Neue Ansätze zur Herstellung von Teilen für das Ölfeld
Fracking hat zu großen Veränderungen im Ölfeld und großen Veränderungen in der Teilebearbeitung geführt.
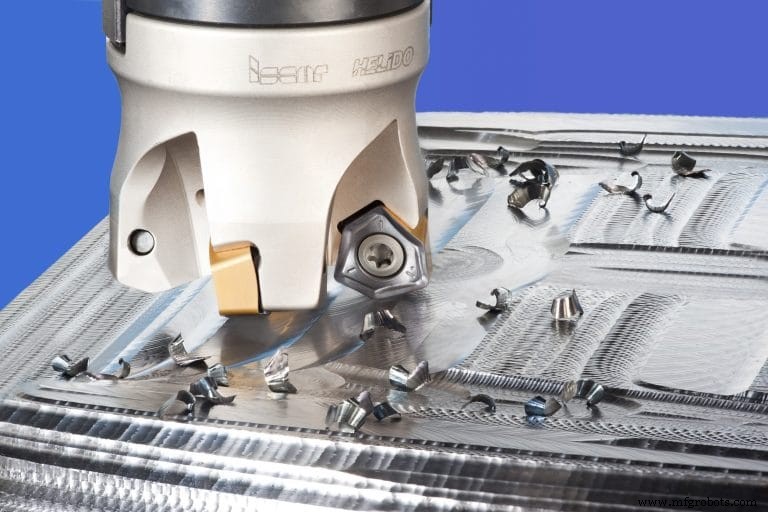
Rod Zimmerman vom Schneidwerkzeughersteller Iscar Metals lebt in einer angenehmen grünen Zone in einem Vorort von Fort Worth. Doch innerhalb einer halben Meile von seinem Haus hat eine Ölgesellschaft ein vertikales Loch mit einer Tiefe von 7.500 Fuß (2.286 m) versenkt, von dem aus neun seitliche Linien gespreizt wurden, die jeweils etwa eine halbe Meile lang sind. Es pumpt Fracking-Flüssigkeit mit 9.000 psi in diese Leitungen, um das Erdgas zu extrahieren. Es ist ein ebenso gutes Beispiel wie jedes andere für die Allgegenwart der Fracking-Revolution und die erstaunliche Technologie, die damit verbunden ist.
Und obwohl die Revolution vielleicht nicht buchstäblich „überall“ ist, sagte Salvatore Deluca, Produktmanager für einen anderen Schneidwerkzeughersteller, Allied Machine &Engineering, dass die riesigen Fracking-Anlagen in seinem Landkreis „Städte“ genannt werden. Abgesehen davon, dass sich diese „Städte“ im Gegensatz zu Dallas-Fort Worth im fernen Ohio befinden, einem Staat, der zuvor nicht für Erdöl bekannt war. Kein Wunder also, dass große Änderungen im Ölfleck zu großen Änderungen bei der Bearbeitung von Teilen für den Ölfleck geführt haben.
Bekämpfung des Fracking-Blocks
Wie oben angedeutet, werden beim hydraulischen Brechen (häufiger als Fracking bezeichnet) Gas und Öl aus Schieferformationen gewonnen, indem in die Erde gebohrt und eine Mischung aus Wasser, Sand und Chemikalien mit extrem hohem Druck in das Gestein injiziert wird. Um diesen Druck zu erzeugen, sind riesige Pumpen erforderlich, deren Schlüsselkomponente das „Flüssigkeitsende“ oder der „Fracking-Block“ und seine Ventile, Kolben und Laufbuchsen sind.
