Experteninterview:Arevo-Mitbegründer Wiener Mondesir über die Herstellung des weltweit ersten 3D-gedruckten Carbonfaser-Fahrradrahmens
Das im Silicon Valley ansässige Unternehmen Arevo machte 2018 Schlagzeilen, nachdem es den ersten 3D-gedruckten Kohlefaser-Fahrradrahmen der Welt vorgestellt hatte. Der Anwendungsfall demonstrierte die einzigartigen Fähigkeiten der proprietären 3D-Drucktechnologie von Arevo, die Robotik und Software kombiniert, um leichte, maßgeschneiderte Verbundteile herzustellen.
Seitdem arbeitet Arevo mit dem Fahrradhersteller Franco Bicycles zusammen, um 3D-gedruckte Carbonfaser-Unibody-Rahmen für eine neue eBike-Marke zu liefern.
Diese Woche freuen wir uns, mit Wiener Mondesir, dem Mitbegründer und Chief Technology Officer von Arevo, über Arevos proprietäre Technologie, die Vorteile des 3D-Drucks von Verbundwerkstoffen und die Zukunft der Verbundwerkstoffherstellung zu sprechen.
Können Sie uns etwas über Arevo erzählen?
Unser Ziel bei Arevo ist es, die Herstellung von Verbundteilen in großem Maßstab zu ermöglichen. Wir tun dies mit einem Zusammenfluss von Robotik, Materialien und Software.
Wenn man sich die Verbundwerkstoffindustrie ansieht, bietet die Herstellung von Verbundwerkstoffteilen eine sehr große Chance. Kohlefaser kann stärker sein als einige Metalle und ist leicht, sodass sie in vielen Branchen eine breite Anziehungskraft hat.
Aber aus einer Reihe von Gründen wurde die Einführung der Herstellung von Verbundwerkstoffen erstickt, sodass die Gelegenheit nicht genutzt wird. Ein Grund dafür sind ineffiziente Fertigungsprozesse.
Die Verbundherstellung ist derzeit sehr arbeits-, ressourcen- und kapitalintensiv, was bedeutet, dass sie nicht wirklich auf große Mengen skaliert werden kann. Die Industrien, die wirklich von der Verbundwerkstoffherstellung profitieren konnten, waren diejenigen, die sich den Business Case leisten konnten, wie die Luft- und Raumfahrt und die sehr hochwertige Automobilindustrie.
Darüber hinaus gibt es lange Konstruktionszyklen aufgrund unzureichender Software und ineffizienter Simulation. Ein weiterer oft übersehener Grund ist das mangelnde Verständnis von Verbundwerkstoffen in anderen Branchen.
Arevo geht all diese Probleme an. Wir überdenken die Herstellung von Verbundwerkstoffen, indem wir die sogenannte Digitalisierung von Verbundwerkstoffen nutzen.
Wir haben uns entschieden, dieses Problem zu lösen, indem wir eine Software entwickeln, die die Wissenslücke schließt.
Sie beginnen mit einem 3D-Modell und unsere Software führt die Analyse durch, ermittelt die optimale endgültige Ausrichtung, die richtige Materialmenge und erstellt Anweisungen zur Herstellung des Teils mit unserer Fertigungstechnologie.
Nehmen wir als Beispiel ein Spinnennetz. Wenn Sie sich ein Spinnennetz ansehen, handelt es sich um eine 3D-Struktur mit der richtigen Menge an Material für ihren Zweck.
Die Faser, im Falle des Spinnennetzes die Seide, verwendet nur die richtige Menge an Material und ist perfekt dort platziert, wo sie gebraucht wird. Daraus lassen wir uns inspirieren, wenn wir eine optimierte Art des 3D-Drucks von Verbundteilen entwickeln.
Das ist also unsere Mission als Unternehmen:die Herstellung von Verbundwerkstoffen in großem Maßstab zu ermöglichen.
Welche Vorteile bietet der 3D-Verbunddruck?
Kohlefaserverbundwerkstoffe bieten ein hervorragendes Verhältnis von Festigkeit zu Gewicht, sodass Sie ein wirklich starkes und dennoch leichtes Material erhalten.
Wenn man sich den Trend im 3D-Druck ansieht, verwenden viele verschiedene Techniken Gitterstrukturen zum Leichtmetall, das von Natur aus dicht und schwer ist.
Aber wenn Sie von Anfang an mit einem leichten, starken Material wie Kohlefaser beginnen, kommen Sie viel schneller zum Endergebnis. Daher sind Verbundwerkstoffe für bestimmte Anwendungen viel besser geeignet als Produkte mit Metallgitterstruktur, die zwar gut aussehen, aber nicht unbedingt ihren Zweck erfüllen.
