Die umfassendste Zusammenfassung des Casting-Prozesses
Klassifizierung des Gießverfahrens
- Sandguss
- Schalenguss
- Feinguss
- Druckguss
- Niederdruckguss
- Schleuderguss
- Schwerkraftguss
- Vakuumguss
- Druckgießen
- Verlorener Schaumguss
- Kontinuierliches Casting
Sandguss
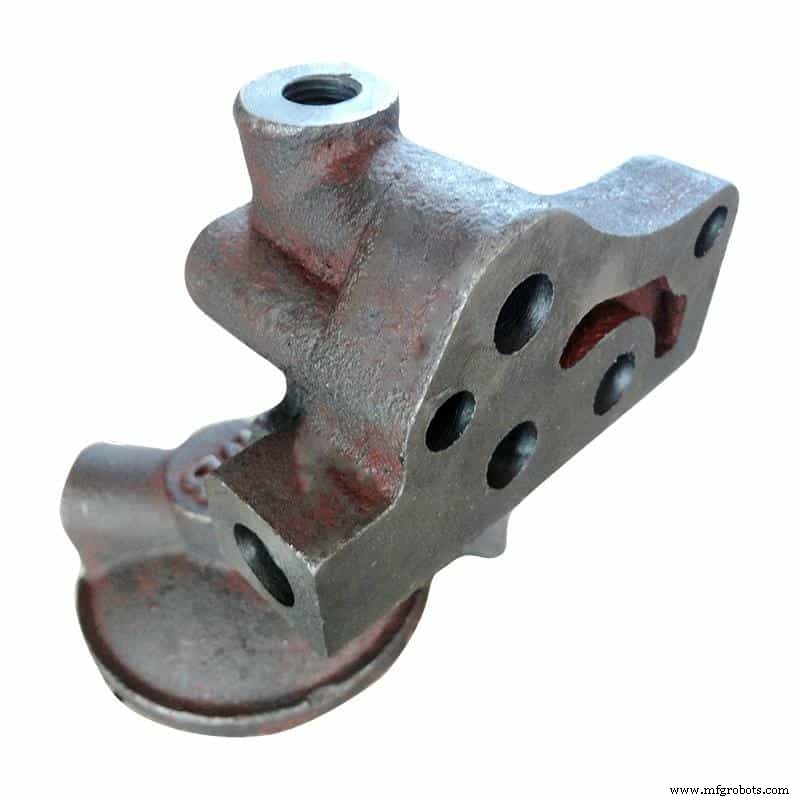
Gießverfahren zur Herstellung von Gussstücken in der Sandform. Gussteile aus Stahl, Eisen und den meisten Nichteisenlegierungen können durch Sandguss erhalten werden.
Prozessablauf:
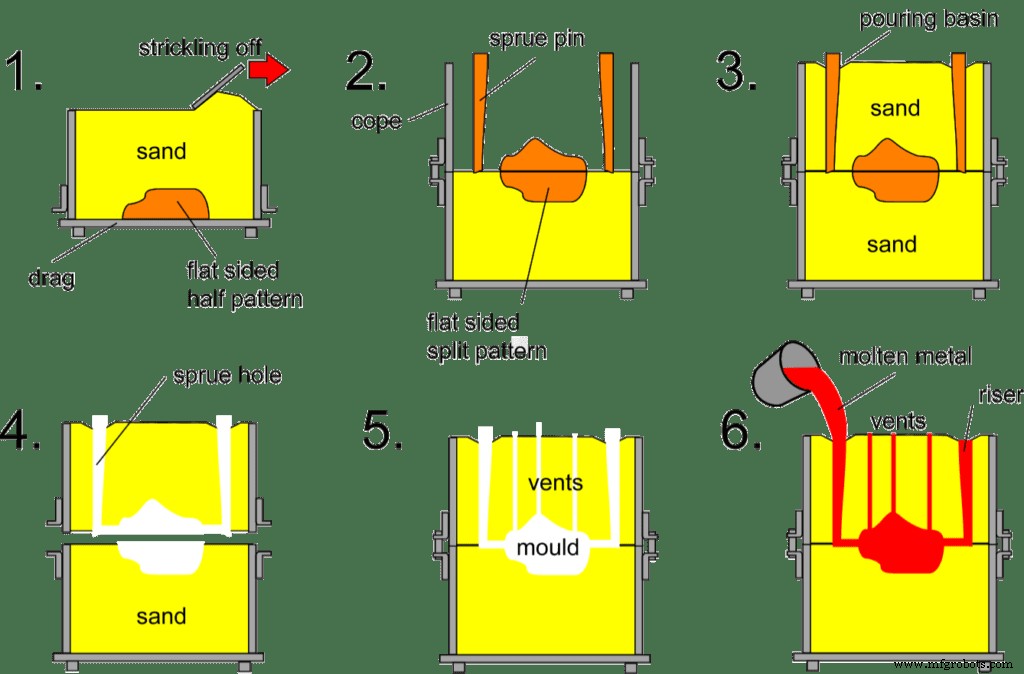
Technische Merkmale:
- Geeignet für die Herstellung von Rohlingen mit komplexer Form, insbesondere mit komplexem Innenhohlraum;
- Breite Anpassungsfähigkeit und niedrige Kosten;
- Für einige Materialien mit geringer Plastizität, wie z. B. Gusseisen, ist Sandguss das einzige Formgebungsverfahren zur Herstellung der Teile oder Rohlinge.