Der hohe Druck und die Abrasivität des Schlamms, der durch diese Blöcke gepumpt wird, verursachen schnellen Verschleiß und Risse. Und da Ölfeldbetreiber hohen Druck aufrechterhalten müssen, sind sie laut Paul Best, einem Produktspezialisten bei Allied Machine, Dover, Ohio, gezwungen, die Fluidenden alle paar Tage auszutauschen. Am besten werden besagte Fluidenden aus massiven Stahlblöcken bearbeitet und sind im Allgemeinen etwa 3 Fuß hoch, 4 Fuß breit und 2–3 Fuß (0,61–0,91 m) dick. Mit komplexen Konturen, zahlreichen Kanälen, drei bis fünf Durchgangsbohrungen (jeweils bis zu 8″ [203,2 mm] Durchmesser) und drei bis fünf sich kreuzenden Querbohrungen erfordern Fluidends einen enormen Aufwand an Fräsen, Bohren und Gewinden.
Zimmerman, Vice President of Sales, West Zone bei Iscar, sagte, dass Fluidends traditionell aus legiertem Stahl der Serie 4000 hergestellt wurden, aber um den Verschleiß zu bekämpfen, versuchen die Benutzer „exotischere Legierungen wie 17-4 PH-Edelstahlmaterial, Super-Duplex-Edelstahl und 15-5 Edelstahl.“ Deluca schätzt, dass ungefähr die Hälfte der flüssigen Enden, die er jetzt sieht, eine Variante eines vorgehärteten Edelstahls sind, und der Anteil wächst weiter.
Gayle Vollmer, Engineering Services für Hartwig in Houston (Okuma-Händler in der Gegend), sagte, dass es auch einen Schritt gibt, härtere Materialien für die Teile eines Fracking-Blocks zu verwenden, die am anfälligsten für Verschleiß sind, und einen Versuch, Fracking-Blöcke so umzugestalten, dass mehr Komponenten vorhanden sind sind leicht austauschbar. Aber er vermutete, dass die aktuelle Nachfrage nach hoher Produktion diese Forschung „auf Eis gelegt“ hat.
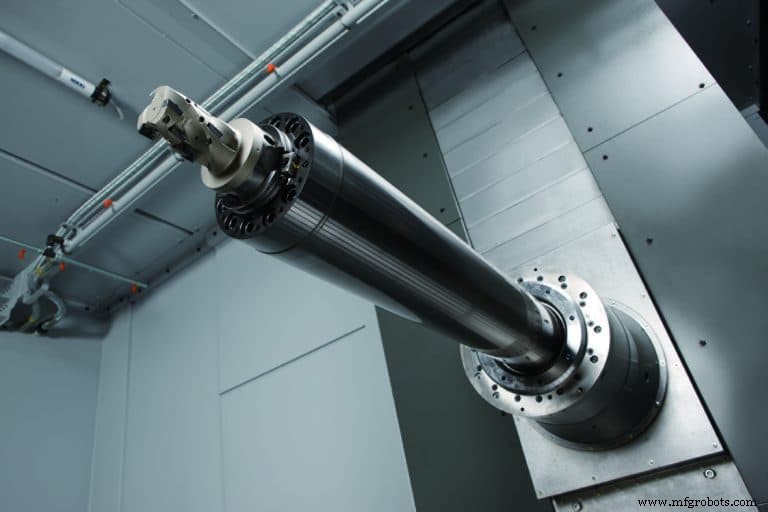
Ob aus 4340 oder einem härteren Edelstahl, die Bearbeitung eines Fluidends erfordert praktisch ein großes Bohrwerk oder ein horizontales Bearbeitungszentrum. Jason Schooley, Regional Sales Manager für JTEKT Toyoda Americas, Arlington Heights, Illinois, sagte, das Ziel sei es, so viele Operationen wie möglich in einer einzigen Maschine durchzuführen, was bei einem so großen und schwer zu bewegenden Teil doppelt wichtig sei.
