Verbundwerkstoffe beschleunigen die Herstellung von Betonfassaden
Jedes heute gebaute mehrstöckige Gebäude benötigt eine Fassade. Abgeleitet vom französischen Wort Fassade , das wiederum aus dem italienischen facciata stammt , es bedeutet "Gesicht". Kurzum, die Fassade ist die nach außen gerichtete Struktur, die dem Gebäude Charakter, Farbe und Form verleiht. Für Architekten ist die Fassade sehr prägend für den Rest des Gebäudes und sagt viel über die architektonische Absicht des Designers aus.
Eine Fassade ist auch funktional. Es bildet die Struktur, die Fenster und Türen umgibt, schützt das Gebäude vor Witterung und Stößen und beeinflusst die Energieeffizienz des Gebäudes. Eine Fassade kann aus einer Vielzahl von Materialien hergestellt werden, darunter Verbundwerkstoffe, Stein, Stahl, Glas oder Beton. Beton in einer Fassade kann aufgrund seiner Formbarkeit verwendet werden, um einem Gebäude ein sehr dimensionales und optisch wirkungsvolles Erscheinungsbild zu verleihen, insbesondere wenn die Betonformen variiert werden.
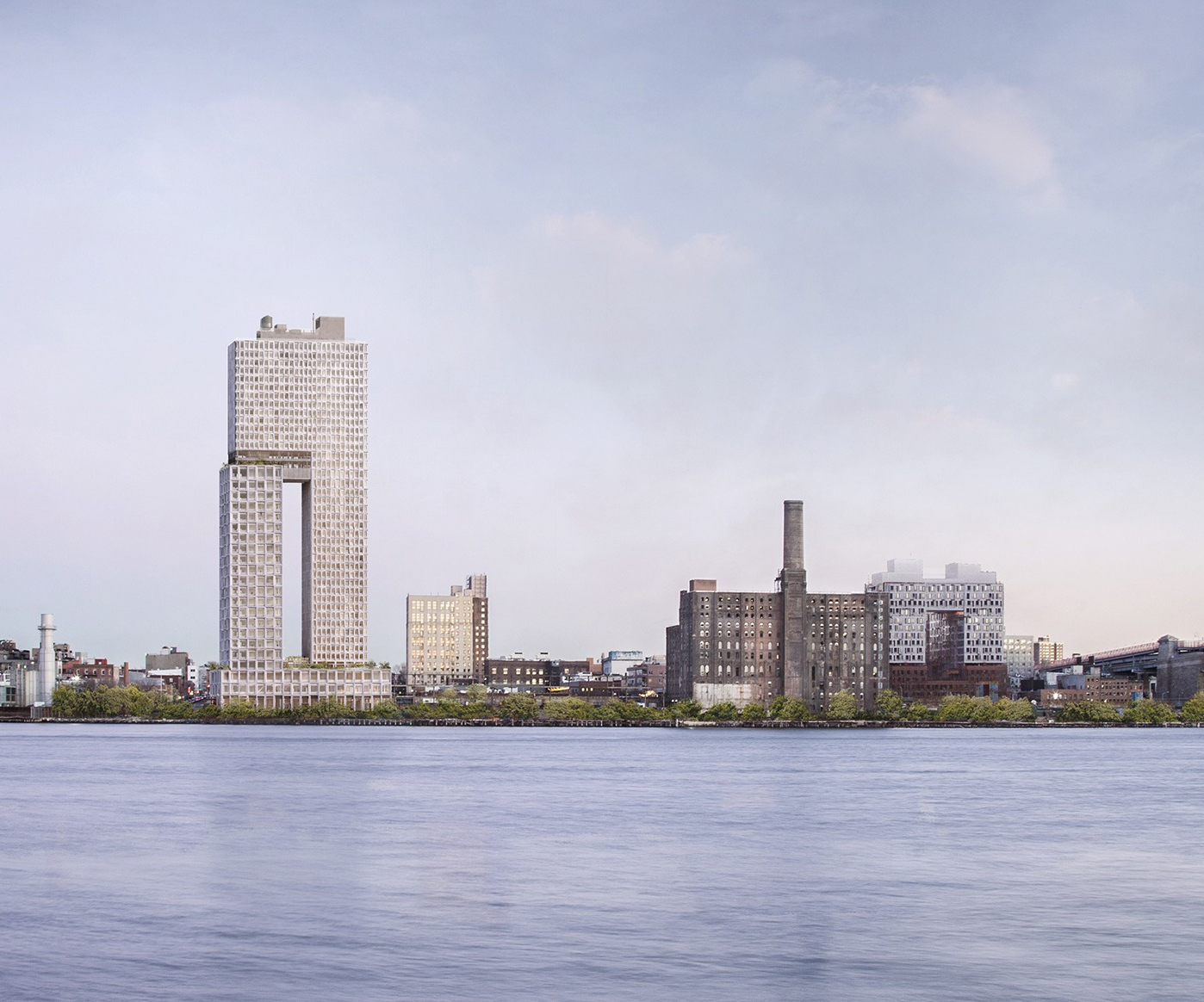
Zucker ist König
Dies war bei Domino Park der Fall, einem 11 Hektar großen Sanierungsprojekt entlang der Williamsburg Waterfront in Brooklyn, NY, USA als Büro- und Einzelhandelsflächen. Ein Teil des Domino Parks umfasst mehrere neue Gebäude, darunter das 45-stöckige One South First und das verbundene 10 Grand. Für diese Gebäude entschied sich der Architekt COOKFOX (New York, NY) für eine Betonfassade mit mehreren Oberflächenwinkeln, mehreren Fensterrahmenformen und mehreren Fensterrahmenbreiten, um aus der Ferne ein Gefühl von Zuckerkristallinität zu vermitteln, in mit dem Verlauf der Website.
