RAPM-Entwicklung mit PtFS
Dieser Blog ist eine Online-Seitenleiste für das Feature „Revolutionizing the Composites Cost Paradigm, Part 2:Forming“ vom Mai 2020, in dem das von The Boeing Co. (Chicago, Illinois, USA), dem „formenden“ Teil des Tailorable Feedstock and Forming (TFF)-Programms von DARPA, um eine schnelle, kostengünstige und flexible Herstellung kleiner, komplex geformter Verbundteile zu ermöglichen.
Alle drei Material- und Prozesswege im RAPM-Programm – Harzinfusion, Duroplast-Prepreg und thermoplastisches Formen – umfassten Versuche mit einem PtFS-Steuerungs- und Werkzeugsystem für pixelierte Erwärmung (Production to Functional Specification, PtFS), das von Surface Generation geliefert und bei Boeing R&T in . untergebracht wurde St. Louis (siehe Tabelle unten).
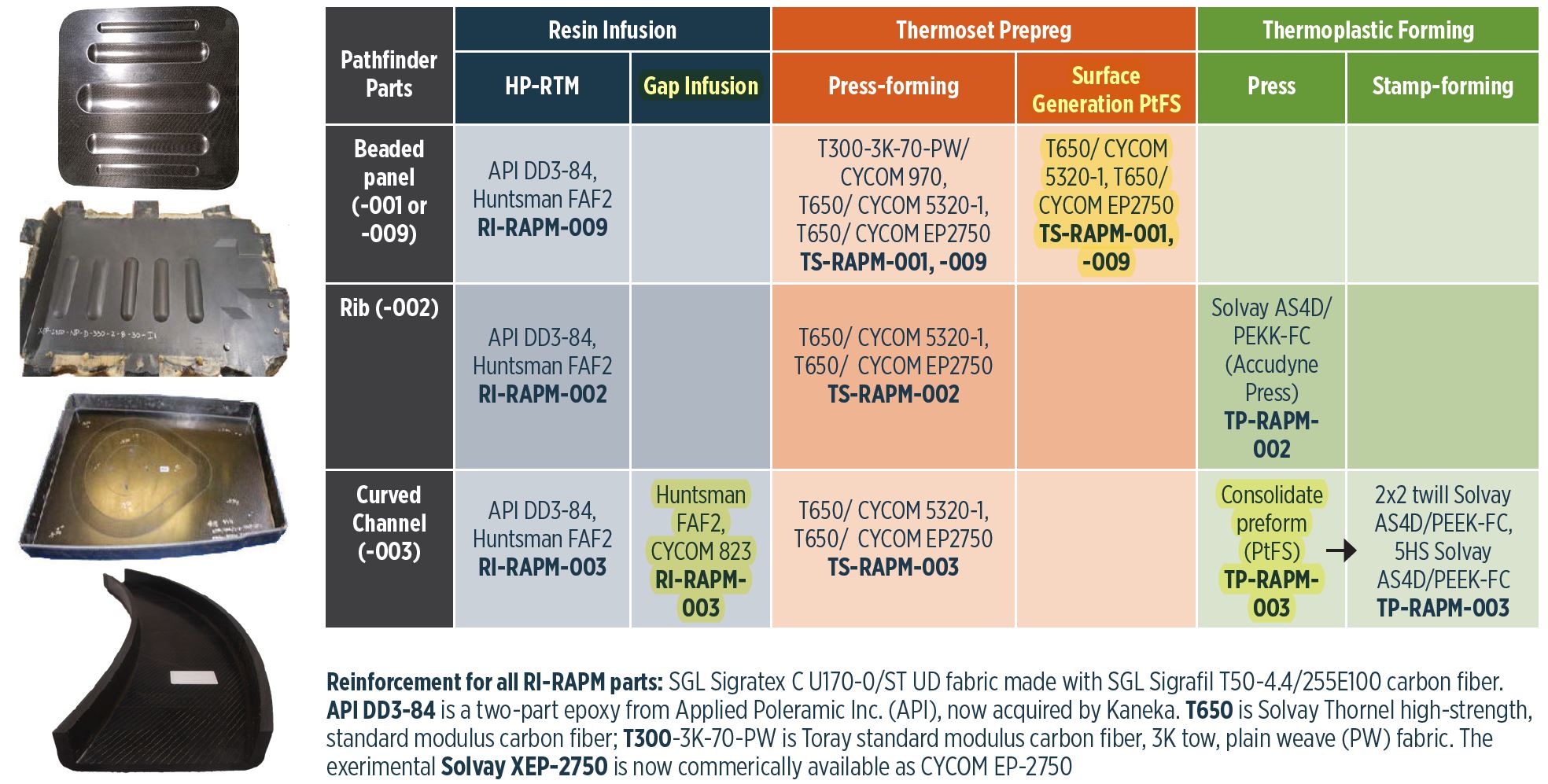
Beachten Sie, dass PtFS seit Jahren kommerzialisiert wird. Dieser Blog betrifft die Prozessentwicklung von RAPM mit dem PtFS-System. Referenzen für diesen Blog sind:
- 2019 SAMPE (20.-23. Mai, Charlotte, N.C.) Fachbeitrag und Dia-Präsentation zum Thema „Entwicklung skalierbarer dynamischer Steuerungsarchitekturen für Arbeitszellen zur Herstellung flexibler Verbundwerkstoffe“ von Steven M. Shewchuk 1 , Ben Halford 2 , Michael P. Matlack 1 , Andrew Sharpe 2 und Pete Massey 2 . 1 The Boeing Company, St. Louis, Missouri, USA 2 Surface Generation Ltd. (Rutland, Großbritannien).
- Technisches Papier von SAMPE 2020, „Compression Molding of Complex Duroplast Laminates“ von Travis R. Adams, Timothy J. Luchini, Jared B. Hughes, Steven M. Shewchuk, Adam Martinez und Gail Hahn, The Boeing Company.
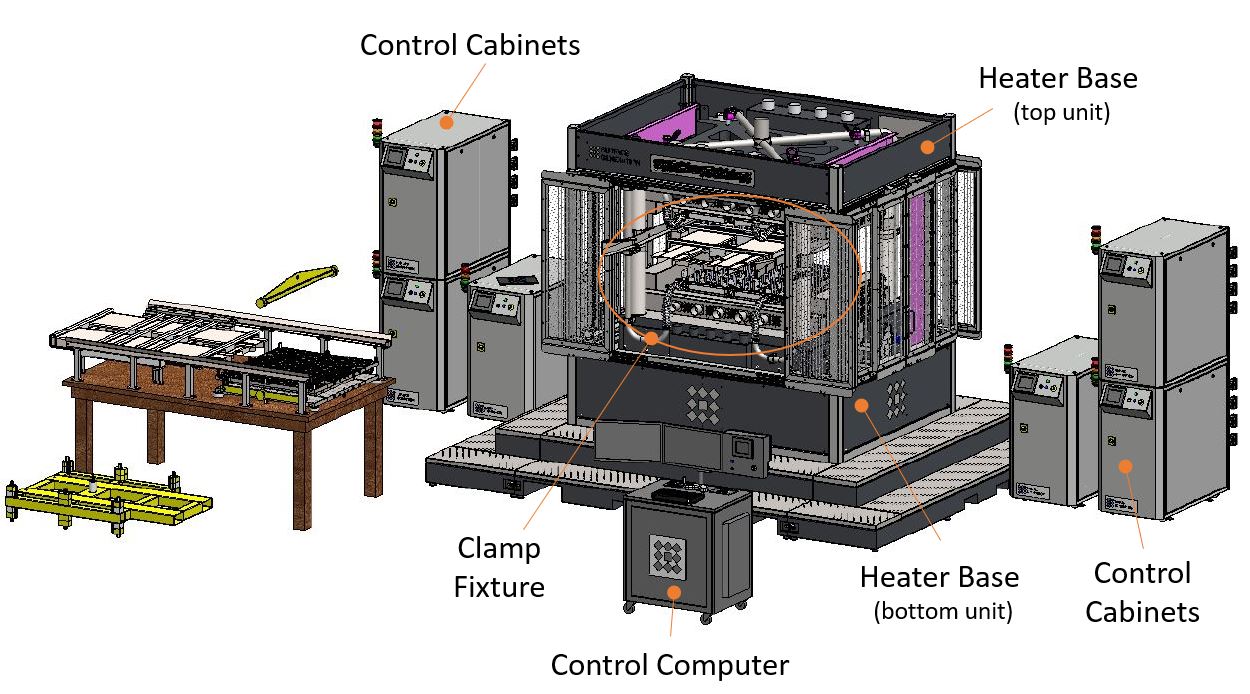
PtFS-Systemkomponenten
Das PtFS-System ist modular aufgebaut und kann komplett eigenständig sein oder Teile der bestehenden Infrastruktur nutzen. Für den Verdichtungs-/Konsolidierungsdruck kann das System eine vorhandene hydraulische Presse oder eine hydraulisch betätigte Werkzeugspannvorrichtung verwenden. Die Boeing St. Louis PtFS-Zelle ist mit letzterem ausgestattet, einer 150 Tonnen schweren Spannvorrichtung von Surface Generation entwickelt. Diese Formzelle nimmt ein Teilevolumen von 750 x 750 x 100 Millimeter auf.
