IIAMS Wing Box Roadmap zur Zertifizierung
Abb. 7 „Zertifizierungsprozess der Modifikationen für den Prototyp“, der den Außenflügel FTB#2 umfasst. Bildnachweis: „Structural Radar Research of Airbus Defence and Space as Clean Sky Partnership“ von Manuel Iglesias Vallejo, Rubén Tejerina Hernanz, Antonio Jiménez, et al., Airbus Defence and Space, 8th European Conference for Aeronautics and Space Sciences (EUCASS), 1. Juli – 4, 2019.
Diese Online-Seitenleiste des Artikels „Advancing the OOA Infused Wing Box“ vom März 2021 enthält weitere Details dazu, wie Clean Sky 2-Projekte wie IIAMS in Roadmaps für die Reifung von Flüssigharzinfusions- (LRI) und thermoplastischen Verbundwerkstoffen (TPC) während des Abschlusses passen die Arbeit, die erforderlich ist, um sie in Verbundstrukturen außerhalb des Autoklaven (OOA) für Flugzeuge der nächsten Generation zu zertifizieren.
Airbus DS, FTB#2 und zukünftige Turboprop-Flugzeuge
Airbus Defence and Space (Airbus DS, Cadiz, Spanien) trat als EADS CASA in das Forschungs- und Technologieprogramm der Europäischen Union von Clean Sky ein. CASA wurde 1923 als Construcciones Aeronáuticas SA in Getafe, Spanien, gegründet und blickt auf eine lange Geschichte in der Flugzeugproduktion zurück und war eines der Gründungsmitglieder des Airbus-Konsortiums. Der zweite Standort wurde 1926 in Cadiz gegründet und das Unternehmen hat 22 Flugzeugmodelle sowie Komponenten für Airbus- und Eurofighter-Militärflugzeuge sowie für kommerzielle hergestellt Flugzeuge von Airbus und Boeing.
Sauberer Himmel 1 umfasst 7 Projektbereiche — 6 Integrated Technology Demonstrators (ITDs) und den Technology Evaluator. Die ITDs, die jeweils von zwei Industrieorganisationen gemeinsam geleitet werden, decken verschiedene Segmente des Luftverkehrs ab.
Sauberer Himmel 2 umfasst 9 Projektbereiche — 3 Innovative Aircraft Demonstrator Platforms (IADPs), 3 ITDs, 2 Transverse Activities und den Technology Evaluator.
https://www.cleansky.eu/discover
Airbus DS hat sich von einem Co-Leader des integrierten Technologiedemonstrators (ITD) des Green Regional Aircraft (GRA) im ursprünglichen Clean Sky entwickelt (2008-2017) zum Co-Leiter des AIRFRAME ITD sowie zum Leiter des Flugprüfstands 2 (FTB#2) in der REGIONAL Integrated Aircraft Demonstrator Platform (IADP) im Nachfolgeprogramm Clean Sky 2 Programm (2014-2024).
A.E. Jiménez Gahete vom Structures and Design, Engineering &Technology Directorate bei Airbus DS beschreibt die FTB#2-Entwicklung im Materiales Compuestos vom September 2020 Artikel mit dem Titel „Hochintegrierter Flügelkastenabschnitt von Airbus Defence and Space, hergestellt durch Trockenfaserplatzierung und Flüssigharzinfusion“. Diese Arbeit von Airbus DS in Clean Sky 2 wird auf ein zukünftiges militärisches Transportflugzeug oder ein kommerzielles regionales Turboprop-Flugzeug angewendet . Eines seiner Hauptziele ist die Entwicklung des Außenflügels für den FTB#2, der über Primärstrukturen aus OOA-Verbundwerkstoff verfügen wird, einschließlich eines integral versteiften Thermoplasts oberer Flügelkastendeckel aus Verbundwerkstoff und ein einteiliger One-Shot-Flügelkasten, hergestellt durch automatisierte Faserplatzierung (AFP) mit trockenen Faserbändern und Flüssigharzinfusion .
Letzteres ist in der Tat die Struktur, die MTorres im Rahmen des Clean Sky 2 IIAMS-Projekts entwickelt und produziert hat, wie in CompositesWorld . beschrieben 's März 2020 Artikel, „Die OOA-infundierte Wing Box voranbringen“. Bemerkenswert ist, dass dieser Flügelkasten die untere Haut, die vorderen und hinteren Holme integriert, jedoch nicht die obere Haut umfasst. Aus den unten abgebildeten Straßenkarten wird deutlich, dass die Oberhaut aus thermoplastischem Verbundmaterial besteht.