Bewerbung:
Zylinderblock, Zylinderkopf, Kurbelwelle und andere Gussteile von Kraftfahrzeugmotoren.
Kokillenguss
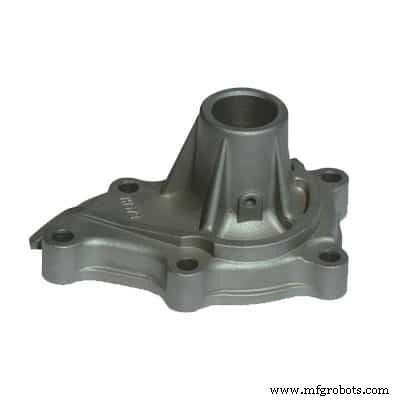
Shell Mold Casting ist ein Verbrauchsformgussverfahren, das heißt, geschmolzenes Metall wird in eine Einwegform gegossen. Der mit Harz bedeckte Sand wird auf die erhitzte wiederverwendbare Metallform aufgetragen, um ihn zu einer dünnen Formschale zu härten, und dann wird die dünne Formschale erhitzt und verfestigt, um eine ausreichende Festigkeit und Steifheit zu erreichen. Daher kann, nachdem die oberen und unteren Formschalen mit Klammern festgeklemmt oder mit Harz verklebt wurden, eine Wegwerfform gebildet werden.
Prozessablauf:
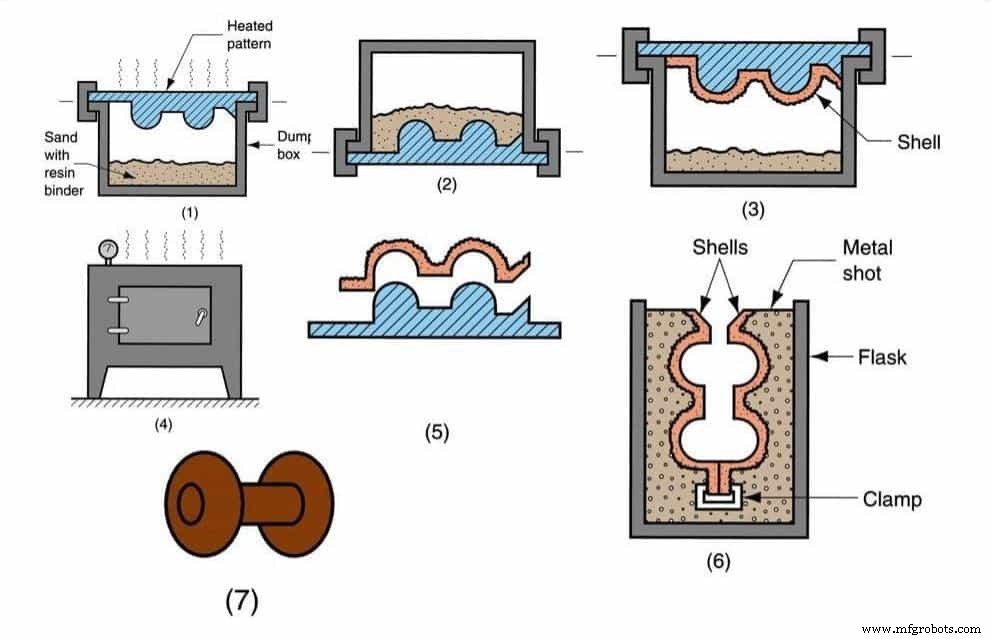
Technische Merkmale:
Vorteile:
- Kann automatisierte Massenproduktion realisieren;
- Gute Oberflächengüte und Bearbeitungsgenauigkeit, die nachfolgende Bearbeitungskosten reduzieren können;
- Große Teile und komplexe Formen können hergestellt werden;
- Niedrige Formkosten und weniger Abfall.
Nachteile:
- Das beim Schalenformgießen verwendete Harz ist teuer;
- Die wiederverwendbare Metallform muss mit hohen Kosten präzisionsgefertigt werden;
- Beim Ausgießen entsteht Reizgas;
- Gussstücke mit geringer Festigkeit und hoher Porosität.
Bewerbung:
Geeignet für die Herstellung verschiedener kleiner und mittlerer Legierungsgussteile mit großen Chargen, hoher Maßgenauigkeit, dünner Wand und komplexer Form, wie z. B. Zylinderkopf, Pleuel, Krümmer usw.
