Die Technik hinter der Fast-Radius-Gesichtsmaske
Von Izzy de la Guardia, Anwendungstechniker, Fast Radius
Während die globale Pandemie viele Schwachstellen in unserer Lieferkette aufgedeckt hat, hat sie auch Innovationen hervorgebracht. Insbesondere der 3D-Druck hat es Fachleuten und Bastlern gleichermaßen ermöglicht, ihre Ängste mit beispielloser Geschwindigkeit und Zugänglichkeit in die Tat umzusetzen. Wir haben dies aus erster Hand bei der Entwicklung unseres Open-Source-Atemschutzmaskendesigns erlebt.
Hier ist ein Einblick in den Prozess und wie wir in nur zwei Wochen vier verschiedene Prototypen erstellen und drei Benutzertestsitzungen durchführen konnten, indem wir den 3D-Druck, ein funktionsübergreifendes Team und die persönlichen und beruflichen Netzwerke unseres Unternehmens nutzten.
Rapid Prototyping und Benutzertests
Als viele Amerikaner Mitte März begannen, vor Ort Schutz zu suchen, erhielt Fast Radius angesichts der wachsenden Besorgnis über den Mangel an PSA mehrere Anfragen nach 3D-gedruckten Atemschutzmasken. Ich wurde von unserem General Manager, John Nanry, an einem Freitagnachmittag angezapft, um die Designbemühungen zu leiten, um auf diesen Bedarf zu reagieren. Stunden später hatten wir unser erstes druckfertiges Design, inspiriert von den Open-Source-Designs von Copper 3D und La Factoría 3D
