Rockwell zählt, wie sich die digitale „Reise“ ausgezahlt hat
Tom O’Reilly, VP, Global Business Development bei Rockwell Automation, spricht mit dem Smart Manufacturing Magazin.
Tom, bitte erzählen Sie uns etwas über den Fünfjahresplan von Rockwell Automation, Ihre Anlagen- und Lieferantennetzwerke umzustrukturieren und zum „vernetzten Unternehmen“ zu gelangen.
Diese Reise begann vor mehr als fünf Jahren. Während wir diesen Prozess durchlaufen haben, haben wir einen sechsstufigen Prozess entworfen, der meiner Meinung nach veranschaulicht, was wir getan haben und wie wir diese Dinge jetzt tun, und auch, wie wir mit Kunden sprechen. Der erste Schritt besteht darin, die geschäftlichen Anforderungen zu verstehen. Der zweite Schritt besteht darin, festzustellen, wo die größten Lücken in der Lieferkette liegen. Dann auch Bestimmung Ihrer Bereitschaft:Bewertung Ihres aktuellen Zustands Ihrer Produktionsanlagen und -prozesse. Viertens ist die Entwicklung von Implementierungsplänen, dann das Projektmanagement, während Sie die Implementierungspläne umsetzen, und dann eine Phase der kontinuierlichen Verbesserung.
Sie mussten 20 verschiedene Werke koordinieren. Welche Lektionen hat das Unternehmen gelernt, die es jetzt auf Kunden anwendet?
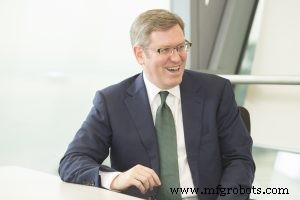
Das größte Problem, das wir entdeckten, war die fehlende Konnektivität – insbesondere zwischen dem ERP-System und der Fabrik für unsere Automatisierungssysteme. In vielen Fällen hatten wir nicht die richtigen Daten. In einigen Fällen gab es keine Daten. Und in einigen Fällen gab es schlechte Daten. Wenn Sie sich diese Daten ansehen und analysieren und sie entweder falsch oder nicht robust genug sind, kann dies zu falschen Entscheidungen führen. Eines der wichtigsten Dinge in der Phase der Bestimmung der Bereitschaft ist die Bewertung Ihrer Infrastrukturfähigkeiten. Das war eine wichtige Lektion, die wir gelernt haben. Und wir haben mit unseren Kunden darüber gesprochen.
Der zweite wirklich wichtige Punkt für Unternehmen, die sich auf die Reise zur intelligenten Fertigung begeben möchten, ist, dass Sie zuerst den Wert finden müssen. Betrachtet man die Geschäftsanforderungen, was sind die wahren Werttreiber? Was sind die wirklich großen Probleme, die Sie angehen müssen – die das beste Preis-Leistungs-Verhältnis bieten? Manchmal sind Leute nur mit der Technologie beschäftigt.
Ich habe gehört, Rockwell schreibt dieser Änderung eine jährliche Produktivitätssteigerung von vier bis fünf Prozent zu. Wie ist das möglich? Und glauben Sie, dass die meisten Hersteller damit rechnen können?
Bei den meisten Herstellern würde ich sagen ja. Aber es hängt von Ihrer Branche und Ihrem aktuellen Zustand ab. Es ist also schwer zu verallgemeinern. Wenn Sie sich ansehen, wie wir es gemacht/gemacht haben, hier sind einige Beispiele:Die Bestandstage sind von 120 auf 82 gesunken. Wir haben unsere CAPEX, das, was wir CAPEX-Vermeidung nennen, um 30 Prozent pro Jahr reduziert. Unsere Lieferung innerhalb unserer Lieferkette stieg von 80 Prozent auf 96 Prozent. Unsere Vorlaufzeiten wurden sogar um 50 Prozent reduziert. Und dann, beim Kundenservice, stieg unser Wunschtermin für die Lieferung an den Kunden von 82 Prozent auf 98 Prozent. Und in puncto Qualität haben wir unsere PPM (parts per million) um 50 Prozent reduziert. Weißt du, das passiert nicht alles am ersten Tag. Man muss sich also weiterhin auf die Bereiche konzentrieren und sie mit der Zeit immer weiter vertreiben. Wir glauben, dass wir die Kosten kontinuierlich um vier bis fünf Prozent senken können.