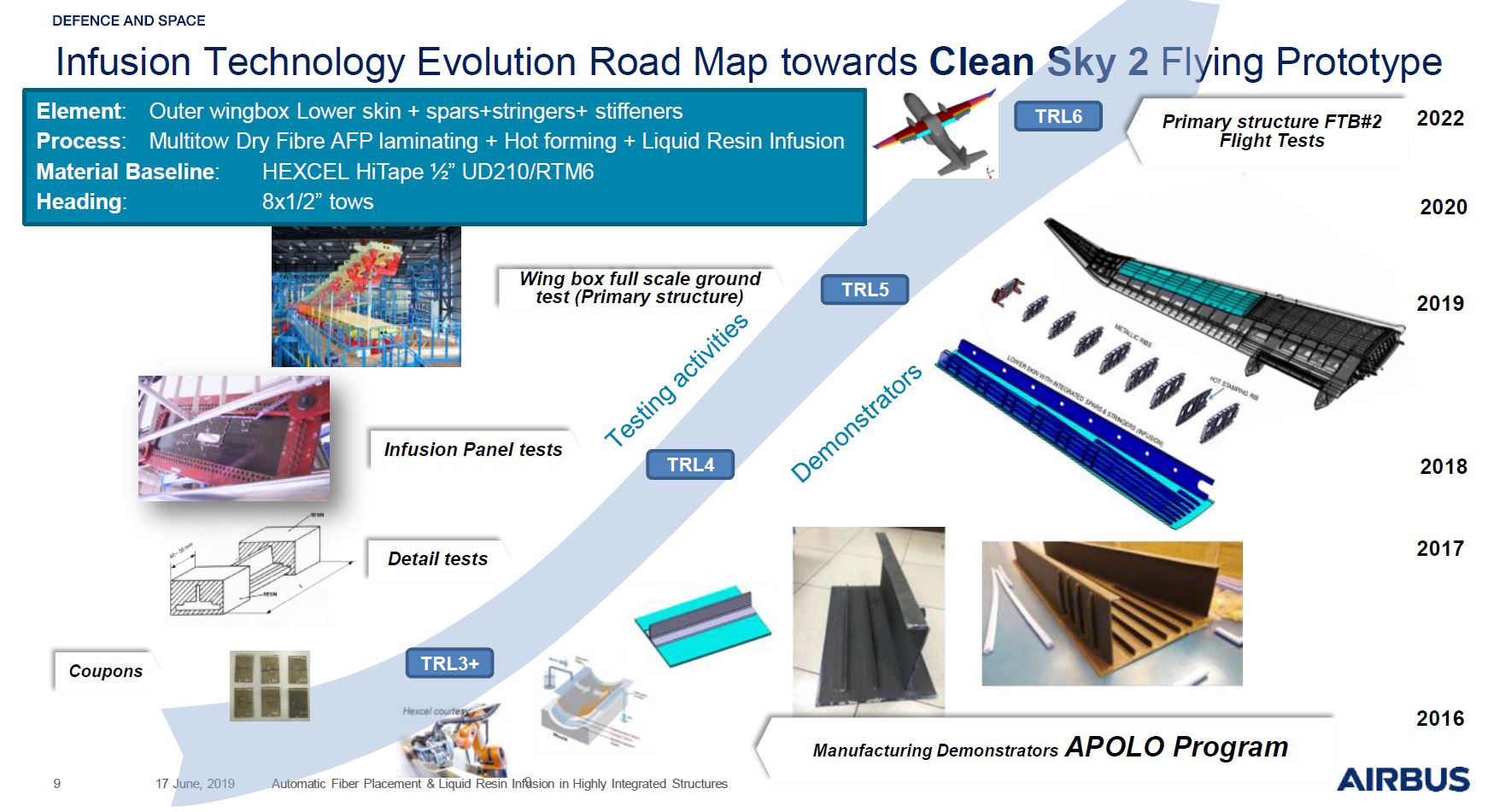
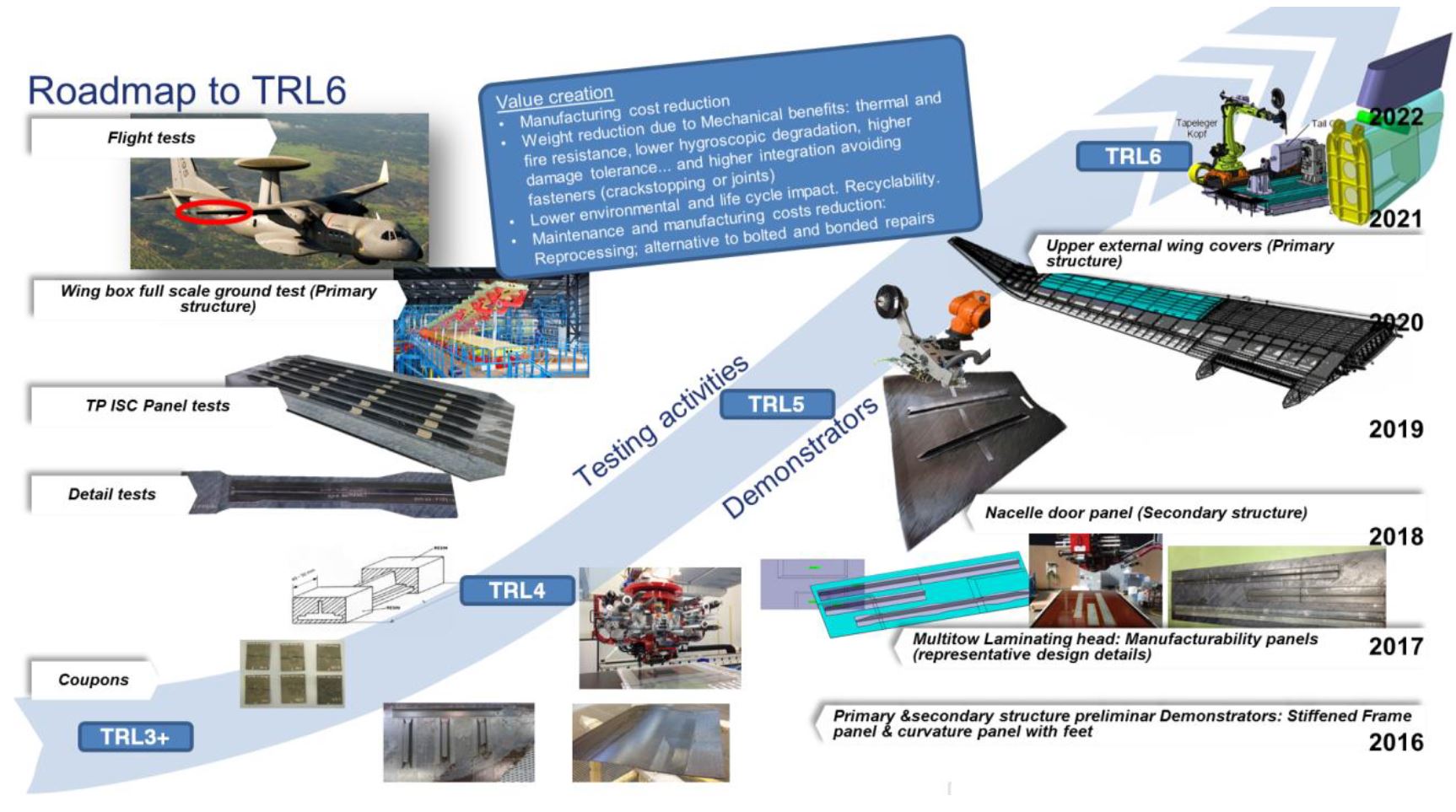
FTB#2 externe Flügeltore und Hintergrund
„Jedes zukünftige Flugzeugdesign erfordert mehr Ökoeffizienz über den gesamten Lebenszyklus“, sagt Gahete. Dies sollte Folgendes beinhalten:
- Weniger Energie für die Komponentenfertigung
- Weniger Primärmaterialschrott
- Geringerer Verbrauch von Produktionsflüssigkeiten und Hilfsstoffen
- Erhöhte Recyclingfähigkeit.
Solche Verbesserungen waren Schlüsselfaktoren bei der Entwicklung des strukturellen Designs und des Produktionsprozesses für den FTB#2-Außenflügel, zusammen mit Zielen für geringeres Gewicht (-10 %) und Herstellungskosten sowie eine höhere Produktionseffizienz.
Thermoplastische Verbundwerkstoffe und Harzinfusion spielen beide eine Schlüsselrolle im Außenflügel des FTB#2. In-situ-konsolidierte (ISC) thermoplastische Verbundwerkstoffe (TPC) und trockene Faser/Harz-Infusion ermöglichen die Herstellung großer Primärstrukturen OOA zu geringeren Kosten im Vergleich zu herkömmlichen Autoklaven-basierten Prozessen. Thermoplastisches Schweißen und hochintegrierte Strukturen in einem Schuss reduzieren auch die Auswirkungen der Montage, mechanischer Befestigungselemente, der Bearbeitung dieser Befestigungselemente und der gesamten Inspektion.
Infusionstechnologie Die Entwicklung von Clean Sky 2 begann mit früheren Clean Sky-Projekten wie GRA, ECO-DESIGN, APOLO und CERTERIN. In der Zwischenzeit ISC TPC wurde in den Clean Sky-Projekten ICARO, TARGET, ECO-DESIGN und Green Regional Aircraft-Light Weight (GRA-LW) ausgereift, sodass diese Technologie in den Flugdemonstrator Clean Sky 2 FTB#2 integriert werden kann.