Die Boeing St. Louis PtFS-Zelle umfasst Positions- und Drucksteuerung. „Die Orchestrator-Software von Surface Generation wird verwendet, um die CF-OaO-RAPM PtFS-Arbeitszelle zu steuern“, sagt Boeing Technical Fellow und RAPM-Programmmanagerin Gail Hahn. „Jedes Werkzeug wird im System durch Weg- und Druckabstimmung kalibriert. Die Druckkalibrierung wird durchgeführt, um die Hydraulik auf die erwarteten Drücke abzustimmen, denen das Werkzeug während der Bearbeitung ausgesetzt ist. Werkzeugtrennung und Verschiebungskalibrierung werden durchgeführt, um die Öffnungs-/Schließposition des Werkzeugs sowie die langsamen/schnellen Schließbereiche einzustellen, was die Werkzeugstirnseite während der manuellen und automatischen Steuerung schützt.“ Positionsmessungen werden mit vier String-Potentiometern durchgeführt, erklärt der Boeing-Ingenieur für Verbundwerkstoffe und RAPM-Forscher Steven Shewchuk. „Jeder befindet sich an einem Führungspfosten der Spannvorrichtung, um auch die Plattenposition zu messen und eine Sicherheitsmethode zur Identifizierung von Plattenregalen während des Betriebs bereitzustellen. Die Druckregelung wird durch einen einzelnen Inline-Druckwandler vervollständigt, der eine Feedback-Regelung für die Hydraulikpumpe der Spannvorrichtung bietet.“
Oberhalb und unterhalb der Spannvorrichtung befinden sich oben und unten Heizungsunterteile . Diese enthalten alle Heiz-/Kühlkomponenten und reagieren auf die Ausgänge der Schaltschränke (drei Schränke für jede Heizungsbasis im Boeing-Setup). Werkzeugflächen sind für jeden Heizsockel ausgelegt und werden mit einem Schienen- und Ladesystem installiert.
Jede Werkzeugstirnseite wird mit Druckluft erwärmt und gekühlt, die auf die Unterseite jeder Werkzeugstirnseite gerichtet und über einen Diffusor verteilt wird. Jeder Satz abgestimmter Werkzeugflächen aus Metall sind in 180 individuell steuerbare Heizungskanäle unterteilt — 90 für die obere Werkzeugfläche und 90 für die untere. Die Heizkanäle sind über jede Werkzeugstirnfläche in einem Raster von 10,0 Zentimetern beabstandet. Jeder Kanal verfügt über eine Heizung, eine zweistufige Druckluftquelle und zwei Feedback-Thermoelemente die federbelastet sind, um einen engen Kontakt mit der Rückseite der Werkzeugstirnseite zu gewährleisten. Das Aufheizen der RAPM-Werkzeugflächen verbrauchte 1 Kubikfuß pro Minute Druckluft pro Heizkanal, während das Kühlen 3 Kubikfuß pro Minute verbrauchte.
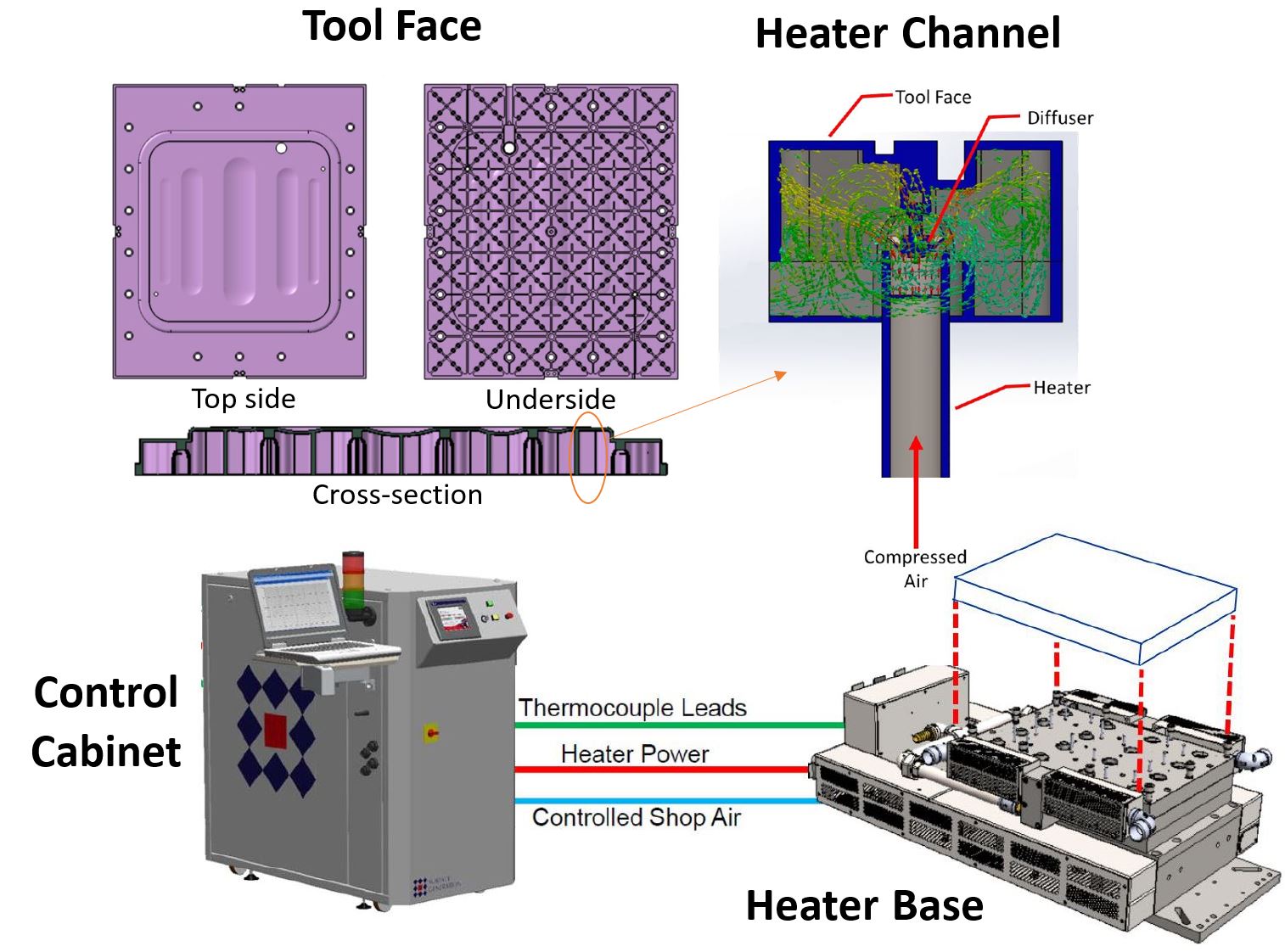
Werkzeugflächen
Werkzeugstirnseiten in RAPM wurden aus Werkzeugstahl auf eine Dicke von ≈3 Millimetern bearbeitet. Die untere Werkzeugstirnseite für TS-RAPM-001-201 ist oben links in der obigen Abbildung dargestellt. Die Oberseite des Werkzeugs sieht aus wie ein Standard-Stanzwerkzeug, aber die Unterseite zeigt die Heizkanäle.
