Herstellung von nanoskaligen Gruben mit hohem Durchsatz auf Polymerdünnschicht unter Verwendung der AFM-Spitzen-basierten dynamischen Pfluglithographie
Zusammenfassung
Wir zeigen, dass ein auf Rasterkraftmikroskopen (AFM) basierender dynamischer Pfluglithographie (DPL)-Ansatz verwendet werden kann, um nanoskalige Gruben mit hohem Durchsatz herzustellen. Das Verfahren beruht darauf, im Tapping-Modus mit relativ großer Geschwindigkeit über eine Probenoberfläche zu kratzen, was für den Abstand benachbarter Pits verantwortlich ist. Kratztests werden an einem dünnen Film aus Poly(methylmethacrylat) (PMMA) unter Verwendung einer diamantähnlichen Kohlenstoffbeschichtungsspitze durchgeführt. Die Ergebnisse zeigen, dass 100 μm/s der kritische Wert der Ritzgeschwindigkeit ist. Wenn die Ritzgeschwindigkeit größer als 100 μm/s ist, können Pit-Strukturen erzeugt werden. Im Gegensatz dazu können Nanorillen mit Geschwindigkeiten unter dem kritischen Wert gebildet werden. Aufgrund der Schwierigkeit, die Molekülkette eines Polymers im Glaszustand mit einer aufgebrachten Hochfrequenzlast und einer geringen Energiedissipation in einer Wechselwirkung der Spitze und der Probe zu brechen, erfordert eine Vertiefung 65–80 Durchdringungen. Anschließend wird der Umformprozess der Grube im Detail analysiert, der drei Phasen umfasst:elastische Verformung, plastische Verformung und Überklettern der Aufschüttung. Insbesondere können mit dieser vorgeschlagenen Methode 4800–5800 Gruben in 1 s erhalten werden. Sowohl Experimente als auch theoretische Analysen werden vorgestellt, die das Potenzial dieser vorgeschlagenen Methode zur effizienten Herstellung von Gruben vollständig bestimmen.
Hintergrund
Die jüngste und rasante Entwicklung der Nanotechnologie hat der Anwendung von Nanostrukturen in verschiedenen Bereichen, wie nanoelektromechanischen Systemen, Nanosensoren und Nanophotonik, zunehmend Aufmerksamkeit geschenkt. Insbesondere Nanodots, definiert als eindimensionale Nanostrukturen, werden häufig in den Bereichen der hochdichten Speicherung und Herstellung von Quantenpunkten eingesetzt [1]. Die effiziente Herstellung von Nanodots steht jedoch immer noch vor enormen Herausforderungen. Viele Wissenschaftler haben verschiedene Methoden vorgeschlagen, um Nanopunkte auf einer Vielzahl von Materialien herzustellen. Unter diesen wird die chemische Synthesemethode häufig verwendet, um Nanopunkte für die meisten Eigenschaftendetektions- und nanoskaligen Geräte zu erhalten [2]. Allerdings ist es mit dieser Methode schwierig, die Abmessungen und die räumliche Verteilung der Nanopunkte zu bestimmen. Dies führt zu einem erhöhten Aufwand für Ortung und Manipulation in nachfolgenden Prozessen. Daher haben viele Wissenschaftler Ressourcen der Erforschung kontrollierbarerer Methoden gewidmet, um Nanopunktstrukturen mit Abmessungen von mehreren Nanometern zu erhalten, wie z. B. fokussierte Ionenstrahllithographie [3], Elektronenstrahllithographie [4] und Nanoimprint-Lithographie [5]. Die Komplexität, die strengen Umweltauflagen und/oder die hohen Kosten erschweren jedoch die Anwendung dieser Techniken stark.
Seit der Erfindung des Rasterkraftmikroskops (AFM) im Jahr 1986 wird es häufig als hochpräzises Oberflächenprofiler verwendet [6]. Wenn die Wechselwirkungskraft zwischen der AFM-Spitze und der Probe auf einen relativ großen Wert vergrößert wird, beispielsweise mehrere hundert Nanonewton oder sogar mehrere hundert Mikronewton, kann das Probenmaterial mit der scharfen Spitze plastisch abgetragen werden, ähnlich einem kleinen Schneidwerkzeug [7 ]. Chemische und thermische Energien wurden auch in das AFM-System durch lokale Oxidation [8] oder Erhitzen der Probe [9] eingebracht, um das Entfernen von Probenmaterial zu unterstützen. Es führt daher zu einigen neuen Herstellungsverfahren, um den Anwendungsbereich der bestehenden AFM-Spitzen-basierten Nanolithographie (TBN)-Verfahren zu erweitern. Unter allen TBN-Methoden ist die mechanische Entfernungsmethode die einfachste und flexibelste [10]. Dieses Verfahren besteht zunächst aus Eindrücken und anschließendem Kratzen auf verschiedenen Materialien, bei denen die Spitze-Material-Wechselwirkung stark von der Art des Materials abhängt, wie beispielsweise Metalle [11], Halbleiter [12, 13] und Polymere [14]. Durch die präzise Steuerung der Spitze-Material-Wechselwirkung auf der Nanoskala wurden komplexe und hochpräzise Nanostrukturen wie Nanopunkte, Nanorillen und sogar 3D-Nanostrukturen erfolgreich hergestellt. Insbesondere haben einige Wissenschaftler AFM-Spitzen-basierte Nanoindentationsverfahren auf der Oberfläche von Halbleitermaterialien durchgeführt, um Nanopunktstrukturen zu erhalten [15, 16]. In ihren Studien wurde festgestellt, dass die durch Nanoindentation verursachten kristallinen Defekte Nukleationsstellen für InAs-Nanostrukturen sind. Die relativ große Härte der Halbleitermaterialien könnte jedoch zu ernsthaftem Spitzenverschleiß führen. Daher haben einige Forscher vorgeschlagen, den Nanoindentationsprozess auf weicheren Materialien, wie beispielsweise Polymer-Dünnfilmresist, durchzuführen, um zunächst Nanopunktstrukturen herzustellen. Diese Nanodot-Strukturen könnten dann durch reaktives Ionenätzen (RIE) oder Nassätzverfahren auf Halbleitermaterialien übertragen werden [17]. Aufgrund ihrer geringen Härte und ultradünnen Dicke konnte die Resistschicht mit relativ geringer Normalbelastung durchdrungen werden. Einige Wissenschaftler haben einen zweistufigen Ritzansatz vorgeschlagen, um Nanodot-Arrays auf einer Polycarbonatoberfläche zu erhalten [18]. Dieses Verfahren beruht auf den Wellen der Materialien, die durch den AFM-Spitzen-basierten kraftkonstanten Kratzprozess gebildet werden. Der Abstand zwischen benachbarten Nanopunkten hängt jedoch nur von der Geometrie der AFM-Spitze ab, und der Bildungsmechanismus der Nanopunkte bleibt unklar.
