Was ist Extrusion? Verschiedene Arten von Extrusionsprozessen?
Der Extrusionsprozess ist eine der Arten von Massivumformprozessen, bei denen Arbeitsmetall durch ein Matrizenloch gezwungen oder komprimiert wird, um eine bestimmte erforderliche Querschnittsform zu erreichen.
Einfach ausgedrückt ist die Extrusion ein Metallbearbeitungsverfahren, bei dem Metall unter erhöhtem Druck durch ein Matrizenloch gepresst wird, um seinen Querschnitt zu komprimieren.
Seit der Entwicklung des Extrusionsverfahrens ist die Welt abhängig von der Extrusion geworden, um Stangen, Rohre und Profile jeder Form herzustellen, entweder hohl oder massiv.
Da dieser Vorgang das Schieben oder Ziehen des Barrens durch die Matrize beinhaltet, sind die zum Extrudieren des Barrens erforderlichen Kräfte ziemlich groß. Das Warmfließpressen ist das gebräuchlichste Verfahren, da der Verformungswiderstand des Metalls bei hohen Temperaturen gering ist, während das Kaltfließpressen im Allgemeinen nur bei weichen Metallen durchgeführt wird.
Geschichte:
Obwohl das Konzept der Extrusion aus dem Umformprozess stammt. Es wird berichtet, dass 1797 ein Ingenieur namens Joseph Bramah das Extrusionsverfahren patentieren ließ.
Der Versuch umfasste das Vorheizen von Metall und das anschließende Pressen durch einen Formhohlraum, um aus dem Knüppel ein Rohr herzustellen. Er benutzte einen handgetriebenen Kolben, um das Metall zu zwingen.
Bramah erfand dann das hydraulische Verfahren nach der Erfindung der Extrusion. Dann verwendete Thomas Burr die Technologie der hydraulischen Presse und der grundlegenden Extrusionstechnik, die die einzelnen Technologien kombinierte, um ein Rohr (Hohlrohr) herzustellen. Es wurde dann auch im Jahr 1820 patentiert.
Die Technologie wurde dann zu einem Grundbedürfnis in der wachsenden Welt, während das Verfahren bei den Hartmetallen nicht funktionieren konnte. Im Jahr 1894 führte Thomas Burr das Strangpressen mit Kupfer- und Messinglegierungen ein, was eine Weiterentwicklung der Strangpresstechnik mit sich brachte.
Seit der Erfindung der Extrusionstechnik hat sich das Verfahren zu einer Vielzahl von Techniken entwickelt, die in der Lage sind, eine breite Palette von Produkten mit komplexen Strukturen zu möglichst geringen Kosten herzustellen.
Klassifizierung oder Arten des Extrusionsverfahrens:
Verschiedene Arten von Extrusionsprozessen :
- Heißextrusion
- Kaltextrusion
- Warmextrusion
- Reibungsextrusion
- Mikroextrusion
- Direktextrusion
- Indirekte Extrusion
- Hydrostatische Extrusion und
- Schlagextrusion Verarbeiten.
#1. Heißextrusionsverfahren:
Bei diesem Heißstrangpressverfahren wird der Knüppel oberhalb seiner Rekristallisationstemperatur bearbeitet. Diese Warmumformung verhindert, dass das Werkstück kaltverfestigt wird, und sorgt dafür, dass der Stößel es leicht durch die Matrize drückt.
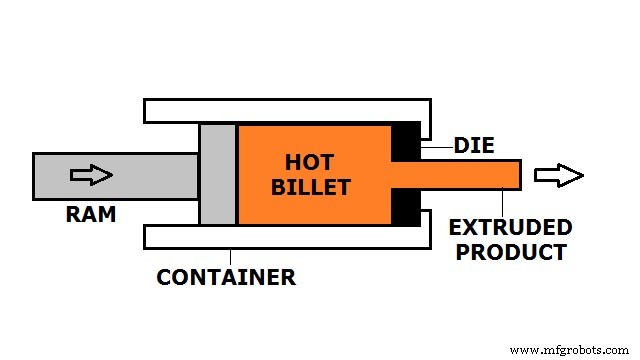
Heißextrusionen werden im Allgemeinen auf horizontalen hydraulischen Pressen durchgeführt. Der an diesem Prozess beteiligte Druck kann von 30 MPa bis 700 MPa variieren. Um den hohen Druck aufrechtzuerhalten, wird eine Schmierung eingesetzt. Öl oder Graphit wird als Schmiermittel bei Niedertemperatur-Extrusionen verwendet und Glaspulver wird für Hochtemperatur-Extrusionen verwendet.