Gate Precast Co. (Jacksonville, Florida, USA) erhielt den Auftrag zum Bau der Betonfassade – im Wesentlichen einer Reihe von Fensterrahmen – für das One South First-Projekt. Das Unternehmen würde, wie für eine Betonfassade typisch, die Rahmen im eigenen Werk fertigen und dann die fertigen Rahmen zur Baustelle transportieren, wo sie per Kran zur Montage angehoben werden. Hätte Gate beschlossen, der Tradition zu folgen, hätte es Holzformen gebaut, mit denen alle Betonrahmen geformt wurden. Gate entschied sich jedoch, der Tradition nicht zu folgen.
Um das zu verstehen, gehen Sie zurück ins Jahr 2017, als Gate mit dem Precast/Prestressed Concrete Institute (PCI, Chicago, Illinois, USA) und dem Oak Ridge National Laboratory (ORNL, Oak Ridge, Tennessee, USA) zusammenarbeitete, um eine vorläufige Bewertung von den Einsatz großformatiger additiver Fertigung zum Bau von Verbundformen für die innerbetriebliche Betonfertigteilformung. Diese Bewertung wurde mit einer BAAM-Maschine (Big Area Additive Manufacturing) bei ORNL durchgeführt. BAAM ist eine großformatige additive Fertigungsmaschine mit einem 25 Quadratmeter großen Bauraum, die von ORNL und Cincinnati Inc. (Harrison, Ohio, USA) gemeinsam entwickelt wurde. Gate hat sich zum Ziel gesetzt, Verbundformen für die One South First-Fassade zu bauen. Das Projekt erforderte insgesamt 80 Formen, von denen 37 gedruckt werden sollten. Die restlichen 43 würden aus Holz bestehen. Als diese Entscheidung getroffen wurde, waren die Fristen für die Lieferung der Formen knapp.
