Unterschiedliche Schneidprozessanforderungen für Schneidflüssigkeiten
Metallschneidflüssigkeit wird als Schneidflüssigkeit abgekürzt; Die Schmierwirkung im Schneidprozess kann die Reibung zwischen der Spanfläche und den Spänen sowie der Freifläche und der bearbeiteten Oberfläche verringern, die Teil des Schmierfilms sind, wodurch die Schnittkraft, die Reibung und der Stromverbrauch verringert werden, die Oberflächentemperatur und das Werkzeug verringert werden Verschleiß des Reibungsteils zwischen Werkzeug und Werkstückrohling und Verbesserung der Schnittleistung des Werkstückmaterials.
Unterschiedliche Schneidprozesse stellen unterschiedliche Anforderungen an die Schneidflüssigkeit. Die richtige Auswahl des geeigneten Kühlschmierstoffs ist sehr wichtig für die Qualität des Werkstücks.
R ob T urn
Beim Schruppdrehen ist die Bearbeitungszugabe groß, sodass die Schnitttiefe und der Vorschub groß sind, der Schnittwiderstand groß ist, eine große Menge an Schnittwärme erzeugt wird und der Werkzeugverschleiß ebenfalls schwerwiegend ist. Es sollte hauptsächlich zum Kühlen und mit gewissem Reinigen, Schmieren und Rostschutz verwendet werden. Die effektive Schneidflüssigkeit auf Wasserbasis leitet die Schnittwärme rechtzeitig ab, reduziert die Schnitttemperatur und verbessert die Standzeit des Werkzeugs. Im Allgemeinen ist es besser, eine Hochdruckemulsion zu verwenden. Neben einer guten Kühlleistung haben EP-Emulsionen auch eine gute EP-Schmierfähigkeit. Achten Sie bei der Verwendung von wasserbasiertem Kühlschmierstoff auf die Pflege der Führungsschienenoberfläche der Werkzeugmaschine. Trocknen Sie die Schneidflüssigkeit auf der Werkbank und tragen Sie Schmiermittel auf, bevor Sie die Arbeit verlassen.
F Fertigstellung T urn
Beim Fertigdrehen ist die Schnittzugabe klein, die Schnitttiefe beträgt im Allgemeinen nur 0,05-0,8 mm und die Die Vorschubgeschwindigkeit ist ebenfalls gering. Es ist erforderlich, um die Genauigkeit und Oberflächenrauheit des Werkstücks sicherzustellen. Aufgrund der geringen Schnittkraft und niedrigen Temperatur beim Fertigdrehen sollten Kühlschmierstoffe mit niedrigem Reibungskoeffizienten und guter Schmierleistung verwendet werden. Generell sollten hochkonzentrierte (Massenanteil über 10%) Emulsionen und Kühlschmierstoffe mit öligen Zusätzen verwendet werden. Beim Drehen mit hohen Genauigkeitsanforderungen, wie Feingewinden, müssen Rapsöl, Sojaöl oder andere Produkte als Schmierflüssigkeit verwendet werden, um die Genauigkeitsanforderungen zu erfüllen. Wie oben erwähnt, verwenden einige Fabriken aufgrund der geringen Stabilität von Pflanzenölen und der leichten Oxidation (Massenanteil) JQ-1-Präzisionsschneidschmiermittel mit 15 % und L-AN32-Gesamtverlustsystemöl mit 85 % als Präzisionsschneidöle mit guten Ergebnissen.
Langweilig
Der Mechanismus des Bohrens ist derselbe wie der des Drehens, aber es handelt sich um eine Innenlochbearbeitung, der Schnittbetrag und die Schnittgeschwindigkeit sind nicht groß, aber die Wärmeableitungsbedingungen sind schlecht, die Emulsion kann als Schneidflüssigkeit verwendet werden, und der Fluss und Druck der Schneidflüssigkeit sollten gegebenenfalls entsprechend erhöht werden.