Das Hauptaugenmerk unseres Designs lag auf der Herstellbarkeit auf allen unseren hauseigenen Additivmaschinen (Stratasys FDM, Carbon DLS™ und HP Multi Jet Fusion), indem die richtigen Überhangwinkel und Vakuumbelüftung sichergestellt wurden. Wir haben in dieser Nacht unseren ersten Prototyp auf Carbon DLS produziert.
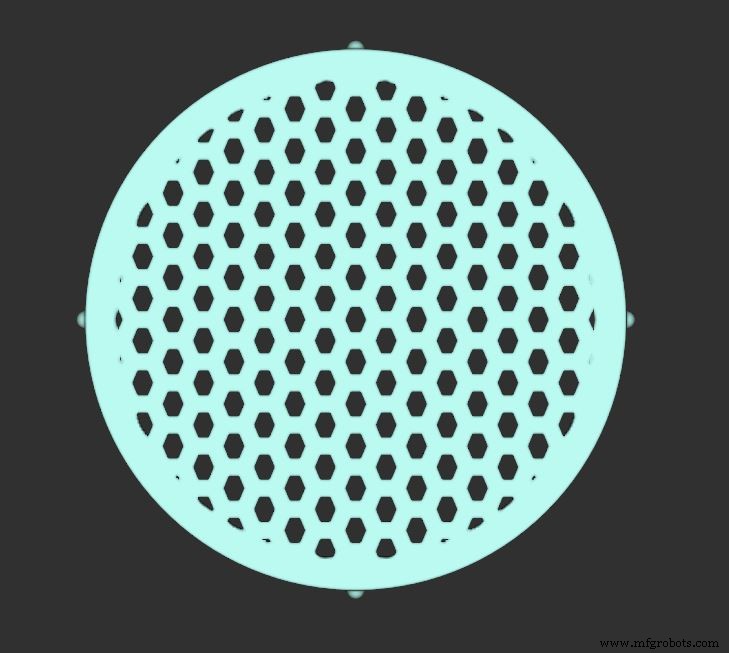
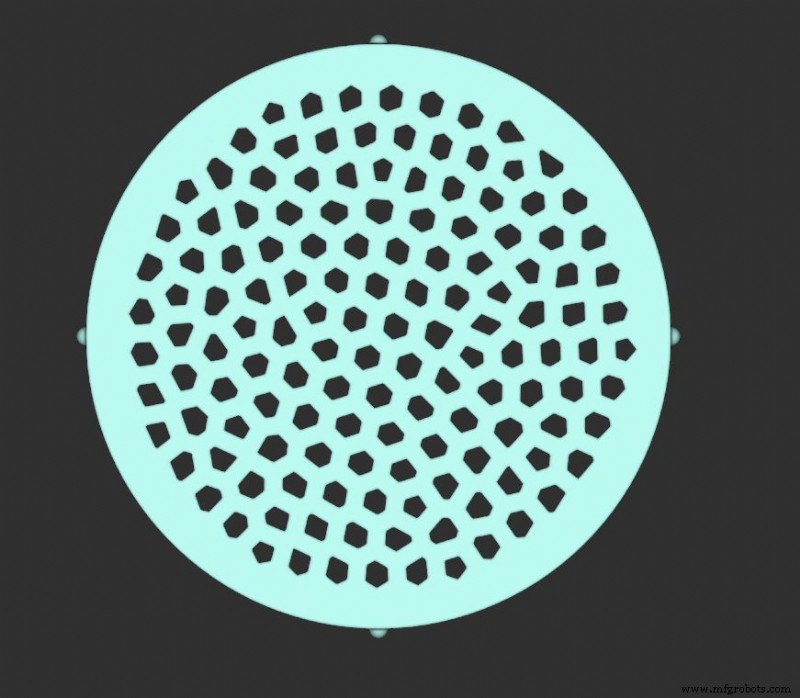
Fortgeschrittene Designtools wie nTop Platform unterstützten schnelle Iterationen, wie z. B. den Wechsel von einem Voronoi-Muster zu einem regelmäßigeren Hex-Muster, das für Hobby-FDM-Drucker einfacher zu handhaben war
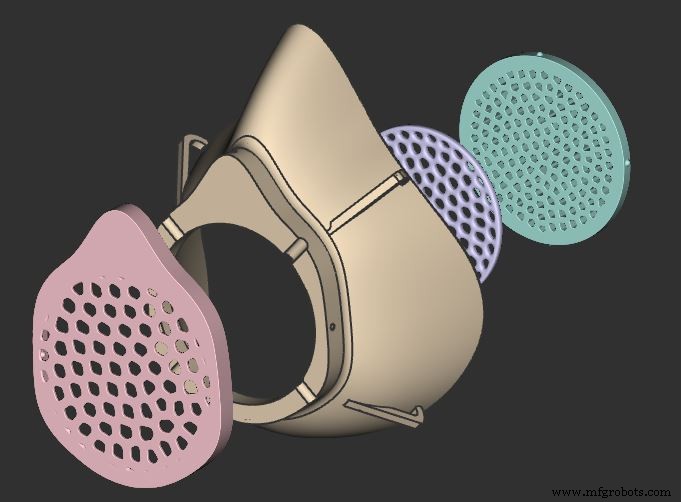
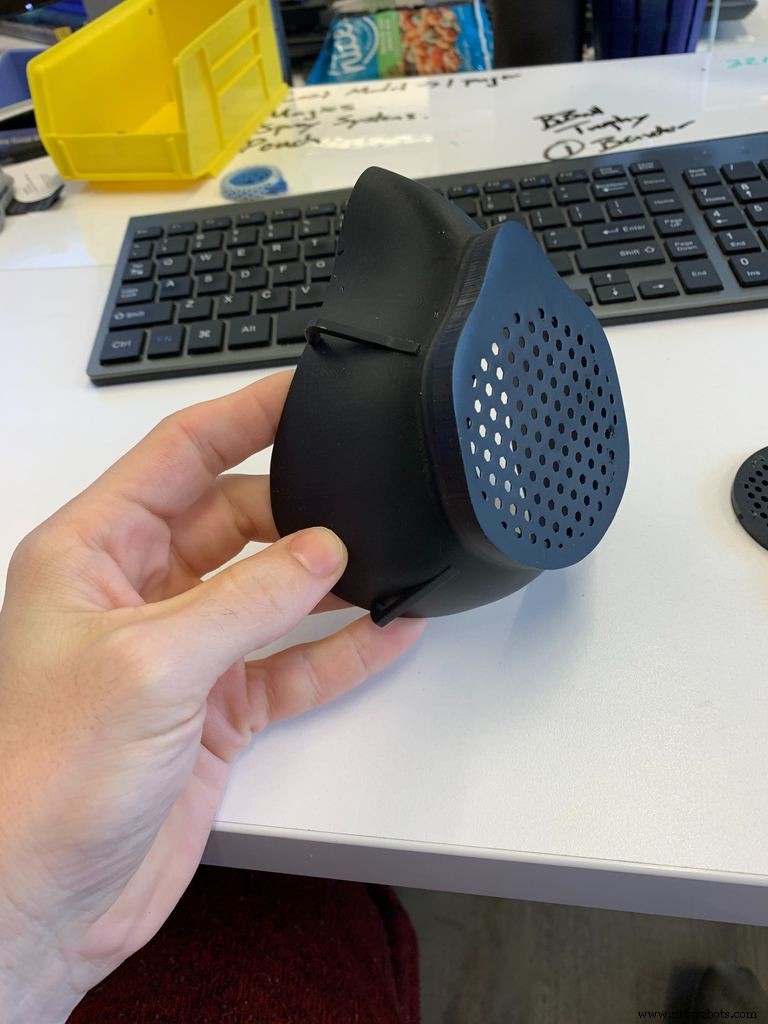
Unser erster gedruckter Prototyp enthielt FDM-freundliche Überhänge und Kanäle, um Vakuum bei DLS zu verhindern
Diese Prototypen führten zu weiteren Designänderungen:Konsolidierung der Frontabdeckung mit dem Hauptmaskenkörper zum Drucken in einem Stück, Verdicken der Riemenschlaufen für eine längere Lebensdauer und Verringern der Dichte des Gittermusters und kreisförmiges Gestalten zum einfacheren Drucken auf FDM. Nach nur 24 Stunden Projektlaufzeit konnten wir Samstagabend mit dem Druck unserer zweiten Prototypen beginnen.
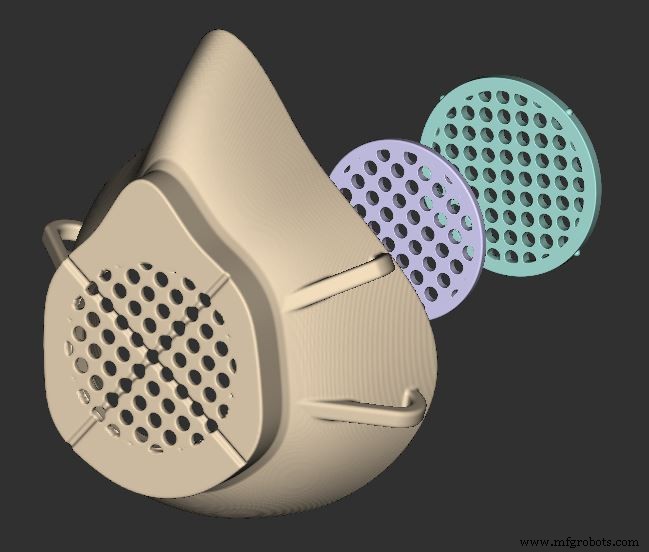
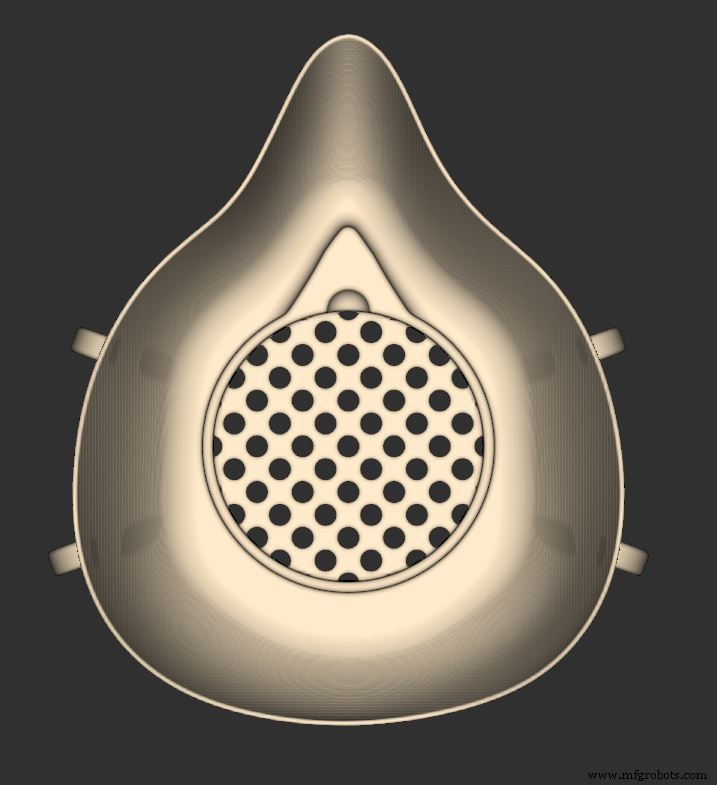
Unser zweiter gedruckter Prototyp konstruiert konsolidierte Teile (links). Innenseite der Maske mit Aussparung zum Einführen des Fingers und Herausspringen der Snap-In-Filterabdeckung (rechts).
