Spanende Fertigung Bohrtechnik 101
Als gebräuchlichstes Werkzeug in der Lochbearbeitung sind Bohrer in der mechanischen Fertigung weit verbreitet. Gerade für die Bearbeitung von Kühlgeräten, Rohrböden von Energieerzeugungsanlagen, Dampferzeugern und anderen Teilen ist die Anwendung besonders umfangreich und wichtig.
Funktionen A f D Rillung
Der Bohrer hat normalerweise zwei Hauptschneiden, und während der Bearbeitung führt der Bohrer das Schneiden durch, während er sich dreht. Der Spanwinkel des Bohrers wird von der Mittelachse zur Außenkante immer größer. Die Schnittgeschwindigkeit des Bohrers ist umso höher, je näher am äußeren Kreis, und die Schnittgeschwindigkeit wird allmählich zur Mitte hin verringert, und die Schnittgeschwindigkeit des Rotationszentrums des Bohrers ist null. Die Querschneide des Bohrers befindet sich in der Nähe der zentralen Rotationsachse, der sekundäre Spanwinkel der Querschneide ist groß, es gibt keinen Spanraum und die Schnittgeschwindigkeit ist niedrig, was einen großen axialen Widerstand erzeugt. Wenn die Querschneide nach DIN1414 auf A-Typ oder C-Typ geschliffen wird und die Schneidkante in der Nähe der Mittelachse einen positiven Spanwinkel aufweist, kann der Schnittwiderstand verringert und die Schnittleistung erheblich verbessert werden.
Je nach Form, Material, Struktur und Funktion des Werkstücks lassen sich Bohrer in viele Arten einteilen, wie z , Tieflochbohrer, Nestingbohrer und Wechselbohrer usw.
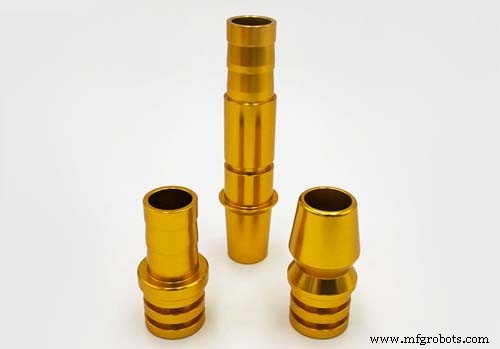
Spanbrechen und Spanentfernung
Das Schneiden des Bohrers erfolgt in einem schmalen Loch, und die Späne müssen durch die Nut des Bohrers abgeführt werden. Daher hat die Form der Späne einen großen Einfluss auf die Schnittleistung des Bohrers. Übliche Chipformen umfassen Flockenchips, röhrenförmige Chips, Nadelchips, konische Spiralchips, Bandchips, Fächerchips, Pulverchips und so weiter.
Wenn die Spanform ungeeignet ist, treten die folgenden Probleme auf:
① Feine Späne blockieren die Schneidkantenrille, beeinträchtigen die Bohrgenauigkeit, verringern die Lebensdauer des Bohrers und brechen sogar den Bohrer (z. B. pulverförmige Späne, fächerförmige Späne usw.);
② Lange Späne wickeln sich um den Bohrer, behindern den Betrieb, führen zum Brechen des Bohrers oder verhindern das Eindringen der Schneidflüssigkeit in die Bohrung (z. B. Spiralspäne, Bandspäne usw.).
So lösen Sie das Problem der ungeeigneten Spanform:
① Methoden wie Erhöhung der Vorschubgeschwindigkeit, intermittierender Vorschub, Schleifen der Querschneide und Installieren des Spanbrechers können separat oder in Kombination verwendet werden, um die Wirkung des Spanbrechens und der Spanentfernung zu verbessern und die durch Späne verursachten Probleme zu beseitigen.
② Zum Bohren von Löchern kann ein professioneller Spanbrecher verwendet werden. Beispiel:Das Hinzufügen eines speziell entwickelten Spanbrechers in der Nut des Bohrers bricht die Späne in leichter zu reinigende Späne. Schmutz wird entlang der Rille glatt entfernt und blockiert nicht in der Rille. Daher hat der neue Spanbrecher-Bohrer eine viel gleichmäßigere Schneidwirkung als herkömmliche Bohrer.
Gleichzeitig erleichtern die kurz gebrochenen Eisenspäne das Anströmen des Kühlmittels an die Bohrerspitze, was die Wärmeableitungswirkung und Schnittleistung während des Bearbeitungsprozesses weiter verbessert. Und weil der neu hinzugefügte Spanbrecher die gesamte Rille des Bohrers durchdringt, behält er auch nach mehrmaligem Schleifen seine Form und Funktion. Zusätzlich zu den oben genannten funktionalen Verbesserungen ist es erwähnenswert, dass dieses Design die Steifigkeit des Bohrerkörpers verstärkt und die Anzahl der vor einem einzigen Schleifvorgang gebohrten Löcher erheblich erhöht.
