Stellen Sie mit dieser Checkliste sicher, dass Spritzgusskonstruktionen produktionsreif sind
Der Spritzguss ermöglicht die Massenproduktion identischer Teile zu einem niedrigen Preis pro Teil. Der Prozess beinhaltet das Einspritzen von geschmolzenem Material in haltbare Metallformen durch eine unter Druck stehende Düse, das Auswerfen des Teils, sobald das Material ausgehärtet ist, und das Wiederholen. Eine breite Palette von Alltagsgegenständen, darunter Wasserflaschen, Plastikspielzeug und Elektronikgehäuse, werden im Spritzgussverfahren hergestellt. Während Thermoplaste und Duroplaste die am häufigsten beim Spritzgießen verwendeten Materialien sind, kann auch Metall spritzgegossen werden.
Wenn Sie ein Teil im Spritzgussverfahren herstellen, müssen Sie eine Reihe von Variablen berücksichtigen, die sich auf die Qualität und Funktionalität des Endprodukts auswirken. Es gibt viele Möglichkeiten, wie ein Spritzgussteil versagen kann – einschließlich Fließlinien, Einfallstellen und Verzug – aber Sie können die meisten Probleme vermeiden, indem Sie einige wichtige Konstruktionsprinzipien befolgen.
Hier bei Fast Radius arbeiten wir jeden Tag mit Kunden an ihren Spritzgussteilen. Ingenieure kommen oft mit großartigen Teiledesigns zu uns, die angepasst werden müssen, bevor sie effektiv hergestellt werden können. Unsere Design-for-Manufacturing-Experten (DFM) haben Tausende von Teiledesigns bewertet und angepasst und die häufigsten Probleme, die sie sehen, identifiziert und zusammengestellt. Das Beheben dieser häufigen Fehler in Ihrem Design kann kostspielige Fehler verhindern und viel Zeit bei Designüberarbeitungen sparen.
Bevor Sie Ihr Teiledesign zum Spritzgießen einreichen, prüfen Sie es anhand dieser Liste von Designregeln:
Verwenden Sie geeignete Formschrägen
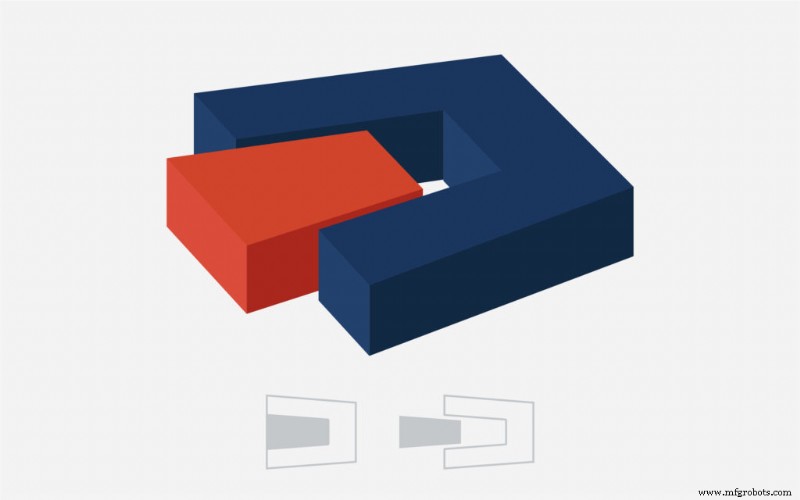
1,5–2 Grad Formschräge sind in der Regel ein sicheres Minimum für die meisten Teile.
Entformungswinkel beziehen sich auf die sanfte Verjüngung, die den Oberflächen eines spritzgegossenen Teils hinzugefügt wird, die mit der Zugrichtung ausgerichtet sind, wodurch das Teil aus der Form entfernt werden kann, ohne durch Reibung oder Sog beschädigt zu werden.
