Fallstudie:Für den Erfolg nutzt Mikromechanik einen vollständigen Systemansatz
Um die nächste Produktivitätsstufe zu erreichen, geht es nicht um die Integration einzelner Produkte, sondern um die Integration kompletter Systeme, die zusammenarbeiten, um Herstellern zu helfen, höhere Effizienz zu erzielen. Bei Micro-Mechanics haben sie genau das getan, um die Produktivität, Rentabilität und einen globalen Wettbewerbsvorteil zu steigern.
Micro-Mechanics entwickelt, fertigt und vermarktet hochpräzise Teile und Werkzeuge, die in prozesskritischen Anwendungen für die Halbleiter- und Luft- und Raumfahrtindustrie eingesetzt werden. Ihr CEO, Chris Borch, glaubt an das, was er die „Wissenschaft der maschinellen Bearbeitung“ nennt. Er beschloss, unseren Anspruch auf die Probe zu stellen. Im wahrsten Sinne des Wortes.
Eine proaktive, wissenschaftliche Suche nach Exzellenz
Laut ihrer Website besteht die Mission des Unternehmens darin, seinen Kunden „perfekte Teile und Werkzeuge, pünktlich, jedes Mal“ bereitzustellen, basierend auf skalierbaren, wiederholbaren und kostengünstigen Herstellungsprozessen. Ihre Strategie, um diese Mission zu erfüllen, besteht darin, „unermüdlich Produkt- und Betriebsverbesserungen zu verfolgen“. So kamen sie zu HAIMER.
Wie alles begann
Vor sechs Jahren zeigte eine interne Studie des gesamten Bearbeitungsprozesses, dass das Einrichten und Kalibrieren der Werkzeuge den größten Teil der bearbeitungsfreien Zeit in Anspruch nahm. Mikromechanik stellt sehr komplexe Teile mit vielen Merkmalen her, für deren Fertigstellung bis zu 70 Werkzeuge pro Teil erforderlich sind. Die meisten sind kleine Läufe. Bei durchschnittlich bis zu 10 Minuten pro Werkzeugeinstellung verbrachte das Unternehmen oft bis zu acht Stunden damit, Werkzeugbaugruppen zu laden und für die Bearbeitung vorzubereiten.
Es lag nahe, dass die Eliminierung von Werkzeugabweichungen und die Offline-Verlegung so vieler Rüstvorgänge wie möglich die Maschinenlaufzeit drastisch verbessern würden.
Um zu sehen, ob die neueste Werkzeughaltetechnologie eine Lösung bieten könnte, wurde ein Fact-Finding-Team nach Deutschland geschickt, um verschiedene Werke zu besuchen und eine umfassende Marktstudie zu erstellen. HAIMER stieg schnell an die Spitze der potenziellen Technologieunternehmen, die ihnen helfen könnten, zum Teil, weil ihre Lösungsplattform aus einem ganzen System von Produkten bestand, die nahtlos zusammenarbeiteten, um genau die Probleme zu lösen, die Micro-Mechanics angehen wollte.
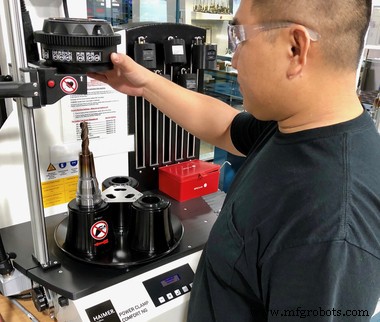
Die HAIMER Full Process Testlinie
Im Gegensatz zu vielen Situationen, in denen HAIMER Kunden bei einem bestimmten Problem hilft und diese dann nach und nach eines oder mehrere unserer Produkte übernehmen, ergriff Chris Borch die mutige Maßnahme, eine brandneue Engineering-Linie im kalifornischen Werk des Unternehmens aufzubauen, um speziell das komplette HAIMER-Werkzeugmaschinenzubehör zu testen Lösung.
„Wir stellten fest, dass es schwierig sein würde, alte und neue Geräte zu mischen und gute Daten zu sammeln“, sagte er. „Wir haben mit drei brandneuen CNC-Maschinen mit jeweils 300 Werkzeugen, die alle HAIMER-Werkzeugaufnahmen enthalten, neu gestartet.“ Alle Werkzeugbaugruppen wurden von Ingenieuren modelliert und von einem Techniker auf HAIMER Einstell- und Auswuchtgeräten zertifiziert, bevor sie an die Maschinen gingen.
Schrumpfanpassung für exzellente Baseline
Die Mikromechanik hat bereits Schrumpfsitz-Werkzeughalter als primäre technologische Lösung erkannt. Da es keine beweglichen oder verschleißenden Teile gibt, die potenzielle Abweichungen bei der Bearbeitung schaffen könnten, erfüllt es das Ziel des Unternehmens, perfekte Teile zu liefern, da es in der Lage ist, wiederholbare Rundlaufgenauigkeit, Auswuchtgenauigkeit und Greifmoment aufrechtzuerhalten.
Wiederholbarkeit
Konstante Qualität war entscheidend. „Mit einem Koordinatenmessgerät (CMM) erkennen wir geprüfte Proben, die vom Band kommen“, erklärt Borch. „Die Ergebnisse zeigten eine hervorragende Qualität.“ Es wurde festgestellt, dass die Teile bei Cpk 1,33 halten (ungefähr 63 Ausschuss pro Million produzierter Teile). Das bedeutet, dass das Unternehmen von Charge zu Charge eine Teilequote von 99,99 % innerhalb der Toleranzen hielt.