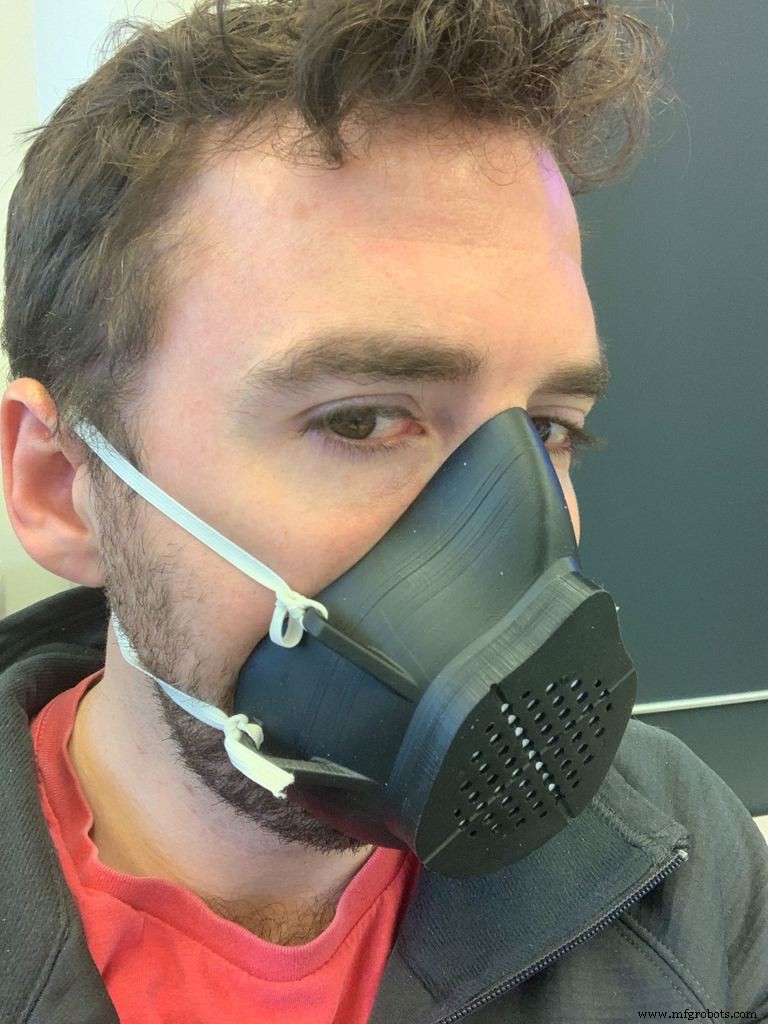
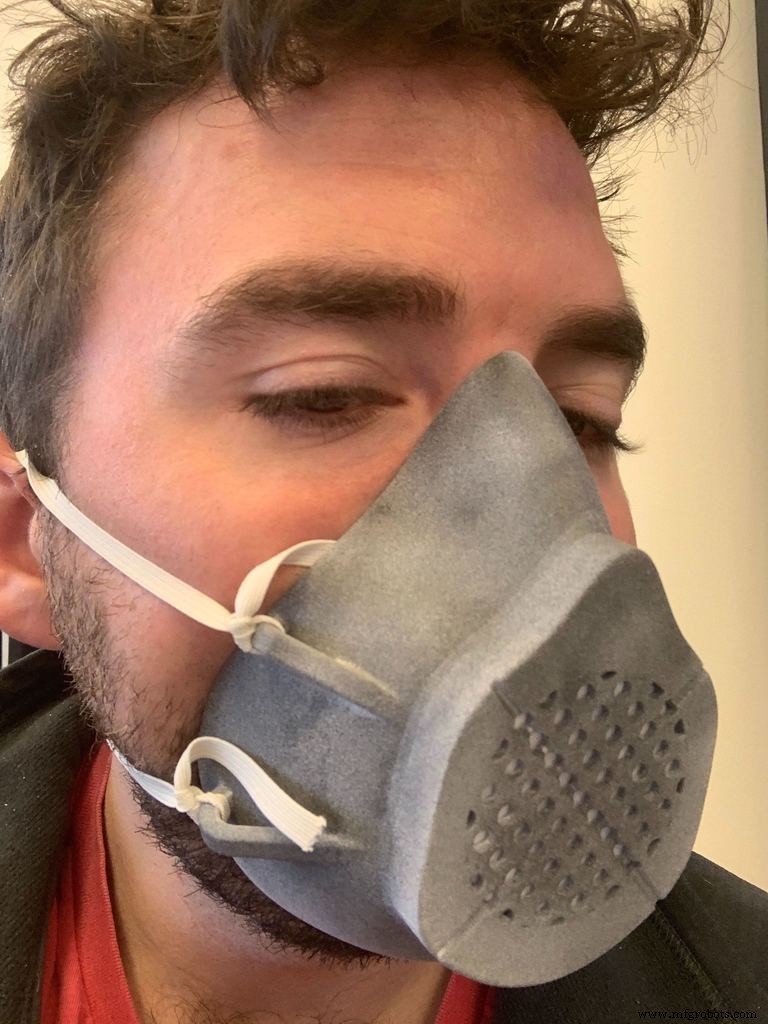
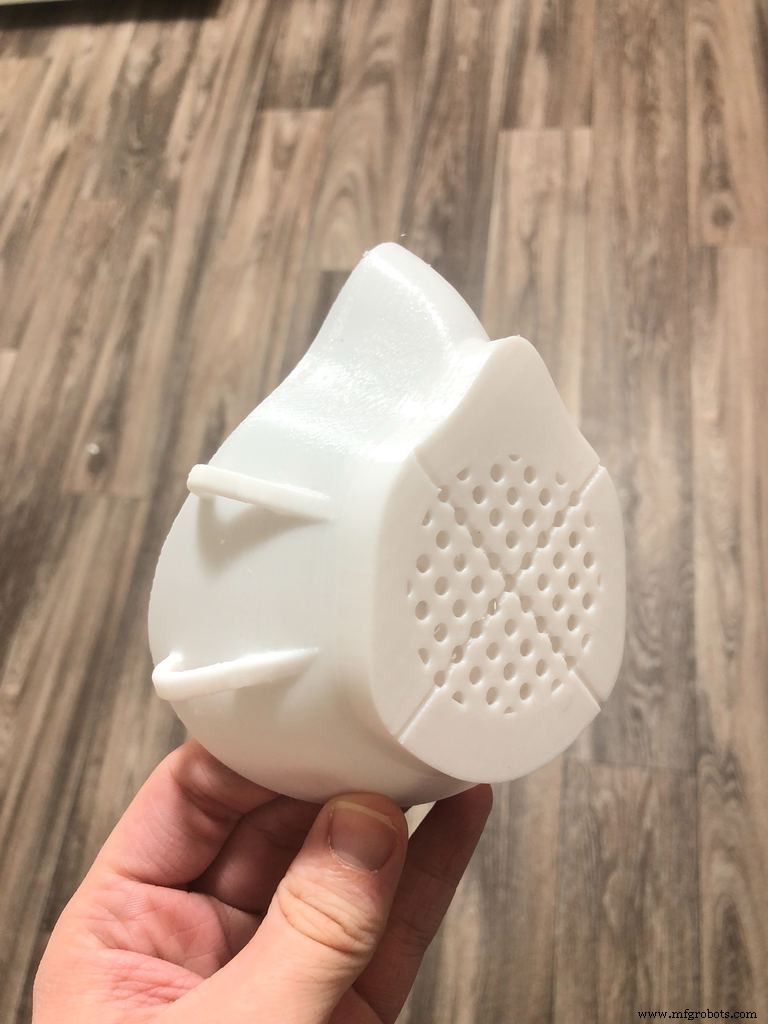
Zweiter gedruckter Prototyp aus Carbon RPU70 (links), HP PA12 (Mitte) und FDM-gedrucktem PLA (rechts)
Parallel zum Designprozess nutzten wir unser Netzwerk, um den Bedarf besser zu verstehen und Personen für Benutzertests zu identifizieren. In weniger als 24 Stunden brachten uns unsere Freunde von P33 mit einem Dutzend Ärzten und Mitarbeitern einer medizinischen Forschungsstiftung zusammen, um einen besseren Einblick in N95-Masken zu erhalten. Unsere Mitarbeiter haben sich auch an die ihnen bekannten medizinischen Fachkräfte gewandt. Am Sonntag, nur zwei Tage nach Beginn des Projekts, führten wir mit unserem zweiten Prototypen Dichtsitztests an 10 Personen an vier Standorten durch.
