8 kritische Sicherheitsverfahren, die Lagerverwalter befolgen sollten
Ein gut funktionierendes Lager ist hochgradig organisiert, und moderne Abläufe werden von Tag zu Tag effizienter. Ein angemessenes Sicherheitsmanagement geht weit über die grundlegenden bekannten Gefahren hinaus und antizipiert potenzielle Fehler in jedem Bereich des Lagers und bei jedem Vorgang. Die Todesrate in Lagerumgebungen ist basierend auf Daten der letzten Jahre fast doppelt so hoch wie der nationale Durchschnitt, und es ist sicherlich ein Bereich, der Respekt und Management mit einem robusten Sicherheitsprogramm verdient.
Laut OSHA waren einige der Hauptfehler in einer Lagerumgebung, die zu Verletzungen geführt haben, auf unsachgemäße Verfahren, unsichere Verwendung von Gabelstaplern, unsachgemäßes Stapeln von Paletten, schlechte Lagergestaltung und Verletzungen durch sich wiederholende Bewegungen zurückzuführen. Hier sind acht kritische Sicherheitsverfahren, die jeder Lagerleiter überprüfen und anhand von Best Practices zum Schutz vor diesen Risikobereichen verbessern kann.
Verladedock-Fahrzeugbewegungsprotokolle 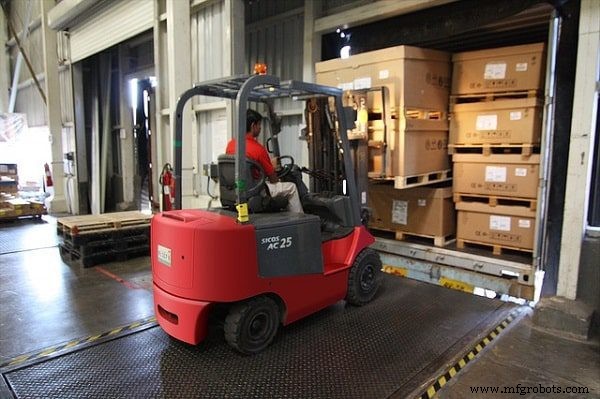
Die Laderampe ist ein stark frequentierter Bereich im Lager, in dem an jedem Tag viel los ist, da Lastwagen be- und entladen und Materialien für den Versand bereitgestellt werden. Arbeiter in der Gegend müssen bei diesen Aktivitäten wachsam sein, da es verheerend sein kann, zwischen einem Gabelstapler oder Lastwagen und der Laderampe eingeklemmt zu werden. Die Verfahren, die Ihre Gabelstaplerfahrer zum Bereitstellen, Empfangen und Laden von Materialien befolgen, sind entscheidend, um sicherzustellen, dass Bewegungen vorhersehbar und leicht zu überwachen sind. Streng durchgesetzte Geschwindigkeitsbegrenzungen, klare Warnschilder und das Freihalten des Docks und der Umgebung sollten Teil aller Schulungen sein.
Gabelstaplerbetrieb und Sturzgefahren
Jedes seriöse Lager verfügt über klare Verfahren, die für das Fahren mit Gabelstaplern und grundlegende Vorgänge im gesamten Lager definiert sind. Aber eine potenziell übersehene Gefahr in jedem Lager ist der Zusammenbruch von Paletten zur Erfüllung von Bestellungen. Dies kann ebenerdig erfolgen, aber in einigen Fällen ist es einfacher, einen Arbeiter mit einem Gabelstapler oder mit Laufstegen zur Palette zu bringen. Zu einem angemessenen Absturzschutz gehört eine geeignete Gabelstaplerplattform, die bei Bedarf für eine Person geeignet ist, die Abdeckung aller Zwischengeschosse und Laufstege sowie angemessene Geländer ohne unnötige freiliegende Lücken.
Lock-Out-Tag-Out-Verfahren für Förderer
Die Automatisierung in der Lagerhalle wird zu einem Standardbestandteil der Auftragsabwicklung und bringt eine Reihe beweglicher Teile mit sich. Insbesondere Förderbänder können einen unglaublichen Einfluss auf die Effizienz haben und helfen, Inventar schnell und vorhersehbar durch die Anlage zu bewegen. Da die Förderer eine Reihe von potenziellen Quetschpunkten und die Möglichkeit zum Herunterfallen von Gegenständen aufweisen, ist es wichtig, dass geeignete Schutzvorrichtungen zwischen Arbeitern und der Ausrüstung vorhanden sind. Darüber hinaus sollten die Lock-out- und Tag-out-Verfahren, die Mitarbeiter für die Wartung verwenden, sehr robust sein, um jeden unnötigen Kontakt zu vermeiden, während die Förderbänder in Bewegung sind.
Palettenlagerung und -regale 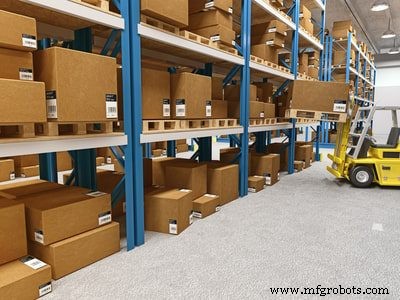
Das Verpacken und Lagern von Paletten ist ein hochgradig manueller Vorgang, der viel Interaktion zwischen Personal, Paletten und Regalen erfordert. Sie können Sicherheitsrisiken durch herabfallende Gegenstände vermeiden, indem Sie sicherstellen, dass Ihre Verfahren zum Packen von Paletten allgemeine Probleme berücksichtigen. Das Personal sollte darin geschult werden, Paletten ordnungsgemäß zu verpacken und zu sichern, persönliche Schutzausrüstung (PSA) zu tragen, ein empfohlenes Stapelmuster zu verwenden und die Herstellerrichtlinien für sichere Stapelhöhe und Gewichtskapazität zu befolgen. Verfahren, die Mitarbeiter auch anweisen, Paletten auf lose Nägel oder andere Probleme zu untersuchen, und sie ordnungsgemäß anweisen, Regale oder andere Bereiche, die Schäden verursachen können, nicht zu betreten, können zusätzliche Sicherheitsebenen hinzufügen.
