Wie man Geräte für eine bessere Anlagenverwaltung in Betrieb nimmt
Es wäre nicht schön, wenn jedes neue Gerät oder System von der Installation und Inbetriebnahme bis zum ersten Ausfall viele Jahre später einwandfrei funktionieren würde. Das wäre bei den meisten Industrieanlagen eine Ausnahme.
Wenn es um die Einrichtung von Geräten geht, stellen wir möglicherweise fest, dass einige Komponenten während des Versands beschädigt wurden, der Außendiensttechniker über wenig Erfahrung verfügt oder wir Betatests für ein neues Design durchführen (ob wir dem zugestimmt haben oder nicht). Dasselbe kann für sanierte Geräte gelten, die in der ursprünglichen Anwendung und Position installiert werden.
Warum laufen Autos vom Fließband und haben selten ernsthafte Garantieprobleme? Der Grund dafür ist, dass die Automobilhersteller sowohl das Design als auch die Produktionsprozesse an Tausenden von Autos gründlich testen, verbessern und inspizieren. Industrielle Ausrüstung wird in der Regel in kleinen Fertigungslosen betrieben; daher werden nicht alle Fehler behoben.
Deshalb ist die Inbetriebnahme von Industrieanlagen eine Kunst und eine notwendige. Ich nenne es eine Kunst, weil das Einrichten neuer Geräte per Definition Kreativität, handwerkliches Geschick und deduktives Denken erfordert. Dieselben Attribute gelten für eine Kunst im wahrsten Sinne des Wortes.
Meine Einrichtung, die Upper Occoquan Service Authority (UOSA), hat ihren Wartungs- und Asset-Management-Ansatz so weit ausgereift, dass die Konzentration auf die Inbetriebnahme der nächste logische Schritt ist. Dieser Gedanke entstand als Teil unseres allgemeinen Strebens nach Best Practices in den Bereichen Zuverlässigkeit und Vermögensverwaltung.
Die Nichtbeachtung eines Inbetriebnahmeprozesses ist gleichbedeutend mit der Installation Ihres nächsten Fehlers. Die ordnungsgemäße Inbetriebnahme von Geräten kann die Nutzungsdauer verlängern, was ein wichtiges Ziel im Asset Management ist. Daher ist die Inbetriebnahme ein wesentlicher Bestandteil eines guten Asset-Management-Programms.
Nach mehreren Jahren der Entwicklung und Implementierung von Wartungsunterstützungsprozessen werden wir die verbesserte Zuverlässigkeit überprüfen, indem wir die mittlere Zeit zwischen Ausfällen (MTBF), die mittlere Zeit bis zur Reparatur (MTTR) und die Geräteverfügbarkeit verfolgen.
Eine Philosophie der Inbetriebnahme
Die grundlegenden Herausforderungen bei der Einrichtung neuer oder rehabilitierter Geräte sind ziemlich universell. Sie laufen auf die Antizipation von Problemen, die Wahrnehmung von Problemen und die Korrektur von Problemen hinaus. Nehmen wir diese Worte (Vorausschau, Wahrnehmung und Korrektur) und untersuchen, wie sie auf den Beauftragungsprozess zutreffen.
Es mag schwierig sein, sich vorzustellen, wie man Probleme antizipiert, aber ein guter Ausgangspunkt ist die Suche nach Reparaturhistorien. Reparaturhistorien können Ihnen sagen, was wann, warum, wie, wo und wer ausgefallen war. Dies setzt voraus, dass Ihr Unternehmen über genaue Reparaturhistorien in einem CMMS verfügt. Wenn Reparaturhistorien nicht von ausreichender Qualität sind, verbessern Sie sie nach Bedarf. Interviews mit Ihren Bedienern und anderen, die dieselbe Ausrüstung besitzen und betreiben, sind von unschätzbarem Wert.
Im Rahmen eines Inbetriebnahmeplans muss dieses wertvolle Wissen in einem abrufbaren Format festgehalten werden. Dies ist ein Kernstück des Plans – der Rahmen für die Erfassung von Informationen. Betrachten Sie es als die Regeln eines Spiels. Der Rahmen für die Aufzeichnung sollte den teilnehmenden Nutzern zur Verfügung stehen. Die Möglichkeit, Einträge in den Aufzeichnungen zu ändern, muss überwacht und kontrolliert werden, um Konsistenz und Genauigkeit zu gewährleisten.
