Fallstudie zur Zuverlässigkeit pharmazeutischer Anlagen
Wartungs- und Zuverlässigkeitsprofis können einen Unterschied machen. In den meisten Produktionsstätten bedeutet dies konzentrierte Arbeit, die es dem Betrieb ermöglicht, mehr Endprodukte (sei es Erfrischungsgetränke, Motorräder, Glühbirnen, Autos, Cupcakes, Wasserkocher usw.) aus der Tür zu bekommen.
In der biosynthetischen Humaninsulin (BHI)-Fabrik von Eli Lilly in Indianapolis wird es noch wichtiger, etwas zu bewegen.
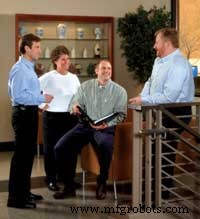
Fast 21 Millionen Menschen in Amerika – und 200 Millionen Menschen weltweit – haben Diabetes. Allein in den USA werden jedes Jahr fast 1 Million neue Fälle diagnostiziert. Viele Menschen mit Diabetes benötigen Insulin, um ihren Blutzucker (Glukose) zu kontrollieren, und die BHI-Pflanze hilft, diesen Bedarf zu decken. Der Standort wurde 1992 für die Produktion eröffnet und produziert einen erheblichen Anteil des weltweiten medizinischen Insulins. Wartungs- und Zuverlässigkeitsarbeiten, die die Produktivität steigern, ermöglichen es dem Unternehmen, hochwertige, lebenserhaltende Medikamente in die Hände derer zu bringen, die sie benötigen.
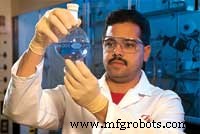
Egal, ob Sie für ein Unternehmen arbeiten, das Computerchips oder Kartoffelchips herstellt, wenn Sie einen Mehrwert für die Interessenvertreter oder die Wirtschaft schaffen, das kann in keiner Weise herabgesetzt werden“, sagt Ken Swank, der Leiter des Wartungs- und Zuverlässigkeitsteams des Werks. „Es ist egal, was du tust. Es ist wichtig. Es gibt jedoch einen deutlichen Unterschied. Ich habe früher für ein Unternehmen für Industrielacke gearbeitet. Unsere Beschichtungen gingen in alles ein, von Golfbällen über das Space Shuttle bis hin zu chirurgischen Instrumenten. Als ich das Endprodukt sah, wusste ich, dass ich ein Teil davon war. Aber wenn Sie für ein Pharmaunternehmen arbeiten. . . es bedeutet viel auf persönlicher Ebene.
Ich habe am Wochenende ein Paar kennengelernt, das einen kleinen Sohn hat. Wir kamen ins Gespräch und ich fand heraus, dass der Junge Diabetes hat. Ich fragte, ob er Typ 1 oder Typ 2 hätte. Der Vater fragte, woher wissen Sie so viel über Diabetes? Der Junge sagte mir, er sei Typ 1. Ich sah ihn an und sagte:‚Rate mal, was ich beruflich mache? Ich mache Insulin. Ich arbeite bei Eli Lilly und mache Humulin.“ Er sagte:„Danke. Ich mag meine Medizin sehr. Dadurch fühle ich mich viel besser.“
„Meine Abteilung ist dafür verantwortlich, dass dieses Gebäude jedes Mal die Medizin herstellt, die es herstellen soll. Es gibt Millionen von Menschen, die darauf angewiesen sind und jeden Tag danach greifen.“
Auf dem Firmengelände in Indianapolis befinden sich
Produktionsstätten und Firmensitze.
Steigende Anforderungen
Die BHI-Anlage ist groß und technisch komplex. Es beherbergt mehr als 17.000 Geräte, 13.000 Ein-/Ausgabepunkte und 600 Betriebseinheiten. Das Verarbeitungsverfahren zur Erzeugung des BHI-Moleküls umfasst mehrere Zentrifugationsschritte, eine Handvoll Reaktionen, viele Reinigungsschritte und verschiedene Lösungsmittelaustauschschritte. Dadurch wird etwa ein Drittel der Betriebseinheiten entweder als risikoreicher oder sicherheitskritischer Betrieb eingestuft.