Auf der anderen Seite ist ein geringer Durchsatz ein kritischer Faktor, der die Entwicklung von Nanofabrikationsverfahren auf Basis von AFM-Spitzen behindert. Es wurde gezeigt, dass der auf AFM-Spitzen basierende Nanoindentationsprozess zeitaufwendig ist, um großflächige Nanopunktstrukturen zu erhalten [19]. Um dieses Problem zu lösen, haben Vettiger et al. präsentierte das Konzept des „Tausendfüßlers“, der große Arrays von Mikroauslegern verwendet, die parallel arbeiten, um eine Ultra-High-Density-Bearbeitungsfähigkeit zu erreichen [20]. In Anbetracht des starken Spitzenverschleißes nach einem großflächigen Kratzprozess haben einige Wissenschaftler einen neuen intermittierenden Kontaktmodus vorgeschlagen, um die Wechselwirkungskraft zwischen Spitze und Probe zu reduzieren und somit den Spitzenverschleiß zu verringern [21, 22]. Die bei diesem Ansatz verwendeten großen Arrays von Mikroauslegern erfordern jedoch komplizierte Konstruktions- und Herstellungsverfahren, und es ist ein langwieriges Verfahren erforderlich, um die Position aller Spitzen auf einer Sonde einzustellen, um den Kontakt mit der Probe zu gewährleisten. Daher haben einige Forscher das kommerzielle AFM-System, einschließlich Hardware und Software, modifiziert, um die Hochgeschwindigkeitsbearbeitungsfähigkeit zu fördern [23,24,25]. Bei diesen Verfahren wurden Spitzen mit einem Ausleger verwendet. Mit diesen Ansätzen können jedoch nur Nanorillen effizient hergestellt werden, und auch das Kratzen mit großen Geschwindigkeiten könnte zu ernsthaftem Spitzenverschleiß führen. Neben der statischen Bearbeitung mit einer AFM-Spitze hat in letzter Zeit auch die AFM-Spitzen-basierte dynamische Pfluglithographie (DPL) immer mehr Aufmerksamkeit auf sich gezogen; dieser Vorgang wird mit dem Tapping-Modus des AFM-Systems durchgeführt. Wenn die Antriebsamplitude des Cantilevers erhöht wird, kann die AFM-Spitze die Probenoberfläche durchdringen, um den Bearbeitungsprozess zu erreichen [26,27,28]. Aufgrund des intermittierenden Kontakts zwischen Spitze und Probe beim DPL-Ansatz konnte der Spitzenverschleiß reduziert werden, ähnlich wie bei den in Lit. vorgeschlagenen Methoden. [21, 22]. Die durch das DPL-Verfahren erzielte Bearbeitungstiefe liegt normalerweise in der Größenordnung von wenigen Nanometern, was für die Herstellung von Nanostrukturen auf einem dünnen Film wie Polymer-Dünnfilm-Resist und zweidimensionalen Materialien geeignet ist [29]. Darüber hinaus könnte bei der DPL-Methode der Cantilever der AFM-Spitze zu Schwingungen mit mehreren Tausend Hertz angetrieben werden, was dazu führen würde, dass die Spitze in kurzer Zeit viele Male mit der Probenoberfläche wechselwirkt. Somit könnte die DPL-Methode ein potenzieller Ansatz sein, um nanoskalige Pit-Strukturen auf einer Dünnfilm-Probenoberfläche effizient herzustellen.
In dieser Studie wird eine Fast-Scan-Nanolithographie (FSN)-Methode vorgestellt, die auf dem DPL-Fertigungsansatz basiert und ein kommerzielles AFM-System verwendet. Abbildung 1a zeigt eine schematische Darstellung des Nanokratzprozesses mit einer diamantähnlichen Kohlenstoffbeschichtungsspitze, die eine Ansicht der Spitze in Kontakt mit einem dünnen Film aus Poly(methylmethacrylat) (PMMA) auf einem Siliziumsubstrat veranschaulicht. Der Ausleger wird nahe seiner Resonanzfrequenz angetrieben, um einen intermittierenden Kontakt zwischen der Spitze und der Probenoberfläche zu erzeugen. Die Antriebsamplitude der Spitze wird vom Steuersystem (AM-AFM) auf einem konstanten Wert gehalten. Das mit dem AFM-System ausgestattete Nanoman-Modul wird für alle Bearbeitungsverfahren verwendet, und die Ritzrichtung wird parallel zur Längsachse des Cantilevers gewählt. Der Einfluss der Kratzgeschwindigkeit auf die bearbeiteten Nanostrukturen wird untersucht. Darüber hinaus wird auch der Bildungsmechanismus der Pit-Struktur untersucht.
