Wie wird Schleppnetz verteilt?
Als der Feature-Artikel „The Spread of Spread Tow“ in Druck ging, war diese Side Story ganz anders und handelte hauptsächlich davon, wie viel wir nicht wissen darüber, wie Schleppseil verbreitet wird. Und dann stieß ich auf einen Artikel im AZL-Newsletter NewsLIGHT #7:ITA mit dem Titel „Neues Ultraschall-Spreizverfahren zur Verarbeitung von Bewehrungskabeln “. Es stellt sich heraus, dass das Institut für Textiltechnik (ITA) der RWTH Aachen (Aachen, Deutschland) seit 2011 Spread-Tow-Verfahren untersucht über die jeweiligen Einflussfaktoren und deren Optimierung“, sagt Wilko Happach, Leiter der Forschungsgruppe Tapes im ITA-Geschäftsbereich Composites. Als Ergebnis hat ITA eine neue Technologie entwickelt, die eineHochgeschwindigkeitsproduktion ermöglicht — bis zu 100 m/min — gespreiztes Schleppband mit viel geringerer Breitenschwankung dank integrierter Steuerung. ITA nennt diese Technologie AutoTow .
Verstehen von Spread Tow-Techniken
ITA begann seine Forschungen auf der Suche nach Klebeband. „Wir hatten gesehen, dass Gewebe und Gelege erheblichen Verschnitt verursachten und zudem keine optimierten Designs zuließen“, erinnert sich Happach. „Da die Fasern nicht alle in Lastrichtung aufgebracht werden, werden Fasern verschwendet.“ Daher begann sein Team, sich mit der automatischen Klebebandverlegung zu befassen , aber es fehlte damals sowohl an Bandversorgung als auch an Wissen, sagt Happach. „Also haben wir unsere eigenen gemacht und uns entschieden, Trockenfaser-Bindebänder zu entwickeln Erste." Dazu mussten sie jedoch erst die Verbreitung verstehen.
Happach beschreibt drei grundlegende Methoden zum Verteilen von Roving in breitere, dünnere Bänder:
- Fasern mit hoher Spannung über Spreizstangen ziehen.
- Luftverteilung mit einer Schlitzdüse.
- Anwenden von Ultraschall oder anderen Vibrationen auf Fasern.
Technologien und Prozessparameter verbreiten
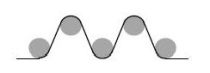
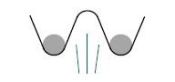
- Anzahl Spreizbalken (3-5)
- Umschlingungswinkel um Stäbe (90-180°)
- Bartemperatur
(22-150 °C) - Stangenoberfläche (poliert, TopoCrom-beschichtet oder Bechem-beschichtet)
- Roving-Vorspannung (bis zu 2.000 CentiNewton)
- Luftdruck
(0-6 bar) - Luftstromwinkel (0-180°)
- Anzahl aktiver Streubalken (3-5)
- Umschlingungswinkel um Stäbe (1-120°)
- Ultraschallfrequenz (30 kHz)
- Amplitudenintensität
(50-100 %) - Roving-Vorspannung (bis zu 2.000 CentiNewton)
QUELLE:ITA Tape Center, RWTH Aachen.
Spreizleisten scheint die älteste und grundlegendste Technik zu sein, die in einem 2001 vom Kohlefaserhersteller Zoltek eingereichten Patent verwendet wurde. Happach weist darauf hin, dass auch der Ausrüster Karl Mayer bei seinen Tape- und Spread Tow-Gewebemaschinen auf Spreizstangen gesetzt hat. „Das Problem bei dieser Methode ist, dass die Produktionsgeschwindigkeit auf 25 m/min begrenzt wird“, sagt er. „Wenn Sie versuchen, höher zu gehen, ist die Reibung zu hoch und beschädigt die Roving-Filamente. Auch das Balkenstreuen ist in der maximalen Streubreite begrenzt. Sie können den Roving höchstens auf das Dreifache seiner ursprünglichen Breite ausbreiten.“
Luftausbreitung , sagt Happach, kommt zum Einsatz, wenn maximale Streubreite bei geringerem Flächengewicht gewünscht wird. „Der Luftstrom trennt die Filamente und ermöglicht eine Spreizung bis zum 6-7-fachen der anfänglichen Roving-Breite mit viel geringeren Filamentschäden, da weniger Reibung auftritt“, erklärt er. „Bei hoher Spannung wird die Faser nicht über die Stäbe gezogen.“
Es gibt jedoch eine Einschränkung in Abhängigkeit von der auf die Glas- oder Kohlefaser aufgebrachten Größe. Happach erklärt:„Fasern, die für Epoxidharze und andere duroplastische Harze geeignet sind, können klebrig sein, sodass der Luftverteilungsprozess die Filamente nicht leicht trennen kann.“ In diesem Fall ist möglicherweise ein Vorprozess erforderlich, um die Größe etwas aufzubrechen. Mit thermoplastischen Matrixharzen kompatible Schlichte, die ebenfalls thermoplastisch ist, ist jedoch überhaupt nicht klebrig und verhält sich fast wie eine ungeschlichtete Faser. Mit anderen Worten, es gibt keine Adhäsion zwischen den Filamenten. „Dies ist also leicht zu verteilen, aber schwierig zu handhaben, da es dazu neigt, auseinander zu fallen“, bemerkt Happach.