Der erforderliche Entformungswinkel für ein Teil hängt von einigen Faktoren ab, einschließlich der Wandstärke, der Schrumpfrate des Teilematerials, der Ziehtiefe und ob das Teil während der Nachbearbeitung oberflächenveredelt oder strukturiert werden muss. Während die durchschnittliche Formschräge um 1 Grad für jeden zusätzlichen Zoll an Teiletiefe zunehmen sollte, sind 1,5–2 Grad Formschräge normalerweise ein sicheres Minimum für die meisten Teile.
Halten Sie nach Möglichkeit eine gleichmäßige Wandstärke ein
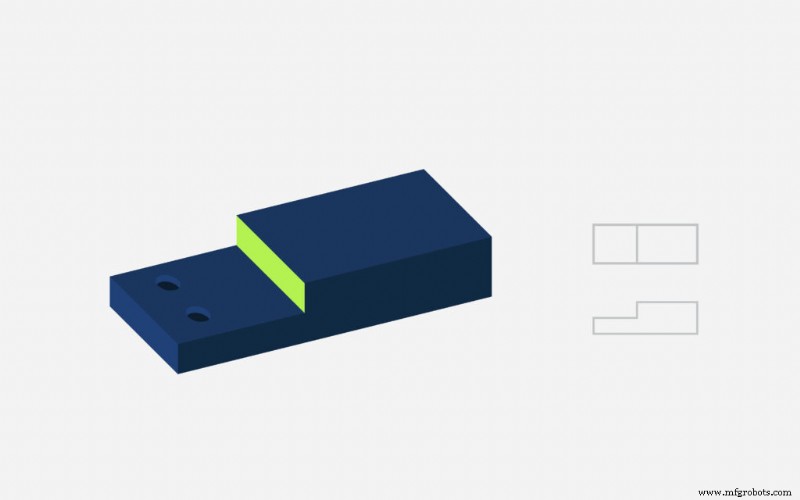
Spritzgussteile sollten möglichst über das gesamte Bauteil eine gleichmäßige Wandstärke aufweisen. Schwankungen in der Wandstärke können dazu führen, dass das eingespritzte Material unterschiedlich schnell abkühlt, was zu Einfallstellen, Hohlräumen und Verzug führen kann.
Im Allgemeinen sind Wandstärken zwischen 1,2 mm und 3 mm ideal (obwohl je nach Material mit einigen Abweichungen zu rechnen ist). Die Wandstärke sollte fast immer unter 5 mm bleiben, da dickere Wände die Produktionszykluszeiten verlängern und sich auch negativ auf die mechanischen Eigenschaften des Teils auswirken können.
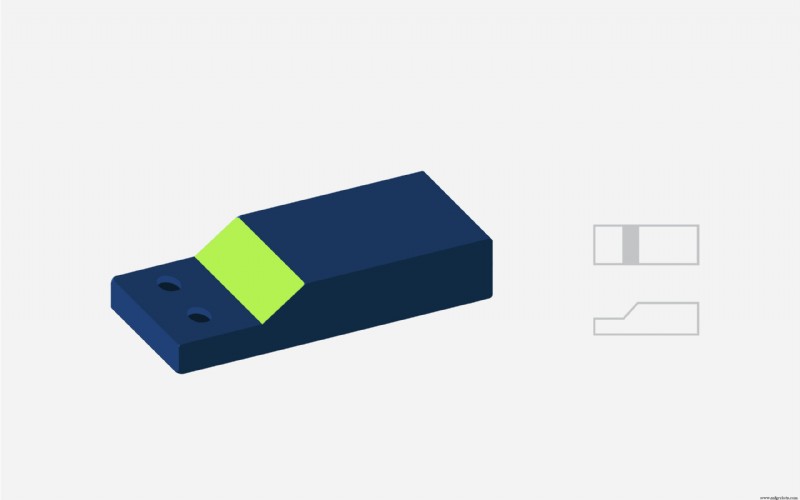