Dem Knüppel wird eine Wärme zwischen 0,5 Tm bis 0,75 Tm zugeführt, um einen Qualitätsbetrieb zu erhalten.
Heißextrusionstemperaturen einiger häufig verwendeter Materialien sind wie folgt aufgeführt:
Material | Temperatur (˚C) |
Aluminium | 350 bis 500 |
Kupfer | 600 bis 1100 |
Magnesium | 350 bis 450 |
Nickel | 1000 bis 1200 |
Stahl | 1200 bis 1300 |
Titan | 700 bis 1200 |
PVC | 180 |
Nylon | 290 |
Vorteile des Heißextrusionsverfahrens:
- Die Verformung kann nach Bedarf kontrolliert werden.
- Der Knüppel wird keiner Verfestigung durch Kaltverfestigung unterzogen.
- Zum Pressen sind geringere Kräfte erforderlich.
- Auch Materialien mit Frührissen können bearbeitet werden.
Nachteile des Heißextrusionsverfahrens:
- Schlechte Oberflächenbeschaffenheit.
- Die Maßhaltigkeit kann beeinträchtigt werden.
- Geringere Containerlebensdauer.
- Möglichkeit der Oberflächenoxidation.
#2. Kaltextrusion:
Es ist der Prozess, Metall zu formen, indem man es mit einer Schnecke schlägt. Dieses Schlagen wird mit einem Stempel oder Stößel in einem geschlossenen Hohlraum durchgeführt. Der Stößel zwingt das Metall durch den Formhohlraum, um den festen Knüppel in eine feste Form umzuwandeln.
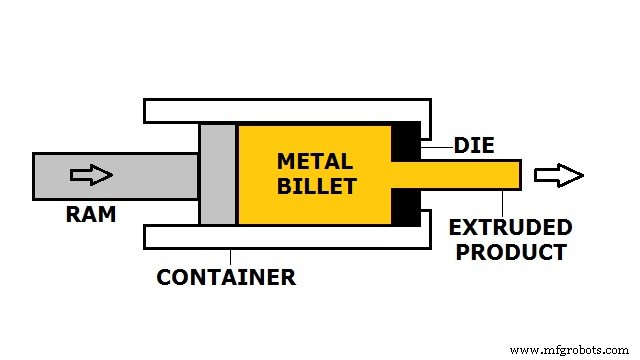
Bei diesem Verfahren wird das Werkstück bei Raumtemperatur oder leicht über Raumtemperatur verformt.
Da die erforderlichen Kräfte zu hoch sind, wird bei dieser Technik eine leistungsstarke hydraulische Presse verwendet. Der Druck reicht bis 3000 MPa.
Vorteile:
- Keine Oxidation.
- Verbesserte Festigkeit des Produkts.
- Engere Toleranzen.
- Verbesserte Oberflächenbeschaffenheit.
- Härte wird verbessert.
Nachteile:
- Höhere Kräfte sind erforderlich.
- Für den Betrieb ist mehr Leistung erforderlich.
- Nicht duktile Materialien können nicht bearbeitet werden.
- Die Kaltverfestigung des extrudierten Materials ist eine Einschränkung.
#3. Warmextrusionsverfahren:
Beim Warmstrangpressen wird ein Strang über Raumtemperatur und unterhalb der Rekristallisationstemperatur des Materials stranggepresst. Dieses Verfahren wird dort eingesetzt, wo das Material vor mikrostrukturellen Veränderungen geschützt werden muss, die während des Extrusionsprozesses auftreten.
Dieser Prozess ist wichtig, um das richtige Gleichgewicht zwischen erforderlichen Kräften und Duktilität zu erreichen. Die Temperatur jedes Metalls, das bei diesem Vorgang verwendet wird, kann zwischen 424 Grad Celsius und 975 Grad Celsius liegen.
Vorteile des Warmverfahrens:
- Verbesserte Kraft.
- Es verbesserte die Härte des Produkts.
- Fehlende Oxidation.
- Es können sehr enge Toleranzen erreicht werden.
Nachteile:
- Nicht duktile Materialien können nicht extrudiert werden.
- Ein Heizgerät ist zusätzlich.
#4. Reibungsextrusion:
Bei der Friktionsextrusionstechnik werden der Barren und der Behälter dazu gezwungen, sich gegeneinander zu drehen, während gleichzeitig der Barren durch den Matrizenhohlraum gedrückt wird, um das gewünschte Material herzustellen.