Die nächsten zwei Wochen gingen in diesem Muster weiter – entwerfen, drucken, testen, wiederholen. Unser dritter gedruckter Prototyp zeigte eine Neugestaltung des Filterrückhaltemechanismus. Die versetzte Halbkreis-Umfangsgeometrie fungiert als Nocke, die das Teil verriegelt, wenn es durch Reibung verdreht wird (siehe unten). Es gibt zwei Laschen, die die Abdeckung in der gedrehten oder verriegelten Position nach unten drücken, um eine gute Abdichtung um den Filter herum zu gewährleisten. Wir haben eine Version mit einem herzförmigen perforierten Bereich erstellt, um die Maske weniger einschüchternd zu machen. Beginnend mit dieser Runde von Prototypen haben wir Masken in zwei verschiedenen Größen entworfen und getestet.
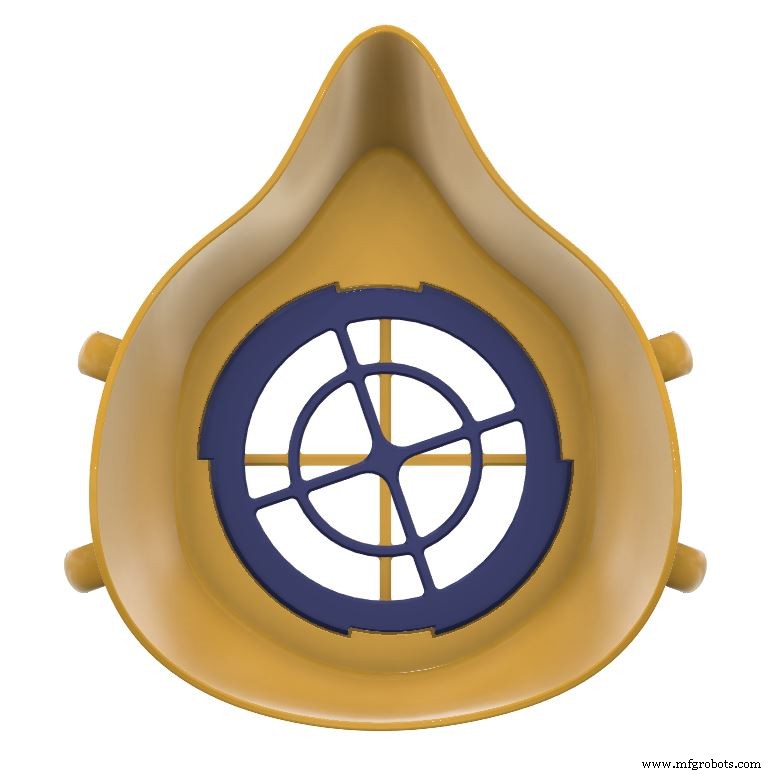
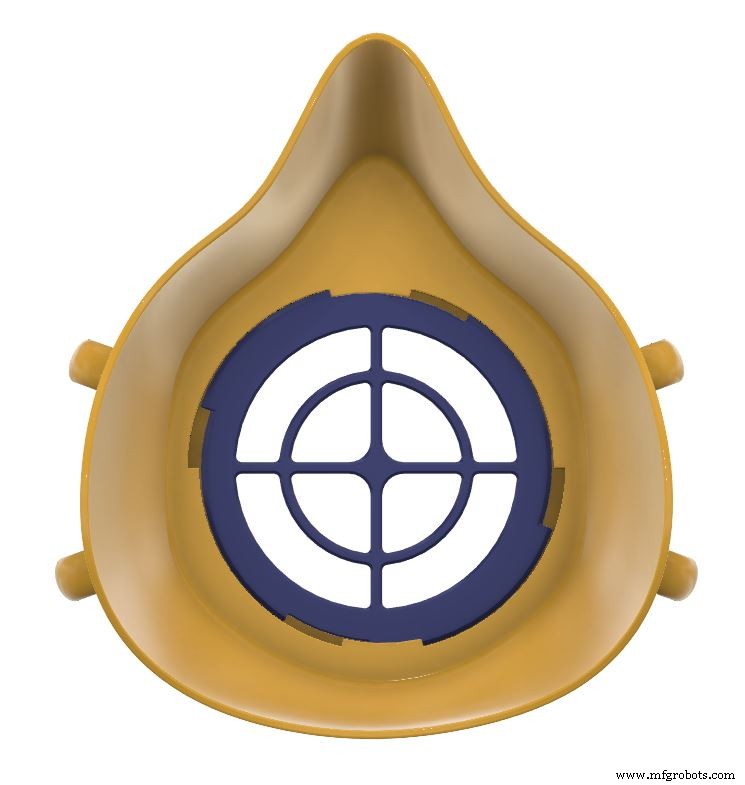
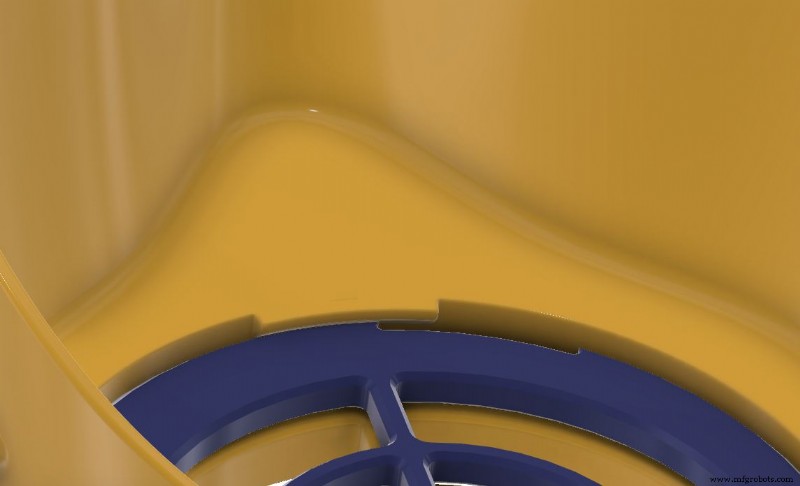
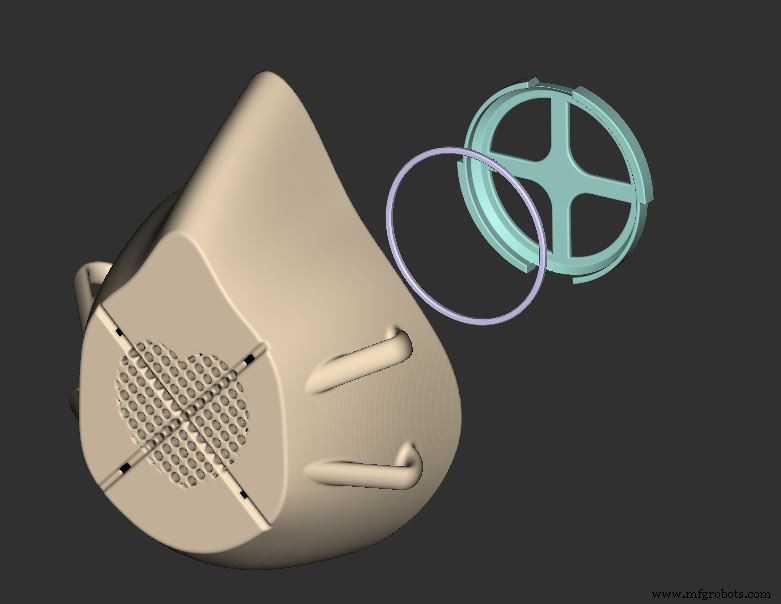
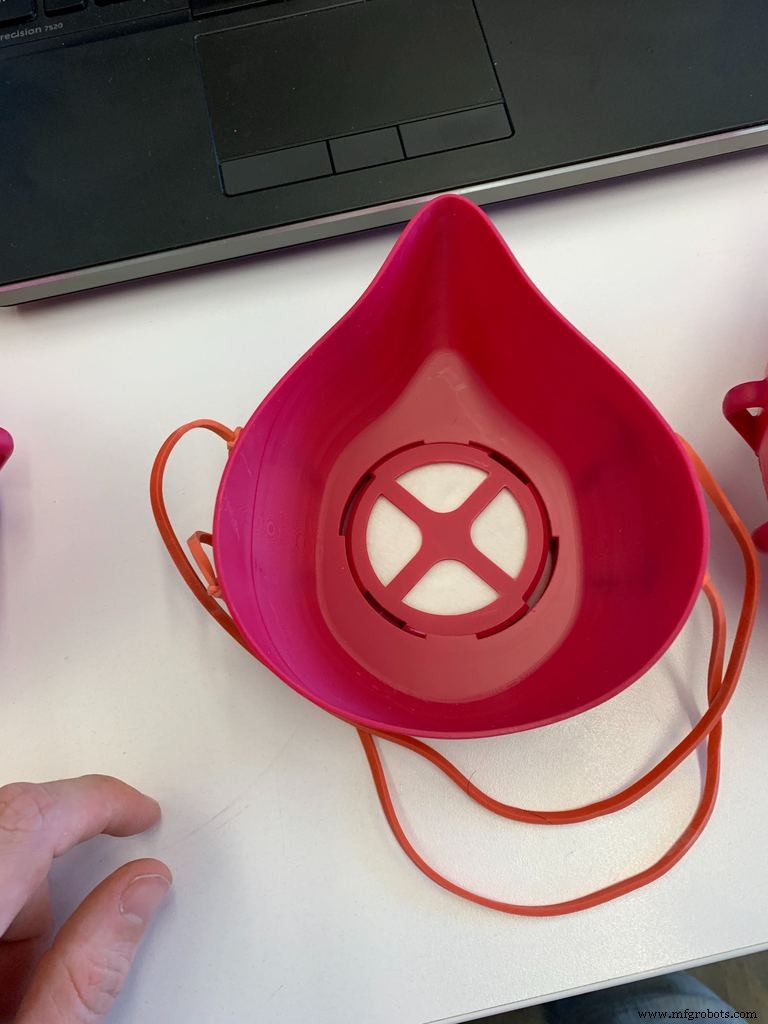
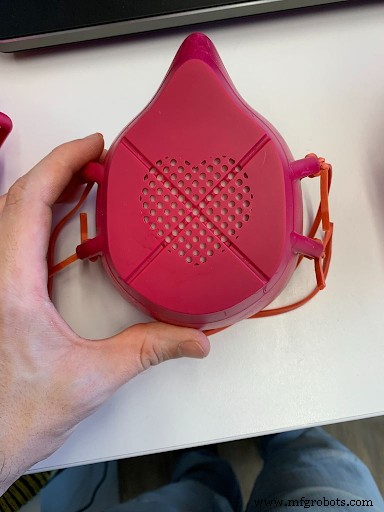
Dritter gedruckter Prototyp mit Drehverschluss.
Beim vierten Prototypen ging es uns vor allem um Atmungsaktivität und Passform. Um dem entgegenzuwirken, haben wir versucht, den perforierten Bereich zu maximieren und seine Dichte zu minimieren (wobei wir leider das Herz verloren haben), um den Widerstand