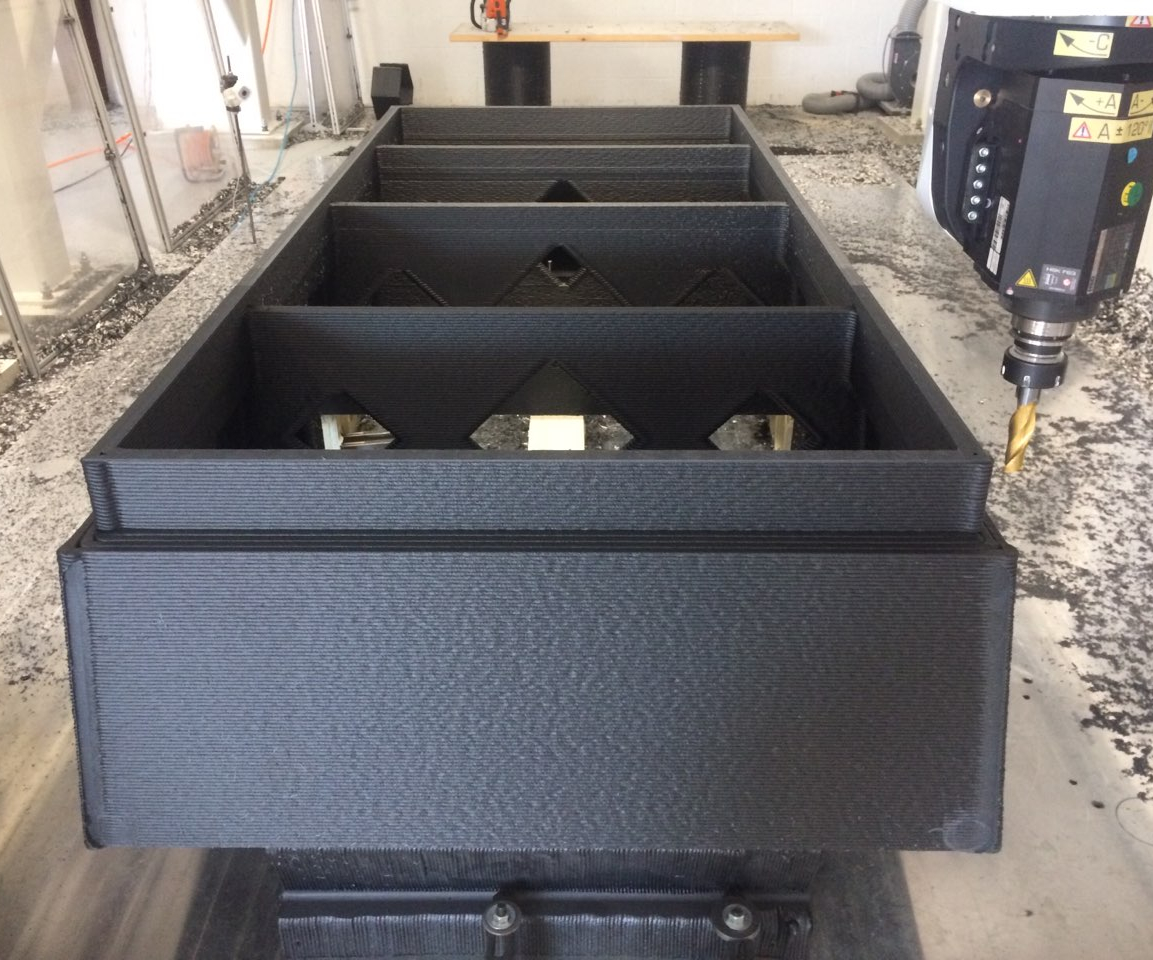
Im Jahr 2016 hatte Additive Engineering Solutions (AES, Akron, OH) seine erste BAAM-Maschine von Cincinnati Inc. erworben. Aus diesem Grund wandten sich ORNL und Gate Precast an AES, um Hilfe zu erhalten. Andrew Bader, VP und Mitbegründer von AES, sagt, dass sein Unternehmen und ORNL das Arbeitspaket aufteilten, wobei AES 18 der 37 Formen herstellte. Bader sagt, dass jede Fensterrahmenform etwa 5-6 Fuß breit, 9-10 Fuß hoch und 16 Zoll tief ist und etwa 500 Pfund wiegt.