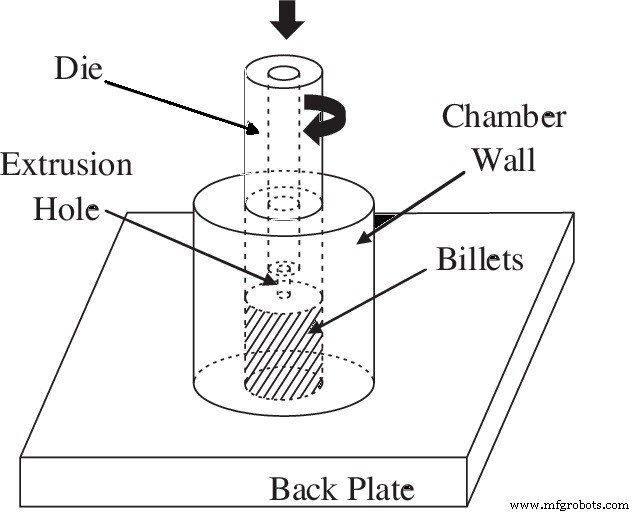
Der Prozess wird durch die relative Rotationsgeschwindigkeit zwischen Knüppel und Matrize beeinflusst. Die relative Rotationsbewegung der Charge und der Matrize hat eine signifikante Auswirkung auf den Prozess.
Erstens führt dies zur Erzeugung einer großen Anzahl von Scherspannungen, die bewirken, dass sich der Barren plastisch verformt. Zweitens wird während der relativen Bewegung zwischen dem Knüppel und der Matrize eine große Wärmemenge erzeugt, sodass kein Vorwärmen erforderlich ist, was den Prozess effizienter macht.
Es kann im Wesentlichen konsolidierte Drähte, Stäbe, Rohre und andere nicht kreisförmige Metallgeometrien direkt aus einer Vielzahl von Vorläuferchargen erzeugen, wie z. B. Metallpulver, Flocken, Bearbeitungsabfall (Späne oder Späne) oder massive Knüppel.
Vorteile des Friktionsverfahrens:
- Es ist keine Erwärmung erforderlich.
- Die Erzeugung von Scherspannungen führt zu einer verbesserten Ermüdungsfestigkeit des Produkts.
- Jede Art von Material kann als Barren verwendet werden, was diesen Prozess wirtschaftlich macht.
- Geringer Energieeinsatz.
- Bessere Korrosionsbeständigkeit.
Nachteile der Reibung Prozess:
- Erwartete Oxidation.
- Hohe anfängliche Einrichtung.
- Komplexe Maschinen.
#5. Mikroextrusionsverfahren:
Aus seiner Nomenklatur geht hervor, dass dieser Prozess die Herstellung von Produkten im Submillimeterbereich betrifft.
Ähnlich wie bei der Extrusion auf Makroebene wird der Barren hier durch die Düsenöffnung gedrückt, um die erwartete Form auf dem Barren zu erzeugen. Der Ausgang passt durch ein Quadrat von 1 mm.
Die Vorwärts- oder Direkt- und die Rückwärts- oder indirekte Mikroextrusion sind die zwei grundlegendsten Techniken, die in dieser Ära zur Herstellung von Mikroelementen verwendet werden.
Bei der Vorwärts-Mikroextrusion bewegt sich der Stempel vorwärts und der Block bewegt sich in die gleiche Richtung, während bei der Rückwärts-Mikroextrusion der Stempel und der Block sich in entgegengesetzte Richtungen bewegen.
Die Mikroextrusion wird häufig bei der Herstellung von Komponenten für resorbierbare und implantierte medizinische Geräte eingesetzt, die von bioresorbierbaren Stents bis hin zu Systemen mit kontrollierter Arzneimittelfreisetzung reichen.
Während im mechanischen Bereich die Anwendung bei der Herstellung von winzigen Zahnrädern, winzigen Rohren usw. weit verbreitet ist.
Vorteile des Mikroprozesses:
- Es können sehr komplexe Querschnitte erstellt werden.
- Winzige Elemente können hergestellt werden.
- Verbesserte geometrische Toleranzen.
Nachteile :
- Eine kleine Matrize und einen Behälter zu entwickeln, die unseren Anforderungen entsprechen, ist eine Herausforderung.
- Ein geschickter Arbeiter wird benötigt.
