Beseitigung von Hindernissen zur Optimierung neu installierter Schleifprozesse
Im Allgemeinen durchlaufen neue Großserienlinien, die komplexe Teile herstellen, die Schleifprozesse umfassen, wie z. B. Schaufeln und Leitschaufeln für Automobiltriebwerke oder Flugzeugtriebwerke, verschiedene Phasen von der Maschinenbeschaffung bis zur eigentlichen Produktion, wie in Abbildung 1 dargestellt. Wenn diese Zeilen einen Prozess beinhalten, der als „hohes Risiko gilt „Es wird mit „Entwicklungszeit“ als Teil der Leistungsbewertung und des Erwerbs der Mühle (Schritte 4 und 5) durch Testen und Verfeinern geplant. Dies ist eine effektive Strategie und reduziert die mit dem Programmstart verbundenen Probleme erheblich, kann jedoch zeitaufwändig und teuer sein; Sehr oft sind Werkstückmuster nicht einmal verfügbar oder Prototypen, die weiteren Konstruktionsänderungen unterliegen. In solchen Fällen oder für abweichende Komponentendesigns, aber nicht radikal anders von bestehenden Konstruktionen wird selten „Optimierungszeit“ vor der eigentlichen Maschinenqualifizierung eingeplant.
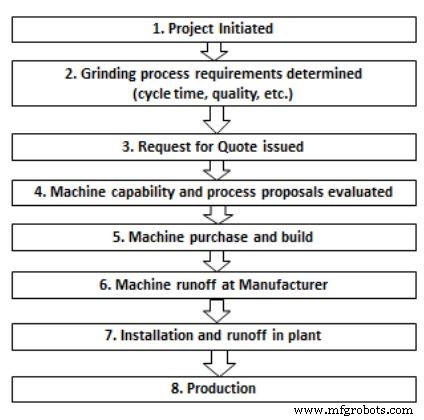
Wenn Maschinen mit „nicht-radikalem ” Prozesse liegt der Fokus auf Teilequalität und Zykluszeit. Radspezifikationen können gut ausgewählt werden, um die höchste Qualität inmitten von Unsicherheiten des neuen Teiledesigns und ihrer Auswirkungen auf das Halten von Teiltoleranzen auf oft strengeren CpK-Spezifikationen als für die Produktion erforderlich zu gewährleisten. Außerdem werden aus Kosten- oder Verfügbarkeitsgründen oft nur 50 oder 100 Teile zur Qualifizierung bereitgestellt, was die Etablierung eines langfristig stabilen Prozesses fraglich macht. Es gibt normalerweise nicht viel Zeit oder Komponenten, um die Werkzeug- oder Schleifmittelkosten pro Teil zu optimieren. Nach der Installation übernimmt in vielen Fällen eine „Wenn es nicht kaputt ist, repariere es nicht“-Haltung und Prozesse werden blockiert. Eine Optimierung wird selten versucht.
Es ist daher sehr wichtig, dass der „zusätzliche Schritt“ der Optimierung als abschließendes „Audit“ des Prozesses betrachtet wird. Meistens könnte dieser Schritt einfach eine „Abstimmung“ des Prozesses sein, sodass eine erneute Qualifizierung des gesamten Prozesses nicht erforderlich ist, aber gelegentlich können ausreichend große Möglichkeiten aufgedeckt werden, die größere Änderungen am Fahrrad und/oder der Laufradspezifikation rechtfertigen würden. Eine Kosten-Nutzen-Analyse würde durchgeführt werden, um festzustellen, ob eine größere Prozessänderung vorgenommen werden sollte.
Es gibt mehrere Gründe, warum fehlende „Optimierungszeit“ zu suboptimalen Prozessen führen kann:
- Zyklen können in der Maschine akzeptabel funktionieren, aber nicht „radfreundlich“ sein. Das heißt, die Laufradlebensdauer kann suboptimal sein
- Die Radtechnologie entwickelt sich weiter. Schätzungen, die anhand bestehender Technologien vorgenommen wurden, sind möglicherweise nicht optimal für neue Technologien
- Kleine Abweichungen in der Teilekonfiguration, im Maschinendesign und in den Qualitätsanforderungen machen die Prozessoptimierung außerhalb der Produktionslinie sehr schwierig. Dies liegt daran, dass die Produktionslinie viele Teile und eine Umgebung mit echten Variationen und Messtechnik bietet. Diese beiden Qualitäten liefern einen Test für die „Robustheit“ des „optimierten“ Prozesses.