Fräsen
Fräsen ist intermittierendes Schneiden. Die Schnitttiefe jedes Zahns ändert sich von Zeit zu Zeit, was zu Vibrationen und einem gewissen Schlag führt, sodass die Fräsbedingungen schlechter sind als beim Drehen. Beim Einsatz von Schnellarbeitsstahlwerkzeugen zum Hochgeschwindigkeits-Flachfräsen oder Hochgeschwindigkeits-Schaftfräsen sind Kühlschmierstoffe mit guten Kühleigenschaften und bestimmten Schmiereigenschaften erforderlich, wie z. B. Hochdruckemulsionen. Beim Niedriggeschwindigkeitsfräsen ist Schneidöl mit guter Schmierfähigkeit erforderlich, wie z. B. Präzisionsschneidöl und inaktives Hochdruckschneidöl. Für rostfreien Stahl und hitzebeständigen legierten Stahl kann Schneidöl verwendet werden, das Schwefel- und Chlor-Hochdruckzusätze enthält.
Reiben
Reiben ist das Schlichten von Löchern und erfordert eine hohe Präzision. Reiben ist ein Schneiden mit niedriger Geschwindigkeit und kleinem Vorschub, hauptsächlich weil das Werkzeug und die Lochwand gequetscht und geschnitten werden und die Spanfragmente leicht in der Nut bleiben oder an der Kante der Klinge haften bleiben, was den Quetscheffekt beeinträchtigt von dem Land. Zerstören Bearbeitungsgenauigkeit und Oberflächenrauheit, erhöhen das Schnittmoment, erzeugen aber auch Aufbauschneiden und erhöhen den Werkzeugverschleiß. Reiben gehört grundsätzlich zum Zustand der Grenzschmierung. Im Allgemeinen können hochkonzentrierte Hochdruckemulsionen oder Hochdruckschneidöle mit guter Schmierfähigkeit und bestimmter Fließfähigkeit verwendet werden, um gute Ergebnisse zu erzielen. Für rostfreien und hitzebeständigen Stahl kann eine zusammengesetzte Schneidflüssigkeit mit hohem Hochdruck verwendet werden. Zum Tiefbohren kann Tieflochbohr-Schneidöl mit guter Schmierleistung die technologischen Anforderungen erfüllen.
Räumung
Die Räumnadel ist ein Bearbeitungswerkzeug, bei dem eine große Anzahl von Zähnen entlang der axialen Richtung entsprechend den Zähnen der Klinge angeordnet ist. Das Räumen zeichnet sich dadurch aus, dass es Werkstücke mit komplexen Formen mit hoher Präzision bearbeiten kann. Da die Räumnadel ein wertvolles Werkzeug ist, wirkt sich die Haltbarkeit des Werkzeugs stärker auf die Produktionskosten aus. Darüber hinaus ist das Räumen eine Endbearbeitung, die strenge Anforderungen an die Oberflächenrauheit des Werkstücks stellt. Beim Räumen ist der Schneidwiderstand groß, die Spanabfuhr schwierig, die Kühlbedingungen schlecht und die Oberfläche des Werkstücks wird leicht zerkratzt, so dass die Schmierfähigkeit und die Spanabfuhrleistung der Schneidflüssigkeit erforderlich sind. In China gibt es spezielle Räumöle mit schwefelhaltigen Hochdruckadditiven.
Zum Räumen von rostfreiem Stahl und hitzebeständigen Legierungen kann die folgende Formel (Massenanteil) verwendet werden:JQ-2 Hochdruckschmiermittel 20 %, Chlorparaffin 15 %, Benzol 80 verwendet 1 %, L-ANN22 Gesamtverlustsystemöl 64 %.
D Rillung
Das Bohren mit einem allgemeinen Spiralbohrer ist eine Schruppbearbeitung. Beim Bohren lassen sich die Späne nur schwer abführen und die Schnittwärme lässt sich nicht gut abführen, was häufig zum Ausglühen der Klinge führt, was sich auf die Lebensdauer und Bearbeitungseffizienz des Bohrers auswirkt. Die Wahl einer Schneidflüssigkeit mit guter Leistung kann die Lebensdauer des Bohrers um ein Vielfaches oder mehr verlängern und die Produktionseffizienz kann ebenfalls erheblich verbessert werden. Im Allgemeinen können Hochdruck-Emulsionen oder synthetische Hochdruck-Schneidflüssigkeiten verwendet werden. Die synthetische Hochdruck-Schneidflüssigkeit hat eine niedrige Oberflächenspannung und eine gute Durchlässigkeit. Es kann den Bohrer rechtzeitig kühlen, was sehr effektiv zur Verlängerung der Werkzeuglebensdauer und zur Verbesserung der Bearbeitungseffizienz beiträgt. Für schwer zerspanbare Materialien wie Edelstahl und hitzebeständige Legierungen können niedrigviskose Höchstdruck-Schneidöle verwendet werden.
