Werkzeughalter stellen das entscheidende Bindeglied zur Bearbeitungsproduktivität dar
Präzise Werkzeugmaschinen und fortschrittliche Schneidwerkzeuge sorgen zusammen für eine hervorragende Produktivität bei der Metallzerspanung. Die Verbindung zwischen Schneidwerkzeug und Maschinenspindel – der Werkzeughalter – ist jedoch entscheidend, um diese Produktivität voll zu erreichen. Werkzeughersteller bieten eine Vielzahl von Werkzeughalterstilen an, von denen jeder für eine optimale Leistung bei bestimmten Bearbeitungsanwendungen ausgelegt ist. Eine Zerspanungswerkstatt sollte daher ihre Auswahl an Werkzeughaltern auf ihre spezifischen Operationen sowie auf die von ihr produzierten Teile stützen. Obwohl Betriebe bestrebt sind, die fortschrittlichste Maschinentechnologie und Schneidwerkzeugmaterialien zu erwerben, legen sie oft nur minimalen Wert auf die Auswahl, Anwendung und Wartung von Werkzeughaltern, die ihren spezifischen Produktionsanforderungen am besten entsprechen.
Nicht alle Inhaber sind gleich
Keine Werkzeughaltemethode ist für alle möglichen Anwendungen geeignet. Einem Werkzeughalter, der für Hochgeschwindigkeits-Schlichtoperationen ausgelegt ist, fehlt typischerweise die Steifigkeit und Festigkeit, die erforderlich sind, um beispielsweise beim tiefen Schruppen von Rohgussteilen effektiv zu sein. Umgekehrt fehlt es einem für die Grobbearbeitung gedachten Halter in der Regel an Auswuchtqualitäten, die es ihm ermöglichen würden, bei Endbearbeitungsvorgängen bei hohen Geschwindigkeiten reibungslos zu laufen. Darüber hinaus können das robuste Design und die Masse eines Schrupphalters seinen Zugang zu feinen oder tiefen Teilemerkmalen einschränken. Zähe Werkstückmaterialien erfordern Werkzeughalter mit erhöhter Festigkeit und Steifigkeit. Die Fähigkeit eines Werkzeughalters, Vibrationen zu dämpfen und Kühlmittel zuzuführen, sind ebenfalls wichtige Auswahlkriterien.
Die Verwendung eines ungeeigneten Werkzeughalters kann zu Maßfehlern und verschrotteten Teilen sowie zu übermäßigem Verschleiß an Werkzeugmaschinenspindeln, kürzerer Werkzeuglebensdauer und einem Anstieg von Werkzeugbruch führen. Bei nicht kritischen Arbeiten kann ein preisgünstiger Werkzeughalter zufriedenstellende Ergebnisse erzielen. Aber in Betrieben, in denen wiederholbare Präzision zwingend erforderlich ist – und insbesondere wenn das Verschrotten eines teuren Werkstücks die Gewinnspanne des Teils schmälert – bietet die Investition in anwendungsorientierte, hochwertige Werkzeughalter eine kostengünstige Versicherung gegen solche unvorhergesehenen Verluste.
Für einige Werkstattleiter sind lange Versionen von Werkzeughaltern, die in einer Reihe von Anwendungen verwendet werden, eine gültige Strategie zur Kosteneinsparung. Wenn Sie jedoch immer den kürzestmöglichen Halter verwenden, wird die Steifigkeit maximiert, oberflächenzerstörende Vibrationen minimiert und die Lebensdauer des Werkzeugs verlängert.
Werkzeughalter machen weniger als zwei Prozent der gesamten Produktionskosten aus. Selbst eine Halbierung dieser Kosten führt zu vernachlässigbaren Einsparungen, während ein verschrottetes Werkstück oder ein gebrochenes Werkzeug einen messbaren finanziellen Effekt hat. Premium-Werkzeuge und -Halter können die Produktionsraten bei der Metallzerspanung steigern, sodass sich die Werkzeuginvestition sofort auszahlt. Insbesondere in Branchen wie der Herstellung von Luft- und Raumfahrtkomponenten, in denen die Stabilität des Bearbeitungsprozesses von größter Bedeutung ist, konzentrieren sich viele Hersteller vor allem auf den Erwerb hochwertiger Werkzeuge, um die Produktion fehlerhafter Teile und Zeitverschwendung mit Fehlerbehebungsmaßnahmen und Produktionsunterbrechungen zu vermeiden. Luft- und Raumfahrthersteller nehmen sich in der Regel viel Zeit, um neue Halterungskonzepte zu validieren, bevor sie für die Produktion zertifiziert werden.