Bader sagt, dass die Geometrie der Formen im Inneren relativ einfach war, da sie so konstruiert sind, dass sie Rahmen erzeugen, die rechteckige Fenster umgeben. Die Gestaltung der Außenflächen der Rahmen war jedoch, wie erwähnt, komplexer, mit unterschiedlichen Tiefen und Winkeln, die in jede Form integriert wurden. Eine gedruckte Form ersetzte eine Holzform, die aus vielen einzeln geschnittenen zusammengenagelten Teilen bestand. „Die Geometrie war einfach, aber kompliziert“, sagt Bader. „Das Projekt erforderte mehrere einzigartige Rahmendesigns, je nach Rahmenposition.“
Für einen Teil seiner Produktion hat sich AES für ein LNP THERMOCOMP AM Compound entschieden, ein hochmoduliges, verzugsarmes Material auf ABS-Basis mit 20 % geschnittener Kohlefaserverstärkung von SABIC (Houston, Tex., USA). Bader sagt, dass die BAAM-Maschine 8-10 Stunden brauchte, um jede monolithische Form zu bauen, gefolgt von 4-8 Stunden Bearbeitung und Endbearbeitung in einer Quintax (Stow, Ohio, USA) CNC-Maschine. Er berichtet, dass die Formen auf die erforderlichen Maße geschliffen, aber nicht versiegelt wurden.
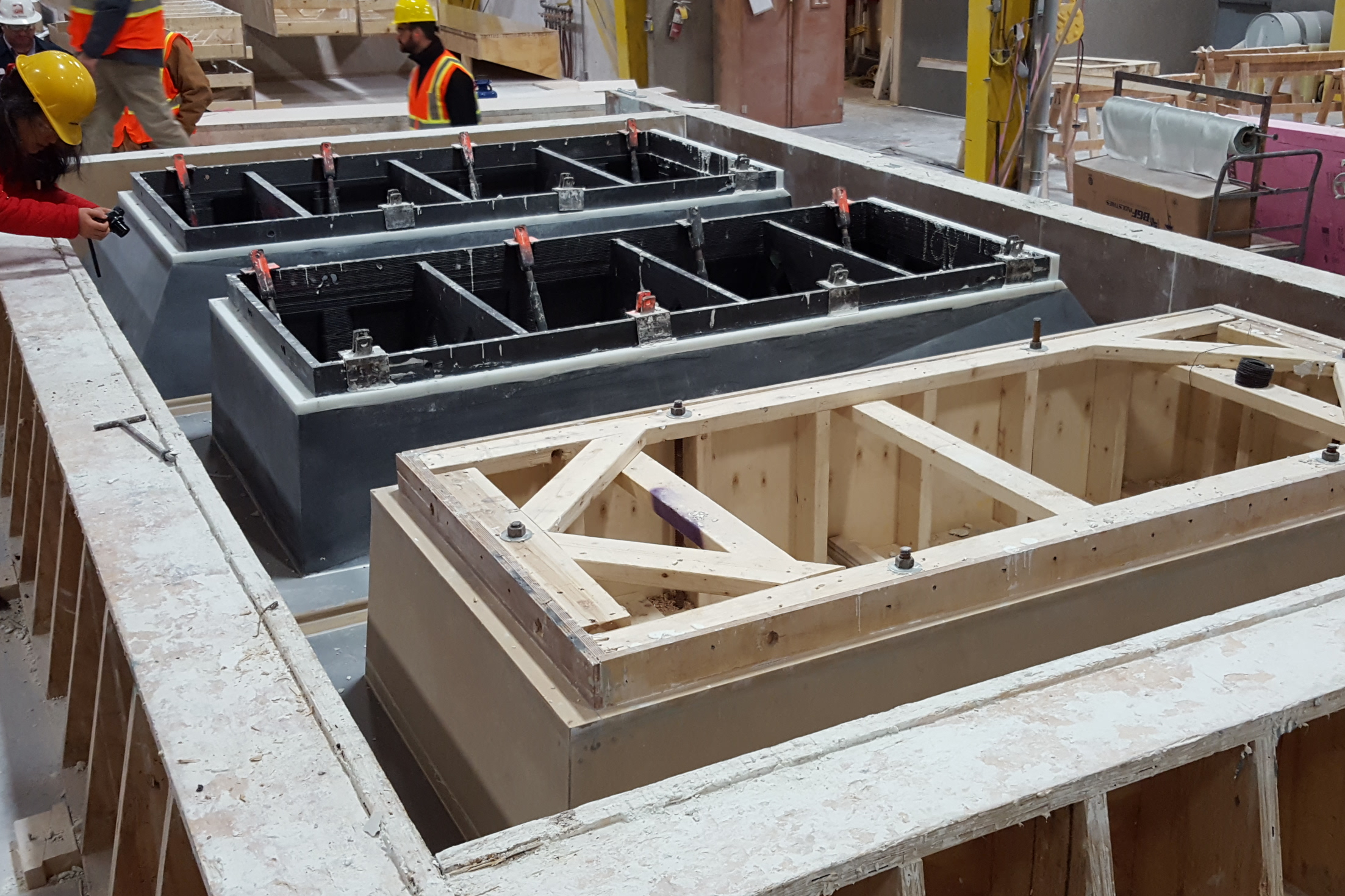
Fensterrahmen herstellen
Die Formen wurden an Gates Werk in Winchester, Kentucky, USA, geliefert, wo sie zusammen mit den 43 traditionellen Holzformen verwendet wurden, die Gate für das Projekt baute. Die Holzformen wurden von Gate-Mitarbeitern von Hand zusammengebaut, dann wurden eine Glasfasermatte und eine Harzbeschichtung aufgetragen, wobei Formöl aufgesprüht wurde, um das Lösen des geformten Betonrahmens zu erleichtern. Formöl wurde auch auf die Verbundformen gesprüht, um das Ablösen zu erleichtern.