Thread Bearbeitung
Beim Gewindeschneiden liegt das Werkzeug keilförmig am Schneidstoff an und die Schneide ist an drei Seiten vom Schneidstoff umgeben. Das Schneiddrehmoment ist groß und die Spanabfuhr ist schwierig. Die Wärme kann von den Spänen nicht rechtzeitig abgeführt werden. Das Werkzeug lässt sich leicht abnutzen, der Schneidabfall wird eingeklemmt und es treten leicht Vibrationen auf. Besonders beim Gewindeschneiden und Gewindeschneiden sind die Schnittbedingungen anspruchsvoller, und manchmal kommt es zu Absplitterungen und gebrochenen Gewindebohrern.
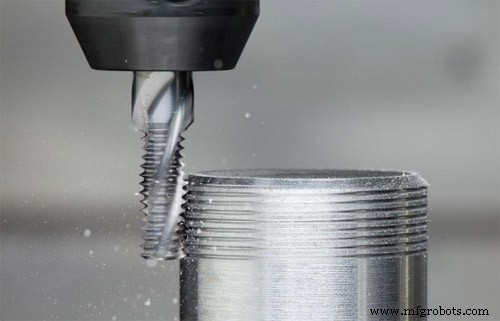
Die Schneidflüssigkeit muss gleichzeitig einen niedrigeren Reibungskoeffizienten und einen höheren Extremdruck aufweisen, um den Reibungswiderstand des Werkzeugs zu verringern und die Lebensdauer des Werkzeugs zu verlängern. Im Allgemeinen sollte eine zusammengesetzte Schneidflüssigkeit gewählt werden, die sowohl ölhaltiges Mittel als auch Hochdruckmittel enthält. Außerdem ist die Durchlässigkeit des Kühlschmierstoffs beim Schneiden des Gewindes sehr wichtig. Ob die Schneidflüssigkeit rechtzeitig in die Schneide eindringen kann, hat großen Einfluss auf die Haltbarkeit des Gewindebohrers. Die Durchlässigkeit von Schneidflüssigkeit hängt von der Viskosität ab. Öl mit niedriger Viskosität hat eine bessere Durchlässigkeit. Bei Bedarf kann zur Verbesserung der Durchlässigkeit eine kleine Menge Diesel oder Kerosin zugesetzt werden. In einigen Fällen ist es beim Gewindeschneiden von Sacklöchern schwierig, dass Schneidflüssigkeit in das Loch eindringt. In diesem Fall ist eine Schneidflüssigkeit mit hoher Viskosität und starker Haftung effektiver.
Hier sind einige Formeln (Massenanteil) von Schneidflüssigkeiten zum Gewindeschneiden:
- Sulfiertes fettes Öl 10 %, chloriertes Paraffin 10 %, fettes Öl 8 %, L-AN15-Gesamtverlustöl 72 %, geeignet für Schneidgewinde aus Stahl und legiertem Stahl.
- JQ-2 Hochdruckschmiermittel 20 %, JQ-1 Präzisionsschneidschmiermittel 10 %, L-AN15 Totalverlustsystemöl 70 %, geeignet zum Gewindebohren in Stahl und legiertem Stahl.
- JQ-2 Hochdruckschmiermittel 15 %, Dieselmotoröl 20 %, L-AN15 Gesamtverlustsystemöl 65 %, geeignet für das Gewindebohren von Aluminium und Aluminiumlegierungen.
- JQ-2 Hochdruckschmiermittel 30 %, Chlorparaffin 10 %, Fettöl 10 %, L-AN32 Total Loss System Oil 50 %, geeignet für Edelstahl und Sacklochgewindebohren.
- Hochdruckemulgiertes Öl 20 % + Wasser 80 %, geeignet für die Gewindebearbeitung von Stahlnormteilen.
