Anwendungs-Spotlight:3D-Druck für Flugzeugkabinen
Wenn Sie in einem Flugzeug fliegen, werden Sie wahrscheinlich nicht bemerken, dass Ihre Armlehne oder Ihr Tabletttisch 3D-gedruckt wurde, aber die Verwendung dieser Technologie für Kabinenteile kann Fluggesellschaften völlig neue Möglichkeiten eröffnen.
Zu diesen Möglichkeiten zählen beispielsweise eine kostengünstige Innenausstattung sowie eine schnellere Produktion und Lieferung von Ersatzteilen.
Wir untersuchen die Hauptgründe für den Einsatz von 3D-Druck für die Innenausstattung von Flugzeugen und zeigen, wie führende Unternehmen der Luft- und Raumfahrtindustrie die Technologie heute anwenden.
Schauen Sie sich die anderen Anwendungen an, die in dieser Serie behandelt werden:
3D-Druck für Wärmetauscher
3D-Druck für Lager
3D-Druck für die Fahrradherstellung
3D-Druck für die digitale Zahnheilkunde und die Herstellung von Clear Alignern
3D-Druck für medizinische Implantate
3D-gedruckte Raketen und die Zukunft der Herstellung von Raumfahrzeugen
3D-Druck für die Schuhherstellung
3D-Druck für elektronische Komponenten
3D-Druck in der Bahnindustrie
3D-gedruckte Brillen
3D-Druck für die Endfertigung
3D-Druck für Halterungen
3D-Druck für Turbinenteile
Wie 3D-Druck leistungsfähigere Hydraulikkomponenten ermöglicht
Wie 3D-Druck Innovationen in der Kernkraftindustrie unterstützt
Warum 3D-Druck für Kabinenteile einsetzen?
Innovation beim Kabinendesign
Fluggesellschaften sind ständig auf der Suche nach Möglichkeiten, das Flugerlebnis ihrer Kunden zu verbessern, und das Kabinendesign spielt dabei eine entscheidende Rolle.
Benutzerdefinierte Innenausstattungen zu erstellen, die den spezifischen Anforderungen und Funktionen von Fluggesellschaften entsprechen, ist ein wachsender Trend und eine perfekte Aufgabe für den 3D-Druck.
3D-Druck eröffnet neue Möglichkeiten für die Individualisierung von Kabinenteilen, da keine teuren Werkzeugänderungen aufgrund individueller Spezifikationen erforderlich sind. Die Herstellung von Sonderteilen ist daher schneller und kostengünstiger.
Gewichtsreduktion
Da die Treibstoffausgaben für Fluggesellschaften einer der Hauptkosten sind, neigen sie dazu, in Flugzeuge mit überlegener Treibstoffeffizienz zu investieren. Herkömmliche Herstellungsverfahren haben jedoch eine begrenzte Fähigkeit, das Gewicht von Flugzeugteilen zu reduzieren.
Hersteller halten daher die Suche nach fortschrittlicheren und alternativen Verfahren zur Herstellung von Teilen mit reduziertem Gewicht am Leben.
3D-Druck bietet eine der Lösungen zur Gewichtsreduzierung durch optimierte Teilegeometrie, die Materialeinsparungen ermöglicht.
Mit 3D-Druck können Hersteller Kabinenteile aus leichten Materialien bauen, mit dünneren Wänden als beim Spritzgießen.
Darüber hinaus ermöglicht die Technologie eine Funktionsintegration, wobei mehrere separate Teile eines Bauteils als eine Einheit konstruiert und gedruckt werden können, wodurch das Gewicht eines Teils weiter reduziert wird.
On-Demand-3D-Druck von Ersatzteilen für die Innenausstattung von Flugzeugen
Die Vorhersage des Ersatzteilbedarfs ist eine Herausforderung und manchmal wird ein Ersatzteil möglicherweise nicht mehr produziert. Diese Faktoren erschweren den Flugzeug-Aftermarket-Service und führen zu Ineffizienzen der gesamten Lieferkette. Während ein hoher Lagerbestand die Ausfallzeiten von Flugzeugen reduzieren kann, führen sie zu astronomisch hohen Kosten für die Aufrechterhaltung eines solchen Lagerbestands.
