Werden Getriebehersteller zum Unrunddrehen übergehen?
Weissers Hyperspeed Oval Turning (HOT)" heraus -of-round"-Bearbeitungseinheit ermöglicht unter anderem die Hart- und Weichbearbeitung von Hubkolben für Verbrennungsmotoren aus Aluminium und Stahl, gehärtete Nockenwellen, Mehrkantprofile oder -formen sowie Kfz-Kraftstoffpumpen.
Fahrzeuggetriebe sind weiter auf dem Vormarsch. Sie verwenden auch weiterhin Keil- und Schrumpfverbindungen für interne Wellenkomponenten. Reiner Jörg, Chefingenieur der Forschungs- und Entwicklungsabteilung des Werkzeugmaschinenbauers Weisser in Süddeutschland, sagt jedoch, dass Polygonkupplungen oder Polygon-Welle-Nabe-Verbindungen eine gute Alternative zu diesen traditionellen Verbindungsmethoden für Getriebekomponenten sind.
„Polygonkupplungen sind nichts Neues“, sagt er. „Das allgemeine Polygonsystem wurde entwickelt, um häufige Fehlerprobleme im Zusammenhang mit Keilwellen und Wellenbefestigungen mit Passfeder zu beseitigen. Es ist eine bewährte überlegene Methode zur Herstellung anspruchsvoller mechanischer Verbindungen, die stärker, präziser und mit einer wesentlich längeren Lebensdauer sind, da eine effektive Lastverteilung den Punkt praktisch eliminiert Kontakt, wodurch Stressermüdung und Verzerrung minimiert werden. Das Polygon hat eine größere Drehmomentkapazität als jede andere Wellenbefestigung. Die Kraftübertragung und Tragzahlen werden optimiert und oft kann eine kürzere Wellenverbindung verwendet und wertvoller Bauraum gespart werden. Weniger beschleunigte Masse auf kleinerem Raum wie Getriebe trägt zur oben erwähnten Kraftstoffeffizienz bei.“
Dennoch sagt er, dass Autohersteller Polygonkupplungen für ihre Getriebe noch einführen müssen. Ein Grund dafür ist, dass die Teile schwer zu bearbeiten sind. Die Unrunddrehtechnologie von Weisser könnte dies jedoch ändern, indem sie es Herstellern ermöglicht, fertige polygonale Formen in einer Aufspannung auf einer Maschine zu drehen. Eine solche Fähigkeit kann das Unrunddrehen zu einer effizienteren Alternative zu den Profilfräs- und Schleifprozessen machen, die typischerweise zur Herstellung herkömmlicher Welle-Nabe-Verbindungen in der Automobilindustrie verwendet werden.
Seit seiner Einführung im Jahr 1993 wird das Unrunddrehen zur Hart- und Weichbearbeitung von Hubkolben für Verbrennungsmotoren aus Aluminium und Stahl, gehärteten Nockenwellen, Mehrkantprofilen oder -formen sowie Kfz-Kraftstoffpumpen eingesetzt. Jetzt arbeitet Weisser an mehreren Projekten mit Erstausrüstern (OEMs), um zu demonstrieren, wie eine breitere Anwendung dieses Verfahrens es möglich machen könnte, traditionelle Welle-Nabe-Verbindungen durch Polygonkupplungen zu ersetzen.
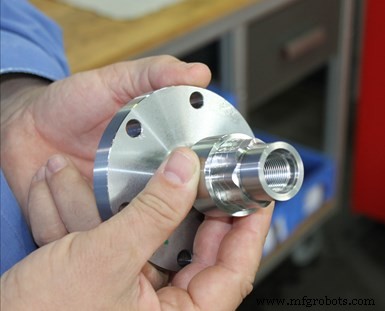
Polygonwellen wurden entwickelt, um allgemeine Fehlerprobleme zu beseitigen in Verbindung mit Keilwellen und Keilwellenbefestigungen. Das Polygon hat eine größere Drehmomentkapazität als jede andere Wellenbefestigung. Die Kraftübertragung und Tragzahlen werden optimiert und oft kann platzsparend eine kürzere Wellenverbindung verwendet werden.
Beispielsweise ist das Unrundbearbeitungssystem Hyperspeed Oval Turning (HOT) des Unternehmens eine separate Einheit, die in die vertikale Drehmaschine Vertor des Unternehmens integriert werden kann. Ovale oder unrunde Formen entstehen durch das Zusammenwirken der Werkstückspindelachse mit der durchmessererzeugenden Vorschubachse des Werkzeugs.
Die Werkzeugschneide bewegt sich in Richtung der X-Achse und senkrecht zur Werkstückspindelachse. In dieser gedachten Ebene kann die Schneide variabel positioniert werden, um radiale und stirnseitige Konturen oder halbkugelförmige Unrundheiten zu erzeugen. Zur Beschleunigung der Ovaldreheinheiten setzt Weisser auf Linearantriebe statt auf Kugelgewindetriebe.