Besteht die in Betrieb zu nehmende Ausrüstung aus Baugruppen bekannter Komponenten, so können zu erwartende Ausfälle durch einzelne Komponenten definiert werden. Ein Zentrifugalgebläse sollte beispielsweise über ein Leistungskurvendiagramm, eine zulässige Schwingungsgrenze und andere Spezifikationen verfügen. Wenn das Gebläse außerhalb dieser Werte arbeitet, ist eine Untersuchung erforderlich, gefolgt von geeigneten Korrekturmaßnahmen.
Manche Probleme schleichen sich so langsam ein, dass sie erst erkannt werden, wenn ein Schaden aufgetreten ist. Dies ist eine Wahrnehmungsstörung. Hier ist es notwendig, die entscheidenden Testpunkte zu bestimmen und die akzeptablen Werte zu ermitteln. Manchmal wissen wir nicht, was akzeptabel ist; Hier bietet eine Rücksprache mit dem Hersteller oder anderen mit ähnlichen Geräten eine Anleitung.
Ist die Ursache eines Problems endgültig geklärt, ist der nächste Schritt die Korrektur. Die Lösung sollte das Kernproblem behandeln. Wenn beispielsweise eine Unwucht mit einmaliger Drehzahl erkannt wird, den rotierenden Körper auswuchten. Wenn die Struktur der Maschine eine harmonische Resonanz aufweist, so dass die geringste Erregung zerstörerische Schwingungen verursacht, achten Sie auf die Steifigkeit der Struktur.
Wenn die Korrekturmaßnahmen abgeschlossen sind, überprüfen Sie, ob die erwarteten Verbesserungen wahrnehmbar sind. Verwenden Sie Messwerkzeuge, um zu überprüfen, ob die Korrektur das tat, was sie tun sollte. Hier glänzen PdM-Tools – Schwingungsanalyse, Ultraschallerkennung, Motorstromsignaturen, Ölanalyse und Thermografie.
Keine der oben genannten Bemühungen wird die gewünschten Ergebnisse erzielen, es sei denn, es werden Maßnahmen ergriffen. Tun Sie etwas und dokumentieren Sie, was getan wurde. Dies steigert den Wert des Inbetriebnahmeprojekts.
Vorbereitung der Inbetriebnahme
Es ist unbedingt erforderlich, sich mit den in Betrieb genommenen Geräten vollständig vertraut zu machen. Dies bedeutet, die Handbücher im Voraus zu lesen (wenn möglich), die Einzelblätter für Komponenten zu lesen, die Bedienungsanleitung zu studieren, den Hersteller dazu zu bringen, Ihre Fragen zu beantworten und andere mit der gleichen Ausrüstung zu kontaktieren, um zu erfahren, wie sie erfolgreich waren.
Es ist nützlich, Einrichtungen zu besuchen, in denen ähnliche Geräte sowohl erfolgreich als auch erfolglos funktionieren. Sprechen Sie mit den Bedienern und Wartungspersonal, da diese eine enge Verbindung zu den Geräten haben.
Ich sprach mit einem befreundeten Elektriker über einige der interessanteren und schwierigeren Jobs, die wir im Laufe der Jahre gemacht hatten. Wir haben darüber diskutiert, wie man Kabel in eine überfüllte Anschlussdose einpasst. Mein Freund sagte:"Du musst einen Plan haben." Das ist mir geblieben, weil es zeigt, dass selbst die banalste Aufgabe, wie das Abrichten von Drähten auf engstem Raum, einen Plan erfordert.
Auch die Inbetriebnahme erfordert einen Plan. Ein Plan ist nichts anderes als ein gut durchdachter Leitfaden, der Regeln, Zeichnungen, Checklisten und Verfahren beinhalten kann. Ein Inbetriebnahmeplan ist so etwas wie ein Kochrezept; du befolgst es, aber passst es je nach Erfahrung nach Bedarf an.
