Arevo im Jahr 2018:Industrialisierte Produktion von 3D-gedruckten Endlosfaserteilen
QUELLE für alle Bilder:Arevo.
CW deckt Arevo (Santa Clara, CA, USA) seit 2014 ab. Bekannt für die Verwendung von hochleistungsfähigen thermoplastischen Polymeren einschließlich Polyetheretherketon (PEEK), Polyaryletherketon (PAEK), Polyetherimid (PEI) und Polyphenylensulfid (PPS), war das Unternehmen auch führend in der Entwicklung von geschlossenen Robotersteuerungen für den 3D-Druck , ermöglicht die Platzierung der Faser in z-Richtung und entlang von 3D-Kurven. Das Unternehmen hat eine Liste mit neuen Entwicklungen, einschließlich seines Direct Energy Deposition (DED)-Verfahrens mit Laserheizung für eine 100-fache Steigerung der Produktionsgeschwindigkeit.
Neuer CEO und Finanzierung der B-Serie
Jim Miller kam vor drei Monaten als CEO zu Arevo. Er war ein früher Amazon-Mitarbeiter und war acht Jahre bei Google tätig, zuletzt als VP of Worldwide Operations. „Ich habe die meiste Zeit meiner Karriere damit verbracht, jungen Unternehmen beim Aufbau zu helfen“, sagt Miller Anwendungen.“
Das Unternehmen hat auch gerade seine Series-B-Finanzierung abgeschlossen und 12,5 Millionen US-Dollar aufgebracht, wobei Asahi Glass Co. (AGC, Tokio, Japan) die Runde anführt. „Sie sind der weltweit größte Autoglashersteller“, sagt Miller. „Sie haben gute Beziehungen zur Automobilindustrie und sehen große Chancen für neue Verbundtechnologien in den Automobilanwendungen .“ Weitere Investoren sind In-Q-Tel (Arlington, VA, USA), Sumitomo Corporation (Tokio, Japan) und Leslie Ventures. Miller sagt, dass Sumitomo , einer der größten japanischen Mischkonzerne und führend in der Öl- und Gastechnologie, ist daran interessiert, die 3D-Drucktechnologie von Arevo in seinen industriellen Aktivitäten einzusetzen , die Bau, Transport, Infrastruktur und Energie umfassen.
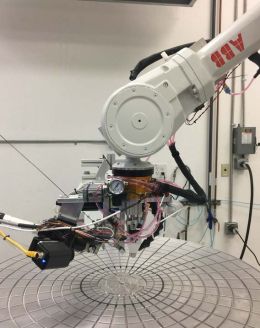
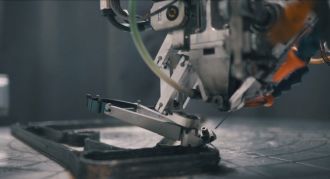
Die Direct Energy Deposition (DED)-Fertigungszellen von Arevo umfassen einen Industrieroboter, einen Druckkopf mit Laserheizung und eine rotierende Bauplattform. Der Druckkopf (rechts während des automatischen Schneidens und Wiederanfahrens zu sehen) umfasst Wärmemanagementgeräte und Bildverarbeitungssysteme für die In-Situ-Inspektion. QUELLE:Arevo.
Industrielle Produktion von thermoplastischen Verbundwerkstoffen
„Unsere neuen Fertigungszellen verwenden einen Standard-Industrieroboter , eine rotierende Build-Plattform und ein Laser zum Heizen “, erklärt Müller. „Wir nennen das Verfahren direkte Energiedeposition (DED).“ In der lasersicheren Fertigungszelle verfügt der Roboter über einen Druckkopf-Endeffektor mit proprietärem Thermomanagement Ausrüstung, kundenspezifische Elektronik und Vision-Systeme die eine Inspektion vor Ort ermöglichen . „Der Prozess ist meistens „hands-off/lights-out“, sagt Miller. „Diese neuen Zellen erzeugen eine mehr als 100-fache Steigerung der Produktionsgeschwindigkeit.“ Das technische Hauptbüro Wiener Mondesir ergänzt:„Der Laser liefert unbegrenzte Energie. Wir können das kontrollieren und schneller vorgehen, um industrielle Produktionsraten zu erreichen.“ Miller betont jedoch:„Es geht nicht darum, wie schnell sich Maschinen bewegen oder wie viel Material aufgebracht werden kann, denn wir bauen komplexe Strukturverbundwerkstoffe zu einem Viertel der Kosten von traditionellen Verbundwerkstoffen.“
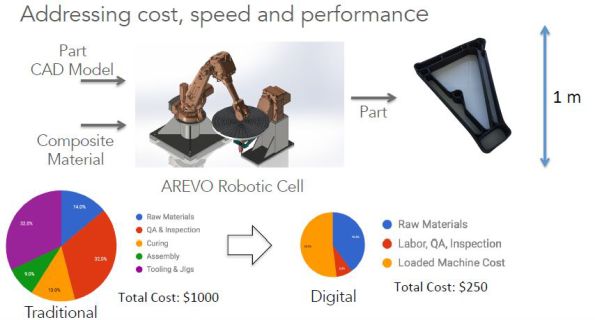
Herstellung von nicht-traditionellen Verbundwerkstoffen — Der DED-Prozess von Arevo ermöglicht Berichten zufolge die Herstellung von endlosfaserverstärkten thermoplastischen Verbundteilen zu einem Viertel der Kosten herkömmlicher Verbundwerkstoffe. (Berechnungen basieren auf einem 1 m großen Teil.)