Werkstückfaktoren beeinflussen die Halterauswahl
Zu den Faktoren, die die Auswahl des Werkzeughalters beeinflussen, gehören die Bearbeitbarkeit des Werkstückmaterials bei jedem Auftrag sowie die Konfiguration des endgültigen Teils, die die Abmessungen des Werkzeughalters bestimmen kann, die zum Erreichen bestimmter Konturen und/oder Merkmale erforderlich sind. Werkzeughalter sollten jedoch so einfach und benutzerfreundlich wie möglich sein, um die Möglichkeit von Bedienerfehlern zu minimieren.
Unabhängig davon, welche Werkzeughaltetechnologie angewendet wird, bestimmen die Steifigkeit, die Spindelleistung und die Fähigkeit einer Werkzeugmaschine, enge Toleranzen zu erzeugen, welche Operationen durchführbar sind. Beispielsweise ist der Versuch, Toleranzen im Mikrometerbereich auf einer verschlissenen Maschine herzustellen, Zeitverschwendung.
Die Grundelemente einer Werkzeugmaschine spielen eine Schlüsselrolle – eine schnelle Maschine mit Linearführungen wird die Vorteile von Werkzeughaltern, die für Hochgeschwindigkeitsanwendungen ausgelegt sind, am besten nutzen, während Maschinen mit Hohlführungen Unterstützung für die Schwerzerspanung bieten. Eine Multitasking-Maschine nutzt die Möglichkeiten von Werkzeughaltern, die sowohl Dreh- als auch Fräs-/Bohroperationen ausführen können, voll aus.
Die verwendete Bearbeitungsstrategie beeinflusst auch die Auswahl des Werkzeughalters. Werkstätten können beispielsweise Werkzeuge auswählen, um die Produktivität beim Hochgeschwindigkeitsschneiden (HSC) mit geringeren Schnitttiefen oder beim Hochleistungsschneiden (HPC) zu maximieren, bei denen der Schwerpunkt auf der Erzeugung hoher Metallabtragsraten auf Maschinen mit ausreichender Leistung, aber begrenzter Geschwindigkeit liegt .
Ein niedriger, wiederholbarer Rundlauf kann dazu beitragen, einen konstanten Werkzeugeingriff sicherzustellen und dadurch Vibrationen zu reduzieren und die Werkzeuglebensdauer zu maximieren. Die Auswuchtung ist entscheidend, und ein hochwertiger Werkzeughalter sollte bei G2,5-25000 RPM-Qualität (1 g.mm) feingewuchtet sein. Bearbeitungsbetriebe können ihre eigenen Untersuchungen durchführen und sich mit ihren Werkzeuglieferanten beraten, um das oder die Werkzeughaltesysteme zu bestimmen, die ihre Produktionsanforderungen kostengünstig erfüllen.
Jeder Halter hat seine Nische
Ob einfache Weldon-, Spannzangen-, Warmschrumpf-, mechanische oder hydraulische Ausführung, auch Werkzeugaufnahmen sollten auf die konkreten betrieblichen Anforderungen abgestimmt sein. Einfache Schaftfräserhalter für Weldon-Schaftwerkzeuge zum Beispiel sind starr, einfach zu handhaben, können hohe Drehmomente übertragen und bieten eine sichere und starke Klemmung mit starkem Auszugsschutz. Sie eignen sich gut für schweres Schruppen, haben aber keinen präzisen Rundlauf. Im Allgemeinen sind sie von Natur aus unausgeglichen und eignen sich nicht produktiv für Anwendungen mit hohen Drehzahlen.
Spannzangenfutter und Wechselspannzangen sind die gängigste Form der Rundwerkzeug-Aufnahmetechnik. Kostengünstige ER-Typen sind in einer Vielzahl von Größen erhältlich und bieten ausreichend Grip für zuverlässige leichte Fräs- und Bohrarbeiten. Hochpräzise ER-Spannzangenhalter zeichnen sich durch einen geringen Rundlauf (<5 μm an der Werkzeugspitze) und ein symmetrisches Design aus, das für Hochgeschwindigkeitsoperationen ausgewuchtet werden kann, und verstärkte Versionen sind für die Schwerzerspanung erhältlich. ER-Halter ermöglichen einen schnellen Wechsel und können eine Reihe von Werkzeugdurchmessern aufnehmen.
Warmschrumpfhalter bieten eine starke Klemmkraft, eine Rundlaufgenauigkeit von 3 μm bei 3xD und hervorragende Wuchteigenschaften. Ihre kleinen, einfachen Nasenkonfigurationen bieten einen guten Zugang zu engen Teilemerkmalen.