Um einen Betonguss durchzuführen, wurden mehrere Formen auf einen 40-50 Fuß langen Holzgießtisch gelegt. Formen wurden zu einem Einzelrahmen, einem Doppelrahmen oder einem Dreifachrahmen zusammengefügt. In jede Form wurde ein Bewehrungsstahl eingelegt und um den Bewehrungsstab herum wurde Beton gegossen. Der Gießtisch wurde dann vibriert, um den Beton zu verfestigen. Nach 14-20 Stunden Aushärten wurden die Fensterrahmen entformt, mit Säure gewaschen und poliert. Dann wurden die Fenster eingebaut und das gesamte Paket per LKW zur Baustelle in Brooklyn verschifft.
Bader sagt, dass die AES-Verbundformen, die neben den traditionellen Holzformen arbeiten, schnell ihre Vorteile offenbart haben. Erstens, sagt er, erlaubt eine Holzform nur 15-20 Betonierungen, bevor sie außer Betrieb genommen und renoviert oder ersetzt werden muss. Die AES-Formen hingegen ermöglichten 200 Betoniervorgänge mit minimaler Sanierungs- oder Stillstandszeit. Und die 200 Güsse, sagt Bader, stellten das Ende des Projekts dar, nicht das Ende der Werkzeuglebensdauer. „Da haben sie aufgehört“, sagt er. „Wenn unsere Formen richtig gepflegt werden, können sie unserer Meinung nach Hunderte und Hunderte Male verwendet werden.“
