ULCORED-Prozess
ULCORED-Prozess
ULCORED ist ein Direktreduktionsverfahren (DR), bei dem DRI (Direct Reduced Iron) in einem Schachtofen entweder aus Erdgas (NG) oder aus durch Vergasung von Kohle gewonnenem Reduktionsgas hergestellt wird. Das Abgas aus dem Schacht wird nach der Abscheidung von Kohlendioxid (CO2) in den Prozess zurückgeführt, das die DR-Anlage in einem konzentrierten Strom verlässt und gelagert wird. Der DRI-Schritt erzeugt ein festes Produkt, das dann unter Verwendung eines Elektrolichtbogenofens (EAF) geschmolzen wird. Der Prozess wurde hauptsächlich im Jahr 2006 von einem Team unter der Leitung von LKAB, Voest-Alpine und MEFOS entworfen.
Das Ziel des ULCORED-Prozesses bestand darin, den zur Herstellung von DRI erforderlichen NG-Verbrauch zu reduzieren. Dies wurde erreicht, indem die herkömmliche Reformierungstechnologie durch die partielle Oxidation (POx) von NG ersetzt wurde. In Kombination mit einem CCS-Gerät kann ULCORED die CO2-Emission im Vergleich zum Durchschnitt auf der BF-Route um 70 % reduzieren.
Das Konzept des ULCORED-Verfahrens beinhaltet die Abtrennung von CO2 aus dem Prozessgas. Es zeichnet sich durch das Bestreben aus, gasbasierte DR-Prozesse auf eine minimierte Emission von Treibhausgasen (THG) umzustellen, indem CO2-Abscheidungs- und -Speicherungstechnologie (CCS) und gleichzeitig ein minimierter Energieverbrauch verwendet werden. Der Prozess ist so ausgelegt, dass CO2 extrahiert und gespeichert werden kann. Der Prozess ist daher auch auf CCS mit einer ähnlichen In-Process-Erfassung angewiesen.
Das Verfahren basiert auf der Verwendung eines Shifters zur Umwandlung des Kohlenmonoxidgases (CO) aus dem Schacht in Wasserstoff (H2) zusammen mit einer CO2-Entfernungseinheit. Dies eröffnet eine neue innovative Weiterentwicklung des Prozesskonzepts.
Zu den Hauptmerkmalen des ULCORED DR-Prozesses gehören (i) die Verwendung von Sauerstoff (O2) anstelle von Luft, was zu einem Abgas mit nahezu 100 % CO2 führt, das nur komprimiert werden muss, (ii) es gibt Möglichkeiten, den Bedarf an CO2 zu reduzieren NG um 15 % bis 20 %, und (iii) Kohle, Biomasse, Bioabfallvergasung und H2 können als Alternative zu NG verwendet werden.
Das Konzept von ULCORED besteht darin, die Nachfrage nach reduzierten CO2-Emissionen durch die auf Eisenerz und Gas basierende Direktreduktion für die DRI-Produktion zu erfüllen. Das Konzept umfasst die Verwendung von 100 % Sauerstoff (O2), POx anstelle von Reformern, Shifter zur Produktion von CO2-freiem Reduktions-/Überschussgas und das Reduktionsmittel ist entweder Erdgas oder Synthesegas aus Kohle-/Biomassevergasung. Anstelle von Erdgas kann auch Reduktionsgas aus der Vergasung von Kohle verwendet werden.
ULCORED DR-Prozess basierend auf NG
Die Hauptmerkmale des auf Erdgas basierenden ULCORED DR-Prozesses sind (i) kein Reformer, (ii) kein Erhitzer und (iii) hoher Druck. Aufgrund des hohen Drucks gibt es im DR-Schacht eine geringere Gasgeschwindigkeit, weniger Fluidisierung und weniger Feinanteile, die den DR-Schacht verlassen. Außerdem werden aufgrund des hohen Drucks kleinere CO2-Entfernungs- und POx-Einheiten benötigt, und es besteht ein geringerer Strombedarf für den Rückführungskompressor.
Die Originalität des Konzepts ist die Verwendung von O2 anstelle von Luft, was bedeutet, dass das Gas entweder keinen oder nur wenig Stickstoff (N2) enthält. Die Reformierung erfolgt durch eine POx-Einheit zur Konditionierung des Reduktionsgases (Bild 1). Die Technologie ersetzt das herkömmliche Reformieren von NG durch partielle Oxidation des Gases, um den Verbrauch von NG zu reduzieren, das zur Herstellung von DRI benötigt wird. Die stattfindende POx-Reaktion ist CH4 + 0,5O2 =CO + 2H2 mit Delta H =– 8,6 Kcal/mol.
