Die letzten fünf Jahre feiern
Letzten Monat haben wir fünf Jahre gefeiert, seit eine Handvoll Leute in einer Garage den ersten Kohlefaser-3D-Drucker entwickelt haben. Vielen Dank an unsere Kunden, die zu unserem Erfolg beigetragen und in den letzten fünf Jahren an uns geglaubt haben. Hier ist die Geschichte unserer Anfänge, der Early Adopters, die an uns geglaubt haben und wie unsere Kunden es uns ermöglicht haben, den Weg der Innovation fortzusetzen.
The Mark One
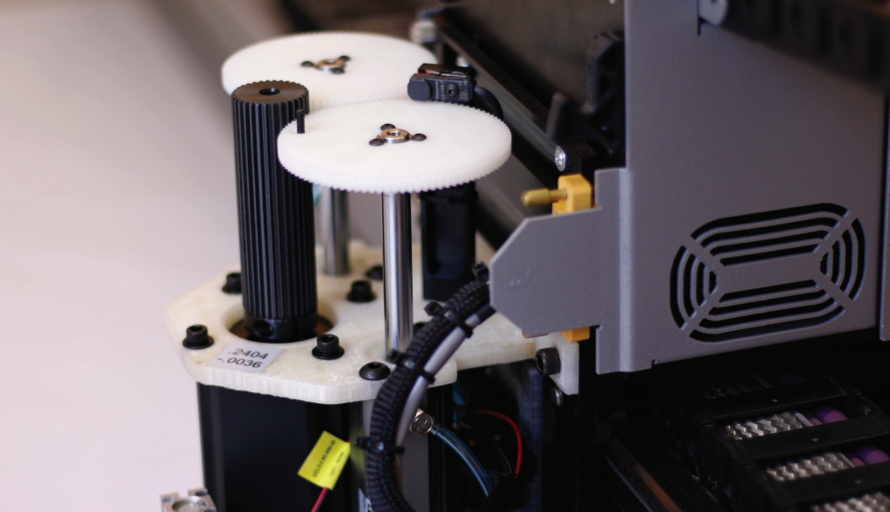
Im Januar 2014 stellten wir auf der SolidWorks World den ersten 3D-Drucker der Welt vor, der in der Lage ist, Endlos-Carbonfasern zu drucken:den Mark One. Autometrix glaubte an das Konzept und kaufte einen der ersten Markforged-Drucker.
Autometrix bietet Schneideausrüstung und Musterungssoftware für eine Vielzahl von industriellen Anwendungen, die für alles vom Transport bis hin zu medizinischen Geräten verwendet werden. Das Unternehmen wollte das Prototyping ins eigene Haus bringen, aber die Ingenieure „mussten sicherstellen, dass die Ergebnisse des Prototyping-Prozesses dem entsprechen, was [sie] zu entwerfen versuchten“, so Tyler Green, Elektroingenieur bei Autometrix. Nachdem das Team erkannt hatte, dass es ein faserverstärktes Teil in 3D drucken konnte, das tatsächlich an seinem Schneidkopf funktionierte, wurde das Team mit dem Mark One verkauft.
Das war erst der Anfang. Autometrix druckte dann einen kompletten Schneidkopf mit dem Mark One, und die Ingenieure stellten fest, dass der gedruckte Schneidkopf ein halbes Pfund weniger wog als sein Gegenstück aus Aluminium. Die leichten Teile des Mark One hielten allen Belastungen stand, die ihre Gegenstücke aus Metall und mehr ausüben, und ermöglichten es Green und anderen Ingenieuren bei Autometrix, ihre mechanischen Systeme zu verbessern und zu erweitern.