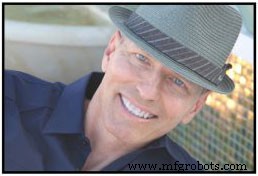
In Ihrer MES-Praxis arbeiten mit FANUC an Möglichkeiten auf der ganzen Welt. Welches Hauptproblem taucht bei dieser Art von Zusammenarbeit auf?
Wir haben eine großartige Partnerschaft mit FANUC, die vor etwa sieben Jahren begann. Es geht nicht nur um MES. Wir konzentrieren uns mit FANUC hauptsächlich auf den Powertrain-Bereich in der Automobilindustrie. Das größte Problem, mit dem unsere Kunden konfrontiert waren, und einer der Gründe für die Partnerschaft, war die Integration zwischen den Automatisierungssystemen und entweder ihrer CNC oder ihren Robotern. Um unseren Kunden dabei zu helfen, dieses Problem anzugehen, haben wir FANUC dabei geholfen, EtherNet/IP für die Kommunikation einzuführen. Wir bauen in unserer Programmierung auf sogenannten Addon-Profilen auf. Grundsätzlich handelt es sich um Bildschirme, die eingeblendet werden, damit Sie die Kommunikation in der CNC automatisch konfigurieren können. Daher haben wir die Integration nahtlos gestaltet und vorkonfiguriert, sodass es sehr einfach ist, sowohl die CNCs als auch die Roboter in unser Automatisierungssystem zu integrieren.
Würden Sie also sagen, dass die Integration jetzt immer ein Kinderspiel ist, oder ist sie unter bestimmten Umständen immer noch eine Herausforderung?
Es hängt davon ab, was Sie versuchen zu tun. Aber es ist definitiv viel einfacher als früher. Und das sagt nicht nur Rockwell. Das sagen uns unsere Kunden wie General Motors. Ihre Integration und der anschließende Informationsfluss aus beiden Systemen, sei es FANUC oder unserem System, bis in das MES-System und dann weiter zum ERP, ist viel einfacher. Ich weiß nicht, ob sie sagen würden, dass es ein Kinderspiel ist, aber sie würden sagen, dass es viel einfacher ist.
Ist diese gemeinsame Arbeit hauptsächlich im Automobilbereich? Welche anderen Märkte sind in dieser Beziehung wichtig? Und können Sie bitte darüber sprechen, wo Sie mit ihnen auf der Welt arbeiten?
Die Partnerschaft entstand aus der Notwendigkeit der Integration zwischen CNC-Robotik und Automatisierungssystemen in der Automobilindustrie. Bis heute war der größte Teil der Arbeit dem Automobilbereich gewidmet. Einer der am schnellsten wachsenden Bereiche der Robotik ist die Konsumgüterindustrie. Wir arbeiten also ziemlich viel mit FANUC auf der ganzen Welt zusammen, hauptsächlich für die Robotik und Konsumgüter, in Nordamerika und Europa. Bei der Arbeit, die wir mit FANUC geleistet haben, würde ich sagen, dass die Hauptmärkte Nordamerika, China, Europa, Japan und Korea sind. Das liegt daran, dass dies Automobilzentren sind, in denen die Entscheidungen getroffen und/oder die Maschinen gebaut werden.
Welche Art von Verbraucherprodukten?
Entweder Lebensmittel und Getränke oder verpackte Waren.
Und sind diese in verschiedenen Ländern?
Das sind hauptsächlich die weiter entwickelten Märkte, wo sie nach größeren Kostensenkungen, größerer Effizienz und vielleicht sogar größerem Durchsatz suchen, ohne größere Kapitalausgaben zu haben:Westeuropa und Nordamerika.
Welche Länder sind sicher große Wachstumsmärkte für Ihre MES-Praxis?
Nordamerika ist einer. Es gibt viele fortschrittliche Fertigungsinitiativen. Und um wettbewerbsfähig zu sein, müssen Sie mit der Ausführung der Konnektivität beginnen und die Konvergenz zwischen IT und OT erreichen. (Wir sagen Connected Enterprise.) MES ist dafür ein Schlüsselfaktor. Wir sehen auch einige aufstrebende Märkte wie China oder Indien, die in ihrer Entwicklung in Bezug auf die Produktionsreife früher sind. Aber sie erkennen, dass sie, um dauerhaft global wettbewerbsfähig zu sein, ihre Entwicklung fast überspringen müssen, um global wettbewerbsfähig zu werden.