Schleifen
Die Schleifbearbeitung kann eine hohe Maßgenauigkeit und eine geringe Oberflächenrauheit erzielen. Beim Schleifen ist die Schleifgeschwindigkeit hoch, die Wärmeentwicklung ist groß und die Schleiftemperatur kann bis zu 800-1000 ℃ oder sogar noch höher sein. Es ist leicht, Oberflächenverbrennungen des Werkstücks und Oberflächenrisse und Teileverformungen aufgrund thermischer Belastung zu verursachen. Die Schleifscheibe trägt Passivierung und Schleifpartikel fallen ab, und Schleifstaub und Schleifscheibenpulver können leicht spritzen und auf die Oberfläche des Teils fallen, was die Verarbeitungsgenauigkeit und Oberflächenrauheit beeinträchtigt. Bei der Bearbeitung von zähen und plastischen Materialien kann der Schleifstaub leicht in den Spalt auf der Arbeitsfläche der Schleifscheibe gesteckt werden oder der Schleifstaub und das Bearbeitungsmetall werden auf der Oberfläche der Schleifscheibe verschmolzen, wodurch die Schleifscheibe entsteht verliert seine Schleiffähigkeit. Um die Schleiftemperatur zu senken, Schleifrückstände und Schleifscheibenpulver wegzuspülen und das Schleifverhältnis und die Oberflächenqualität des Werkstücks zu verbessern, ist es daher erforderlich, eine Schneidflüssigkeit mit guter Kühlleistung und Reinigungsleistung zu verwenden ein gewisses Maß an Schmierfähigkeit und Rostbeständigkeit.
1. Normales Schleifen:
Es können Rostschutzemulsion oder Sodawasser und synthetische Schneidflüssigkeit (Massenanteil) verwendet werden, wie z. B.:Rostschutzemulsion 2 %, Natriumnitrit 0,5 %, Natriumcarbonat 0,2 %, Wasser 97,3 %; 0,8 % Natriumnitrit, 0,3 % Natriumcarbonat, 0,5 % Glycerin, 98,6 % Wasser; verwenden Sie direkt 3%-4% Anti-Rost-Emulsion oder chemische Syntheseflüssigkeit.
Beim Präzisionsschleifen mit hohen Präzisionsanforderungen kann die Verwendung von H-1-Feinschleifflüssigkeit die Bearbeitungsgenauigkeit und Schleifeffizienz des Werkstücks erheblich verbessern, und die Verwendungskonzentration beträgt 4-5%.
2. Hochgeschwindigkeitsschleifen:
Das Schleifen mit einer Scheibengeschwindigkeit von mehr als 50 m/s wird üblicherweise als Hochgeschwindigkeitsschleifen bezeichnet. Wenn die lineare Geschwindigkeit der Schleifscheibe zunimmt, steigt die Schleiftemperatur erheblich an. Gemäß dem Test ist die Schleiftemperatur (durchschnittliche Temperatur des Werkstücks) bei einer Lineargeschwindigkeit der Schleifscheibe von 60 m/s etwa 50–70 % höher als bei 30 m/s; Wenn die Lineargeschwindigkeit der Schleifscheibe 80 m/s beträgt, ist die Schleiftemperatur höher als bei 60 m/s. 15-20% höher. Nachdem die lineare Geschwindigkeit der Schleifscheibe erhöht wurde, nimmt die Anzahl der am Schleifen in einer Zeiteinheit beteiligten Schleifpartikel zu, die Reibung wird intensiviert und der Energieverbrauch wird ebenfalls erhöht, was die Oberflächentemperatur des Werkstücks erhöht und erhöht die Möglichkeit von Verbrennungen und Rissen auf der Oberfläche. Zur Lösung Kühlmittel mit effizienter Kühlleistung verwenden. Daher können beim Hochgeschwindigkeitsschleifen keine gewöhnlichen Schleifflüssigkeiten verwendet werden, es sollten jedoch Hochgeschwindigkeits-Schleifflüssigkeiten mit guter Penetrations- und Kühlleistung verwendet werden. Beispielsweise können GMY-Hochgeschwindigkeits-Schleifflüssigkeiten den Hochgeschwindigkeits-Schleifprozess mit einer linearen Geschwindigkeit von 60 m/s beanspruchen.
