Schweißprüfung für sicherheitskritische Baugruppen
Für Hersteller von Automobilteilen steht viel auf dem Spiel. Autofahrer und Beifahrer verlassen sich darauf, dass die Schweißqualität den Bedingungen standhält, für die sie entwickelt wurden. Ein unentdeckter Fehler während des Herstellungsprozesses könnte ein Unternehmen angreifbar oder schlimmer machen, insbesondere wenn das betreffende Teil für eine Baugruppe „sicherheitskritisch“ ist.
Autositze stehen beispielsweise in direktem Kontakt mit den Passagieren; Daher gelten die Sitzschweißnähte als sicherheitskritisch. Diese Klassifizierung schreibt ein bestimmtes Protokoll vor der Produktion vor. Obwohl die OEM-Anforderungen unterschiedlich sind, stimmen sie in der Regel mit der Branchenpraxis überein und werden je nach verwendetem Teil, Anlage und Industrieausrüstung mit geringfügigen Unterschieden implementiert. Hier sind die Grundelemente eines Protokolls:
Vorproduktionsprotokoll
- Einstellungsparameter - Festlegung von Schweißparametern und Überprüfung ihrer Akzeptanz. Dies kann durch Schneiden und Ätzen von Schweißabschnitten erfolgen, um die Schweißdurchdringung zu überprüfen (15–20 %).
- Freigabeprozess - Ein festgelegter Prozess zur Freigabe oder Genehmigung der Produktion, sobald das Obige verifiziert wurde.
- Änderungsmanagement - Änderungen wesentlicher Variablen über bestimmte Grenzen hinaus erfordern eine erneute Validierung durch Schnitt- und Ätztests.
- Qualitätssicherung - Zufällige Teile können aus der Produktion zum Schneiden und Ätzen mit einer vom OEM vorgegebenen Häufigkeit ausgewählt werden.
Das Roboterschweißen hat dazu beigetragen, die Teilequalität immens zu verbessern, indem Schweißnähte immer an derselben Stelle mit programmierten Schweißparametern platziert werden. Die Einhaltung der oben genannten Verfahren trägt zur Herstellung eines qualitativ hochwertigen Schweißprodukts bei. Automobil-OEMs haben sich auf sicherheitskritische Schweißnähte konzentriert, was zu einer Überprüfung einiger Schlüsselelemente geführt hat:
Produktionsprotokoll
- Sicherheit - Stellen Sie sicher, dass qualifiziertes Personal Zugang zur Ausrüstung hat und dass keine Änderungen vorgenommen werden, die die Qualität beeinträchtigen.
- Lichtbogenüberwachung - Die Implementierung eines Lichtbogenüberwachungssystems kann dabei helfen, zu überprüfen, ob der Prozess unter Kontrolle ist, und kann es ermöglichen, die Häufigkeit der zerstörenden Prüfungen zu reduzieren. Die Lichtbogenüberwachung überprüft, ob die Schweißparameter die festgelegten Grenzwerte einhalten. Schweißnähte außerhalb der Grenzen werden zur weiteren Überprüfung gekennzeichnet.
- Rückverfolgbarkeit - Verfolgen Sie Änderungen und Schweißergebnisse und behalten Sie die Möglichkeit bei, Datum, Uhrzeit und Seriennummer von Teiländerungen zu protokollieren.
Bei Yaskawa Motoman nehmen wir uns die Zeit, uns über die Anforderungen unserer Kunden an Herstellung und Rückverfolgbarkeit zu informieren. Im Laufe der Jahre haben wir mehrere Software- und E/A-Verbesserungen für unsere Steuerungen entwickelt, die es Herstellern ermöglichen, zuverlässige, rückverfolgbare Schweißnahtprüfungen durchzuführen.
Sicherheitsfunktionen
Passwortfunktion
Das standardmäßige Sicherheitssystem mit einem globalen Passwort auf verschiedenen Ebenen ist für mehrere Techniker praktisch, um mehrere Roboterzellen innerhalb einer Anlage zu warten. Es besteht jedoch die Gefahr, dass globale Passwörter vom Werkspersonal geteilt werden, ohne dass kontrolliert wird, was geändert wird und von wem.
Die Passwortfunktion des DX-Controllers von Yaskawa erstellt eine Datenbank von Benutzern mit Passwörtern und Freigaben für Sicherheitsstufen. Benutzer müssen sich anmelden, um den Roboter zu bedienen; die Logging-Funktion zeichnet den Benutzernamen und die vorgenommenen Änderungen auf.