Lassen Sie uns über die FactoryTalk Cloud Gateway-Plattform sprechen, bei der es darum geht, Informationen aus Produktionsanlagen, die Ihre Automatisierung nutzen, in eine Cloud-Datenstruktur zu bringen, wo sie sein können B. mit anderen Daten von Drittanbietern und ERP-Daten kombiniert und dann Business Intelligence darüber gelegt, um Analysen für Ihre Kunden durchzuführen und ihnen neue Geschäftseinblicke zu geben.
Mit dem FactoryTalk Cloud Gateway gehen wir eine Partnerschaft mit Microsoft ein. Wir basieren auf der Microsoft Azure Cloud. Aber die Software baut auf unserer jahrelangen Erfahrung mit Vor-Ort-Bereitstellungen auf und nutzt die Anlagenmodellierung aus unserem FactoryTalk VantagePoint mit anderen modernen web- und cloudbasierten Technologien. Der Vorteil der FactoryTalk Cloud Gateway-Plattform besteht darin, dass wir Daten aus mehreren Industrie- und Geschäftssystemen streamen können. Und dann, wenn wir sie kombinieren, können wir sie kontextualisieren, den Daten eine Bedeutung geben und sie dann in sehr benutzerfreundlichen Dashboards und Berichten präsentieren – sodass Nicht-Datenwissenschaftler die Trends im Prozess interpretieren und Maßnahmen zur Optimierung ergreifen können.
Wie wichtig sind Cloud-Lösungen wie FactoryTalk Cloud, wenn Sie mit Unternehmen außerhalb der USA zusammenarbeiten? Hat Ihr Update dieser Cloud-Plattform im letzten Herbst bei internationalen Partnern und/oder Kunden geholfen?
Wir aktualisieren unsere Cloud-Plattform schneller als unsere herkömmlichen Softwareprodukte. Viele unserer globalen Kunden interessieren sich für den geografischen Standort ihrer Daten, die Datenspeicherung und die Infrastruktur von Microsoft Azure ist am besten in Bezug auf Transparenz und Compliance von Cloud-Daten. Die Akzeptanz der Cloud-Plattform bei einem globalen Kundenstamm ist also überraschend hoch.
Was tun Sie, um Hersteller dazu zu bewegen, FactoryTalk Cloud einzuführen?
Wir versuchen es sehr einfach zu machen. Zum Beispiel ist die Konfiguration der Dashboards und die Anbindung an unser Gateway wirklich einfach. Mit ein paar einfachen Schritten können Sie das Gateway mit dem Steuerungssystem verbinden. Die Daten fließen automatisch in die Cloud und Sie können Ihre Dashboards sofort einrichten.
Mit wem haben Sie beim Bau des Gateways zusammengearbeitet?
Die Gateway-Software ist unsere eigene Entwicklung, aber sie ist so konzipiert, dass sie mit benutzerdefinierten Adaptern und Anwendungen sehr erweiterbar ist. Wir werden diese APIs bald unserer gesamten Partner-Community anbieten.
Welche anderen Plattformen und Anwendungen bieten oder erstellen Sie, um für Ihre Kunden im Ausland einen Mehrwert zu erzielen?
Auf der Automation Fair im vergangenen November haben wir FactoryTalk Analytics for Machines, FactoryTalk Analytics for Devices, die FactoryTalk TeamONE-Anwendung angekündigt, und viele davon sind zweckgebundene Anwendungen. Sehr skalierbar, einfach zu bedienen, einfach zu implementieren. Wir hoffen, dass die Menschen durch die Herstellung dieser modularen Anwendungen, die sehr kostengünstig sind, einen schrittweisen Ansatz verfolgen können, anstatt zu versuchen, den Elefanten in einem Bissen zu essen.
Wenn Sie diese Software verwenden, um Fehler zu erkennen und zu beseitigen, was sind die zwei oder drei häufigsten Fehler, die sie findet und beseitigt?