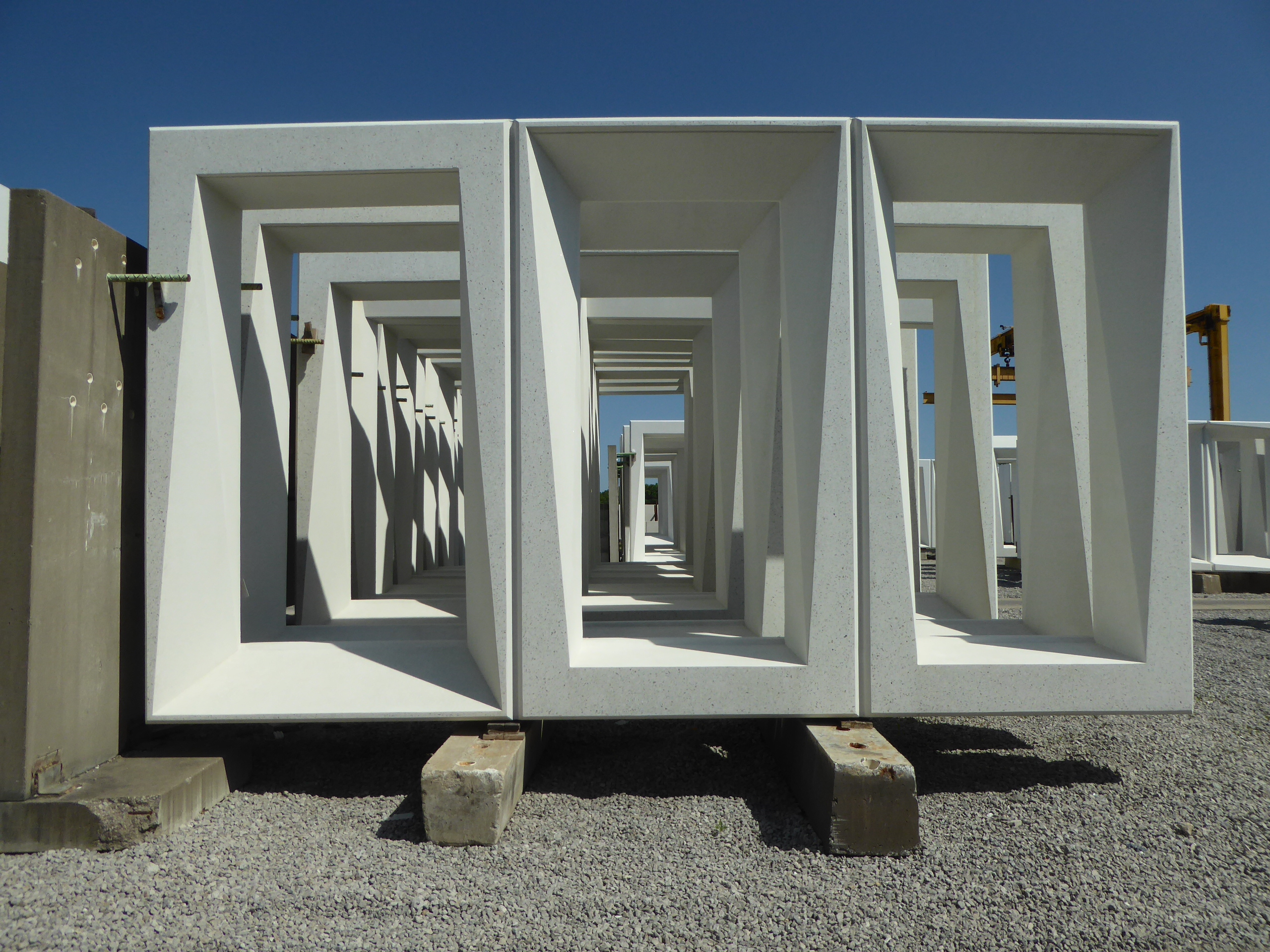
Darüber hinaus berechnet Gate bei einer Verwendung von 150 oder mehr Gussformen bis zu 10 Holzformen, um die Leistung einer AES-Form zu erreichen. Angesichts der Tatsache, dass Gate 40 Arbeitsstunden benötigt, um eine Holzform herzustellen, hätte das Unternehmen ohne die 37 Verbundformen die Zeitplananforderungen des One South First-Projekts nicht erfüllt.
Bader räumt ein, dass eine AES-Verbundform viermal so viel kostet wie eine Holzform, aber mindestens zehnmal haltbarer ist. „Die Bauweise von Fertigteilen ist über Jahrzehnte relativ unverändert geblieben“, stellt Bader fest. "Plötzlich, eines Tages, machen wir 3D-Formulare mit einem Gewicht von 500 Pfund und alle waren schockiert." Er räumt jedoch ein, dass die additive Fertigung solcher Formen die meisten ist kosteneffektiv bei Anwendungen, bei denen Betonformen eine komplizierte Geometrie oder eine hohe Wiederholungszahl aufweisen – dieselbe Form viele Male.
AES, berichtet Bader, besitzt und betreibt jetzt vier BAAM-Maschinen und kann Teile mit einer Höhe von bis zu 2,40 m produzieren. Viel größere Teile wurden durch Zusammenfügen mehrerer Teile konstruiert.