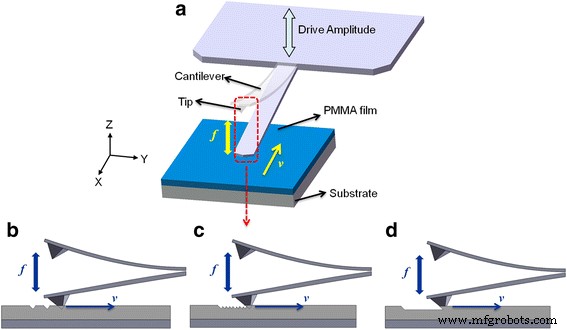
a Schematische Darstellung des Linienkratzprozesses auf PMMA-Folienoberfläche mit dem FSN-Verfahren. Der Cantilever schwingt auf seiner Resonanzfrequenz f in vertikaler Richtung. Die Kratzgeschwindigkeit v wird entlang der schnellen Abtastrichtung modifiziert. Es werden verschiedene Kratzgeschwindigkeitsbereiche dargestellt:b hohe Kratzgeschwindigkeit, c mittlere Kratzgeschwindigkeit und d niedrige Kratzgeschwindigkeit
Methoden
Die Konzentration der PMMA-Lösung beträgt 1,25 Gew.-%, hergestellt durch Auflösen des PMMA-Pulvers mit einem Molekulargewicht Mw = 120.000 in Chlorbenzol. Die PMMA-Filme werden hergestellt, indem die Lösung auf ein Stück eines einkristallinen Si-Substrats geschleudert wird, das durch aufeinanderfolgende Ultraschallbäder in Aceton und Alkohol für ungefähr 10 Minuten gereinigt wird. Die Rotationsgeschwindigkeit wird in den Experimenten auf 6000 U/min gewählt, um Filme mit Dicken von mehreren zehn Nanometern zu erzeugen. Nach dem Beschichtungsprozess werden PMMA-Filme bei 125 °C, was nahe der Glasübergangstemperatur von PMMA liegt, 30 Minuten lang nachgebrannt.
Die Experimente werden mit einem handelsüblichen AFM (Dimension Icon; Bruker Corporation, USA) betrieben. Es wird eine Siliziumspitze mit einer Nennfederkonstante von 42 N/m und einer Resonanzfrequenz von 320 kHz ausgewählt, die vom Hersteller (TESPD; Bruker Corporation, USA) bereitgestellt wird. Die Spitzenseite des Cantilevers ist mit einer diamantähnlichen Kohlenstoffbeschichtung (DLC) für eine längere Lebensdauer der Spitze gehärtet. Die Messung von Nanostrukturen auf der PMMA-Oberfläche erfolgt im Tapping-Modus mit einer Scanrate von 1 Hz und einer Scanlinie von 256. Bei Verwendung anderer Sonden muss das Cantilever-System abgestimmt werden. Der Einstellpunkt ist in dieser Studie auf etwa 300 mV abgestimmt. Die Bilder werden durch Abflachung erster Ordnung unter Verwendung der Nanoscope Analysis-Software von Bruker Company verarbeitet.
Das ausgerüstete Nanoman-Modul im AFM-System wird für den Scratch-Prozess in dieser Studie verwendet, der weit verbreitet ist, um die Flugbahn der Spitze zu entwerfen, um gewünschte Strukturen wie Rechtecke oder Kreise auf der Probenoberfläche zu erzielen. Um die Oberfläche zu modifizieren, sollte der Antriebsamplitudenwert der Spitze auf V . erhöht werden w (Schreiben), wobei die Wechselwirkung zwischen der Spitze und dem PMMA-Film gefördert wird, um sicherzustellen, dass die Spitze die Probenoberfläche durchdringt. Nach dem Ritzvorgang wird der Antriebsamplitudenwert der Spitze sofort auf V . abgesenkt r (Lesen) ohne den Cantilever zu verändern. Im Vergleich zum statischen Pfluglithographieverfahren erweist sich der Spitzenverschleiß beim DPL als sehr gering und kann daher vernachlässigt werden. Durch das Vermeiden des Wechsels der Sonde und der Suche nach der Position der Nanostruktur kann dieses in-situ-Bildgebungsverfahren die Effizienz des Ritzprozesses verbessern. Alle Experimente werden bei Raumtemperatur durchgeführt.
Ergebnisse und Diskussion
Unter Berücksichtigung der Geschwindigkeitsbegrenzung des AFM-PZT werden in den experimentellen Tests Kratzgeschwindigkeiten im Bereich von 0,1 bis 1000 μm/s gewählt. Abbildung 1 zeigt eine schematische Darstellung des Nanobearbeitungsprozesses mit drei Geschwindigkeitsbereichen. Beim Kratzen mit relativ hoher Geschwindigkeit (etwa mehrere hundert Mikrometer pro Sekunde) können separate Pits gebildet werden, wie in Fig. 1b gezeigt. Wenn sich die Kratzgeschwindigkeit auf einen mittleren Wert (etwa 100 μm/s) verlangsamt, können sich die Pits überlappen, wie in Abb. 1c gezeigt. Wie in Fig. 1d gezeigt, können die Grübchen in Nanorillen umgewandelt werden, wenn die Kratzgeschwindigkeit einen relativ kleinen Wert (dutzende Mikrometer pro Sekunde) erreicht. Dieses Ergebnis zeigt, dass der Abstand zwischen den beiden hergestellten Vertiefungen von der Kratzgeschwindigkeit abhängt, die einen großen Einfluss auf die hergestellten Nanomuster hat.