Einer der wichtigsten Vorteile, die wir gesehen haben, ist, dass Kunden unbekannte Probleme aufdecken. Typischerweise wissen in einer Produktionsstätte entweder der Bediener oder die Mitarbeiter der Betriebstechnik, wo sie Herausforderungen in Bezug auf Leistung, Qualität oder Durchsatz haben. Sobald Kunden das System installiert haben und beginnen, diese Probleme zu lösen, finden sie oft andere Probleme, von denen viele ihnen nicht bewusst waren. Sie könnten beispielsweise Engpässe in vor- oder nachgelagerten Herstellungsprozessen haben.
Wie alle anderen waren auch die Kunden von Rockwell vorsichtig bei der Einführung der Cloud. Was tun Sie, um sie davon zu überzeugen, dass jetzt der richtige Zeitpunkt für die Einführung ist? Und werden die Ransomware-Angriffe dieser Woche die Bemühungen zur Förderung der Cloud-Einführung erschweren?
Erstens hat sich die Zuverlässigkeit und Leistungsfähigkeit von Cloud-Lösungen enorm verbessert. (Außerdem müssen unsere Kunden keine eigene Infrastruktur unterhalten, und das wird für viele unserer Kunden immer wichtiger.) Zweitens ist die Skalierbarkeit von Cloud-Diensten mit On-Premise-Funktionen fast unmöglich zu reproduzieren. Unsere Kunden können klein anfangen und viel schneller skalieren, als wenn sie es selbst bauen und warten würden. Die Sicherheit von Cloud-Lösungen ist wahrscheinlich viel besser als bei On-Premise-Lösungen. Und das, denke ich, spielt in den zweiten Punkt hinein. Cloud-Dienste werden viel häufiger aktualisiert.
Wir glauben, dass viele der aktuellen Ransomware [betroffen] sind, was die Leute als nicht verwaltete IT-Ressourcen bei unseren Kunden bezeichnen würden – wo sie sie nicht auf dem neuesten Stand gehalten haben oder nicht haben Sie die richtige Sicherheit an Ort und Stelle. Das war entweder der Einstiegspunkt oder der Anfang. Cloud-Dienste wären möglicherweise eine größere Prävention. Das ist unser erster Gedanke. Offensichtlich würden die Leute Angst haben, daraus herauszukommen und zu versuchen zu verstehen, was passiert ist. Aber unser anfänglicher Gedanke ist, dass dies tatsächlich mehr unserer Kunden dazu bringen könnte, die Cloud stärker zu nutzen.
Als Rockwell Werke in Singapur und Mexiko bauen musste, wie haben Sie das Stammeswissen über die Herstellungsprozesse bei Rockwell auf diese Märkte übertragen?
Wir haben die Anlagen in Singapur und Mexiko später auf unserer Reise bearbeitet, also hatten wir unseren sechsstufigen Prozess zur Implementierung des vernetzten Unternehmens in allen unseren Anlagen entwickelt – und ihn in mindestens 10 Werken durchgeführt. Es ist wichtig, die besten Fachexperten für bestimmte Aspekte des Prozesses zu haben, die komplex, einzigartig oder sehr kritisch waren. Wir haben diese Fachexperten in jedes Werk gebracht, um sicherzustellen, dass diese Prozesse auf die richtige Weise beschleunigt werden. Schließlich haben wir festgestellt, dass es sehr wichtig ist, vor Beginn der Reise standardisierte Systeme und Architekturen zu haben.
Automatisierungssteuerung System
- Fünf Wege, wie die Digital-Twin-Technologie Unternehmen durch die Pandemie hilft
- In der neuen Logistiklandschaft gibt es kein Zurück zu alten Wegen
- Kunden auf dem ganzen Weg von Norwegen zu unserer CNC-Fräserfabrik
- GE Digital:eine fortlaufende Reise der digitalen Transformation
- Wie hat COVID-19 die digitale Transformation verändert?
- Censornet:Sicherung der Zukunft der Fertigungsindustrie
- Die übergroßen Auswirkungen von Industrie 4.0 auf das Backoffice
- CS Ellis:Vier Wege zur Digitalisierung der Lieferkette
- Der Aufstieg digitaler Plattformen in der Fertigung
- Rockwell Automation:Beschleunigung der digitalen Transformation