Feinguss
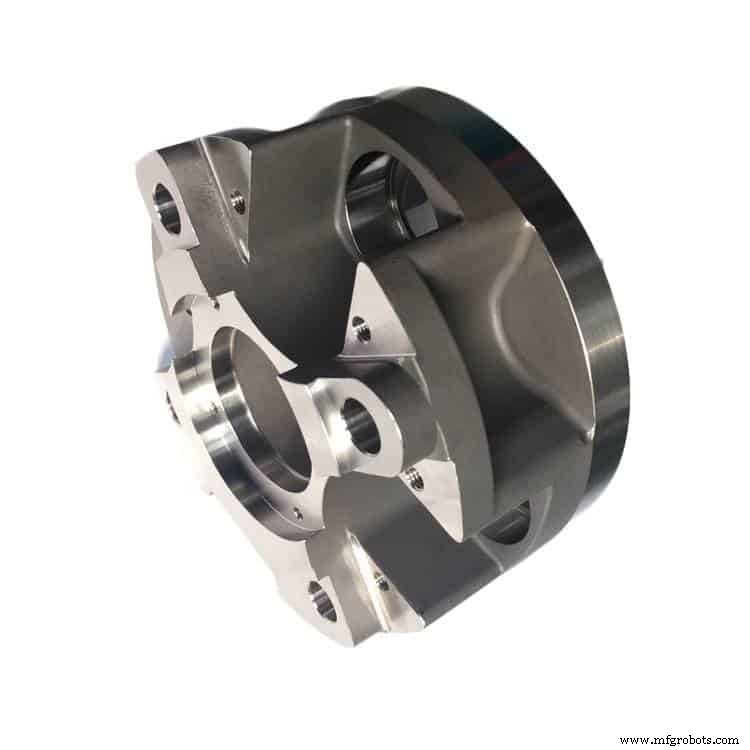
Es bezieht sich normalerweise auf ein Gießschema, bei dem das schmelzbare Material zu einem Modell verarbeitet wird, mehrere Schichten aus feuerfesten Materialien auf die Oberfläche des Modells aufgetragen werden, um eine Formschale herzustellen, und dann das Modell aus der Formschale geschmolzen wird um eine Form ohne Trennfläche zu erhalten, die nach dem Hochtemperaturrösten mit Sand gefüllt werden kann. Es wird oft als „Wachsausschmelzverfahren“ bezeichnet.
Prozessablauf:
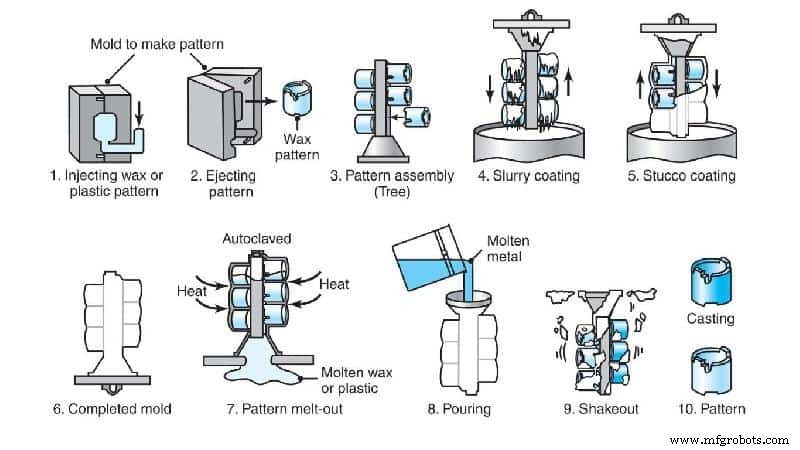
Technische Merkmale:
Vorteile:
- Hohe dimensionale und geometrische Genauigkeit;
- Hohe Oberflächenrauheit;
- Fähig, komplexe Gussteile zu gießen, und die Gusslegierung ist nicht begrenzt.
Nachteile:
Komplizierter Prozess und hohe Kosten.
Bewerbung:
Geeignet für die Herstellung kleiner Teile mit komplexen Formen, hohen Präzisionsanforderungen oder anderen Verarbeitungsschwierigkeiten, wie z. B. Schaufeln von Turbinentriebwerken.
Druckguss
Hochdruck wird verwendet, um das geschmolzene Metall mit hoher Geschwindigkeit in einen Präzisions-Metallformhohlraum zu pressen, und das geschmolzene Metall wird abgekühlt und unter Druck verfestigt, um Gussteile zu bilden.
Prozessablauf:
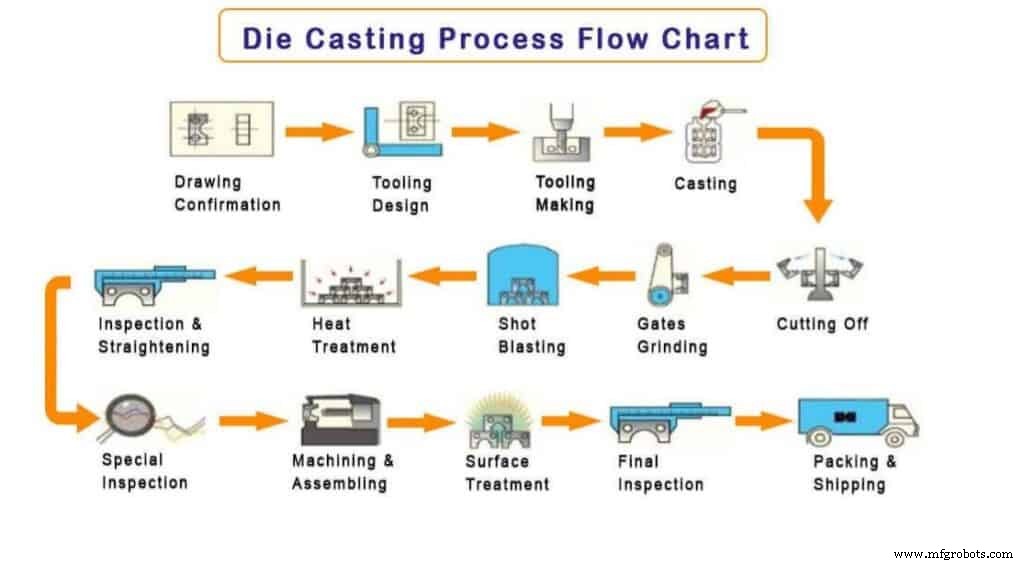
Technische Merkmale:
Vorteile:
- Geschmolzenes Metall steht unter hohem Druck und hoher Fließgeschwindigkeit;
- Hohe Produktqualität, stabile Größe und gute Austauschbarkeit;
- Hohe Produktionseffizienz und lange Lebensdauer der Druckgussform;
- Geeignet für die Massenproduktion mit guten wirtschaftlichen Vorteilen.