The Mark Two
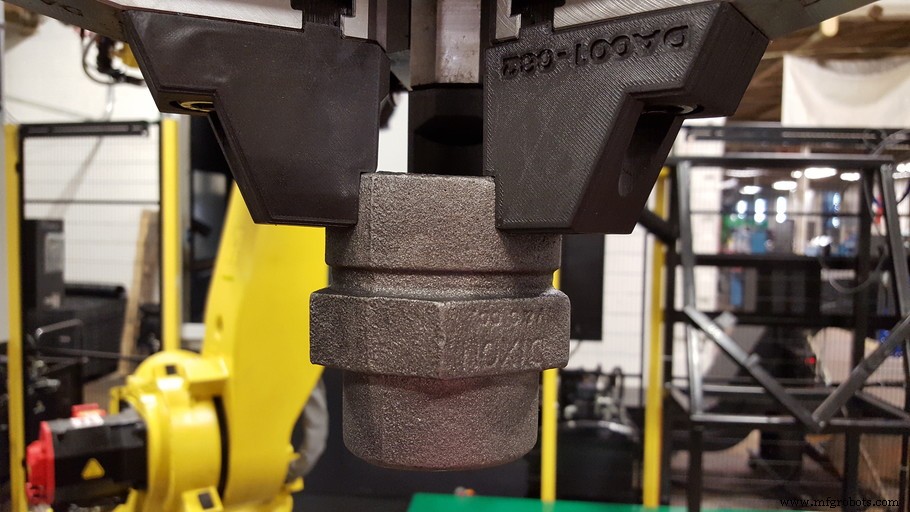
Wir haben den Mark Two – die nächste Generation des Mark One – im Februar 2016 auf den Markt gebracht. Der Mark Two verfügte über ein komplett neu entwickeltes Verbunddrucksystem, das eine höhere Festigkeit und höhere Qualität von Teilen als sein Vorgänger ermöglichte. Der Armaturen- und Ventilhersteller Dixon Valve benötigte einen Drucker, der hochfeste Teile herstellen konnte, was den Mark Two zu einer idealen Lösung für das Unternehmen machte.
Dixon-Ventil war auf der Suche nach einer Verbesserung seiner Produktionslinienlösungen. Die Ingenieure Max de Arriz und J.R. Everett mussten in ihrem Fertigungsprozess hochfeste Greifbacken für industrielle Roboterarme entwickeln. Der Roboterarm transferiert mehrere verschiedene Teile zwischen zwei vertikalen Drehzentren, und das Unternehmen benötigte starke, sichere und chemikalienbeständige Backen. Jedes Produktlinien-Setup erforderte eine kundenspezifische Ausrüstung, um bestimmte Teile effizient zu halten. Das Unternehmen wusste, dass es einen 3D-Drucker für anpassbare Teile benötigte, was seine Ingenieure zum Mark Two führte.
„Mit dem Mark Two konnten wir einen Roboterarm in einer Fertigungszelle in weniger als 24 Stunden umrüsten“, erklärt Everett. Der Mark Two ermöglichte es Dixon Valve, neue Fertigungslösungen mit beispielloser Geschwindigkeit und Kosten zu produzieren, und bietet dem Unternehmen ein leistungsstarkes neues Werkzeug in seiner Toolbox. Everett ist der Ansicht, dass der Mark Two eine kritische Komponente im Designprozess des Unternehmens ist und sagt:„Es verändert unsere Arbeitsweise wirklich so weit, dass wir tatsächlich unsere Verfahren und Pläne ändern, um dieses bahnbrechende Produkt unterzubringen.“
Die Einführung von Onyx
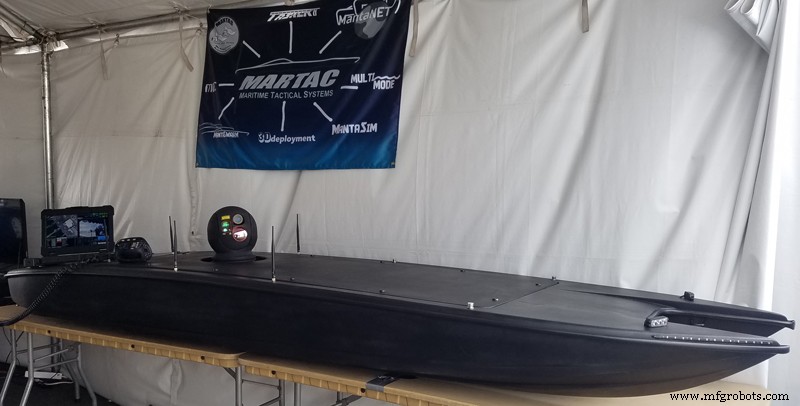
Im Jahr 2016 haben wir Onyx auf den Markt gebracht, unseren verbundverstärkten Thermoplast der nächsten Generation, der sich einzigartig für Fertigungsumgebungen eignet. Da Onyx eine sehr hohe thermische Stabilität besitzt, neigt es nicht zum Verziehen. Es hat eine überlegene Festigkeit und Steifigkeit und ist ein hochpräzises Material mit hoher Wiederholbarkeit. Es war diese hohe Präzision, die MARTAC zum ersten Mal dazu brachte, in Onyx zu drucken.