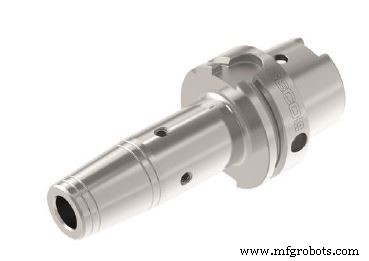
Verstärkte Versionen können mittelschweres bis schweres Fräsen ausführen, aber die Greifkraft hängt von den ID-Toleranzen des Werkzeugschafts und Halters ab. Schrumpfwerkzeuge erfordern den Kauf einer speziellen Heizeinheit, und der Heiz-/Kühlprozess erfordert mehr Einrichtungszeit als das einfache Wechseln der Spannzangen.
Mechanische Fräsfutter bieten eine starke Spannkraft und hohe radiale Steifigkeit durch mehrreihige Nadellager. Das Design ermöglicht schweres Fräsen und schnelle Werkzeugwechsel, aber der Rundlauf kann größer sein als der von Spannzangensystemen. Mechanische Spannfutter sind im Allgemeinen größer als andere Werkzeughaltertypen, was den Werkzeugzugriff auf einige Teilemerkmale einschränken kann.
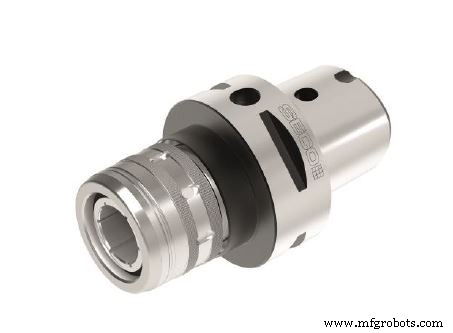
Hydrodehnspannfutter, die den Öldruck zur Erzeugung der Spannkraft verwenden, haben weniger interne Elemente als mechanische Spannfutter und haben daher ein vergleichsweise schlankeres Profil. Hydraulische Spannfutter weisen einen geringen Rundlauf auf und eignen sich zum Reiben, Bohren und leichten Fräsen bei hohen Spindeldrehzahlen, sind jedoch empfindlich gegenüber starken radialen Belastungen.
Genauso wichtig wie ein Halter ein Schneidwerkzeug sichert, ist auch die Befestigung an einer Werkzeugmaschinenspindel. Das Spindel- oder Kegelende eines Werkzeughalters bestimmt die Drehmomentübertragungsfähigkeit und legt die Genauigkeit der Werkzeugzentrierung fest. Herkömmliche BT-, DIN- und CAT-Werkzeugkegel sind auf kleineren Maschinen effektiv, können jedoch in ihrer Hochgeschwindigkeitsfähigkeit eingeschränkt sein. Versionen, die sowohl am Halterkonus als auch an der Fläche Kontakt bieten, sorgen für erhöhte Steifigkeit und Genauigkeit, insbesondere in Situationen mit langem Überhang. Größere Konusgrößen sind erforderlich, um ein größeres Drehmoment zuverlässig zu übertragen. Ein HSK-E32-Halter kann beispielsweise einen HSK-A125A in einer schweren Zerspanungssituation nicht ersetzen.
Die Wahl des Konustyps des Halters wird oft durch regionale Vorlieben bestimmt. HSK entstand in Deutschland Mitte der 1990er Jahre, als 5-Achs-Maschinen immer beliebter wurden. CAT-Kegel sind überwiegend in den Vereinigten Staaten zu finden, während in Asien BT-Schäfte beliebt sind, häufig in Versionen mit Kegel-/Flächenkontakt.
HSK ist für die 5-Achs-Bearbeitung weit verbreitet. PSC- (Polygonspannsystem:Capto) und KM-Verbindungen werden hauptsächlich auf Multitasking-Maschinen verwendet und sind heute ISO-Standards. Sowohl KM als auch Capto sind ebenfalls modulare Systeme, die die Montage spezifischer Werkzeuge in verschiedenen Längen durch Stapeln von Verlängerungen oder Reduzierstücken ermöglichen. Werkzeughalterstile, die es ermöglichen, Teile in einer Aufspannung zu drehen, zu fräsen oder zu bohren, werden immer beliebter, da Multitasking-Maschinen immer häufiger verwendet werden.
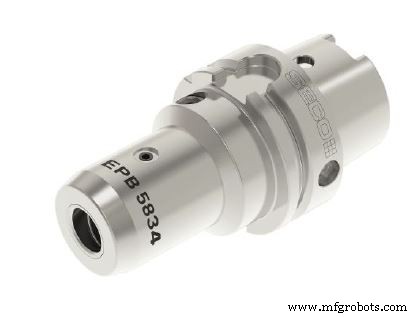
Während es proprietäre Werkzeughaltesysteme gibt, die einzigartige Halter und Spannzangen auf innovative Weise verwenden, um beeindruckende Ergebnisse zu erzielen, muss eine Werkstatt ihre Vorteile berechnen. Diese Systeme sind in der Regel mit höheren Kosten und einer begrenzten Werkzeugauswahl von einem einzigen Anbieter verbunden.