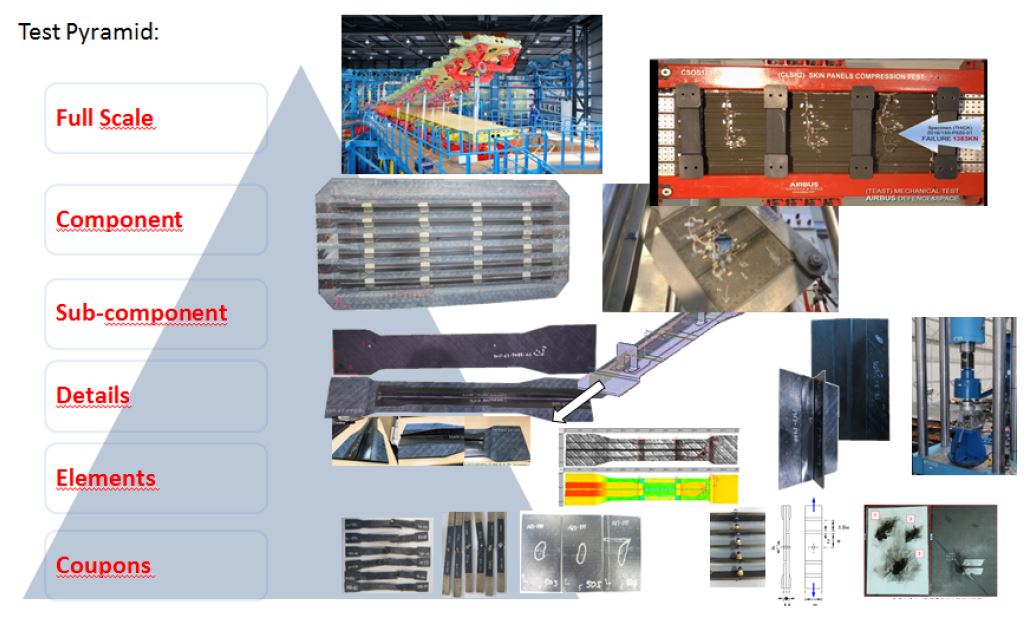
Abb. 10. Testpyramide. Bildnachweis:„Hochintegrierter Flügelkastenabschnitt von Airbus Defence and Space, hergestellt durch Trockenfaserplatzierung und Flüssigharzinfusion“, von A.E. Jiménez Gahete, Materiales Compuestos vol. 4, Nr. 4, S. 19-26, Sept. 2020.
FTB#2-Zertifizierung für externe Flügel
Wie Gahete erklärt:„Schritt für Schritt durchlaufen wir [Airbus DS] die gesamte Testpyramide der Flugzeugstruktur, von Coupons bis hin zu den vollständigen strukturellen Tests des Außenflügels.“ Hexcel HiTape, UD 210 Gramm pro Quadratmeter (gsm) und 12,7 mm breit mit thermoplastischem Schleier V800E auf beiden Seiten (Schleiergewicht 4 gsm pro Seite), angereichert mit Hexcel HexFlow RTM6 180 °C härtendem Epoxidharz, wurde vollständig charakterisiert, einschließlich unidirektionaler und mehrwinkliger Eigenschaften. Testergebnisse zeigten, dass dieses Material im Vergleich zu HexPly M21E Epoxid-Prepreg aus HexTow IMA-Zwischenkohlefaser, das zur Herstellung von Flügelhäuten, Holmen und Mittelflügelkästen für den Airbus A350 verwendet wird, eine gute Leistung im Modul, aber eine geringere Festigkeit in Bezug auf die Festigkeit aufweist. Quasi-isotrope Laminate zeigten im Vergleich zur gleichen Referenz gute Ergebnisse.
