Big Data Analytics kann Herstellern Millionen sparen, indem sie die Prozesseffizienz verbessert
Fertigungstechnik: Data Mining und Big Data sind heiße Themen. Ihr Unternehmen entwickelt Process-Mining-Software; Wie unterscheidet es sich von Data Mining?
Alex Rinke: Data Mining war traditionell KPI [Key Performance Indicator]-orientiert und konzentrierte sich auf die Identifizierung von Mustern, um zukünftige Trends vorherzusagen, und die Analyse von Daten, um umsetzbare Erkenntnisse zu gewinnen. Unternehmen nutzen Data Mining, um Schlussfolgerungen zu ziehen und spezifische Probleme zu lösen, aber Process Mining verfolgt einen völlig anderen Ansatz. Die Process-Mining-Technologie nutzt Ereignisprotokolle, um eine visuelle Rekonstruktion jedes Prozesses in seinem Ist-Zustand zu erstellen, und plötzlich können Benutzer, anstatt Datensätze zu durchsuchen, um ein relevantes Muster zu finden, tatsächlich sehen, wie ein Prozess in Echtzeit abläuft. Wir beschreiben den Unterschied zwischen Data Mining und Process Mining gerne so, dass man im Dunkeln mit einer Taschenlampe leuchtet oder einen Lichtschalter umlegt; beides sind nützliche Ansätze, aber einer ist für volle Sichtbarkeit eindeutig überlegen.
ICH: Was genau bietet Process Mining diskrete Fertigungsabläufe?
Rinke: Ein entscheidender Vorteil von Process Mining ist, dass es grundsätzlich auf jeden Prozess anwendbar ist, und dazu gehören auch Fertigungsabläufe. Wenn Ereignisprotokolle erstellt werden, kann Process Mining ein klareres Bild davon zeichnen, wie Vorgänge tatsächlich ausgeführt werden. Davon abgesehen ist die diskrete Fertigung eine Branche, die die meisten Erkenntnisse aus Process Mining gewinnen wird, und Kunden wie Siemens, ABB und 3M sind nur einige der Unternehmen, die sich stark auf Process Mining verlassen, um die Flexibilität und Effizienz von zu verbessern ihre Operationen.
Häufige Anwendungsfälle, denen wir in der Fertigung begegnen, sind die Verbesserung der Termintreue, die Überwachung der Automatisierung, die Modellierung der Kapazität und die Reduzierung von Verschwendung, und Process Mining hat sich für all diese Bereiche als unschätzbar erwiesen. Beispielsweise ist ABB eines der größten und komplexesten Fertigungsunternehmen der Welt, das Process Mining derzeit für eine Vielzahl von Prozessen einsetzt, vom Purchase-to-Pay-Prozess bis hin zu seinen Produktionsprozessen. Mitarbeiter des ABB-Werks in Hanau, Deutschland, extrahierten früher mehrmals täglich Auswertungen aus ihren SAP-Systemen, importierten sie in Excel und nutzten komplexe Formeln, um Prozesse zu analysieren und zu verstehen. Heute erhalten die zuständigen Produktions- und Montageteamleiter bei ABB morgens als erstes eine E-Mail, in der die Produktionsvarianten des Vortags, die Durchlaufzeiten und die Anzahl der Ausschüsse aufgeführt sind. Und es ist wichtig zu beachten, dass wir hier nicht nur über KPIs sprechen – das gesamte Ökosystem der Prozesse der Anlage ist mit Process Mining sofort sichtbar, wodurch die Entdeckung von Ineffizienzen zum Kinderspiel wird. Es kann schwierig sein, ein Problem zu lösen, das Sie kennen, aber es ist fast unmöglich, ein Problem zu lösen, das Sie noch nicht entdeckt haben.
ICH: Wie funktioniert die Celonis Proactive Insights Process Mining Engine?