Darüber hinaus ist es oft problematisch, termingerechte MRO-Leistungen zu erbringen. Die Notwendigkeit, in kurzer Zeit qualitativ hochwertige Ersatzteile aus teuren Materialien herzustellen, setzt die Hersteller unter Druck, da die Lieferzeiten bei herkömmlichen Fertigungsverfahren oft mehrere Monate betragen.
Darüber hinaus sind bei der Reparatur oder dem Austausch älterer Flugzeugkomponenten die zugehörigen Werkzeuge möglicherweise nicht mehr bei den OEMs erhältlich.
Der 3D-Druck bietet eine enorme Chance, einige dieser Herausforderungen zu meistern, indem er schnellere Durchlaufzeiten ermöglicht und den Lagerbestand durch On-Demand-Fertigung reduziert.
3D-Druck ermöglicht es Unternehmen, Teile direkt aus einer digitalen Konstruktionsdatei herzustellen, ohne Werkzeuge wie Formen zu verwenden. Dies bedeutet, dass einige Ersatzteile, insbesondere weniger nachgefragte Teile wie veraltete Komponenten, für den 3D-Druck umgestaltet und in einem virtuellen Inventar aufbewahrt werden können, wodurch Platz in einem Lager frei wird und die Lagerkosten gesenkt werden.
Bei Ersatzbedarf kann einfach eine Konstruktion aus dem virtuellen Teilekatalog gezogen und zum Druck gesendet werden.
Dank seiner Fähigkeit, kleine Stückzahlen wirtschaftlich zu produzieren, ermöglicht der 3D-Druck Unternehmen auch, nur so viele Teile wie nötig herzustellen, wodurch das für traditionelle Produktionsmethoden typische Problem der Überproduktion gelöst wird.
4 Beispiele für die Verwendung von 3D-Druck für Kabinenteile
Viele Innenausstattungskomponenten von Flugzeugen, von Lüftungsöffnungen und elektrischen Gehäusen bis hin zu Distanzplatten und Armlehnen, können vom 3D-Druck profitieren. Im Folgenden untersuchen wir, wie OEMs und Fluggesellschaften die Technologie für Kabinenteile nutzen.
1. Etihad Airways sieht einen erheblichen Mehrwert im 3D-Druck
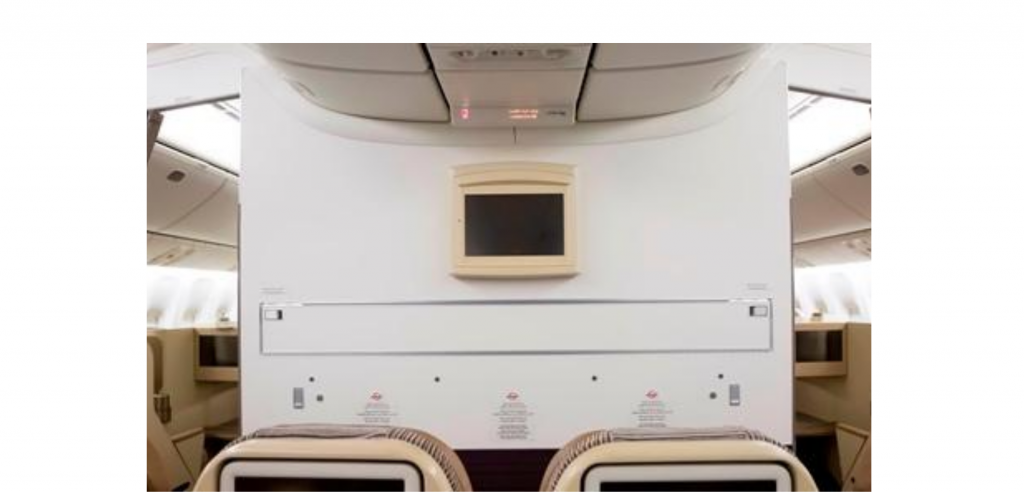
Die zweitgrößte Fluggesellschaft der Vereinigten Arabischen Emirate, Etihad Airways, war eine der ersten Fluggesellschaften, die das Potenzial des 3D-Drucks für Kabinenteile erforscht hat.