Ultraschallausbreitung verwendet das gleiche Grundprinzip wie Spreizstangen, jedoch mit halbzylinderförmigen Sonotroden, die, so Happach, „sehr viel Energie übertragen. Das Roving umschlingt die Sonotroden und durch die Anwendung von Ultraschall vibrieren die Filamente und setzen sich auf der Oberfläche ab und breiten sich aus.“ Diese Technik kann zu höheren Ausbreitungsraten führen (d. h. größere Faserkabel werden in sehr dünne, breite Bänder verteilt), können jedoch nicht mit Glasfasern oder Kohlefasern auf Pechbasis verwendet werden, da sie zu spröde sind und brechen.
„Sie können auch mechanisch induzierte Vibrationen mit niedrigerer Frequenz verwenden“, sagt Happach, „und Wärme kann verwendet werden, um die Fasergröße zu erweichen, sodass sich die Filamente leichter bewegen können.“
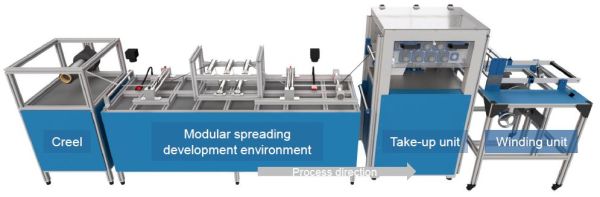
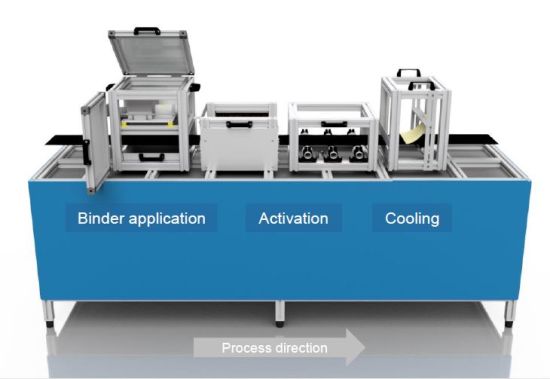
AutoTow
ITA hat AutoTow entwickelt, um die Probleme zu überwinden mit diesen grundlegenden Verbreitungsmethoden. Happach merkt an, dass das Tape Center hauptsächlich mit 24K, 50K und 60K Schleppseil arbeitet (er bemerkt, dass es von Mitsubishi ist), weil die Ausbreitungseffekte am höchsten sind. „Wir erreichen höhere Produktionsgeschwindigkeiten von bis zu 100 m/min, weil wir rotieren können die einzelnen Spreizbalken mit bis zu 80 m/min ," er erklärt. „Die relative Geschwindigkeit beträgt also 20 m/min, was gut ist, um ohne Filamentschaden zu spreizen.“
Happach weist darauf hin, dass das Input-Roving/Tow Variationen aufweist , variiert auch die Breite des ausgegebenen gestreuten Kabels. „Bei Prepreg-Bändern schneiden die Lieferanten einfach die Kanten ab. Aber wir haben mit trockenem, gebundenem Klebeband angefangen, das viel weniger Harz enthält, daher ist es zu schwer, die Kanten zu schneiden.“ Das Team von Happach erkannte, dass es ein besseres Mittel zur Steuerung der Streubreite brauchte.
„Wir verwenden Kameras um die Breite beim Ein- und Ausfahren des Streuers zu messen“, erklärt er. „Ein Algorithmus verwendet diese Breitenmessung, die Prozessgeschwindigkeit und bestimmte bekannte Faktoren für jedes Material, um die Geschwindigkeit zu berechnen und zu steuern von jedem der 5 rotierenden Balken um die Bandbreite stufenlos einzustellen. Wir können die Abweichung auf weniger als 1 Millimeter reduzieren .”
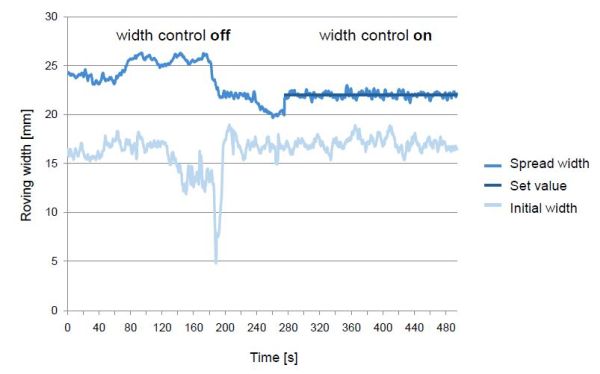
Integrierte AutoTow-Breitenkontrolle mit Kameramessung, um die Breitenabweichung auf weniger als 1 mm zu reduzieren. QUELLE:ITA Tape Center, RWTH Aachen.