#6. Direkt- oder Vorwärtsextrusion:
Beim Direktextrusionsverfahren wird zunächst ein Metallbarren in den Behälter eingelegt. Der Behälter hat ein konturiertes Matrizenloch. Ein Stößel wird verwendet, um den Metallbarren durch das Matrizenloch zu treiben, und das Produkt wird hergestellt.
Bei diesem Typ ist die Richtung des Metallflusses dieselbe wie die Bewegungsrichtung des Stempels.
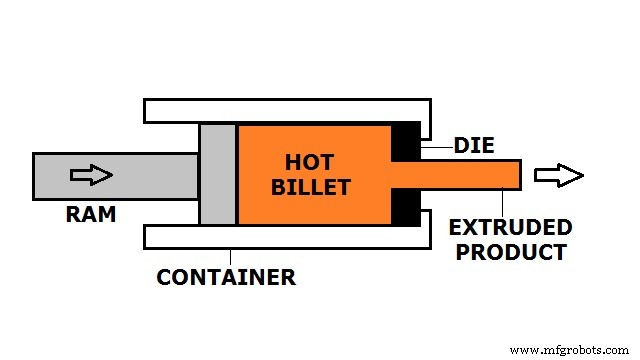
Wenn der Barren dazu gezwungen wird, sich in Richtung der Matrizenöffnung zu bewegen, wird eine große Reibung zwischen der Oberfläche des Barrens und den Behälterwänden erzeugt. Das Vorhandensein von Reibung erfordert eine deutliche Erhöhung der Stößelkraft, wodurch mehr Energie verbraucht wird.
Bei diesem Verfahren ist das Extrudieren von spröden Metallen wie Wolfram- und Titanlegierungen schwierig, da sie während des Verfahrens brechen. Die Zugkräfte während des gesamten Prozesses führen zur schnellen Bildung von Mikrorissen, die zu Brüchen führen.
Das Extrudieren spröder Metalle wie Wolfram- und Titanlegierungen ist schwierig, da sie während des Prozesses brechen. Durch Zugkräfte bilden sich schnell Mikrorisse, die zu Brüchen führen.
Außerdem verstärkt das Vorhandensein einer Oxidschicht auf der Oberfläche des Barrens die Reibung. Diese Oxidschicht kann Fehler im extrudierten Produkt verursachen.
Um dieses Problem zu lösen, wird ein Dummy-Block zwischen dem Stößel und dem Werkstück platziert, um die Reibung zu mindern.
Beispiele sind Rohre, Dosen, Becher, kleine Zahnräder, Wellen und andere extrudierte Güter.
Am Ende jeder Extrusion bleiben immer einige Teile des Barrens zurück. Es wird der Hintern genannt . Es wird aus dem Produkt entfernt, indem es unmittelbar hinter dem Ausgang der Matrize geschnitten wird.
Vorteile des direkten Prozesses:
- Das Verfahren ist in der Lage, längere Werkstücke zu extrudieren.
- Verbesserte mechanische Eigenschaften des Materials.
- Gute Oberflächenbeschaffenheit.
- Kalt- und Heißextrusion sind möglich.
- Fähigkeit zum kontinuierlichen Betrieb.
Nachteile des direkten Prozesses:
- Spröde Metalle können nicht extrudiert werden.
- Großer Kraft- und Leistungsbedarf.
- Möglichkeit der Oxidation.
#7. Indirekte oder Rückwärtsextrusion:
Bei diesem Rückwärtsstrangpressverfahren bleibt die Matrize stationär, während sich Barren und Behälter gemeinsam bewegen. Die Matrize ist eher auf dem Stößel als auf dem Behälter montiert.
Das Metall fließt durch das Matrizenloch auf der Stößelseite in die entgegengesetzte Richtung der Stößelbewegung, da es durch den Stößel komprimiert wird.
Wenn der Knüppel komprimiert wird, wird das Material zwischen dem Dorn und somit der Matrizenöffnung passieren.
Da es keine Relativbewegung zwischen dem Knüppel und dem Behälter gibt, wird keine Reibung aufgezeichnet. Dies hebt das Verfahren gegenüber dem Direktextrusionsverfahren ab, wodurch die eingesetzte Presskraft geringer ist als bei der Direktextrusion.
Um die Matrize stationär zu halten, wird ein „Stiel“ verwendet, der länger als die Länge des Behälters ist. Die Säulenfestigkeit des Stiels bestimmt die endgültige und maximale Extrusionslänge.