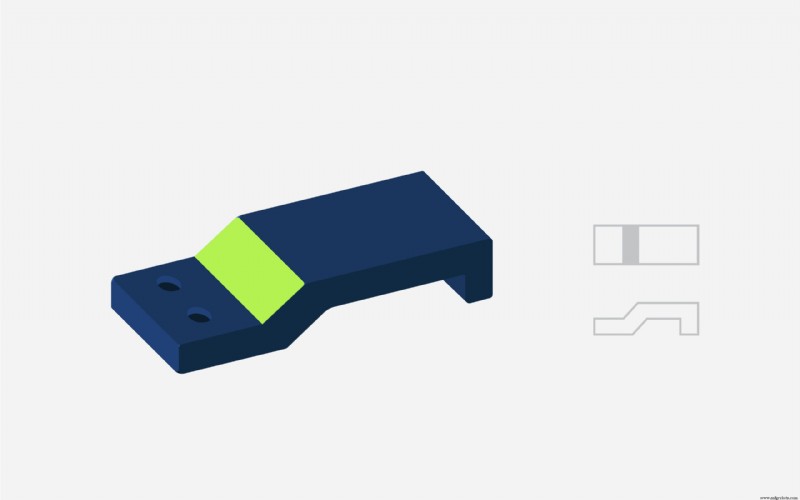
Wenn ein Teil unterschiedliche Wandstärken erfordert, sollten Sie den Übergang zwischen den Abschnitten so fließend wie möglich gestalten. Sie können dies tun, indem Sie Fasen (schräge Ecken oder Kanten) oder Verrundungen (abgerundete Ecken oder Kanten) in das Teiledesign integrieren, die dazu beitragen, dass der Schuss aus geschmolzenem Kunststoff die Form vollständig ausfüllt, gründlich und gleichmäßig abkühlt und ein Verziehen oder Nichtverziehen verhindert -einheitliche Schrumpfung.
Als allgemeine Regel gilt, dass die Länge des Übergangs zwischen Abschnitten mit unterschiedlicher Wandstärke das 3-fache der Wandstärkenänderung betragen sollte (z. B. wenn die Wandstärke um 1 mm abnimmt, sollte der Übergang über 3 mm erfolgen).
Unterschnitte vermeiden
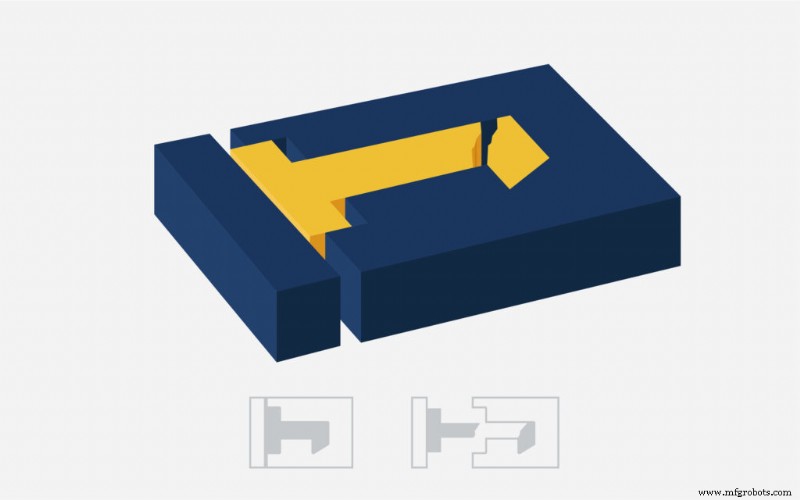
Hinterschnitte sind vertiefte oder überhängende Oberflächen oder Merkmale – wie Gewinde, Rillen oder Schnappverbindungen – die verhindern, dass ein Teil mit einem einzigen, unidirektionalen Zug ohne Beschädigung aus der Form ausgeworfen wird. Es ist möglich, Hinterschneidungen zu vermeiden, indem Sie Merkmale parallel zur Ziehlinie ausrichten oder Aktionen in Ihr Formdesign integrieren.
