Experteninterview:Carbons Mitbegründer Philip DeSimone über den Übergang zur Großserienproduktion mit 3D-Druck
Carbon hat seit seiner Gründung im Jahr 2013 einen kometenhaften Aufstieg erlebt. In den letzten sechs Jahren wurde die firmeneigene Digital Light Synthesis™ (DLS)-Technologie von Kunden aus einer Reihe von Branchen übernommen, von der Luft- und Raumfahrt über die Automobilindustrie bis hin zum Verbraucher Waren und Medizin. Schneller Vorlauf ins Jahr 2019, wo das von Risikokapital unterstützte Unternehmen mit Sitz im Silicon Valley nun einer von nur drei 3D-Druckerherstellern ist, die eine Bewertung von über 1,7 Milliarden US-Dollar erreicht haben.
Carbon hat mit seiner Technologie große Pläne, die Art und Weise, wie Polymerteile hergestellt werden, zu verändern. Und mit hochkarätigen Kunden auf seiner Liste, darunter adidas, Ford Motor Company und Lamborghini, ist das Unternehmen bereit, seine Vision zu verwirklichen.
Wir konnten mit Philip DeSimone, dem Mitbegründer und VP of Business Development von Carbon, sprechen, um mehr über die Technologie, Wachstumsstrategie und Mission des Unternehmens zu erfahren.
Die Herstellung von Polymerteilen neu erfinden
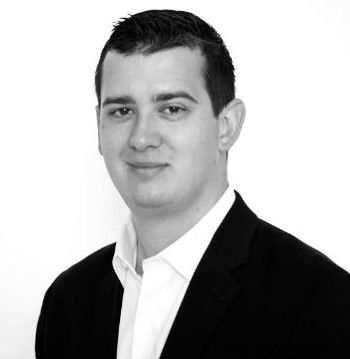
Für DeSimone ist die Mission von Carbon klar. „Unser Ziel ist es, die Art und Weise, wie Polymerprodukte entworfen, konstruiert, hergestellt und geliefert werden, neu zu erfinden“, sagt er. „Unsere proprietäre Digital Light Synthesis-Technologie ist dabei ein wesentlicher Bestandteil.“
Digital Light Synthesis, kurz DLS, ist ein Kernelement des Leistungsversprechens von Carbon. Die Technologie wurde erstmals im Jahr 2015 bei einem TED-Vortrag des Mitbegründers und CEO des Unternehmens, Dr. Joseph DeSimone, öffentlich vorgestellt. Ein wesentlicher Grundsatz des Gesprächs war damals die Geschwindigkeitsverbesserung durch die neue Technologie.
Wie genau funktioniert der DLS-Prozess?
Kurz gesagt ist DLS eine 3D-Drucktechnologie, die Licht und Sauerstoff miteinander verschmilzt, um Teile aus einem Pool programmierbarer flüssiger Harze herzustellen.
Das photochemische Druckverfahren funktioniert, indem Licht durch eine sauerstoffdurchlässige Membran in einen Bottich aus UV-härtbarem Flüssigharz projiziert wird. Ein programmiertes thermisches Härtungsbad oder -ofen wird dann verwendet, um die mechanischen Eigenschaften des Teils einzustellen, um es zu verstärken.
Für Kunden bietet die Technologie eine Reihe von Vorteilen, insbesondere die Möglichkeit des 3D-Drucks langlebige Hochleistungsteile mit hervorragender Oberflächengüte und isotropen mechanischen Eigenschaften – und das alles zu geringeren Kosten als bei herkömmlichen Herstellungsverfahren.
Natürlich ist die steigende Nachfrage nach 3D-Druck nur einer der wichtigsten Indikatoren für die zunehmende Digitalisierung der Fertigung. Für DeSimone sind die Vorteile davon unbestreitbar.
„Wenn ein Unternehmen erst einmal digitalisiert ist, kann es nie mehr zurück“, sagt er fest.
„Der 3D-Druck ermöglicht es Herstellern, neue Geschäftsmöglichkeiten wie Massenanpassung, On-Demand-Inventar und zuvor unmögliche Produktdesigns zu erschließen. Es verändert grundlegend, wie Designer und Ingenieure denken, wie Menschen zusammenarbeiten und arbeiten, und beseitigt herkömmliche Beschränkungen.“
Vom Prototyping zur Massenproduktion
Die Verlagerung des Gesprächs vom Rapid Prototyping zur Produktion war in den letzten Jahren ein wichtiges Vorrecht der additiven Fertigungsindustrie.