Der Plan
-
Wählen Sie einen Projektleiter aus – einen, der die Zeit und das Temperament hat, Ressourcen effektiv zu kommandieren
-
Definieren Sie die absoluten Anforderungen für einen akzeptablen Betrieb – welche Arbeit muss das Gerät leisten?
-
Identifizieren und beheben Sie erwartete Fehlermodi für das Gesamtsystem und alle Subsysteme.
-
Stellen Sie sicher, dass die Betriebsbedingungen (wie vom Geräteverkäufer angegeben) eingehalten werden – d. h. die Betriebsumgebungsbedingungen (Temperatur, Feuchtigkeit, Druck, Spannung usw.).
-
Definieren Sie die erforderlichen Testschritte und die Reihenfolge dieser Schritte im Inbetriebnahmeprozess. Diese Schritte werden aus Erfahrung, Wissen und Forschung abgeleitet.
-
Definieren Sie die erforderlichen Fähigkeiten – Mechanik, Elektrik, Steuerung und Technik
-
Planen Sie die Ressourcen und das Personal ein, um die definierten Schritte durchzuführen
-
Notieren Sie die Beobachtungen und Testpunktwerte, die während jedes Schritts gemessen (wahrgenommen) wurden
-
Ergebnisse überprüfen (Daten in Informationen umwandeln)
-
Ergreifen Sie bei Bedarf Korrekturmaßnahmen
-
Stellen Sie sicher, dass die Korrekturmaßnahmen zu den gewünschten Ergebnissen führen
-
Schulen Sie die Bediener, um sicherzustellen, dass sie wissen, wie das Gerät unter allen Umständen richtig bedient wird
-
Implementieren Sie ein Programm zur vorbeugenden Wartung (PM), das Best Practices berücksichtigt
-
Wiederholen Sie diese Schritte nach Bedarf, bis alle absoluten Betriebsanforderungen erfüllt sind
-
Zeichnen Sie den Inbetriebnahmeprozess auf und beschreiben Sie, was zum Erfolg geführt hat und was nicht, um später darauf zurückgreifen zu können.
-
Erstellen Sie einen Wissensschatz für die Inbetriebnahme und aktualisieren Sie ihn, wenn im Rahmen der Inbetriebnahmeprozesse neue Informationen bekannt werden.
Der Leiter der Kommissionierung
Ein Inbetriebnahmeprojekt erfordert auch einen Leiter, der die Schritte verwaltet und den Plan ausführt. Dieser Leiter fungiert als zentrale Kommunikationsdrehscheibe für das mit dem Inbetriebnahmeprojekt betraute Personal. Ähnlich wie bei der Ursachenforschung ist es ratsam, keine dominante Persönlichkeit als Führungskraft zu wählen.
Menschen mit dominanten Überzeugungen können den Prozess mit ihren Veranlagungen korrumpieren. Die optimale Führungskraft ist jemand, der dem Plan folgt und überprüft, ob alle Schritte durchgeführt und dokumentiert wurden. Diese Führungskraft muss neben Durchsetzungsfähigkeit auch über gute Organisations- und Kommunikationsfähigkeiten verfügen.
Wählen Sie einen kompetenten Leiter aus, der genügend Zeit hat, sich dem Projekt zu widmen, ohne sich auf ein weiteres Projekt einzulassen. Das macht nur Sinn und bringt erfolgreiche Unternehmen voran.
Fehler, es richtig zu machen (und richtig von falsch zu wissen)
Es ist eine Tatsache unserer Zeit, dass von uns erwartet wird, die Effizienz und Genauigkeit mit dem Fest der computerbasierten Werkzeuge, die uns vorgelegt werden, dramatisch zu steigern. Die Inbetriebnahme ist kein Prozess, der überstürzt werden kann. Es muss umsichtig mit angemessenen Mitteln durchgeführt werden. „Je schneller wir fahren, desto schlechter werden wir“ ist ein althergebrachter Ausdruck, der sowohl Erfahrung als auch Volksweisheit verkörpert.