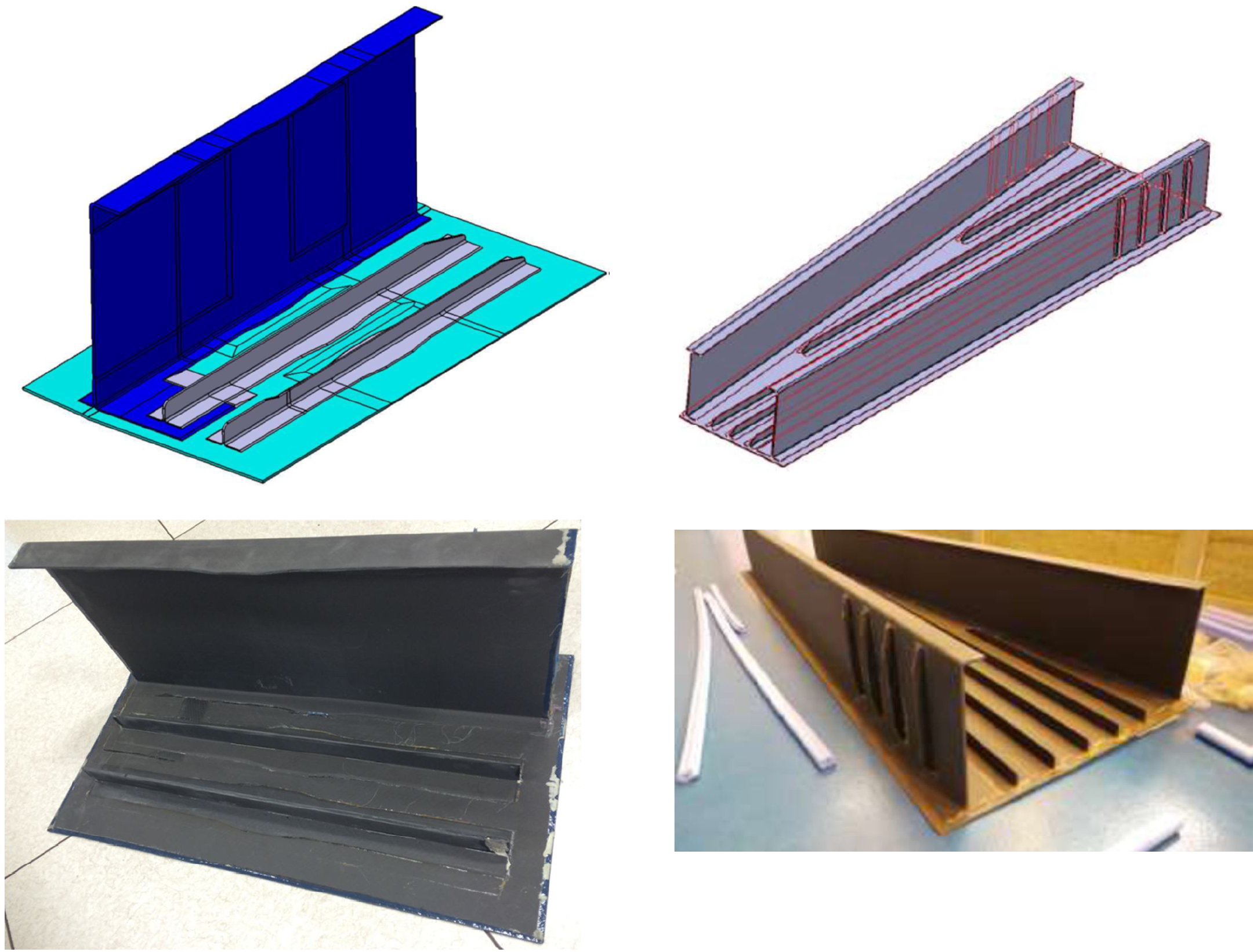
Gahete erklärt, dass zusätzlich zu den Coupons für die Materialcharakterisierung und vor den Detail- und Panel-Unterkomponententests, um die zulässigen Konstruktionsmerkmale zu erhalten, Fertigungsdemonstratoren verwendet wurden, um zu validieren, „welche Konstruktionsmerkmale mit den ausgewählten Herstellungsprozessen erzielt werden könnten“. DEMO1 integriert einen Abschnitt aus einer Haut mit variabler Dicke, einem J-Holm mit Rippenversteifungen und zwei Stringern, die in die Haut und den J-Holm-Flansch integriert sind. Und DEMO2 – 3 Meter lang x 0,86 Meter breit x 3,44 Meter hoch – simuliert die Gesamtabmessungen des Außenflügelkastens FTB#2 und umfasst fünf Stringer. Gahete stellt fest, dass einige Prozessanpassungen in einigen Iterationen vorgenommen wurden, bevor erfolgreiche Ergebnisse bei Strukturteiltests erzielt wurden.
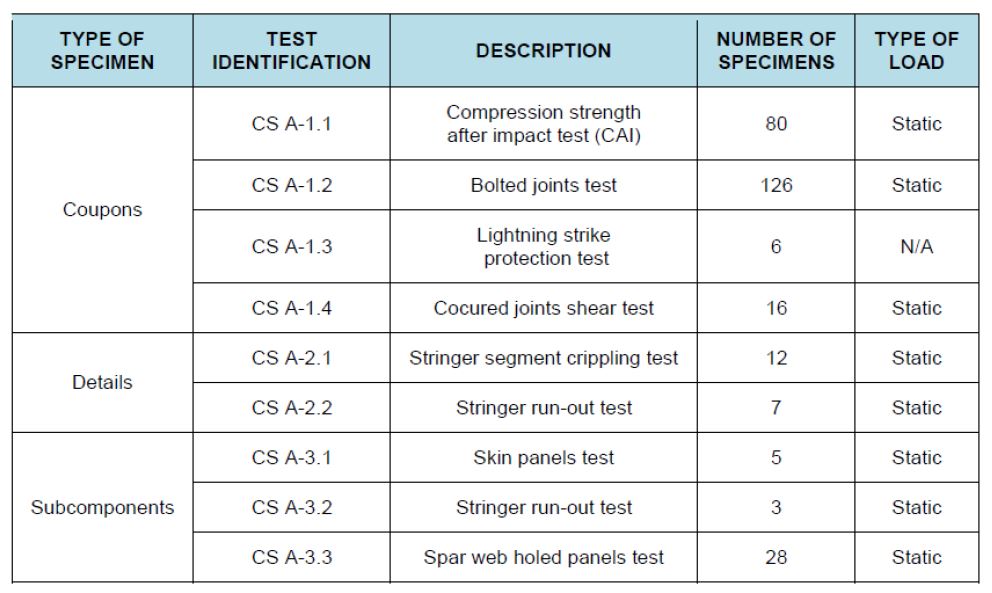
Abb. 9. Entwicklungstestmatrix für den Außenflügel FTB#2. Bildnachweis:Gahete, Materiales Compuestos vol. 4, Nr. 4, S. 19-26, Sept. 2020.