Dem DX200-Controller wurde Software hinzugefügt, um eine Passwort-Fernsteuerung durch die SPS zu ermöglichen. Steuerungstechniker können Logik implementieren, um werks-/zellenbasierte Steuerungen zu verwenden, um Benutzer und Anmeldungen basierend auf ihren internen Mitarbeiterausweisen oder Sicherheitssystemen fernzuverwalten.
Sicherheitsstufen
- Betriebsebene - Standardmäßig erlaubt diese Basisebene jedem, sich durch ein Programm zu bewegen oder es schrittweise zu durchlaufen, aber keine Punkte oder Schweißeinstellungen zu ändern.
- Stufe bearbeiten - Ermöglicht dem Benutzer, Programme zu erstellen und Schweißeinstellungen zu ändern, aber keinen Zugriff auf Parameter oder übergeordnete Daten.
- Verwaltungsmodus - Bietet vollen Zugriff auf Parameter und Wartungsfunktionen.
- Sicherheitsstufe - Ermöglicht den Zugriff auf die Einrichtung und Verwaltung der steuerungszuverlässigen Softwaregrenzen und der Sicherheitslogik, die in DX-Controllern implementiert sind (Functional Safety Unit – FSU).
Was diese Ebenen den Benutzern erlauben, wird vom System definiert. Die Ebene, auf die das Management den Zugriff kontrolliert, variiert je nach Werksstandort.
Logging-Funktion
Viele neuere Robotersteuerungen verfügen über eine Standardprotokollierungsfunktion, die Änderungen am System nach Datum und Uhrzeit verfolgt. Beispielsweise kann ein Mitarbeiter der Tagschicht sehen, ob jemand aus der Nachtschicht eine Änderung vorgenommen hat. Der Roboter verwaltet eine lokale Datei der letzten Änderungsserie, sodass durch eine routinemäßige Datenspeicherung ein historisches Protokoll der Benutzeraktivitäten geführt werden kann. Der Roboter kann auch Passwortsicherheit verwenden, sodass Benutzer sich anmelden müssen, um Änderungen vorzunehmen. Auch Benutzernamen werden bei Änderungen vermerkt.
Sicherheits-Re-Teach-Bearbeitungsfunktion
Die Betriebsebene erlaubt Benutzern nicht, Programmpunkte zu ändern, aber einige Unternehmen gestatten Bedienern oder Technikern der ersten Ebene, geringfügige Änderungen für Teilevariationen vorzunehmen. Safety Re-Teach ermöglicht es Benutzern auf Betriebsebene, programmierte Punkte innerhalb eines durch den Verwaltungsmodus definierten 3D-Bereichs zu ändern. Dies ist normalerweise auf wenige Millimeter eingestellt, und ein Manager kann den Betrag der Winkeländerung für den Brenner oder die externe Achse begrenzen. Benutzer der Betriebsebene können Schweißparameter nicht ändern, daher werden wesentliche Schweißvariablen nicht geändert. Dies vermeidet wiederholte zerstörende Prüfungen. Safety Re-Teach kann per Parameter im Verwaltungsmodus auf jedem DX-Controller aktiviert werden.
Lichtbogenüberwachung
Als Roboterlieferant, der Schweißsysteme integriert und auf einer Joint-Venture-Geschichte mit einem Schweißunternehmen aufbaut, verfügt Yaskawa Motoman über umfassende Erfahrung mit der Lichtbogenüberwachung. Wir haben unsere Schweißschnittstellen so konzipiert, dass sie die Lichtbogenüberwachungsfunktion unterstützen, die Stromquellenhersteller möglicherweise integriert haben.
Die integrierten Funktionen von Miller Insight Centerpoint™ und Lincoln Electric Production Monitoring™ sind über das Programmierhandgerät des Roboters zugänglich. WeldCube von Fronius kommuniziert direkt mit der/den Stromquelle(n). Yaskawa und Fronius arbeiten daran, dass das Überwachungsergebnis in den Schweißer-Statusbits gemeldet wird.
Die Herausforderung, die „sicherheitskritischen“ Anforderungen zu erfüllen, beinhaltet auch die klare Darstellung der Schweißergebnisse aus der Lichtbogenüberwachung der Stromquelle in einem nützlichen Format. Das beste Format ist die Hervorhebung von Überwachungsergebnissen in einem Teilediagramm auf einer Roboterzellen-HMI. Auf diese Weise können Bediener von Schweißstationen Unregelmäßigkeiten leicht erkennen und schnell reagieren. Die Bediener müssen die vom System gekennzeichneten Schweißnähte visuell inspizieren, um zu beurteilen, ob die Schweißnähte konform oder nicht konform sind.