Es gibt Gelegenheiten, in denen Inbetriebnahmeteams zu tief nach Problemen suchen und Probleme übersehen, die offensichtlich sind. Es ist wichtig, alle verfügbaren Informationen zu überprüfen und alle zumutbaren Schritte bei der Inbetriebnahme zu unternehmen. Scheuen Sie sich nicht, Ihre Prozesse von einem unabhängigen Beobachter von außen betrachten zu lassen. Erwarten Sie während der Inbetriebnahme einige Ursachenforschung.
Viele Probleme sind vor der ersten Inbetriebnahme neuer Geräte zu erwarten. Die Aufnahme kritischer Aufgaben in das PM-Programm gehört ebenso zur Inbetriebnahme wie alle anderen Schritte. Alle erforderlichen Wartungsaufgaben, die mühsam, zeitaufwändig oder unordentlich sind, werden oft aufgeschoben. Rechnen Sie mit Problemen wie Filterverstopfungen und Lüfterflügeln, die sich mit Schmutz aufladen und unausgeglichen werden.
An der UOSA gelernte Lektionen
In den letzten Jahren haben wir einige wertvolle Lektionen gelernt. Wir haben Probleme mit dem Fehlen eines ordnungsgemäßen Inbetriebnahmeprozesses sowie die Vorteile ordnungsgemäßer Verfahren aufgedeckt. Unsere Lektionen heben den vorteilhaften Einsatz von Predictive Maintenance-Technologien (PdM) wie Ultraschall, Vibration, Ölanalyse, Wärmebildgebung und Motorstromsignaturanalyse hervor, aber auch die menschlichen Sinne sind Teil des Bewertungsprozesses.
Elektromotoren in kritischen Anwendungen
Ob ein Motor neu vom Hersteller oder generalüberholt, der Zustand mit einem Motorstrom-Signatur-Analysegerät ist unbedingt zu prüfen, sobald er vor Ort eintrifft. Wenn dieser Test nicht sofort durchgeführt wird, wird er schnell vergessen oder schnell vor der Installation des Motors durchgeführt. Wer möchte wissen, dass ein Motor ein Problem hat, kurz bevor er eingebaut wird oder noch schlimmer, sobald er eingeschaltet ist?
Unsere Erfahrung hat gezeigt, dass die Installation ein schlechter Zeitpunkt ist, um Geräteprobleme zu entdecken, da Personal und Rigging-Equipment mobilisiert werden und es zu Betriebseinschränkungen kommen kann, wenn der Motor nicht termingerecht installiert wird.
Für die Qualitätskontrolle von Motoren, ob neu oder umgebaut, muss ein vollständiger Satz von Verfahren festgelegt werden, wenn sie empfangen werden. Anbieter von Motortestgeräten sind eine gute Quelle für die Entwicklung dieser Verfahren. Für die Reparatur eines Motors ist auch eine Reihe von Richtlinien erforderlich, um zu überprüfen, was während der Reparatur durchgeführt wurde. Es gibt viele Online-Ressourcen dazu, wie ein Motor repariert werden sollte.
Vergleichen Sie die Empfehlungen verschiedener Autowerkstätten, um einen breiten Überblick zu erhalten. Motoren sind die Hauptantriebskräfte der Industrie und müssen kritisch beobachtet werden, oder Prozessfehler sind sicher.
Grundlegende Offline-Tests sollten durchgeführt werden, bevor ein Motor an seinen Stromkreis angeschlossen wird. Ein Polarisationsindextest und ein Stoßspannungstest sind unabdingbar. Wenn der Motor zum ersten Mal eingeschaltet wird, ist es wichtig, den Strom in allen drei Phasen zu messen. Wenn ein Online-Test möglich ist, sollte dieser durchgeführt werden. Wenn ein Ultraschallgerät verfügbar ist, sollten die Schallsignaturen der Peilung aufgezeichnet werden, um grundlegende Dezibelpegel und Zeitbereichsdiagramme für zukünftige Vergleiche zu erhalten.
Wenn der Motor vor dem Ankuppeln an die angetriebene Komponente betrieben werden kann, ist es wünschenswert, die Schwingungseigenschaften zu messen und aufzuzeichnen. Wenn einer dieser Tests Probleme aufdeckt, muss die Installation unterbrochen und Korrekturmaßnahmen ergriffen werden.