Nachteile:
- Gussteile neigen zu kleinen Poren und Schwindungsporosität;
- Nicht geeignet für Arbeiten unter Stoßbelastung und Vibration, aufgrund der geringen Plastizität von Druckgussteilen;
- Druckguss aus Legierungen mit hohem Schmelzpunkt könnte die Lebensdauer der Druckgussform verringern und die Ausweitung der Druckgussproduktion beeinträchtigen.
Bewerbung:
Druckgussteile wurden zuerst in der Automobilindustrie und der Instrumentenindustrie verwendet und dann schrittweise auf verschiedene Branchen ausgeweitet, wie z. B. Landmaschinen, Werkzeugmaschinenindustrie, Elektronikindustrie, nationale Verteidigungsindustrie, Computer, medizinische Geräte, Uhren, Kameras, tägliche Hardware und andere Branchen.
Niederdruckguss
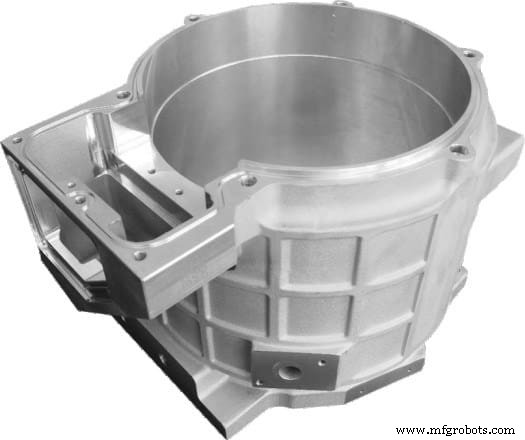
Es bezieht sich auf das Verfahren zum Füllen der Form mit geschmolzenem Metall unter niedrigerem Druck (0,02 ~ 0,06 MPa) und Kristallisieren unter Druck, um Gussteile zu bilden.
Prozessablauf:
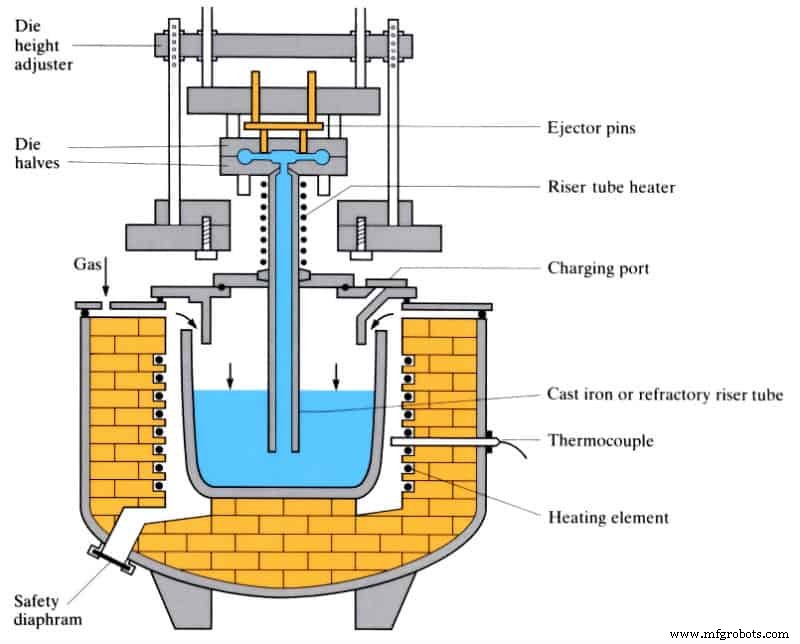
Technische Merkmale:
- Der Druck und die Geschwindigkeit während des Gießens können angepasst werden, sodass es auf eine Vielzahl unterschiedlicher Gussformen (Metallformen, Sandformen usw.) angewendet werden kann, die zum Gießen verschiedener Legierungen und Gussstücke verschiedener Größen geeignet sind;
- Füllung vom Bodeninjektionstyp wird verwendet, die Füllung mit geschmolzenem Metall ist stabil und frei von Spritzern, wodurch der Einschluss von Gas und das Auswaschen der Formwand und des Kerns vermieden werden können, was die qualifizierte Gussrate verbessert. li>
- Gussstücke kristallisieren unter Druck mit kompakter Struktur, klarer Kontur, glatter Oberfläche und hohen mechanischen Eigenschaften, was besonders für Gussstücke mit großen und dünnen Wänden von Vorteil ist;
- Der Beschickungssteg entfällt und die Metallausnutzungsrate wird auf 90 ~ 98 % erhöht;
- Geringe Arbeitsintensität, gute Arbeitsbedingungen, einfache Ausrüstung und leicht zu realisierende Mechanisierung und Automatisierung.
Bewerbung:
Hauptsächlich traditionelle Produkte (Zylinderkopf, Radnabe, Zylinderrahmen usw.).