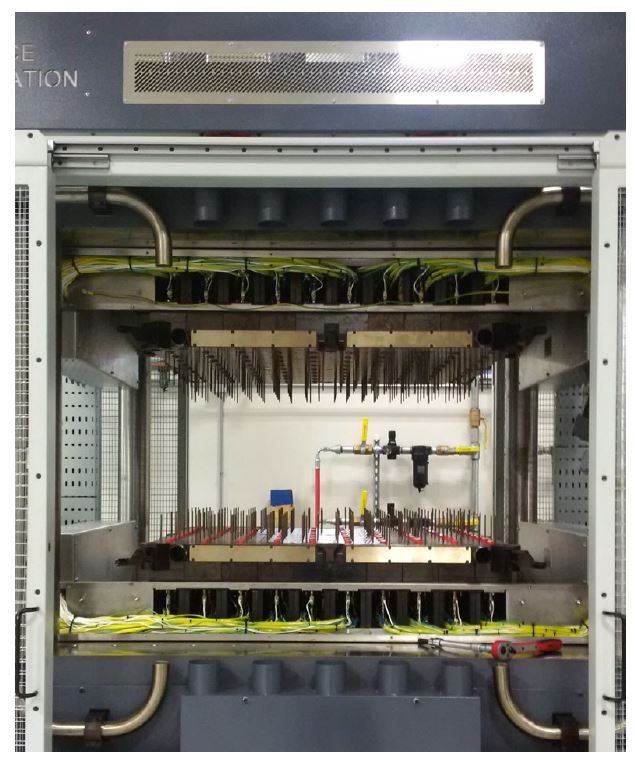
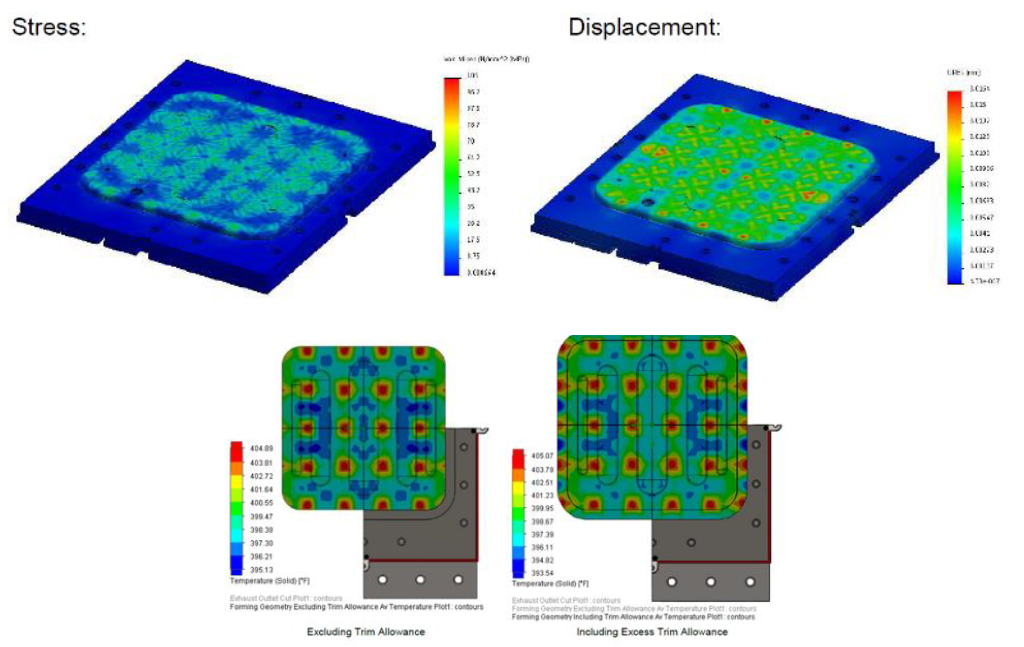
Werkzeugstirnseiten mit akzeptablen Geometrien können mit anderen Werkzeugstirnseiten ausgetauscht werden, die für dieselbe Heizbasis entwickelt wurden. Das Werkzeug benötigt die gleichen Abmessungen des Heizkanals, die ungefähre Platzierung des Thermoelements und eine Tiefe, die innerhalb des Federwegs des Thermoelements liegt.
Das zum Wechseln einer Werkzeugstirnseite verwendete Schienenladesystem richtet alle 180 federbelasteten Feedback-Thermoelemente in Hülsen auf der Rückseite der Werkzeugstirnseite aus. Stifte richten die Werkzeugstirnfläche aus und ermöglichen das Laden des Werkzeugs ohne präzise Staplersteuerung. Der Werkzeugwechsel kann in 2-4 Stunden mit zwei Bedienern abgeschlossen werden, einschließlich des Zerlegens und Wiedereinsetzens der Werkzeugfront in den Bilderrahmen.
Es wird so viel Material wie möglich abgetragen, um die thermische Masse zu reduzieren und die Heiz- und Kühlraten zu verbessern. Aus diesem Grund erforderte jede in RAPM verwendete Werkzeugfläche eine strukturelle Finite-Elemente-Analyse (FEA), um zu bestimmen, ob die Werkzeugfläche der Verarbeitungstemperatur und dem Druck standhält. Die Werkzeugflächen wurden mit linearer und nichtlinearer FEA sowie stationärer und transienter thermischer Strömungsanalyse (Computational Fluid Dynamics, CFD) optimiert. Letzteres trug zu einer gleichmäßigen Werkzeugerwärmung bei. Sowohl die Werkzeugdicke als auch die Luftdiffusoren in jedem Heizkanal wurden modifiziert, um die Temperaturgleichmäßigkeit zu verbessern. Eine iterative Schleife zwischen FEA und CFD ermöglichte die Anpassung der Geometrie, um die gewünschte Werkzeugstirntemperatur beizubehalten und gleichzeitig die erforderlichen Sicherheitsfaktoren für die Werkzeugstirnunterstützung zu erfüllen.
Heizzonen und Temperaturregelung
Heizungskanäle werden normalerweise in Zonen gruppiert, wobei die Anzahl der Heizungskanäle pro Zone pro Teil angegeben wird. Jeder Zone ist ein Heizprofil zugeordnet, und Toleranzen können nach Bedarf innerhalb und zwischen den Zonen eingestellt werden. Dadurch können alle Heizungen in jeder Zone gemäß ihrem vorgeschriebenen Heizprofil heizen, kühlen oder die Temperatur halten, indem sie die Heizleistungsstufen und die Druckluftdurchflussmengen dynamisch variieren.
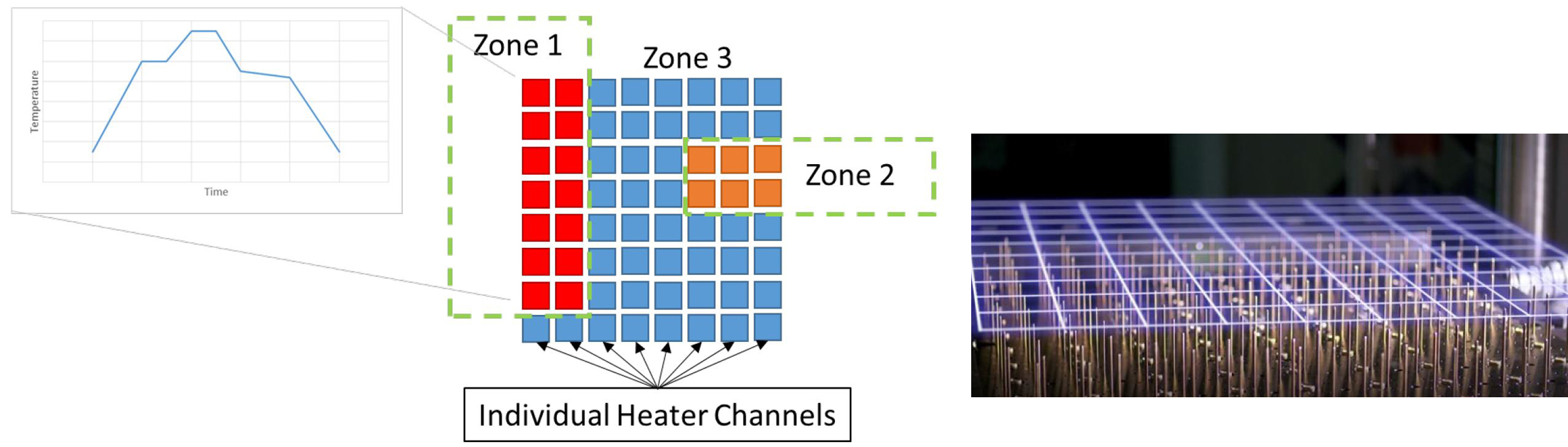
Obwohl die PtFS-Gerätesteuerungssoftware sowohl über analoge als auch digitale Heizstrategien verfügt, die auf verschiedene Heizszenarien zugeschnitten werden können, verwendet die RAPM-Zelle eine analoge Steuerung. Dies erfordert eine automatische Abstimmung des Systems, um die Heizleistungsstufen bei den Zieltemperaturen zu bestimmen. Die Leistungsstufen für jede Heizung werden eingestellt, um ein Über- oder Unterschwingen während der Heiz-/Kühlrampen zu verhindern und die Temperatursollwerte beizubehalten. Die automatische Abstimmung bestimmt automatisch konstante Werte für ein modifiziertes Proportional-Integral-Differential-Regelverfahren für jeden Heizkanal bei jeder spezifizierten Temperatur. Sobald die automatische Abstimmung abgeschlossen ist, können Heizprofile für jede Zone geschrieben werden. Alle thermischen Profile wurden überprüft, um sicherzustellen, dass das Verbundteil Temperaturen innerhalb von ±5,5 °C (±10 °F) des gewünschten Sollwerts ausgesetzt war.