Die Kraft des dynamischen Antriebs wird teilweise für die Beschleunigung der Masse und teilweise als Krafteinwirkung auf die Werkzeugschneide während der Bearbeitung benötigt. Das Schneidwerkzeug kann in einer radial oszillierenden Bewegung um bis zu 130 Gs beschleunigt werden. Dieses Beschleunigungsniveau ist selbst für die neuesten CNCs von Siemens und Bosch Rexroth so extrem, dass die meisten Anwendungen Beschleunigungen von nur 30 bis 90 Gs erfordern.
„Die maximal zulässige Drehzahl des Werkstücks steht bei gegebener Unrundheit in Relation zur maximalen Beschleunigung des Werkzeugeinsatzes, wie sie der oszillierende Antrieb erzeugt. Eine Nennbeschleunigung von 30 Gs ermöglicht höchste Genauigkeit und die Erzeugung eines erstklassigen Oberflächenfinishs“, sagt Jörg.
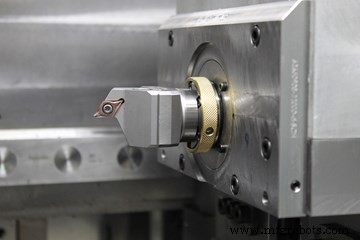
Die Bewegung der Werkzeugschneide ist in Richtung der X-Achse und damit senkrecht zur Werkstückspindelachse. In dieser gedachten Ebene kann die Schneide variabel positioniert werden, so dass radiale und stirnseitige Konturen oder halbkugelförmige Unrundheiten erzeugt werden können.
Trotz der hohen Nennbeschleunigung sollen spezielle stoßdämpfende Eigenschaften die Präzision gewährleisten, indem sie die Krafteinwirkung auf die Maschinengrundstruktur begrenzen. „Unser System kompensiert Beschleunigungskräfte, indem es Beschleunigungsarbeit in kinetische Energie umwandelt, sodass Maschinenschwingungen eliminiert und hohe Oberflächenqualitäten erreicht werden“, erklärt Jörg. „Durch die integrierte Schnittkraftkompensation können die Netto-Schnittkräfte (Passivkräfte) nahezu vollständig neutralisiert werden.“
Ein Kunde von Weisser fertigt Polygonnocken in weniger als einer Minute in einer Aufspannung und vier Drehdurchgängen inklusive Planbearbeitung und Anfasoperationen. Bei 1.500 U/min erzeugt die Unrunddreheinheit einen Vorschub von 0,1 mm pro Umdrehung und eine Schnitttiefe von 0,8 bis 2 mm. Die Teile werden mit einer Genauigkeit von ±10 Mikron fertig bearbeitet.
Ein anderer Kunde, der einen Schritt weiter gegangen ist als viele internationale Wettbewerber, hat bereits eine Polygonkupplung mit der HOT-Technologie von Weisser in ein neu entwickeltes Getriebe integriert. „Der Kunde hat im siebten Gang die Keilwelle durch eine Polygonwelle ersetzt, wodurch sich die Wellenlänge von 20 auf 12 mm reduzierte, da der Polygon eine größere Drehmomentkapazität hat als jede andere Wellenbefestigung“, sagt Jörg. „So kann eine kürzere Wellenverbindung verwendet und wertvoller Platz gespart werden.“ Die Platzersparnis trug dazu bei, das Übersetzungsverhältnis des ersten Gangs zu optimieren, der bei der ursprünglichen Konstruktion auf Ermüdungsprobleme stieß.
Mit der HOT-Technologie für Polygon-Welle-Nabe-Verbindungen hat Weisser bisher rund 100 Maschinen mit integrierter Unrunddreheinheit verkauft. Für eine noch flexiblere Bearbeitung bietet das Unternehmen seine Vertikaldrehmaschine Vertor C jetzt mit automatischem Werkzeugwechsler an. Laut Jörg ist die erreichbare Genauigkeit derzeit durch die Kapazität der CNC begrenzt. „Wenn Sie Ihre Maschine mit 1.800 U/min betreiben und Ihr Teil mit unserer Unrunddreheinheit mit einer Auflösung von einem Grad bearbeiten wollen, muss die Steuerung 9.180 Signale pro Sekunde verarbeiten. Wir sprechen hier von einer Auflösung im Bereich von Nanosekunden. Das ist der limitierende Faktor. Aber wir arbeiten daran, diese Systemgrenzen weiter auf die Bearbeitung im Mikrometer-Toleranzbereich einzuschränken.“
Industrielle Ausrüstung
- Was ist Getriebeöl und was bewirkt es?
- Drei Möglichkeiten, wie Hersteller in diesem Jahr die Servitisierung ausweiten
- Werden US-Hersteller von einer stärkeren "Buy American"-Richtlinie profitieren?
- Warum Hersteller von „Reborn in Digital“ die Konkurrenz übertreffen werden
- Die führenden Hersteller von Industriegetrieben
- CNC-Drehen einfacher machen
- Universal-Drehmaschinen
- Schrägbett-Drehzentren
- Drehen ist optional
- Ein Bearbeitungszentrum einschalten