7 Lagerprozesse und wie man sie optimiert
Jedes Warenlager, Vertriebszentrum oder Fulfillment-Center muss einen konstanten Bestandsfluss in und aus der Einrichtung verwalten. Die Technologie hat diesen Prozess mit zentralisierten Plattformen wie einem Warehouse Management System (WMS) erheblich vereinfacht. Diese Softwareprogramme können mit Sensoren, Scannern und Barcodes verbunden werden, um eine digitale und automatisierte Arbeitsumgebung zu schaffen.
Um den Bestandsfluss zu optimieren, müssen Lagerverwalter die Arbeitsverteilung in bestimmte Schritte unterteilen. In diesem Beitrag werden wir die sieben Hauptprozesse in einem Lager betrachten und erörtern, wie jeder von ihnen optimiert werden kann. Durch die Betrachtung des gesamten Systems lassen sich wichtige Schritte identifizieren, die optimiert werden können, um das Lager effizienter zu machen. Das ultimative Ziel eines jeden Verbesserungsplans sollte die Verbesserung der Bestandsgenauigkeit, der Genauigkeit von Bedarfsprognosen und anderer wichtiger Standortmetriken sein.
1. Empfangen
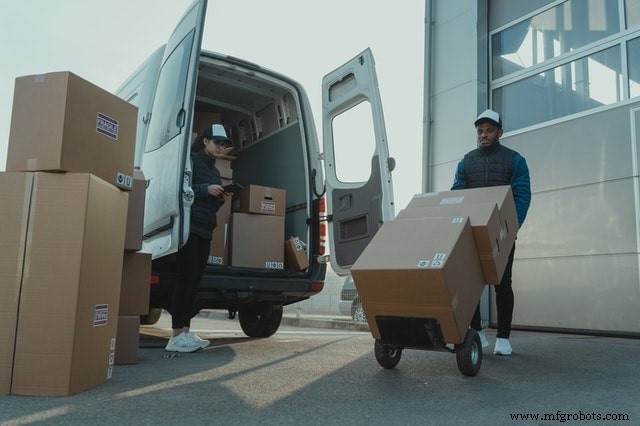
Der Empfangsprozess ist in einer Lagerumgebung von entscheidender Bedeutung, da er das Tempo für alle anderen Aktivitäten innerhalb der Einrichtung vorgibt. Ein effizienter Betrieb sollte einen gut organisierten Empfangsbereich haben, um eine unnötige Häufung von Lieferungen zu vermeiden. Zur Optimierung der Empfangsaktivitäten kann es vorteilhaft sein, Förderbänder und andere Formen automatisierter Handhabungsgeräte zu installieren.
Handhabungsgeräte können besonders hilfreich sein, wenn zwischen dem Wareneingangsbereich und anderen Orten für die Bereitstellung und Lagerhaltung viel Platz vorhanden ist. Empfehlenswert ist auch die Automatisierung des Wareneingangs durch Barcodes, die jederzeit schnell gescannt werden können. Eine weitere bewährte Methode besteht darin, Advanced Shipping Notices (ASNs) mit Ihren Lieferanten zu verfolgen, die nach Erhalt gescannt werden können, um Artikel schnell dem Bestand hinzuzufügen.
2. Einlagerung
Der nächste Prozess in einem typischen Lagerablauf ist die Einlagerung, wenn Waren vom Wareneingang in die Lagerbereiche bewegt werden. Eine der wichtigsten Überlegungen bei der Bestandsverwaltung ist die Auswahl der richtigen Lagerorte. Um den Einlagerungsprozess schnell und effizient zu gestalten, ist es wichtig, Lagerorte im Voraus zu definieren und klare Fahrwege für Personen und Gabelstapler innerhalb des Lagers zu schaffen.
Diese Standorte können mit Lagerbodenetiketten, retroreflektierenden Lagerschildern und -etiketten, hängenden Lagerschildern und Lagergangschildern gekennzeichnet werden, die gut sichtbar und/oder aus größerer Entfernung, z. B. mit einem Gabelstapler, scannbar sind, damit Arbeiter sie schnell finden können die richtigen Lagerorte für Einlagerungsaufgaben. Paletten-Barcode-Etiketten und -Anhänger sowie Barcode-Etiketten für Mehrwegbehälter, Tabletts und Behälter können auch Lagerarbeitern dabei helfen, den Bestand in den entsprechenden Lagerbereichen zu organisieren. Eine WMS-Plattform kann beim Zuweisen von Inventarstandorten und beim Scannen von Artikeln in und aus dem Lager enorm helfen.
3. Speicher
Um Lagerorte in einer Fabrik richtig zu planen, muss das Layout sorgfältig überlegt werden, um die Menge an nutzbarem Platz zu maximieren. Der spezifische Organisationsplan für jedes Lager ist einzigartig und basiert auf den Geschäftsanforderungen, der Einrichtungsstruktur und den verwendeten Systemen vor Ort.
Eine der besten Möglichkeiten zur Optimierung der Lagerung besteht darin, klare Metriken zu definieren, die die Auslastung und Effizienz für verschiedene Arten von Waren verfolgen können. Dies wird dabei helfen, Verbesserungen zu identifizieren, wie z. B. die Verlagerung von langsam drehendem Inventar an einen Lagerort, der abseits von stark befahrenen Fahrspuren positioniert ist.