MARTAC (Maritime Tactical Systems) entwickelt und fertigt unbemannte Hochleistungs-Wasserschiffe. Das Unternehmen wollte geometrisch komplexe Einlässe schaffen, die dazu beitragen könnten, Meerwasser durch Kühlkanäle zu leiten. Durch den 3D-Druck dieses Teils in Onyx war MARTAC in der Lage, eine komplexe, benutzerdefinierte Geometrie zu erstellen, die nicht den Bedingungen der subtraktiven Bearbeitung entsprechen musste.
Onyx ist heute das Hauptmaterial für MARTAC-Schiffe. „Das Schöne an der Verwendung des Onyx ist, dass er durch den ständigen Aufenthalt im Salzwasser nicht korrodiert. Diese Teile haben sich auch als ziemlich widerstandsfähig gegenüber Schmutz im Wasser erwiesen“, sagt Ian Weaver, Operations Coordinator bei MARTAC. Das Drucken dieser Einläufe senkt die Herstellungskosten für das Unternehmen drastisch, was ein unglaublich schwierig herzustellendes Teil wäre.
Wird industriell
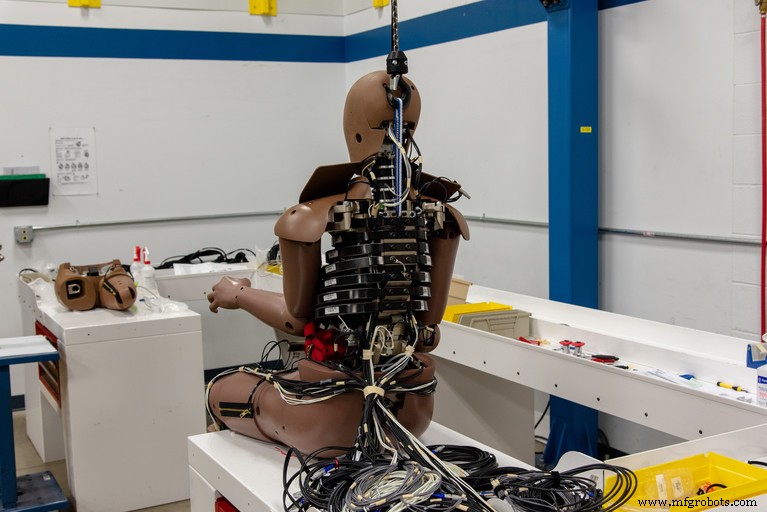
Mit fast dem dreifachen Bauvolumen und einer fortschrittlichen selbstüberwachenden Sensorsuite war der X7 unser erster 3D-Drucker im Industrieformat. Humanetics – der weltweit führende Anbieter von Crashtest-Dummys – benötigte eine neue Technologie, um den Prozess zum Austausch großer Teile zu beschleunigen. Der X7 war die perfekte Lösung für sie.
Humanetik “ Crashtest-Dummys werden in der Automobil-, Militär- und Luft- und Raumfahrtindustrie eingesetzt. Angesichts des Problems, dass die Formen zu schnell verschleißen, suchte Humanetics nach einer kostengünstigen Möglichkeit, langlebige Teile herzustellen, die hohen Temperaturen standhalten. Kris Sullenberger, Design Engineer bei Humanetics, schaute sich 3D-Druckformen für Crashtest-Dummy-Teile an und stieß auf den X7.
Humanetics hat zwischen fünf und zehn Formen gedruckt und plant, viele der 150 Formen des Unternehmens durch Markforged-Drucke zu ersetzen. Zusätzlich zu den Kosten- und Haltbarkeitsvorteilen stellte Kris fest, dass gedruckte Formen bessere Teile ergeben. Wo Silikonformen Nähte und andere Unvollkommenheiten hinterlassen, führt die präzise Passform gedruckter Formen zu einem nahezu perfekten Teil. Vom Druck von Produktions-Crashtest-Dummy-Teilen für sein Konstruktionsteam bis zum Austausch massiver, alternder Vorrichtungen für Montagetechniker hat Humanetics fast immer die Maschinendrucke. Kris gefällt es, wie er wählen kann, ob er "Tausende und Abertausende von Dollar ausgeben kann, um diese im Freien bearbeiten oder produzieren zu lassen" oder "sie im Haus für buchstäblich Dutzende oder Hunderte von Dollar zu machen".