Schooley sagte, dass Bohrwerke zwar normalerweise größere Tische für noch größere Teile haben, Horizontalbohrwerke wie der FH1250SX von Toyoda jedoch fast viermal schneller sind. Das liegt unter anderem an einer zahnradgetriebenen 6.000er-Spindel (optional 8.000er oder 15.000er High-Torque-Spindel) und einem Eilgang von 1.654 ipm (42 m/min). Die Maschine ist auf einer Meehanite-Gusseisenbasis für maximale Steifigkeit mit zylindrischen Rollenführungen für erhöhte Geschwindigkeit aufgebaut, während der doppelte Kugelumlaufspindelantrieb auf den Y- und Z-Achsen die Bearbeitungsstabilität bei schwerer Zerspanung erhöht.
Der FH1250SW verfügt außerdem über eine W-Achsen-Pinole für Tiefbohr- und Bohrarbeiten. Er fügte hinzu, dass sich in den letzten Jahren „eine Reihe von Werkzeugmaschinenherstellern für einen eingebauten U-Achsenkopf“ oder eine W-Achse entschieden haben, die parallel zur X-Achse bzw. Z-Achse fahren. Dadurch ist es möglich, den Drehpunkt für einen feststehenden Drehmeißel zu ändern, ein nützliches Feature beim Schneiden großer Bohrungen oder anderer großer Konturen. Denn Fluid Ends haben nicht nur große Bohrungen, die Bohrungen sind innen oft auch „flaschenförmig“, sodass sie nicht einfach aufgebohrt werden können. Für Maschinen, die keine eingebaute U-Achse haben, können Benutzer einen „Feed-Out“-Kopf hinzufügen, der die gleiche Funktion erfüllt, D’Andrea ist einer dieser Lieferanten.
Es gibt Nachteile bei der Montage eines großen Kopfes auf einer rotierenden Spindel, einschließlich möglicher Teileinterferenzen und Inkompatibilität mit Kühlmittelzufuhr durch die Spindel. Die Aftermarket-Option benötigt auch einen eigenen externen Antrieb und es ist möglicherweise nicht möglich, das Rig automatisch auszutauschen, wie Sie es bei anderen Werkzeugwechseln tun würden.
Schooley sagte jedoch, dass Interferenzen bei Frack-Block-Anwendungen kein Problem darstellen, wenn der Z-Achsen-Verfahrweg der Maschine lang genug ist, um zu verhindern, dass der Zusatzkopf über die Spurlinie hinausragt. Mit 1.850 mm Verfahrweg der Z-Achse und 200 mm von der Spindelnase bis zum Totband in der Tischmitte bewältigt die 1250-Maschine Fracking-Blöcke ohne Beeinträchtigung. Er fügte hinzu, dass Toyoda die automatische Wechselfunktion für seine Konturierköpfe weiterentwickelt hat, um „unseren Kunden zu helfen, in einer Branche, die so volatil wie Öl ist, einen Schritt voraus zu sein.“
Nach Schooleys Erfahrung sind die modularen Bohrwerkzeuge, die von Innovative Tooling Solutions und anderen erhältlich sind, standardmäßig mit Kühlmittel durch die Spindel ausgestattet, und viele Werkstätten, die Frack-Blöcke herstellen, verwenden ein spezielles horizontales Bohrwerk mit einem Konturkopf, um die Bohrungen fertigzustellen. Toyoda bietet auch horizontale Bearbeitungszentren mit Pinolenspindel und einem Drehmoment von 1.560 ft-lb für den Schwerlastbetrieb an. Laut Schooley kombiniert die Pinolenspindel mit 4.000 U/min die Reichweite und Kraft, die zum Bohren und Tiefbohren erforderlich sind, sodass Werkstücke, die zuvor zwei Arbeitsgänge erforderten, auf einer einzigen Maschine fertiggestellt werden können. Die drehbare Palette mit 360.000 Positionen der Maschine bietet maximale Flexibilität für die Schwerzerspanung einer Vielzahl von Werkstücken.