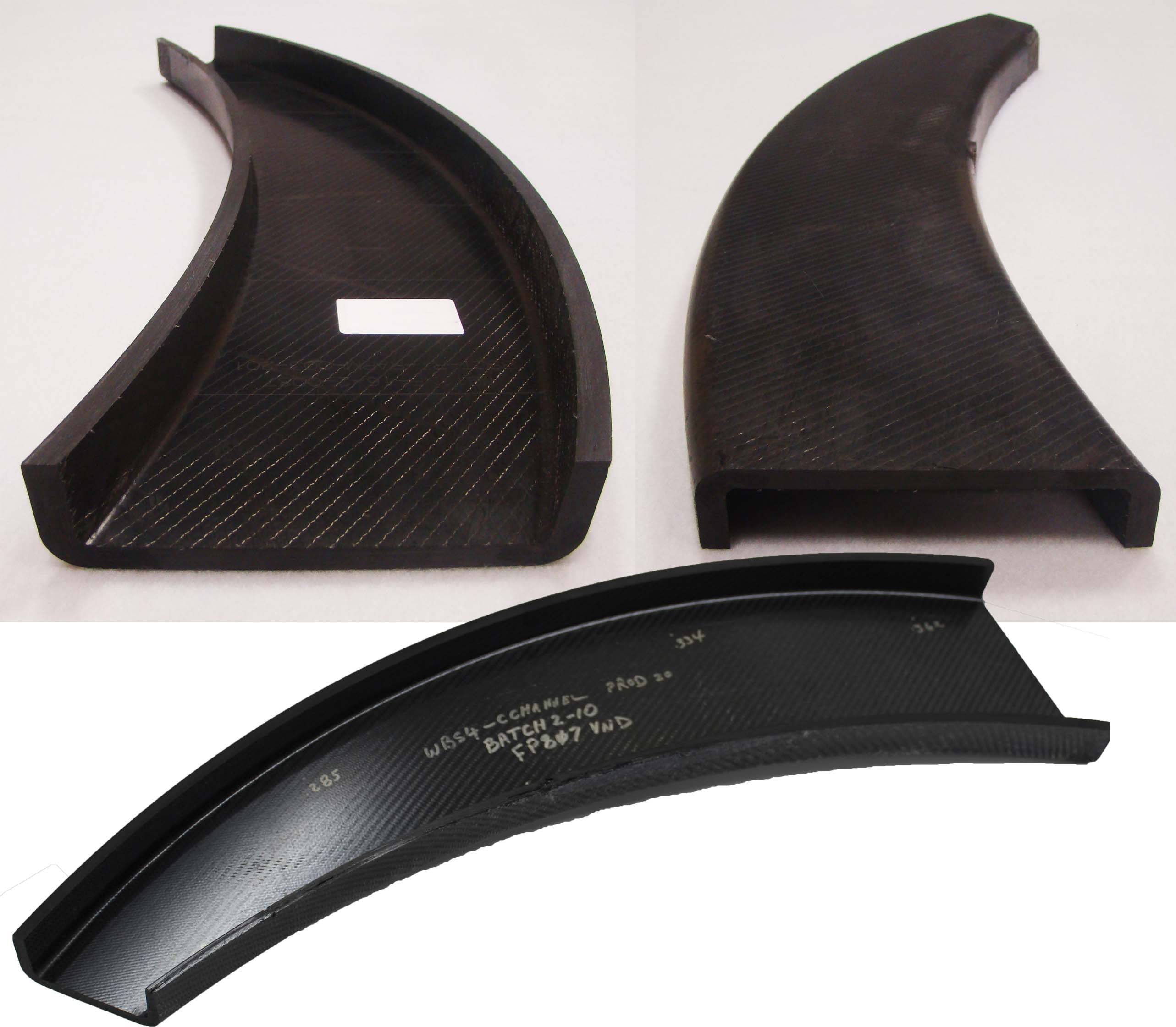
Die Boeing PtFS-Zelle hat eine maximale Temperatur von 440 °C. Als Boeing anfangs mehrere Hochtemperaturzyklen an einem Tag verarbeitete, gab es Bedenken, dass bestimmte Komponenten aufgrund mangelnder Kühlung zwischen den Verarbeitungszyklen beschädigt werden könnten. Das Kühlsystem wurde jedoch im September-Oktober 2019 aufgerüstet, einschließlich zusätzlicher Lüfterkapazität zur Wärmeabfuhr. Mit dieser verbesserten Kühlung kann die Zelle kontinuierlich bei 440 °C verarbeitet werden.
Unter Verwendung eines großen Volumens an Druckluft bei Umgebungstemperatur als Kühlmethode war die Abkühlung der Werkzeugstirnfläche am oberen Ende des Temperaturbereichs schnell, verlangsamte sich jedoch deutlich, als sie 60 °C (140 °F) erreichte. Während des Erhitzens auf thermoplastische Temperaturen (> 350 °C) stieg die Werkzeugstirnflächentemperatur mit einer durchschnittlichen Geschwindigkeit von 41 °C/min (74 °F/min) an. Während des Abkühlens desselben Durchlaufs betrug die durchschnittliche Spitzenkühlrate 36°C/min (65°F/min). Die Verwendung von Druckluft zum Kühlen sorgte für eine kontinuierlichere Kühlrampe und in Kombination mit aktivem Thermomanagement (d. h. Heizen bei Bedarf) blieb die Temperatur während des Abkühlens relativ linear.
Isothermes TS-Prepreg-Stanzen
Die ersten Teilversuche mit der PtFS-Arbeitszelle waren für TS-RAPM-001 gesickte Zugangsabdeckungsplatten, die mit duroplastischem Prepreg-Formpressen (Stanzen) hergestellt wurden. Das Werkzeug für diesen Teil belegt 112 der 180 Kanäle in der RAPM PtFS-Arbeitszelle. Dazu gehören 56 Kanäle auf der oberen Werkzeugfläche und 56 Kanäle auf der unteren Werkzeugfläche. Der eigentliche Teil deckt jedoch nicht das gesamte Werkzeug ab – sondern nur 30 dieser 56 Kanäle für jede Werkzeugfläche, oben und unten. Die Abbildung unten zeigt die Platzierung der 78 Thermoelemente (TCs), die für RAPM-001-Teile verwendet werden – 39 für die Oberseite und 39 für die Unterseite mit derselben Platzierung für beide. Die Anzahl der TCs umfasst einen pro Zelle (Heizungskanal) plus zusätzliche TCs in heißen und kalten Regionen, die in der CFD-Thermoanalyse identifiziert wurden.
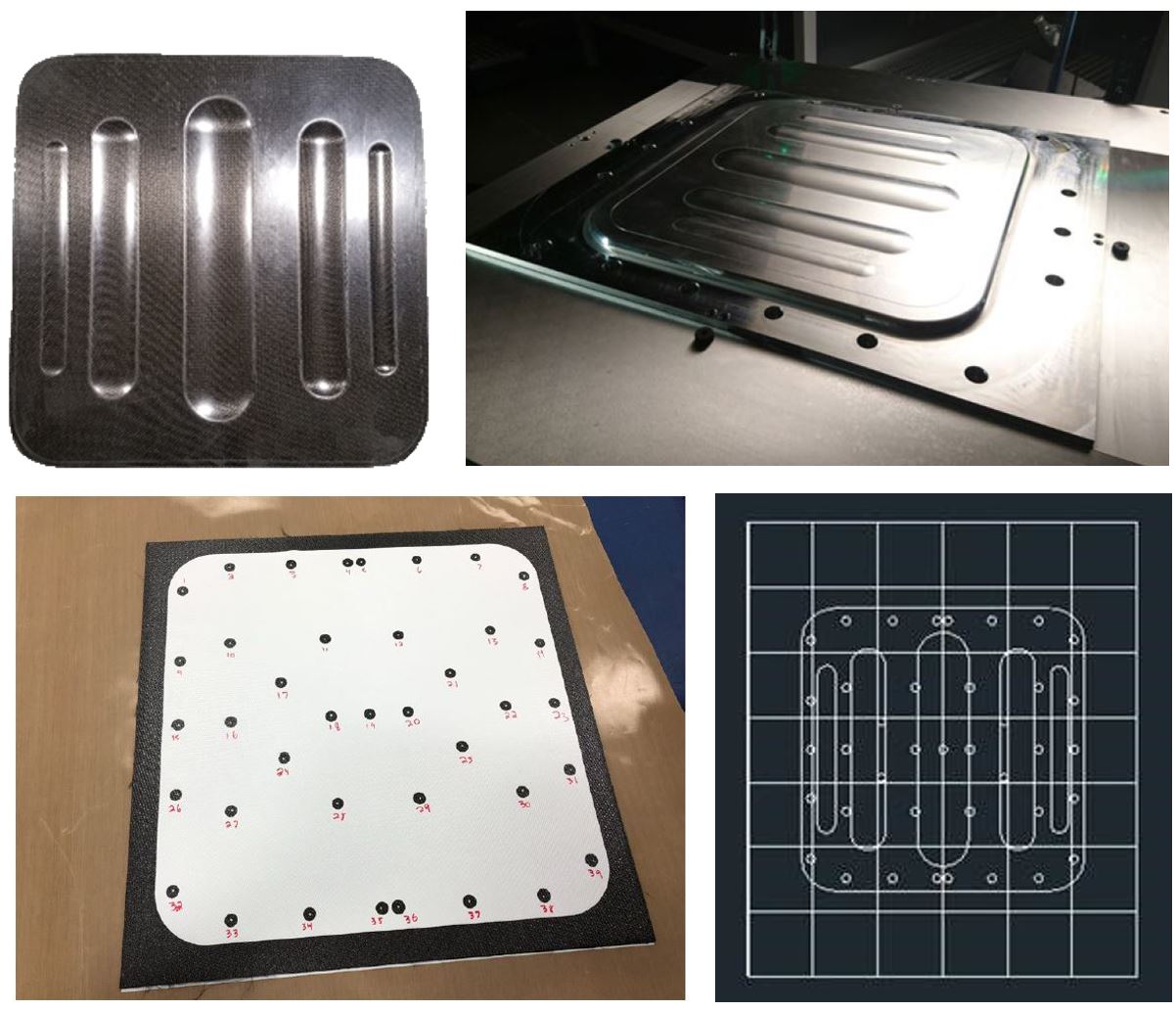
Die leere Werkzeugstirnseite wurde auf Temperaturgleichmäßigkeit getestet und der Test wurde dann nach dem Einbetten von Thermoelementen in der Mitte eines 16-lagigen Kohlefasergewebe/Epoxid-Laminats wiederholt. Sobald Verbundmaterial hinzugefügt wird, wird die Temperaturverteilung der Werkzeugstirnseite enger, da das Verbundmaterial als Wärmeübertragungspfad fungiert. Außerdem war die Temperaturgleichmäßigkeit innerhalb des Verbundlaminats enger als die Messwerte der Werkzeugstirnfläche. Der einzelne TC in Run 1 (siehe die Abbildungen unten, oben in der Tabelle rechts) die über dem gewünschten Temperaturbereich oszillierte, war in der Nähe der Teilekante und wurde vermutlich durch Temperaturschwankungen benachbarter Zellen außerhalb der Teilebeschnittlinie verursacht.