Da Unternehmen 3D-Drucktechnologien in ihre Produktionsabläufe integrieren möchten, stehen Hardwarehersteller vor der Aufgabe der Entwicklung von Maschinen, die eine verbesserte Geschwindigkeit und größere Teilegenauigkeit bieten.
Carbon erweist sich für manche bereits als Vorreiter in dieser Hinsicht. Erst letzten Monat stellte das Unternehmen seinen neuen L1-Drucker vor, die erste Maschine des Unternehmens seit seinem M2-Drucker, der 2017 auf den Markt kam.
Als „End-to-End-Fertigungslösung“ in Rechnung gestellt, wurde der L1 mit Blick auf die Massenfertigung entwickelt (beachten Sie, dass das „L“ für „groß“ steht). Sie bietet eine fünfmal so große Baufläche wie ihr Vorgänger und ist auf die Produktion mehrerer Teile in einem Durchgang ausgerichtet.
Der Gerätehersteller Riddell wurde als einer der ersten Benutzer der Maschine angekündigt. Das Unternehmen hat bereits damit begonnen, den L1 für seine Diamond-Helmplattform zu verwenden: maßgeschneiderte, 3D-gedruckte Helmeinlagen für NFL-Spieler.
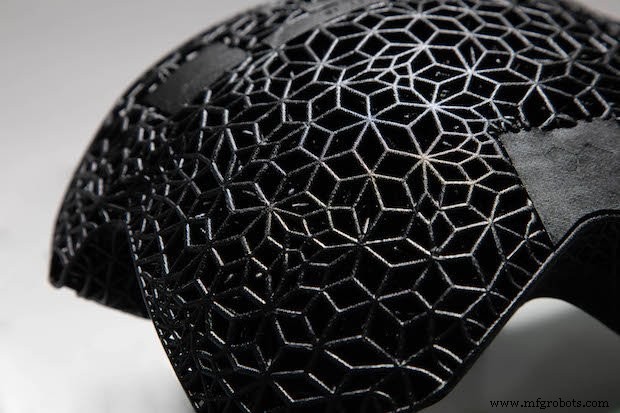
Die Helmauskleidungen wurden aus einem speziellen, hochdämpfenden Elastomer von Carbon in Form einer Gitterstruktur gedruckt und wurden entwickelt, um die stärksten Stöße zu absorbieren und gleichzeitig Komfort und eine individuelle Passform zu bieten. Durch das kundenspezifische Element können die Designs an die Abmessungen eines Spielers angepasst werden.
Aber vielleicht ist es Carbon hoch beachteten Partnerschaft mit adidas, das wirklich dem Unternehmen hochvolumigen Ambitionen zum Tragen Herstellung bringen wird.
Mit Blick auf eine Zwischensohle zu entwickeln, die das erfüllen könnten Leistungsanforderungen von Spitzensportlern benötigte adidas ein Mittel zur Herstellung von Zwischensohlen, das die Anforderungen in Bezug auf Komfort, Dämpfung und Bewegung erfüllt. Der 3D-Druck – und genauer gesagt die DLS-Technologie von Carbon – erwies sich als die ideale Lösung.
Seit der Ankündigung von Plänen zum 3D-Druck von Zwischensohlen für die Futurecraft 4D-Sneaker von adidas haben sich die Unternehmen verpflichtet, im Jahr 2019 100.000 Paar Schuhe zu produzieren Einheiten in den nächsten zwei Jahren. Über die Zusammenarbeit sagt er:„Diese Massenproduktion wird durch unseren L1-Drucker ermöglicht, der für die Produktion hochspezialisierter Produkte in großem Maßstab ausgelegt ist.“
In der Tat ist dieser Produktionsanstieg ein Hinweis auf den breiteren Fokus der Branche auf den 3D-Druck für die Massenfertigung.
„Bei Carbon haben wir reine Drucker, Materialien, Software und die Designtools entwickelt, die für die Bereitstellung einer vollständigen Fertigungsanlagenlösung erforderlich sind. All diese Dinge werden benötigt, um die Kluft zwischen Prototyping und Produktion zu überwinden.“
Wachstumsstrategie von Carbon
Tauchen Sie weiter in das Wachstum von Carbon ein und die Bedeutung seiner Partnerschaften wird deutlich.
In den letzten Jahren hat das Unternehmen eine Reihe hochkarätiger Kooperationen angekündigt, die insbesondere nicht auf einen Sektor oder eine Branche beschränkt sind.
Was ist Carbons Ansatz für Partnerschaften und welche Rolle spielen sie in der Wachstumsstrategie des Unternehmens?