Bohrgenauigkeit
Die Genauigkeit des Lochs setzt sich hauptsächlich aus Faktoren wie Öffnungsgröße, Positionsgenauigkeit, Koaxialität, Rundheit, Oberflächenrauheit und Lochgraten zusammen.
Faktoren, die die Genauigkeit des während des Bohrens bearbeiteten Lochs beeinflussen:
① Die Spanngenauigkeit und die Schnittbedingungen des Bohrers, wie z. B. Werkzeughalter, Schnittgeschwindigkeit, Vorschubgeschwindigkeit, Schneidflüssigkeit usw.
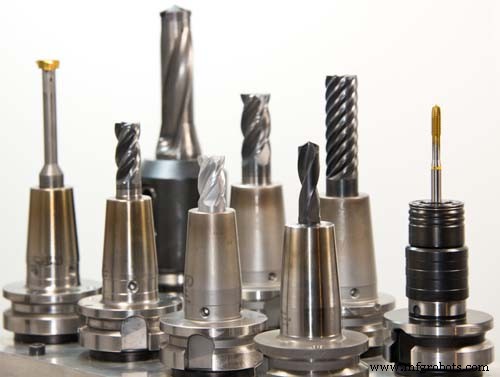
② Die Größe und Form des Bohrers, wie z. B. die Länge des Bohrers, die Form der Klinge, die Form des Bohrkerns usw.
③Die Form des Werkstücks, wie z. B. die Form der Seite der Öffnung, die Form der Öffnung, die Dicke und der Klemmzustand.
Reiben
Das Reiben wird durch das Schwingen des Bohrers während der Bearbeitung verursacht. Die Schwingung des Werkzeughalters hat einen großen Einfluss auf den Lochdurchmesser und die Positioniergenauigkeit des Lochs, daher sollte bei starkem Verschleiß des Werkzeughalters rechtzeitig ein neuer Werkzeughalter ausgetauscht werden. Beim Bohren kleiner Löcher ist es schwierig, den Schwung zu messen und einzustellen, daher ist es am besten, einen Bohrer mit grobem Schaft und kleiner Klinge mit einer guten Koaxialität zwischen Klinge und Griff zu verwenden. Bei Verwendung eines nachgeschliffenen Bohrers liegt der Grund für die Abnahme der Bohrgenauigkeit meist in der Asymmetrie der Rückenform. Die Steuerung der Blatthöhendifferenz kann das Schneiden und Aufweiten des Lochs wirksam unterdrücken.
Lochrundheit
Aufgrund der Vibration des Bohrers ist das gebohrte Loch leicht polygonal, und an der Lochwand erscheinen gewehrartige Linien. Übliche polygonale Löcher sind meist Dreiecke oder Fünfecke. Der Grund für das dreieckige Loch ist, dass der Bohrer beim Bohren zwei Rotationszentren hat. Sie vibrieren mit einer Frequenz von 600 Wechseln alle 600. Der Hauptgrund für die Vibration ist der unausgeglichene Schnittwiderstand. Wenn sich der Bohrer um eine Umdrehung dreht, ist die Rundheit des bearbeiteten Lochs nicht gut, die Widerstandskraft ist während der zweiten Umdrehung des Schneidens unausgeglichen, und die letzte Vibration wird erneut wiederholt, aber die Vibrationsphase wird bis zu einem gewissen Grad verschoben, was dazu führt Gewehrleinen an der Lochwand. Wenn die Bohrtiefe ein bestimmtes Niveau erreicht, nimmt die Reibung zwischen der Kantenfläche des Bohrers und der Lochwand zu, die Vibration wird gedämpft, die Gewehrlinie verschwindet und die Rundheit wird besser. Diese Art von Öffnung ist im Längsschnitt betrachtet trichterförmig. Aus dem gleichen Grund können beim Schneiden auch fünfeckige und siebeneckige Löcher entstehen. Um dieses Phänomen zu beseitigen, sollte zusätzlich zur Kontrolle der Vibration des Spannfutters, des Höhenunterschieds der Schneidkante, der Asymmetrie des Rückens und der Form der Klinge usw. die Steifigkeit des Bohrers erhöht werden Vorschub pro Umdrehung, der Freiwinkel und der Schliff sollten verbessert werden. Maßnahmen wie Schneide.
Bohren Sie Löcher auf geneigten und gekrümmten Oberflächen
Wenn die Schneidfläche oder die Bohrfläche des Bohrers geneigt, gekrümmt oder abgestuft ist, ist die Positionierungsgenauigkeit schlecht. Zu diesem Zeitpunkt verwendet der Bohrer ein radiales einseitiges Schneidwerkzeug, was die Standzeit des Werkzeugs verkürzt.