Vertikale Turbinenpumpen (VTP)
Die Wasserindustrie setzt VTP häufig für Prozesse ein. Das Laufrad dieser Pumpen ist in einer Spirale montiert, die bis zu 9 m unter der Erdoberfläche sitzt. Das Laufrad wird von einer langen Welle angetrieben, die durch eine Reihe von „Spider“-Lagern entlang der Innenseite der Pumpensäule, durch die das Wasser fließt, stabilisiert wird. Der Motor ist oberirdisch auf einem Sockel in der vertikalen Achse montiert.
Auf Anregung eines PdM-Technikers eines benachbarten Wasserwerks haben wir vor dem Absenken in den Nassbrunnen zwei hermetisch abgedichtete Schwingungssensoren an der Spirale eines neuen VTP angebracht. Die Sensoren wurden in der horizontalen Ebene installiert, um 90 Grad radial zueinander positioniert. Als die Sensoren bei der Erstinbetriebnahme starke Vibrationen feststellten, war der Installateur überrascht. Sie hatten noch nie zuvor jemanden auf Vibrationen an der Spirale testen sehen. Der Motor vibrierte nicht nennenswert, daher gingen sie davon aus, dass die Installation zufriedenstellend war.
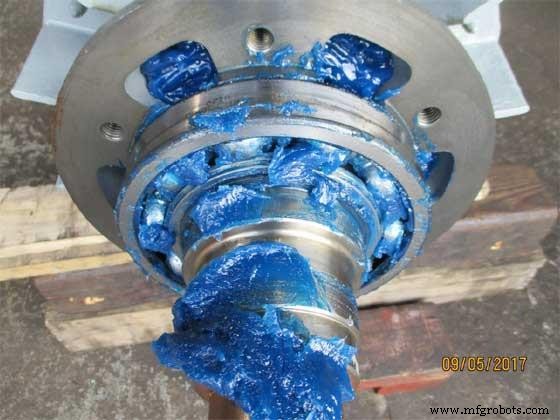
Brandneuer Motor war überfettet
Die Erkennung dieser Schwingung führte zu der Entdeckung, dass eine Gruppe von Befestigungsschrauben in der Sohlenplatte zu lang war und in Sackgewindebohrungen endete. Die Sicherungsscheiben dieser Schrauben wurden nicht vollständig zusammengedrückt, was Resonanzen ermöglichte, die sich als an der Spirale erfasste Schwingung bemerkbar machten. Wir installieren diese Schwingungssensoren jetzt an allen vertikalen Turbinenpumpen, wenn sie zur Wartung gezogen werden.
Wir haben auch gelernt, dass bei der Aufstellung dieser Pumpentypen einige Besonderheiten zu beachten sind. Die Grundplatte muss eben und die Pumpensäule senkrecht stehen. Auch die Sohlenplatte muss fest verfugt werden, um Vibrationen zu vermeiden. Die Pumpenwellenabschnitte sollten sich innerhalb eines Nennwerts von 0,005 Zoll des angezeigten Gesamtschlags befinden.
Die Vibrationsstandards 2000 des Hydraulics Institute (HI) lieferten einen Wert für die zulässige Vibration, die an der Oberseite des Motors für diesen Pumpentyp gemessen wurde. Spätere HI-Standards enthielten diesen Wert nicht. Der Eigentümer muss den zulässigen Wert bestimmen. Unsere Erfahrung ist, dass die Pumpenhersteller selten einen Wert angeben. Im Allgemeinen sind nach unserer Erfahrung weniger als 0,2 Zoll pro Sekunde akzeptabel.
Zentrifugalgebläse
Ein Zentrifugalgebläse (für Saugzuganwendung) wurde mit einem regenerativen thermischen Oxidationssystem geliefert. Das Gebläserad wurde direkt auf einer 7,5 PS-Motorwelle montiert, und ein auf Zoll der Wassersäule kalibriertes Druckmessgerät wurde an der Gebläseausgangsleitung installiert. Die Gebläsevibration nahm nach drei Betriebsjahren deutlich zu, der Motor fiel aus und ein kritischer Prozess wurde abgeschaltet.