2017 präsentierte das Unternehmen das erste zertifizierte 3D-gedruckte Flugzeuginnenteil der Region, einen Monitorrahmen aus Kunststoff, und seitdem hat Etihad seine Bemühungen um 3D-Druck intensiviert.
Der Aufbau strategischer Partnerschaften mit den 3D-Druckunternehmen EOS und BigRep war ein Teil dieser Bemühungen.
Die Ergebnisse der Zusammenarbeit mit führenden 3D-Hardwareherstellern ließen nicht lange auf sich warten. Im vergangenen Jahr eröffnete Etihad in Abu Dhabi eine Produktionsstätte für additive Fertigung (AM), die von der Europäischen Agentur für Flugsicherheit (EASA) die Konstruktions- und Produktionsgenehmigung erhalten hatte, um Flugzeugteile mit der Pulverbett-Fusionstechnologie von EOS herzustellen.
Etihad Engineering, ein Geschäftsbereich der Etihad Aviation Group, wird den EOS 3D-Drucker nun zur Entwicklung, Herstellung und Zertifizierung von AM-Komponenten für hochwertige Flugzeuganwendungen und Kabinenteile einsetzen.
Das Unternehmen geht davon aus, dass der Einsatz des 3D-Drucks weit über den Austausch einfacher, unkritischer Teile hinausgeht.
Die additive Fertigung von Kabinenteilen bietet einen erheblichen Mehrwert in Bezug auf optimierte Reparatur, Leichtbau, kürzere Lieferzeiten und Individualisierung. Etihads neuer 'Greenliner' zum Beispiel, ein gemeinsames Projekt mit Boeing zur Förderung der Nachhaltigkeit in der Luftfahrtindustrie, soll viele 3D-gedruckte Komponenten enthalten.
Mit Blick in die Zukunft sieht Etihad eine komplette Nachrüstung eines Flugzeugs in nur 30 Tagen durch 3D-Druck, was zu 30 Prozent schnelleren Upgrades führt.
2. Das 3D-gedruckte Vorhang-Header-Gehäuse von Diehl Aviation
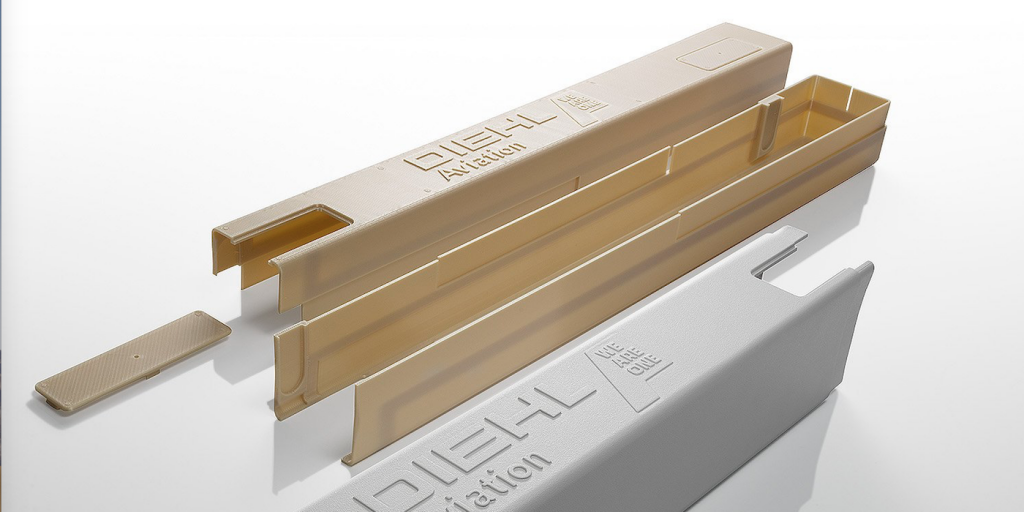
Der auf Kabinen- und Avionik spezialisierte Luft- und Raumfahrthersteller Diehl Aviation präsentierte ein weiteres Beispiel für den 3D-Druck von Interieurteilen.