„Wir verfolgen eine wirtschaftlich tragfähige Fertigung von großflächigen thermoplastischen Verbundteilen “, sagt Müller. „Wir nähern uns dieser Fertigung aus einer nicht-traditionellen Verbundsicht.“ Der Druckkopf verfügt jedoch über eine Verdichtungsfunktion und die Teile entsprechen immer noch den herkömmlichen Qualitätsanforderungen für Verbundwerkstoffe. „Wir können thermoplastische Verbundteile mit einem Hohlraumanteil von viel weniger als 1 % herstellen. “, bestätigt Müller. „Arevo verbessert seinen Prozess weiter und wird in naher Zukunft die mechanischen Eigenschaften für die Primärstrukturanforderungen erfüllen.“
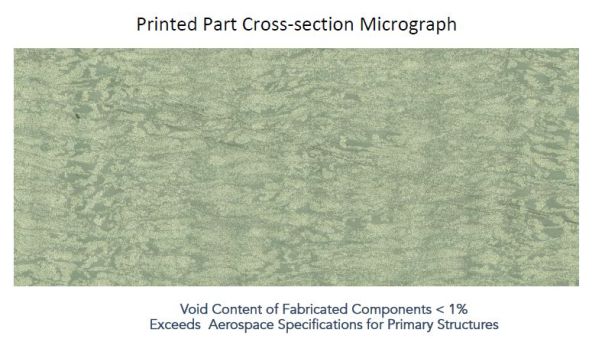
Pathfinder-Software
Ein Teil der „nicht-traditionellen Verbundwerkstoff-Perspektive“, auf die Miller oben Bezug nimmt, ist die Investition von Arevo in digitale Konstruktions- und Prozesssoftware. "Wir haben einen gesamten Workflow reduziert in die Software“, sagt Miller. „Es kann eine vollständige 3D-Analyse des Teils liefern und die optimierte Faserorientierung mithilfe von Additiver FEA entwickeln. (AFEA) Module. Ein Großteil unseres Erfolgs wird durch die Software- und Teilefertigungssimulation angetrieben. Wir führen das computergenerierte Design durch unsere Prozesssimulationssoftware und es zeigt die Prozessparameter einschließlich Temperaturen, Druckpfad, Verzug und Schrumpfung des gedruckten Materials , sowie Eigenspannungen. Dadurch können wir den Prozess wirklich verstehen und optimieren, um sehr hochwertige Teile zu produzieren.“
Er sagt, dass die Software von Arevo bezeugt, dass die Eigenschaften des hergestellten Teils innerhalb von 5% der simulierten Eigenschaften liegen, was Miller feststellt, dass dies im Wesentlichen auf die Fehlertoleranz der Testmessung zurückzuführen ist. Er fügt hinzu, dass Arevo auch maschinelles Lernen verwendet auf einzigartige Weise.