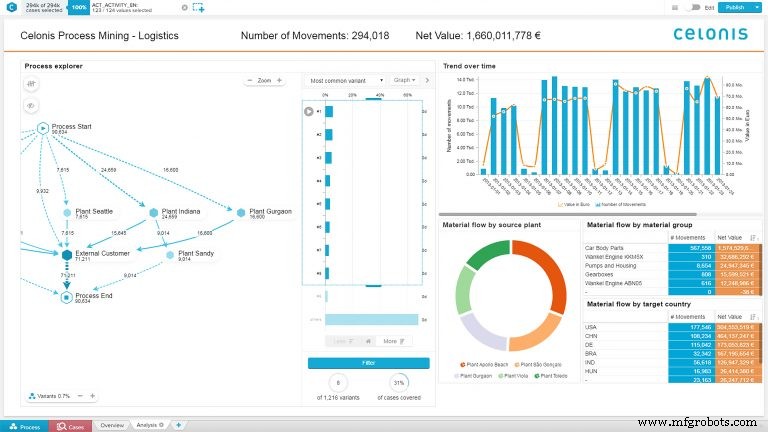
Rinke: Celonis PI ist eine sehr aufregende Ergänzung unserer Kerntechnologie, mit dem enormen Versprechen, unseren Kunden einen kontinuierlichen Mehrwert zu bieten. Im Wesentlichen nehmen die maschinellen Lernalgorithmen, die wir auf Celonis gelegt haben, frühere Anwendungsfälle auf und bauen darauf auf, fungieren als automatisierte Unternehmensberater und empfehlen Verbesserungen. Die automatisierten Mustererkennungsfunktionen bedeuten, dass Celonis, wenn es in der Vergangenheit auf ähnliche Ineffizienzen gestoßen ist, entsprechende Lösungen zur Überwindung dieser Ineffizienzen zurückmelden kann. Wenn wir uns Celonis als MRT für Geschäftsprozesse vorstellen, dann ist PI wie ein automatisierter Arzt, der die Ergebnisse dieses MRT-Scans interpretiert.
ICH: Welche Hersteller verwenden diese Technologie und wie setzen sie sie ein?
Rinke: ABB, 3M und Siemens sind einige Celonis-Kunden, die Process-Mining-Technologie in einer Vielzahl von Prozessen eingesetzt und einer Vielzahl von Mitarbeitern zur Verfügung gestellt haben. Siemens beispielsweise hat sich entschieden, seine Mitarbeiter durch eine breite Bereitstellung zu stärken; Mehrere tausend Siemens-Mitarbeiter nutzen täglich Celonis, um genau zu verstehen, was in ihren Prozessen passiert. Materialbeschaffung, Lieferantenmanagement, Produktion und Montage, Shared Services – jeder dieser Prozesse wird transparent und verständlicher, wenn der sprichwörtliche Lichtschalter umgelegt wird.
ICH: Welche Fertigungsindustrien können Process Mining am besten nutzen?
Rinke: Das Schöne am Process Mining ist, dass es für alle Branchen, die Fertigung oder andere, absolut relevant ist. Wir haben gesehen, wie Beschaffungsabteilungen vollständig transformiert und effizienter gemacht wurden, und Fabriken, die durch das Erreichen vollständiger Datentransparenz intelligenter wurden. Der Trend geht derzeit in Richtung „Industrie 4.0“ und sich selbst optimierende intelligente Fabriken, und eine der Kernaspekte dieses Trends ist die Informationstransparenz – Celonis Process Mining ist eine Out-of-the-Box-Lösung, um dieses Maß an Transparenz zu erreichen.
ICH: Wie sieht die Zukunft für Fertigungsbetriebe aus, die maschinelles Lernen und KI nutzen, gebündelt in Ihre Process-Mining-Datenanalyse?
Rinke: Das Potenzial für KI innerhalb von Process-Mining-Software ist grenzenlos, denn je mehr Informationen das System auf Grundlage von immer mehr Anwendungsfällen sammelt, desto intelligenter wird Celonis. Wie bei allen maschinellen Lern- und KI-Anwendungen wird das System bei der Erkennung von Mustern immer besser, je mehr Daten eingespeist werden. Anstatt sich auf komplexe manuelle Analysen von Prozessen zu verlassen, erwarten wir von Celonis PI sofortige Ergebnisse. Stellen Sie sich einen Produktionsprozess mit Engpässen vor, der Verzögerungen in einer Fabrik verursacht – und stellen Sie sich vor, Sie hätten keine Ahnung, wo der Engpass auftritt oder welche Auswirkungen der Engpass hat. Celonis kann die Quelle des Engpasses leicht identifizieren, und PI gibt Empfehlungen, wie die Grundursache des Engpasses effektiv gemindert werden kann. Es ist eine aufregende Zeit für Hersteller in allen Branchen.
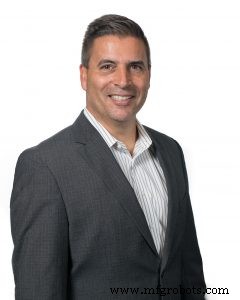
Epicor ernennt Stephen Murphy zum CEO
Der ERP-Entwickler Epicor Software Corp. (Austin, TX) gab am 5. Oktober bekannt, dass Joe Cowan, Präsident und CEO von Epicor, Ende Oktober in den Ruhestand treten wird. Der Vorstand von Epicor hat Stephen Murphy, den ehemaligen Präsidenten von OpenText (Waterloo, Ontario), zum CEO von Epicor ernannt.