Gemeinsam mit Airbus hat Diehl einen 3D-gedruckten Curtain Comfort Header entwickelt – ein Gehäuse, das über der Vorhangschiene sitzt und Klassen an Bord trennt – installiert auf einem Airbus A350 XWB von Qatar Airways.
Das Gehäuse wurde zuvor aus mehreren Schichten laminiertem Fiberglas hergestellt und erforderte spezielle Aluminiumwerkzeuge, was zeitaufwendig und kostspielig war.
Diehl konnte dieses Teil aus 12 3D-gedruckten thermoplastischen Bauteilen zusammenbauen, wodurch die Werkzeugkosten drastisch gesenkt und Arbeitszeit eingespart werden.
Darüber hinaus erfordern die Teile weniger Nacharbeit und können für Reparaturen oder Austausch leicht entnommen werden, was noch kürzere Durchlaufzeiten bei der Reparatur bedeutet.
Dieses Stück ist angeblich das größte vollständig 3D-gedruckte Passagierflugzeugteil, das bisher für Passagierflugzeuge hergestellt wurde.
3. British Airways prognostiziert eine zunehmende Verbreitung des 3D-Drucks für die Innenausstattung von Flugzeugen
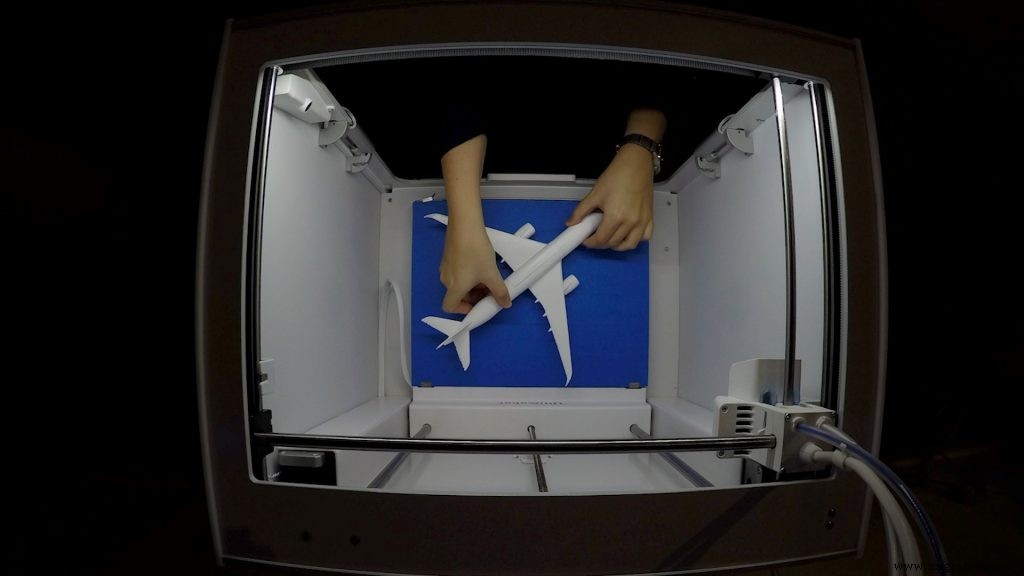
Während es den Anschein hat, dass sich die meisten Bemühungen für den 3D-Druck von Kabinenteilen auf die EMEA-Region konzentrieren, holen die europäischen Fluggesellschaften auf.
British Airways untersucht beispielsweise die Möglichkeit, 3D-Drucker zur Herstellung von Flugzeugteilen zu verwenden, angefangen bei nicht wesentlichen Kabinenteilen, einschließlich Teilen von Tabletttischen, Inflight-Entertainment-Systemen (IFE) und Toiletten.
Obwohl diese Komponenten den sicheren Flugbetrieb nicht beeinträchtigen, können sie im Falle eines Defekts die Anzahl der für Kunden verfügbaren Sitze oder Toiletten reduzieren und zu Verzögerungen führen, während die Ingenieure auf die Reparatur oder den Austausch der Teile warten .
Nach Angaben der Fluggesellschaft können 3D-Drucker Ersatzteile herstellen, die zwar so robust und langlebig sind wie herkömmliche Komponenten, aber in viel kürzerer Zeit verfügbar sind.