Nach dem Austausch des Motors waren die Vibrationen weiterhin hoch. Es wurde vermutet, dass Stoßresonanzen zu einer Delamination des Gebläserades führen, was zu einer dynamischen Unwucht und den hohen Vibrationen führte. Bevor weitere Maßnahmen zur Behebung des Problems ergriffen wurden, klemmte das Rad im Gebläsegehäuse durch Delamination. Der Radschaden führte dazu, dass der kritische Prozess erneut beendet wurde.
Bei der Inbetriebnahme hat der Auftragnehmer für dieses Gebläse keine Schwingungsgrenze vorgegeben. Als wir nach dem Fehler beim Gebläsehersteller nachfragten, stellten wir fest, dass die Vibrationsgrenze weniger als 0,2 Zoll pro Sekunde betrug. Es wurde festgestellt, dass das Gebläse vor dem Ausfall mit 0,7 Zoll pro Sekunde arbeitete, d. h. weit außerhalb der Spezifikation. Niemand hatte eine anfängliche Basislinien-Vibrationsmessung gemacht, daher gab es keine guten Vergleichsdaten.
Der Manometerwert an der Ausgangsleitung wurde während der Inbetriebnahme nie aufgezeichnet. Niemand wusste, was die Anzeige während des normalen Betriebs sein sollte. Die Messnadel hatte während der Pumpbedingungen heftig oszilliert, bis sie bei 19 Zoll der Wassersäule (WC) klemmte. Ein neues Manometer wurde installiert und der Druck bei normalem Betrieb wurde als 39 Zoll WC aufgezeichnet.
Die gewonnenen Erkenntnisse bei der Inbetriebnahme bestehen darin, Vibrations- und Ausgangsdruckwerte aufzuzeichnen, diese mit den zulässigen Grenzwerten des Herstellers zu vergleichen und die Bediener darüber zu informieren, welche Bedingungen Schäden verursachen könnten. Als Aufgabe der vorbeugenden Wartung (PM) wurde auch die Trendanalyse von Schwingungen hinzugefügt.
Lagerfehler des Schlammtrockner-Mischers
Bei der Installation einer neuen Schlammtrocknungsanlage wurde jeder Schritt der Inbetriebnahme vom Auftragnehmer sorgfältig durchgeführt. Die großen Kugellager an der Mischtrommelwelle versagten jedoch auf spektakuläre Weise. Ihnen fehlte es komplett an Fett aus der Fabrik und sie zerkauten sich zu unförmigen Schrottkugeln. Eine einfache Messung mit einem Körperschallgerät hätte das Fehlen von Schmierfett festgestellt, während die Lager noch zu retten waren. Die Ultraschallprüfung wurde jetzt gegebenenfalls in die Inbetriebnahmeprozesse aufgenommen.
Tauchpumpen-/Motoreinheiten
Tauchpumpen sind bei Abwasseranwendungen sehr beliebt geworden. Sie können in Prozessschächte abgesenkt werden, wo sie relativ einfach in einen Kupplungsflansch gleiten und dann an das Stromnetz angeschlossen werden. Sie sind dem „Plug-and-Play“ so nah, wie Industrieanlagen nur kommen können.
Wir haben festgestellt, dass es ratsam ist, die Stromverkabelung mit Instrumenten zur Analyse der Motorstromsignatur zu testen, bevor der Pumpenmotor an den Stromkreis angeschlossen wird. Auf diese Weise können die Techniker nachweisen, dass der Stromkreis keinen Erdungswiderstand aufweist, der zu Fehlern im Frequenzumrichter führen kann. Der Pumpenmotor sollte sowohl Offline- als auch Online-Tests unterzogen werden.
Einige dieser Tauchpumpen verfügen über einen Ölbehälter für die Wellenabdichtungen. Als Teil der PM muss dieses Öl abgepumpt und auf die Menge an Prozesswasser überprüft werden, die durch die Spiraldichtung eindringt. Die PM-Anforderung für diese Prüfung beträgt im Allgemeinen einen Zyklus von 365 Tagen. Wir haben jedoch festgestellt, dass es beim Einbau einer neuen Pumpe sinnvoll ist, nach den ersten 90 Tagen den Wassergehalt im Öl zu überprüfen. Es hat gelegentlich überschüssiges Wasser aufgedeckt.