Bevor er zu Epicor kam, war Murphy President von OpenText, einem 2-Milliarden-Dollar-Entwickler von Enterprise Information Management (EIM)-Software. Murphys Karriere erstreckt sich über mehr als 20 Jahre im Technologiesektor, einschließlich Vertriebs- und Betriebsführungspositionen bei Oracle, Sun Microsystems und Manugistics, sowie Herstellungs- und Vertriebserfahrung als Leiter globaler Logistik- und Lieferkettenstrategien und wichtiger ERP-Implementierungen bei Accenture und Procter &Zocken. Murphy hat einen MBA der Harvard Business School und einen Bachelor of Science in Maschinenbau der University of California, Davis.
Software zur Optimierung einer Vollverbund-Flugzeugstruktur
Als Stratolaunch Systems Corp. (Seattle) in diesem Frühjahr sein vollständig aus Verbundwerkstoffen bestehendes Stratolaunch-Flugzeug ausrollte, um sich auf Bodentests in der Mojave-Wüste vorzubereiten, zeigte das gigantische Flugzeug, wie weit das Design und die Herstellung von Verbundwerkstoffen in den letzten Jahren fortgeschritten sind. Im vergangenen Monat wurde die erste Phase der Triebwerkstests an den sechs Pratt &Whitney-Turbofan-Triebwerken des Flugzeugs abgeschlossen.
Das nach Spannweite größte Flugzeug der Welt – größer als ein Fußballfeld lang ist – ist fast vollständig aus Verbundwerkstoffen gefertigt, die ein geringes Gewicht, eine hohe Steifigkeit und Festigkeitseigenschaften bieten, die in den Bereichen Luft- und Raumfahrt, Automobil, Sport, Medizin und Industrie zunehmend gefragt sind. Die HyperSizer-Optimierungssoftware von Collier Research (Newport News, VA) wurde ausgiebig vom Hersteller Scaled Composites verwendet, um die Rumpf- und Flügelstruktur aus Verbundwerkstoff des Flugzeugs zu optimieren.
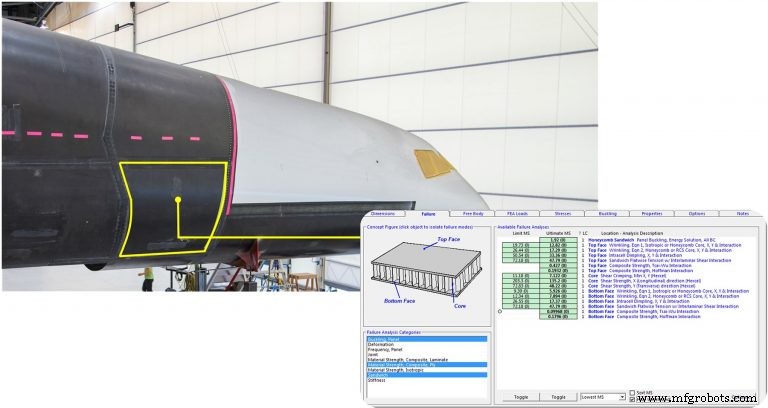
HyperSizer, das erste Softwarepaket, das von der NASA kommerzialisiert wurde, wurde bei einer Vielzahl von Luft- und Raumfahrt- und anderen Industrieprojekten eingesetzt, die mit Verbund- oder Metallmaterialien hergestellt wurden. Die Software führt automatisch Design, Belastungsanalyse und Größenoptimierung durch, wodurch das Gewicht von Strukturen in der Regel um 20–40 % reduziert wird.
„Um die effizienteste Nutzung von Materialien in einer Vollverbundstruktur jeder Größe zu gewährleisten, ist der effektive Einsatz von Konstruktions- und Fertigungsoptimierungstools von den frühesten Stadien an erforderlich“, sagte Craig Collier, Präsident von Collier Research.
Das Stratolaunch-Flugzeug ist die Idee des Stratolaunch System Corp.-Gründers Paul G. Allen. Es hat zwei Rümpfe, die durch einen riesigen Einzelflügel verbunden sind, und wird von sechs Triebwerken angetrieben, die es ihm ermöglichen, mit einer Nutzlast von bis zu 247.500 kg (550.000 lb) von einer Landebahn abzuheben. Auf der Reiseflughöhe eines Verkehrsflugzeugs wird die Startplattform Stratolaunch die Nutzlast der Trägerrakete freisetzen und zur Wiederverwendung zum Flughafen zurückkehren. Die erste Startdemonstration soll bereits 2019 stattfinden.