Vor einigen Jahren entschieden die Leiter der Wartungs- und Zuverlässigkeitsabteilungen, dass wesentliche Änderungen vorgenommen werden mussten, um die Zeit, die Fähigkeiten, die Ressourcen und die potenziellen Auswirkungen der Abteilung auf die Anlage zu maximieren. BHI lief mehr als doppelt so viel wie ursprünglich geplant, und die Geschäftsnachfrage nahm weiter zu. Techniker waren überlastet, Sanierungsbemühungen wurden häufig neu priorisiert, um den aktuellen Anforderungen gerecht zu werden, und wichtige Systeme erhielten nicht einen angemessenen Prozentsatz an Aufmerksamkeit.
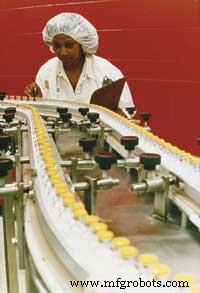
Wir haben uns nie Sorgen gemacht, dass unsere Geräte in einem qualifizierten Zustand funktionieren“, sagt Swank. „Aber wie der Rest der Pharmaindustrie zu dieser Zeit legten wir keinen besonderen Wert auf unsere Ausrüstung, außer dass wir immer die größtmögliche Verfügbarkeit wollten, um das meiste Medikament herzustellen. Aber wenn man versucht, so viele Kilos wie möglich aus der Tür zu bekommen, kamen wir an den Punkt, an dem Sie sich fragen:'Wird die Einrichtung ständig erweitert oder machen wir es aus geschäftlicher Sicht klug und konzentrieren uns auf Zuverlässigkeit?'“
Eine ganze Reihe von Einrichtungen von Eli Lilly dachten Ende der 90er Jahre darüber nach. Zum Beispiel leitete BHI Engineering Manager Ron Reimer am Standort Clinton (Ind.) Laboratories des Unternehmens Bemühungen, die proaktive Arbeit und Betriebszeit zu erhöhen und die Wartungskosten zu senken. Als Teil dieses Projekts, das dann systematisiert und als Proactive Asset Management bezeichnet wurde, stellte er den ersten Zuverlässigkeitsingenieur des Unternehmens ein.
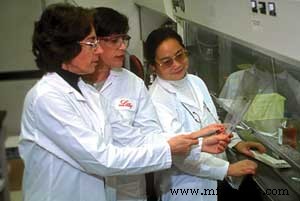
Direkte Einbindung aller wichtigen Akteure der Anlagenzuverlässigkeit
(Produktion, HSE, Qualitätskontrolle, Finanzen, Engineering und
Management) trägt dazu bei, den Erfolg der Initiative zur Prioritätensetzung der Zuverlässigkeit
sicherzustellen.
Die Verbesserungsbemühungen von BHI begannen mit der Aufnahme eines Zuverlässigkeitsingenieurs im Jahr 1999 und der Einführung von Projekten zur Zuverlässigkeitszentrierten Wartung (RCM) und Ursachenanalyse (RCFA). Diese Bemühungen nahmen zu, als Aufsichtsbehörden wie die Food and Drug Administration und die Environmental Protection Agency begannen, die Wartung in der pharmazeutischen Industrie genau zu untersuchen. Die Botschaft der Agenturen war einfach:Wartung ist gleich Anlagenzuverlässigkeit; Anlagenzuverlässigkeit ist gleich Produktzuverlässigkeit; und die Gesamtzuverlässigkeit entspricht der Einhaltung. „Unzuverlässigen“ Unternehmen können Strafen drohen, einschließlich der Einstellung des Betriebs.
Die Bedeutung der Kommunikation
Laut Ken Swank, dem Leiter des Wartungs- und Zuverlässigkeitsteams, spielt die Kommunikation eine wichtige Rolle für den Erfolg der Zuverlässigkeitspriorisierungsinitiative des BHI-Werks.