Okuma America Inc., Charlotte, N.C., hat eine Programmieroption namens Turn-Cut entwickelt, die es einem horizontalen Bearbeitungszentrum ermöglicht, eine Drehmaschine beim Schneiden von kreisförmigen und eckigen Merkmalen an großen, unausgeglichenen Teilen nachzuahmen, ohne einen U-Kopf zu verwenden. Wie Ted Winkle, Koordinator des Tech Centers von Okuma in Houston, erklärte:„Anstatt das Teil zu drehen, was bei einigen großen Teilen schwierig oder unmöglich wäre, drehen Sie das Werkzeug um das Teil. Und anstatt dass ein U-Kopf das Werkzeug aus der Mitte der Rotationsachse herausbewegt, interpoliert Turn-Cut diese Achsen in X und Y, während es auch ein Einzelpunkt-Drehwerkzeug in Z zuführt.“
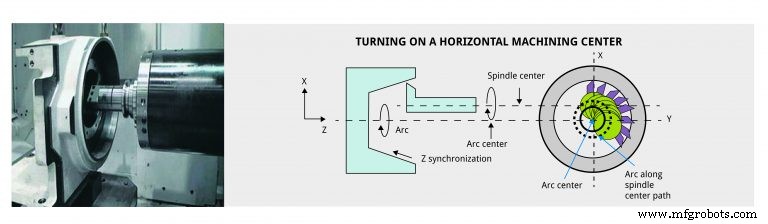
Winkle glaubt, dass Turn-Cut in der Öl- und Gasindustrie für Teile wie Fracking-Blöcke eine größere Rolle spielen wird, weil „bei zunehmendem Durchmesser der Bohrungen viel Drehmoment erforderlich ist, um ein solides Werkzeug zum Bohren eines Lochs dieser Größe einzusetzen. Die Drehschneidefähigkeit im Gegensatz zu einem U-Kopf und all den damit verbundenen teuren Werkzeugen ist ein Vorteil.“
Andererseits ist Turn-Cut nicht billig, da es zusätzliche Software für spezielle Beschleunigung, Verzögerung und Synchronisierung sowie Glasmaßstäbe und Kugelumlaufkühlung erfordert. Aber Sie erhalten mit diesen Funktionen eine bessere Präzision für eine Vielzahl von Teilen und es erhöht die Wahrscheinlichkeit, dass Sie Teile in einer Aufspannung fertigstellen können.
Schooley entgegnete, dass die Technik viele sich wiederholende Bewegungen im selben Bereich der Kugelumlaufspindeln und Führungsbahnen erfordert (je kleiner der Durchmesser, desto mehr würde dies passieren) und dies könnte die Lebensdauer der Maschine verkürzen.
Andererseits, sagte Winkle, würden Sie keine übermäßige Bewegung im selben Bereich haben, es sei denn, Sie verwenden diese Funktion häufig für Teile gleicher Größe. Und wenn Sie die Fähigkeit nicht häufig benötigen, könnten Sie die hohen Kosten einer U-Achse nicht rechtfertigen, sodass Turn-Cut eine logischere Option wäre. Wie bei jeder Werkzeugmaschinenfunktion gibt es Kompromisse.