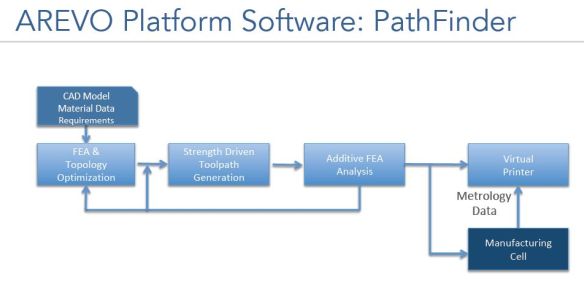
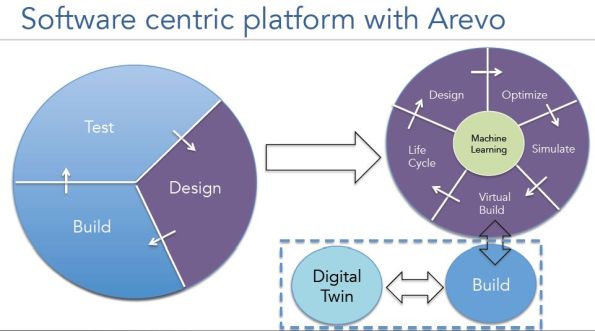
Die Möglichkeiten demonstrieren
Vor nur einem Monat präsentierte Arevo das seiner Meinung nach erste 3D-gedruckte Fahrrad der Welt beim Sea Otter Event (19.-22. April, Monterey, CA, USA). „Unser Ziel war es, zu demonstrieren, was unsere Software und unser Prozess leisten können“, erklärt Miller. "Wir haben mit dem in Colorado ansässigen Industriedesign-Unternehmen Studio West zusammengearbeitet, um das Design des Freischwinger-Fahrradrahmens zu entwickeln. .“ Er stellt fest, dass Studio West in der Fahrradbranche bekannt ist und mit einigen der Top-Hersteller zusammenarbeitet. „Sie haben uns anfangs ein sehr traditionelles Rahmendesign gegeben“, sagt Miller. „Aber wir wollten zeigen, wie Arevo Endlosfasern auf neuartige Weise einsetzen kann , also haben wir in verschiedenen Iterationen weiter mit ihnen zusammengearbeitet.“ Er fügt hinzu, dass das Arevo-Team die Steifigkeit und Biegung des Fahrradrahmens optimieren, aber auch die neuartige Ästhetik demonstrieren wollte, die mit seiner additiven Fertigungstechnologie möglich ist. „Am Ende haben wir ein sehr einzigartiges Fahrraddesign erhalten“, sagt Miller. Der Fahrradrahmen besteht aus kontinuierlichem 12K CF-Schleppzug und PEEK aber Miller sagt, dass es auch möglich ist, Nylon zu verwenden.
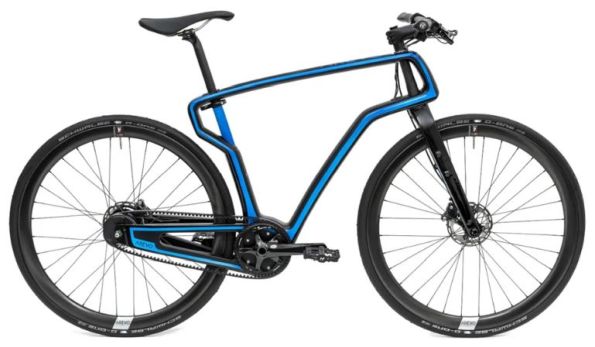
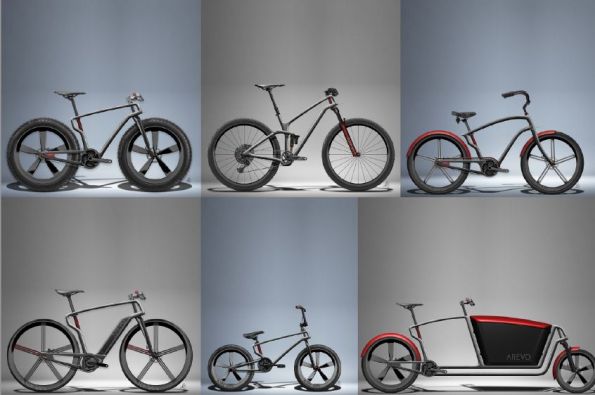
Der 3D-gedruckte CF-Composite-Fahrradrahmen von Arevo lässt sich problemlos an eine Vielzahl von Produkten für den Fahrradmarkt anpassen, darunter E-Bikes, Lastenräder, Liegeräder, 3-Räder, Kinderräder, Fatbikes, BMX, Cruiser und mehr. QUELLE:Arevo.
Fahrradrahmen sind nicht das einzige Beispiel dafür, was Arevo bei der additiven Fertigung von Verbundwerkstoffen erreicht. „Kleine Robotikunternehmen bauen Roboter mit großem Rahmen dass wir helfen, leicht zu machen zu einem Bruchteil der Kosten herkömmlicher Materialien“, sagt Mondesir. Arevo hebt auch Impeller- und Propelleranwendungen hervor , wobei gemeldete Vorteile umfassen:
- On-Demand-Produktion zur Verwaltung der Lagerkosten
- Höhere Effizienz gegenüber Metallbauweise
- Beständig gegenüber Serviceumgebungen
- Komplexe Geometrien sind mit der Legacy-Fertigung nicht möglich.