Schleuderguss
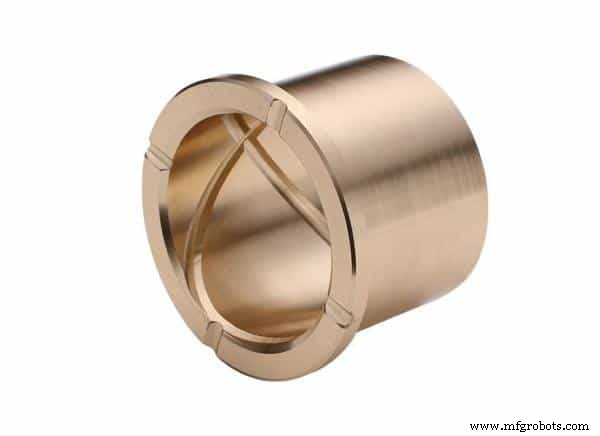
Ein Gießverfahren, bei dem geschmolzenes Metall in eine rotierende Form gegossen wird und die Form unter Einwirkung der Zentrifugalkraft gefüllt wird, um das geschmolzene Metall in Form zu verfestigen.
Prozessablauf:
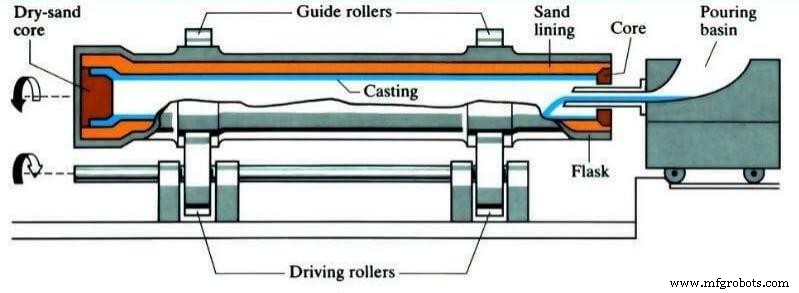
Technische Merkmale:
Vorteile:
- Es gibt fast keinen Metallverbrauch des Angusssystems und Steigrohrsystems, um die Prozessausbeute zu verbessern;
- Der Formkern ist bei der Herstellung von Hohlgussstücken unnötig, sodass die Metallfüllkapazität bei der Herstellung von langen röhrenförmigen Gussstücken stark verbessert werden kann;
- Weniger Poren, Schlackeneinschlüsse und andere Defekte, hohe Dichte und hohe mechanische Eigenschaften der Gussteile;
- Praktisch zur Herstellung von Metallgussteilen aus Zylinder und Hülse.
Nachteile:
- Es gibt bestimmte Einschränkungen bei der Herstellung von speziell geformten Gussteilen;
- Schlechte Gussqualität, ungenauer Innenlochdurchmesser, raue Innenlochoberfläche und große Bearbeitungszugabe;
- Gussteile neigen zur Entmischung nach spezifischem Gewicht.
Bewerbung:
Der Schleuderguss wurde erstmals zur Herstellung von Gussrohren eingesetzt. Das Schleudergussverfahren wird in der Metallurgie, im Bergbau, im Transportwesen, in Entwässerungs- und Bewässerungsmaschinen, in der Luftfahrt, in der Landesverteidigung, in der Automobilindustrie und in anderen Industrien zur Herstellung von Gussteilen aus Stahl, Eisen und Nichteisen-Kohlenstofflegierungen eingesetzt. Unter ihnen sind Schleudergussrohre, Zylinderlaufbuchsen und Wellenhülsen des Verbrennungsmotors am häufigsten.
Schwerkraftguss
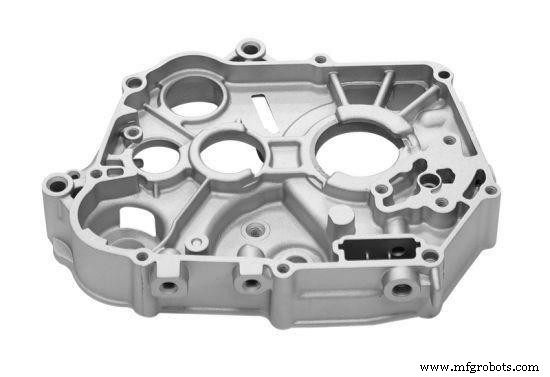
Es bezieht sich auf ein Umformverfahren, bei dem geschmolzenes Metall unter Einwirkung der Schwerkraft in eine Metallform gefüllt und in der Form gekühlt und verfestigt wird, um Gussteile zu erhalten.
Prozessablauf:
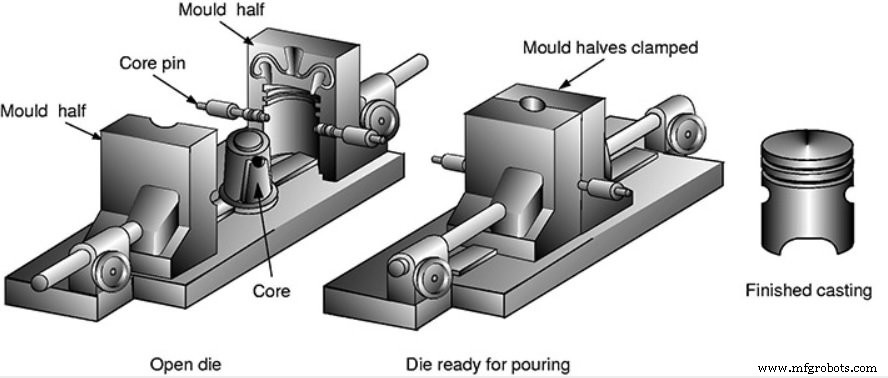
Technische Merkmale:
Vorteile:
- Große Wärmeleitfähigkeit und Wärmekapazität der Metallform, schnelle Abkühlgeschwindigkeit, dichte Gussstruktur und mechanische Eigenschaften sind etwa 15 % höher als bei Sandgussteilen;
- Gussteile mit hoher Maßhaltigkeit und geringer Oberflächenrauheit bei guter Qualitätsstabilität;
- Da der Sandkern nicht oder selten verwendet wird, kann er die Umwelt verbessern, Staub und schädliche Gase reduzieren und die Arbeitsintensität verringern.