Kosten und andere Überlegungen
Während die Grundkosten eines hydraulischen oder mechanischen Halters im Vergleich zu einem Spannzangen- oder Schrumpfhalter höher sind, spielen andere Faktoren eine Rolle, wie z. B. die Kosten des Schrumpfheizsystems und die zum Werkzeugwechsel erforderliche Zeit. Es ist auch erforderlich, einen Schrumpfsitzhalter zu haben, der zu jedem Werkzeugdurchmesser passt, im Vergleich zur Anpassung an unterschiedliche Durchmesser durch einfaches Wechseln der Spannzangen in einem Spannzangenhaltersystem.
Maschinenbediener und Werkzeugwartungspersonal spielen ebenfalls eine wichtige Rolle für den erfolgreichen Einsatz von Werkzeughaltern. Wie bei Werkzeugmaschinen und anderen Fertigungsanlagen müssen Werkzeughalter korrekt verwendet und gewartet werden, um ihre Vorteile zu maximieren und ihr volles Potenzial auszuschöpfen. Beispielsweise muss der Bediener den Werkzeugschaft bis zu seiner vollen Länge in den Halter einführen, da ein unsachgemäßer Sitz zu einer die Genauigkeit zerstörenden Vibration oder sogar zum Auswurf des Werkzeugs führt. Die Einhaltung der Spezifikationen für die Werkzeugmontage ist von entscheidender Bedeutung. Bediener sollten beim Anziehen eines Spannfutters keinen Verlängerungsgriff verwenden, um ein übermäßiges Drehmoment aufzubringen, das die Spannzange verdreht und zu einer Fehlausrichtung des Werkzeugs führt.
Auch die Werkzeugwartung ist wichtig, wird aber oft vernachlässigt. Bediener sollten Halter vor Gebrauch immer reinigen und auch die Werkzeugmaschinenspindel inspizieren. Halter sollten sauber und trocken gelagert werden, mit Kappen zum Schutz des Werkzeugkegels. Der Flüssigkeitsdruck von Hydrodehnspannfuttern sollte regelmäßig überprüft werden.
Schlussfolgerung
Maschinenwerkstätten müssen die Bedeutung von Werkzeughaltern im Bearbeitungssystem erkennen und lernen, wie die richtige Abstimmung des richtigen Werkzeughalters auf ihre spezifischen Werkzeugmaschinen, Bearbeitungsstrategien und Werkstücke die Produktivität steigern und Kosten senken kann. Gleichzeitig bieten Werkzeughalterhersteller eine umfassendere Auswahl an Haltern an (siehe Seitenleiste) entwickelt, um individuelle betriebliche Anforderungen zu erfüllen.
Zukünftige Verbesserungen gehen über die Halterungshardware selbst hinaus. Die Werkzeugverwaltung über Software und RFID-Tags ist ein Element der datenbasierten Fertigung und wird immer häufiger. Zu den Fortschritten in der Werkzeughaltertechnologie gehören mit Sensoren ausgestattete Halter, die eine Überwachung der Kräfte auf den Halter in Echtzeit ermöglichen. Die gesammelten Daten ermöglichen eine prozessinterne Anpassung der Bearbeitungsparameter entweder durch den Bediener oder sogar automatisch über künstliche Intelligenz (KI) in Verbindung mit der Maschinensteuerung. Diese und andere neue Technologien werden die produktiven Beiträge, die Werkzeughalter bei Bearbeitungsvorgängen leisten, weiter verstärken.
Industrietechnik
- Die Geschichte der Fräsmaschine:Bearbeitungsmaschinen, die einen langen Weg zurückgelegt haben
- Die Hauptunterschiede zwischen 3-Achsen- und 5-Achsen-Bearbeitung
- Unwucht:Das versteckte Problem, das Maschinenwerkstätten lösen müssen
- Bearbeitung von Titan:Finden Sie die richtigen Fräswerkzeuge für Superlegierungen
- Oberflächeninspektion in die Hände des Werkzeugmaschinenbedieners legen
- Unterricht in Hochleistungsbearbeitung:Werkzeughalter nicht vergessen
- Die Bedeutung von Kühlmitteln bei der Bearbeitung
- CNC-Bearbeitung:Ein wichtiger Prozess in der Fertigung
- Das Herz der Werkzeugmaschine:Werkzeugmaschinenspindeln.
- Fräsen und Drehen gemeinsam zum Vorteil der Produktivität