Außerdem wurde eine Testmatrix für Konstruktionsdetails erstellt, einschließlich Blitzschlag-, Stringer-Auslauf- und Stringer-Verkrüppelungstests (zur Beul- und Versagensbewertung). Die Tests der Teilkomponenten-Panels wurden ebenfalls mit positiven Ergebnissen abgeschlossen. Nachdem die gesamte Testpyramide erfolgreich abgeschlossen wurde, von Coupons bis hin zu Unterkomponenten, bleiben laut Gahete nur noch die letzten vollständigen statischen und funktionalen Tests des Außenflügels, um die FTB#2-Qualifikation für den Flug zu erhalten. Diese Tests sollen bis Ende 2021 abgeschlossen sein.
FTB#2 als Teil einer umfassenderen Technologieentwicklung
Die externe Flügelbox ist nur ein Teil von FTB#2, das Airbus DS liefert. Andere strukturelle Demonstratoren – wie in dem 2019 von Airbus DS verfassten und 2019 von der European Conference for Aeronautics and Space Sciences (EUCASS) veröffentlichten Papier „Structural Radar Research of Airbus Defence and Space as Clean Sky Partnership“ erläutert – umfassen MT1 oder MT2-Cockpits (siehe Bild unten) mit hoher struktureller Integration zur Gewichts- und Kostenreduzierung, Flügelvorderkanten mit Morphing-Funktionen und vollständiger Außenflügel mit Winglet und Morphing-Flap. (Beachten Sie, dass letzteres über das Air Green 2-Projekt von CIRA – Italian Aerospace Research Centre – vorangetrieben wird.)
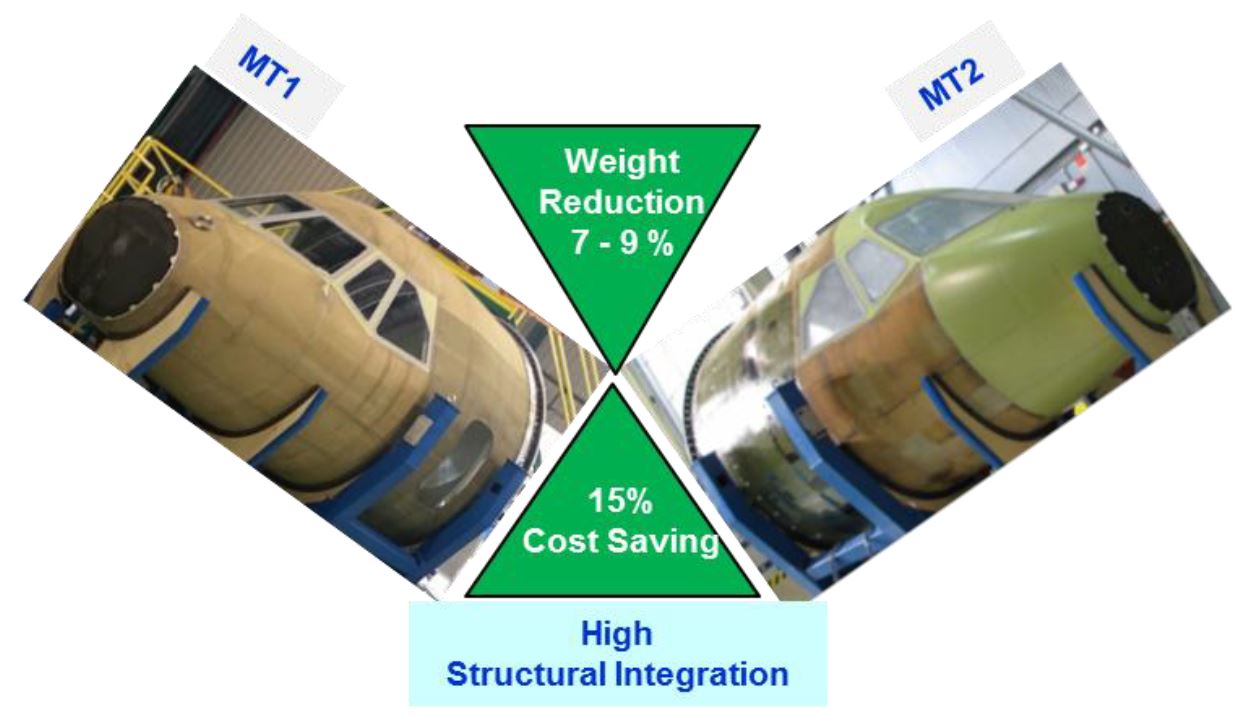
Die folgende Abbildung zeigt verschiedene Forschungsarbeiten von Airbus DS innerhalb von Clean Sky (CS1) und Clean Sky 2 (CS2) als Teil eines breiten Technologieportfolios.