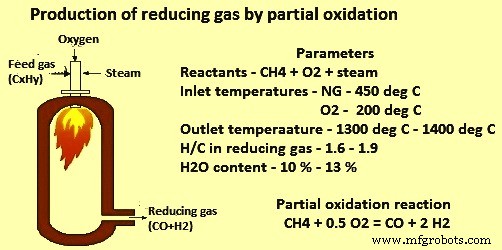
Abb. 1 Reduzierung der Gasproduktion durch partielle Oxidation
Die Pilotanlage zur partiellen Desoxidation wurde bei Linde in zwei Kampagnen mit neu konzipierten Brennern für H2-reiches Einsatzgas getestet. Es wurde ein Rohrreaktor mit vorgewärmtem Gas (60 % H2 und 40 % CH4) verwendet. Die Schlussfolgerungen der Pilotversuche waren (i) Brenner und Reaktor konnten ohne Probleme betrieben werden, (ii) es konnte eine stabile Flamme ohne signifikante Geräuschentwicklung erhalten werden, (iii) die Rußproduktion wird voraussichtlich unter 300 mg liegen /N cum auf 460 mg/N cum Nassgasvolumen, und (iv) der CO2- und CH4-Gehalt aufgrund des atmosphärischen Drucks höher war als die Vorberechnungen auf der Grundlage des angenommenen Gleichgewichts. Ein höherer Betriebsdruck bis 7 kg/cm² kann diesen Gehalt reduzieren.
Der DR-Schacht hat einen Gegenstrom aus Reduktionsgas, das an den Windformen eingespritzt wird, und Eisenerz wird kalt von oben zugeführt. Der Ofen wird bei einem Druck von 6 kg/cm² und einer Temperatur von etwa 900ºC betrieben. Das Schachtabgas enthält wahrscheinlich hauptsächlich CO, CO2, H2 und H2O.
Das Schachtabgas, das hauptsächlich CO, CO2 und H2O enthält, wird durch einen Shifter (ein- oder zweistufig) geleitet, der CO in H2 umwandelt. Der Einsatz eines Wassergasshifters führt zu einem hohen H2-Gehalt im Reduktionsschacht. Die Wassergas-Shifter-Reaktion ist CO (g) + H2O (g) <–> CO2 + H2. Fast das gesamte CO im Schachtabgas wird in H2 umgewandelt und das CO2 in der CO2-Entfernungseinheit entfernt. Eine erhöhte Produktion von überschüssigem Gas erhöht den Energiebedarf für die CO2-Entfernungseinheit und die O2-Produktion. Die Berechnung des korrekten Gasüberschusses ist ein iterativer Prozess. Aus diesem Grund werden die geschätzten Mengen an überschüssigem Gas höher sein. Ein geschätzter Überschuss von 2,2 Gigakalorien pro Tonne DRI wird voraussichtlich den zusätzlichen Strombedarf kompensieren. Dies kann durch einen Bypass von etwas Gas direkt zum Schalthebel erreicht werden. Die umgeleitete Gasmenge wird basierend auf den Eigenschaften des Reduktionsgases in den Reduktionsschacht bestimmt. Aufgrund erhöhter Gasvolumina im System sind zusätzliche Investitionen für die Shifter- und CO2-Entfernungseinheiten erforderlich.
In der Shifter-Einheit ist die CO-Shift-Reaktion exotherm, und das Gleichgewicht begünstigt die CO-Umwandlung bei hohem Dampf-zu-Gas-Verhältnis und niedrigen Temperaturen, während es vom Druck unbeeinflusst bleibt. In einem adiabaten System wird der erreichbare CO-Schlupf durch die Austrittstemperatur bestimmt. Die Umwandlung in einem einzelnen Katalysatorbett ist durch das Gleichgewicht begrenzt, und wenn die Reaktion fortschreitet, schränkt die hohe Temperatur schließlich die weitere Reaktion ein. Diese Einschränkung kann mit einem zweistufigen System überwunden werden, das aus einer Hochtemperaturverschiebung gefolgt von einer Niedertemperaturverschiebung mit Zwischenbettkühlung besteht. Eine niedrige Betriebstemperatur ergibt das günstigste thermodynamische Gleichgewicht und damit den minimalen CO-Schlupf. Die meisten modernen H2-Anlagen haben Kühlsysteme vor dem Niedertemperatur-Shift-Reaktor, um einen Betrieb nahe dem Taupunkt des Prozessgases zu ermöglichen. Zur vollständigen Verdunstung von Wassertröpfchen, die sich im Kühler bilden können, ist ein Sicherheitsabstand über dem Taupunkt einzuhalten.
