKA Robotics (Augsburg, Deutschland) geliefert.
Schritt 5: Der geformte Vorformling wird in eine 350-kN-Presse eingelegt und mit Ultra-RTM geformt.
Das RTM-Verfahren zum Formen des A8 Rückwand ist die gleiche, die im Audi Leichtbauzentrum für den bisherigen R8 entwickelt wurde Rückwand, als Ultra-RTM bezeichnet. Es ermöglicht das Formen großer Teile durch schnelles Spritzen bei niedrigem Druck. Im Vergleich zu den für HP-RTM typischen 140 bar ist der In-Mold Resin-Injection-Druck beim Ultra-RTM des Audi A8 Rückwand <15 bar, noch weniger als beim R8 . Dadurch werden statt 2.500 kN Presskraft nur noch 350 kN benötigt. Daher kann eine kleinere, kostengünstigere Presse verwendet werden, um qualitativ hochwertige Teile mit hohem Faservolumen herzustellen.
Das Epoxidharz VORAFORCE 5300, ein Dreikomponentensystem inklusive Entformung, härtet in 90-120 Sekunden bei 120°C aus und hat eine Verarbeitungsviskosität von 20 cps. Für den A8 Rückwand wird ein 1,3 kg schwerer Harzschrot in den Preform eingespritzt, gefolgt von einer 120-sekündigen Aushärtung.
Das ausgehärtete Teil wird robotergesteuert entformt und zur Bearbeitung von Ausschnitten in eine geschlossene CNC-Fräszelle geladen. Anschließend wird das Frästeil in einen Waschautomaten gegeben, um Reste von CFK-Staub zu entfernen.
Die gewaschene Rückwand wird in eine mit zwei Robotern ausgestattete Montagezelle überführt. Der erste Roboter legt das Formteil in einen Nietautomaten, der die beim Nieten aufgebrachte Kraft dokumentiert. Dies ist Teil der Fertigungsintelligenz, die in den Gesamtprozess integriert ist, und wird dem digitalen Verarbeitungsprotokoll jedes Teils (d. h. dem digitalen Faden) hinzugefügt. Anschließend wird das Teil in den Bonding-Bereich bewegt und ein zweiter Roboter bereitet die Bonding-Bereiche mit einem automatisierten Lösungsmittelwisch vor. Derselbe Roboter trägt dann den schnell härtenden Zweikomponenten-Polyurethan-Strukturklebstoff Dow BETAFORCE 9050M auf (Schritt 6), der mit dem Dreikomponenten-Epoxidharz kompatibel ist. Das Teil wird als nächstes für einen kurzen Klebstoffhärtungszyklus in einen Ofen gelegt.
Schritt 6: BETAFORCE Polyurethan-Klebstoff wird für verklebte Anbauteile roboterartig aufgetragen und dann in einem kurzen Ofenzyklus ausgehärtet.
Diese Produktionslinie hält eine 5-Minuten-Zykluszeit für das fertige Teil ein und der aktuelle Bedarf an Teilen kann in einer oder zwei 8-Stunden-Schichten gedeckt werden. Ein 3D-Laserscanning-Gerät wird regelmäßig verwendet, um die 3D-Form und die Abmessungen des Teils zu überprüfen. Fertige Teile werden dann für den Versand an den Audi A8 vorbereitet Endmontagelinie in Neckersalm, Deutschland, ca. 3 Autostunden entfernt (Schritt 7).
Schritt 7: Das fertige Teil wird dann für den Versand an die Audi A8 Endmontagelinie vorbereitet.
Direkte Glasfaserplatzierung =zukünftige Flexibilität
Bei all den getätigten Investitionen ist es überraschend zu erfahren, dass Voith Composites dieses Geschäft nicht zugesichert hat, sondern das Unternehmen die Entwicklung abgeschlossen hat und sich dann an einem wettbewerbsorientierten Ausschreibungsverfahren beteiligt hat, um die Produktion zu gewinnen. „Wir konnten die von Audi definierten Teilekostenziele sowie die Qualitäts- und Teileleistungsanforderungen erfüllen“, sagt Ufer. Dies war keine leichte Aufgabe, wenn man bedenkt, dass sich einige Unternehmen um das Programm bewarben.
Voith Composites hat mehrere Teile seines Verfahrens patentieren lassen. „Der VRA hat die Industrialisierung durch Direct Fiber Placement [DFP] von Bändern demonstriert, die durch ein hochoptimiertes Layup sowohl Ausschuss als auch Materialverbrauch reduziert“, sagt Ufer. Es verwendet auch die kostengünstigsten Materialien – unbehandelte Schwerkabel und Pulverbindemittel. Sein Verfahren der zweiten Generation ersetzt Pulverbindemittel durch direktes Auftragen von Harz, wodurch mehr Prozessschritte entfallen. Das Unternehmen hat jedoch andere DFP-Verfahren entwickelt, darunter den Voith Longfiber Preformer und Voith Prepreg Winding.
„Wir setzen neue Maßstäbe bei Kohlefaserbauteilen für die automobile Großserienfertigung“, sagt Voith Composites-Geschäftsführer Dr. Lars Herbeck. „Die von uns aufgebaute Smart Factory hebt die automatisierte Fertigung von CFK-Bauteilen auf ein neues Effizienz- und Flexibilitätsniveau, das nahezu jede Form sowie individuelle Losgrößen umfasst.“ Dies ist in der Tat, wohin die Branche steuert.
Harz
- Warum PEEK-Material an der Spitze seiner Klasse steht
- Kohlefaserverstärkter Kunststoff (CFK)
- K 2019:Materials Matter auf der Messe
- Arkema startet „Start-Up Connect“-Programm
- Polykemi investiert in eine eigene US-amerikanische Compoundieranlage
- Polykemi plant Compounding-Produktion auf drei Kontinenten
- Klebeband aus thermoplastischem Thermoplast auf PPS-Basis
- Herausforderungen des lasergestützten Wickelns von thermoplastischen Verbundwerkstoffen
- Split-Tow-Kohlefaser steigert die SMC-Leistung
- CFK-Modul spart Gewicht beim Raketendesign