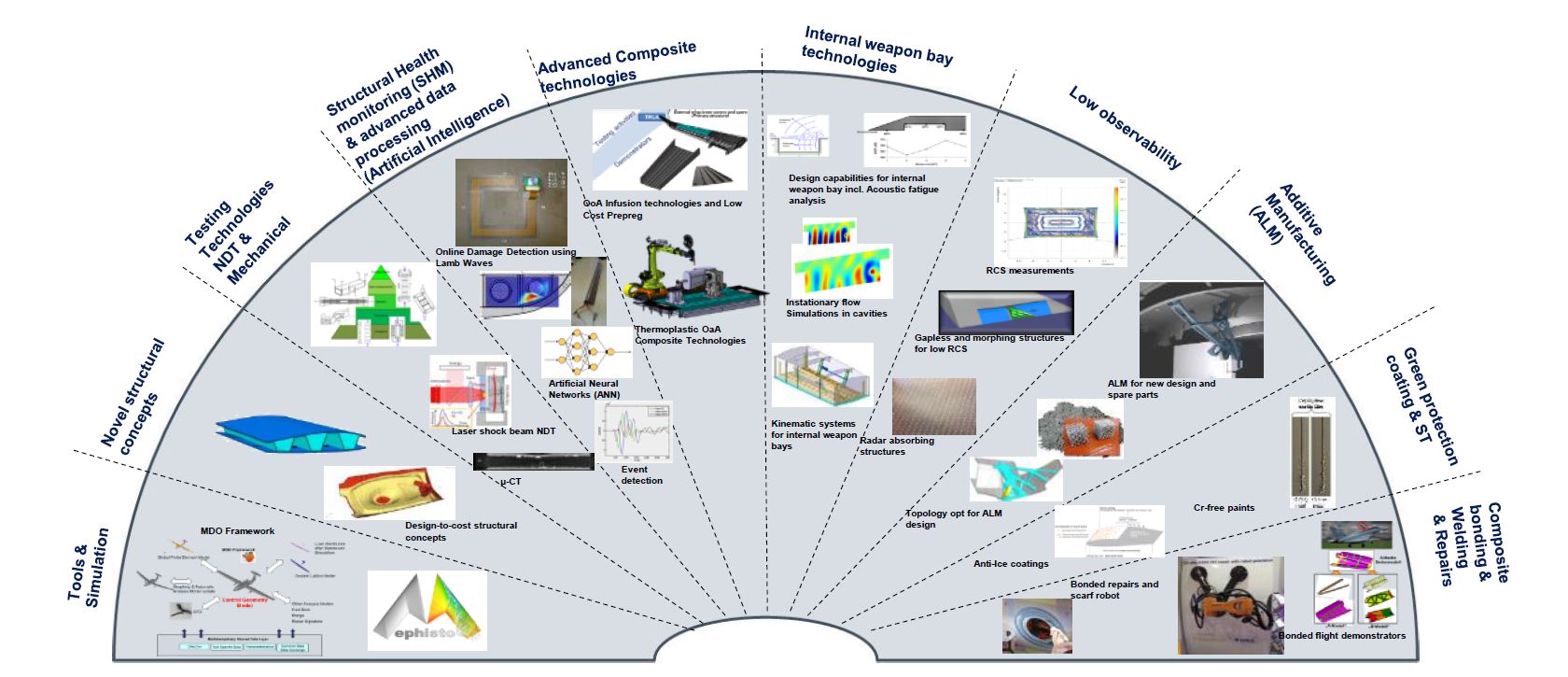
Auch im EUCASS-Papier erläutert, haben diese Forschungsprojekte nicht nur fortgeschrittene Verbundwerkstofftechnologien, sondern auch neue Entwicklungen bei Metallen sowie additive Fertigung, Werkzeugbau und Reparatur:
- Hochintegrierte Primärstruktur
- Einmaliges co-gehärtetes, versteiftes multifunktionales, doppelt gekrümmtes festes Laminat
- Hohe Integration von Bulk-Frames durch Flüssigharzinfusion (LRI)
- Volllaminat (unterer ehemaliger FR-9)
- Versteiftes Sandwich (Vorwärtsdruckschott FR-1)
- Untere Haut und Holme der FTB#2-Flügelbox
- Hohe Integration durch thermoplastische In-situ-Konsolidierung (ISC)
- Kleine Krümmung (FR-4 von MT1/MT2; Oberhaut von FTB#2 Außenflügelkasten)
- Thermoplastisches kontinuierliches Formen (Stringer)
- Hohe/doppelte Krümmung (Vorderkante und Verkleidung)
- Rumpfrahmen/Flügelrippe aus warmgeprägtem Leichtmetallblech
- Sekundärstruktur:kostengünstige TPC- und ALM-Fensterrahmen (Additive Layer Manufacturing)
- Werkzeugtechnologien:kostengünstiger Verbundwerkstoff und ALM
- Reparaturen und Wartung
- Standardreparatur auf hochintegrierter gebogener, versteifter Haut (Pre-Preg)
- Thermoplastische ISC-Co-Konsolidierung und -Schweißen
- RTM-LRI-Strukturelemente
- Prepreg-Patch-Anwendung
- Trockenmaterialpflaster plus Harzinjektion
- Harzinjektion zur Fixierung externer Multifunktionsschichten
Die vorrichtungslose Montage war ebenfalls ein wiederkehrender Schwerpunkt, ebenso wie die Entwicklung neuer digitaler 4.0-Systeme und Prüftechnologien, wie sie im EUCASS-Papier aufgeführt sind:
- Interferometrie (DIC)
- Multi-Impact-Test mit mittlerer Energie
- Vibrationstests
- Thermografie
- NDT-Antrag
- Strukturelles Verhalten in heißer Umgebung
- SHM-Sensoren und Messtechniken
- Faseroptik FBG (Fiber Bragg Grating)
- OBR (Optische Rückstreu-Reflektometrie)
- MEMS (Mikro-Elektro-Mechanische Systeme, die elektrische und mechanische Komponenten auf einem einzigen Computerchip kombinieren)
- p-U-Akustik (Druck-Geschwindigkeits-basierte in-situ-Absorptionsmessung)
Gemeinsamer EU-Rahmen für die Zertifizierung