Abhängig vom Dampfverhältnis kann der Niedertemperatur-Shift-Reaktor bei einer so niedrigen Temperatur wie 190°C betrieben werden, ohne dass eine Kondensation zu befürchten ist. Bei dem Konzept durchläuft das Topgas einen Hoch- und einen Niedertemperaturshifter mit dazwischenliegender Wärmerückgewinnung. Der Hochtemperatur-Shifter wandelt 97,2 % des CO um und der Niedertemperatur-Shifter vervollständigt die Umwandlung zu 99,5 %. Der Wärmetauscher erwärmt das rückgeführte Gas und seine Kapazität wird basierend auf einer eingestellten Temperaturdifferenz auf der heißen Seite von 50 °C berechnet. Ein Wärmeüberschuss im Wärmetauscher erzeugt Dampf für das Dampfnetz durch einen Kondensator/Reboiler.
Die CO2-Entfernungseinheit wird verwendet, um das CO2 aus dem Gas zu entfernen, wodurch ein H2-reiches Reduktionsgas entsteht, das in den Prozess zurückgeführt wird. Die CO2-Entfernungseinheit wird durch eine Verteilung für die CO2-Entfernungseffizienz, H2- und N2-Rückgewinnung festgelegt. Die zwei CO2-Entfernungsverfahren, die verwendet werden können, sind das Vakuumdruckwechseladsorptionsverfahren (VPSA) oder das Aminwäscherverfahren. Die Wahl der CO2-Entfernungseinheit (VPSA oder Amin) hängt von den örtlichen Anforderungen ab. Wenn ein Dampfüberschuss vorhanden ist, kann das energieaufwändige CO2-Stripping mit Dampfenergie in der Anlage statt mit Strom, der für die VPSA benötigt wird, durchgeführt werden. Beide Technologien haben Vor- und Nachteile, die weiter analysiert werden müssen. Beide Technologien arbeiten mit dem ULCORED-Konzept. Es besteht auch die Möglichkeit, anstelle der VPSA-Einheit eine Druckwechseladsorption (PSA) zur CO2-Entfernung zu verwenden, da im Prozess bereits ein hoher Druck zur Verfügung steht.
Die gewählte Verfahrensart wirkt sich auf das Verfahrensfließbild und das Layout aus. Der VPSA-Prozess erfordert, einschließlich Kryotechnik und Kompression auf 110 kg/cm² Druck, 260 kWh Strom pro Tonne abgeschiedenem CO2. Im Falle eines Amin-Wäscher-Prozesses mit Hochleistungsaminen (aktiviertes Methyldiethanolamin, aMDEA) erfordert der vollständige Prozess (Amine und Kompression auf 110 kg/cm² Druck) etwa 1,6 Tonnen Niederdruckdampf und 160 kWh Strom pro Tonne CO2 erfasst.
Der N2-haltige Teil des gereinigten H2-Reichgases wird aus dem Prozess ausgeschleust, um einer N2-Anreicherung im Reduktionsgas entgegenzuwirken. Das Zapfgas ist ein wertvolles Gas, das zur Erzeugung von Dampf oder Heizung innerhalb des Systems verwendet werden kann.
Das Flussdiagramm des ULCORED-Prozesses auf Basis von Erdgas ist in Abb. 1 dargestellt.
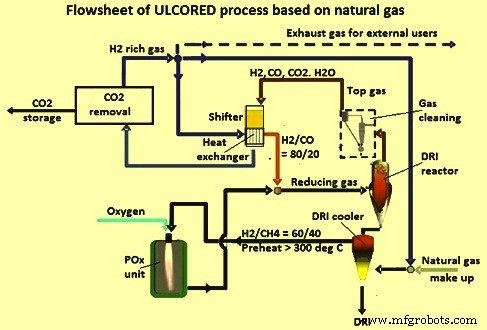
Abb. 2 Flussdiagramm des ULCORED-Prozesses auf Basis von Erdgas
ULCORED DR-Prozess basierend auf Kohlevergasung
Die CO2-sparendste Option mit ULCORED ist die Verwendung eines Kohlevergasers, der Syngas für die DR-Anlage und CO2-armes H2-Gas für alle Nutzer der Anlage produziert. Dieses Konzept kann sowohl für bestehende Anlagen als auch für nachgerüstete Anlagen angepasst werden.
