Optimierung der Aluminiumbearbeitung in der Automobilindustrie
Mit dem Automobilsektor Durch die zunehmende Verwendung von Motor-, Antriebsstrang-, Wasserpumpen- und Bremssystemteilen aus Aluminium besteht die Herausforderung für OEMs und ihre Lieferkettenpartner darin, produktivere Fräsvorgänge zu liefern. Die Werkzeugauswahl ist der Schlüssel zu einer echten Marktdifferenzierung in diesem Segment, in dem sich die korrekte Anwendung optimierter Fräser über den gesamten Bereich der Bearbeitung von Motorkomponenten hinweg erheblich auszahlen kann.
Im Jahresvergleich steigt die Zahl der produzierten Aluminiummotoren sowohl für herkömmliche als auch für Hybrid-Personenwagen weiter an. Tatsächlich werden jetzt jedes Jahr fast 100 Millionen hergestellt. Diese Motoren enthalten Teile, die oft eine komplexe Form haben und nach dem Gießen eine Reihe von verschiedenen, aber wesentlichen Fräsvorgängen erfordern.
Sandvik Coromant hat jetzt ein komplettes Angebot für die Bearbeitung von Aluminium in der Automobilindustrie, von der ersten Stufe des Cubings über das Schruppen, Vorschlichten und Schlichten. Jedes konstruierte Fräswerkzeug, insgesamt fünf, ist darauf ausgelegt, optimierte Qualität und Kosten pro Teil zu liefern. Um Letzteres zu erreichen, erfüllen bestimmte Werkzeuge des Sortiments eine Kombination von Aufgaben, z. B. das Schruppen und Schlichten in einem einzigen Arbeitsgang, um die Zykluszeiten zu verkürzen.
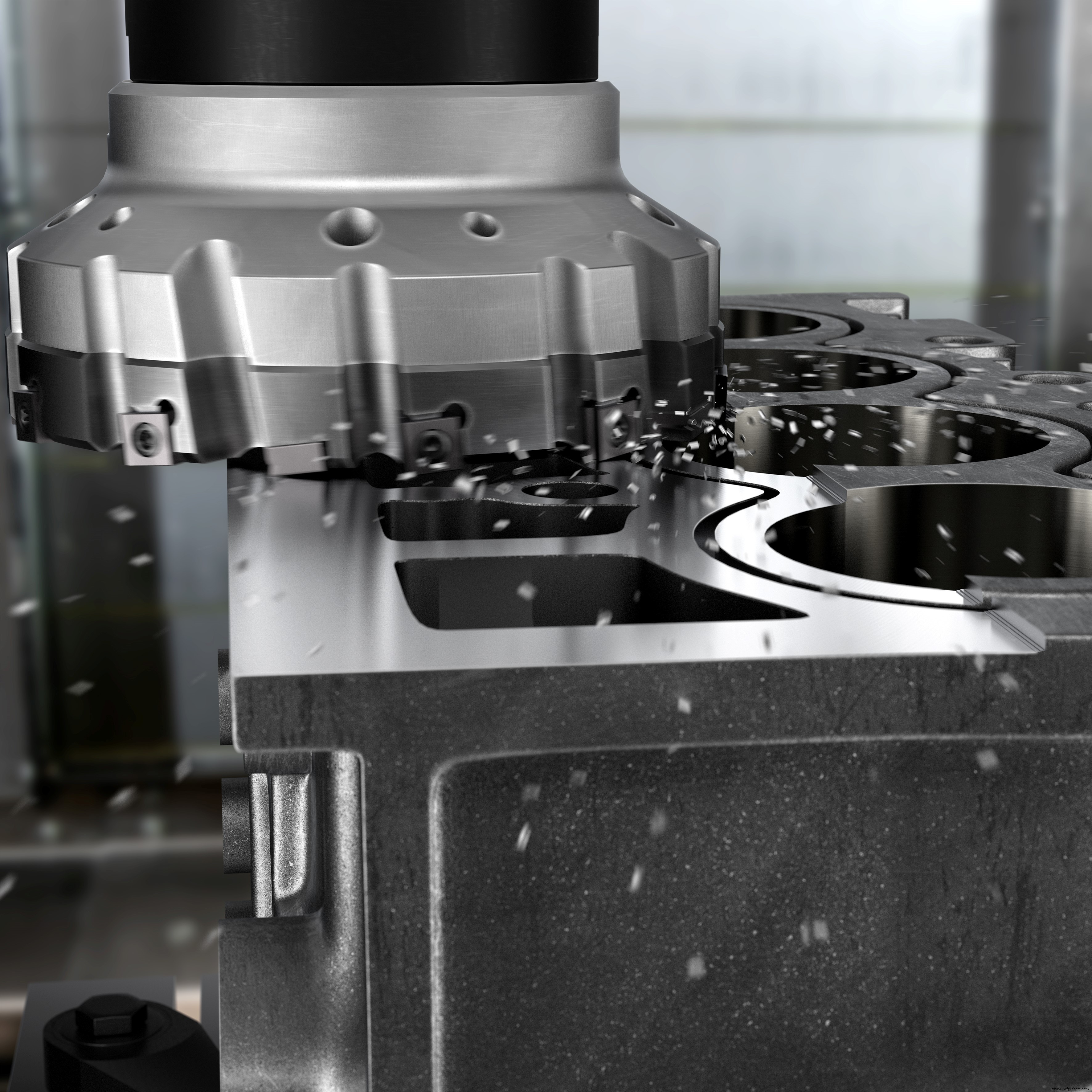
Ein typisches Beispiel ist der M5C90, ein innovativer Fräser, der Schruppen und Halbschlichten in einem Werkzeug. Das M5C90 ist ein Hochgeschwindigkeits-Planfräswerkzeug, das speziell angefertigt wird, um lange Rüstzeiten beim Kunden zu vermeiden. M5C90 arbeitet mit einer reduzierten Anzahl von Zähnen im Vergleich zu herkömmlichen Fräsern, hauptsächlich als Ergebnis der einzigartigen radialen und axialen Positionierung der Wendeschneidplatte auf der Abschlussreihe/dem Innendurchmesser (keine Wendeschneidplatteneinstellung erforderlich). Diese Positionierung gewährleistet gratfreies Fräsen und optimale Oberflächengüte an Zylinderköpfen, Zylinderblöcken, Bremssystemteilen und allen Aluminiumkomponenten, bei denen ein breiter Fräsereingriff erreicht werden kann (gilt nicht für dünnwandige Teile).