Raut scharfe Kanten und Ecken ab
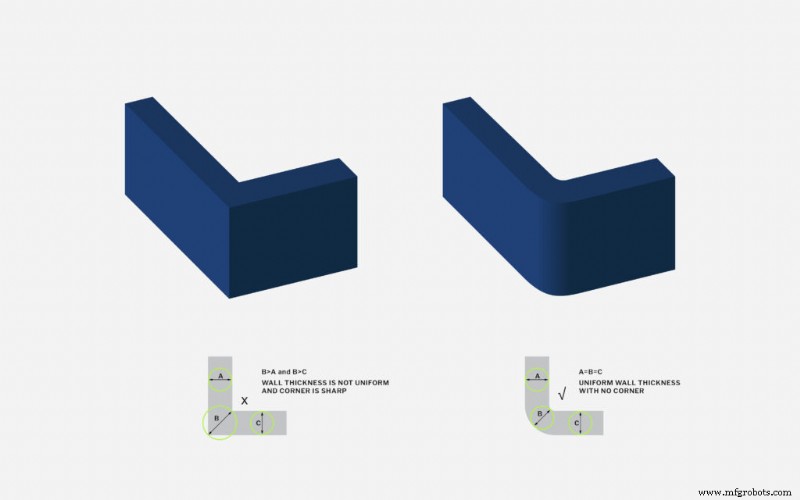
Designer und Ingenieure sollten sich nach Möglichkeit für runde Merkmale anstelle von scharfen Kanten und Ecken entscheiden. Kanten erfordern zusätzlichen Druck zum Füllen, was es schwieriger macht, dass ein Schuss effizient und gleichmäßig in die Form fließt. Scharfe Kanten neigen auch dazu, beim Auswerfen an der Form zu haften, was das Risiko von Teilebeschädigungen und Defekten erhöht. Sie können diese beiden Probleme mit abgerundeten Innen- und Außenecken vermeiden.
Innenecken oder solche, an denen Teilwände auf den Boden treffen, sollten einen Radius von mindestens 50 % der angrenzenden Wandstärke haben. Außenecken oder solche an der Oberseite von Teilwänden sollten einen Radius von 150 % der angrenzenden Wand haben, damit der Kunststoff effizienter und effektiver fließen kann. Dies trägt auch dazu bei, Restspannung und Rissbildung zu minimieren.
Die Basis aller vertikalen Merkmale innerhalb eines Teils (z. B. Vorsprünge, Rippen oder Schnappverbindungen) muss ebenfalls gerundet werden. Bossenradien sollten 25 % der angrenzenden Wand betragen, mit einem Mindestradius von 0,015 Zoll (oder 0,381 mm).
Platzieren Sie Trennlinien strategisch
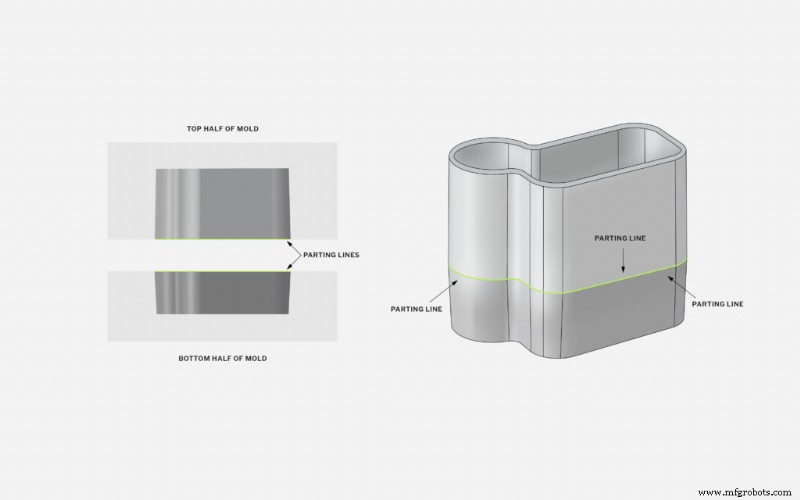
An der Stelle, an der sich die beiden Hälften einer Form treffen, erscheint eine physische Markierung, die als Trennlinie bekannt ist. In vielen Fällen sind Trennlinien leicht zu sehen und zu fühlen, aber es ist mehr als ein ästhetisches Problem. Die Platzierung der Trennlinie bestimmt, wie sich die Form öffnet (und damit die Richtung, in der Sie den Merkmalen des Teils Formschräge hinzufügen müssen), und sie kann sowohl die Kosten für die Formwerkzeuge als auch die erforderliche Nachbearbeitung beeinflussen.