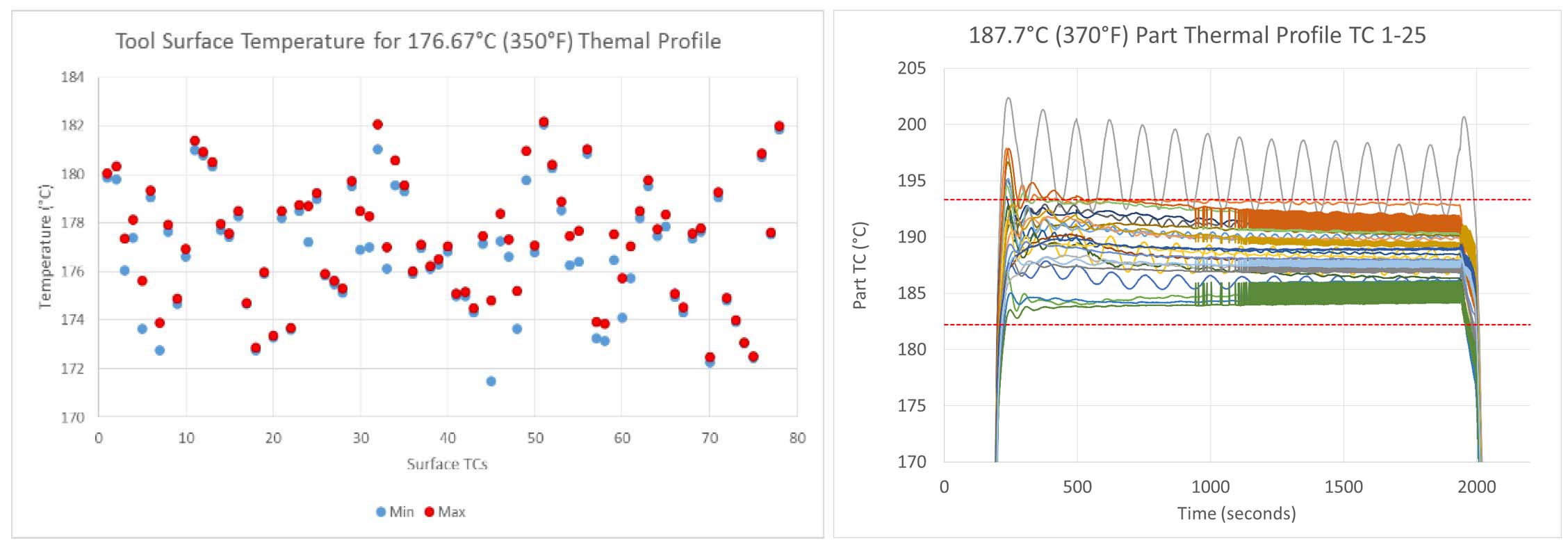
Das isotherme Formpressen der Verarbeitung hielt das Werkzeug bei 176,7 °C (350 °F) innerhalb der Toleranz von ±5,5 °C (±10 °F). Für TS-RAPM-001 wurde die folgende Reihenfolge befolgt:
- System heizt auf 187,7 °C in App. 8 Minuten
- Composite-Rohling in heißes Werkzeug geladen
- Tool geschlossen um 12:09 (zum Beispiel)
- 30 Minuten Zeit, um das Komposit zu gelieren
- Erste Druckstufe:anfängliche schnelle Erwärmung des Rohlings bei gleichzeitiger Minimierung des Harzauspressens
- Zweite Druckstufe:Rampe auf 300 psi, um eine gute Konsolidierung zu gewährleisten und das Wachstum von Hohlräumen zu verhindern
- Entfernen Sie das „grüne“ Komposit aus dem heißen Werkzeug zum Nachhärten
Mit diesem Prozess wurden qualitativ hochwertige Teile erzielt und Teile mit geringerer Zykluszeit als aktuelle Verbundwerkstoffprozesse gezeigt. Eine höhere Prozesstemperatur könnte den Verbundstoff noch schneller gelieren, kann aber auch Materialabbau und das Risiko einer Exothermie verursachen. Dies war ein Problem, da PtFS-Werkzeuge keine herkömmliche große thermische Masse verwenden, um Exothermie zu absorbieren, sondern sich stattdessen auf die aktive Kühlung der Rückseite von Werkzeugen mit geringer thermischer Masse verlassen, um Exothermie abzuleiten.
Die PtFS-Zelle wurde auch verwendet, um TS-RAPM-012 „Wellen“-Herausforderungsteile herzustellen. Unter Verwendung früherer Entwicklungsversuche wurde festgestellt, dass diese Teile unter Verwendung eines 30-minütigen isothermischen Zyklus bei 177 °C gefolgt von einer 2-stündigen Nachhärtung bei der gleichen Temperatur gehärtet werden. Zu den Unterschieden zu früheren Versuchen gehörten jedoch eine aggressivere Geometrie und ein quasi-isotropes Lay-up mit CYCOM 5320-1 Epoxid – Standard für Autoklaven-Luft- und Raumfahrtteile – kombiniert mit 8-Harness-Satin- und unidirektionalen Kohlefaserschichten und einer Außenlage aus Glasgewebe Style 108 auf einer Seite. Der RAPM PtFS-Controller wurde so programmiert, dass er einen minimalen Druck auf das Laminat ausübt, bis eine geeignete Viskosität erreicht wurde. Nach diesem ersten Schritt wurde ein Enddruck aufgebracht, um die Härtung abzuschließen. Ein Versuch wurde in einem Ofen nachgehärtet, während der Rest in der PtFS-Spannvorrichtung nachgehärtet wurde, um die Zeit zwischen den Versuchen zu verkürzen. Es wurden mehrere hochwertige Teile hergestellt.