Zur Verbesserung der Positionsgenauigkeit können folgende Maßnahmen ergriffen werden:
- Bohren Sie zuerst das Loch in der Mitte;
- Fräsen Sie den Lochsitz mit einem Schaftfräser;
- Wählen Sie Bohrer mit guter Durchdringung und Steifigkeit;
- Verringern Sie die Vorschubgeschwindigkeit.
Gratbehandlung
Beim Bohren entstehen am Ein- und Ausgang des Lochs Grate, insbesondere bei der Bearbeitung von zähen Materialien und dünnen Blechen. Denn beim Durchbohren des Bohrers kommt es zu einer plastischen Verformung des bearbeiteten Materials. Zu diesem Zeitpunkt wird der dreieckige Teil, der von der Schneidkante des Bohrers in der Nähe der Außenkante geschnitten werden sollte, nach außen verformt, nachdem er durch die axiale Schneidkraft beeinflusst wurde, und wird unter der Wirkung an der Außenkante des Bohrers gebogen Anfasung und Schneidkante kräuselt es sich weiter, um eine Kräuselung oder einen Grat zu bilden.
Verarbeitungsbedingungen für das Bohren
Im allgemeinen Produktkatalog für Bohrer gibt es eine „Referenztabelle der grundlegenden Schnittparameter“, die nach Bearbeitungsmaterialien geordnet ist. Benutzer können sich auf die bereitgestellten Schnittparameter beziehen, um die Schnittbedingungen für das Bohren auszuwählen. Ob die Auswahl der Schnittbedingungen angemessen ist oder nicht, sollte anhand von Faktoren wie Bearbeitungsgenauigkeit, Bearbeitungseffizienz und Standzeit des Bohrers umfassend durch Probeschneiden beurteilt werden.
1. Lebensdauer des Bohrers und Verarbeitungseffizienz
Unter der Prämisse, den technischen Anforderungen des zu bearbeitenden Werkstücks gerecht zu werden, sollte der sachgerechte Einsatz des Bohrers umfassend an der Standzeit und Bearbeitungseffizienz des Bohrers gemessen werden. Der Bewertungsindex der Lebensdauer des Bohrers kann den Schnittabstand wählen; Der Bewertungsindex der Bearbeitungseffizienz kann die Vorschubgeschwindigkeit wählen. Bei Schnellarbeitsstahlbohrern wird die Lebensdauer des Bohrers stark von der Rotationsgeschwindigkeit und weniger vom Vorschub pro Umdrehung beeinflusst. Daher kann die Bearbeitungseffizienz verbessert werden, indem der Vorschub pro Umdrehung erhöht wird, während eine längere Lebensdauer des Bohrers sichergestellt wird. Es ist jedoch zu beachten, dass bei zu großem Vorschub pro Umdrehung die Späne dicker werden und den Spanbruch erschweren. Daher ist es notwendig, den Bereich des Vorschubs pro Umdrehung für einen reibungslosen Spanbruch durch Probeschneiden zu ermitteln. Bei Hartmetallbohrern hat die Schneidkante eine größere Fase in Richtung des negativen Spanwinkels, und der optionale Vorschubbereich pro Umdrehung ist kleiner als bei Bohrern aus Schnellarbeitsstahl. Wenn der Vorschub pro Umdrehung während der Bearbeitung diesen Bereich überschreitet, wird die Lebensdauer des Bohrers reduziert. Da die Hitzebeständigkeit von Hartmetallbohrern höher ist als die von Schnellarbeitsstahlbohrern, hat die Drehzahl nur geringe Auswirkungen auf die Lebensdauer des Bohrers. Daher kann das Verfahren zum Erhöhen der Rotationsgeschwindigkeit verwendet werden, um die Verarbeitungseffizienz von Hartmetallbohrern zu verbessern, während die Lebensdauer des Bohrers sichergestellt wird.
2. Angemessene Verwendung von Schneidflüssigkeit
Das Schneiden des Bohrers erfolgt in einem Loch mit engem Raum. Daher haben die Art der Schneidflüssigkeit und das Injektionsverfahren einen großen Einfluss auf die Lebensdauer des Bohrers und die Bearbeitungsgenauigkeit der Bohrung. Schneidflüssigkeiten können in zwei Kategorien eingeteilt werden:wasserlöslich und nicht wasserlöslich. Die nicht wasserlösliche Schneidflüssigkeit hat eine gute Schmierfähigkeit, Benetzbarkeit und Antihafteigenschaften und hat auch eine Anti-Rost-Wirkung. Der wasserlösliche Kühlschmierstoff hat gute Kühleigenschaften, ist rauchfrei und nicht brennbar. Aus Rücksicht auf den Umweltschutz ist der Einsatz wasserlöslicher Kühlschmierstoffe in den letzten Jahren relativ groß geworden. Wenn jedoch die Verdünnungsrate der wasserlöslichen Schneidflüssigkeit ungeeignet ist oder sich die Schneidflüssigkeit verschlechtert, verkürzt dies die Lebensdauer des Werkzeugs erheblich, so dass bei der Verwendung vorsichtig vorgegangen werden muss. Egal ob wasserlöslicher oder nicht wasserlöslicher Kühlschmierstoff, der Kühlschmierstoff muss während des Einsatzes vollständig an die Schneidstelle gelangen. Gleichzeitig müssen die Durchflussmenge, der Druck, die Anzahl der Düsen und die Kühlmethoden (interne oder externe Kühlung) des Schneidöls streng kontrolliert werden.