Während die Robotersteuerung den Status des Lichtbogenmonitors lokal auf einem HMI melden kann, bieten die Stromquellenhersteller auch Software an, die entwickelt wurde, um die Ergebnisse des Lichtbogenmonitors aus der Ferne über einen PC oder eine Cloud-basierte Software zu melden.
Miller Insight Centerpoint
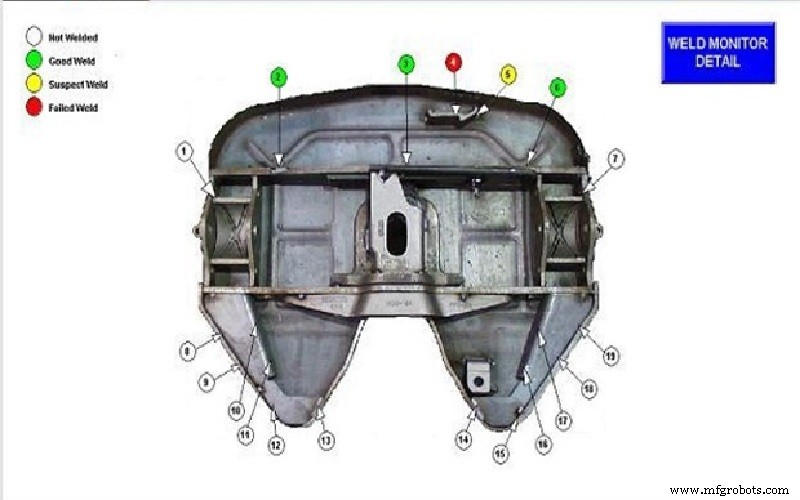
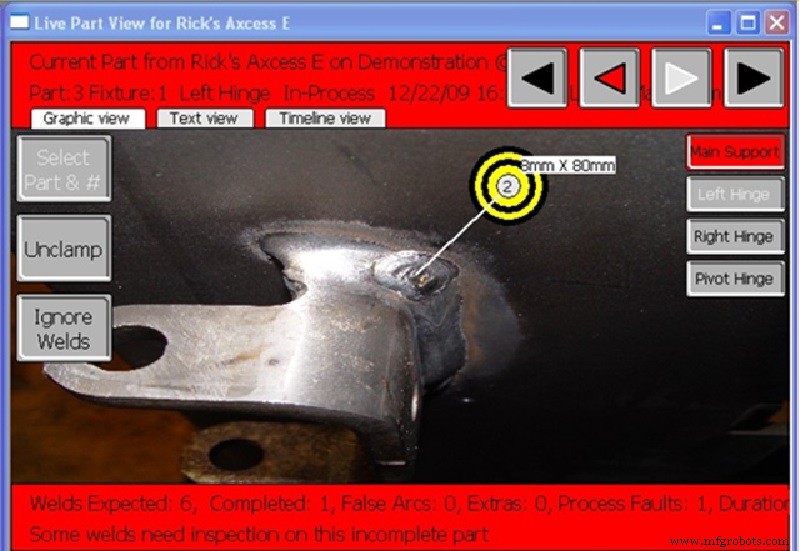
Rückverfolgbarkeit
Automobil-OEMs verlangen von ihren Zulieferern nicht nur, dass sie gute Teile herstellen, sie fordern sie auch auf, Qualitätssysteme zu implementieren, um eine „Rückverfolgbarkeit“ zu gewährleisten, die die Schweißergebnisse eines Teils seiner Seriennummer zuordnet. Ziel ist es, bis zu einem Zeitpunkt in der Produktion zurückverfolgen zu können, an dem bekannt war, dass Teile konform sind, wenn ein nicht konformes Teil erkannt wird.
Um Herstellern dabei zu helfen, die Rückverfolgbarkeit einzuhalten, müssen die Lichtbogenüberwachungsdaten von der Schweißstromquelle und der Robotersteuerung sowie alle teilespezifischen Daten, auf die aus der Ferne zugegriffen und schließlich in der SPS protokolliert werden muss, erfasst und mit der Teileseriennummer verknüpft werden. Wie dieses Daten-Mashup harmonisiert werden kann – und wie schwierig dies ist – hängt davon ab, was ein Hersteller standardmäßig integrieren kann, ohne die internen Sicherheitsprotokolle zu gefährden.