Nachteile:
- Die Metallform selbst ist nicht luftdurchlässig, daher müssen bestimmte Maßnahmen ergriffen werden, um die Luft im Hohlraum und das durch den Sandkern erzeugte Gas abzuführen;
- Die Metallform ist nicht verformbar und das Gussteil neigt zu Rissen, wenn es erstarrt ist;
- Ein langer Herstellungszyklus und hohe Produktionskosten der Metallform können nur in der Massenproduktion eine gute wirtschaftliche Wirkung zeigen.
Bewerbung:
Der Schwerkraftguss eignet sich nicht nur für die Massenproduktion von Nichteisenlegierungen wie Gussteilen aus Aluminiumlegierungen und Magnesiumlegierungen mit komplexen Formen, sondern auch für die Herstellung von Metallgussteilen und Barren aus Eisen und Stahl.
Vakuumguss
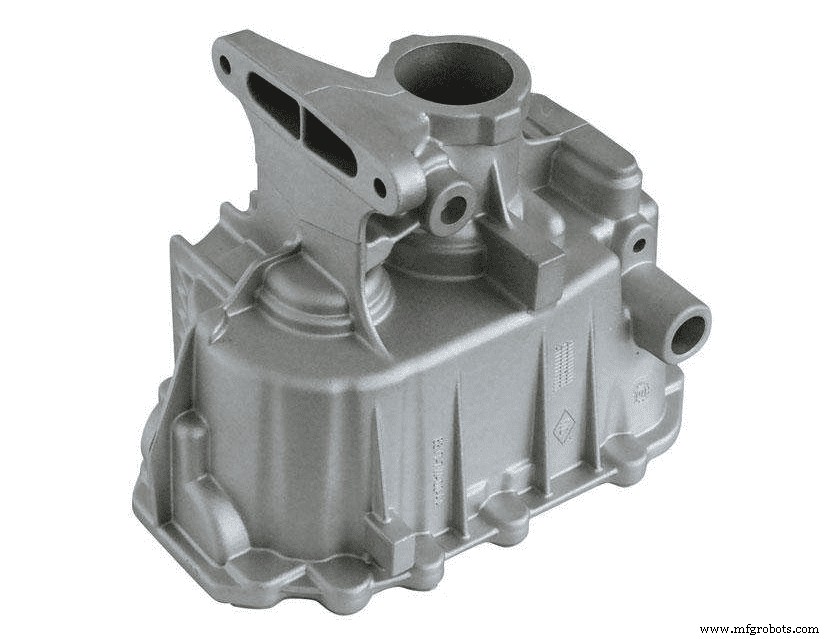
Ein fortschrittliches Gießverfahren, das die Poren und gelösten Gase in den Gussteilen beseitigt oder deutlich reduziert, indem das Gas während des Gießvorgangs aus dem Hohlraum der Gussform abgesaugt wird, wodurch die mechanischen Eigenschaften und die Oberflächenqualität der Gussteile verbessert werden.
Prozessablauf:
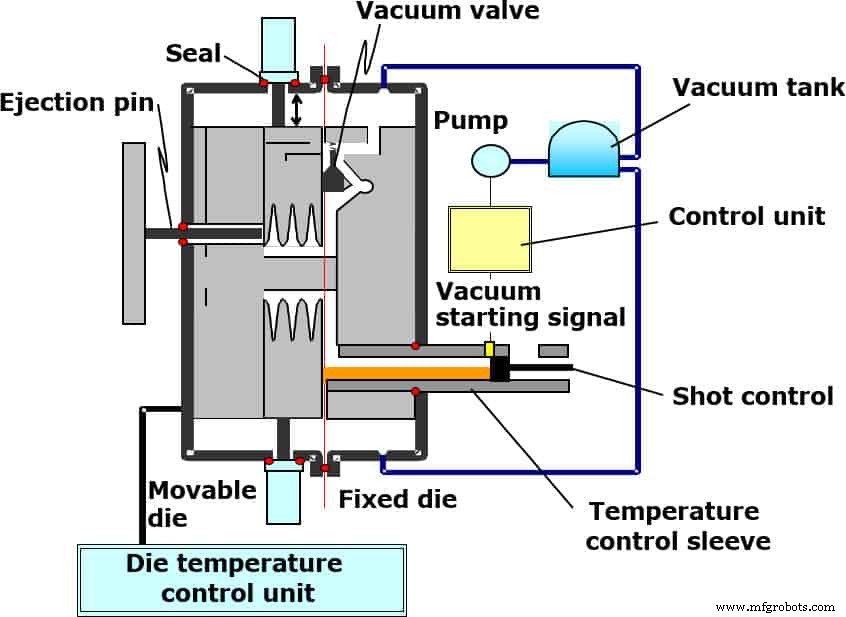
Technische Merkmale:
Vorteile:
- Beseitigen oder reduzieren Sie die Poren in den Gussteilen, verbessern Sie die mechanischen Eigenschaften und die Oberflächenqualität der Gussteile und verbessern Sie die Beschichtungsleistung;
- Reduzieren Sie den Gegendruck des Hohlraums, die Legierung mit niedrigem spezifischem Druck und schlechter Gießleistung kann verwendet werden, und es ist möglich, große Gussteile mit kleinen Maschinen zu gießen;
- Die Füllbedingungen werden verbessert und die Gussstücke mit dünneren Wandstärken können hergestellt werden.