Pferdestärken-Himmel
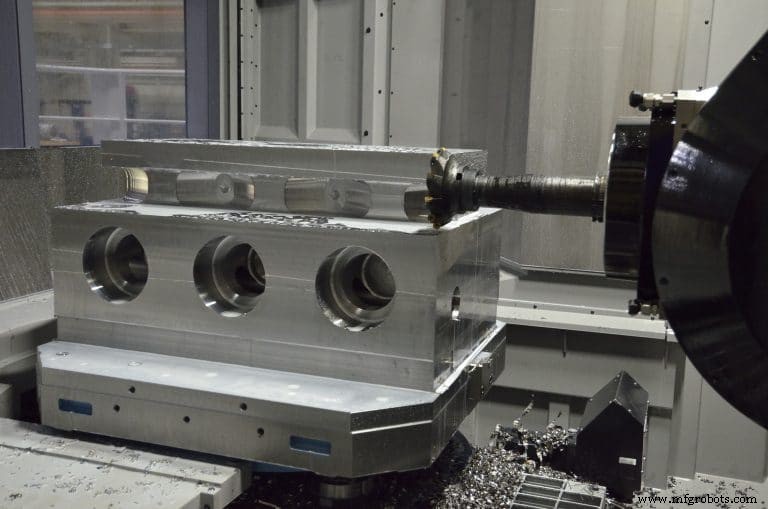
Für Makino Inc., Mason, Ohio, sind die horizontalen fünfachsigen Bearbeitungszentren T1 und T2 die „go-to“-Plattformen für Teile wie Fracking-Blöcke. David Ward, Product Marketing Manager, sagte, dass beide Maschinen direkt angetriebene Spindeln haben, die „ideal für die anspruchsvollen rostfreien und hochlegierten Stähle sind, die in dieser Branche verwendet werden.“
Der T1 verfügt über eine HSK100-Spindel mit 12.000 U/min mit 143 PS und 740 ft-lb Nenndrehmoment. Die größere T2-Spindel verwendet eine HSK125-Schnittstelle für radiale Steifigkeit. Die T2-Spindel mit 4.000 U/min liefert 200 PS und 1.107 ft-lb Nennleistung und Drehmoment.
Ward fügte hinzu, dass beide Spindeln ihre maximalen Drehmomentwerte bis 1.000 U / min beibehalten. „Indem die maximalen Drehmomentwerte bis zu diesem Punkt ausgeführt werden, wird sichergestellt, dass die Spindel neue Fortschritte in der Schneidwerkzeugtechnologie, wie z. B. Hochtemperatur-Wendeplattenbeschichtungen, nutzen kann.“
Winkle bemerkte, dass der Ölfleck von CAT 50-Maschinen dominiert wird, stimmte jedoch zu, dass der Flächenkontakt, der durch die HSK- und BIG Plus-Schnittstellen bereitgestellt wird, ein Vorteil wäre, „wenn Sie einen langen Überhang haben. Da aber die meisten Bearbeitungskräfte axial wirken, macht es keinen großen Unterschied, für welchen Spindeltyp Sie sich entscheiden. Solange es fleischig ist. „Die Annäherung an einen Frack-Block mit einer ISO 40-Spindelmaschine wäre eine vergebliche Übung“, sagte er.
Quellen waren sich einig, dass Hochdruckkühlmittel für die Wärme- und Spanabfuhr in vielen Öl- und Gasanwendungen unerlässlich ist, oder wie Zimmerman von Iscar es ausdrückte, „fast unabhängig von der Anwendung. Beim Arbeiten tief in einer Bohrung an einem Flüssigkeitsende ist es wichtig, die Späne herauszuspülen, und dies ist schwierig. Ein kühlmittelgeführtes Fräswerkzeug ist bei solchen Anwendungen mit Abstand der richtige Weg.“
Wenn die Maschine also nicht mit dieser Fähigkeit ausgestattet ist, fügen Benutzer sie mit Einheiten von Anbietern wie ChipBLASTER hinzu. „Ich würde heute nicht einmal mehr daran denken, eine Fräsmaschine ohne Hochdruck-Kühlmittel durch die Spindel zu kaufen“, sagte Zimmerman. „Es ist ein Wendepunkt sowohl beim Fräsen als auch beim Bohren.“ Die einzige Ausnahme ist eine Situation, in der Sie das Kühlmittel nicht auf die Schneide richten können. In diesem Fall „arbeitet Kühlmittel manchmal gegen Sie und es ist besser, trocken zu bearbeiten, um thermische Risse an den Einsätzen zu vermeiden“, sagte er.
Deluca sagte, dass Werkzeugmaschinenhersteller auf diese Nachfrage reagiert haben, sodass er jetzt häufig Maschinen mit einer vom OEM gelieferten Pumpe findet, die 1.000 psi bei 20 gpm liefert. Ward sagte, Makinos T1 liefert 26 gpm bei 1.000 psi, während der T2 denselben Druck bei 53 gpm liefert.