In dieser Studie werden vier typische Kratzrichtungen gewählt, wie in Abb. 2a gezeigt. V 1 und V 3 stellen das Kratzen entlang der Längsachse des Auslegers dar; V 2 und V 4 sind definiert als Kratzen senkrecht zur Längsachse des Auslegers. Die Spitzenflugbahnen werden durch Steuerung des AFM PZT erhalten. Abbildung 3 zeigt AFM-Bilder von Nanostrukturen mit quadratischen Linien, die mit unterschiedlichen Kratzgeschwindigkeiten hergestellt wurden, und die entsprechenden Querschnitte der Nanostrukturen, die mit der Richtung V . gekratzt wurden 1 , wenn die Resonanzfrequenz des Auslegers 380 kHz beträgt. Mit einer relativ großen Kratzgeschwindigkeit von 200 μm/s können kontinuierliche Pits gebildet werden, wie in Fig. 3a gezeigt. Bei vier im Voraus festgelegten Kratzrichtungen würden sich sofort Pits in weit weniger als 1 s bilden, obwohl die Kratzgeschwindigkeit am Wendepunkt der beiden Richtungen abrutscht. Bei einer mittleren Ritzgeschwindigkeit (100 μm/s) sind entlang des Bearbeitungspfads keine offensichtlichen Grübchen zu finden und es bilden sich fluktuierende Nanostrukturen, wie in Abb. 3b gezeigt. Am Schnittpunkt der beiden benachbarten Kratzpfade ist nur ein Pit mit viel größerer Tiefe zu beobachten, was wie folgt erklärt werden kann. Während der Transformationszeit zwischen den beiden benachbarten Ritzbahnen sollte sich die Ritzgeschwindigkeit auf 0 verlangsamen und die Spitze kann sich öfter als beim Ritzvorgang in die Probenoberfläche eindrücken, was der mögliche Grund für die Erzeugung einer größeren Tiefe sein kann der Grube. Die Kratzgeschwindigkeit von 100 μm/s kann als kritischer Wert für die Herstellung kontinuierlicher Vertiefungen auf einem PMMA-Dünnfilm angesehen werden. Abbildung 3c zeigt die bearbeiteten Nanorillen mit einer Ritzgeschwindigkeit von 50 μm/s. Aus dem Querschnitt der maschinell bearbeiteten Nanorille ist ersichtlich, dass der Boden der Nanorille relativ flach ist und eine offensichtliche Tiefe der Nanorille gebildet werden kann. Da die Spitze auf dem PMMA-Film pflügt, werden außerdem, wie in Fig. 3 gezeigt, während des Kratzens keine Späne gebildet, und es können nur Anhäufungen auf einer Seite oder beiden Seiten der Nut gebildet werden. Darüber hinaus sind die Profile der verschiedenen Seiten der erhaltenen Nanostrukturen beim Kratzen mit unterschiedlichen Richtungen inkonsistent, was den Ergebnissen bei statischer Lithographie mit einer asymmetrischen Spitze ähnelt. Bei anderen Resistmaterialien wie SU-8 oder Polystyrol (PS) unterscheiden sich die Schwellenwerte der Ritzgeschwindigkeit aufgrund des unterschiedlichen Spannungsrelaxationsmoduls von denen der PMMA-Folie. Ihre Schwellenwerte können jedoch durch das Scratching-Experiment erhalten werden, indem der gleiche Ansatz wie in dieser Studie verfolgt wird.
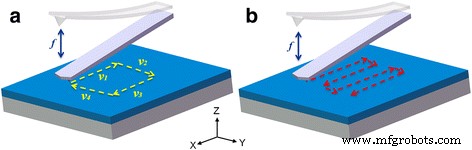
a Vier typische Kratzrichtungen (V 1 , V 2 , V 3 , und V 4 ) werden in dieser Studie für die Nanobearbeitung ausgewählt. b Die Spitzenbahn mit dem Vorschub für großflächige Muster
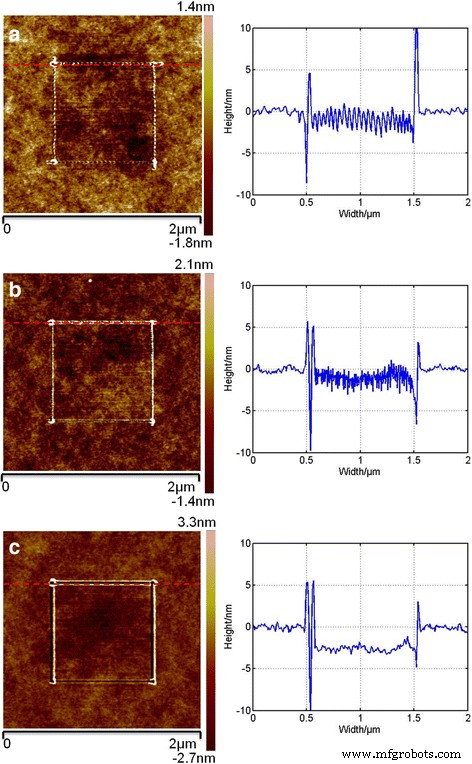
AFM-Bilder von drei Arten von Nanostrukturen und deren Querschnitt mit Kratzgeschwindigkeiten von a 200 μm/s, b 100 μm/s und c 50 μm/s
Bei Kratzgeschwindigkeiten von weniger als 100 μm/s können Nanorillen mit guter Qualität erhalten werden. Abbildung 4 zeigt die Beziehung zwischen der bearbeiteten Tiefe der Nanorille und der Ritzgeschwindigkeit mit den in Fig. 2a gezeigten unterschiedlichen Ritzrichtungen. Für jede Nanorille wird die experimentelle Tiefe durch den Durchschnitt von fünf Tiefenwerten an fünf verschiedenen Stellen berechnet. Die Kratzabstände für alle Kratzrichtungen sind gleich – 1 μm in dieser Studie. Es ist zu beobachten, dass die Bearbeitungstiefe mit zunehmender Ritzgeschwindigkeit für alle Ritzrichtungen abnimmt. Ein möglicher Grund lässt sich wie folgt erklären. Für einen in dieser Studie ausgewählten Ritzabstand von 1 μm beträgt die Anzahl der Pressvorgänge unter Ritzgeschwindigkeiten von 100 μm/s und 1 μm/s 3870 bzw. 387.000. Bei gleichem Ritzabstand kann eine große Anzahl von Pressvorgängen durch die AFM-Spitze zu einem relativ großen Überlappungsprozentsatz zwischen den benachbarten Pressvorgängen führen, was zu einer größeren Bearbeitungstiefe der Nanorille führen kann. Darüber hinaus sind, wie in Abb. 4 gezeigt, die Tiefen der in alle Richtungen geritzten Nanorillen konsistent, wenn die Ritzgeschwindigkeit weniger als 5 μm/s beträgt, während die Tiefe der in Richtung V . bearbeiteten Nanorillen 3 wird viel kleiner als die Bearbeitungstiefen, die durch andere Richtungen mit Ritzgeschwindigkeiten von mehr als 5 μm/s erhalten werden. Außerdem sind die Fehlerbalken der Bearbeitungstiefen in Richtung V 3 sind viel größer, wenn die Kratzgeschwindigkeit weniger als 5 μm/s beträgt, als bei anderen. Ein möglicher Grund lässt sich wie folgt erklären. Die in dieser Studie verwendete geometrische AFM-Sonde ist unsymmetrisch, und eine Neigung der Sonde, die durch die typische Auslegerneigung von 12° verursacht wird, um sicherzustellen, dass nur die AFM-Spitze die Probenoberfläche berührt, kann zu einer Differenz der Kontaktfläche führen zwischen Spitze und Probenoberfläche mit unterschiedlichen Kratzrichtungen. Bei einer Ritzgeschwindigkeit von weniger als 5 μm/s ist der Überlappungsbereich der benachbarten Pressvorgänge sehr groß. Somit ist auch die Kontaktfläche zwischen Spitze und Probenoberfläche extrem groß. Der Einfluss der Ritzrichtung auf die Bearbeitungstiefe kann daher vernachlässigbar sein. Der sich entlang der Spitzenoberfläche bildende Stapel ist jedoch auch abhängig von der Ritzrichtung, ähnlich dem statischen Ritzprozess. Daher kann die Anhäufung im V . nicht stetig gebildet werden 3 Richtung kratzen. Die eingefügten Zahlen in Abb. 4a, b sind die Querschnitte typischer Nanorillen, die mit Kratzgeschwindigkeiten von 0,5 bzw. 50 μm/s bearbeitet wurden. Vom Querschnitt der Nanorille, der mit einer Ritzgeschwindigkeit von 0,5 μm/s bearbeitet wurde, schwankt der Boden der Nanorille beim Kratzen im V 3 Richtung, was zu einem relativ großen Fehlerbalken für die bearbeitete Tiefe führen kann. Beim Kratzen mit einer Geschwindigkeit von mehr als 5 μm/s wird der Überlappungsbereich mit benachbarten Pressvorgängen klein. Somit spielt die Ritzrichtung eine wichtige Rolle, was zu einer relativ kleinen Bearbeitungstiefe führen kann, die im V . erreicht wird 3 Kratzrichtung.
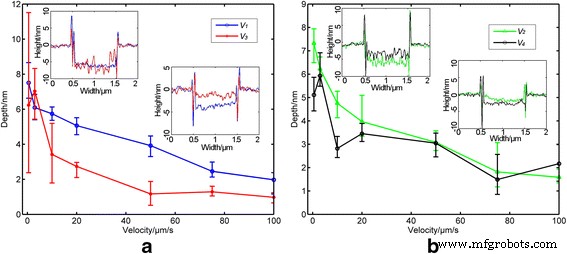
Abhängigkeit der Rillentiefe von der Ritzgeschwindigkeit in typischen Ritzrichtungen:a V 1 und V 3 , parallel zur Längsachse des Auslegers; b V 2 und V 4 , senkrecht zur Längsachse des Auslegers. Die Einschübe zeigen den Querschnitt von Nanorillen für Kratzgeschwindigkeiten von 0,5 und 50 μm/s
Ein PMMA-Dünnfilm ist eine Art zeitabhängiges und viskoelastisches Material. Daher kann die von der AFM-Spitze aufgebrachte periodische Last einen Einfluss auf den Young-Modul der Probe haben. Die allgemeine Darstellung für den Spannungsrelaxationsmodul G ist definiert durch G 1 und G 2 [30]:
$$ G\left(\omega \right)={G}_1\left(\omega \right)+{iG}_2\left(\omega \right) $$ (1) $$ {G}_1\left (\omega \right)=\left[{G}_r\right]+{\int}_{-\infty}^{+\infty}\frac{H\left(\tau\right){\omega} ^2{\tau}^2}{1+{\omega}^2{\tau}^2}d\left(\ln\tau\right) $$ (2) $$ {G}_2\left( \omega \right)={\int}_{-\infty}^{+\infty}\frac{H\left(\tau\right)\omega \tau}{1+{\omega}^2{\ tau}^2}d\left(\ln\tau\right) $$ (3)wo G r ist eine Konstante und ω hängt mit der frequenz zusammen. H (τ ) ist das zur Spannungsrelaxation beigetragene Relaxationszeitspektrum, das eine Beziehung zu den Relaxationszeiten zwischen lnτ . hat und lnτ + d (lnτ ). Wenn die Anregungsfrequenz auf einen Wert nahe der Resonanzfrequenz des Cantilevers eingestellt ist, die 387 kHz beträgt, kann der Modul einen hohen Wert erreichen. Aus der Berechnung mit den oben genannten Gleichungen ergibt sich, dass der PMMA-Dünnfilm bei einer angelegten Hochfrequenzbelastung als Glaszustand vorliegt [30]. Da der Gewindeschneidmodus während des gesamten Bearbeitungsprozesses verwendet wird, sind die Wechselwirkungskraft und die Energiedissipation zwischen der AFM-Spitze und der Probenoberfläche während des Ritzprozesses relativ klein, und sogar die Antriebsamplitude V w /V r ist auf einen relativ hohen Wert im Bereich von 10 bis 20 eingestellt. Bei diesen Bearbeitungsbedingungen können die Ketten zwischen den Polymermolekülen aufgrund der glasartigen Eigenschaft des PMMA-Dünnfilms und einer relativ geringen Belastung durch die AFM-Spitze nicht Es ist schwierig, gebrochene und plastische Verformungen zu erzeugen, um die Probenoberfläche durch einen Zyklus des Pressvorgangs zu modifizieren. Die Spitze hat jedoch während der ersten 20–30 Pressvorgänge genügend Energie (> 1~2 eV), um dies zu erreichen [27]. Somit können die Kettenbindungen zwischen den Polymermolekülen abgeschnitten werden, um eine plastische Verformung auf der Dünnfilmoberfläche zu erzeugen.