„Partnerschaften sind entscheidend für unseren Erfolg und in jedem Aspekt unseres Geschäfts wichtig “, sagt DeSimone auf Nachfrage. „Jedes Mal, wenn wir einen Abonnementvertrag mit einem Kunden unterzeichnen, gehen wir eine Partnerschaft mit diesem Unternehmen für die Dauer der Vereinbarung ein. Carbon ermöglicht es den Kunden, in noch nie dagewesenem Maßstab zu produzieren, und dies ist nur dann erfolgreich, wenn wir Tag für Tag Seite an Seite daran arbeiten, es Wirklichkeit werden zu lassen.“
Nehmen Sie als Beispiel die jüngste Partnerschaft mit der Ford Motor Company im vergangenen Januar. Beim Additive Manufacturing for Automotive Workshop auf der North American International Auto Show 2019 in Detroit präsentierten die beiden Unternehmen eine Reihe von Automobilteilen, die im 3D-Druck hergestellt wurden. Dazu gehörten Hebelarm-Serviceteile für Heizung, Lüftung und Kühlung (HVAC) für den Ford Focus, Ford F-150 Raptor-Zusatzstecker und Ford Mustang GT500 elektrische Feststellbremshalterungen.
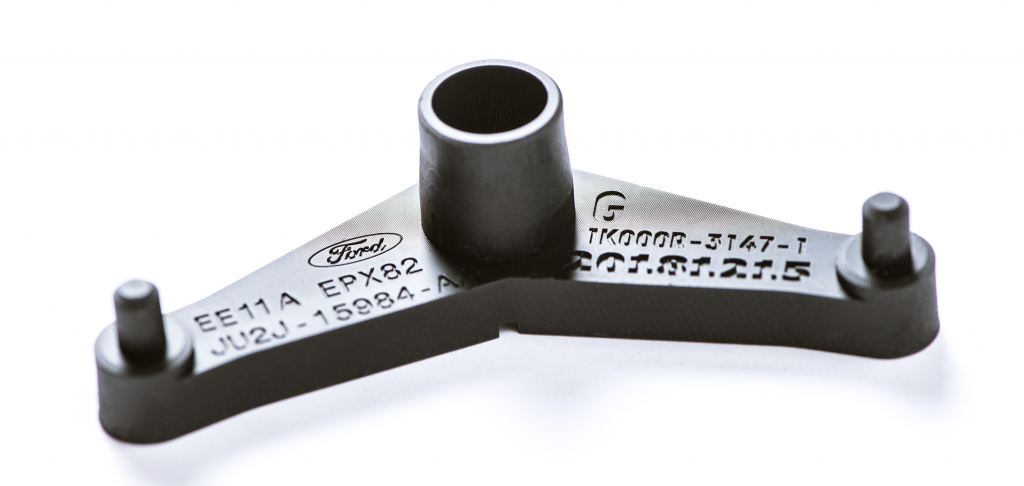
Für Carbon stellt dieser Meilenstein einen weiteren Schritt in Richtung seines Ziels dar, Teile in technischer Qualität bereitzustellen, die in industriellen Endteilanwendungen verwendet werden können. Es weist auch auf das nachhaltige Potenzial des 3D-Drucks für die Automobilbranche hin.
"Wir glauben, dass Carbon eine große Chance bietet, mit Autoherstellern zusammenzuarbeiten, um leichtere Autos und Lagerbestände nach Bedarf herzustellen", sagt DeSimone. „Mit Ford konnten wir bereits eine 60-prozentige Gewichtsreduzierung für die Halterungen der elektrischen Ford Mustang GT500-Feststellbremse, eine 50-prozentige Reduzierung der Vorlaufzeit und eine 90-prozentige Reduzierung der Kosten für den Ford Focus HVAC-Hebelarm erzielen. ”
Natürlich sind Partnerschaften nicht der einzige Erfolgsfaktor von Carbon – auch die Produktpositionierung und die Erfüllung der Marktnachfrage sind entscheidend, wie DeSimone betont. „Ich denke, das zugrunde liegende Prinzip unseres Erfolgs ist, dass wir uns als ‚wahres Lösungsunternehmen‘ positioniert und mit Partnern zusammenarbeiten.“
Materialentwicklung
Neben den Hardware-Entwicklungen hat Carbon auch die Materialentwicklung im Blick.
Mit dem, was DeSimone als "mehrgleisigen Ansatz" für Materialien bezeichnet, lädt Carbon sowohl zur Entwicklung und Validierung durch Dritte als auch zur internen Materialentwicklung ein.