Schneidwerkzeugfortschritte
Während Sie vielleicht gerne ein PS-starkes Monster für Ihre Fracking-Blöcke haben, sagte Deluca von Allied Machine, dass sie sich zunehmend der gegenteiligen Herausforderung gegenübersehen:der Notwendigkeit, große Löcher mit Maschinen zu bohren, die sich auf das Fräsen konzentrieren, wo die Spindeldrehzahlen höher sind, aber PS bei 40 PS maximal sind bis 50.
„Die Unternehmen, die diese Teile herstellen, sind normalerweise klein bis mittelgroß und in der Regel nicht auf die Herstellung von Frack-Blöcken spezialisiert“, sagte er. „Und viele Leute sind misstrauisch, sich auf diesen Markt zu konzentrieren und eine halbe Million Dollar für eine Maschine für eine Branche auszugeben, die wie eine Achterbahn läuft. Also mussten wir
ein Werkzeug entwickeln, das ein Loch mit 4″ Durchmesser bei viel höheren Spindeldrehzahlen und viel niedrigeren Vorschüben schneiden kann als unsere herkömmlichen Bohrprodukte.“
Die Herausforderung beim Bohren von Fracking-Blöcken geht über die Größe der erforderlichen Löcher hinaus. „Unterbrochene Schnitte sind der Fluid-Endblock-Fertigung inhärent, da die Querbohrungen senkrecht zu bestehenden Löchern gebohrt werden“, sagte Allied Machine’s Best. „Aufgrund der resultierenden Form der sich kreuzenden Löcher werden die Außenkanten des Bohrers weiterhin in den Schnitt eingreifen, während die Innenkante dies nicht tut. Dies kann den Bohrer destabilisieren, was das Werkzeug zerstören und die Integrität des Fracking-Blocks beschädigen kann.“
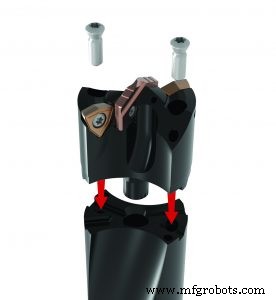
Auch wenn der Kunde durch die Verwendung von nicht wärmebehandeltem Material Einsparungen erzielt, kann der Bohrer erheblichen Abweichungen ausgesetzt sein. Deluca von Allied sagte normalerweise, dass ein Bediener den Prozess ständig überwachen muss oder innerhalb von Sekunden nach dem Auftreffen auf eine Tasche im Gussstück einen katastrophalen Bohrfehler riskieren muss, der ein Teil zerstören könnte, in das Sie Stunden investiert haben. Werkstätten erfahren auch Materialabweichungen von Block zu Block, was es schwierig macht, die perfekten Bohr- und Betriebsparameter auszuwählen.