Der Abstand zwischen benachbarten Pressvorgängen ist ein kritischer Parameter, der eine Beziehung mit der Ritzgeschwindigkeit und der Schwingfrequenz der Spitze hat. Der Abstand einer Boxenlinie (L ) kann durch die Zeit erreicht werden, die für eine Boxenlinie verwendet wird (t ) multipliziert mit der Kratzgeschwindigkeit (v ). Die Gesamtzahl der AFM-Spitzenoszillationen in einer Grubenlinie (N ) kann über die Schwingfrequenz des Cantilevers berechnet werden (f ) multipliziert mit der Zeit (t ). Somit ist der Abstand zwischen benachbarten Pressvorgängen (D ) erhält man durch Gl. 4.
$$ D=\frac{L}{N}=\frac{v}{f} $$ (4)Die Eigenschwingungsfrequenz des in dieser Studie ausgewählten Cantilevers beträgt ungefähr 387 kHz. Die Antriebsfrequenz des AFM-Systems wird nahe diesem Wert gewählt. Wie oben erwähnt, sollte die Ritzgeschwindigkeit im Bereich von 200 bis 900 μm/s gewählt werden, um die Bildung der Grübchen zu gewährleisten. Somit ist der Abstand zwischen den benachbarten Pressvorgängen (D e ) während des Ritzvorgangs im Bereich von 0,52 bis 2,33 nm berechnet werden, was in Abb. 5a als rote Kurve bezeichnet ist. Die blaue Kurve in Abb. 5a stellt die Beziehung zwischen dem Abstand zwischen benachbarten Pits (D ) aus den Experimenten und der Kratzgeschwindigkeit erhalten. Die eingefügten AFM-Bilder werden für Pits erhalten, die mit drei typischen Ritzgeschwindigkeiten von 400, 600 und 800 μm/s bearbeitet wurden. Daher kann die Anzahl der Pressvorgänge für eine Grubenbildung als das Verhältnis von D zu D e in Abb. 5b gezeigt. Unter der Annahme, dass die Ritzgeschwindigkeit ein konstanter Wert ist, können 4800–5800 Pits auf einem PMMA-Dünnfilm in 1 s erzeugt werden, berechnet aus der Ritzlänge (L ) und der Abstand (D ). Aus Abb. 5b ist zu erkennen, dass die Anzahl der Pressvorgänge für eine Grubenbildung mit zunehmender Ritzgeschwindigkeit zunimmt und meist im Bereich von 65 bis 80 liegt. Betrachtet man das ebene Gelände zwischen den beiden Gruben, entspricht dies fast den Abmessungen von Pits sind nur etwa 32–40 Pressvorgänge erforderlich, um die Polymerketten zu brechen und eine plastische Verformung der Probenoberfläche zu erzeugen, was mit Cappellas Schlussfolgerung übereinstimmt [27]. Darüber hinaus lässt sich schlussfolgern, dass es beim Kratzen mit relativ geringer Geschwindigkeit leichter ist, die Polymerketten zu brechen. In dieser Studie ist die Federkonstante des Cantilevers identisch. Für die Herstellung von Pits könnte ein steiferer Cantilever verwendet werden, was zu einer größeren aufgebrachten Kraft und einer höheren Resonanzfrequenz führt. Wird eine größere Kraft auf die Probenoberfläche ausgeübt, erhöht sich der Energieeintrag in jedem Zyklus. Somit wird mehr Energiedissipation zur Verformung des PMMA-Films beigetragen. Ein Pit kann daher mit verringerten Zyklen erzeugt werden. Wenn jedoch die Resonanzfrequenz für das Schwingsystem erhöht wird, wird somit der Zyklus des Pressvorgangs zwischen der Probenoberfläche und der Spitze erhöht. Außerdem würde die Energiedissipation in einem Zyklus aufgrund des in den Experimenten verringerten Setzpunktes erhöht. Die kritische Geschwindigkeit kann durch den Wert des Einstellpunktes bestimmt werden. Basierend auf den obigen Diskussionen könnte der Schwellenwert der Geschwindigkeit durch die aufgebrachte Kraft, die Resonanzfrequenz des Cantilever-Systems und den Einstellpunkt beeinflusst werden, was im Mittelpunkt zukünftiger Untersuchungen stehen wird.
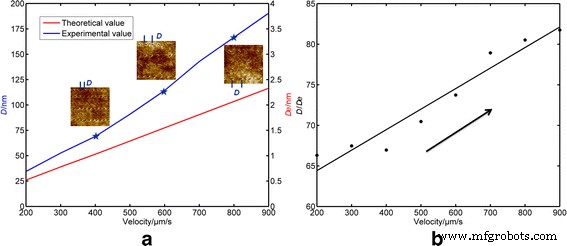
a Variation von D und D e mit Kratzgeschwindigkeit (200–900 μm/s); Einschübe zeigen Fertigungsergebnisse für verschiedene Kratzgeschwindigkeiten. b Verhältnis von D zu D e
Der Grubenbildungsprozess ist in Abb. 6 dargestellt und umfasst drei Phasen:elastische Verformung, plastische Verformung und Überklettern der Aufschüttung. Gemäß der obigen Diskussion ist während des Spitzenkratzens über den Abstand von Fig. 6a, b die Anzahl der Pressvorgänge nicht groß genug, um die Polymerketten des PMMA-Dünnfilms zu brechen und eine plastische Verformung der Probenoberfläche zu erzeugen. Es wurde gezeigt, dass die oszillierende Spitze während der ersten 40–50 Operationen allmählich in die Polymerprobe eindringt [27]. Verglichen mit dem Einrückungsverfahren in Ref. [27] könnte das Drücken mit seitlicher Geschwindigkeit einen Abstand zwischen zwei benachbarten Durchdringungen erzeugen. Der Abstand zwischen zwei benachbarten Durchdringungen (im Bereich von 0,52 bis 2,33 nm) ist jedoch viel kleiner als der Radius der AFM-Spitze (ungefähr 15 nm). Somit ist die Situation in dieser Studie ähnlich wie beim Einrückungsprozess. Aufgrund fehlender Energieakkumulation während der ersten 30–40 Durchdringungen ist im Bearbeitungsbereich keine offensichtliche plastische Verformung festzustellen. Dieses Ergebnis weist darauf hin, dass der vorherrschende Mechanismus der Energiedissipation die elastische Verformung im ersten Stadium des Kratzens ist. Somit gleitet die AFM-Spitze in kontinuierlichem Kontakt mit der Probenoberfläche während des Zeitraums zwischen Fig. 6a, b. Wenn die Anzahl der von der AFM-Spitze durchgeführten Penetrationen einen kritischen Wert erreicht (in dieser Studie das 40-fache), beginnen die Polymerketten zu brechen und es kommt zu einer plastischen Verformung, wie in Abb. 6c gezeigt. Gleichzeitig würde an der Wechselwirkungsfläche zwischen der Vorderseite der AFM-Spitze und dem Probenmaterial eine Normal- und Scherspannung auftreten; somit kann ein Pile-up vor der Vorderseite der AFM-Spitze erzeugt werden. Es würde eine Dehnung (Δ) auftreten, die auf die seitliche Spitzenbewegung gegen den Stapel zurückzuführen ist. Dies würde zu einer Spannung innerhalb des Polymerfilms führen, die durch Rissausbreitung abgebaut werden könnte [31]. Die Dehnungsenergiefreisetzungsrate V s kann wie folgt beschrieben werden:[32].