Da sich der Knüppel in Kombination mit dem Behälter bewegt, werden alle Reibungskräfte leicht eliminiert.
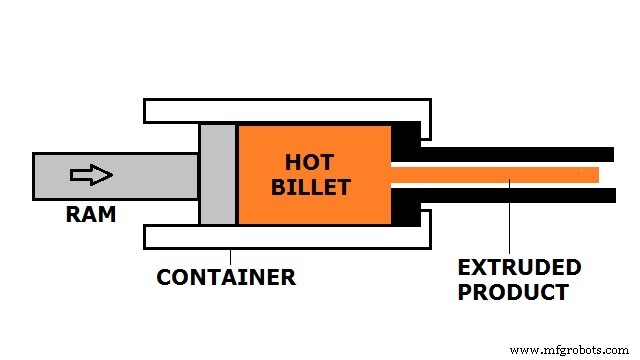
Vorteile indirekter Prozesse:
- Es ist weniger Extrusionskraft erforderlich.
- Kleinere Querschnitte können extrudiert werden.
- Reduzierung der Reibung um 30 %.
- Verbesserte Betriebsgeschwindigkeit.
- Es wird nur sehr wenig Verschleiß festgestellt.
- Extrusionsfehler oder grobkörnige Ringzonen treten seltener auf, da der Metallfluss gleichmäßiger ist.
Nachteile des indirekten Verfahrens.
- Der Querschnitt des extrudierten Materials wird durch die Größe des verwendeten Stiels begrenzt.
- Möglichkeit von Restspannungen nach der Extrusion.
- Verunreinigungen und Defekte beeinträchtigen die Oberflächenbeschaffenheit und machen das Produkt angreifbar.
#8. Hydrostatische Extrusion:
Beim hydrostatischen Extrusionsverfahren ist der Barren im Behälter von Flüssigkeit umgeben, die durch die Vorwärtsbewegung des Stempels gegen den Barren gedrückt wird. Es gibt keine Reibung innerhalb des Behälters aufgrund der Flüssigkeit und es gibt sehr wenig Reibung an der Matrizenöffnung.
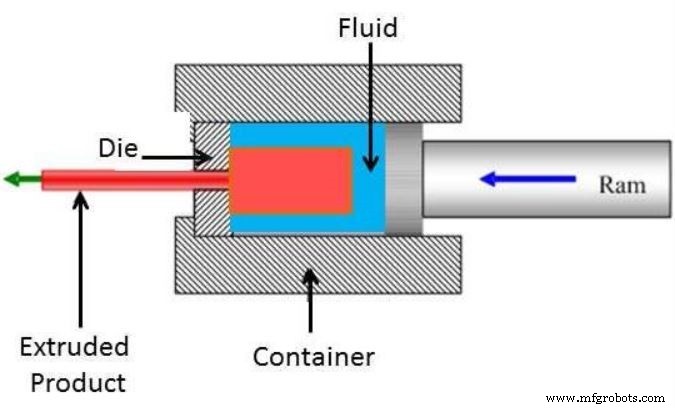
Der Knüppel wird beim Füllen der Bohrung des Behälters nicht gestört, da er einem gleichmäßigen hydrostatischen Druck ausgesetzt ist. Dies führt erfolgreich zu einem Knüppel mit einem enormen Längen-zu-Durchmesser-Verhältnis, selbst Drahtspulen oder ein ungleichmäßiger Querschnitt können fehlerfrei extrudiert werden.
Der Hauptunterschied zwischen hydrostatischem und direktem Strangpressen besteht darin, dass während des hydrostatischen Strangpressens kein direkter Kontakt zwischen dem Behälter und dem Barren besteht.
Das Arbeiten bei hohen Temperaturen erfordert den Einsatz spezieller Flüssigkeiten und Verfahren.
Wenn ein Material hydrostatischem Druck ausgesetzt wird und es keine Reibung gibt, nimmt seine Duktilität zu. Daher kann dieses Verfahren bei Metallen angewendet werden, die für typische Extrusionsverfahren zu spröde sind.
Dieser Ansatz wird bei duktilen Metallen verwendet und ermöglicht hohe Reduktionsverhältnisse.
Vorteile:
- Extrudierte Ware hat eine hervorragende Oberflächenpolitur und ist maßhaltig.
- Keine Frage von Reibung.
- Minimierter Kraftbedarf.
- Keine Knüppelrückstände bleiben dabei zurück.