gegen den Luftstrom zu verringern. Wir haben auch die Maße für die beiden Größen basierend auf dem Feedback von Benutzertests optimiert. Zu diesem Zeitpunkt waren wir von der Funktion und Größe der Maske überzeugt genug, um die erste Version als Open-Source-Design zu veröffentlichen.
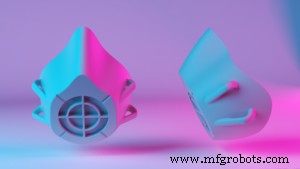
Design für Barrierefreiheit
Um die Maske möglichst vielen Menschen zugänglich zu machen, haben wir ein Open-Source-Design entwickelt, das auf Haushalts-3D-Druckern hergestellt werden kann. Diese Entscheidung fügte Design- und Materialbeschränkungen hinzu. Eine starre Maske konnte sich nicht an eine Vielzahl von Gesichtsformen anpassen, daher haben wir versucht, ein flexibles Material am inneren Rand der Maske hinzuzufügen, um die Abdichtung zum Gesicht zu verbessern.
Wir haben ein erstes Konzept mit SIL 30 auf Carbon DLS prototypisiert. Anschließend haben wir viele Methoden getestet, um eine wirksame Abdichtung zum Gesicht zu schaffen (unten beschrieben), darunter ein zerschnittener Handschuh, bedrucktes und geformtes Silikon, formbares Kostüm-Gesichtsprothesenmaterial, FDM-gedruckte TPU- und PLA-Dichtungen und Dichtungen. Letztendlich haben wir uns für Wetterschutz entschieden, der biokompatibel, leicht zu reinigen und leicht zu beschaffen ist.