Die Komplikation bei Kohlefaser besteht darin, dass sie anisotrop ist, was bedeutet, dass es in eine Richtung stark ist. Das macht den Umgang ohne spezielle Werkzeuge etwas schwieriger.
Wir bei Arevo haben das Toolset für Designer entwickelt, sodass Sie keinen Doktortitel haben müssen, um mit Kohlefaserverbundwerkstoffen herzustellen. Dafür sorgt unsere Software.
Ihr 3D-gedruckter Fahrradrahmen aus Kohlefaser wurde bei seiner Vorstellung weithin bekannt gemacht. Wie war der Entstehungsprozess des Fahrradrahmens, vom Design bis zur Produktion?
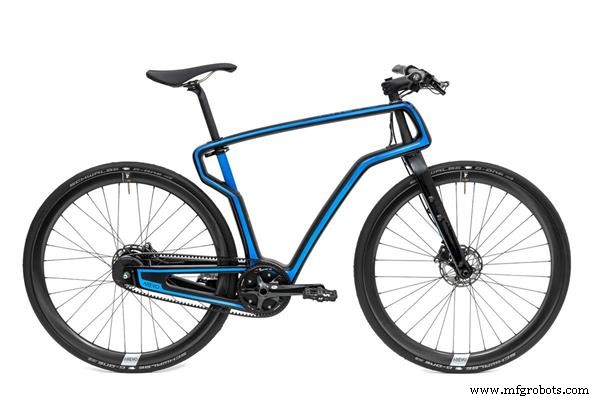
Diese spezielle Anwendung begann, um zu demonstrieren, was mit der Technologie möglich ist.
Ein Fahrradrahmen ist sehr zugänglich, aber er hat eine sehr komplexe Form und ist eine große Struktur, die Last, Torsion und die Fähigkeit, Gewicht aufzunehmen, erfordert. Es war also die perfekte Anwendung, um unsere Technologie zu demonstrieren.
Wenn Sie einen Schritt zurücktreten und sich traditionelle Composite-Bikes von heute ansehen, durchlaufen sie ein Design, eine Prototypen-Iteration und dann den ganzen Weg zur Produktion. Dieser Prozess dauert fast ein Jahr.
Darüber hinaus werden traditionelle Composite-Bikes in einem sehr manuellen Verfahren hergestellt. Rahmen werden aus 20 bis 30 Teilen zusammengeklebt und bis zu 40 Personen berühren jeden Rahmen. Es ist ein sehr arbeitsintensiver Prozess und Sie erhalten ein sehr teures Produkt, das nicht unbedingt skaliert.
Die Designs sind auch sehr ähnlich, sodass Sie nicht viele Anpassungen vornehmen können.
Mit unserer Technologie haben wir diesen Prozess von fast einem Jahr auf wenige Tage verkürzt. Die Software von Arevo nimmt ein CAD-Design und führt ein isotropes generatives Design auf dem Rahmen durch, das ein Designer entwickelt. Es optimiert auch die Orientierung und führt eine prädiktive Analyse durch.
Der nächste Schritt erfolgt in unserer Fertigung. Wir haben in Kalifornien eine Produktionsstätte gebaut, die mit unserer Roboter- und Abscheidungstechnologie maßgeschneiderte Fahrradrahmen auf Anfrage herstellen kann.
Als wir das Fahrrad auf den Markt brachten, wurden wir von allen großen Fahrradherstellern angesprochen, weil sie an der Gestaltungsfreiheit der Technik interessiert waren.
Wenn man sich das Design des Arevo Fahrradrahmens anschaut, dann geht das eigentlich einen Umweg vom herkömmlichen Fahrraddesign. Es hat beispielsweise keine Sitzstrebe und sieht ganz anders aus als ein herkömmliches Fahrrad.
Das Fahrrad von Arevo ist ein Unibody-Bike aus sehr starken Carbonfasern, die in der optimalen Ausrichtung im 3D-Raum ausgerichtet sind. Wir sind in der Lage, das Design in einer Unibody-Struktur zu erreichen, die es sehr solide und leicht macht.
Wir können das tatsächliche Fahrverhalten des Fahrrads mithilfe von Softwaretools optimieren. Wir können die Steifigkeit in bestimmten Bereichen des Fahrrads tunen und auf Wunsch eine noch federndere Fahrt ermöglichen. Bei herkömmlichen Fahrrädern versucht man im Grunde immer, immer wieder den gleichen Rahmen zu bauen.