"Kommunikation ist einer der wichtigsten Bestandteile meiner Arbeit", sagt er. „Ich treffe mich regelmäßig mit den Produktionsleitern und erkläre ihnen, was auf uns zukommt. Ich bekomme ihr Engagement und helfe ihnen, den Mehrwert zu verstehen, den es bietet. Sie müssen auch einige Ressourcen aufbringen. Eine ordentliche Analyse ist natürlich nicht nur unsere Abteilung. Es umfasst Engineering, Wartung, Zuverlässigkeit, Betrieb, technische Dienstleistungen und manchmal Automatisierung. Wir verbringen viel Zeit damit, sicherzustellen, dass sie den Wert verstehen.
Ich muss ziemlich viel tanzen und singen, um ihnen zu helfen, sie zu verstehen. Aber von allen Konten war das Buy-In gut.“
"Ab diesem Zeitpunkt rückte Zuverlässigkeit meiner Meinung nach in den Mittelpunkt", sagt Swank. "Auf unserem Weg zu einem wirklich zuverlässigen Werk ist die Vision, dass, wenn die Produktion ein Stück Geräte, es ist in einem qualifizierten Zustand, es ist verfügbar, wenn es benötigt wird und es wird auf dem vorgegebenen Leistungsniveau laufen. Wir haben natürlich einen großen Anteil daran. Die Wartungsstrategien, die wir zusammengestellt haben, befassen sich damit, dass dieses Gerät in einem qualifizierten Zustand. Die Tiefe der Wartungsstrategien richtet sich auch nach der erforderlichen Auslastung oder Betriebszeit. Es gibt Vorgänge in der Anlage, die mehr laufen als andere, weniger redundant sind als andere oder wichtiger als andere sind. Diese erfordern mehr Aufmerksamkeit und detailliertere Untersuchungen. .”
Eine Initiative zur Priorisierung, die Anfang 2004 begann, war von zentraler Bedeutung für diese Strategie, um den Betriebseinheiten, die die meiste Aufmerksamkeit verdienen, Betriebszeit und Zuverlässigkeit zu bieten.
Wie Eli Lilly Zuverlässigkeitsrollen definiert
Laut Eli Lilly BHI Wartungs- und Zuverlässigkeitsleiter umfassen die Aufgaben und Verantwortlichkeiten ihrer Zuverlässigkeitsingenieure:
- Minimieren Sie Geräteausfälle durch RCFAs, FMEAs, RCM-Analysen, Untersuchungen zu Ableitungsabweichungen usw.
- Entwickeln Sie Kennzahlen, um die Zuverlässigkeitsbemühungen und Ressourcen zu optimieren.
- Eigene Wartungspläne (überprüfen/generieren/genehmigen) für neue und vorhandene Geräte.
- Stellen Sie zuverlässigkeitsorientierte Projekte bereit, die sich auf den gesamten Fluss auswirken.
- Konzentrieren Sie sich bei den Geschäftspraktiken auf Wartung und Zuverlässigkeit, um die Geräteverfügbarkeit zu erhöhen.
- Betreuen Sie Zuverlässigkeitstechniker.
- Integrieren Sie sich in Kontrollraumteams, um deren Geschäft effektiv zu unterstützen.
- Suchen und implementieren Sie neue Technologien zur Verbesserung der Geräteleistung und -verfügbarkeit.
Zu den Aufgaben und Verantwortlichkeiten von Zuverlässigkeitstechnikern gehören:
- Unterstützen Sie Site-Initiativen.
- Ausfüllen und Verarbeiten von CMMS-Dateneingabeformularen.
- Zuverlässigkeitsingenieure bei RCFAs, Data Mining, FMEAs, RCMs, Abweichungen, Änderungskontrollen, Feldüberprüfung, CMMS-Datenverbesserungen usw. unterstützen
- Spezielle Projekte – Unterstützung der Zuverlässigkeitsbemühungen usw.
Machen Sie es zu einer Priorität
Swank erzählt von den Marschbefehlen, die schließlich zu einer Zuverlässigkeitslösung führen würden.
„Mein damaliger Chef sagte:‚Überlegen Sie, wie wir die BHI-Anlage zuverlässiger machen. Das müssen wir in den Griff bekommen“, sagt Swank. „Was er eigentlich sagen wollte, war:‚Sie und Ihr Team müssen die Geschäftsanforderungen der Einrichtung verstehen, eine Methode festlegen, um einen Weg zur Behebung der korrekt priorisierten Zuverlässigkeitslücken zu finden, sie an das Unternehmen verkaufen, ausführen und herstellen es nachhaltig.“
Klingt einfach genug, dachte er zumindest.