Mit anderen Worten – es fanden, wenn überhaupt, nur sehr wenige Mängel den Weg zum Kunden. „Genau das ist unser Leitbild“, sagte Borch. Außerdem blieb der Abfallbehälter leer und kostspielige Nacharbeiten wurden praktisch eliminiert.
Genauigkeit
Der Wechsel von einer CAT- zu einer HSK-Spindelschnittstelle war eine entscheidende Änderung, die zur Verbesserung der Z-Höhengenauigkeit beitrug. Eine weitere Änderung war der Umstieg von einem älteren Werkzeugvoreinstellgerät auf die neue Microset-Linie von HAIMER. Vor der Umstellung lag die Genauigkeit bestenfalls zwischen 5 und 10 Mikrometer für ein bestimmtes Teil, was zusätzliches Basteln und Zeit zur Verbesserung bedeutete. Das HAIMER Einstellgerät erreichte eine Genauigkeit von +/- 2 Mikron. Dieses Maß an Präzision ermöglicht es Micro-Mechanics, direkt von der Voreinstellung zur Maschine zu wechseln, ohne weitere Anpassungen vorzunehmen, und während die Genauigkeit des Teils innerhalb von 10 Mikrometern oder weniger bleibt.
Guthaben
Mit den Vorteilen von HAIMER Werkzeughaltern, Schrumpfsitzen und Voreinstellgeräten entschied sich Micro-Mechanics für 100%ige Sicherheit durch den Einsatz von HAIMER Auswuchtgeräten. „Wir wussten aus Erfahrung, dass unsere alten Weldon-Aufnahmen und Spannzangen unwuchtig waren“, erklärt Borch. „Und obwohl die HAIMER-Schrumpfpassung nahezu perfekt ist, können wir sie nicht immer verwenden, und selbst wenn, möchten wir zu 100 % wissen, wie der Gleichgewichtszustand der Baugruppe ist.“ Durch den Wechsel zu HAIMER und der Einrichtung der Waagenprüfung konnte das Unternehmen eine um 70-80 % höhere Standzeit feststellen.
Einrichtungszeit
Die Auswirkungen der Offline-Werkzeugeinstellung waren tiefgreifend, da bei jedem Werkzeugwechsel die besten Verfahren zum Schrumpfen, Voreinstellen und Auswuchten eingeführt wurden. Der gesamte Einrichtungsprozess, der früher bis zu acht Stunden dauerte, wurde jetzt auf 5 Minuten reduziert! „Wir konnten den Unterschied sofort sehen“, sagte Borch. Und die Wiederholbarkeit der Leistung ist für jede Werkzeugbaugruppe konsistent.
100 % HAIMER weltweit
Micro-Mechanics bedient einen weltweiten Kundenstamm aus fünf Produktionsstätten in Asien und den USA. Als Ergebnis des Erfolgs der HAIMER-Engineering-Linie hat Micro-Mechanics sie auf der Fertigungslinie repliziert, nicht nur in Kalifornien, sondern in ihren anderen vier Werken weltweit. Die gesamte Organisation hat das komplette HAIMER Werkzeugsystem in ihre Standardarbeitsabläufe eingebaut. Das ist eine ziemliche Bestätigung!
Wie es funktioniert
Ingenieure modellieren jede Werkzeugbaugruppe, komplett mit Attributen wie Versatzhöhen und Ausgleichstoleranzen. Anschließend baut es ein Techniker im Werkzeugbau über HAIMER Schrumpfaufnahmen auf, die Abweichungen zwischen Werkzeugwechseln eliminieren. Anschließend werden diese Eigenschaften von HAIMER Einstell- und Auswuchtmaschinentechnik zertifiziert. „Die Geometrie ist perfekt auf dem Computermodell und mit HAIMER Toolholding Best Practices; Es gibt nur sehr wenige Abweichungen zwischen dem, was auf dem Bildschirm angezeigt wird, und der Werkzeugbaugruppe, die an die Maschine geliefert wird.“
„Wir haben langwierige einmalige Anpassungen an der Linie eliminiert. Wir nehmen in der Regel keine Anpassungen mehr vor, bis das Werkzeug abgenutzt ist. Es wird erst ausgetauscht, wenn es die vorgegebene Lebensdauer erreicht hat, die wir über RFID-Chips in den Haltern selbst verfolgen.“
Industrie 4.0 – Intelligent laufen
Von der Schrumpfpassung über die Installation von RFID-Chips bis hin zum Einstellen und Auswuchten bietet HAIMER die Lösung und das Know-how, um Hersteller beim Übergang in die Arena von Industrie 4.0 zu unterstützen. „Die Woche hat 168 Stunden, und unser Ziel war es, sie alle zu nutzen. Aus unserem Engagement für HAIMER-Produkte geht hervor, dass wir glauben, dass sie uns dabei helfen, dies zu erreichen und uns einen Wettbewerbsvorteil verschaffen“, so Borch abschließend.
Zuvor in Haimers Blog vorgestellt .
Industrietechnik
- Speicher mit beweglichen Teilen:„Antriebe“
- Aufbau eines Business Case für das Manufacturing Execution System in der additiven Fertigung
- Was ist der Business Case für das Additive Manufacturing Execution System in der Ersatzteilproduktion?
- Formnext 2017 Rückblick:Ein fulminanter Erfolg für die Welt des 3D-Drucks
- Ein moderner Ansatz zur Ausbildung moderner Arbeitskräfte
- Ein Fall für die Aufrüstung alternder Lkw
- Passivierung für Edelstahlteile und Gehäuse
- Fallstudie:Steigerung der termingerechten Produktivität der maschinellen Bearbeitung durch das HAIMER Schrumpfsystem
- Der Fall für den 3D-Druck in der Fertigung
- Eine Fallstudie zu Präzisionstrennen vs. Stanzen