Metall X
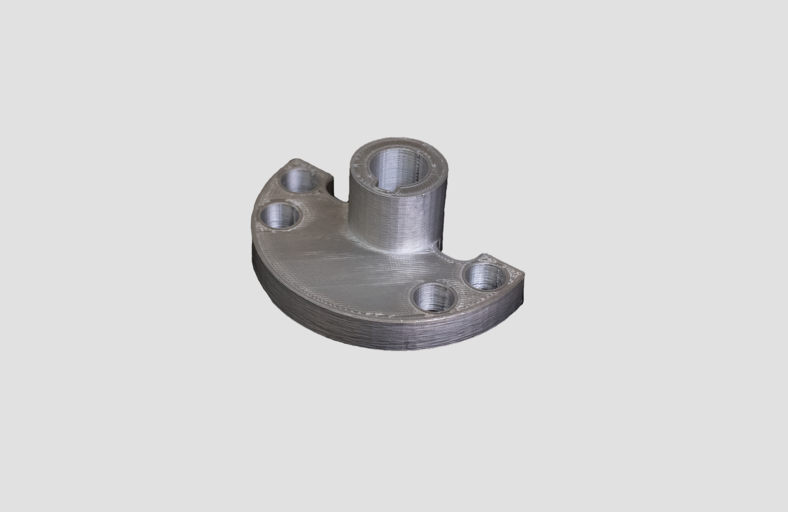
Im letzten Jahr haben wir mit dem Metal X den Metall-3D-Druck in unsere Produktlinie aufgenommen. Die Möglichkeit, Edelstahlteile zu drucken, eröffnet neue Möglichkeiten zum Drucken von gleichwertigem Ersatz für eine Vielzahl von Produktlinien . Stanley Infrastructure hat das Metal X eingeführt, um zu untersuchen, wie teure maßgeschneiderte Teile durch billige gedruckte ersetzt werden.
Stanley-Infrastruktur , ein Geschäftsbereich von Stanley Black &Decker, ist der weltweit größte Hersteller von handgeführten Hydraulikwerkzeugen. Das Unternehmen benötigte ein schwer zu bearbeitendes Teil zur Aufnahme verstellbarer Führungsräder an einer Eisenbahnherzschleifer. Die Ingenieure entschieden sich, Radwellen aus einem einzigen Stahlblock zu bearbeiten, aber aufgrund des Durchmessers des Flansches und der Länge der Welle wurden in jedem Teil ~90% des Ausgangsmaterials verschwendet. Mit Hilfe der Markforged-Ingenieure hat Stanley Infrastructure die Radwelle zu einer dreiteiligen Baugruppe umgestaltet. Durch den Kauf einer handelsüblichen Welle und Passfeder war das Unternehmen in der Lage, den komplexeren Flansch problemlos auf ein Metall-X zu drucken. Die neue Baugruppe bestand sowohl die Haltbarkeits- als auch die Missbrauchsfallprüfung.
Laut einem Ingenieur von Stanley Infrastructure Innovation „ist es sehr machbar, die Metal X-Plattform bei der additiven Fertigung des diskutierten Aktuatorgehäuses mit sehr minimalem Kapital- und Zeitaufwand zu nutzen.“ Seit dem Kauf des Druckers konzentriert sich Stanley Infrastructure auf den Druck hochwertiger Teile, wodurch die Bearbeitungszeit minimiert und die Kosten gesenkt werden.
Was kommt als nächstes
Von Fortune-100-Unternehmen bis hin zu Herstellern in Familienbesitz verwenden Tausende von Unternehmen Markforged-Technologie, um ihre Produkte und Prozesse zu verbessern. Und genau wie diese Unternehmen suchen wir ständig nach neuen Wegen, um unsere Produkte und Prozesse besser denn je zu machen.
Auf viele weitere Innovationsjahre unserer Kunden!
Möchten Sie die Leistungsfähigkeit unserer Drucker testen? Fordern Sie hier ein kostenloses Markforged-Musterteil an .
Möchtest du mehr solcher Beiträge sehen? Folgen Sie uns auf Facebook , Twitter , Instagram , und LinkedIn für weitere Updates!
3d Drucken
- Wir feiern 10 Jahre 3D-Druck von Formlabs
- Carl Calabrias Leitfaden zur Verwendung von Beilagen auf dem Mark One
- So verwenden Sie den Klebestift auf Ihrem Mark One Druckbett
- Amazon-Vollwertkost:Zwei Jahre nach dem Deal
- Fünf Wege zu einer umweltfreundlicheren letzten Meile
- Die fünf beliebtesten Baumaschinenhersteller
- 5G-IoT-Einnahmen werden in den nächsten fünf Jahren explodieren
- Die digitale Fertigung wächst in zwei Jahren um das Dreifache
- ProtoPumpkins im Laufe der Jahre
- Bearbeitung, Disruption und die kommenden Jahre