„Wir können auch den Umschlingungswinkel anpassen des Rovings um jeden Spreizbalken“, fährt Happach fort, „aber nicht in Echtzeit.“ Dies ist also eher eine Kalibrierung für jeden Produktionslauf. „Alles andere wird inline erledigt “, behauptet er. „Wenn Sie die Streubreite von 25 mm auf 30 mm erhöhen möchten, geben Sie einfach diese Zahl ein und innerhalb weniger Sekunden es wird sich während der Produktion ändern , und bei hoher Geschwindigkeit sogar 100 m/min.“
Zukünftige Entwicklung
Das Ziel des ITA Tape Centers ist die vollständige Tape-Prozesskette um die Entwicklung der Industrie zu unterstützen. „Unser Ziel ist es, Industriepartner zu gewinnen, um für sie neue Lösungen zu entwickeln“, erklärt Happach. „Wir sind dabei, eine Bandproduktionslinie und eine Teileproduktionslinie zu bauen Auch. Wir wollen alle Operationen haben:Formatieren, Spreizen, Tape-Produktion, automatisiertes Tape-Legen und Aushärten.“ Er sagt, dass ITA niemals ein Maschinenlieferant oder Teilehersteller sein wird. „Wir wollen die Produktion von leichten Dünnschichtteilen erreichen, weil wir gesehen haben, dass die Schichten dünner sind , desto höher die mechanischen Eigenschaften . Da wir nun trockene, gebundene Bänder mit hohen Geschwindigkeiten und einem hohen Qualitätsniveau produzieren können, ist es unser Ziel, das Flächengewicht zu senken und neben der Produktion von Thermoplast und Duroplast-Prepreg Bänder.“
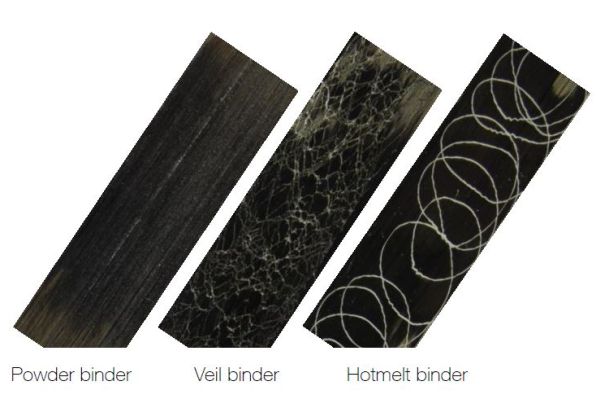
Das ITA Tape Center hat verschiedene duroplastische und thermoplastisch kompatible Bindertechnologien erforscht.
So wie das ITA Tape Center den Produktionsraum für Spread-Tow-Prozesse und deren Parameter definiert hat, hat es auch bedeutende Kenntnisse über den Einfluss der Fasergröße . entwickelt und Band Binder Technologie. „Wir haben Lieferanten, die Rezepte unterschiedlicher Größe testen um zu sehen, was sich am besten für die Verbreitung eignet“, sagt Happach.
Bei Bindemitteln sei der wichtigste Faktor die Verträglichkeit mit dem Matrixharz. „Ein duroplastisches Bindemittel erreicht die höchsten Eigenschaften für eine duroplastische Matrix.“ Ebenso sollte das Bindemittel für eine thermoplastische Matrix thermoplastisch sein und kann unter Verwendung von Pulver, Schleier oder Heißschmelz aufgetragen werden. Die beiden letzteren ermöglichen eine sehr schnelle Anwendung und verleihen dem Tape eine hohe Stabilität, aber Happach bemerkt den Schleier ergibt etwas höheren Bindemittelgehalt . Dies kann in Abhängigkeit von den Erwägungen des Teiledesigns und des Herstellungsprozesses erwünscht sein oder nicht. Die Forschung zu Binderparametern und deren Auswirkungen auf die Endteile wird fortgesetzt, während ITA seine gesamte Prozesskette ausbaut.
Harz
- Druck vs. CNC-Maschinen
- um das Brechen von Schaftfräsern zu stoppen
- zur Fehlerbehebung bei einem Notstopp einer CNC-Maschine
- Ist SFM in der Bearbeitung?
- Roboter mit künstlicher Intelligenz
- Industrielle Automatisierung
- Hyperspektralkameras
- Maschinelles Sehen
- Vernetzte Industrie 4.0 Aufruf
- Wie Industrie 4.0 die Cybersicherheit beeinflusst