Nachteile:
- Höhere Kosten aufgrund der komplexen Dichtungsstruktur der Form, schwierig herzustellen und zu installieren.
- Der Effekt ist nicht sehr signifikant, wenn das Vakuumgießverfahren unsachgemäß gesteuert wird.
Auspressen von Castin g
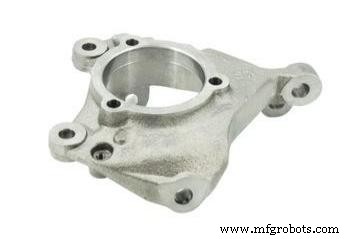
Es ist ein Verfahren zum Erstarren und Fließformen von flüssigem oder halbfestem Metall unter hohem Druck, um direkt Teile oder Rohlinge zu erhalten. Es hat die Vorteile der hohen Ausnutzungsrate von Flüssigmetall, des vereinfachten Prozesses und der stabilen Qualität. Es handelt sich um eine energiesparende Umformtechnik mit potenziellen Anwendungsperspektiven.
Prozessablauf:
Direktes Squeeze-Casting:
Beschichtungsspritzen, Legierungsgießen, Formschließen, Druckbeaufschlagung, Druckbeibehaltung, Druckentlastung, Formspaltung, Rohlingsentformung und Neueinstellung;
Indirektes Quetschen:
Beschichtungsspritzen, Formschließen, Zuführen, Formfüllen, Druckbeaufschlagung, Druckhalten, Druckentlastung, Formspaltung, Rohteilentformung und Neueinstellung.
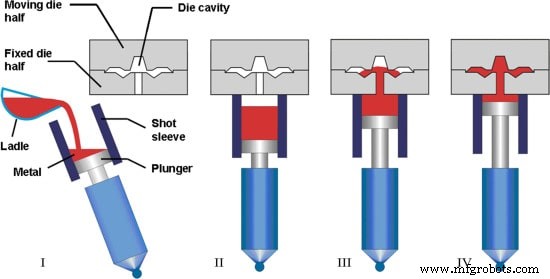
Technische Merkmale:
- Kann innere Defekte wie Poren, Lunker und Schrumpfporosität eliminieren;
- Geringe Oberflächenrauheit und hohe Maßhaltigkeit;
- Kann Gussrisse verhindern;
- Einfach zu realisierende Mechanisierung und Automatisierung.
Bewerbung:
Es kann verwendet werden, um verschiedene Arten von Legierungen herzustellen, wie z. B. Aluminiumlegierungen, Zinklegierungen, Kupferlegierungen, Sphäroguss usw.
Verlorener Schaumguss
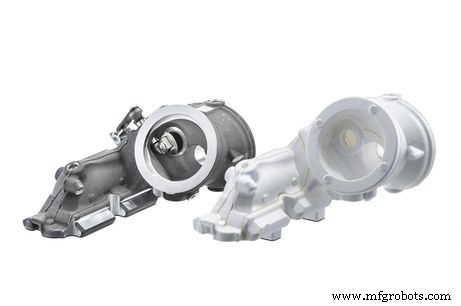
Lost Foam Casting (auch bekannt als Vollformguss):
Dabei handelt es sich um ein neuartiges Gießverfahren, das die in Größe und Form den Abgüssen ähnlichen Paraffinwachs- oder Schaummodelle zu den Modellclustern verbindet und zusammenfügt. Nach dem Bürsten und Trocknen der feuerfesten Beschichtung wird sie zum Vibrationsmodellieren in trockenen Quarzsand eingegraben, unter Unterdruck gegossen, um das Modell zu vergasen, das flüssige Metall nimmt die Position des Modells ein und bildet nach dem Erstarren und Abkühlen einen Guss.
Prozessablauf:
Vorschäumen→Schaumformen→Tauchbeschichtung→Trocknen→
Modellieren→Gießen→Sandtropfen→Reinigen
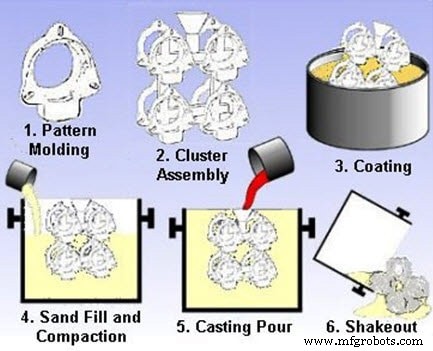
Technische Merkmale:
- Hochpräzise Gussteile, es wird kein Sandkern benötigt, wodurch die Bearbeitungszeit gespart wird;
- Keine Trennfläche, flexibles Design und hohe Gestaltungsfreiheit;
- Saubere Produktion ohne Verschmutzung;
- Investitions- und Produktionskosten senken.
Bewerbung:
Geeignet für die Herstellung von Präzisionsgussteilen verschiedener Größen mit komplexer Struktur, unbegrenzten Legierungstypen und Produktionschargen. Wie Motorkasten aus Grauguss, Krümmer aus Manganstahl usw.