British Airways nennt Gewichtsreduzierung als weiteren Treiber für die Einführung von AM und sagt, dass 3D-Druck dazu beitragen kann, das Gewicht eines Teils um bis zu 55 Prozent zu reduzieren. Auch bei kleinen Bauteilen können die Auswirkungen erheblich sein, denn jedes entfernte Kilogramm spart während der Lebensdauer eines Flugzeugs tonnenweise CO2-Emissionen ein.
Die Fluggesellschaft prognostiziert, dass in Zukunft der 3D-Druck möglich sein wird a viel umfangreicheres Angebot an Kabinenteilen, von Besteck und Sitzen bis hin zu Gepäckbehältern und Flugzeugfenstern.
4. Stratasys, SIA Engineering Company und Additive Flight Solutions 3D-Druck Tausende von Kabinenteilen
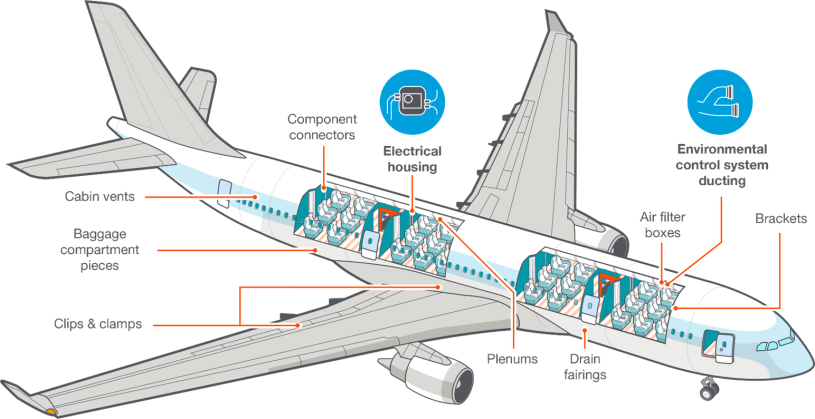
Stratasys betrachtet AM zusammen mit der SIA Engineering Company, die MRO-Dienste für Flugzeuge anbietet, und dem 3D-Druckservice-Büro Additive Flight Solutions ebenfalls als kritische Technologie, um Fluggesellschaften Lösungen anzubieten.
In einem 2018 gegründeten Joint Venture haben 3 Partner mit der Stratasys FDM-Technologie bis heute über 5.000 zertifizierte Teile für Flugzeugkabinen hergestellt.
Ein solches Teil ist eine Abdeckung, die Sitzsteuerungen schützen soll und verhindert, dass Passagiere versehentlich die Tasten drücken. Einer der Hauptgründe für die Wahl des AM-Verfahrens gegenüber einem anderen traditionelleren ist die Möglichkeit, diese Abdeckungen in kleinen Stückzahlen schneller und kostengünstiger zu produzieren.
In einem anderen Beispiel druckte das Team in 3D einen Clip, um Flugzeugvorhänge zurückzuhalten, die sich zu oft lösten. Es gibt 7 verschiedene Designs für diese Abdeckungen/Vorhänge, was bedeutet, dass das Team die Vorhangschienen-Endabdeckungen für jedes der Designs anpassen musste. Der 3D-Druck ist viel flexibler als andere Technologien, um ein solches Maß an Anpassung zu ermöglichen.
Darüber hinaus wurde 3D-Druck angewendet, um eine Sicherheitsverriegelung für die Nottüren der Boeing 787 herzustellen. Das Teil ist eine kritische Komponente, die sicherstellen soll, dass sich die Nottüren während des Flugzeugs nicht öffnen liegt am Boden, wodurch Verletzungsgefahr besteht, da versehentlich Fluchtrutschen ausgelöst werden könnten Seifen- und Desinfektionsmittelspender.
Alle Teile müssen strenge Anforderungen erfüllen, wie z. B. Wärmebeständigkeit und Flammen-, Rauch- und Toxizitätsbewertungen für Flugzeuginnenräume.
So viele Anwendungen, die das Team bereits entwickelt und in Verkehrsflugzeugen installiert hat, zeigen, dass die Zukunft des Flugzeuginnenraums eng mit ausgereiften 3D-Drucktechnologien verbunden ist.