Allied ist diesen Herausforderungen mit einem Tool der „nächsten Generation“ namens APX begegnet. Es verfügt über ein härteres Hartmetallsubstrat und eine proprietäre Beschichtung, um dem Schlag beim Schlagen in eine Tasche standzuhalten. „Sie könnten das Werkzeug abbrechen und quietschen“, sagte Deluca, „aber Sie können das Loch immer noch fertigstellen.“
Er fügte hinzu, dass Allied die Schwierigkeiten beim Bohren von Querbohrungen angegangen sei, indem dem Einsatz ein Abstreifer hinzugefügt wurde, um die Stabilität zu verbessern, sowie Verschleißpolster, um zusätzliche Stabilität zu bieten, wenn der Pilot in einen leeren Raum oder ein Querloch austritt. „Wir empfehlen auch, den Vorschub zu verringern und die gleiche Geschwindigkeit beim Bohren von abgewinkelten Austrittslöchern beizubehalten, damit das Werkzeug nicht abstoßen oder laufen möchte. Es ist normalerweise nicht notwendig, die Hauptlinie oder die Querlöcher zu bohren, aber es gibt nur so viel Technik, die Sie in ein Werkzeug stecken können, um den extrem unterbrochenen Schnitt der abgewinkelten Löcher zu kompensieren.“
Zum Fräsen, so Zimmerman, eignet sich die doppelseitige Wendeschneidplatte HeliDo H600 mit sechs Ecken von Iscar hervorragend für diese Art von Material. „Wir bieten auch den Mill 4 Feed an, eine quadratische, einseitige Wendeschneidplatte mit einer positiveren Geometrie für einen weicheren Schnitt, der weniger Leistung erfordert.“
Seine Hauptbotschaft ist, dass Iscar, da er sich seit langem in der Öl- und Gasindustrie engagiert und nur erfahrene Maschinisten einstellt, den optimalen Prozess für einen Kunden entwickeln und aus einer Vielzahl von Werkzeugen auswählen kann. „Wir haben viele Arten von Futtermühlen und können eine Futtermühle basierend auf der Anwendung, dem Material und der Maschine unter Berücksichtigung ihrer Steifigkeit, Leistung und ihres Drehmoments optimieren.“
Multitasking und Automatisierung
Es ist wahrscheinlich, dass 9.500-Pfund-Fracking-Blöcke einen nicht dazu bringen, an „Automatisierung“ zu denken, aber Makino und andere Bauherren bieten Lösungen an, die es einem Bediener ermöglichen, mehrere Maschinen zu betreiben. Bei Frack-Blöcken bedeutet das in der Regel einen rotierenden Palettenwechsler, der in weniger als einer Minute zwischen Rohguss und Fertigteil wechselt. Danach hat der Bediener ausreichend Zeit, das fertige Teil zu entnehmen.
Mit Taktzeiten von wenigen Minuten liegen Fracking Gun Tubes am anderen Ende des Spektrums. Und da es sich um „Einwegartikel“ handelt, sind die Produktionsraten astronomisch, sagt Vollmer. Tausende werden jeden Tag hergestellt.“
Dadurch eignet sich das Teil ideal für die Automatisierung, und Hartwig und Okuma haben zusammengearbeitet, um mehrere Optionen anzubieten. Dazu gehören Roboter zum Be- und Entladen und Stangenvorschubsysteme, wie sie für Kleinteile auf Drehmaschinen im Schweizer Stil verwendet werden, außer dass sie hier Durchmesser von 2 bis 4 Zoll handhaben. Der schnellste Ansatz führt das Material in eine Doppelspindelmaschine ein, bearbeitet ein Ende und führt das Teil dann direkt in die Nebenspindel ein, um das andere Ende zu bearbeiten.
Vollmer sagte, die Teile erforderten Drehen, Gewindeschneiden und etwas Fräsen, idealerweise mit angetriebenen Werkzeugen für letzteres, ein Merkmal, das Winkle als „eine der größten Veränderungen in der Branche in den letzten Jahren“ bezeichnete. Fracking und Directional Drilling sind wiederum ein wichtiger Grund für diesen Übergang.
Für viele der weitgehend zylindrischen Teile, die in den heutigen Bohrlochoperationen benötigt werden, hat die ideale Drehmaschine jedoch mehr als angetriebene Werkzeuge und einen oder zwei Revolverköpfe. Es verfügt über einen schwenkbaren Kopf und Mehrachsen-Fräsfunktionen wie die MULTUS-Mühl-Dreh-Serie von Okuma.
„Die Teile, die sowohl für das Bohren als auch für die Fertigstellungsphase benötigt werden, sind viel komplexer als bei herkömmlichen Vertikalbohrungen“, erklärte Winkle. „Sie müssen in der Lage sein, Ventile zu öffnen und zu schließen, um Produktionszonen zu wechseln. Teile sind mit hydraulischen Rohrleitungen sowie elektronischen Überwachungsgeräten ausgestattet.“
Dies erfordert Querbohrungen und kompliziert gefräste Merkmale am Außen- und Innendurchmesser, sodass die Maschinen eine Fünf-Achsen-Positionierung und etwa neun Achsen der Maschinenbewegung benötigen, um ein Teil an einem Ende zu schneiden und die Spindeln zu wechseln, um das andere zu bearbeiten.