Implementieren Sie ein Nummerierungssystem für Lagerstandorte
Ein Nummerierungssystem für Lagerplätze hilft, unnötige Gänge zu vermeiden, indem es eine klare Anleitung bietet, um Mitarbeiter zu den richtigen Bereichen zu leiten. Durch die Verringerung der Gangüberlastung haben die Mitarbeiter leichteren Zugang zu Regalen und anderen Lagerbereichen, was wiederum Unfälle reduziert. Verwenden Sie Schilder und Lageretiketten, um sicherzustellen, dass alle Bereiche deutlich gekennzeichnet sind, einschließlich retroreflektierender Schilder und Etiketten für Langstrecken-Scananwendungen. Wenn Sie sich nicht sicher sind, welche Lagerschilder und -etiketten für Ihre verschiedenen Lageranwendungen geeignet sind, besuchen Sie unsere dreistufige Anleitung zur Auswahl der richtigen Lageretiketten. Tipps zur Auswahl der besten Beschilderungslösungen auf höchstem Niveau finden Sie in unserer Kaufberatung für Lagerschilder.
Richtige Verwendung von Ladestationen
Die in den meisten Lagern verwendeten Gabelstapler-Ladestationen erscheinen einfach genug und sind, was die Ausstattung betrifft, äußerst sicher. Das meiste Risiko in diesen Bereichen ergibt sich aus der Tätigkeit der Mitarbeiter bei der Vorbereitung des Ladevorgangs und der Batteriewartung. Das Rauchen im Bereich zu verbieten ist eine offensichtliche Sicherheitsüberprüfung, aber es ist auch entscheidend, dass der Bereich ausreichend belüftet wird und die Aufzüge vor dem Laden angemessen positioniert und gebremst werden. Batteriewartungsverfahren sollten auch gut dokumentiert sein und die Verwendung geeigneter PSA anleiten, angemessene Ausrüstung für die Wartung von Batterien enthalten und Anweisungen für die Verwendung von Notfalleinrichtungen wie Augenwaschstationen im Falle einer Batteriesäurebelastung enthalten.
Ein gründlicher und ansprechender HazCom-Plan
Verfahren, die potenziellen Gefahren angemessen begegnen, sind weniger nützlich, wenn sie nicht Teil eines Gesamtplans für die Gefahrenkommunikation (HazCom) sind. Ein schriftlicher HazCom-Plan ist eine OSHA-Anforderung und sollte Sicherheitsinformationen zu Etiketten und Warnhinweisen, Sicherheitsdatenblätter, Mitarbeiterschulungen und eine Liste der im Lager vorhandenen gefährlichen Chemikalien enthalten. Während die Erstellung des Plans eine Grundvoraussetzung ist, besteht die Best Practice darin, sicherzustellen, dass er regelmäßig überprüft und auf dem neuesten Stand gehalten wird und Teil eines Sicherheitsschulungsprogramms ist, das die Mitarbeiter auf dem Laufenden hält.
Richtige ergonomische Verfahren und Schulung
Jeder manuelle Vorgang vom Heben von Gegenständen bis zum Betrieb digitaler Anzeigen für automatisierte Geräte kann ein ergonomisches Sicherheitsrisiko darstellen. Ordnungsgemäße Verfahren sollten die maximale sichere Arbeitslast (SWL) aller Geräte und die Gewichtsgrenzen für die manuelle Handhabung für manuelles Heben klar angeben. Die Vermeidung der Notwendigkeit manueller Vorgänge durch Automatisierung und Geräteunterstützung kann dazu beitragen, das ergonomische Risiko drastisch zu reduzieren, und das Halten der Geräte innerhalb sicherer Betriebsparameter stellt sicher, dass unsachgemäße Belastung vermieden und unsichere Ausfälle verhindert werden können.
Sicherheit ist Teil der Arbeit eines jeden Mitarbeiters, und die Lagerverwaltung spielt eine besonders wichtige Rolle, da sie die Arbeitsabläufe in allen Bereichen überwacht. Die Behandlung größerer und kleinerer Risiken innerhalb Ihrer Verfahren gibt Ihrem Betrieb das beste Potenzial, um Verletzungen der Belegschaft zu vermeiden und die Sicherheit Ihrer Mitarbeiter zu gewährleisten.
Industrietechnik
- Die 10 Kodierungsregeln der NASA zum Schreiben sicherheitskritischer Programme
- Sicherheitsausrüstung und -richtlinien sollte in keinem Lager fehlen
- So stellen Sie die Notfallvorsorge im Lager sicher
- 5 Sicherheitstipps für Kranheber, die jeder Kranführer befolgen sollte
- 7 Bestandskennzahlen, die Lagerverwalter verfolgen sollten
- Erstellen Sie Sicherheitsverfahren für Arbeiter und Techniker
- Arbeitssicherheitsleitfaden für die Fertigungsindustrie
- 7 Strategien hervorragender Sicherheitsmanager
- Überlegungen zum Brandschutz von CNC-Maschinen für EHS-Manager
- Sicherheitsvorkehrungen in der Gasschweißwerkstatt