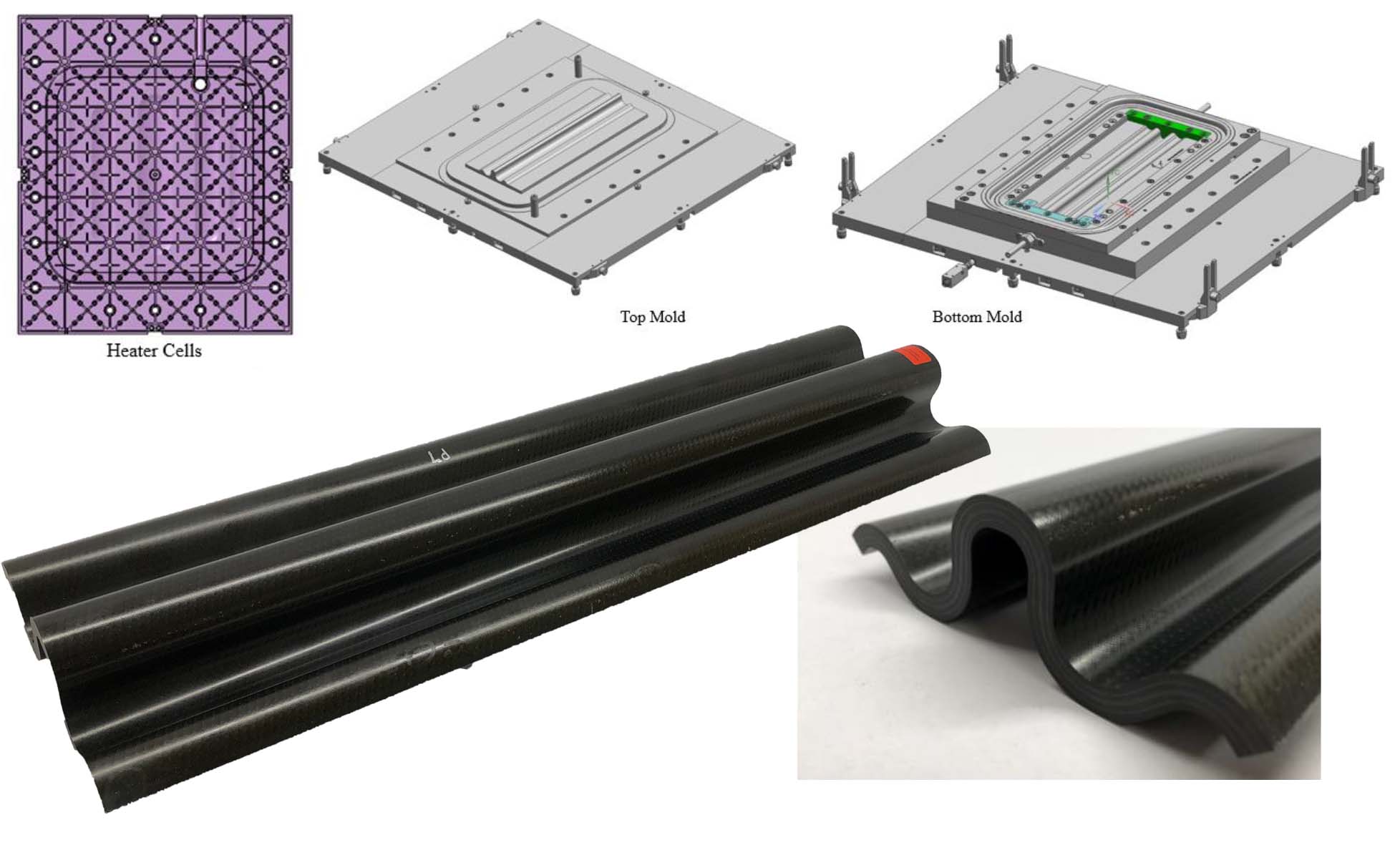
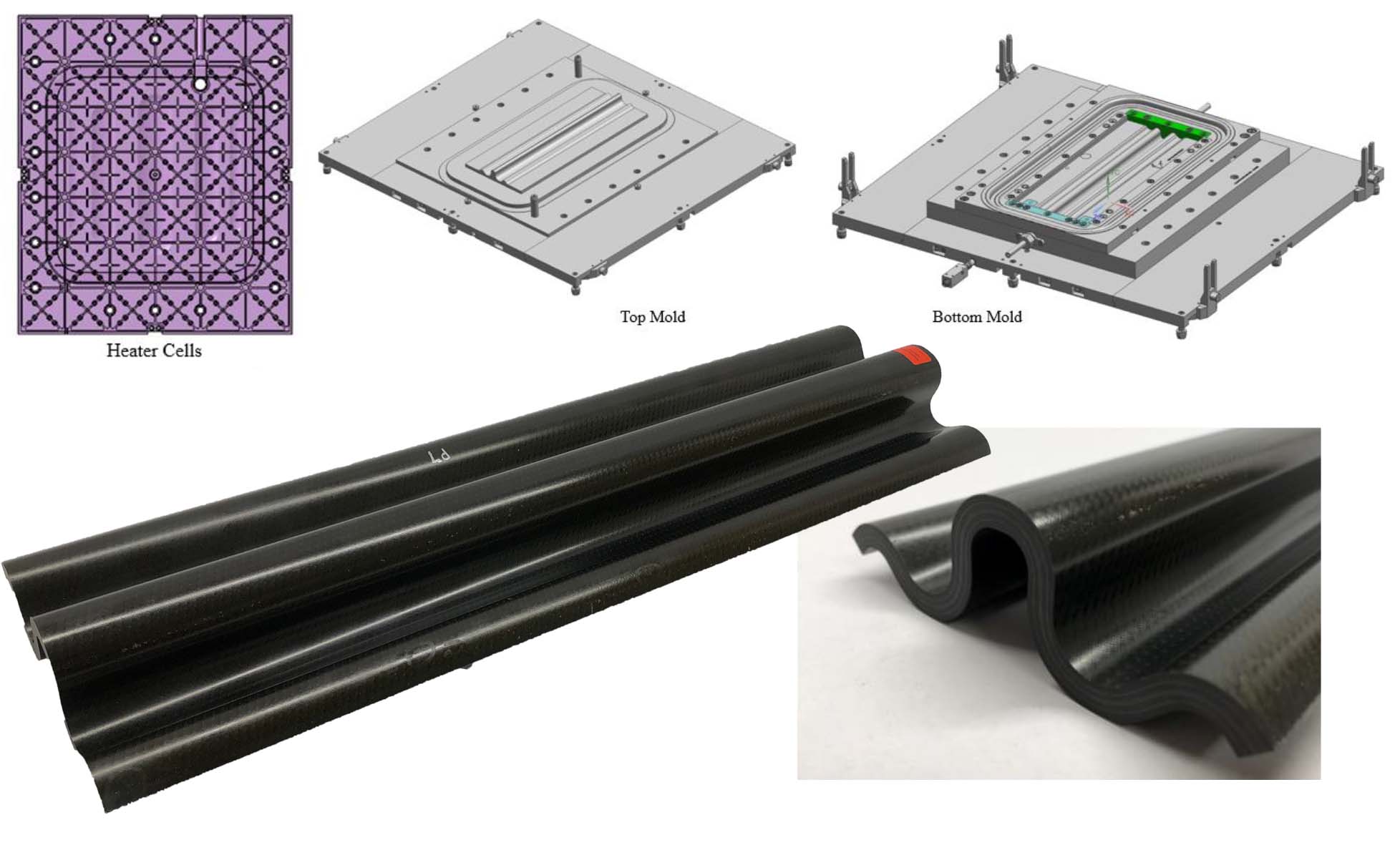
Dynamische Temperaturzyklen für die Harzinfusion
Die Versuche mit Harzinfusionsteilen unter Verwendung der PtFS-Arbeitszelle begannen mit dem gebogenen C-Kanal-Teil RI-RAPM-003. Zunächst wurden drei verschiedene Epoxidharzsysteme getestet:
- Solvay CYCOM 823, bei 80 °C infundiert und dann auf 125 °C erhitzt
- Huntsman FAF2 (Schnellhärtungssystem) infundiert bei 100°C mit 150°C Verweildauer
- Angewandte Polemik (jetzt von Kaneka erworben) API DD3-84 (ebenfalls ein Schnellhärtungssystem) infundiert bei 60 °C mit einer Verweiltemperatur von 160 °C.
Der Vorformling aus Non-Crimp-Gewebe wurde infundiert, mit 2 °C/min auf die spezifizierte Verweiltemperatur hochgefahren und dann 60 Minuten vor dem Abkühlen gehalten. Bei den schnellhärtenden Harzen führte das PtFS mit fortschreitender exothermer Reaktion automatisch eine aktive Kühlung in bestimmten Werkzeugbereichen ein, um die festgelegten Teiletemperaturen aufrechtzuerhalten.