Um ein Beispiel für die potenziellen Vorteile zu geben, die sich durch die Verwendung des M5C90 bieten, betrachten Sie einen laufenden Kundenfallversuch mit einem Gehäuseventil eines Bremssystems aus AlSi12Cu1. Mit einer Außendurchmesseranordnung von 10 Hartmetalleinsätzen und einem Innendurchmesser von vier Einsätzen (plus einem Wiper-Einsatz) wird das Werkzeug mit einer Spindeldrehzahl von 8000 U/min und einer Schnittgeschwindigkeit von 4021 m/min eingesetzt. (13.192 ft./min.) und einem Vorschub von 0,25 mm/Zahn (0,009 Zoll/Zahn). Außerdem beträgt die axiale Schnitttiefe 2 mm (0,078 Zoll) bei einer radialen Schnitttiefe von 140 mm (5,51 Zoll), was eine Metallabtragungsrate von 5600 cm 3 ergibt /Mindest. (342 Zoll. 3 /Mindest.). Obwohl die Gesamtlebensdauer des Werkzeugs noch ermittelt werden muss, befindet sich dasselbe Werkzeug nach 18 Monaten Betrieb immer noch in der Maschine.
Für diejenigen, die einen Fräser benötigen, der auch dünnwandige Aluminiumteile wie Getriebegehäuse und Gehäuse fertigstellen kann, hat Sandvik Coromant einen weiteren Fräser, der ebenso effektiv ist, den M5F90. Der M5F90 ist ein weiteres One-Shot-Schrupp- und Schlichtwerkzeug. Der Fräserkörper (25-80 mm, 0,98-3,15 Zoll Durchmesser) ist für die Bearbeitung von dünnwandigen Aluminiumteilen und Senkoperationen bestimmt und enthält gelötete PKD-Spitzen. Jede Spitze enthält sowohl eine Schruppkante als auch eine Schlichtkante. Der Schruppbereich arbeitet wie ein konventionelles Fräswerkzeug, alle Schneiden auf gleichem Durchmesser und gleicher Höhe, während der Schlichtbereich aus radial und axial abgesetzten Schneiden besteht. Dieses Konzept ermöglicht eine enge Teilung für eine gratfreie Bearbeitung und eine hervorragende Oberflächengüte. In dem kurzen Video unten zeigt Sandvik die Fräser der M5-Serie für die Aluminiumbearbeitung in der Automobilindustrie.