Eine letzte Anmerkung aus den Papieren von EUCASS und Gahete ist die Anerkennung der engen Zusammenarbeit mit und der Arbeit, die von einer Reihe wichtiger Airbus DS-Partner wie NLR (Netherlands Aerospace Centre), Airborne (Den Haag, Niederlande), Applus+ Laboratories (Barcelona, Spanien), MTorres (Torres de Elorz, Spanien) und FIDAMC (Getafe, Spanien), letztere beschrieben als „wesentlich beteiligt an allen Technologien, die mit Verbundwerkstoffen und deren Herstellungsprozessen entwickelt werden“.
Ich habe seit einiger Zeit die Aktivitäten und Veröffentlichungen von Ingenieuren bei Airbus in Getafe zur Kenntnis genommen und über die ISC-TPC-Arbeit von FIDAMC und anderen geschrieben. CW hat auch in vielen Artikeln über Clean-Sky-Projekte die Führungsrolle von Airbus DS hervorgehoben. Aber bis jetzt habe ich nicht verstanden, wie langfristig und geplant die DS-Strategie von Airbus ist, die ihre Beteiligung an und ihren Beitrag zu Clean Sky-Programmen optimal nutzt. Es ist durchaus sinnvoll, bei der Entwicklung neuer Cockpit- und Flügeldemonstratoren die Grundlagen für die Zertifizierung zu legen. CW schrieb über denselben Ansatz, den Themenführer Airbus Deutschland im Rahmen des Clean Sky 2 Multifunctional Fuselage Demonstrator (MFFD) verfolgt. In diesem Fall wird im Teilprojekt MECATESTERS eine vollständige Charakterisierung von niedrigschmelzendem Polyaryletherketon (LM PAEK) in Schweißverbindungen erreicht.
Die in diesem Bericht gezeigten Airbus DS-Roadmaps und Strukturtechnologie-Radarabbildungen sind ein weiteres Beispiel dafür, wie die europäische Luftfahrt- und Verbundwerkstoffindustrie zusammenarbeiten, um für die Zukunft gerüstet zu sein. Clean Sky 2 ist weiterhin erfolgreich, indem es Europas Flugzeug- und Verbundwerkstoffindustrie eine ehrgeizige Vision und einen finanzierten Rahmen für die Zusammenarbeit bietet, um klare Ziele zu erreichen. Diese Arbeit wird auch dazu beitragen, dass sich die Branche auf Elektrifizierung, Wasserstoff und alternative Kraftstoffe umstellt, um den Klimawandel zu überwinden, und sowohl die Luftfahrt als auch Verbundwerkstoffe spielen dabei eine Schlüsselrolle.
Harz
- Saftbox
- Topografische Karte
- Raspberry Pi CD-Box-Roboter
- Craftech Industries erhält ISO 9001:2015-Zertifizierung
- C# - Klassen
- C# – Überladen von Operatoren
- Kaneka Aerospace erhält die AS9100D-Luft- und Raumfahrtzertifizierung
- Was ist ein Box Cut?
- Was ist Straßenöl?
- Flugzeugkomponenten und Präzisionsflugzeugteile