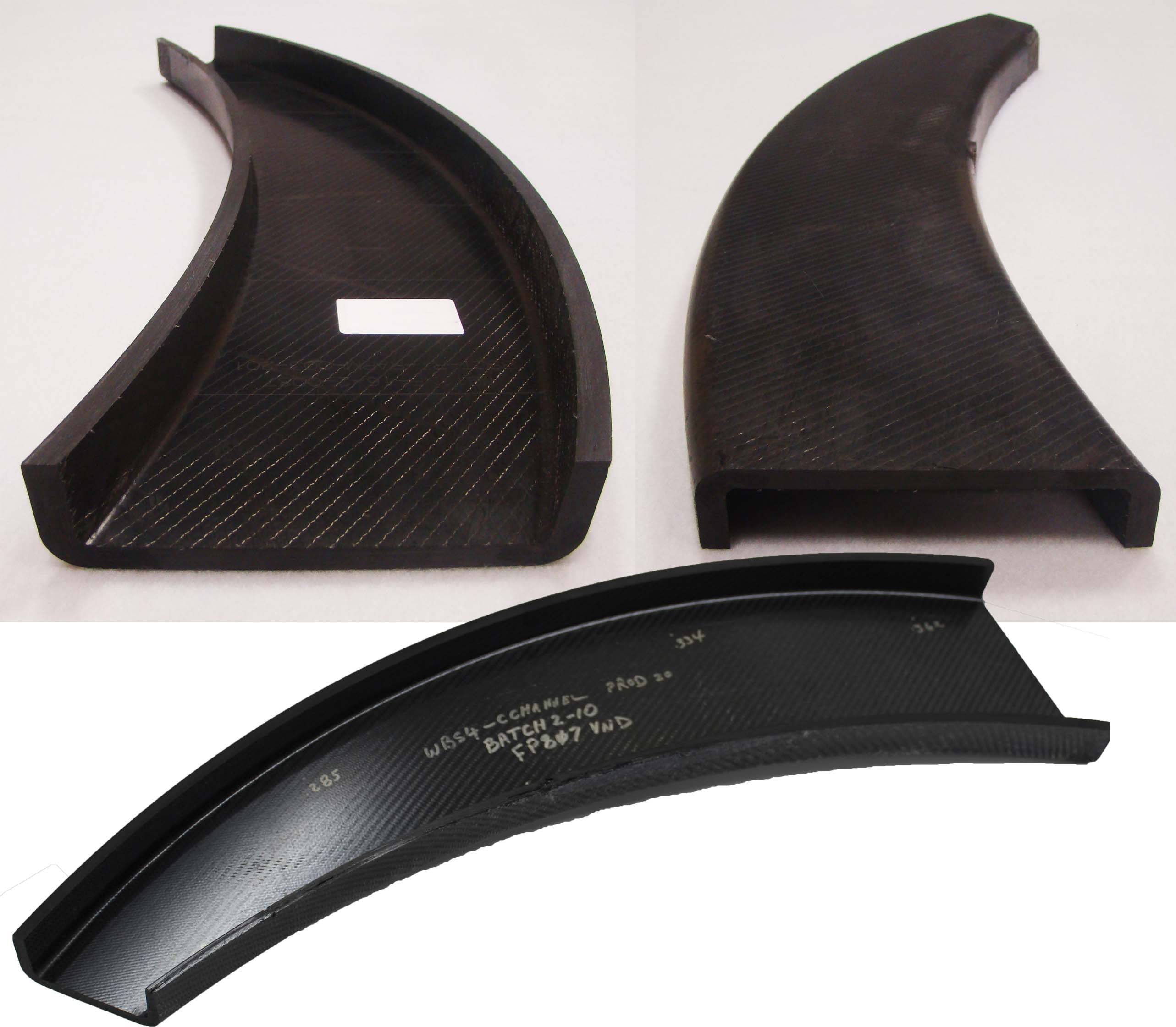
Die PtFS-Ausrüstung war auch in der Lage, die Positionskontrolle zur Unterstützung einer Spaltinfusionsmethode für die RI-RAPM-003-Teile bereitzustellen. Bei diesem Verfahren wurde das Werkzeug bis zu einer Anfangshöhe der Vakuumdichtung geschlossen, so dass das Werkzeug während der Infusion 1,3 Millimeter offen blieb. Nachdem die Infusion abgeschlossen war, wurde das Werkzeug dann die verbleibende Distanz geschlossen, um das Harz in z-Richtung in die Vorform zu treiben. Teile wurden mit diesem Verfahren erfolgreich hergestellt.
Dynamische Temperaturregelung für thermoplastisches Stanzen
Die PtFS-Ausrüstung wurde auch verwendet, um den gebogenen C-Kanal RAPM-003 aus thermoplastischen Verbundwerkstoffen herzustellen. Konkret wurde es verwendet, um einen komplexen Vorformling, der über die Länge des Teils von 32 auf 24 Lagen abfiel, zu einem flachen Rohling mit verjüngtem Querschnitt zu konsolidieren. Die konsolidierten Rohlinge wurden dann an ATC Manufacturing (Post Falls, Idaho, USA) geschickt, die das letzte Teil mit vertikalen Flanschen stanzten.
Das konsolidierte Material für den gebogenen C-Kanal TP-RAPM-003 war ein mit Polyetheretherketon (PEEK) pulverbeschichtetes Kohlefaser-2x2-Köpergewebe. Die PtFS-Arbeitszelle wurde verwendet, um eine AZ31-Magnesiumblase über der thermoplastischen Ladung superplastisch zu formen, die Blase und die Ladung auf eine PEEK-Prozesstemperatur von 400°C in ca. 55 Minuten.
Bei dieser Formungstemperatur wurde Argongas auf die Blase aufgebracht, wodurch ein Verfestigungsdruck auf das thermoplastische Verbundmaterial ausgeübt wurde. Die Zelle kühlte dann die Blase ab und lädt sich in 30 Minuten unter die PEEK-Kristallisationstemperatur auf, was eine Gesamtzykluszeit von 3 Stunden ergibt.
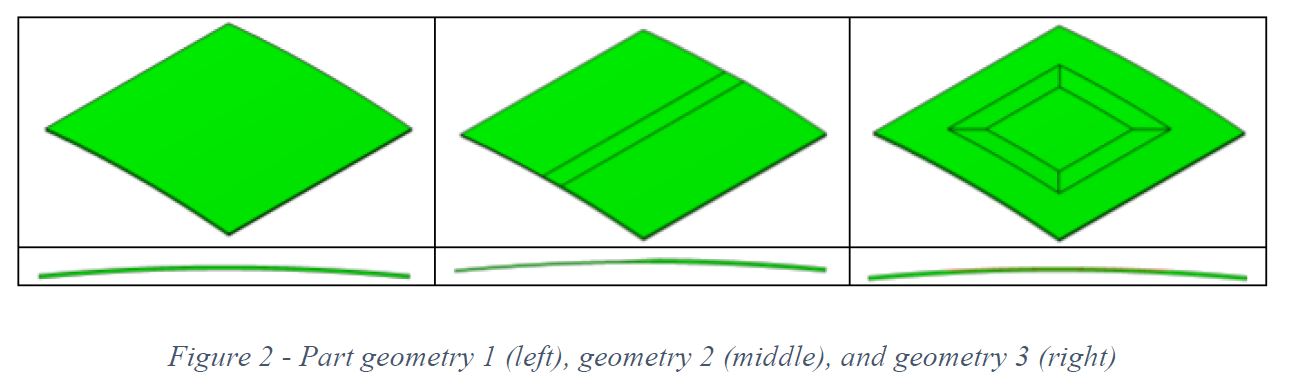
Folie 11 oben zeigt den Verlauf des ausgeübten Drucks während des superplastischen Formens der Blase und der Verfestigung des Thermoplasts – ansteigend von 20 psi auf 140 psi, nachdem die Blase die superplastische Formgebungstemperatur erreicht hatte, die während des Abkühlens aufrechterhalten wurde. Vorformlinge wurden erfolgreich konsolidiert und an ATC Manufacturing gesendet, wo Teile für diese extrem anspruchsvolle Geometrie gestanzt wurden.
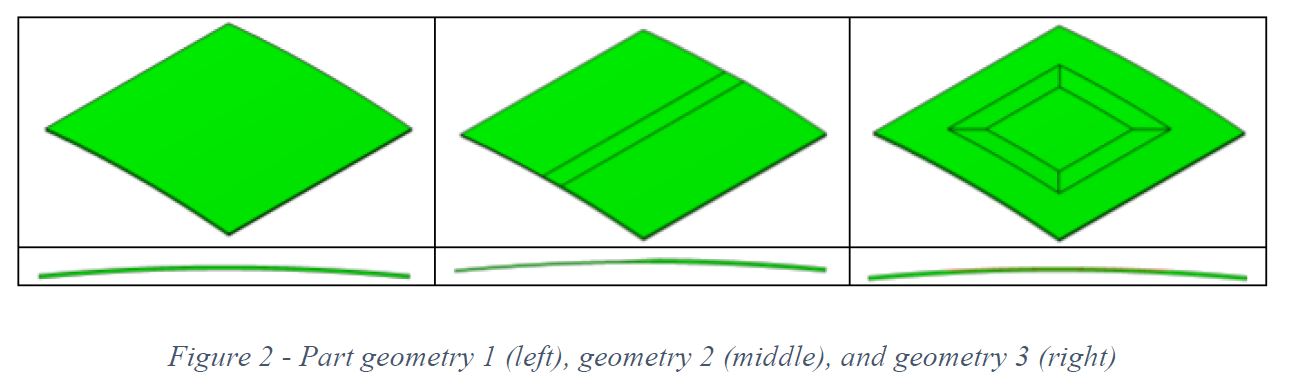
Die PtFS-Zelle wurde auch für das einstufige Stanzen von Rohling zu Teil von TP-RAPM-017-Platten verwendet, die aus einem ausgewogenen und symmetrischen Aufbau von unidirektionalem (UD) Kohlefaser-/Polyetherketonketon (PEKK)-Band hergestellt wurden, um verschiedene Optionen zu untersuchen und Teilemerkmale beeinflussen die Blasenbildung. Die TP-RAPM-017-Platten maßen 40,6 x 40,6 Zentimeter mit einer sanften Kontur, die eine Höhe von 1,3 Zentimeter erreichte. Drei verschiedene Teilegeometrien wurden bewertet – flach (kein Lagenabfall), Lagenabfall in einer Richtung und Bilderrahmen – mit 32 Lagen in dicken Bereichen, 16 Lagen in dünnen Bereichen und einem Lagenabfallverhältnis von 20:1 dazwischen. Die Teilezykluszeit betrug für alle Geometrien 1,5 Stunden.
Die Werkzeugflächen wurden aus Invar 42 bearbeitet, um der Wärmeausdehnung des thermoplastischen UD-Verbundbandes am besten zu entsprechen. UD-Bandlagen-Kits wurden geschnitten und kollationiert, mit Ultraschall zusammengeschweißt und in das Härtungswerkzeug gegeben, wo sie auf 385 ± 15°C erhitzt wurden. Es wurden verschiedene Druckzyklen getestet und das Teil wurde dann auf unter 220 °C abgekühlt, wonach der Druck abgelassen und das Teil entformt wurde.