Für den massiven Stratolaunch-Flügel waren Durchbiegungsgrenzen ein wichtiger Faktor, der berücksichtigt werden musste. Die Paneele der Duellrümpfe wurden für Stärke, Stabilität und Wabensandwich-Versagensmodi bemessen. Durch die Verwendung von HyperSizer hatte das Belastungsteam Zugriff auf einen umfassenden Satz automatisierter Fehleranalysen, darunter eine schnelle Freikörperanalyse; diskrete Laminatleimung; Lagenbasierte Komposit-Versagensanalyse; Waben-Sandwich-Analyseverfahren wie Faltenbildung, Kernscherung, Flatwise Tension und Intracell-Dimpling; und Skript-API, um Lasten aus Excel-Tabellen einzufügen.
Collier sieht eine kontinuierliche Entwicklung bei der Integration der Toolsets, die für das Design und die Herstellung von Verbundwerkstoffen verwendet werden. „Die HyperSizer-Software kann Aufschluss darüber geben, wie herstellbar eine Struktur ist und ob es möglicherweise Herstellungsprobleme gibt“, sagte Craig Collier. „Es kann die Vorlieben für die Laminatherstellung in die Designüberlegungen in der frühen Phase einbeziehen; einfache Herstellung wird zu einem wichtigen Einflussfaktor bei der Festigkeitsauslegung von Laminatstrukturen.“
Neuerscheinungen
BigLever Software (Austin, TX), Entwickler von Product Line Engineering (PLE), und Method Park (Pittsburgh), ein Anbieter von Engineering-Prozessmanagement, haben das neue funktionsbasierte PLE Process Framework entwickelt, das eine Standardvorlage der Besten bietet Praktiken, die PLE-Erfolge ermöglicht haben.
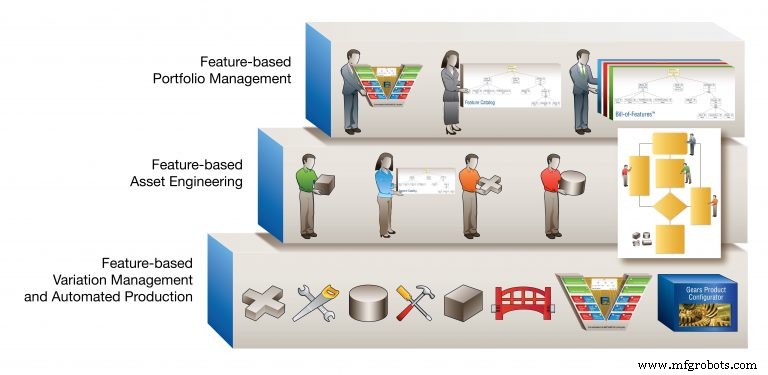
Das neue Framework, das derzeit verfügbar ist, kombiniert das Stages Process Management System von Method Park mit der dreistufigen PLE-Methodik von BigLever, um Unternehmen den Übergang zur PLE-Praxis zu beschleunigen und eine funktionsübergreifende Ausrichtung im gesamten Unternehmen zu erreichen. Unternehmen können das Prozess-Framework verwenden, um ihre PLE-Vorgänge zu optimieren, indem sie die Kommunikation und Zusammenarbeit über Software-, elektrische und mechanische Domänen hinweg verbessern und die Fallstricke von Ad-hoc- und einmaligen Ansätzen vermeiden. BigLever hat das neue Framework als Schlüsselelement in die ganzheitliche onePLE-Lösung des Unternehmens integriert.
Funktionsbasiertes PLE vereinfacht die Erstellung, Bereitstellung, Wartung und Weiterentwicklung eines Produktlinienportfolios erheblich, indem ein gemeinsam genutzter Satz von technischen Ressourcen, ein verwalteter Satz von Funktionen und ein effizientes Mittel zur Automatisierung der Produktion der Produktlinie verwendet werden. Das neue Prozess-Framework bietet eine vollständig anpassbare Concept of Operations (ConOps)-Vorlage, die die Organisationsstruktur darlegt und diese Struktur in Gang setzt, indem die organisatorischen Rollen, Verantwortlichkeiten und Prozesse klar definiert werden, die für einen effektiven Betrieb unter dem PLE-Paradigma erforderlich sind.