Beispiele:
Der in Abbildung 2 abgebildete Schleifzyklus wurde vom OEM geliefert, der in einer Anlage installiert ist, und befindet sich derzeit in der Produktion. Dieser Zyklus funktioniert gut und produziert akzeptable Teile, aber er ist nicht „radfreundlich“.
Die „Unfreundlichkeit“ des Rads dieses Zyklus ist auf die große Spitze (Leistung/Kraft) zu Beginn des Zyklus zurückzuführen. Der Scheibenverschleiß ist proportional zum Quadrat der Schleifkraft, hohe Kräfte führen zu einem schnellen Verschleiß der Scheibe. In diesem Fall würde die Verringerung des schnellen Vorschubs und die Erhöhung des mittleren Vorschubs die Lebensdauer der Scheibe verlängern, während die Zykluszeit und die Teilequalität erhalten bleiben.
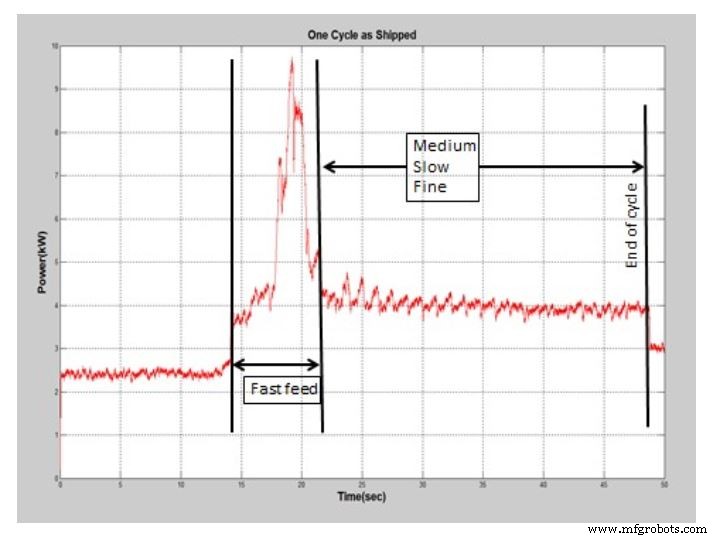
Ein Kreislauf im Prozess der Optimierung
In einem kürzlichen ungewöhnlichen Fall hat der Hersteller zugestimmt, den Schleifprozess „in situ“ zu optimieren. Anfänglich wurde der Schleifzyklus geändert, um ihn, wie oben besprochen, "scheibenfreundlicher" zu machen. In diesem Fall war der freundlichere Zyklus auch ~5 Sekunden kürzer als der anfängliche Zyklus.
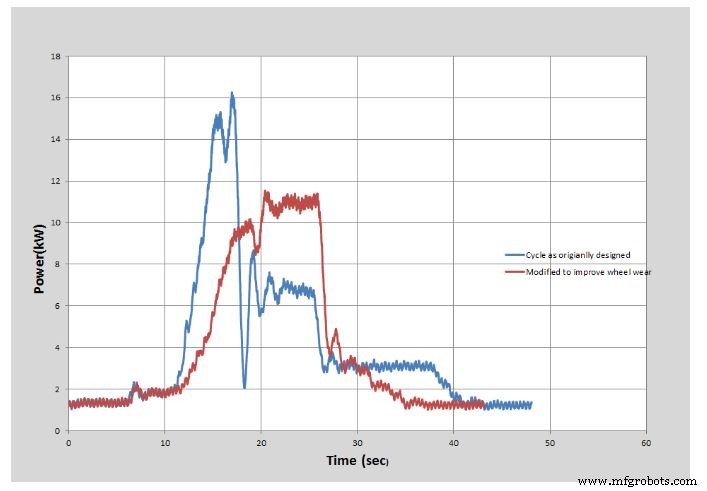
Nachdem der modifizierte Zyklus mehrere Wochen lang gelaufen war, um die kontinuierliche Teilequalität zu validieren, wurde die Anzahl der Teile pro Abricht von 8 auf 20 erhöht und die Abrichttiefe von 0,03 mm auf 0,02 mm reduziert. Dieser Prozess läuft nun seit ca. 6 Wochen ohne wesentliche Veränderung der Teilequalität. Eine Zusammenfassung der Kosteneinsparungen pro Jahr ist unten aufgeführt.