„Wir glauben, dass es an uns liegt, wenn ein Dritter ein differenziertes Material erstellt, es für die Plattform zu validieren und es den Kunden in unserem Resin Store anzubieten“, erklärt DeSimone. „Wir haben auch ein Team bei Carbon, das Materialien entwickelt, die noch niemand im 3D-Druck gesehen hat. Diese Materialien tragen dazu bei, Unternehmen neue Möglichkeiten zu eröffnen, bisher nicht herstellbare Produkte herzustellen, wie die Futurecraft 4D-Zwischensohle für adidas.“
Natürlich hat der Fokus auf Materialien strategische Auswirkungen, die es Carbon ermöglichen, entwickeln spezialisierte Materialien, die auf die Bedürfnisse verschiedener Branchen zugeschnitten sind.
Wie Automobil. In der Zusammenarbeit mit Ford wurde das Material Epoxy (EPX) 82 verwendet. Das hochfeste Harz ist ein starker Kandidat für Produktionsanwendungen mit Eigenschaften wie Haltbarkeit, geringes Gewicht, Hochtemperaturbeständigkeit und Beständigkeit gegen hohe Drücke.
Die medizinische Industrie ist ein weiterer Bereich, den Carbon für die Materialentwicklung ins Visier genommen hat. Im September 2018 kündigte Carbon das erste medizinische Material für seine DLS-Technologie an:Medical Polyurethane 100 (MPU 100), das entwickelt wurde, um die Qualität von Medizinprodukten zu verbessern und die Produktentwicklungszeiten zu beschleunigen.
Das weiße Polymerharz weist eine Reihe mechanischer Eigenschaften auf, darunter hohe Festigkeit, Abriebfestigkeit, Biokompatibilität und Sterilisierbarkeit. Die Kombination dieser Eigenschaften macht MPU 100 ideal für medizinische Einwegprodukte, chirurgische Werkzeuggriffe und Prothetik – um nur einige Anwendungen zu nennen.
Nach vorne schauen
Wie werden die nächsten fünf, zehn Jahre für die additive Fertigungsindustrie aussehen? DeSimone gab seine Gedanken.
Eine zentrale Herausforderung wird es sein, den 3D-Druck über die reine Prototypenindustrie und Ausbildung hinaus zu entwickeln, um das volle Potenzial von 3D-Drucktechnologien auszuschöpfen“, sagt er.
Dennoch setzt sich DeSimone für die Zukunftschancen der Technologie ein.
„Ich glaube wirklich, dass Sie die Auswirkungen der digitalen Fertigung als Lösung für die Serienfertigung sehen werden. Die digitale Fertigung bietet eine enorme Chance, den 300-Milliarden-Dollar-Markt für Polymerspritzguss zu erobern. Carbon wird seine Rolle spielen, um zu zeigen, was möglich ist, wenn man Innovationen bei Software, Hardware und Materialien kombiniert, um das Unmachbare zu machen.“
Was kommt als nächstes für Carbon? „Wir konzentrieren uns auf Wachstum und den Aufbau eines erfolgreichen Unternehmens“, sagt DeSimone. „Wir haben 2018 ein dreistelliges Wachstum verzeichnet und sind 2019 wieder auf Kurs für ein dreistelliges Wachstum. Wir haben auch weitere spannende Partnerschaften und Anwendungen in Arbeit, auf die wir uns sehr freuen.“
Um mehr über Kohlenstoff zu erfahren, besuchen Sie: https://www.carbon3d.com/
———————————-
Experteninterviews
Die Showcases der AMFG Experteninterviews innovative Unternehmen und Einzelpersonen, die die Zukunft der additiven Fertigung mitgestalten. Weitere Informationen zur Teilnahme an der Serie erhalten Sie unter [email protected].
3d Drucken
- Interview mit einem Experten:Professor Neil Hopkinson, Direktor für 3D-Druck bei Xaar
- Interview mit einem Experten:Philip Cotton, Gründer von 3Dfilemarket.com
- Interview mit einem Experten:Spencer Wright von pencerw.com und nTopology
- Interview mit einem Experten:Dr. Alvaro Goyanes von FabRx
- Interview mit einem Experten:Dr. Bastian Rapp von NeptunLab
- 3D-Druck mit Silikon – kommt die Zeit?
- Interview mit einem Experten:Ibraheem Khadar von Markforged
- Motorsport, Performance Racing und 3D-Druck:ein Interview mit Revannth Murugesan von Carbon Performance
- Experteninterview:Nano Dimension-Mitbegründer Simon Fried über den Aufstieg des 3D-Drucks für die Elektronik
- Carbon-DLS-3D-Druck:Technologieüberblick