Ein 3D-gedruckter Rahmen hingegen eröffnet ein neues Geschäftsmodell für eine Branche, die den sehr langen Prozess der Markteinführung eines neuen Fahrrads gewohnt ist. Heute werden jährlich etwa eine Million Verbundrahmen hergestellt. Und jetzt können Sie mit unserer Technologie tatsächlich sehr maßgeschneiderte Rahmen nach Bedarf einführen.
Unser Ziel ist es, weiterhin neue Anwendungen zu entwickeln, die diese Möglichkeit nutzen.
Ist der maßgeschneiderte Produktionsansatz ein skalierbares Geschäftsmodell?
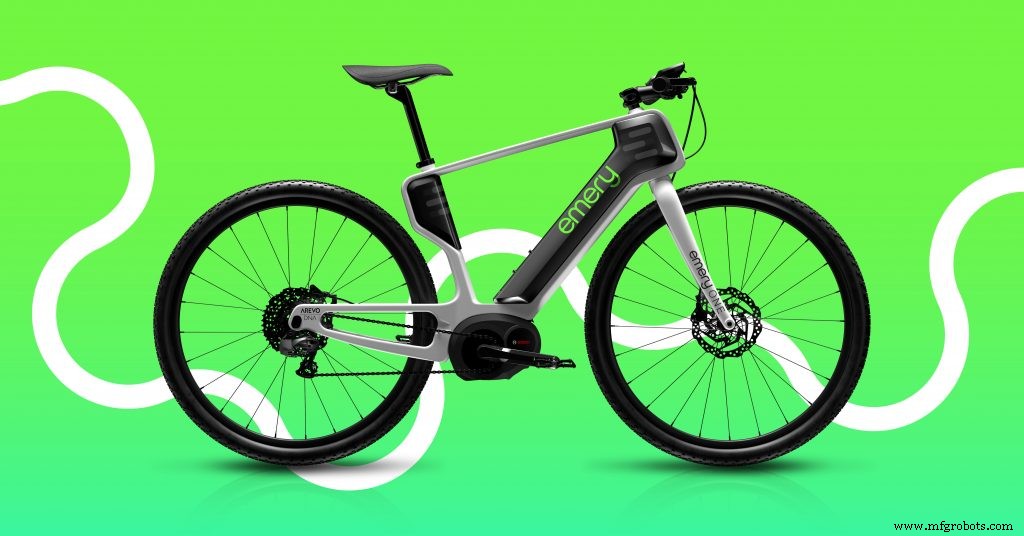
Bei Fahrrädern wird auf Individualisierung Wert gelegt. Jeder Mensch ist einzigartig. Du wirst müder, wenn du kein Fahrrad fährst, das für deinen Rahmen entworfen, eingestellt oder angepasst wurde. Ein Fahrrad ist also eigentlich ein gutes Vehikel, um den Wert der Individualisierung zu demonstrieren.
Es gibt einen ganzen Trend rund um die Mikromobilität und die Möglichkeit, mit einem sehr bequemen Fahrzeug herumzulaufen. Das Fahrrad steht dafür. In vielen verschiedenen Ländern ist es ein vorherrschendes Transportmittel.
Wenn Form und Funktion angepasst werden müssen, ist dies nicht auf dem Massenmarkt möglich. Aber mit unserer Technologie kann ein Verbraucher den Rahmen entwerfen und unsere Software kann garantieren, dass der von ihm entworfene Rahmen strukturell einwandfrei ist.
Dann können sie das an unsere 3D-Druckzellen senden, um dieses Fahrrad nach Bedarf herzustellen. Dadurch wird der Prozess vom Konzept bis zur Produktion sehr vereinfacht.
Welche anderen Anwendungen stellen Sie sich mit Ihrer Technologie vor?
Heute konzentrieren wir uns auf die Fahrrad- und Mobilitätsanwendungen. Dies sind Anwendungen, die das von uns angebotene Wertversprechen nutzen können, das aus sehr geringem Gewicht, hohem Festigkeits-Gewichts-Verhältnis und kundenspezifischen Produkten besteht.
Wenn man sich branchenübergreifend ansieht, ist es wirklich wichtig, die Leistung zu verbessern im Sportbereich sowie in der Automobil-, Energie- und Luft- und Raumfahrtindustrie.
Wir haben eine Reihe verschiedener Anwendungen, an denen wir arbeiten, bei denen geringes Gewicht, hohe Leistung und hohe Anpassungsfähigkeit erforderlich sind. Und das sind die Schlüsselbereiche, in denen unsere Technologie eingesetzt werden kann.