„Wir begannen im Februar (2004) und gingen davon aus, dass wir im März oder April fertig sein würden“, sagt er. „Wir haben schnell gemerkt, dass dies aufwendiger und komplexer war, als wir erwartet hatten. Außerdem wollten wir es richtig machen.“
Der Plan wäre, eine Analyse zu entwickeln, die vorhandene Daten verwendet, um die Systembehebung als kontinuierliche Verbesserungsmaßnahme außerhalb der täglichen Supportbemühungen der Abteilung zu priorisieren. Die Analyseanforderungen waren:
- es würde die identifizierten Systeme nehmen und sie basierend auf den Daten nach geschäftlichen Auswirkungen einordnen;
- alle Beteiligten wären vertreten;
- die Analyse konnte in weniger als einer Mannwoche (40 Stunden) durchgeführt werden.
Diese Herausforderung wurde auf die Schultern des Bereichs Zuverlässigkeitstechnik der Abteilung gelegt. Die Gruppe umfasste die leitenden Zuverlässigkeitsingenieure Mark Lafever, Vadim Redchanskiy und Rod Matasovsky (jetzt im Ruhestand) sowie die Zuverlässigkeitstechniker David Doyle, Mary Ann Dust und Matt O’Dell. Sie begannen, den Inhalt der Analyse zu planen.
„Sie sind die Klugen. Ich war der Übersetzer vom Management zu den Leuten vor Ort“, sagt Swank. „Sie verstanden die Datensysteme und was Sinn machte und was nicht.“
Die Gruppe räumte ein, dass die Analyse, um Unterstützung für diese Initiative zu erhalten, auf Fakten beruhen und alle wichtigen Interessengruppen im Bereich Anlagenzuverlässigkeit – Produktion – direkt einbeziehen und aussagekräftig sein muss; Gesundheit, Sicherheit und Umwelt (HSE); Qualitätskontrolle (QC); Finanzen; Ingenieurwesen; und Management. Das würde ein unglaublicher Balanceakt werden.
„Jeder kann rausgehen und eine Menge Daten abrufen“, sagt Lafever. „Wir mussten entscheiden, woher wir die Daten ziehen, wie wir sie abrufen, und herausfinden, ob die Daten uns die Informationen liefern, die wir brauchen, um die richtigen Entscheidungen zu treffen.“
Tabelle 1. Zusammenfassung der Gewichtungen für die fünf Szenarien.
Tabelle 2. Beispiel aus der Sensitivitätsanalyse des ersten Szenarios.
Nach mehreren Iterationen – und „viel Kopfschütteln“, sagt Lafever – schloss das Team eine Analyse ab, die die Interessengruppen unter Verwendung vorhandener Daten der letzten 12 Monate berücksichtigte. Diese Daten umfassen:
1) Notarbeitsstunden, die mit Ausfallzeiten der Ausrüstung gleichgesetzt werden, um die Produktion zu befriedigen. Dies wurde aus dem computergestützten Wartungsmanagementsystem des Werks gesammelt, das alle Stunden verfolgt, die jeder Betriebseinheit in Rechnung gestellt wurden. Notarbeit wurde als „Arbeit, die nicht warten kann“ definiert. Obwohl es sich nicht um eine herkömmliche Messung der Systemausfallzeit handelt, korreliert dies direkt mit dem Ausmaß der Produktionsunterbrechung, wenn das System nicht richtig funktionierte.
2) Risikoklassifizierung gemäß Lillys Globally Integrated Process Safety Management (GIPSM), um HSE zu erfüllen. Das Klassifizierungssystem hat vier Möglichkeiten:sicherheitskritischer Betrieb, der größte Risikofaktor; hohes Risiko, das ein erhebliches Umwelt-, Gesundheits- und Brandrisiko mit sich bringt; mechanische Integrität, die von der Arbeitsschutzbehörde definiert wird; und kein Risiko oder „keines der oben genannten.“
3) Anzahl der Abweichungen vom Prozess, die durch Gerätefehler verursacht wurden, um die QC zu erfüllen. Dies zielte auf Abweichungen ab, die das Ergebnis von Zuverlässigkeitsproblemen der Ausrüstung waren, nicht von Bedienungsfehlern oder anderen nicht ausrüstungsbezogenen Problemen. Die Anzahl der Abweichungen wurde zusammen mit einer Stufe (1, 2 oder 3) berücksichtigt, die die Auswirkungen der Abweichung auf die Produktqualität festlegte.