Kontinuierliches Casting
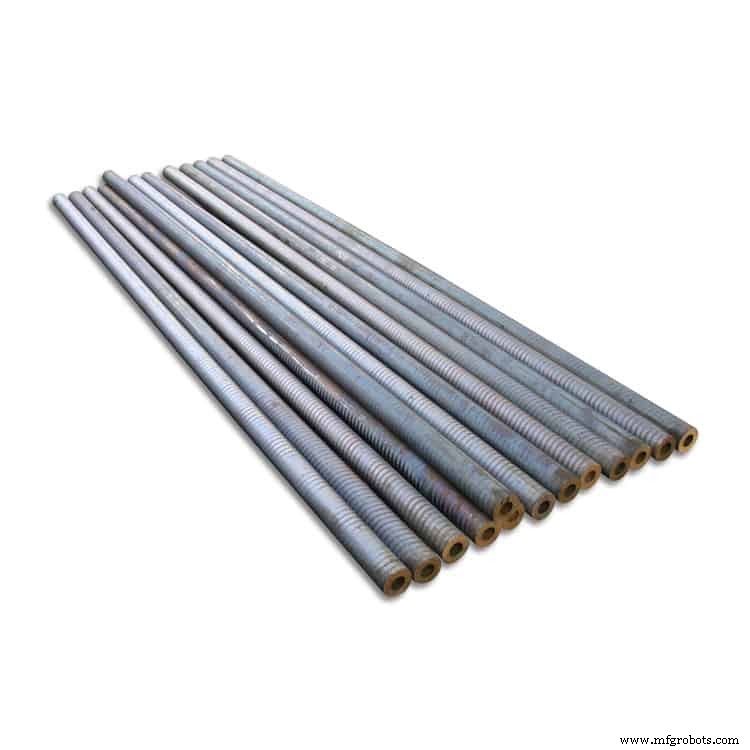
Kontinuierliches Casting ist ein fortschrittliches Gießverfahren, dessen Prinzip darin besteht, geschmolzenes Metall kontinuierlich in eine spezielle Metallform namens Kristallisator zu gießen. Der erstarrte (verkrustete) Guss wird kontinuierlich aus dem anderen Ende des Kristallisators herausgezogen. Mit diesem Gießverfahren können Gussteile beliebiger Länge oder spezifischer Länge erhalten werden.
Prozessablauf:
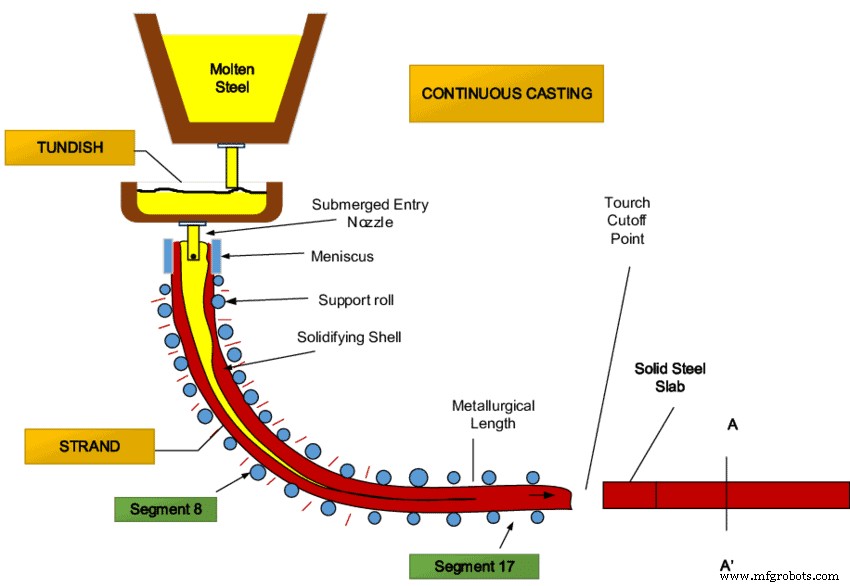
Technische Merkmale:
- klarer Kristall, gleichmäßige Struktur und gute mechanische Eigenschaften, da das Metall schnell abgekühlt wird;
- Metall sparen und Ausbeute steigern;
- Vereinfachter Prozess, Eliminierung von Modellierung und anderen Prozessen, Verringerung der Arbeitsintensität und erhebliche Reduzierung der erforderlichen Produktionsfläche;
- Einfach zu realisierende Mechanisierung und Automatisierung, Verbesserung der Produktionseffizienz.
Bewerbung:
Das kontinuierliche Gießverfahren kann zum Gießen von Stahl, Eisen, Kupferlegierungen, Aluminiumlegierungen, Magnesiumlegierungen und anderen langen Gussteilen mit unveränderten Querschnittsformen wie Barren, Brammen, Stangenrohlingen, Rohren usw. verwendet werden.
Industrietechnik
- Der 6-Schritte-Prozess des Schalenformgusses
- Die 4 wichtigsten Ansätze für den Dauerformguss
- Ein kurzer Überblick über den Casting-Prozess
- Den Prozess des Stranggießens von Stahl verstehen
- Temperaturkontrolle und -beeinflussung während des Druckgussverfahrens
- Informieren Sie sich über den Prozess des Metallgusses
- Der gesamte Prozess der Formenherstellung
- Verständnis des Prozesses zur Herstellung von Feingussschalen
- Einführung in das Edelstahl-Feingussverfahren
- Wann das Harz-Sandgussverfahren gewählt werden sollte