Abwasserklärer - Zahnradgetriebe
Als der Auftragnehmer ein neues, großes Zahnradgetriebe (mit einem Durchmesser von mehr als 2 m) installierte, wurde es mit dem vom Hersteller angegebenen Öl gefüllt. Einer unserer Tests vor der Inbetriebnahme war die Entnahme einer Ölprobe. Als unser Techniker eine Probe des Öls nahm, stellte sich heraus, dass es im Vergleich zur Spezifikation eine kritisch niedrige Viskosität hatte.
Nach einiger Recherche stellte sich heraus, dass der Hersteller diese Getriebe halbgefüllt mit Dieselkraftstoff ausliefert. Ohne sich dessen bewusst zu sein, fügte der Auftragnehmer Öl in die Füllleitung hinzu, was bei der Prüfung des Öls zu einer niedrigen Viskosität führte. Strenge Öltests wurden in die Inbetriebnahme-Checkliste aller Klärantriebe aufgenommen.
Schraubenkompressoren
Diese Verdichtertypen bieten Vorteile beim Energiesparen, gehen jedoch mit wichtigen Wartungsaufgaben einher. Insbesondere muss der Ölzustand genau überwacht werden. Die Erfüllung der Garantieanforderungen hängt oft davon ab, dass nachgewiesen werden kann, dass eine vorbeugende Wartung durchgeführt wurde.
Viele Hersteller von Schraubenkompressoren verlangen von ihren Besitzern, dass sie Ölproben an ihr bestimmtes Öltestlabor senden. Andernfalls kann die Garantie erlöschen. Die Inbetriebnahme dieser Kompressoren beinhaltet, dass ein wachsames PM-Programm mit besonderem Augenmerk auf die Ölanalyse durchgeführt wird.
Nach der Inbetriebnahme
Nach der Inbetriebnahme müssen regelmäßige Kontrollen durchgeführt werden, um sicherzustellen, dass der Betrieb der Ausrüstung so läuft, dass Ausfälle vermieden werden. Der beste Inbetriebnahmeprozess schlägt fehl, wenn die Bediener versuchen, das Gerät auf eine Weise zu verwenden, für die es nicht vorgesehen ist.
Überprüfen Sie, ob die PM-Verfahren richtig oder überhaupt nicht durchgeführt werden. Aus diesen Quartalen resultierende Ausfälle können zu Unrecht auf Fehler im Inbetriebnahmeprozess zurückgeführt werden. Sie sollten regelmäßig Metriken, Key Performance Indicators (KPIs) und PdM-Trends überprüfen, um sicherzustellen, dass die Geräte innerhalb der Spezifikationen funktionieren.
Abschließende Gedanken
Bis zu einem gewissen Grad ist die Inbetriebnahme von Geräten beim ersten Versuch eine Vermutung. Das Raten wird mit jeder Erfahrung besser und je mehr Informationen zum Wissensbestand hinzugefügt werden. Es wird eine Menge Ursachenforschung geben. In Wirklichkeit ist das, was getan wird, der gesunde Menschenverstand. Mit jedem Projekt wächst der Wissensschatz zu einer besseren Referenz für zukünftige Inbetriebnahmeprojekte. Die Inbetriebnahme von Geräten ist wirklich eine wertvolle Kunst.
Gerätewartung und Reparatur
- Strategien für das Digital Asset Management
- So verwenden Sie KI für intelligentes Bestandsmanagement
- Schlüssellehren für die Geschäftsleitung
- Asset Management für neue Einrichtungen:Design, Bau und Inbetriebnahme
- Wie das industrielle Internet das Asset Management verändert
- 4 Tipps und Herausforderungen für besseres IIoT-Asset-Management
- So bereiten Sie Maschinen für den Umzug vor
- 4 Ziele für die Vermögensverwaltung
- So kaufen Sie Asset-Management-Software
- So bereiten Sie Ihre Baumaschinen auf den Frühling vor