4) Kosten der reaktiven Arbeit, um die Finanzierung zu decken. Dies wurde wiederum dem CMMS entnommen, das alle Haushaltsbelastungen gegenüber den operativen Einheiten erfasst. Diese Kosten beinhalteten alle Teile und Arbeit, die mit reaktiver Arbeit am System verbunden sind.
5) Input des Verfahrensingenieurs, um das Engineering zu erfüllen. Der für jedes System verantwortliche Prozessingenieur wurde zu Themen wie Systemalter, stundenlange potenzielle Ausfallzeiten durch Systemausfälle und regulatorische Auswirkungen befragt.
6) Wartungsplan für den Zustand des Systems, auch um die Technik zufrieden zu stellen. Dies wurde so gestaltet, dass es vier Stufen umfasst:Stufe 1, keine routinemäßige Wartung durchgeführt, die als die schwerwiegendste angesehen wurde; Stufe 2, präventive Wartung ist auf dem System vorhanden; Level 3, Periodic Qualification Evaluations (PQEs), die sicherstellen sollen, dass das System ständig qualifiziert und einsatzbereit ist, werden durchgeführt; und Stufe 4 wurde eine RCM-basierte Analyse des Systems verwendet, um einen Wartungsplan zu erstellen.
Diese Daten erstellten eine Bewertung der „entscheidenden Ausrüstung“, bei der die 420 Betriebseinheiten untersucht und diejenigen identifiziert wurden, die das Potenzial haben, entweder die Produktion einzustellen oder einen OSHA- oder EPA-meldepflichtigen Vorfall zu verursachen.
„Die Art und Weise, wie unsere Struktur in unserem CMMS eingerichtet ist, und die Art und Weise, wie wir unsere Ereignisdatenbank steuern, war der beste Weg“, sagt Lafever. „Manchmal ist eine Bedieneinheit ein Gerät. Meistens ist es ein wichtiges Gerät und noch viel mehr.“
Redchanskiy sagt zum Beispiel, dass die Betriebseinheit EV1411 (Verdampfungsprozess) „50 bis 60 Geräte und Instrumente wie Ventile, Wärmetauscher und Pumpen“ umfasst.
Die Auswertung reduzierte die anfängliche Liste um 70 Prozent, von 420 Betriebseinheiten auf 135.
Die Fakten lügen nicht
Wenn es darum geht, die Bedeutung einer bestimmten Betriebseinheit zu bestimmen, ist es schwer, mit den Fakten zu argumentieren.
„Bevor wir diese Analyse machten, war in der Produktion nur die Zentrifuge im Gespräch das Front-End“, sagt Ken Swank, Leiter des Wartungs- und Zuverlässigkeitsteams von Eli Lilly. „Nach der Analyse und der Vorstellung, was wir herausgefunden haben – ich habe darauf hingewiesen, dass die Zentrifuge auf Platz 63 (auf der Liste der 135 Betriebseinheiten) steht – fragen sie nicht viel danach.
“Dies lässt uns auch über die Definition von Produktionsanlagen hinausschauen. Vor der Analyse haben die Leute vergessen, Abwassertanks, Luftbehandlungsgeräte usw. einzubeziehen. Sie haben nicht an Tank 1099 in Kontrollraum 2 gedacht, wo alle Bodenabläufe verlaufen. Die Spülung geht durch die Abflüsse und in den Tank. Wenn dieser Tank nicht funktioniert, müssen wir unsere Reinigungsschritte einstellen.“
Maße und Gewichte
Um eine angemessene Priorisierung der verbleibenden 135 Einheiten zu gewährleisten, beschloss die Gruppe, jede Datenquelle zu gewichten und führte eine Handvoll Sensitivitätsanalysen durch.