Nachschärfen des Bohrers
Beurteilung nachgeschliffener Bohrer
Das Kriterium für das Nachschärfen des Bohrers ist:
- Abnutzungsgrad an Schneidkante, Querschneide und Fasenkante.
- Die Maßhaltigkeit und Oberflächenrauheit des bearbeiteten Lochs.
- Die Farbe und Form der Chips.
- Schnittwiderstand (indirekte Werte von Spindelstrom, Lärm, Vibration usw.).
- Bearbeitungsmenge usw.
Bei der tatsächlichen Verwendung sollten anhand der obigen Indikatoren gemäß den spezifischen Bedingungen genaue und zweckmäßige Beurteilungsstandards bestimmt werden. Wenn der Verschleiß als Kriterium herangezogen wird, sollte der beste Nachschleifzeitraum mit der besten Wirtschaftlichkeit gefunden werden. Da die Hauptschärfteile der Hinterkopf und die Meißelkante sind, verschleißt die Klinge bei zu großem Bohrerverschleiß länger, die Schleifmenge ist groß und die Anzahl der Nachschliffe wird reduziert (Gesamtwerkzeug Standzeit =Standzeit nach Nachschleifen × verfügbare Nachschleifzeiten), verkürzt sich die Gesamtlebensdauer des Bohrers. Wenn Sie die Maßhaltigkeit der bearbeiteten Bohrung als Kriterium verwenden, verwenden Sie die Säulenlehre oder die Grenzlehre, um den Schnitt und die Aufweitung der Bohrung, die Unebenheiten usw. zu überprüfen. Wenn der Kontrollwert überschritten wird, sollte sofort nachgebessert werden. Schärfung. Wenn der Schnittwiderstand als Kriterium verwendet wird, können Methoden wie eine automatische Abschaltung unmittelbar über dem eingestellten Grenzwert (z. B. Spindelstrom) angewendet werden. Wenn die Verarbeitungsmengenbegrenzungsverwaltung angenommen wird, sollte der oben erwähnte Unterscheidungsinhalt integriert werden, um das Kriterium festzulegen.
Schärfmethode des Bohrers
Verwenden Sie zum Nachschärfen des Bohrers am besten eine spezielle Werkzeugmaschine zum Schärfen des Bohrers oder einen universellen Werkzeugschleifer, was sehr wichtig ist, um die Lebensdauer und Bearbeitungsgenauigkeit des Bohrers zu gewährleisten. Befindet sich der Original-Bohrertyp in einem guten Bearbeitungszustand, kann er wie der Original-Bohrertyp nachgeschliffen werden; sollte der originale bohrertyp defekt sein, kann die rückenform entsprechend verbessert und die Querschneide dem einsatzzweck entsprechend geschärft werden.
Achten Sie beim Schärfen auf folgende Punkte:
- Verhindern Sie eine Überhitzung und reduzieren Sie die Härte des Bohrers.
- Die Beschädigung am Bohrer (insbesondere die Beschädigung an der Schneidkante) sollte vollständig entfernt sein.
- Der Bohrtyp sollte symmetrisch sein.
- Achten Sie darauf, die Schneide beim Schärfen nicht zu beschädigen, und entfernen Sie die Grate nach dem Schärfen.
- Bei Hartmetallbohrern hat die Schleifform einen großen Einfluss auf die Leistung des Bohrers. Die Bohrerform im Werk ist die beste Bohrerform, die durch wissenschaftliches Design und wiederholte Tests erzielt wurde. Daher sollte beim Nachschärfen generell die ursprüngliche Klingenform beibehalten werden.
Herstellungsprozess
- Investitionen in Fertigungstechnologie — Post-Pandemie
- 8 wichtige Tipps zur Verbesserung der Spankontrolle beim Bohren
- Ericsson:Beschleunigung der 5G-Technologie in der Fertigung
- Ericsson:5G für die Fertigung
- Leiterplatte 101
- Verwenden Sie eine Tischbohrmaschine
- Komponenten der Bohrmaschine
- CNC-Bearbeitungszentrum-Technologie
- Prototypen bis zur Serienfertigung
- Auftragsfertigungsprozess