$$ {V}_s=E\frac{h}{2}{\left(\frac{\varDelta }{L}\right)}^2 $$ (5)wo E ist der Elastizitätsmodul des Polymermaterials und L ist die interne Defektlänge. h repräsentiert die gesamte Eindringtiefe in die freie Probenoberfläche. Der Oberflächenenergieterm W steuert den internen Defektprozess, der der Freisetzungsrate der Dehnungsenergie durch das thermodynamische Gleichgewicht entspricht. Der Oberflächenenergieterm ist abhängig von der Ausbreitungsgeschwindigkeit des internen Defekts (v L ), die gegeben ist durch [33].
$$ W={W}_0\left(1+\alpha {v}_L^n\right) $$ (6)wo v L ist gleich dL /dt und α ist ein konstanter Wert bezogen auf das Probenmaterial. n ist auch ein materialbezogener Parameter. Eine auf den Spitzenapex ausgeübte Tangentialkraft könnte durch die im Polymersubstrat gespeicherte elastische Energie erzeugt werden, die wie folgt ausgedrückt werden kann [32]:
$$ {F}_t=\frac{Eah}{2}\frac{\varDelta }{L} $$ (7)wo a repräsentiert den Radius der Kontaktfläche zwischen der Spitze und der Probe. Da die Steifigkeit der Sonde viel größer ist als die Steifigkeit der Probe, konnte das Material aus dem gebildeten Loch entfernt werden [31]. Mindlin definierte jedoch einen kritischen Kraftwert, der zum Abrutschen der Spitze auf der Substratoberfläche führen könnte [34]. Die kritische Tangentialkraft (F tc ) für die Gleitbewegung als Funktion der Haftkraft und der Normallast bestimmt werden, ausgedrückt als [35,36,37,38]:
$$ {F}_{tc}=\mu \left(P+3\pi RW+\sqrt{6\pi RW P+{\left(3\pi RW\right)}^2}\right) $$ ( 8)wobei μ ist der Reibungskoeffizient. P ist normal und R repräsentiert den Radius der AFM-Spitze. Wenn F t erreicht den kritischen Wert F tc , würde die AFM-Spitze über die Materialanhäufung gleiten, anstatt das Material aus dem von der Spitze erzeugten Loch zu drücken. Der Kontakt bricht bei jedem Zyklus, und somit kann der Schlupf bei jedem Zyklus im Gewindeschneidmodus leichter auftreten. Obwohl der Einstellpunkt nicht in der Nähe von 100% der Reduzierung der Spitzenoszillation liegt, kann während eines Zyklus eine Kontaktzeit auftreten und der Stick kann während dieser Zeit auftreten.
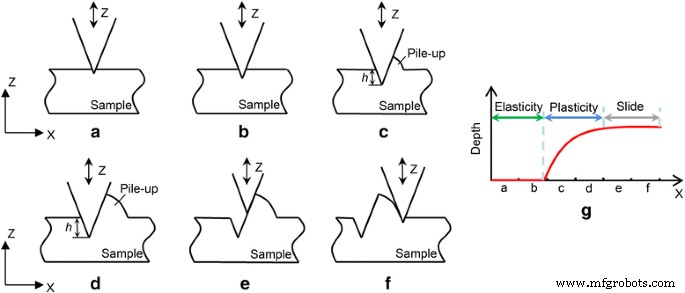
Schema der Grubenbildung mit a , b elasticity stage, c , d plasticity stage, e , f slide stage, and g precedence diagram of pit formation
As shown in Fig. 6d, in this study, the depth that the AFM tip penetrated into the sample surface becomes larger because of the decrease of the tip-sample contact area when the AFM tip undergoes a lateral velocity. The height of the pile-up is also increased. This could contribute to balancing the normal load applied by the AFM tip. At the same time, the tangential force applied on the tip apex described in Eq. 7 could also be increased. With an increasing penetration depth, the tangential force could reach the critical value F tc given in Eq. 8. The AFM tip starts to slide on the formed pile-up without modifying the material. Because of the characteristics of the tracking sample surface of the AFM system, the AFM tip would rise to climb over the pile-up, as shown in Fig. 6e. After the AFM tip moved over the pile-up, one pit could be achieved and another pit would be fabricated by repeating the above steps. The corresponding deformation mechanism of each stage of pit formation can be found in Fig. 6g.