„Wir hatten nicht das Gefühl, dass die sechs Kriterien gleich gewichtet waren“, sagt Swank. „Wir waren der Meinung, dass Sicherheit und Qualität einen größeren Einfluss haben als beispielsweise der Geldbetrag, den wir für Notarbeiten ausgeben.“
Für jeden Datensatz wurde ein Bewertungssystem (Null bis 3, wobei Null die geringste Auswirkung und Schwere und 3 die größte Auswirkung und Schwere ist) entwickelt und auf jede Betriebseinheit angewendet. Die Aufschlüsselung war wie folgt:
Stunden für Notarbeit (HEW) :weniger als 15 Stunden (Punktzahl Null), 15 bis weniger als 25 Stunden (eine), 25 bis weniger als 40 Stunden (zwei) und 40 oder mehr Stunden (drei).
Risikoklassifizierung (RC) :kein HSE-Risiko (null), mechanisches Integritätssystem (eins), Hochrisikoprozess (zwei) und sicherheitskritischer Betrieb (drei).
Abweichungen (D) :Unter Berücksichtigung der Höhe und Anzahl der Abweichungen wurden vier Gruppierungen vorgenommen. Es wurde festgestellt, dass eine Abweichung der Stufe 2 dem Dreifachen einer Abweichung der Stufe 1 und eine Abweichung der Stufe 3 dem Zweifachen einer Abweichung der Stufe 2 entsprach. Dies bedeutete, dass eine Abweichung der Stufe 1 einen Punkt, eine Abweichung der Stufe 2 drei Punkte und eine Abweichung der Stufe 3 sechs Punkte wert ist. Dies wurde auf jede Abweichung angewendet. Als Ergebnis waren die Werte:zwei oder weniger (null), größer als zwei bis fünf (eins), größer als fünf bis acht (zwei) und größer als acht (drei).
Kosten der reaktiven Arbeit (CRW) :weniger als 5.000 USD (null), 5.000 USD bis weniger als 7.499 USD (eins), 7.500 USD bis 14.999 USD (zwei) und 15.000 USD oder mehr (drei).
Eingabe des Verfahrensingenieurs (PEI) :System mit minimaler Auswirkung (null) und eskalierend bis zu System mit maximaler Auswirkung (drei).
Wartungsplan des Systems (SSMP) :RCM-Analyse am System durchgeführt (null), PQE routinemäßig ausgeführt (eins), PMs durchgeführt (zwei) und keine routinemäßige Wartung durchgeführt (drei).
Die 135 Betriebseinheiten wurden bewertet. Die Informationen wurden dann in eine Tabelle geladen und verschiedene Gewichtungen wurden angewendet, um die Bedeutung verschiedener Datensätze hervorzuheben. Das Projekt zur Sensitivitätsanalyse umfasste fünf verschiedene Gewichtungsszenarien, um sicherzustellen, dass ein einzelner Datenpunkt nicht die Priorisierung eines Systems vorantreibt.
Die Szenarien variierten von einer relativ gleichmäßigen Gewichtsverteilung (HEW, HSE, D und SSMP, jeweils 20 Prozent; CRW und PEI, jeweils 10 Prozent) bis hin zur Eliminierung von zwei Kategorien (HEW, HSE, D und CRW, jeweils 20 Prozent; PEI und SSMP, null Prozent). Im letzteren Szenario handelte es sich bei den verbleibenden Datensätzen um „wahre Daten“, die sich entsprechend der vom System nachgewiesenen Zuverlässigkeit veränderten. Die Szenarien sind in Tabelle 1 dargestellt.
Jedes Szenario in der Sensitivitätsanalyse nahm den Risikofaktor und multiplizierte ihn mit der Gewichtung dieses speziellen Szenarios. Das Produkt jeder Kategorie wurde für jede Betriebseinheit summiert. Tabelle 2 zeigt ein Beispiel aus dem ersten Szenario.