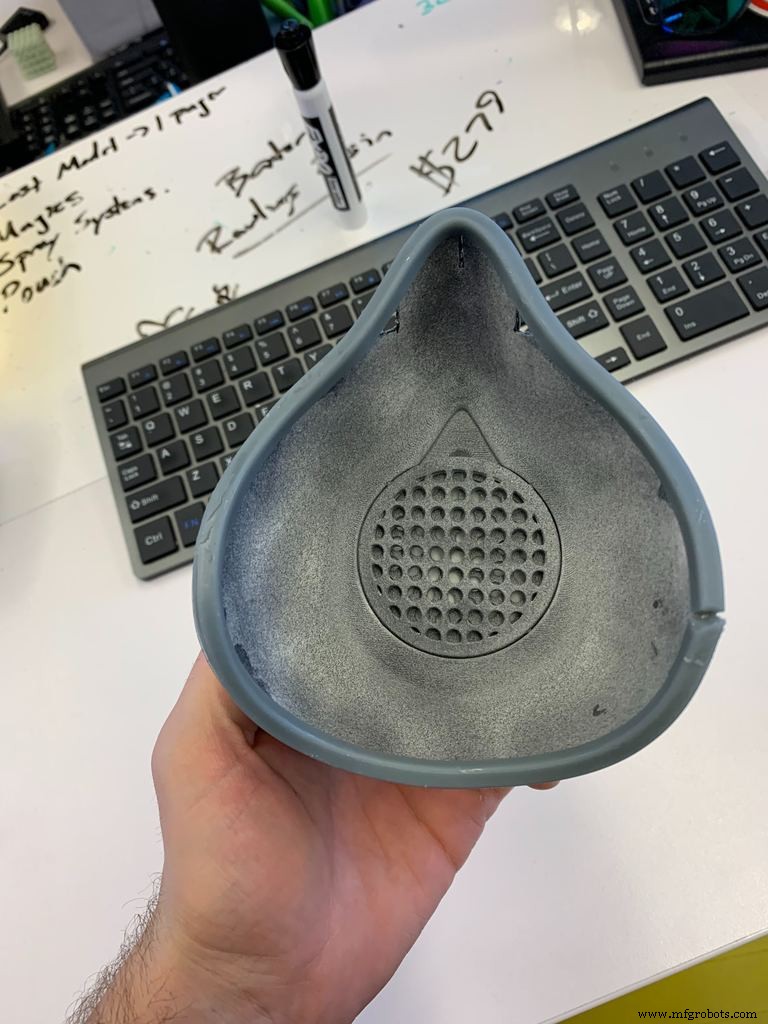
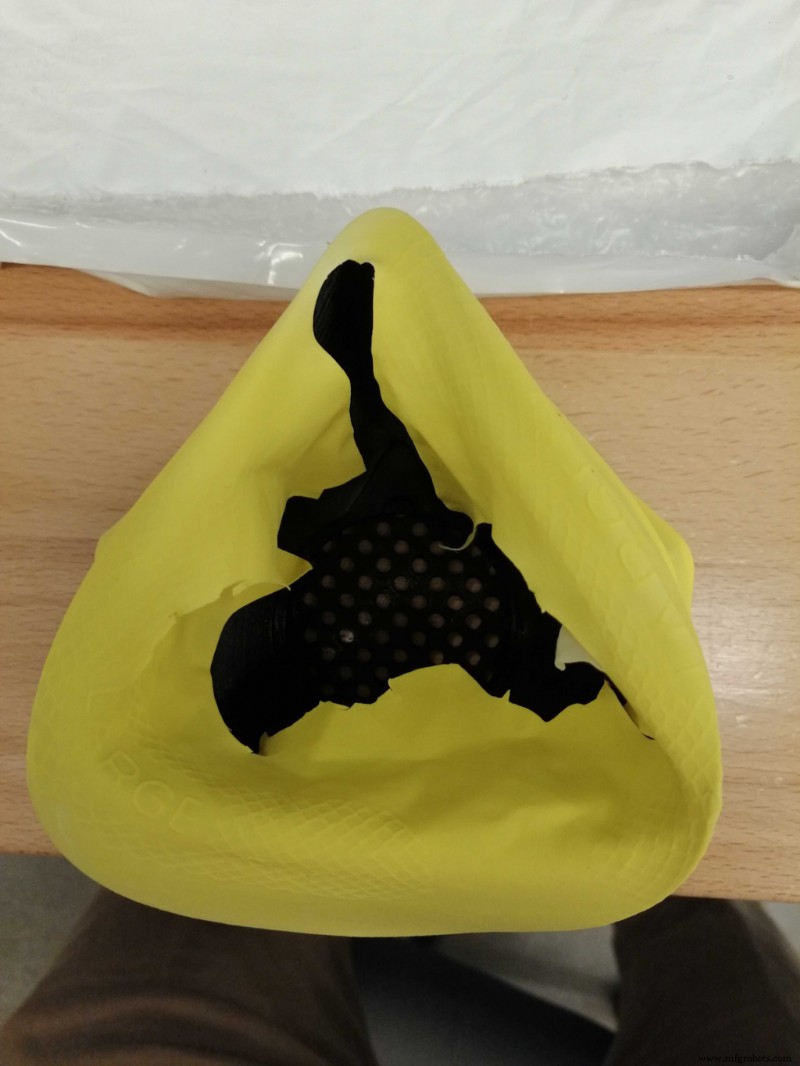
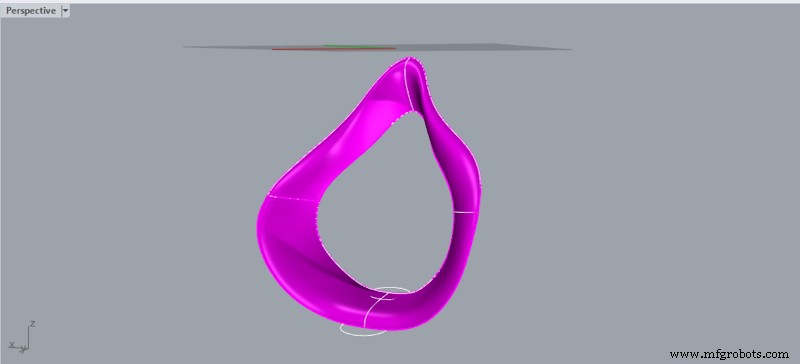
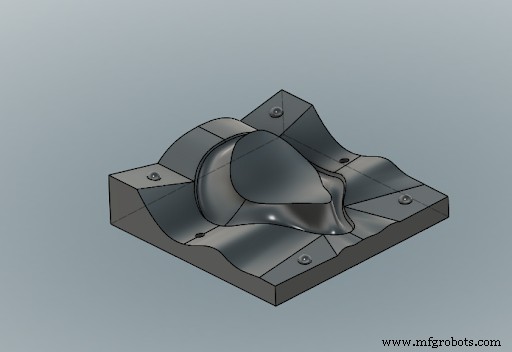
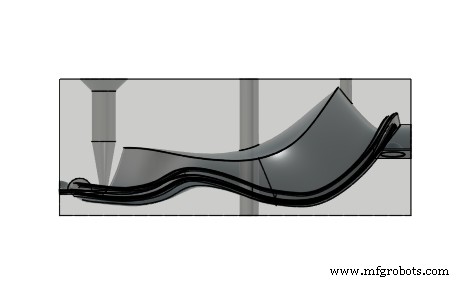
Formmodell für formbares Silikon
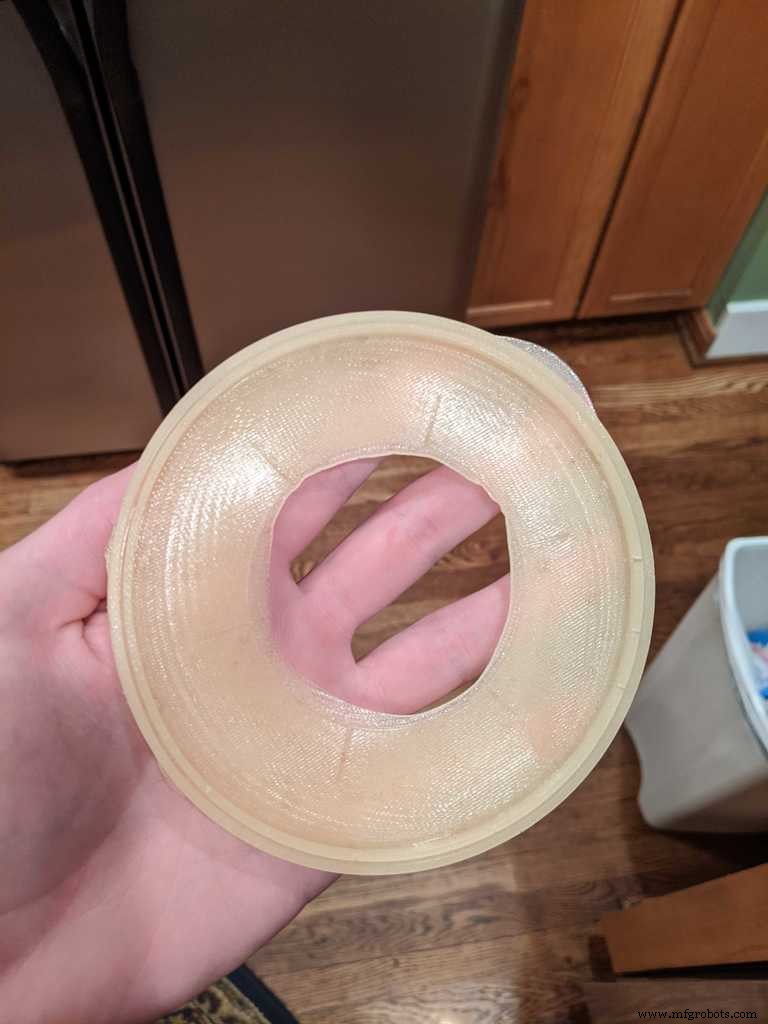
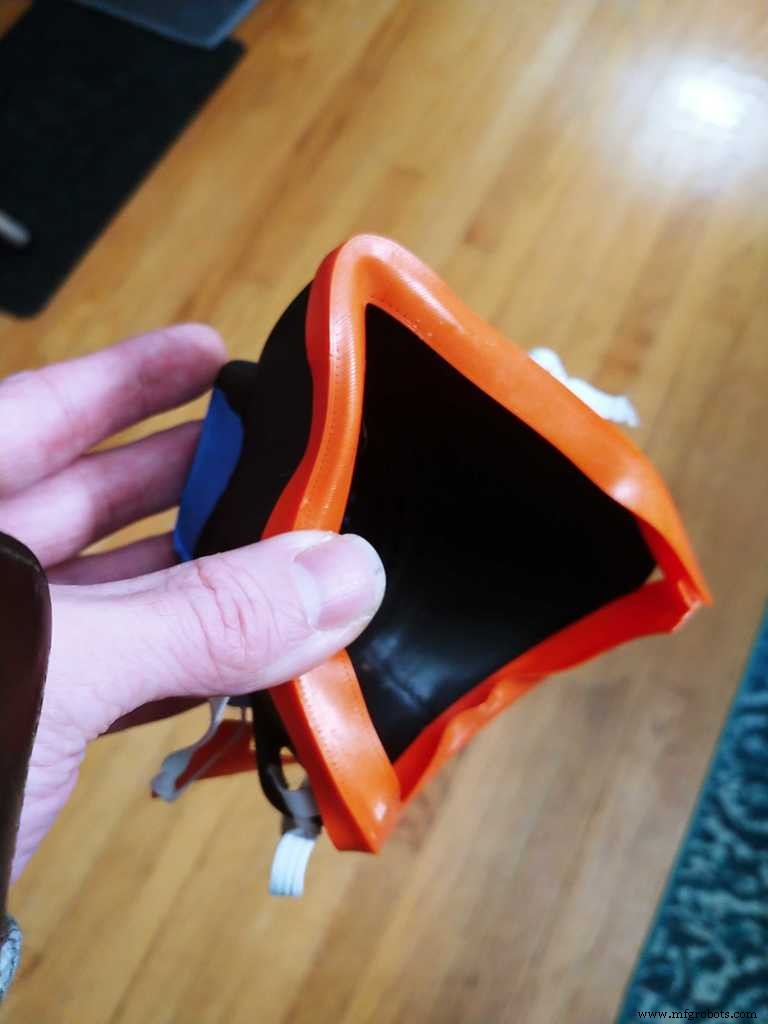
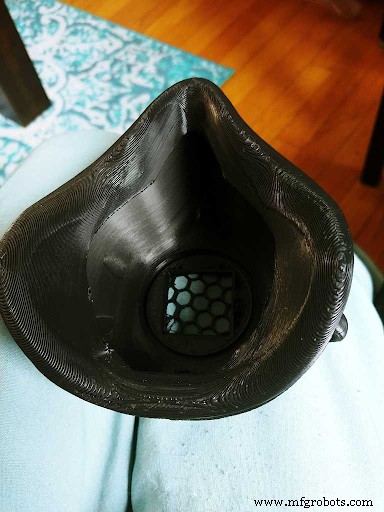
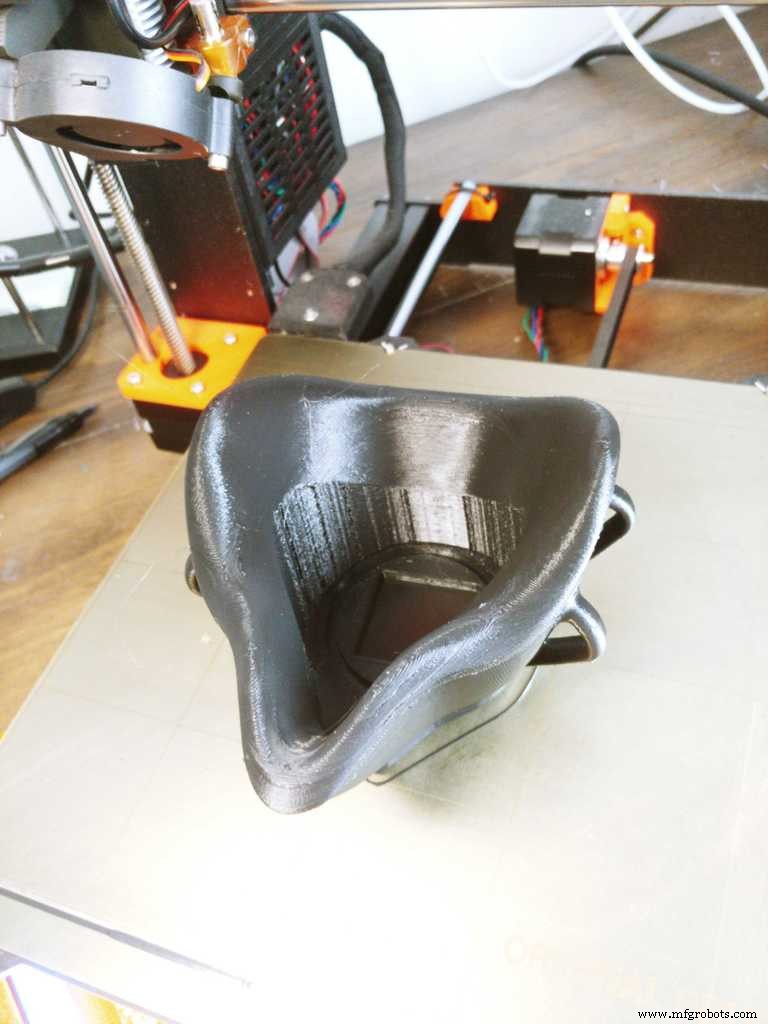
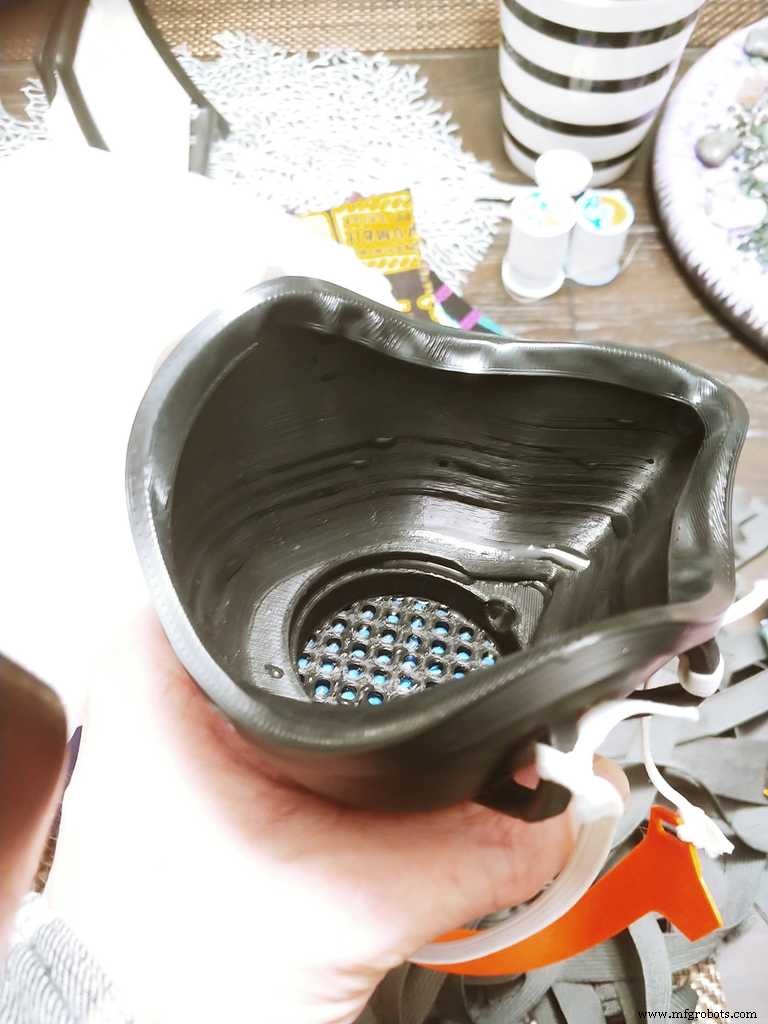
Integrierte dünne PLA-Dichtung
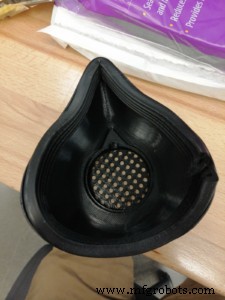
Schnelle Teambildung
Ich schreibe die erfolgreiche schnelle Iteration dieses Projekts nicht nur der Leistungsfähigkeit digitaler Designtools und der additiven Fertigungstechnologie zu, sondern auch dem Engagement und der Vielfalt des Teams, das wir aus verschiedenen Teilen des Unternehmens zusammengestellt haben. Daniel Baker (Manager of Manufacturing Engineering) gab DFM-Feedback und verbrachte die ganze Nacht damit, Prototypen zu drucken und nachzubearbeiten. Tim Ouradnik (Anwendungsingenieur) beschaffte Dichtungsmaterial, baute Prototypen zusammen und fuhr durch ganz Chicago, um sozial