- Der Materialfluss ist gleichmäßig.
Nachteile:
- Beim Betrieb bei hohen Temperaturen sollten spezielle Flüssigkeiten und Verfahren verwendet werden.
- Jeder Knüppel muss vor der Arbeit vorbereitet und an einem Ende verjüngt werden.
- Es ist schwierig, die Flüssigkeit einzudämmen.
#9. Fließpressen:
Fließpressen ist ein weiteres wichtiges Verfahren zur Herstellung von extrudierten Metallprofilen. Im Gegensatz zum traditionellen Strangpressverfahren, das hohe Temperaturen zum Erweichen des Materials erfordert, werden beim Fließpressen häufig kalte Metallbarren verwendet. Diese Knüppel werden mit hohem Druck und Effizienz extrudiert.
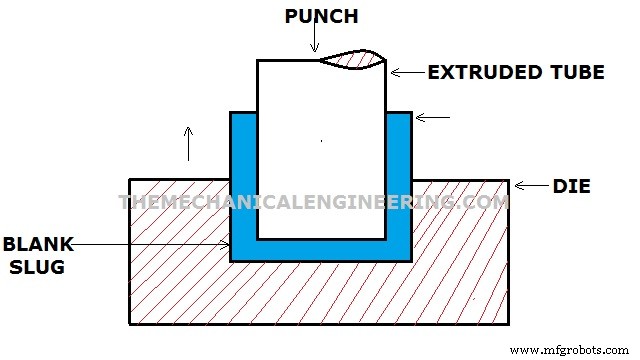
Ein geeignet geschmierter Butzen wird in einen Matrizenhohlraum platziert und während eines herkömmlichen Fließpressvorgangs mit einem Stempel in einem einzigen Hub geschlagen. Dadurch fließt das Metall durch einen Spalt zwischen Matrize und Stempel um den Stempel herum zurück.
Dieser Prozess funktioniert besser mit weicheren Materialien wie Blei, Aluminium oder Zinn.
Dieser Vorgang wird immer im kalten Zustand durchgeführt. Das Rückwärtsschlagverfahren ermöglicht sehr dünne Wandstärken. Stellen Sie zum Beispiel Zahnpastatuben oder Batterieboxen her.
Es wird mit einer schnelleren Rate und mit kürzeren Hüben durchgeführt. Anstatt Druck auszuüben, wird Stoßdruck verwendet, um den Barren durch die Matrize zu extrudieren. Das Impaktieren hingegen kann durch Vorwärts- oder Rückwärtsextrusion oder eine Mischung aus beidem erfolgen.
Vorteile:
- Starke Größenreduzierung.
- Schneller Prozess. Reduzierte Bearbeitungszeit bis zu 90 %.
- Erhöhte Produktionsrate.
- Erhöhte Toleranzintegrität.
- Bis zu 90 % Rohstoffeinsparung.
Nachteile:
- Eine sehr hohe Druckkraft ist erforderlich.
- Die Größe des Knüppels ist eine Einschränkung.
Faktoren, die die Extrusionskraft beeinflussen:
Die folgenden Faktoren beeinflussen die Extrusionskraft:
- Arbeitstemperatur.
- Design der Ausrüstung, horizontal oder vertikal.
- Art der Extrusion.
- Das Extrusionsverhältnis.
- Menge der Verformung.
- Reibungsparameter.
Extrusionsverfahren Anwendung oder Verwendung:
- Es wird häufig bei der Herstellung von Rohren und Hohlrohren verwendet. Und wird auch zur Herstellung von Kunststoffgegenständen verwendet.
- Das Extrusionsverfahren wird zur Herstellung von Rahmen, Türen, Fenstern usw. in der Automobilindustrie eingesetzt.
- Das Metall Aluminium wird in vielen Branchen im Strukturbau eingesetzt.
Industrietechnik
- Was ist Räumen? - Verfahren, Arbeiten und Arten
- Was ist Schmieden? - Definition, Prozess und Arten
- Was ist Extrusion? - Arbeitsweise, Typen und Anwendung
- Was sind die verschiedenen Arten des Rohrbiegens?
- Was sind die verschiedenen Arten von Wartungsarbeitern?
- Welche Arten des Schweißens gibt es?
- Welche Arten von Prototyping gibt es?
- Was sind die 4 Arten von Herstellungsprozessen?
- Verschiedene Arten von Lichtbogenschweißverfahren
- Verschiedene Arten von Blechumformprozessen