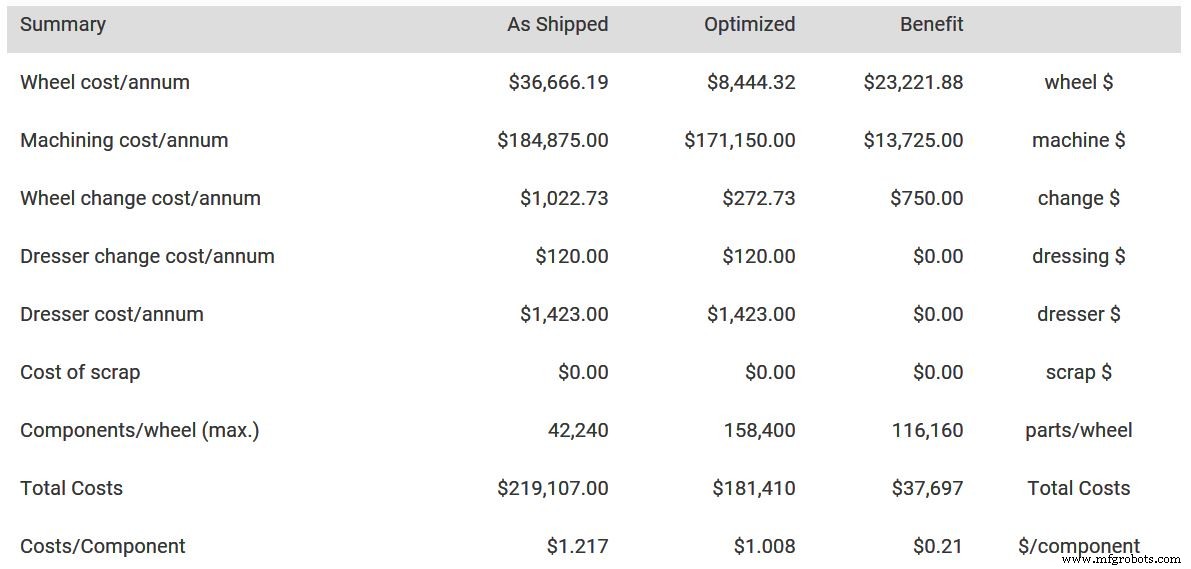
Strategie zur Optimierung
Die Lösung, wie im zweiten Beispiel dargestellt, besteht darin, Zeit und Teile in den frühen Phasen der Produktion (zwischen den Schritten 7 und 8 in Abbildung 1) einzuplanen, um mit dem Maschinenbauer und dem Werkzeug-/Schleifmittel-Anwendungstechnik-Team an der Prozessoptimierung zu arbeiten . In dieser Phase sollten zumindest Geräte zur Leistungsüberwachung verwendet werden, um die Zyklusbewertung und -entwicklung zu unterstützen. Mit diesem zusätzlichen Schritt kann der Prozess bei längeren Stückzahlen auf Stabilität überwacht werden, was Probleme ans Licht bringen und/oder Möglichkeiten für Verbesserungen bieten kann.
Der potenzielle Gewinn aus diesem Schritt ist groß, da in dieser Phase vorgenommene Verbesserungen/Kosteneinsparungen während des gesamten Projektlebenszyklus bestehen bleiben.
Zuvor auf Norton Abrasives vorgestellt
Kaufen Sie unsere Auswahl an Norton Griding Wheels auf MSCdirect.com.
Industrietechnik
- Ausbau betrieblicher Standards und Prozesse
- Airbus stellt die Fabrik der Zukunft vor
- Ausfallarten von Anlagenzuverlässigkeitsprozessen
- Optimierung der Fertigungsabläufe in Ihrer Produktionsstätte
- Schleifscheiben:Herstellung und Qualität | Branchen | Metallurgie
- Die wertvolle Rolle der Prozessautomatisierung bei der Verfolgung von ESG
- Was ist Honen? - Definition, Prozess und Werkzeuge
- So implementieren Sie Geschäftsprozessmanagement
- Flachschleifservice:Prozess und Präzision
- Grundlagen des Außenrundschleifens