According to the previous experimental results, the scratching velocity should be set to larger than 100 μm/s. As shown in Fig. 2b, scratching directions V 1 and V 3 are selected and a feed perpendicular to the scratching direction is conducted to achieve pit arrays with a large dimension of 5 μm. Figure 7a shows the pit arrays obtained with a scratching velocity of 400 μm/s. Figure 7b, c shows the local and 3D AFM images of the machined pits, respectively. Because the scratching velocity slows down to 0 near the transition point of two different scratching directions, the depths of the first and last pits of one horizontal scratching path are much larger than the pits in the middle. One possible reason is explained above. As shown in Fig. 7b, c, the pits in the middle of the scratching path are distributed evenly, which may result from the constant velocity. Moreover, it can be observed from the cross-section of the pits shown in Fig. 7d that the depths of the pits are approximately 2.5 nm. In addition, because of the opposite scratching directions of the adjacent paths, the geometries of the pits in adjacent lines are different. As shown in Fig. 8a, with a scratching velocity of 200 μm/s, the spacing distance between the adjacent pits is relatively small and the geometries of the pits are close to circular. From the fast Fourier transform (FFT) image of the pits, high-density pits can be obtained with a scratching velocity of 200 μm/s. When scratching with a velocity of 900 μm/s, as shown in Fig. 8b, the spacing distance is nearly 100 nm and differences between pits obtained with different scratching directions can be clearly observed. Also from the FFT image of the pits, with a scratching velocity of 900 μm/s, only low-density pits can be achieved.
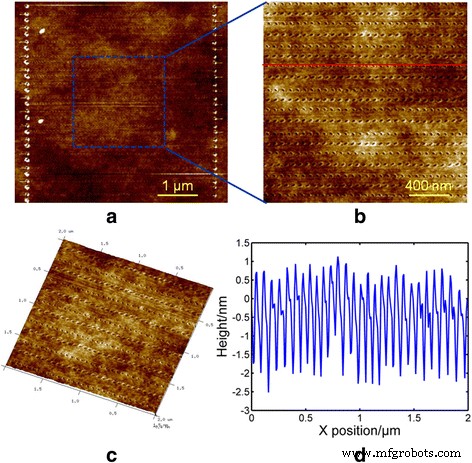
AFM images of an array of pits with a scratching velocity of 400 μm/s, a a dimension of 5 μm, b a portion of a with a dimension of 2 μm, c a 3D AFM image of b , and d a cross-section of pits for the red line in b
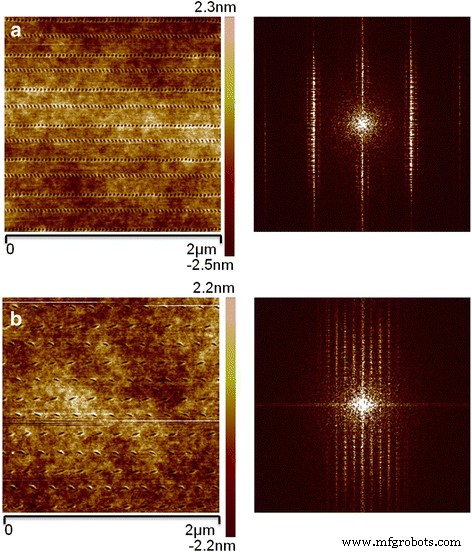
AFM image of pit arrary with a dimension of 2 μm and FFT image of the morphology. The scratching velocities are a 200 μm/s and b 900 μm/s
Conclusions
To improve the fabrication efficiency with the tip-based DPL method, a scratching velocity that ranges from 0.1 to 1000 μm/s is investigated and demonstrated based on the commercial AFM tapping mode. In the present study, results demonstrate that 100 μm/s is the critical value of the scratching velocity for the formation of pits. Nanogrooves with a pile-up can be obtained with scratching velocities less than the critical value. With scratching velocities greater than 5 μm/s, the machined depths are consistent in all typical directions except the V 3 direction, in which the machined depth becomes much smaller. In contrast, the depth is independent of the scratching direction. Separate pits can be generated with scratching velocities larger than the critical value of 100 μm/s. The total number of fabricated pits can reach nearly 4800–5800 in 1 s, when the scratching velocity is a constant value ranging from 200 to 900 μm/s. According to the stress relaxation modulus theory, the polymer surface is in the condition of a glass state when applying a high-frequency load. The energy applied on the sample surface is not large enough to break PMMA molecular chains during one penetration of the AFM tip. To form one pit, 65 to 80 penetrations are required. For the initial stage of penetration, elastic deformation is the dominant material removal mechanism. When the number of penetrations reaches 40 times, the polymer chains start to break and plastic deformation occurs. With increasing penetration depth, the height of the material accumulated beside the machined pit becomes larger, which will lead to an increase in the tangential force applied on the tip apex. This is the possible reason for the AFM tip sliding over the pile-up, after which one pit is created. Finally, pit arrays with dimensions of 5 μm, spacing distance of 70 nm, and machined depth of 2.5 nm are achieved successfully. FFT images are used to reveal the relationship between the density of pits and the scratching velocity.
Nanomaterialien
- AFM-Pioniere mit Kavli-Preis ausgezeichnet
- Stapelfertigung von Breitband-metallischen planaren Mikrolinsen und ihren Anordnungen, die die Selbstmontage von Nanosphären mit konventioneller Photolithographie kombinieren
- Herstellung eines geordneten Nanomusters unter Verwendung von ABC-Triblockcopolymer mit Salz in Toluol
- Hochdurchsatz-Herstellung hochwertiger Nanofasern unter Verwendung eines modifizierten Elektrospinnens mit freier Oberfläche
- Herstellung optischer Schaltmuster mit strukturellen farbigen Mikrofasern
- Maskenbasierte Beugungslithographie in einem Schritt zur Herstellung von schwebenden 3D-Strukturen
- Eine widerstandslose Spannungsreferenz im Nanomaßstab mit hohem PSRR
- Ge-pMOSFETs hoher Mobilität mit amorpher Si-Passivierung:Einfluss der Oberflächenorientierung
- Herstellung von Polydimethylsiloxan-Nanofluidik-Chips im AFM-Nanofräsprozess auf Spitzenbasis
- Stabile Polymertinte mit hoher Leitfähigkeit