Beeindruckende Zeiteinsparungen sind möglich, wie in einem Kundenfallversuch gezeigt wurde, bei dem es um das Planfräsen eines Zylinderkopfs aus Aluminium (mit hohem Si-Gehalt) ging. Hier führte die Verwendung von M5F90 gegenüber einem speziellen PKD-Fräser eines Mitbewerbers nicht nur zu einer Einsparung von 150 % Zykluszeit, sondern eliminierte auch die Gratbildung. Enthaltene Schnittdaten:15.915 U/min Spindeldrehzahl; 2000 m/Min. (6562 ft./min.) Schnittgeschwindigkeit; eine Vorschubgeschwindigkeit von 0,16 mm/Zahn (0,006 Zoll/Zahn); und 1,5 mm (0,06 Zoll) Schnitttiefe.
In einem weiteren M5F90-Beispiel wurden Zykluszeitverkürzungen von 44 % bei einem Aluminium-Kettenkasten im Vergleich zur Verwendung eines Wendeschneidplattenfräsers mit 63 mm (2,48 Zoll) Durchmesser und sechs PKD-Wendeschneidplatten eines Mitbewerbers erzielt. Darüber hinaus wurde durch die Lösung ein zuvor erforderlicher Entgratungsvorgang mit einer Bürste eliminiert.
Ein weiteres neu entwickeltes Werkzeug ist das M610, das zum Fräsen der Deckfläche/Oberseite von Motorzylinderblöcken mit Bimetall-Grenzflächen, typischerweise Aluminium und Grauguss (CGI), entwickelt wurde.
Eine Reihe von thermischen und mechanischen Eigenschaften sorgt für eine anspruchsvolle Bearbeitung, wenn es um Bimetallmaterialien geht. Vorhandene Fräser für diese Anwendung sind komplex und müssen eingestellt werden, was zu beeinträchtigten Durchsatzraten führt. Außerdem verursachen solche Werkzeuge häufig Absplitterungen an den GCI-Teilen des Bauteils.
Im Gegensatz dazu erfordert M610 keine Einrichtung und keine Anpassung und bietet die Möglichkeit, hohe Vorschubgeschwindigkeiten ohne Absplittern, Graten oder Verkratzen von Teilen zu erreichen. Diese Fähigkeit ist wichtig, da Oberflächenfehler das Potenzial haben, Leckagen zwischen dem Zylinderblock und dem Kopf zu erzeugen, was wiederum Leistung und Leistung beeinträchtigt. Einige globale Automobil-OEMs profitieren bereits von der Einführung von M610.
Um auf einen bestimmten Kunden hinzuweisen, wurde beim Endbearbeiten der Verbrennungsfläche von Bimetall-Motorblöcken ein enormer Wettbewerbsgewinn erzielt. Im Vergleich mit dem einstellbaren Fräser mit Kassetten eines Mitbewerbers erzielte der M610 eine Standzeitverbesserung von 833 % und fertigte mehr als 4000 Teile im Vergleich zum Fräser 480 des Mitbewerbers. Darüber hinaus arbeitete der M610 mit der 10-fachen Geschwindigkeit. Schnittdaten für die 15-schneidige M610 inklusive:3000 m/min. (9843 ft./min.) Schnittgeschwindigkeit; eine Vorschubgeschwindigkeit von 5720 mm/min. (225 Zoll/Min.); eine Spindeldrehzahl von 3820 U/min; eine Vorschubgeschwindigkeit von 0,15 mm/Zahn (0,006 Zoll/Zahn); und eine Schnitttiefe bei Aluminium von 0,5 mm (0,02 Zoll) und bei Gusseisen von 0,05 mm (0,002 Zoll).
Zu den weiteren Werkzeugen der Familie gehört der tangentiale Schruppfräser M5Q90, der das Würfeln in der ersten Stufe (erste Bearbeitung der Flächen nach dem Gießen) in einem einzigen Arbeitsgang ohne Gratbildung durchführt. Das Werkzeug ist mit tangentialen PKD-Wendeschneidplatten ausgestattet, die für einen glatten und stabilen Schneidvorgang sorgen, um den Stromverbrauch zu reduzieren und Vibrationen zu eliminieren.