4. Kommissionierung
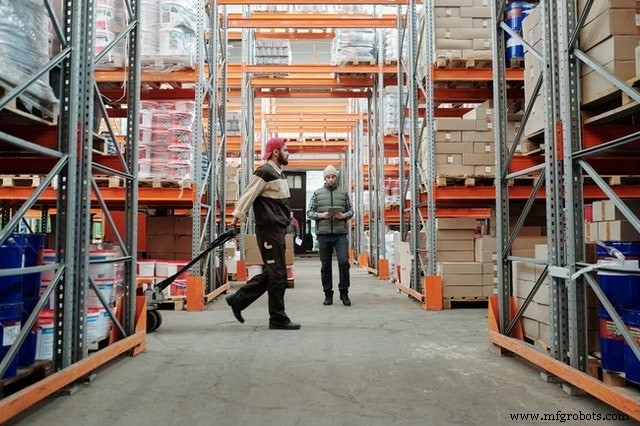
Die Kommissionierung ist ein notwendiger Prozess in jedem Lager, um Waren auszuwählen, die zur Erfüllung von Bestellungen versandt werden müssen. Kommissionierungsaufgaben kosten viel Zeit und Kosten und sind einer der wichtigsten Schritte zur Optimierung. Ein effizienter Kommissionierprozess muss heute durch Technologie ermöglicht werden.
Während viele Kommissionierungsmethoden eingesetzt werden können, ermöglichen Ihnen Lagerregaletiketten, die in ein Softwaresystem integriert sind, die Effizienz über mehrere einzelne Schritte hinweg zu verfolgen und Wege zu finden, um weitere Verbesserungen voranzutreiben. Kühlregaletiketten und Kühlregalplakate ermöglichen die Kennzeichnung von Lagerregalen auch in klimatisierten Lagerbereichen. Das Verständnis der Genauigkeit der Kommissionierung in Ihrem Lager kann auch bei Entscheidungen bezüglich Anpassungen der Kommissionierstrategie und der Anforderungen für einzelne Bestellungen hilfreich sein.
5. Verpackung
Wenn ein Verkaufsauftrag im Lager eingeht und die Artikel kommissioniert wurden, müssen sie verpackt und für den Versand vorbereitet werden. Die Optimierung für diesen Prozess umfasst häufig die Rationalisierung von Verpackungsmaterialien und die Erhöhung der Inspektionsgeschwindigkeit. Es ist auch wichtig, dass jeder Artikel innerhalb des Lagers eine vollständige Kontrollkette hat, damit die Bewegung zurückverfolgt werden kann, wenn ein Problem festgestellt wird.
6. Versand
Der Versand- oder Versandprozess ist der letzte Schritt, bevor Artikel das Lager verlassen. Um Verzögerungen an den Laderampen zu minimieren, müssen Bestellungen sorgfältig mit dem Management des Distributionszentrums koordiniert werden, um sicherzustellen, dass die Waren abgeholt werden, sobald sie bereit sind. Eine der besten Möglichkeiten, den Versand zu optimieren, besteht darin, Kommissionieraktivitäten in „Wellen“ zu organisieren, sodass eine Reihe relevanter Pakete für eine einzige Abholung vorbereitet werden kann.
7. Rückgabe
Ein weiterer Schritt, der besondere Aufmerksamkeit verdient, ist der Rückgabeprozess. Retouren sind zwar kein wünschenswerter Teil der Lagerverwaltung, aber eine Geschäftsrealität. Alle Unternehmen sollten ein RMA-Verfahren (Return Management Authorization) verwenden, um jeder Rücksendung eine eindeutige Nummer zuzuweisen und dem Kunden Anweisungen zu geben. Es ist auch wichtig, einen eigenen Bereich im Lager zu haben, um Rücksendungen und Inventar für die Wiederauffüllung zu handhaben.
Wie Sie sehen können, sind diese sieben Hauptprozesse innerhalb des Lagers miteinander verbunden und können nicht in einem luftleeren Raum verwaltet werden. Durch die Betrachtung des gesamten Systems als Ganzes und die Identifizierung nützlicher Metriken für jeden wichtigen Schritt ist es möglich, selbst das fortschrittlichste Lagerdesign zu verbessern. Wir hoffen, dass die in diesem Beitrag vorgestellten Tipps Ihnen helfen werden, einige Verbesserungsbereiche in Ihrem eigenen Lagerbetrieb zu identifizieren.
Industrietechnik
- Sieben häufige Pick-and-Pack-Fehler – und wie man sie behebt
- Sechs gängige Logistikfehler und wie man sie vermeidet
- Sieben Last-Mile-Lieferherausforderungen und wie man sie löst
- Wie man Cybersicherheit durch Technik, Menschen und Prozesse angeht
- Vier Arten von Cyberangriffen und wie man sie verhindert
- Drei Fallstricke bei der Zustellung auf der letzten Meile – und wie man sie vermeidet
- Sieben häufige Versandfehler und wie man sie vermeidet
- 4 Hauptursachen für Schaltanlagenausfälle und wie man sie vermeidet
- Die häufigsten Ursachen für Maschinenausfälle und wie man sie vermeidet
- 3 Hauptlagerprozesse (und wie man sie verbessert)