Sie können das Aussehen und die Funktionalität eines Teils oft verbessern, indem Sie den Scheitel entlang einer Kante statt auf einer ebenen Fläche platzieren. Dies trägt dazu bei, die Naht zu verbergen, und verringert auch die Wahrscheinlichkeit von Graten (übermäßiges Material an den Stellen, an denen die Form zusammenkommt).
Berücksichtigen Sie die Platzierung des Auswerferstifts
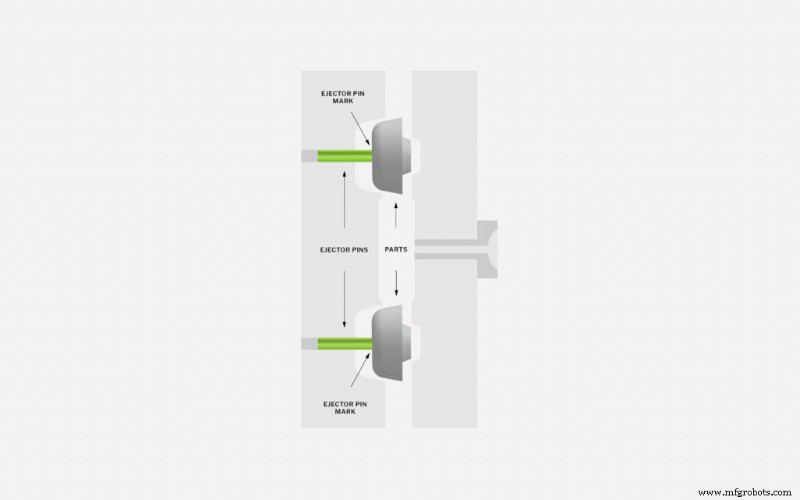
Um richtig zu funktionieren, benötigen Auswerferstifte flache Oberflächen oder Pads, die senkrecht zur Richtung der Stiftbewegung angeordnet sind. Die Platzierung und Anzahl der Stifte sollte von der Teileform, den Formschrägenwinkeln, der Seitenwandtextur und der Wandtiefe bestimmt werden – all dies beeinflusst, wie ein Teil an den Formwänden haftet.
Die Materialwahl sollte auch bei der Platzierung oder Größe der Stifte berücksichtigt werden. Klebrigere Harze erfordern zum Beispiel tendenziell mehr Kraft zum Ausstoßen. Ebenso benötigen weichere Kunststoffe wahrscheinlich entweder eine größere Anzahl von Stiften oder breitere Stifte, um die Auswurfkraft effektiv zu verteilen und eine Beschädigung des Teils zu vermeiden.
Optimieren Sie die Größe der Stützrippen
Rippen werden häufig verwendet, um Teilwände in Situationen zu verstärken, in denen zwei Teilwände in einem 90-Grad-Winkel aufeinander treffen oder wenn die Länge eines bestimmten Abschnitts durch die Wandstärke des Abschnitts geschwächt ist.
Es ist wichtig zu beachten, dass dickere Rippen nicht unbedingt eine bessere Unterstützung bedeuten – tatsächlich führen zu dicke Rippen oft zu Einfallstellen. Die Basisdicke der Stützrippen sollte maximal zwei Drittel der Dicke der angrenzenden Wand betragen.