Zylinderköpfe und -blöcke aus Aluminium gehören zu den Komponenten, die vom M5Q90 profitieren. Beispielsweise würde der Cubing-Vorgang an einem gegossenen Zylinderkopf typischerweise die Bearbeitung der Nockenwellenfläche, der Einlass-/Auslassfläche und der Verbrennungsfläche umfassen. In einer Kundenfallstudie lieferte das grobe Planfräsen von Zylinderköpfen, die aus einer AS-9-Aluminiumlegierung gegossen wurden, auf einem horizontalen Bearbeitungszentrum äußerst beeindruckende Ergebnisse für die Standzeit. Bei 3000m/min. (9843 Zoll/min.) Schnittgeschwindigkeit, Vorschub pro Zahn von 0,2 mm (0,008 Zoll) und 2,0 mm (0,079 Zoll) axiale Schnitttiefe (vollständiger Eingriff bis 40 mm (1,57 Zoll), mehr als 10.000 Komponenten wurden abgeschlossen.
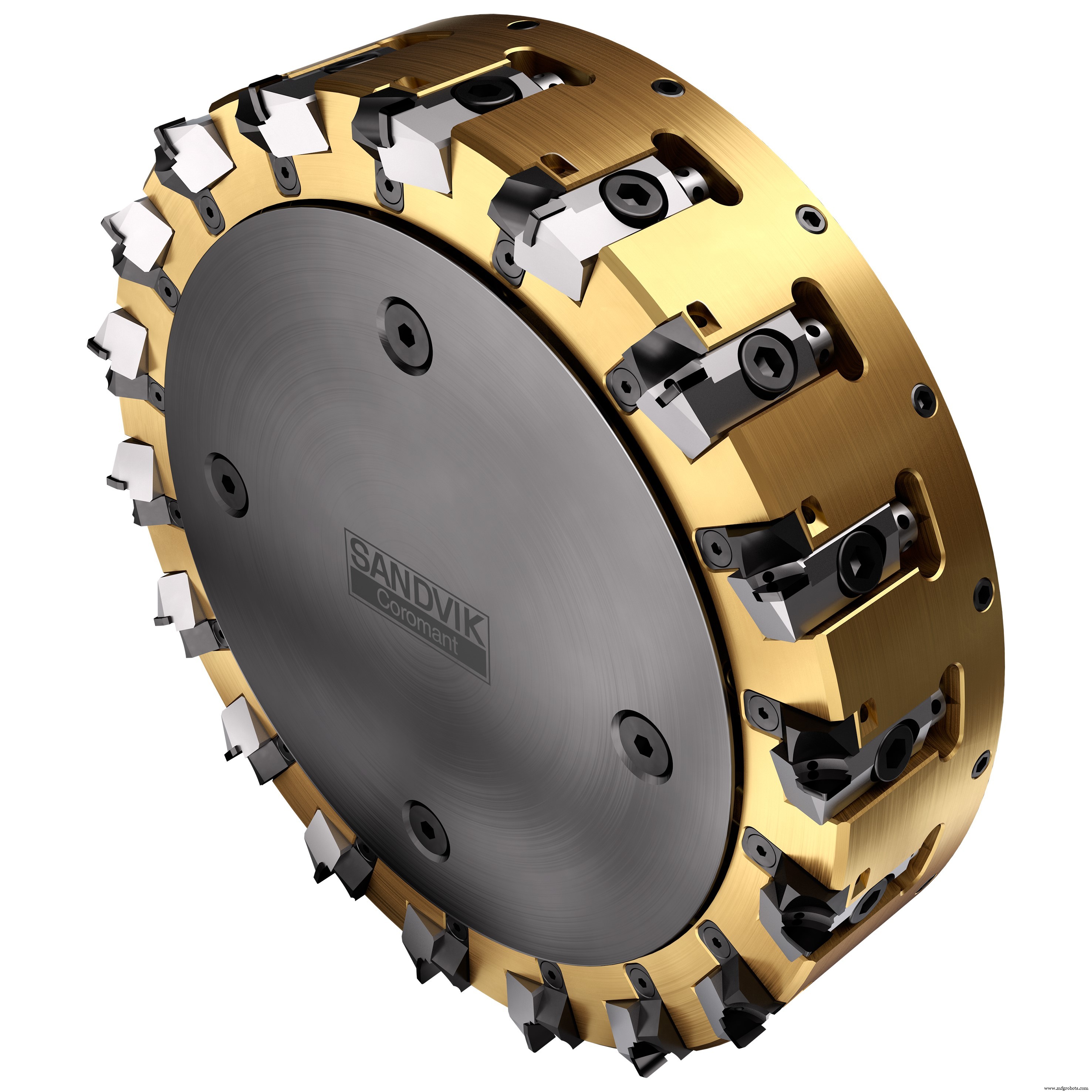
Ein weiteres Werkzeug ist das M5R90 zum Schruppen/Halbschlichten in der zweiten Stufe. Dieser Standardschneider arbeitet mit einstellbaren Kassetten und unterstützt eine Schnitttiefe von bis zu 8 mm (0,315 Zoll) mit einem Radius von 0,4 oder 0,8 mm (0,016 oder 0,031 Zoll), je nach verwendeter Kassette. Einfach einstellbare Patronen sind in vielen Automobilanwendungen von Vorteil, wie in einem kürzlich durchgeführten Kundenversuch zum Planfräsen einer Motorabdeckung gezeigt werden konnte. Der M5R90, der aus der MRHB-Si12-Aluminiumlegierung gegossen wurde, schnitt gegenüber dem etablierten Konkurrenzschneider äußerst positiv ab. Basierend auf identischen Schnittdaten verlängerte die M5R90 die Standzeit von 8.000 auf 10.000 Werkstücke. Darüber hinaus musste der Fräser des Wettbewerbers nach jeweils 1000 Teilen eingestellt werden, da sich die Kartusche bewegte und die Oberflächengüte beeinträchtigte. Im Gegensatz dazu produzierte der M5R90 8000 Teile, bevor eine Anpassung an der Kartusche erforderlich war.