Ein Beispiel für einen Druckzyklus für Geometrie 1 war 20 psi bei Raumtemperatur, Anstieg auf 140 psi, nachdem das nacheilende Thermoelement eine Schmelztemperatur von 310 °C erreicht hatte und dann mit 10 °C/Minute unter Druck abgekühlt wurde, bis das Thermoelement des Teils unter 220 °C gemessen wurde . Anfangsdrücke von 20 psi, 30 psi, 50 psi und 70 psi wurden getestet. Die Druckrampen wurden auch von 10 psi pro Minute bis 10 psi pro 15 Sekunden bis zum maximalen Druck von 140 psi variiert.
Ein bemerkenswertes Ergebnis war, dass alle Platten schlechte C-Scan-Ergebnisse zeigten, wenn die Lagen ultraschall-heftgeschweißt wurden. Um beste Ergebnisse zu erzielen, sollten sich solche Heftschweißungen daher außerhalb der Teilnetzbesatzlinie befinden. Annehmbare Teile wurden hergestellt, aber einige Teile zeigten eine schlechte Verfestigung an den Kanten der Lagen. Dies wurde durch Erhöhen des anfänglichen Verdichtungsdrucks auf 30 psi vor dem Aufheizen behoben. Dieser Druckanstieg verursachte jedoch eine gewisse Oberflächenrauhigkeit/matte Oberfläche auf der Blasenseite des Teils. Außerdem zeigten einige Platten der Geometrie 2, die unter Verwendung des anfänglichen Verdichtungsdrucks von 50 und 70 psi hergestellt wurden, Falten in der Mitte der Teile. Es wurde angenommen, dass diese höheren Drücke möglicherweise verhindert haben, dass die Lagen während der Verarbeitung aneinander vorbeigleiten, wodurch die Falten in den Teilen eingeschlossen werden.
Eine andere ausprobierte Variante bestand darin, Argongas durch billigeres Stickstoffgas zu ersetzen, um die Blase unter Druck zu setzen, aber dies verringerte auch die Teilequalität, einschließlich der Oberflächenrauheit/matter Oberfläche, was zu höheren Dämpfungsgraden in den C-Scan-Ergebnissen führte, obwohl keine Porosität im Querformat gefunden wurde. Abschnitte.
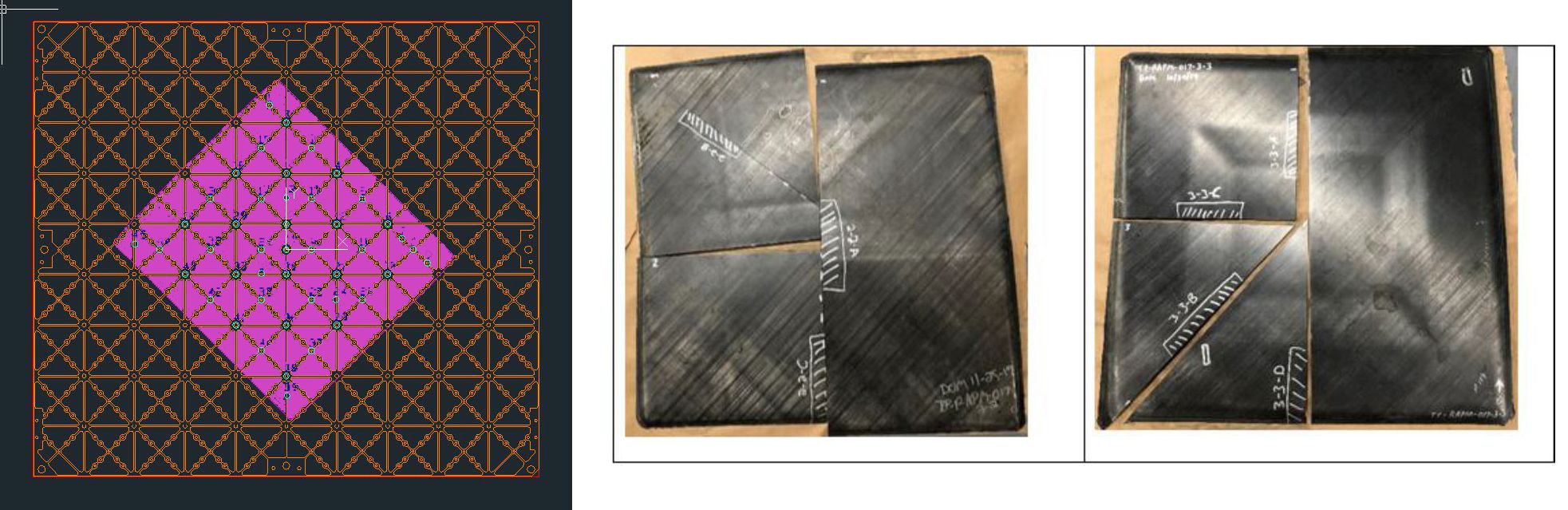
Vor- und Nachteile von PtFS in RAPM
Die PtFS-Arbeitszelle zeigte eine schnelle Erwärmung (<10 Minuten für die Epoxidhärtung bei ≈180 °C). In Kombination mit automatisierten Werkzeugwechseln könnte dies schnelle Teilewechsel ermöglichen und die Kosten von Verbundteilen für kleine Fertigungsserien senken. PtFS eignet sich auch gut für dynamische Hochtemperaturläufe (im Gegensatz zu isothermen Teilzyklen).
Die Leistungsfähigkeit der Boeing St. Louis PtFS-Zelle wurde während des RAPM-Programms dank verbesserter Software-Upgrades für eine bessere thermische Gleichmäßigkeit und Steuerung der Klemmvorrichtung, verbesserter Kühlleistung und Thermoelementsteuerung sowie eines automatisierten Pressklaven-Drucksteuerungssystems erheblich gesteigert. Eine weitere Leistungssteigerung kann möglich sein, wenn die riesige Menge an Daten verwendet wird, die jede Sekunde vom System generiert und aufgezeichnet wird, einschließlich jedes Heizkanal-Sollwerts, Heizleistungshebel, Druckluftpegel usw. Die Anwendung von maschinellem Lernen auf diese Daten könnte die Teilequalität und Prozessverbesserungen. Weitere Softwareverbesserungen könnten es diesen Daten auch ermöglichen, Verarbeitungsanomalien wie übermäßigen Energiebedarf und geringe Reaktionsfähigkeit bestimmter Werkzeugpositionen zu identifizieren.
„PtFS bietet viele Anpassungsmöglichkeiten, wie der Name schon sagt:Production to Functional Specification“, sagt Hahn. Die meisten der maschinell bearbeiteten Werkzeugflächenkonstruktionen aus Metall für RAPM wurden von Surface Generation in Großbritannien hergestellt durch andere Quellen als Surface Generation. Diese Werkzeugformfläche, CMD-TP-RAPM-008-503, wurde erfolgreich zur Herstellung von TP-RAPM-008-203 Kurzfaserzugangsplatten verwendet.
„Während irgendeine Form der Temperaturkontrolle im Werkzeug und/oder Teil bei allen Formteilen aus Verbundwerkstoffen hilft“, erklärt Hahn, „ist eigentlich eine Temperaturkontrolle in kritischen Bereichen und zu kritischen Zeiten erforderlich, die je nach Teil und Prozess unterschiedlich ist. Daher ist es von entscheidender Bedeutung, die Temperatursteuerung zu verstehen, die tatsächlich erforderlich ist, um ein bestimmtes Teil zu formen. Die 180 Zonen in PtFS sind hilfreich, aber auch teuer, da jede einen bearbeiteten Kanal im Werkzeug erfordert. Benötigt das Teil nur eine Außen- und Innenzone oder eine spezielle Zone entlang einer Triggerpunkt-Geometrie, kann eine andere Lösung günstiger sein. Dies eröffnet jedoch die Debatte darüber, was der beste Ansatz ist, um eine Fertigungszelle für Verbundwerkstoffteile zu entwickeln, die über mehrere Arten von Prozessen und Teilen hinweg flexibel ist.“
Boeing und DARPA werden diese Debatte weiter mit Informationen ergänzen, wenn sie das RAPM-Programm im Jahr 2020 abschließen und weitere Ergebnisse veröffentlichen.
Harz
- Herausforderungen bei der Entwicklung neuer Produkte
- Arithmetik mit wissenschaftlicher Notation
- Fragen und Antworten mit einem Industrie-4.0-Lösungsarchitekten
- Boeing arbeitet mit Microsoft zusammen, um Aviation Analytics voranzubringen
- Die Entwicklung moderner Kunststoffe
- Solvay arbeitet mit Boeing für Coronavirus-Gesichtsschutz zusammen
- SABIC arbeitet mit NUDEC zusammen, um erneuerbare PCs auf den Markt zu bringen
- 3D-Druckverbundwerkstoffe mit Endlosfasern
- Projekte mit Outsourcing auf den Weg bringen
- Boeing bestätigt Vereinbarung mit Mentor Graphics von Siemens