Achten Sie auf die Wandstärke der Form
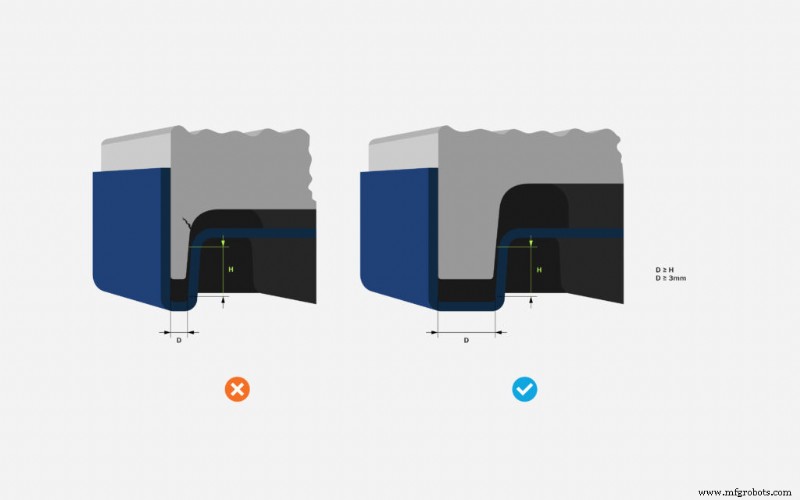
Die Dicke der Wände der Form ist ein weiterer wichtiger Aspekt – und einer, der hauptsächlich durch den Abstand zwischen den Teilemerkmalen bestimmt wird. Stellen Sie sicher, dass vertikale Merkmale wie Rippen und Vorsprünge nicht zu nahe beieinander, an Trennwänden oder dünnen Bereichen liegen, da dies den Kühlprozess erschwert.
Die Wandstärke der Form kann sich auch auf die Werkzeugkosten auswirken. Die meisten Spritzgussformen werden durch CNC-Bearbeitung hergestellt, und dünnere Metallwände in der Form sind schwieriger richtig zu bearbeiten. Dünnere Wände führen auch zu kürzeren Lebenszyklen der Form.
Während die minimal zulässige Formwandstärke von den physikalischen und mechanischen Eigenschaften des Teilematerials bestimmt wird, ist ein Abstand von 3 mm zwischen Teileelementen im Allgemeinen akzeptabel.
Spritzgussteile effizient und effektiv konstruieren
Konstruktionsfehler sind teuer. Ein Werkzeug neu zu schneiden, um einen Designfehler zu beheben, könnte Produktteams um Wochen zurückwerfen und Tausende von Dollar kosten. Ein guter Fertigungspartner hilft Ihnen, kostspielige Überarbeitungen mit DFM zu vermeiden, aber dieser Prozess trägt auch zu Ihrem Zeitplan bei. Wenn Sie Ihr Design auf die Probleme in diesem Leitfaden überprüfen, bevor Sie es an einen Fertigungspartner senden, können Sie schneller bessere Teile erhalten.
Beim Spritzgießen können viele Dinge schief gehen, daher müssen Sie einen Partner finden, dem Sie vertrauen können, um Ihre Teile richtig zu machen. Hier bei Fast Radius sind wir hier, um Ihnen die Arbeit zu erleichtern, und wir investieren in den Erfolg Ihres Projekts. Kontaktieren Sie uns noch heute, um mit Ihrem nächsten Spritzgussprojekt zu beginnen.
Um mehr über das Spritzgießen zu erfahren – von der Materialauswahl über die Unterschiede zwischen Formen mit einer Kavität und mehreren Kavitäten bis hin zur Nutzung des Verfahrens zur Herstellung von Gesichtsmasken zur Bekämpfung der Ausbreitung von COVID-19 – besuchen Sie das Lernzentrum von Fast Radius .
Sind Sie bereit, Ihre Teile mit Fast Radius herzustellen?
Starten Sie Ihr AngebotIndustrietechnik
- Spritzgießen mit PolyJet-Technologie
- Sechsachsige Roboter mit Spritzgusspressen verbinden
- Wie führende Spritzgussunternehmen mit digitalem Marketing mehr Chancen eröffnen
- Was sind Spritzgussfehler und wie lassen sie sich vermeiden:10 Fehler bei Kunststoffteilen
- Mikroformen mit Polyurethanen
- Was ist Reaktionsspritzguss
- Guss vs. Spritzguss
- Spritzguss vs. Reaktionsspritzguss (RIM)
- Gießformen vs. Reaktionsspritzgießen
- Was sind die Vorteile des Kunststoffspritzgusses?