Wie passt Robotik in Ihre Technologie?
Wenn Sie sich den 3D-Druck ansehen, ist der größte Teil des 3D-Drucks schichtbasiert, und die Schichten werden in den X- und Y-Ebenen abgelegt. Wenn man sich die Eigenschaften von Teilen ansieht, die mit diesem Verfahren hergestellt wurden, neigen sie dazu, in Z-Richtung zu leiden.
Für das Ablegen unserer Kohlefasern in X-, Y- und Z-Richtung verwenden wir einen voll gelenkigen Sechs-Achs-Roboter. Wir haben das Z-Stärke-Problem beseitigt, das andere schichtbasierte Technologien plagt, weil wir in der Z-Richtung ablegen können. Das ist eine der einzigartigen Fähigkeiten unserer Abscheidungstechnologie. Dabei spielt die Robotik eine große Rolle.
Der zweite Aspekt ist der Maßstab der Teile, die gedruckt werden können. Heutzutage sind die meisten Systeme auf einen bestimmten Bauraum beschränkt, was bedeutet, dass Sie nur Teile einer bestimmten Größe herstellen können. Wenn Sie eine bestimmte Größe überschreiten, muss das Teil in Unterbaugruppen zerlegt werden, um eine größere Struktur zu erhalten.
Unsere Roboter bieten unbegrenzte Bauraumfähigkeiten, da wir unsere Roboter auf dem Portal platzieren können, um Luft- und Raumfahrtteile herzustellen. Gleichzeitig kann derselbe Roboter ein Fahrrad bauen. Die Reichweite unserer Roboter beträgt vier Meter. Im Wesentlichen ist es sehr skalierbar, um uns diesen großen Druckumschlag zu geben.
Wie würden Sie den aktuellen Stand des Composite-3D-Druckmarktes beschreiben? Wie fortschrittlich ist die Technologie?
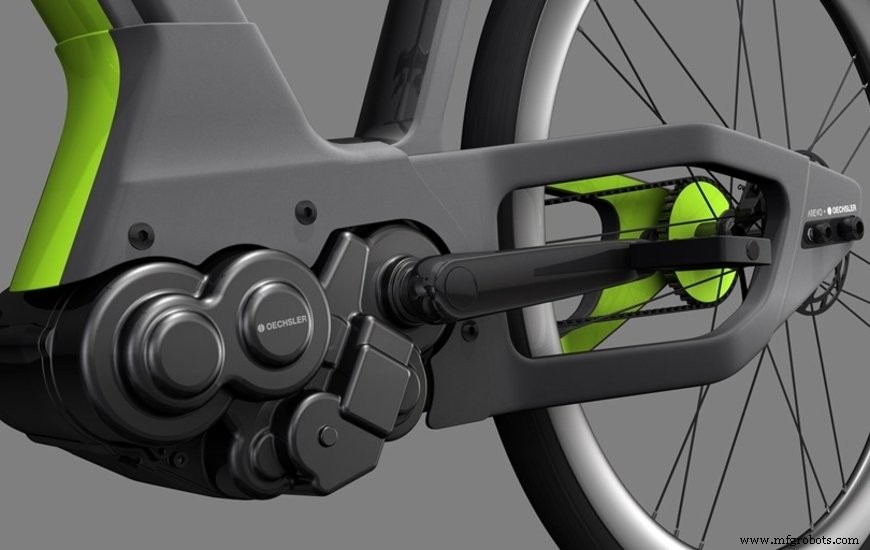
Die Composite-Industrie setzt schon seit geraumer Zeit auf Additiv. Die Komplexität der Geometrien war nur sehr begrenzt auf das, was in eine Form passt, beispielsweise Teile mit einer sehr kleinen Krümmung. Darüber hinaus werden die Schichten normalerweise manuell aufgetragen, was zu einem Teil mit relativ begrenzter Komplexität führt.
Composite-3D-Druck gibt es also schon seit einiger Zeit. Aber jetzt ermöglichen Dinge wie automatisierte Robotik oder mechatronische Systeme, die die Platzierung der Faser automatisieren, komplexere Geometrien.
Es gibt viele Unternehmen, die einen anderen Ansatz zur Automatisierung der Verbundstoffherstellung verfolgen, von verschiedenen Arten von Harzsystemen bis hin zu verschiedenen Anwendungsfällen.
Und das ist sehr hilfreich.
Insgesamt denke ich, dass sich der Sektor des Composite-3D-Drucks in einem gesunden Zustand befindet, wobei Arevo die Führung übernimmt.