3. Kraftschleifen:
Dies ist ein fortschrittlicher hocheffizienter Schleifprozess. Beispielsweise wird beim Einstech-Hochgeschwindigkeits- und Kraftschleifen eine Schleifscheibe mit einer linearen Geschwindigkeit von 60 m/s radial mit einer Vorschubgeschwindigkeit von 3,5–6 mm/min geschnitten. Die Rate kann bis zu 20–40 mm3/mm.s betragen. Zu diesem Zeitpunkt ist die Reibung zwischen den Schleifpartikeln der Schleifscheibe und dem Werkstück sehr stark. Selbst unter den Kühlbedingungen mit hohem Druck und großem Durchfluss beträgt der Temperaturbereich der Oberflächenschicht des Werkstücks in der Reibungszone 700-1000 ℃. Nein, der Mahlvorgang ist nicht möglich. Beim Einstechmahlen wird im Vergleich zum Emulsionsmahlen das Gesamtmahlvolumen um 35 % erhöht, das Mahlverhältnis um 30–50 % erhöht und die normale Mahldauer um etwa 40 % verlängert. Der Leistungsverlust beträgt ca. 40 %. Daher hat die Leistung des Kühlmittels beim starken Schleifen einen großen Einfluss auf die Schleifwirkung. Derzeit umfassen die im Inland hergestellten starken Schleifflüssigkeiten QM starke Hochgeschwindigkeits-Schleifflüssigkeit und HM langsame starke Schleifflüssigkeit.
4. Schleifen von Diamantschleifscheiben:
Dies wird zum Schleifen von Hartlegierungen, Keramik, Glas und anderen Materialien mit hoher Härte verwendet. Es kann grob und fein gemahlen sein. Die geschliffene Oberfläche erzeugt im Allgemeinen keine Risse oder Lücken, wodurch eine bessere geringe Oberflächenrauheit erreicht werden kann. Um eine übermäßige Wärmeentwicklung beim Schleifen und einen vorzeitigen Verschleiß der Schleifscheibe zu verhindern und um eine geringere Oberflächenrauhigkeit zu erhalten, ist eine kontinuierliche und ausreichende Kühlung erforderlich. Aufgrund der hohen Härte des Werkstücks sollte die Schleifflüssigkeit vor allem Kühl- und Reinigungsleistung haben, um die Schleifscheibe scharf zu halten. Der Reibungskoeffizient der Schleifflüssigkeit sollte nicht zu niedrig sein, da es sonst zu einer geringen Schleifleistung und Oberflächenverbrennungen kommt. Als Schleifflüssigkeit wird eine chemisch-synthetische Flüssigkeit auf Basis anorganischer Salze verwendet. Beim Feinschleifen kann eine kleine Menge Polyethylenglykol als Schmiermittel zugesetzt werden, was die Oberflächenbearbeitungsqualität des Werkstücks verbessern kann. Für Teile mit hoher Bearbeitungsgenauigkeit können niedrigviskose Schleifflüssigkeiten auf Ölbasis mit guten Schmiereigenschaften verwendet werden.
5. Gewinde-, Zahnrad- und Schraubenschleifen:
Bei dieser Art des Schleifens wird besonderes Augenmerk auf die Qualität und Maßhaltigkeit der bearbeiteten Oberfläche nach dem Schleifen gelegt. Generell ist es ratsam, Schleiföle mit Hochdruckzusätzen zu verwenden. Diese Art von Schleifflüssigkeit auf Ölbasis ist auf ihre gute Schmierleistung zurückzuführen, kann die Schleifwärme reduzieren und die darin enthaltenen Hochdruckzusätze können mit dem Werkstückmaterial reagieren, um einen Eisensulfidfilm mit geringer Scherfestigkeit und einen Eisenchloridfilm zu erzeugen, die dies können Reduzieren Sie den Verschleiß der Schneidkante des Schleifkorns und machen Sie das Schleifen reibungslos. Um bessere Kühl- und Reinigungseigenschaften zu erzielen und den Brandschutz zu gewährleisten, sollte ein Schleiföl mit niedriger Viskosität und hohem Flammpunkt gewählt werden.
Herstellungsprozess
- Entdecken Sie eine Reihe von Messerschneidemaschinen für verschiedene industrielle Anwendungen
- VERFAHREN ZUR HERSTELLUNG VON KUNSTSTOFFVERPACKUNGEN FÜR VERSCHIEDENE MATERIALARTEN
- Finex-Verfahren zur Herstellung von flüssigem Eisen
- HIsarna-Prozess für die Eisenherstellung
- Technologien zur Verbesserung des Sinterprozesses
- CONARC-Prozess für die Stahlerzeugung
- Anforderungen an Drehwerkzeuge und Schneidflüssigkeiten aus Aluminiumlegierungen
- 5 Schneidprozess für Metall in der Fertigung
- CNC-Schneiden vs. Laserschneiden:Welches Verfahren ist besser für Sie?
- Was ist eine Klinge zum Schneiden?