Das auf Kohle basierende Konzept basiert auf der Produktion von Reduktionsgas unter Verwendung bestehender Kohlevergasungstechnologie und entweder Kaltentschwefelung (basierend auf bestehender Technologie) oder Heißgasentschwefelung. Das Konzept nutzt O2 statt Luft und beinhaltet eine CO2-Speicherung. Der hohe H2-Gehalt im Reduktionsschacht wird durch Wassergasshifter erreicht. Überschüssiges H2-Gas wird an die anderen Nutzer der Anlage geliefert.
Die Kohlevergasung ist eine wohlbekannte Technik und wird voraussichtlich eine der zukünftigen Energieumwandlungsprozesstechniken nach der Erschöpfung der Öl- und Gasreserven sein. Es gibt mehrere Technologien, die für die Vergasung von Kohle entwickelt wurden. Es gibt Unterschiede zwischen den Technologien, aber sie arbeiten im Allgemeinen mit einer relativ hohen C-Umwandlungseffizienz, normalerweise größer als 80 %. Ein großer Vorteil bei der Kohlevergasung ist die Möglichkeit, das Synthesegas vor der Verwendung effizient zu reinigen (z. B. von Schwefel, Quecksilber usw.).
Da der Schachtofen für die Herstellung von DRI mit einem Druck von 6 kg/cm² arbeitet, wird der Gasdruck aus dem Vergaser durch eine Expansionsturbine verringert, die auch Energie zurückgewinnt (von 30 kg/cm² auf 6 kg/cm²).
Das ULCORED DR-Verfahren kann leicht in eine Kohlevergasungsanlage integriert werden, wobei die Vorteile der Originalität des Verfahrenskonzepts integriert werden. Kohle wird der Kohlevergasungsanlage zugeführt. Schwefel wird aus dem Synthesegas entweder durch Heiß- oder Kaltentschwefelung entfernt. Das saubere Synthesegas wird mit gereinigtem, H2-reichem Rückführungsgas gemischt, das im DRI-Kühler oder vom Wärmetauscher zwischen dem Hochtemperatur- und dem Niedertemperatur-Shifter vorgewärmt wird.
Es gibt drei verschiedene Möglichkeiten, den Vergaser in den ULCORED DR-Prozess zu integrieren. Der Vergaser kann entweder als kaltes Syngas oder so integriert werden, dass die thermische Energie im heißen Gas aus dem Vergaser genutzt wird. Drei verschiedene Konfigurationen wurden in Abb. 3 gezeigt. Die Möglichkeit, überschüssiges H2 für das System zu produzieren, wird durch Bypass von gereinigtem Synthesegas direkt zu den Shifter-Einheiten ermöglicht.
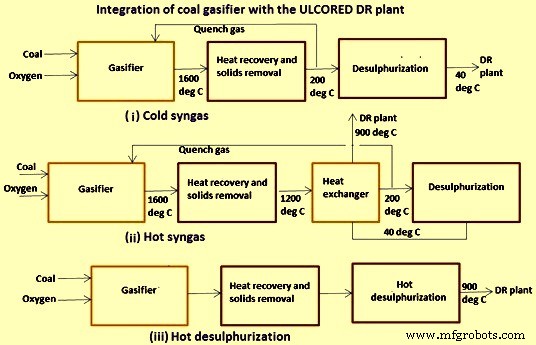
Abb. 3 Integration des Kohlevergasers mit der ULCORED DR-Anlage
Sauerstoff wird hauptsächlich im Kohlevergaser verbraucht, aber auch vor dem Schacht in einem kleinen POX, der für eine korrekte Temperatur des Reduktionsgases sorgt. Geshiftetes Gas ist Gas, das zum Shifter umgeleitet werden muss, um die richtige Zusammensetzung des Reduktionsgases sicherzustellen, d. h. die H2-Menge zu erhöhen. Entferntes CO2 ist die Menge an CO2, die im CO2-Entfernungsprozess aus dem Hauptprozessstrom abgetrennt wird. Das Fließschema des kohlebasierten ULCORED-Prozesses ist in Abb. 4 dargestellt.