Boothroyd Dewhurst Inc. (Wakefield, RI), Entwickler der Software Design for Manufacture and Assembly (DFMA), hat seine aktualisierte DFM Concurrent Costing Version 3.0 veröffentlicht. Als Kostenanalyse-Tool für Engineering- und Beschaffungsteams eingesetzt, ermöglicht die neueste Software den Herstellern, über „Preis“-Modelle hinauszugehen, die weitgehend auf früheren Angeboten basieren, und auf industrielle Kostenmodelle zu setzen, die auf wissenschaftlichen Testdaten und Studien basieren. Das Ergebnis ist eine äußerst zuverlässige „Sollte-Kosten“-Ansicht des Produkts, die Einblicke in versteckte Kostentreiber und Möglichkeiten zur Optimierung von Design und Produktion bietet, so das Unternehmen.
DFM 3.0 ermöglicht es OEMs und ihren Zulieferern, Angebote in einem neutralen Rahmen zu prüfen, in dem Maschinentypen, Geschwindigkeiten, Verarbeitungssequenzen und optimale Automatisierungsgrade diskutiert werden. Dieses besser informierte Umfeld soll Lieferantenvorschläge und vertiefte, integrierte Partnerschaften fördern, die auf Fachwissen, Best-Cost-Praktiken und gemeinsamen Zielen aufbauen.
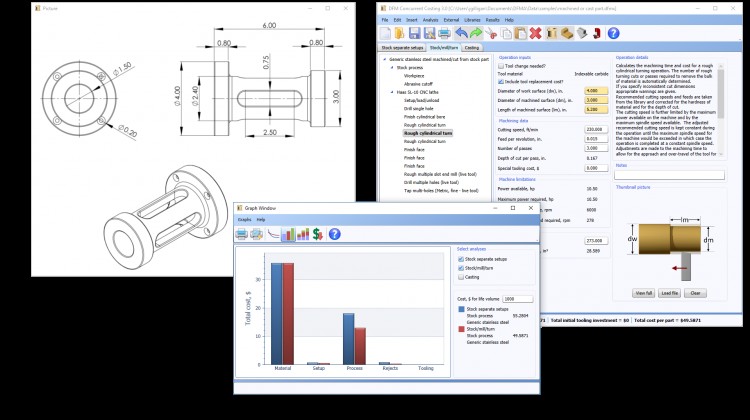
Die Unterschiede zwischen traditionellen Preismodellen und datengesteuerten Kostenmodellen können erheblich sein und sich auf Entscheidungen darüber auswirken, in welche Regionen oder Länder ein Produkt zur Herstellung verlagert wird. Richtig gestaltete und kalkulierte Produkte verbleiben eher an ihrem ursprünglichen Herstellungsort und in der Nähe vorhandener Ressourcen. OEMs und Zulieferer können rund um die DFM-Software zusammenarbeiten, um diese und andere strategische Probleme anzugehen. Die DFM-Analyse, die früh im Design oder während des Prototypings durchgeführt wird, verkürzt die Markteinführungszeit, wirkt sich auf direkte und indirekte Kosten aus und trägt zur Optimierung der Produktfunktionalität bei. Es kann von Einzelpersonen oder Teams verwendet werden, um Kompromissentscheidungen zur Kostensenkung zu treffen.
Zu den Highlights der neuesten Version gehören Geometrierechner in DFM 3.0, die vereinfacht und in die Hauptantwortbereiche der Software integriert wurden, sodass Benutzer unterstützender durch eine DFM-Kostenanalyse ihrer Teile geführt werden.
Die standardmäßigen Fertigungsabläufe und benutzerbasierten Prozessbibliotheken wurden optimiert und allen Formelfenstern wurde ein neues Testansichtsfenster hinzugefügt. Die Entwicklung angepasster Abläufe und Benutzerprozesse ist nach Angaben des Unternehmens schneller und einfacher. Das allgemeine Erscheinungsbild der DFM-Software wurde aktualisiert, um eine kohärentere Benutzererfahrung zwischen Design for Assembly (DFA) und DFM-Kosten zu bieten. Die Leistung der DFA/DFM-Softwareverbindung wurde für eine nahtlosere Datenintegration zwischen Softwarepaketen verbessert.
Automatisierungssteuerung System
- Wie Hersteller die Agilität in einer postpandemischen Welt steigern können
- 5 Möglichkeiten, wie Sie durch die Automatisierung des Herstellungsprozesses Geld sparen können
- Intelligente Automatisierung kann Millionen von Leben pro Jahr retten
- Process Insights:Was nach der Prozessanalyse zu tun ist
- IIoT und Predictive Analytics
- Verbesserung der Energieeffizienz mit HMIs
- Drei Möglichkeiten, wie KI Fertigungsabläufe verbessert
- Celonis Webinar:Verbesserung der Prozessausführung
- Wie kann die Prozessindustrie Industrie 4.0 implementieren?
- Wie Hersteller von der Implementierung von 5G profitieren können