String-Variablen
Ein Trick besteht darin, eine String-Variablen-Erstellungsfunktion von der Robotersteuerung zu verwenden, um eindeutige Kennungen als Ablaufverfolgungsmechanismus zu erstellen. Es gibt eine Mischung aus Variablen, die zum Speichern von Zahlen oder sogar Positionen verwendet werden, und diese Variablen unterscheiden sich je nach Format und Anzahl der Ziffern. String-Variablen können eine Kombination aus Zeichen oder Zahlen mit einer Länge von bis zu 32 Zeichen sein. Diese können aufgerufen werden, um eine Nachricht auf dem Anhänger anzuzeigen oder für andere Zwecke.
Im Falle der Automobilproduktion haben wir diese verwendet, um Seriennummerninformationen für das jeweilige produzierte Teil zu enthalten. Steuerungsingenieure können die Ethernet-Kommunikation verwenden, um die Werte von einer SPS oder einem Barcode-Lesegerät zu "lesen", und wir können sie an andere Geräte weitergeben.
Gleichzeitige E/A
Yaskawa Motoman verwendet Concurrent I/O (CIO), um eine programmierbare Logiksteuerung durchzuführen und Daten zwischen dem Roboter und der Stromquelle zu kommunizieren. Während es für Schweißeinstellungen verwendet wird, kann es auch verwendet werden, um Lichtbogenüberwachungsergebnisse zwischen der Stromquelle und dem Roboter zu übertragen. Zur Rückverfolgbarkeit haben wir es verwendet, um die Schweißergebnisse für jede Schweißstelle zu verketten und zusammen mit der Teileseriennummer an die Werks-SPS für eine Teileaufzeichnung zu senden. Wir nehmen auch die Seriennummer des Teils und senden sie an einen Nadelpräger, der die Seriennummer auf Teile graviert, die die Schweißüberwachung passieren.
Kürzlich haben wir ein System geliefert, das Schweißnahtprüfdaten von Lincoln Electric Production Monitor übernimmt und sie dem Bediener in einer grafischen Darstellung des Teils präsentiert. Es hebt die Überwachungsergebnisse an jeder Schweißstelle in Grün oder Rot hervor – je nachdem, ob sie innerhalb oder außerhalb der Grenzen liegen. CheckPoint™-Überwachung (eine externe Software) dient zum Speichern von Daten in der Cloud. Der CIO ermöglichte den sofortigen Zugriff auf die Ergebnisse des Produktionsmonitors, sodass diese dem Bediener während der Produktion des Teils präsentiert werden konnten.
Implementierung
Die Handhabung von Schweißüberwachungsdaten sollte die Produktionskontrolle zusammen mit den historischen Protokollierungs- und Rückverfolgbarkeitsanforderungen berücksichtigen. Die dabei erfassten Daten werden in der Organisation unterschiedlich verwendet, und diese Anforderungen sollten für jede Rolle bei jedem Schritt berücksichtigt werden.
Während die Verwendung von Schweißüberwachungsdaten es den Bedienern vor Ort erleichtern sollte, die Teilequalität zu überprüfen, können Überwachungspersonal historische Daten verwenden, um Qualitätspläne zu verwalten und Probleme zu beheben. Sicherheitsfunktionen machen es nahezu unmöglich, von etablierten Protokollen und Parametern abzuweichen, und die Lichtbogenüberwachung liefert in Echtzeit grafische Hinweise auf Schweißnähte, die einer weiteren Inspektion bedürfen.
Mit der SPS als endgültigem Ziel werden teilespezifische Schweißdaten protokolliert, gespeichert und rückverfolgbar. Es kann eine beträchtliche Menge an Vorarbeit erfordern, um zu einer vollständigen Datenharmonisierung zu gelangen; Das Ergebnis sind jedoch zuversichtliche Kunden und verbesserte Qualität, die auch dazu beitragen können, die Zukunft Ihres Betriebs zu sichern.
Industrieroboter
- Kritische Temperaturen für Supraleiter
- Warum hervorragende Zuverlässigkeit für die Sicherheit unerlässlich ist
- Die 10 Kodierungsregeln der NASA zum Schreiben sicherheitskritischer Programme
- Sicherheitstipps am Arbeitsplatz für CNC-Maschinisten
- Entwicklung einer neuen Ära für intelligentere Lebensmittelsicherheit
- Ein Fall für die Aufrüstung alternder Lkw
- Strategien für die richtige Schweißnahtvorbereitung
- 5 Sicherheitstipps für die Vorbereitung schwerer Ausrüstung
- Sicherheitstipps für das Schweißen von Kraftstofftanks
- Schweißprüfung verstehen