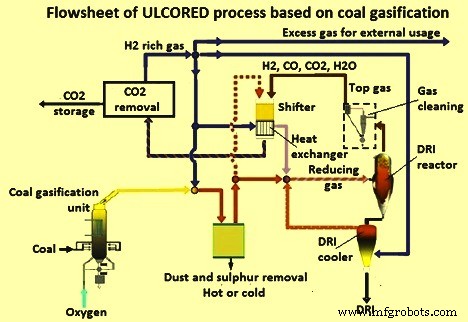
Abb. 4 Flussdiagramm des ULCORED-Prozesses basierend auf Kohlevergasung
Die Verwendung eines Kohlevergasers und eines Shifters im System ermöglicht es, einen Teil des Synthesegases direkt zum Shifter zu leiten, wodurch mehr Gas erzeugt wird, als für die Direktreduktionsanlage benötigt wird. Diese Funktion ermöglicht es, einen CO2-armen Brennstoff für das Stahlwerk zu erzeugen. Es macht es möglich, eine CO2-Quelle außerhalb des Systems zu haben, wodurch es möglich ist, im Grunde das gesamte im Stahlherstellungssystem erzeugte CO2 aufzufangen und zu speichern.
Aktueller Status des ULCORED DR-Prozesses
Eingehende grundlegende Modellstudien für das ULCORED DR-Verfahren wurden abgeschlossen. Diese Modellstudien umfassten Modelle im Pelletmaßstab, Wellenmodelle und Prozessmodelle durch Fließschemasimulationen. Die Modellstudien haben zum grundlegenden Verständnis des DR-Prozesses einschließlich seiner Dynamik beigetragen. Die Fließbildmodellierung hat bei der Optimierung des Prozesslayouts geholfen, um den ULCORED DR-Prozess in die Umgebung eines Stahlwerks zu integrieren. Verschiedene Ansätze, die während der Modellierungsstudien gewählt wurden, haben zu ähnlichen Ergebnissen geführt. Diese Studien haben eine glaubwürdige Grundlage für die Bewertung des Konzepts in verschiedenen Szenarien geschaffen. Materialbilanzierung, Massenbilanzierung, Energiebilanzierung und CO2-Emissionsberechnungen wurden für eine Tonne kalter DRI-Ausgabe mit 92 % Metallisierung und 2,76 % C durchgeführt.
Eine der interessanten Optionen einer ULCORED DR-Anlage ist die Produktion von LRI (weniger reduziertes Eisen) und ein konventioneller oder N2-freier Hochofen (BF) zur Herstellung des Roheisens (HM) mit einer zusätzlichen Einsparung von CO2-Emissionen. LRI ist eine alternative Wahl anstelle von DRI angesichts der erfolgreichen Tests, die im experimentellen BF von LKAB durchgeführt wurden. Der LRI-Test mit einem auf nur 65 % Metallisierungsgrad reduzierten DR-Produkt reagierte im BF sehr positiv mit einem bemerkenswert stabilen Ofenzustand und einem niedrigen Koksverbrauch, der unter 200 kg/tSM lag.
Das Ergebnis dieser Studien ist, dass das ULCORED DR-Verfahren eine „schnelle Lösung“ für eine Reduzierung der CO2-Emissionen auf Brachflächen sein kann, insbesondere dort, wo Erdgas relativ billig ist. Im Falle eines integrierten Stahlwerks mit BF-Route kann LRI angesichts der erfolgreichen Tests, die im LKAB-Experimental-BF durchgeführt wurden, eine Wahl sein.
Das ULCORED DR-Verfahren muss zunächst in einem Pilotversuch getestet werden, ein Schritt, der die Gelegenheit des EDRP-Ofens (Experimental Direct Reduction Pilot) nutzen könnte, den LKAB in den kommenden Jahren als Ergänzung zu seinem experimentellen BF in Lulea, Schweden, errichten will. Die Spezifikationen des EDRP sind (i) 1 Tonne Eisen pro Stunde Produktion, (ii) Rezirkulation des Topgases, (iii) Arbeitsdruckbereich von 0 kg/cm² bis 8 kg/cm² im Schachtofen, (iv ) Gasfluss im Bereich von 1700 N cum bis 3100 N cum pro Stunde und (v) Temperatur des Schachtofens im Bereich von 900 °C bis 1050 °C.
ULCORED wird wahrscheinlich ein Kandidat für die Nachrüstung bestehender Direktreduktionsanlagen sein, sobald seine Realisierbarkeit im Pilot- und dann im Demonstrationsmaßstab nachgewiesen wurde, was ebenfalls 10 bis 15 Jahre oder mehr dauern würde.
Herstellungsprozess