Weg zur industriellen Produktion
Miller sagt, dass das erste Ziel für 2018 darin besteht, acht DED-Fertigungszellen zu installieren und die Kapazitäten auszubauen, um seinen Produktionsrückstand zu bewältigen . „Wir werden dieses Jahr damit beginnen, Produkte in großen Mengen auszuliefern“, bestätigt er. Das Unternehmen arbeitet auch mit strategischen Kunden an Schlüsselanwendungen und Produktentwicklungen. „Unser dritter Schwerpunkt ist die weitere Verfeinerung des Abscheidungsprozesses um die Geschwindigkeit zu erhöhen bei gleichbleibender Qualität und Ausbeute“, sagt Miller. „Wir werden auch Teile mit verschiedenen Fasern und Kabelgrößen vorführen .“ Er sagt, dass der DED-Prozess variable Kabelform und -durchmesser bis zu 24K Kabel verarbeiten kann. „Wir können mit PEKK, PAEK, PPS und auch mit Glas- und Aramid-Endlosfasern drucken“, fügt Miller hinzu.
Wie wäre es mit dem Drucken mit Draht und Faseroptik für multifunktionale Verbundstrukturen ? „Das wäre für uns im Wesentlichen nur eine weitere Faser“, sagt Miller. Diese Fähigkeit wurde bisher im Labor demonstriert. „Wir prüfen geistiges Eigentum und betreiben fortlaufend Forschung und Entwicklung in diesem Bereich“, fügt er hinzu.
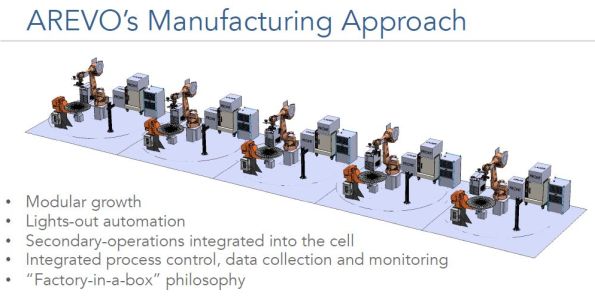
„Nichts hindert uns daran, mehrere Kabel und/oder Bänder zu verwenden “, behauptet Müller. „Und es gibt wirklich kein Limit bis zu welcher Größe wir drucken können. Wir fertigen ein 2,5 m x 1,5 m großes Teil für ein Luft- und Raumfahrtunternehmen und überlegen uns auch, mehrere Roboter zusammen zu verwenden . Das Unternehmen hat seine DED-Fertigungszellen modular entwickelt, in die Nebenoperationen integriert werden können, wie zum Beispiel die Veredelung zur Herstellung hochwertiger Oberflächen.
Wir können unsere Druckköpfe auch an beliebigen Industrierobotern anbringen, sodass unsere Technologie in einen bestehenden Prozess integriert werden kann oder ganz neue Prozesse.“ Er weist darauf hin, dass Arevo „nicht im Druckergeschäft tätig ist, aber diese Anpassungsfähigkeit eröffnet einige Möglichkeiten. Das Unternehmen hat 55 Patente ausgestellt, anhängig oder Anträge in Bearbeitung.
Wie sieht es mit generativem Design aus? Versteht sich Arevo als Akteur, der diesen neuen Ansatz in Design und Fertigung unterstützt? „Generatives Design unterscheidet sich stark von dem, was wir tun, weil es zu schwer herzustellenden Designs führen kann, was die Kosten in die Höhe treibt“, antwortet Miller. „Unser Ansatz ist die Optimierung für die Fertigung vorne.“
Harz
- Kohlefaserproduktion und Kohlefaserteile:Was sind die Grundlagen?
- Ersetzen von Aluminiumteilen durch 3D-gedruckte Kohlefaser
- 2018:Eine IMTS-Odyssee
- AON3D, Astrobotic schickt 3D-gedruckte Teile zum Mond
- Reduzierung der Kosten für Endlosfaser-3D-Druckmaterialien
- Alltec expandiert auf dem nordamerikanischen Markt
- Covestro bringt Maezio Endlosfaser-Thermoplaste auf den Markt
- Kontinuierliche Faserherstellung (CFM) mit Moi-Verbundwerkstoffen
- 3D-Druckverbundwerkstoffe mit Endlosfasern
- Software verbessert die Genauigkeit von 3D-gedruckten Teilen