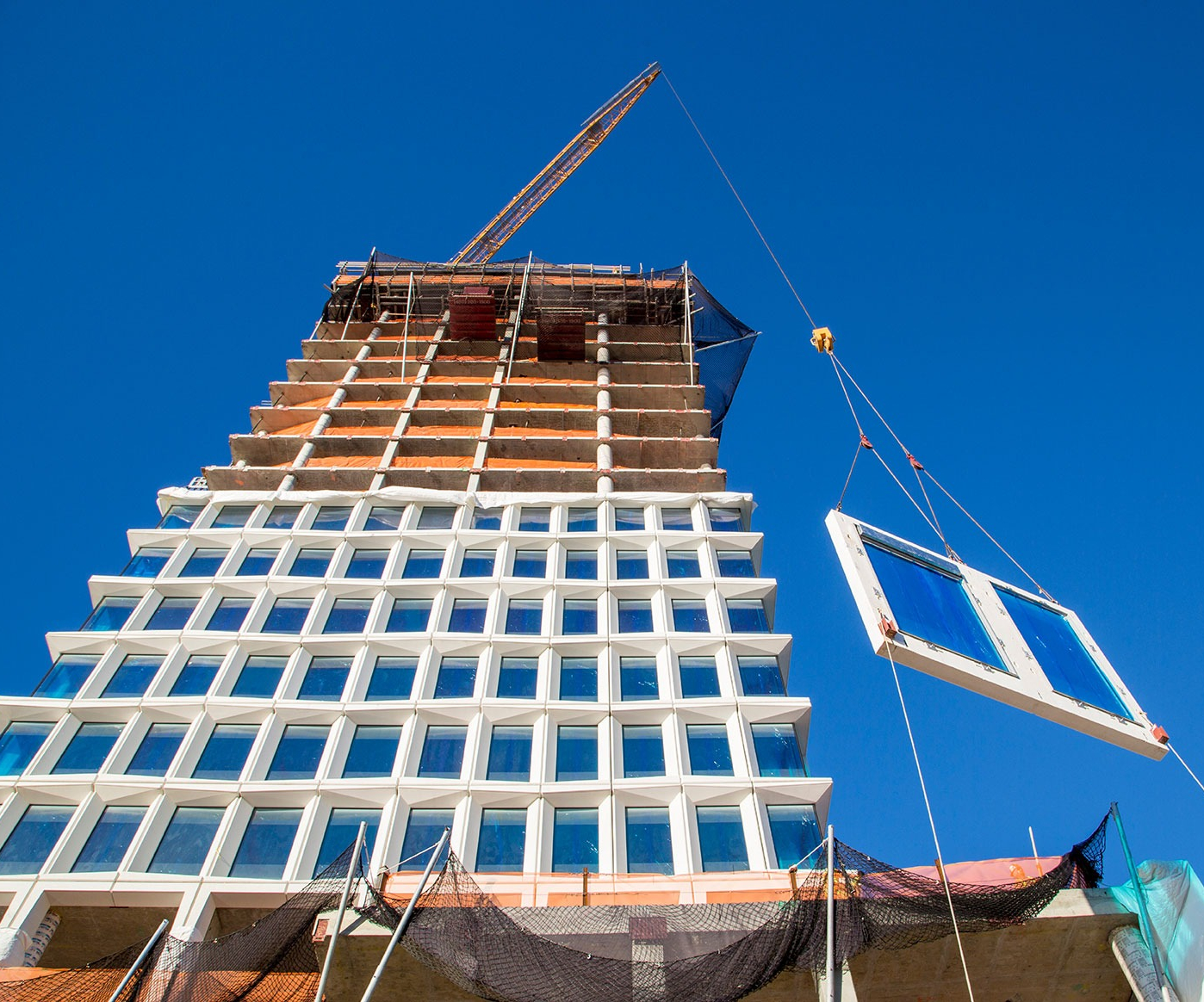
Harz
- Tachometer
- Beton
- CompositesWorld SourceBook 2022
- Fehlerbehebung beim Thermoformen von thermoplastischen Verbundwerkstoffen
- Die Entwicklung additiver Verbundwerkstoffe
- Thermoplastische Verbundwerkstoffe:Strukturelle Stoßstangenhalterung
- ATL Composites trägt zum Sanierungsprojekt für Betonpfeiler bei
- RS Electric Boats wählt Norco für die Herstellung von Verbundwerkstoffen
- Schweißen von thermoplastischen Verbundwerkstoffen
- Hochleistungsverbundwerkstoffe in Israel