Welche Herausforderungen sieht sich die Branche gegenüber, entweder der 3D-Druck im Allgemeinen oder der 3D-Verbunddruck im Besonderen?
Ich denke, die größten Herausforderungen resultieren aus dem Mangel an verfügbaren Softwaretools, um herauszufinden, was mit Additiv möglich ist. Sie haben eine Denkweise, traditionelle Fertigungstechniken zu betrachten, und wir wurden in traditionellen Fertigungstechniken geschult.
Die Leute beginnen oft mit Teilen, die auf traditionelle Weise hergestellt wurden, und möchten dieses Teil mit einem Additiv versehen, aber das passt nicht immer zusammen.
Aber wenn Sie wirklich ausschöpfen, was Sie mit Additiven tun können, sei es auf Metall-, Verbund- oder Polymerbasis, was die Einzigartigkeit und Komplexität angeht, brauchen Sie wirklich Werkzeuge, die Sie durch diesen Prozess führen und die Designer informieren und Ingenieure.
Wie sehen Sie die Entwicklung der Branche in den nächsten fünf Jahren?
Es ist sehr ermutigend. Seit der Gründung von Arevo haben wir uns immer auf Produktionsteile konzentriert.
Wenn man sich heute die Branche ansieht, ist es wirklich ermutigend zu sehen, dass alle über Produktionsteile sprechen. Das ist das gemeinsame Thema.
Ich erwarte, dass die Branche in Zukunft auch über Qualität und Skalierbarkeit spricht. Wenn Sie mit der Herstellung von Produkten beginnen, wird die Produktion in großem Maßstab und mit größerer Wiederholbarkeit der Hauptfokus der Branche sein.
Die Sicherstellung der Qualität von Teilen und Prozessen ist derzeit ein großes Gesprächsthema für die additive Fertigung. Wie geht Arevo dabei vor?
Einer der wichtigsten Durchbrüche, die Arevo erzielen konnte, ist unser laserbasierter Abscheidungsprozess.
Darüber hinaus setzen wir maschinelle Lernalgorithmen ein, die eine In-Situ-Inspektion durchführen können. Wir verfügen über eine Sensorsuite und können ein Teil während der Herstellung vor Ort inspizieren.
Dies ermöglicht uns ein sehr homogenes Druckmaterial mit weniger als 1% Hohlräumen zu erhalten. Sie könnten einen Querschnitt eines Teils erstellen und wenn Sie es unter ein Mikroskop bringen, können Sie sehr homogenes gedrucktes Material beobachten.
Dies bedeutet sehr hochwertige Teile für sehr anspruchsvolle Anwendungen wie die Luft- und Raumfahrt. Diese Qualitätskontrolle vor Ort ermöglicht uns in Kombination mit unserer Closed-Loop-Überwachung eine wiederholbare und vorhersehbare Qualität.
Was halten die nächsten 12 Monate für Arevo bereit?
In den nächsten 12 Monaten werden wir uns auf die Fertigungsausführung konzentrieren. Seit wir das Bike auf den Markt gebracht haben, haben wir tatsächlich mehr Nachfrage, als wir bedienen können. Unser Ziel für das nächste Jahr ist es, weiterhin neue Anwendungen auf den Markt zu bringen, aber hauptsächlich unsere Kapazitäten zu skalieren, um der aktuellen Nachfrage gerecht zu werden.
Um mehr über Arevo zu erfahren, besuchen Sie: https://arevo.com/
3d Drucken
- Experteninterview:Nanoe CEO Guillaume de Calan über die Zukunft des keramischen 3D-Drucks
- Experteninterview:Ultimaker-Präsident John Kawola über die Zukunft des 3D-Drucks
- Experteninterview:Nano Dimension-Mitbegründer Simon Fried über den Aufstieg des 3D-Drucks für die Elektronik
- Experteninterview:Carbons Mitbegründer Philip DeSimone über den Übergang zur Großserienproduktion mit 3D-Druck
- Experteninterview:Jabils Rush LaSelle zur Zukunft der additiven Fertigung
- Experteninterview:Greg Paulsen von Xometry über den Aufstieg des Manufacturing-as-a-Service-Geschäftsmodells
- Experteninterview:VP of Technology Partnerships von VELO3D zur Erweiterung der Fähigkeiten des 3D-Metalldrucks
- Experteninterview:John Barnes, Gründer von The Barnes Group Advisors, über die Zukunft der additiven Fertigung
- Einführung des weltweit ersten Carbonfaser-Smartphones
- Toray stellt die weltweit erste poröse Kohlefaser mit kontinuierlicher Porenstruktur in Nanogröße her