Threads sind eine weitere Herausforderung. Winkle sagte, es gebe buchstäblich Hunderte von Typen und die Toleranzen seien eng:„Plus 1,5 Tausend, minus nichts.“ Denn in Öl und Gas halten Gewinde nicht nur Teile zusammen, „sie müssen perfekt abdichten und enormen Zugbelastungen durch die gigantische Kette von Teilen standhalten, die meilenweit tief in das Loch eindringen“, sagte Winkle. „Und sie müssen mit Wärmeausdehnung und Stoßbelastung fertig werden. Dieses abdichtende und tragende Bauteil gibt es in keiner anderen Branche.“
Das Schneiden dieser Fäden erfordert eine starre Maschine und eine Einrichtung, die Rattern widersteht. Kyle Downs, Direktor für Projektmanagement und Marketing bei SMW Autoblok, Wheeling, Illinois, sagte, dass dies alles durch die Tatsache erschwert wird, dass „eingehendes Material sehr uneinheitlich ist. Die Automatisierung der Zentrierung von Haken-, Bogen- und/oder Langrohren kann mit zwei Szenarien erreicht werden, entweder mit einem automatisch zentrierenden und ausgleichenden 3+3-Spannfutter oder mit einem ausgleichenden Spannfutter und einer am Reitstock montierten Zentrierlösung, die normalerweise auch ein Spannfutter ist .“
Schließlich fügt die Erweiterung der Metallabtragungsmaschinen um Laser-Metallabscheidung neue Möglichkeiten hinzu, wie die neue LASER EX-Serie von Okuma zeigt. Wenn Sie beispielsweise ein Teil mit nur wenigen hervorstehenden Features haben, können Sie diese Features zum Hauptkörper hinzufügen, anstatt die Features aus einem größeren Bestand herauszuschneiden. Das ist potenziell eine enorme Einsparung bei der Bearbeitungszeit.
Winkle fügte hinzu, dass man auch unterschiedliche Materialien verschmelzen kann, indem man beispielsweise Inconel und Edelstahl kombiniert, was „mit rein subtraktiver Technologie niemals möglich ist. Die Verbindung ist so stark oder fester, als wenn sie aus dem Vollen gefräst wäre“, sagte er.
Das hat in der Öl- und Gasindustrie ein unmittelbares Potenzial, um die Verschleißpolster hinzuzufügen, die für Bohrbaugruppen benötigt werden, oder um die Seitenrippen hinzuzufügen, die verwendet werden, um zu verhindern, dass das Rohr den Innendurchmesser einer Bohrlochverrohrung kratzt, wenn es sich durch eine Biegung in einem gerichteten Bohrloch bewegt. Okuma bietet auch die Möglichkeit, eine Materialzone bis zu etwa 50 Rockwell unter Verwendung desselben Lasers mit einer anderen Apertur zu einsatzhärten.
Automatisierungssteuerung System
- Neue Zertifizierung für die Lubrication Elite
- Plädoyer für neuromorphe Chips für KI-Computing
- Intelligente Fertigung für die neue Normalität überdenken
- Wenn Daten das neue Öl sind, wer ist dann Ihre Raffinerie?
- Für Lieferketten ist das Kundenerlebnis das neue Unterscheidungsmerkmal
- Zukunftssichere Lieferkette für die neue Normalität
- Die Pandemie treibt ein neues Modell für die Entscheidungsfindung in der Lieferkette
- Die neue Welle von Herausforderungen für Hersteller von Industrieanlagen
- Die 5 besten Stromag-Teile für Ihre Bohrinsel
- Die richtigen Maschinenteile finden:Ratschläge für Ingenieure