Als alle fünf Szenarien abgeschlossen waren, wurden die Endergebnisse für die Betriebseinheiten grafisch dargestellt und vom Zuverlässigkeitsteam überprüft. Vor der Festlegung der endgültigen Ranglisten und Sanierungspläne wurden zusätzliche Faktoren berücksichtigt. Wurde das betreffende Gerät vor kurzem ersetzt oder ist Ersatz im Kapitalplan vorgesehen? Können Sanierungspläne für diese Einheit auf andere Einheiten angewendet werden? Welche Funktionsgruppen werden für diese Sanierung benötigt und sind diese verfügbar? Welche Sanierungsmaßnahmen wurden in der Vergangenheit durchgeführt?
„Zum Beispiel stand eine der Zentrifugen ganz oben auf der Liste, aber wir wussten, dass ein anderer Standort ein RCM auf einem sehr ähnlichen System durchführte“, sagt Swank. „Wir mussten die Anstrengungen nicht wiederholen.“
Die endgültige Liste der vorgeschlagenen Sanierungsaktivitäten variierte je nach Betriebseinheit von einer eingehenden RCM-Analyse bis hin zu einer vollständigen Nichtbehebung des Systems.
Zu diesem Zeitpunkt wusste das Team, dass es einen umfassenden Plan hatte.
„Es war eine Qual“, sagt Lafever. „Wir haben dreimal einen Plan entwickelt – es fühlte sich an wie 30 – und wir sagten immer wieder:‚Das ist nicht gut genug.‘ ‚Wie würde sich die Qualitätskontrolle damit anfühlen?‘ ‚Wie würde die Verfahrenstechnik dazu stehen?‘ Wir waren sehr ratlos. Wir mussten sicherstellen, dass wir alle Facetten und alle möglichen Fragen adressieren.“
Swank fügt hinzu:„Der erste Angriff war wie:‚Wow, das ist noch nicht einmal annähernd so weit.‘ Es wurde offensichtlich, warum es noch nie zuvor getan wurde. Es ist viel Arbeit. Es gibt auch alltägliche Dinge, die Sie von so etwas abhalten. Aber wir haben uns gesagt, dass wir dabei bleiben und es schaffen.“
Schriftlich
Am 21. September 2004 präsentierte Swank das Priorisierungsmodell offiziell dem leitenden Team des Werks, das den Standortleiter und alle funktionalen Manager umfasst. Die anstrengenden sieben Monate Arbeit haben sich gelohnt.
„Es gab keinen Austausch oder Diskussionen hin und her“, sagt er. „Sie sagten:‚Das ist großartig. Weiter.’“
Kopfnicken und Handwinken gehen natürlich nur so weit. Daher ließ Swank Lafever einen Bericht erstellen, der den Bewertungsprozess zusammenfasste und detailliert darlegte, wie die entscheidende Geräteanalyse Jahr für Jahr durchgeführt werden würde. Der Bericht würde als Vorlage für zukünftige Bewertungen dienen.
„Ich habe den leitenden Teammitgliedern gesagt, dass sie es unterschreiben sollen“, sagt Swank. "Sie taten. Ich habe es schriftlich. Es gab kein Zögern. Das zeigt Ihnen, dass die Analyse, die wir durchgeführt haben, wirklich stark war.“
Am 28. Februar 2005 wurde die entscheidende Geräteanalyse formalisiert und vom leitenden Team genehmigt, und die Sanierungsaktivitäten für die wichtigsten Betriebseinheiten des Werks wurden in die Geschäftspläne des Werks für 2005 und 2006 aufgenommen.
Die Vorlage hat nachfolgende Auswertungen fast nahtlos gemacht.
„Letztes Jahr war die Analyse ein Kinderspiel“, sagt Lafever.
Der Plan für 2006 wurde im Mai fertiggestellt.
Remedy-Ergebnisse
Die Leiter der Wartungs- und Zuverlässigkeitsabteilung in diesem Werk von Eli Lilly sagen, dass sie derzeit nicht in der Lage sind, die Auswirkungen der Initiative zur Priorisierung der Zuverlässigkeit auf das Endergebnis in Dollar und Cent zu quantifizieren.
„Das Bedauerliche daran ist, dass wir nicht immer Jahr für Jahr die Ergebnisse unserer Arbeit sehen“, sagt Lafever. „Es kann zu einer Verzögerung von einem Jahr kommen, weil es Zeit braucht, das System zu durcharbeiten.“
Aber das bedeutet nicht, dass es keine Vorteile und Ergebnisse gegeben hat.