Zur Familie gehört auch der Superschlicht-Planfräser M5B90 mit seiner einzigartigen axialen und radialen Positionierung der Wendeschneidplatten. Diese Konfiguration sorgt zusammen mit der Wiper-Wendeplatte für einen gratfreien Schnitt mit hervorragender Oberflächenqualität, wie kürzlich ein Hersteller von Pkw-Zylinderköpfen feststellen musste. Das Unternehmen hatte Prozessinstabilität und Probleme mit Graten, während ein weiteres Problem die unvorhersehbare Einsatzlebensdauer war, die von Kartuscheneinstellungen abhing, die sich von Einrichtung zu Einrichtung unterschieden. Der Wechsel zum M5B90-Fräser sorgte für einen reibungslosen Endbearbeitungsvorgang mit vorhersehbarem Verschleiß und ohne Grat. Das Werkzeug produziert nur sehr dünne Späne, die während des Schneidvorgangs leicht entfernt werden können, um eine Beschädigung der Bauteiloberfläche zu vermeiden. Darüber hinaus verlängerte der Wechsel zu M5B90 die Standzeit der Werkzeuge von durchschnittlich 30.000 auf 45.000 Teile.
CoroDrill ® und CoroTap ® Die Bohr- und Gewindewerkzeuge der Familie können Kunden auch als Teil der gleichen Lösungsfamilie für die Bearbeitung von Aluminium-Automobilkomponenten angeboten werden, ebenso wie der standardmäßige CoroMill ® Century 590 Planfräser Schlichtfräser.
In allen Fällen ist das Potenzial zur Reduzierung von Zykluszeiten und Kosten pro Teil bei gleichzeitiger Verbesserung der Werkzeuglebensdauer und -qualität sehr real, wie die beschriebenen Kundenfallbeispiele zeigen. In der Automobilindustrie, wo Massenproduktionen vorherrschen, kann selbst eine kleine Einsparung bei der Zykluszeit zu erheblichen finanziellen Erträgen führen. Vor diesem Hintergrund ist jede Technologie, die die Fähigkeit zur Erzielung größerer Gewinne nachweisen kann, schwer zu ignorieren.
Industrietechnik
- Der Wert der additiven Fertigung in der Automobilindustrie
- Wie verändert der 3D-Druck die Automobilindustrie? (2021)
- Wie 3D-Druck den Wandel in der Automobilindustrie vorantreibt
- Wie die Automobillogistikbranche mit COVID-19 konfrontiert ist
- Wie die IoT-Technologie den Betrieb in der Automobilindustrie überwacht
- NADCAP-Zertifizierung und ihre Anwendung auf die Präzisionsbearbeitungsindustrie
- CNC-Bearbeitung in der Automobilindustrie
- Wie Aluminium in der Schifffahrtsindustrie verwendet wird
- Die Bearbeitungseigenschaften von 6061 Aluminiumsorten
- Bearbeitung von Messing vs. Aluminium:Der Vorteil der Tradition