Standardisierung von AM für Kabinenteile
Dennoch hat der 3D-Druck in der Luftfahrtindustrie ohne Standardisierung keine Zukunft. Es überrascht nicht, dass das Fehlen von Standards und Zertifizierungen nach wie vor ein massiver Engpass bei der Verwendung von AM für Flugzeugkabinenteile bleibt.
'Wenn Sie in der Luft- und Raumfahrt keinen Standard haben, nach dem Sie ein Teil nach oder in der Regel mehrere Standards zertifizieren können, dann können Sie es nicht auf einer Luft- und Raumfahrtplattform platzieren.' , sagte Matthew Donovan, jetzt ehemaliger Chefingenieur für Additive Fertigung bei Oerlikon, in einem Interview mit AMFG.
Ohne die richtigen Standards werden Luft- und Raumfahrtunternehmen die Technologie nicht mit dem gleichen Vertrauen einsetzen können, das traditionelle Herstellungsmethoden bieten.
Das Fehlen branchenweiter Standards für AM-Materialien, Prozesse, Qualitätsbewertung und Design sowie die begrenzten Daten zur Materialverarbeitung führen zu längeren Zertifizierungsfristen.
Derzeit zertifizieren Fluggesellschaften und Unternehmen, die Teile für Flugzeuge herstellen, Teile auf Teilbasis, was ein teures und zeitaufwendiges Unterfangen ist.
Zum Glück gibt es einen starken Druck auf die Entwicklung von Standards, Richtlinien und Richtlinien für die Anwendung von AM für Flugzeugkomponenten.
Behörden wie die Federal Aviation Administration (FAA) und European Aviation Safety Agency (EASA) arbeiten mit der AM-Industrie und Normungsorganisationen wie ASTM, SAE und ISO zusammen, um die aktuellen Herausforderungen bei der Standardisierung zu meistern.
Eine Reihe von Spezifikationen für den Polymer-3D-Druck in der Luft- und Raumfahrtindustrie, veröffentlicht von SAE International, war eine der jüngsten Fortschritte in diesem Bereich.
Die Spezifikationen AMS7100:Fused Filament Fabrication Process und AMS7101:Material for Fused Filament Fabrication wurden speziell für den FDM-Prozess entwickelt, um die Einführung des 3D-Drucks für Kunststoffkabinenteile zu fördern.
Die Zukunft des 3D-Drucks für Flugzeuginnenräume
3D-Druck ist eine der Schlüsseltechnologien, die Fluggesellschaften dabei hilft, Flugzeugkabinen an der Spitze der Innovation zu halten. Die Technologie verbessert den MRO-Betrieb, indem sie die Produktion von Ersatzteilen in geringer Stückzahl ermöglicht, und verbessert das Kundenerlebnis durch kundenspezifische Designs von Kabinenteilen.
Hunderte von 3D-gedruckten Innenausstattungskomponenten, die bereits in Flugzeugen verbaut sind, unterstreichen das Potenzial und den Wert der Technologie für die Luft- und Raumfahrtindustrie. Um dieses Potenzial voll ausschöpfen zu können, ist es jetzt entscheidend, sich auf die Ausweitung der Nutzung des 3D-Drucks durch Zusammenarbeit und Entwicklung von Standards zu konzentrieren.
3d Drucken
- Emirate übernehmen 3D-Drucktechnologie für Flugzeugteile
- Anwendungs-Spotlight:3D-Druck für medizinische Implantate
- Anwendungs-Spotlight:3D-Druck für die digitale Zahnheilkunde und die Herstellung von Clear Alignern
- Anwendungs-Spotlight:3D-Druck für die Fahrradherstellung
- Anwendungs-Spotlight:3D-Druck für Lager
- Anwendungs-Spotlight:3D-Druck für Wärmetauscher
- Anwendungs-Spotlight:3D-Druck in der Bahnindustrie
- Anwendungs-Spotlight:5 elektronische Komponenten, die vom 3D-Druck profitieren können
- Anwendungs-Spotlight:3D-Druck für Schuhe
- 10 stärkste Materialien für den 3D-Druck