Redchanskiy und Doyle sagen, dass es unvermeidliche Kosteneinsparungen gibt, wenn man nur neu bewertet, wie die Wartung an einer bestimmten Anlage durchgeführt wird.
„Bei der Analyse haben wir festgestellt, dass wir viel Geld für einige Systeme ausgegeben haben, die keine reaktive Arbeit hatten“, sagt Redchanskiy. „Wir haben eine Menge für vorbeugende Wartung ausgegeben. Wir haben es mit PNs übertrieben. Wir haben die Wartung dieser Systeme geändert.“
„Die größte Veränderung besteht darin, dass man bei einigen Systemen jetzt sagen kann, dass es eigentlich in Ordnung ist, bis zum Ausfall zu laufen“, sagt Doyle. „Wenn das unsere Diagnose und unser Plan für dieses spezielle System ist, ist es in Ordnung. Das ist für uns eine ganz andere Philosophie.“
Swank sagt, dass das Produktivitätsniveau des Werks positiv beeinflusst werden kann.
„Die Tatsache, dass wir unsere Lagerbestände erreicht haben und die Tatsache, dass sich unser Geschäftsmodell in Richtung einer höheren Produktivität bewegt, zeigt, dass wir unseren ersten großen Meilenstein bereits erreicht haben“, sagt er.
Lafever ist der Ansicht, dass die Beteiligung an Sanierungsprojekten zu mehr technischem Wissen und erhöhter Betriebszeit geführt hat.
„Wenn die meisten Wartungs- und Betriebsmitarbeiter aus einer RCM-Analyse hervorgehen, könnten sie als Experten für dieses System eingestuft werden“, sagt er. „Jeder hat ein besseres Verständnis für die einzelnen Funktionen der Gruppen und wie sie zusammenarbeiten, um ihren Beitrag zur Reparatur eines Geräts oder zur Erkennung von Problemen mit einem Gerät zu leisten. Diese Interaktion selbst reduziert meiner Meinung nach die Menge an Notarbeit, die sich entwickelt.“
Der beste Erfolgsindikator?
„Das macht unser oberes Management glücklich“, sagt Doyle.
„Und das macht mich glücklich“, sagt Swank.
All diese Verbesserungen könnten erklären, warum BHI 2005 den Making Medicine Award erhielt, der an das Eli Lilly-Werk geht, das „die Anforderungen des Unternehmens am besten erfüllt und verkörpert, wie die Fertigung im Unternehmen sein soll.“
Andere Lilly-Werke nehmen die Priorisierungsinitiative zur Kenntnis und prüfen die Machbarkeit einer Übernahme. Dies hat zu einer unternehmensweiten Transparenz in Bezug auf Wartung und Zuverlässigkeit geführt.
„Ein Teil des Guten war das Verständnis des Unternehmens und das Bewusstsein für den Mehrwert, den die Wartung bietet“, sagt Reimer. „Das wollen wir unbedingt nutzen.“
Dieses Team demonstriert täglich, dass Wartungs- und Zuverlässigkeitsprofis einen Unterschied machen können und tun.
Gerätewartung und Reparatur
- Fallstudie:Antriebe und Nachrüstungen einer Rollenschneid- und Aufwickelmaschine der Papierfabrik
- Kolbenwerk verfolgt proaktiven Ansatz für Zuverlässigkeit und OEE
- Drew Troyer:Wie Geschäftsprozesse die Zuverlässigkeit beeinflussen
- Wie sich die Anlagenzuverlässigkeit auf eine schlanke Implementierung auswirkt
- Wasserkraftwerk auf Hawaii steigert Effizienz und Zuverlässigkeit
- Saudisches Elektrizitätswerk zur Verbesserung der Kraftwerkszuverlässigkeit
- Drahtloses System zur Erhöhung der Zuverlässigkeit im Kraftwerk in Nevada
- Verbesserung der Verfügbarkeit ist viel mehr als nur Wartung
- NV Energy installiert drahtlose Lösung zur Erhöhung der Anlagenzuverlässigkeit
- Fallstudie:Krisenlösung bei Maschinenausfall