distanzierte Benutzertests durchzuführen. Uriah Foley und Eldon Whitis (Labortechniker) testeten nach Feierabend zu Hause Prototypen und erkundeten integrierte Dichtungen auf ihren persönlichen 3D-Druckern.
Nick Tonini (Programmmanager) lieferte unendlich erfinderische Lösungen und Design-Feedback. Jerry O’Leary (Chief Designer) verbesserte unsere Designs und erstellte Konzept-Renderings. Charlie Wood (Manager of Computational Engineering) übernahm die Leitung des Dichtungsdesigns. Hallee Deutchman (Director of Materials and Manufacturing Technology) hat sich mit unseren Partnern und dem Rechtsteam in Verbindung gesetzt, bevor das Design freigegeben wurde. Sheila Seles (Senior Content Manager) und Austin Belisle (Content Specialist) haben unser Design zusammengestellt, veröffentlicht und beworben.
Die obige Liste der Anerkennungen soll nicht nur den Personen Anerkennung zollen, die zu diesem Prozess beigetragen haben, sondern auch die Macht der Unternehmenskultur bei der Ermöglichung neuer Dinge demonstrieren. Wir haben an diesem Projekt außerhalb unserer normalen Verantwortlichkeiten und Teamstrukturen gearbeitet, weil wir ein Produkt schaffen wollten, das die Welt jenseits von Fast Radius beeinflussen könnte. Dieser Geist ging auch über die Unternehmensgrenzen hinaus; Wir sind P33 und allen Ärzten dankbar, die ihre Zeit und ihr Fachwissen eingebracht haben. Wenn wir nichts anderes aus dieser Pandemie lernen, hoffe ich, dass wir weiterhin darauf bedacht sind, eine Kultur der Vielfalt, Demut und Zusammenarbeit zu pflegen, während wir daran arbeiten, auf dringende globale Herausforderungen zu reagieren.
Unser Design ist verfügbar und druckbereit. CAD-Dateien und Anleitungen finden Sie auf unserer Website.
Sind Sie bereit, Ihre Teile mit Fast Radius herzustellen?
Starten Sie Ihr AngebotIndustrietechnik
- Die Zukunft ist…Zusammenarbeit
- Beitrag im MRO-Magazin
- The Mark Two
- Hinter den Kulissen unseres Blogs
- Die Auswirkungen von COVID-19 auf die Produktion
- Die greifbaren Vorteile von VR im Engineering-Bereich
- Tableau, die Daten hinter den Informationen
- Die Geschichte hinter unserem beliebtesten Video
- Die Bedeutung der Teilentladungserkennung
- Die Zukunft der Instandhaltungstechnik